重卡钢板弹簧断裂分析
重型汽车钢板弹簧的断裂失效形式及其材料的应用现状

其他f 也经 常 f 1 J 现残渣粉术。 、 板 赞 性 能 、 破坏 r 喷 凡肜 战的 表 饯 氽 受 力 发 生 微 振 导 致 的 磨 损 f f I f ,会 人 大 进 而 敛 力策 l I I 肜成 裂纹 。 一 l …} 板 碡 常 常 J L 干 公 l 凡 J 姚会火套 降 低 板 簧 的 坡 寿 命 。微 振 坡 火 效 多 裂 纹 , 片簧 t要的 失效 之 ,而 变 截 板 簧 } :
侏持 r 的 f ‘ 顺性f ¨ 个- . f 性。 能 降 重 已 伤 , 以 及
、 ・ 拔 l £ 溅 和 擦
图 1
7 过 巾 汴 火 裂 纹 、 野 蛮
随蕾i ‘ i 1 、 l k 的 发杖, 成为 l 1 i 』
操作l 乖 l 1 热 处 小 善 等 『 u j 题 , 也址 致 板
板 簧 何 时 会 l 1 1 心扎 处发, I - 断裂。
衬套之问装眦过 紧、 绉…I I f J l = ; 成 的 条纹 、 过 热 、 趔 度 过 “ I 挪 会 甘敛 橄 晴 I
材 料 和 I I : 艺 的 索 , 板 弹 磷 火 效 裂 纹 一般 l 起始 t : r } 1 心 扎 j 板 债 丧 的 交
2 . 2 板 簧卷耳失效
除 J ’ 故和 使 川 小 1 以外.毯 q 币 ¨
簧替代传统钏板弹赞,
l ^ 】 乍 也开 始
推 广 用 。 由 ¨ 1 人 J 艇 的 道路 情 况 和 辆] 况,以1 6 乏 钢 板弹 簧 制逃 过 巾 原
2 . 1 中心孔失效
力 破 传 递 到 板 簧 处 ,
『 f I 心 孔 附 近
车辆的使 J H 环 境 、拔 倚 人 小 、受 力 造 成 r应 力 集 中 。
板弹簧疲劳断裂原因的分析与改进措施

BL客车后钢板弹簧疲劳断裂原因的分析与改进措施田洪森(机电系,北京100044)摘要:本文通过对BL客车后钢板弹簧断裂断口形状、设计应力、原材料及理化性能等方面的分析,找出造成钢板弹簧疲劳断裂的原因,提出了改进的措施,使该钢板弹簧的疲劳寿命达到日本五十铃公司标准的要求。
关键词:钢板弹簧;疲劳断裂;原因分析;改进措施1问题的提出BL客车是对日本五十铃公司BE22客车技术引进、吸收、消化后的一种轻型客车,该客车后悬挂弹性元件是一变刚度钢板弹簧,该种钢板弹簧的优点是在客车空载、满载状态下呈非线性状态,即悬挂在客车空载、满载状态下接近等频性,从而可以提高客车的平顺性,乘客乘坐舒适性,本文通过分析BL客车后钢板弹簧在设计、试制、试验过程中出现非正常疲劳断裂原因分析,提出了改进措施,使其达到了日本五十铃公司BE22客车后钢板弹簧疲劳寿命的标准要求。
2 BL客车后钢板弹簧的结构BL客车后钢板弹簧为一多片半椭圆形且由主、副簧组成的变刚度钢板弹簧,总片数为12片,其中主簧9片,副簧3片,主片片厚为10mm,其余片厚为9mm,采用的弹簧钢为60Si2Mn,其中3~9片端部压延,使钢板弹簧接近等应力梁。
3 BL后钢板弹簧疲劳试验情况3.1 试验标准:按五十铃公司提供的BE22客车后钢板弹簧疲劳寿命试验标准执行即: 1)按实车状态夹紧;2)变形中心:Fa=58.5mm,Fmax=137mm(2.5G),Fmin=20mm;3)振动频率:60-120cpm;4)从产品中随机抽取三架钢板弹簧;5)疲劳寿命:疲劳循环次数3≥20万次。
3.2 试验设备:钢板弹簧疲劳试验机。
3.3 疲劳寿命试验结果如下:4对钢板弹簧疲劳断裂原因分析根据以上试验结果可以看出,疲劳断裂的簧片均在第7片且同在钢板弹簧的大卷耳端,且位置距钢板弹簧中心螺栓距离也差别不大(138、142、150),说明该钢板弹簧在此处存在规律性疲劳断裂源,而非偶然原因造成的,下面根据疲劳断裂试验结果及设计、生产过程对钢板弹簧疲劳断裂的原因进行分析。
钢板弹簧断裂问题研究

钢板弹簧断裂问题研究
钢板弹簧是一种常用的机械弹簧,具有重要的作用。
但是,在长时间使用过程中,弹
簧易发生断裂,对安全和可靠性将造成严重的影响。
因此,钢板弹簧断裂问题的研究具有
重要的意义。
1. 断裂形式
钢板弹簧通常会发生两种断裂形式:疲劳断裂和过载断裂。
疲劳断裂是由于弹簧长期
受重载振动作用,导致弹簧产生裂纹并逐渐扩展,最终导致断裂。
过载断裂则是由于弹簧
在短时间内受到超过其承受范围的负载而导致的断裂。
2. 断裂原因
弹簧的疲劳断裂往往是由于设计不当、材料质量问题或制造工艺不合理造成的。
例如,过小的直径、过低的初始张力或夹紧面积不足等都可能会导致弹簧的疲劳断裂。
过载断裂
的原因则可能是安全阀设置不合理、过载发生时未能及时停机等。
3. 预防方法
为了避免弹簧的断裂,我们可以从以下几个方面进行预防:
(1)合理设计:应根据实际工作负荷选择弹簧的直径、材料和初始张力等参数,并加强弹簧支撑及补强结构设计。
(2)质量控制:对材料进行严格的检测和筛选,确保使用的材料符合要求,同时控制弹簧制造过程中的工艺参数,保证每一只弹簧的品质稳定。
(3)维护保养:定期检查弹簧的使用状况,发现异常及时处理。
特别是在高温、潮湿、腐蚀等环境下,应更加重视弹簧的保养。
4. 结论
钢板弹簧的断裂会给工程师带来安全和可靠性的隐患。
因此,在设计、制造和维护过
程中需要注意弹簧的使用条件,严格执行相关的规范和与之相应的标准,避免断裂问题的
发生。
同时,也需要提高制造工艺和质量管理水平,确保弹簧的品质和寿命符合设计要
求。
钢板弹簧单边折断

焊接修复是一种常见的钢板弹簧单边折断修复方法,通过将断裂部分焊接在一起,实现修复。
详细描述
焊接修复具有操作简单、成本低廉的优点,适用于小范围、小尺寸的钢板弹簧断裂。然而,焊接过程中可能造成 钢板局部变形,影响钢板弹簧的平整度和刚度。此外,焊接质量受操作人员技能水平影响较大,需要经验丰富的 焊接工人进行操作。
钢板弹簧的断裂会影响车辆的制动 性能,特别是在紧急制动时,可能 导致制动距离延长。
承重能力
钢板弹簧是车辆承重的主要部件之 一,单边折断会降低车辆的承重能 力,影响货物运输和乘坐舒适度。
02
钢板弹簧单边折断原因分析
材料缺陷
01
钢板弹簧材料本身存在缺陷,如 夹杂物、气泡、裂纹等,这些缺 陷降低了材料的力学性能,容易 引发断裂。
道路状况不佳,如颠簸、坑洼等,会导致钢板弹簧承受额外的冲击和振动,从而 增加断裂的可能性。
载荷分布不均
钢板弹簧在承载过程中,如果载荷分布不均,会导致部分钢 板过载或欠载,从而引发断裂。
钢板弹簧的设计不合理,如长度、曲率半径等参数不合适, 也会导致载荷分布不均,增加断裂的风险。
03
钢板弹簧单边折断预防措施
材料质量控制
01
02
03
选用优质材料
确保钢板弹簧所用的材料 质量可靠,具有足够的强 度和耐久性,以降低断裂 的风险。
严格控制材料成分
对材料的化学成分进行严 格控制,确保各成分含量 符合标准要求,以提高材 料的综合性能。
进行材料检验
对采购回来的材料进行质 量检验,确保材料质量符 合要求,防止不合格材料 流入生产环节。
定期维护保养
对钢板弹簧进行定期维护 保养,清除表面污垢、锈 迹和杂物,保持其良好的 工作状态。
钢板弹簧断裂问题研究

钢板弹簧断裂问题研究钢板弹簧是一种常用的机械零部件,在许多工程和行业中都有着广泛的应用。
它具有结构简单、性能稳定、承载能力高等优点,因此受到了广泛关注和应用。
在使用过程中,钢板弹簧断裂问题却是一个常见的隐患,一旦发生,往往会给设备运行安全带来严重风险和损失。
对钢板弹簧断裂问题进行深入研究,寻找问题根源并提出解决方案,对于提高设备的安全性和可靠性具有非常重要的意义。
钢板弹簧断裂问题可能由多种因素引起,从材料的选择和制造工艺到使用条件的环境和负载等,都可能对钢板弹簧的断裂性能产生影响。
需要综合性地对这些因素进行研究,并提出相应的解决方案,以提高钢板弹簧的可靠性和安全性。
以下将对钢板弹簧断裂问题进行深入研究,探讨其可能的原因和解决方案。
一、材料和制造工艺钢板弹簧的材料选择和制造工艺对其断裂性能有着重要的影响。
材料的选取需要符合设备的使用条件和要求,具有足够的强度和韧性以及良好的抗蠕变性能,以保证弹簧在长时间的使用过程中不会发生断裂。
制造工艺需要保证弹簧的内部组织和结构均匀,避免出现裂纹和不良组织,从而影响其断裂性能。
在钢板弹簧的材料选择和制造工艺上,需要进行严格的控制和测试,以确保弹簧具有良好的材料和结构性能。
针对特定的使用条件和要求,也可以针对材料和制造工艺进行改进和优化,以提高弹簧的断裂性能。
二、使用条件和环境钢板弹簧在使用过程中,受到的负载和环境条件也会对其断裂性能产生影响。
在高温或低温环境下,弹簧的材料性能和力学性能可能会发生变化,从而影响其断裂性能。
如果弹簧受到超负荷或过载,也可能导致其断裂。
在设计和使用钢板弹簧时,需要充分考虑设备的使用条件和环境条件,合理选择弹簧的型号和规格,以保证其在实际使用过程中不会发生断裂。
对于特殊环境和负载条件下的弹簧,也可以进行特殊的设计和制造,以提高其断裂性能。
三、预防措施和解决方案针对钢板弹簧断裂问题,可以采取一些预防措施和解决方案,以提高其可靠性和安全性。
重型汽车钢板弹簧断裂失效形式及应用现状

重型汽车钢板弹簧断裂失效形式及应用现状钢板弹簧(Leaf Spring)是广泛用于汽车悬架结构的具有一定弹性的元件,由宽度相等长度不相同的复合金属弹簧片组合而成,该元件各个部位的强度是相等的,可以起到很强的减缓压力的作用,但是钢板弹簧由于长期受到大力压迫导致其在达到一定的承受值后会发生断裂,本文重点分析了钢板弹簧断裂的形式,并提出相关的技术改进方案供相关生产商参考。
标签:钢板弹簧;断裂失效形式;应用现状车辆在正常行驶时,会受到自身振动和外部一定强度的挤压力作用,此时钢板弹簧会压缩从而吸收车辆的动能,将动能转化为弹簧的弹性势能,由此车辆的动能逐渐被转化,避免了巨大的冲击作用,起到很好的缓冲效果,使车辆运行更平稳,操作更流畅,安全性更好。
当钢板弹簧承受的压力过大会发生断裂失效,下面重点分析钢板弹簧断裂的几种形式。
1 钢板弹簧断裂失效的形式1.1 中心孔失效中心孔是钢板弹簧最脆弱的部位,因为钢板弹簧受到力作用时,其所承受的力会共同作用于中心孔,使其发生断裂失效。
其断裂时会产生很多裂纹,其位于孔板的结合处,跨越整板。
经过专业人员研究发现,该种失效是由于螺栓松动,弹簧承受的作用力被汇集到中心孔,中心孔承受力的表面积小,故而力的强度就大,当强度超过一定的值,孔就断裂,导致裂纹,随后弹簧便失效。
1.2 卷耳失效车辆在行驶过程中会不可避免受到各种摩擦力以及外力碰撞作用,此外,司机在驾驶过程中也会出现挂挡力度过大等不规范的操作,如果卷耳和衬套之间过于紧密,会导致发热,变硬等现象,这会使钢板膨胀变大,导致一定的变型,使得弹簧卷上方失效。
当车辆行驶过长时间时,卷耳上已有的些许裂纹会进一步加速断裂,加速弹簧失效的过程。
1.3 腐蚀疲劳钢板弹簧持续受力,而且很多零件露天之后会遭到空气腐蚀,生锈变型,致使弹簧在裂纹处承受力大幅度降低,裂纹便会不断加深,当达到极限时,弹簧便会断裂。
失效的切面看起来像是一系列同心的半圆形,在腐蚀和摩擦的作用下,裂纹外侧变暗。
钢板弹簧失效分析
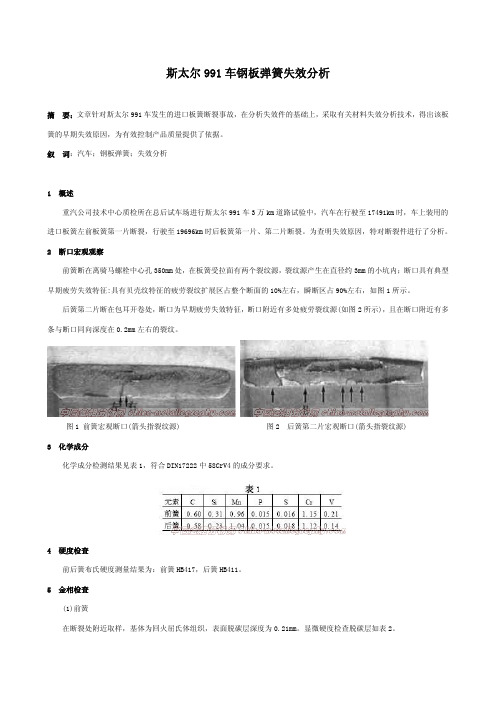
斯太尔991车钢板弹簧失效分析摘 要:文章针对斯太尔991车发生的进口板簧断裂事故,在分析失效件的基础上,采取有关材料失效分析技术,得出该板簧的早期失效原因,为有效控制产品质量提供了依据。
叙 词:汽车;钢板弹簧;失效分析1 概述重汽公司技术中心质检所在总后试车场进行斯太尔991车3万km道路试验中,汽车在行驶至17491km时,车上装用的进口板簧左前板簧第一片断裂,行驶至19696km时后板簧第一片、第二片断裂。
为查明失效原因,特对断裂件进行了分析。
2 断口宏观观察前簧断在离骑马螺栓中心孔350mm处,在板簧受拉面有两个裂纹源,裂纹源产生在直径约3mm的小坑内;断口具有典型早期疲劳失效特征:具有贝壳纹特征的疲劳裂纹扩展区占整个断面的10%左右,瞬断区占90%左右,如图1所示。
后簧第二片断在包耳开卷处,断口为早期疲劳失效特征,断口附近有多处疲劳裂纹源(如图2所示),且在断口附近有多条与断口同向深度在0.2mm左右的裂纹。
图1 前簧宏观断口(箭头指裂纹源) 图2 后簧第二片宏观断口(箭头指裂纹源)3 化学成分化学成分检测结果见表1,符合DIN17222中58CrV4的成分要求。
4 硬度检查前后簧布氏硬度测量结果为:前簧HB417,后簧HB411。
5 金相检查(1)前簧在断裂处附近取样,基体为回火屈氏体组织,表面脱碳层深度为0.21mm。
显微硬度检查脱碳层如表2。
在裂纹源小坑处取样,表层为白亮层,白亮层厚度约为0.2mm;对试样进一步腐蚀,经观察得知白亮层为马氏体组织,如图3所示;白亮层显微硬度HV0.2=743,心部基体显微硬度HV0.2=396。
图3 白亮层组织 400×(2)后簧在裂纹附近取样,心部为回火屈氏体组织,表面脱碳层为0.28mm。
显微硬度检验脱碳层,结果见表3。
6 电镜观察及能谱分析利用SEM535、EDAX进行断口及微区成分分析,得知前簧裂纹源有两处存在许多附着物,裂纹源形貌如图4所示;用能谱仪进行定量分析,确定附着物的主要成份为锌元素,裂纹源小坑内有金属熔化流动结晶现象,附近存在很多小裂纹。
变截面钢板弹簧在行驶过程中驾驶员一侧断裂的原因

变截面钢板弹簧在行驶过程中驾驶员一侧断裂的原因哎呀,今天我们聊聊变截面钢板弹簧,听起来挺专业对吧?可别小看它,虽然名字有点拗口,但它在我们的车里可是个重要角色。
这种弹簧的工作原理就像弹弓,能把压力转化为力量,让车在路上舒舒服服地行驶。
不过,驾驶员一侧的断裂,那可是让人心头一紧的事儿。
咱们就来深入探讨一下,为什么会出现这样的情况。
变截面钢板弹簧的设计理念其实是为了适应不同的载荷。
就像咱们买衣服要看尺寸一样,弹簧也得根据车的不同使用情况调整。
不过,有时候这家伙可就“调皮”了,尤其是在行驶过程中。
如果车子长时间在不平坦的路面上颠簸,弹簧就像个被惹怒的孩子,发起脾气来可真是不得了。
再加上,如果载重过大,弹簧承受的压力就像压在肩上的大山,迟早会出现疲劳,最后就可能导致断裂。
再说说这个疲劳嘛,弹簧在承受不断的压力时,就会像人一样累。
反复的压缩和放松,慢慢就磨损了。
想象一下,如果你天天熬夜,哪天总会有崩溃的一刻。
路上那些坑坑洼洼的地方,简直就是给弹簧加码考验。
每次经过时,弹簧都像在过山车,心里不停叫着:“我受不了了!”久而久之,金属的疲劳就会慢慢显现,最后啪的一声,断了。
别忘了焊接和材料的问题。
好的材料可以让弹簧经得起折腾,反之就像拿个塑料袋来过日子,脆弱得很。
制造过程中如果焊接不当,或者材料本身就有缺陷,都是埋下了隐患的“定时炸弹”。
就好比有的人明明是“好料”,结果却因为出身不好,反而给自己惹来麻烦。
开车时如果发现驾驶员一侧的弹簧“惨了”,那可真是晴天霹雳,心里就想着:“这下可完蛋了!”话说回来,驾驶员这一侧断裂影响的可不仅仅是弹簧本身,整个车辆的稳定性和安全性也会受到影响。
你想想,突然失去了一侧的支撑,车子就像个没头苍蝇,左右摇摆,开起来像坐过山车一样,绝对让人心惊肉跳。
再加上,影响刹车的效率,简直让人提心吊胆,生怕下一秒就翻了车。
修复这样的问题可不便宜,没个几千块,心里都觉得难受。
那到底我们应该如何避免这种尴尬情况呢?定期检查车子的悬挂系统,确保弹簧没问题。
- 1、下载文档前请自行甄别文档内容的完整性,平台不提供额外的编辑、内容补充、找答案等附加服务。
- 2、"仅部分预览"的文档,不可在线预览部分如存在完整性等问题,可反馈申请退款(可完整预览的文档不适用该条件!)。
- 3、如文档侵犯您的权益,请联系客服反馈,我们会尽快为您处理(人工客服工作时间:9:00-18:30)。
重卡钢板弹簧断裂失效分析
白培谦 泮战侠 慕松 赵鹏英 杜飞
(陕西汽车集团有限责任公司质量管理部,陕西西安,710200)
摘 要:通过宏观检查、化学成分分析、硬度测试以及微观组织检查等结果分析,确定了重型卡车用钢板弹簧断裂原因。
分析结果表明:因超载使钢板弹簧出现过度反弓,造成板簧卡中的螺栓与钢板弹簧动态接触,发生磨损腐蚀现象,在过大的交变应力下出现疲劳断裂。
并提出了防止其发生断裂事故的预防措施。
关键词:钢板弹簧;磨损腐蚀;交变应力;疲劳断裂
Fracture Failure Analysis of Heavy Truck Leaf Spring
Bai Pei-qian, PAN Zhan-xia, Mu Song, Zhao Peng-ying, Du Fei,
(1.Shaanxi Automobile Group Co., Ltd. Quality Management Department, Xi ’an 710200, China ) Abstract:The fracture cause of heavy truck leafspring is researched by macrography, chemical composition analysis, hardness test and microstructure test. The research shows that leaf spring excessive inverse arch-shaped for overload causes Frictional Contact between plate spring bolt and leaf spring and erosion corrosion and the leaf spring is broken for fatigue fracture Under alternating stress. In the paper the measures of preventing leaf spring fracture accident is put forward.
Key words: leaf spring; erosion corrosion; alternating stress; fatigue fracture.
钢板弹簧是汽车悬架中重要的弹性元件,主要影响汽车行驶的平顺性和操纵的稳定性,在车辆行驶过程中起到缓冲减振的作用。
同批次某矿山用短途重载卡车行驶约六千公里后发生四起钢板弹簧断裂事故。
断裂钢板弹簧材料为50CrV A ,其生产工艺为:下料→钻孔→卷耳→淬火→回火→喷丸→装配→预压→喷漆。
为了查明钢板弹簧断裂原因,对断裂失效件进行检查分析。
1 检查与结果
1.1 宏观检查
断裂发生在前钢板弹簧组第一片后侧板簧卡附近,见图1(a )箭头所示位置,距吊耳孔中心约26cm 处,断口侧表面可见明显磨损腐蚀痕迹,见图1(b )所示。
在体视显微镜下观察钢板弹簧侧表面磨损腐蚀区域发现:断口侧表面磨损腐蚀区域呈现红褐色,仔细观察存在大量裂纹,且出现腐蚀坑,见图2。
(a ) (b)
图1 断裂位置及外观
Fig.1 the fracture position and appearance
收稿日期:
图2 磨损腐蚀区域
Fig.2 The region of the erosion corrosion
观察断裂钢板弹簧断口形貌可知:断面基本垂直于板簧纵向,有剪切唇,断口上可见多处裂纹源均位于板簧受拉应力一侧,裂纹扩展区有明显的弧线状贝壳纹,具有典型的疲劳断口特征。
疲劳扩展区面积较小,约占断口面积的1/10,瞬断区面积较大,表明该板簧服役时承受了较大的载荷,见图3。
图3 断口宏观形貌
Fig.3 the fracture macroscopic feature
1.2 断口微观检查
图4为钢板弹簧断口中裂纹源区在扫描电镜下的形貌,明显可见裂纹起源于磨损腐蚀部位的腐蚀坑处。
用能谱仪对腐蚀坑处的腐蚀产物进行分析,其分析结果见图5。
能谱分析结果表明:断裂钢板弹簧裂纹源区腐蚀产物主要为氧化物和氯化物。
图4 裂纹源处微观形貌
Fig.4 the micro-morphology on the crack source 作者简介:白培谦(1965-),男,正高级工程师。
图5 腐蚀层能谱分析图
Fig.5 the energy spectrum diagram of the corrosion layer
钢板弹簧断口中裂纹扩展区已被氧化腐蚀,在电镜下除观察到二次裂纹外,其余微观特征无法辨别,见图6。
瞬断区微观特征为解理+准解理+沿晶,见图7。
图6 裂纹扩展区微观形貌
Fig.6 the micro-morphology on the crack extension zone
图7 瞬断区微观形貌
Fig.7 the micro-morphology on the fast fracture area
1.3 硬度检查
在失效钢板弹簧断口附近取样,测量其基体平均硬度为420HBW,检测结果符合相关技术要求。
1.4 化学成分检查
在失效钢板弹簧上取样进行化学成分分析,结果符合GB/T1222-2007标准中50CrV A材
质要求,见表1。
表1 钢板弹簧的化学成分(%)
Tab.1 the chemical constituents of the leaf spring
项目 C S Si Mn P Cr V
实测值0.52 0.014 0.28 0.62 0.020 0.87 0.13
标准值0.46~0.54 ≤0.025 0.17~0.37 0.50~0.80 ≤0.025 0.80~1.10 0.10~0.20 1.5 金相检查
在板簧断裂处附近进行微观检查。
该处表面无脱碳现象,见图8,基体组织为较粗的回火屈氏体,4级,见图9,检测结果符合相关技术要求。
图8 表面组织200X 图9 基体组织500X Fig.8 the surface microstructure 200 X Fig.9 the matrix structure 500X
2 分析讨论
理化检测结果表明断裂钢板弹簧材质、硬度、基体组织均符合相关技术要求。
断口宏观和微观检查结果表明断裂钢板弹簧失效形式为磨损腐蚀引起的多源疲劳断裂,其疲劳断裂的过程是微动磨损、氧化及腐蚀、交变应力等综合作用的过程。
产生这种失效模式的原因是:车辆在服役过程中因超载产生过大的弯曲应力,钢板弹簧出现过度反弓现象,造成板簧卡螺栓杆与钢板弹簧组第一片簧发生摩擦接触,第一片钢板弹簧油漆涂层脱落后,其面上裸露出的金属与空气接触发生氧化反应,形成氧化铁等反应产物,该氧化产物强度低在螺栓杆与第一片钢板弹簧继续摩擦时会从表面剥离下来或破碎,钢板弹簧表面形成凹坑,出现应力集中点。
钢板弹簧在汽车行驶时受交变应力的作用,在交变载荷作用下,磨损区域应力集中点易出现疲劳微裂纹,在交变应力作用下微裂纹不断扩展,某些裂纹在扩展中合并为一主裂纹;同时,磨损过程中形成的腐蚀物及腐蚀介质(空气、水等),也会逐渐渗入裂纹内部,像一个楔子一样嵌入微裂纹内部,使裂纹尖端的应力强度因子幅加大,并伴有化学作用,使裂纹进一步扩大,在裂纹稳定扩展区出现大量腐蚀坑,并使钢板弹簧疲劳寿命下降;最终导致钢板弹簧在过大应力下发生断裂。
为了防止出现此类钢板弹簧断裂事故,应在工作中避免出现过大的弯曲应力造成钢板弹簧反弓后与板簧卡中的螺栓杆接触摩擦。
在汽车行驶时应按设计重量进行承载,避免出现长期超载;同时在行驶中应避免频繁使用紧急制动,防止由于惯性力的作用,车辆的重心前移,使钢板弹簧受到过大的弯曲应力和拉应力。
3 结束语
通过对断裂钢板弹簧进行理化分析,确认了其断裂原因为超载使钢板弹簧出现过度反弓,造成板簧卡螺栓与钢板弹簧动态接触,发生磨损腐蚀现象,在过大的交变应力下出现疲劳断裂。
并在分析钢板弹簧断裂机理的基础上提出了防止其发生断裂事故的预防措施。
参考文献:
[1] 陈亚蓉,张静江,等.汽车钢板弹簧断裂失效分析[J].理化检验—物理分册,2000,36(1):31-33.
[2] 张栋,钟培道,等.失效分析[M].国防工业出版社,2008:241-249.
[3] 钟群鹏,赵子华.断口学[M].高等教育出版社,2006:270-290.。