锻造及锻后热处理工艺规范
锻造工艺过程及模具设计第3章锻造的加热

3.6.2 锻件的冷却规范
1.空冷 :在空气中冷却,速度较快 。
2.坑(箱)冷:锻件锻后放到地坑 或铁箱中封闭冷却,或埋入坑中砂 子、石灰或炉渣内冷却。
3.炉冷:锻件锻后直接装入炉中按 一定的冷却规范缓慢冷却。
3.7 中小钢锻件的热处理
3.7.1 退火 退火是将钢加热到一定的温度,保温
1)反应是可逆反应,向右:氧化反应,向左:
还原反应。 2)加热时,与空气消耗系数有关。
空气消耗系数:又称空气过剩系数,是燃料燃 烧实际供给的空气量与理论计算空气量之比。 3)空气充足时,炉气呈氧化性,空气不足时, 炉 气呈还原性。 4)控制反应前后的生成物与反应物的浓度比。
炉气和被加热钢材的平衡图如下:
• 电热体材料:铁铬铝合金 镍铬合金 碳化硅元件 二硅化钼
图3.1 电阻炉原理图 1-电热体 2-坯料 3-变压器
●盐浴炉加热原理: 电流通过炉内电极产生
的热量把导电介质——盐熔 融,通过高温介质的对流与 传导将埋入介质中的金属加 热。 ●盐浴炉的分类:按照热源的 位置分外热式和内热式。 ●盐浴炉加热的优点:
、
辐射加热坯料。
燃料来源方便、加热炉修造容易、
加热费低、适应性强。
缺点::劳动条件差,加热速度慢, 质量低、热效率低。
应用范围:大、中、小型坯料。
2 电加热 利用电能转换热能来加热坯料。
1)电阻加热 电阻加热与火焰加热原理相同,根据
发热元件的不同分为: 电阻炉加热、 盐浴炉加热、接触电
加热
• 电阻炉加热原理:利用电 流通过炉内的电热体产生 的能量,加热炉内的金属 坯料。原理如图3.1。
升温快、加热均匀,可 以实现 金属坯料整体或局 部的无氧化加热。 ●盐浴炉加热的缺点:
锻造加热规范

1 范围本规范规定了本厂生产、供本厂锻造用的电炉锭、电渣锭与钢坯炉窑加热工艺的编制要素、导则和方法。
本规范适用于冷热钢锭于钢坯。
2 引用标准下列标准所包含的条文,通过本标准中引用而构成本标准的条文。
本标准出版时所示版本均为有效。
所有标准都会被修订,使用本标准的各方应探讨使用下列标准最新版本的可能性。
DYⅡ-39-93 热送钢锭冷处理工艺守则DYⅡ-3-39 水压机自由锻锻后冷却及锻后热处理工艺守则QGSHYZ 22-93 热加工工艺文件制定规程3 名词说明和定义钢锭和钢坯钢锭锭身锻比<的成钢锭,锭身锻比≥的称钢坯。
(简称“锭”、“坯”)冷、热锭(坯)装炉时锭{坯}表面温度<400℃(且内部温度肯定低于表面温度)的称冷锭(坯),表面温度≥400℃(且内部温度肯定高于表面温度)的称热锭(坯)。
表面温度以钢锭冒口端进锭身200mm凹(圆)面处、坯料离端口200mm平面处的实际温度为准。
锻造温度保温时间指炉温(一般指炉窑顶部电偶所测温度)进入工艺规定温度公差范围、开始保持此温度,使钢锭(坯)变形区与此温度趋于基本一致所需时间。
最少保温时间指钢锭(坯)在进行表面区域变形或精锻(如倒棱、滚圆、校直、整型等)前加热到锻造温度时开始保温所需的最少时间。
普通保温时间指钢锭(坯)在进行常规锻造或粗锻(如拔长、冲孔、平整、剥边、扭曲、错移、弯曲等等)前加热到锻造温度时开始保温所需时间。
但镦粗须在此保温时间基础上延长20%。
4 要素确认按本规范编审有关钢锭(坯)的加热工艺前,一般应确定下列基本要素锻造工艺和产品技术质量要求;钢锭(坯)的规格、质量、形状、及其相关现状;加热炉规格及其工作可靠性;装炉单、装炉方式和合炉要求;有关作业方法及其有效性;测温形式及显示的正确,及时,统一性;工装,附件的匹配;作业环境适应性。
5 钢锭(坯)加热曲线和应用导则钢锭(坯)锻造温度范围分三类控制,见表3。
冷锭(坯)加热见表4、表5。
锻造及锻后热处理工艺规范

目录1.钢质自由锻件加热工艺规范2.钢锭(坯)加热规范若干概念3.加热操作守则4.锻造操作守则5.锻件锻后冷却规范6.锻件锻后炉冷工艺曲线7.锻件锻后热装炉工艺曲线8.冷锻件校直前加热、校直后(补焊后)回火工艺曲线9.锻件各钢种正火(或退火)及高温回火温度表10.锻件有效截面计算方法钢质自由锻件加热工艺规范一.范围:本规范规定了钢质自由锻件的通用加热技术条件。
本规范适用于碳素钢、合金钢、高合金钢、高温合金钢(铁基、镍基)的冷、热、半热钢锭(坯)的锻造前加热二.常用钢号分组和始、终锻加热温度范围:注1:始锻温度为锻前加热允许最高炉温,由于钢锭的铸态初生晶粒加热时过热倾向比同钢号钢坯小,故两者的锻前加热温度相差20℃~30℃;注2:根据产品的特性、锻件技术条件、变形量等因素,始锻温度可以适当调整;注3:本规范未列入的钢种,可按化学成分相近的钢号确定;注4:重要的、关键产品的、特殊材质的钢号,其加热工艺曲线由技术部编制;注5:几种不同的钢种,不同尺寸的钢锭(或坯料),在同一加热炉加热时,要以合金成分高的,尺寸大的钢锭(或坯料)为依据编制加热工艺曲线。
三.冷钢坯。
钢锭加热规范:钢锭(坯)加热规范若干概念1.钢锭(坯)入炉前的表面温度≥550℃的称为热钢锭,400~550℃的称为半热钢锭(坯),≤400℃的称为冷钢锭。
2.锻件半成品坯料的加热平均直径计算原则:δ -壁厚H- 高度或长度D- 外径1)实心圆类:当D>H时,按H计算;当D<H时,按D计算。
2)筒类锻坯:H>D 当H>δ时,按1.3δ计算。
3)空心盘(环)类:H<D当H>δ时,按δ计算;当H<δ时,按H计算。
3.为了避免锻件粗晶组织,最后一火的始锻温度可按其剩余锻造比(Y)确定:Y=1.3~1.6 最高加热温度1050℃Y<1.3 最高加热温度950℃4.不同钢种不同规格的坯料同炉加热时,装炉温度和升温速度均按较低的选用,保温时间按较长的选用。
锻造及锻后热处理工艺规范
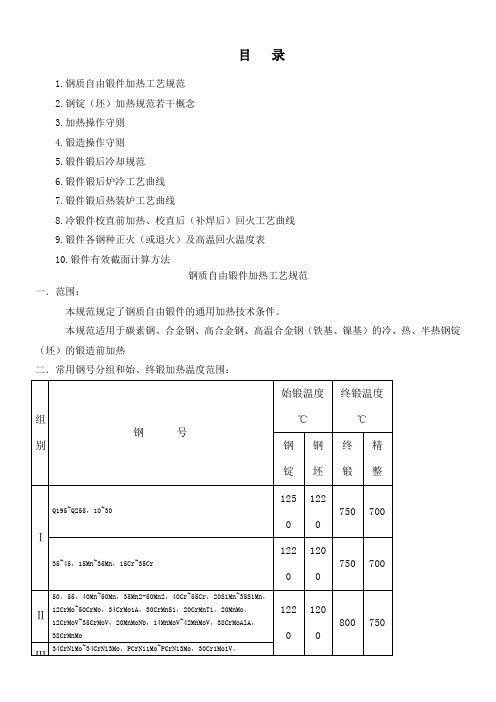
目录1.钢质自由锻件加热工艺规范2.钢锭(坯)加热规范若干概念3.加热操作守则4.锻造操作守则5.锻件锻后冷却规范6.锻件锻后炉冷工艺曲线7.锻件锻后热装炉工艺曲线8.冷锻件校直前加热、校直后(补焊后)回火工艺曲线9.锻件各钢种正火(或退火)及高温回火温度表10.锻件有效截面计算方法钢质自由锻件加热工艺规范一.范围:本规范规定了钢质自由锻件的通用加热技术条件。
本规范适用于碳素钢、合金钢、高合金钢、高温合金钢(铁基、镍基)的冷、热、半热钢锭(坯)的锻造前加热二.常用钢号分组和始、终锻加热温度范围:注1:始锻温度为锻前加热允许最高炉温,由于钢锭的铸态初生晶粒加热时过热倾向比同钢号钢坯小,故两者的锻前加热温度相差20℃~30℃;注2:根据产品的特性、锻件技术条件、变形量等因素,始锻温度可以适当调整;注3:本规范未列入的钢种,可按化学成分相近的钢号确定;注4:重要的、关键产品的、特殊材质的钢号,其加热工艺曲线由技术部编制;注5:几种不同的钢种,不同尺寸的钢锭(或坯料),在同一加热炉加热时,要以合金成分高的,尺寸大的钢锭(或坯料)为依据编制加热工艺曲线。
三.冷钢坯。
钢锭加热规范:钢锭(坯)加热规范若干概念1.钢锭(坯)入炉前的表面温度≥550℃的称为热钢锭,400~550℃的称为半热钢锭(坯),≤400℃的称为冷钢锭。
2.锻件半成品坯料的加热平均直径计算原则:δ -壁厚 H- 高度或长度 D- 外径1)实心圆类:当D>H时,按H计算;当D<H时,按D计算。
2)筒类锻坯:H>D 当H>δ时,按1.3δ计算。
3)空心盘(环)类:H<D当H>δ时,按δ计算;当H<δ时,按H计算。
3.为了避免锻件粗晶组织,最后一火的始锻温度可按其剩余锻造比(Y)确定:Y=1.3~1.6 最高加热温度1050℃Y<1.3 最高加热温度950℃4.不同钢种不同规格的坯料同炉加热时,装炉温度和升温速度均按较低的选用,保温时间按较长的选用。
热处理工艺规范

ZX/JS-007江苏新中信电器设备有限公司热处理工艺规范编制:审批:二零一三年三月江苏新中信电器设备有限公司热处理工艺规范ZX/JS-0071 目的对零部件消除应力,改善材料或零件机械性能的热处理质量实施控制,以保证热处理符合技术条件的要求。
2适用范围本规范适用于本厂钢制零件在周期作业加热炉中的调质、固熔工序。
3准备工作3.1检查设备及仪表是否正常。
3.2检查零件上的材料是否符合图样要求。
3.3检查零件的尺寸是否符合图样及工艺文件的规定。
3.3.1调质件最好先经粗加工,断面大于100mm的零件,当有内孔时,应钻孔后再调质,并且防止出现尖角。
3.3.2调质件的加工余量应大于允许的变形量。
3.3.3不同淬火温度的调质件,不得同炉处理,同炉处理件的有效厚度应相近。
4 工艺规范4.1 技术部根据标准、工艺规程、材料和设计技术条件,负责编制热处理工艺规程。
4.2 热处理工艺规程至少应包括以下内容:a)热处理工件的材料牌号b)热处理设备及热处理种类(调质、固溶等)c)热处理工艺参数(升温、保温、出炉温度、回火温度及各温度段的加热时间等)和工艺曲线图。
d)冷却方法及冷却介质。
4.3 消除应力热处理后一般不得再进行焊接补焊。
否则应重新进行热处理。
4.4 ASTM A276 410或420调质处理(详见附录1)规范见表1。
表14.4.1机械性能参数:≥550MPa 。
Rm ≥690MPa ; Rp0.24.5 ASTM A276 410或420淬火处理(详见附录2)规范见表2。
表24.6 ASTM A182 F304、F316、F321钢固溶处理(详见附录3)规范见表3。
表34.6.2 机械性能参数:≥205MPa A%≥30 Z b%≥50 Rm≥515Mpa Rp0.24.7 淬火冷却方法4.7.1调质件采用的淬火介质一般为水或油。
4.7.2形状简单、断面厚度不足100mm的零件在水或油中冷却,终冷温度不予限制,以淬硬为原则。
锻造工艺规范
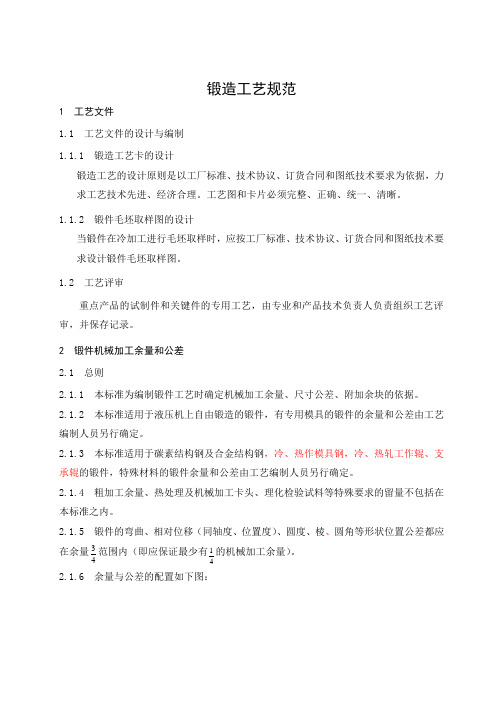
锻造工艺规范1 工艺文件1.1 工艺文件的设计与编制 1.1.1 锻造工艺卡的设计锻造工艺的设计原则是以工厂标准、技术协议、订货合同和图纸技术要求为依据,力求工艺技术先进、经济合理。
工艺图和卡片必须完整、正确、统一、清晰。
1.1.2 锻件毛坯取样图的设计当锻件在冷加工进行毛坯取样时,应按工厂标准、技术协议、订货合同和图纸技术要求设计锻件毛坯取样图。
1.2 工艺评审重点产品的试制件和关键件的专用工艺,由专业和产品技术负责人负责组织工艺评审,并保存记录。
2 锻件机械加工余量和公差 2.1 总则2.1.1 本标准为编制锻件工艺时确定机械加工余量、尺寸公差、附加余块的依据。
2.1.2 本标准适用于液压机上自由锻造的锻件,有专用模具的锻件的余量和公差由工艺编制人员另行确定。
2.1.3 本标准适用于碳素结构钢及合金结构钢,冷、热作模具钢,冷、热轧工作辊、支承辊的锻件,特殊材料的锻件余量和公差由工艺编制人员另行确定。
2.1.4 粗加工余量、热处理及机械加工卡头、理化检验试料等特殊要求的留量不包括在本标准之内。
2.1.5 锻件的弯曲、相对位移(同轴度、位置度)、圆度、棱、圆角等形状位置公差都应在余量43范围内(即应保证最少有41的机械加工余量)。
2.1.6 余量与公差的配置如下图:D :零件尺寸 C :锻件公称尺寸(基本尺寸) C ′:锻件最大尺寸 C ″:锻件最小尺寸 а:锻件名义机械加工余量δ′:下偏差(负公差) δ″:上偏差(正公差)2.1.7 本规范未包括的特殊形状的锻件及尺寸超出本规范的锻件,其余量和公差由工艺编制人员参照本规范确定。
2.1.8 在确定锻件余量时,必须兼顾零件的局部尺寸与整体尺寸的关系,局部应照顾整体,以减少加工余量。
2.1.9 易焊钢种和留有粗加工余量在粗加工后允许存在可以加工掉的局部黑皮的锻件,其锻造余量应比本标准表中规定值减少10~20%(按复杂程度)。
对易产生裂纹又不易焊补钢种(如9Cr2Mo 、32Cr2MnMo 、60CrMnMo )等锻件的余量不应比表中规定值减少。
轴的锻造工序及热处理工艺

轴的锻造工序及热处理工艺轴是一种常见的机械传动部件,用于传递转矩和转速。
轴的锻造工序和热处理工艺关系到轴的强度、韧性、耐疲劳性和寿命。
本文将分别介绍轴的锻造工序和热处理工艺。
一、轴的锻造工序1.坯料加热轴的锻造前需要将坯料加热到一定的温度,通常为1100-1250℃。
在这个温度下,坯料的塑性最好,有利于锻造加工。
2.气锤或液压机锻造轴的锻造可以采用气锤或液压机进行,气锤锻造速度较快,比较适合大批量生产;液压机锻造速度较慢,但可以实现更好的均匀性和精度。
3.摆锤或旋转锻造摆锤或旋转锻造可以让轴在不同的方向进行锻造,从而实现更好的均匀性和强度。
这种工艺比较适用于大型和复杂的轴。
4.辗轧和拉伸辗轧和拉伸是对轴进行细化处理和加强强度的工艺。
辗轧可以将轴的截面尺寸减小,从而加强轴的强度;拉伸可以拉伸轴的分子结构,使其拥有更好的韧性和耐疲劳性。
5.修磨和清洗锻造完成后,轴需要进行修磨和清洗工序,将表面的毛刺和氧化物去掉,从而保证轴的表面平滑度和防止氧化腐蚀。
1.淬火淬火是一种常见的热处理工艺。
将轴加热至一定温度,然后迅速冷却至室温,可以让轴的强度和硬度得到提高。
不过这种工艺也容易导致轴的脆性增加,需要注意控制淬火温度、淬火介质和淬火时间。
2.回火回火是一种常用的强化处理工艺。
将轴加热到一定温度,然后冷却至室温,从而提高轴的强度和韧性,并降低轴的脆性。
回火可以根据不同的需求进行一次或多次处理。
3.热处理和表面处理热处理和表面处理是根据轴的使用条件和要求进行的定制化处理。
这种工艺包括热处理、渗碳、质量热处理、表面喷涂等,可以大大提高轴的使用性能和寿命。
4.磨削和平衡磨削和平衡是对轴进行后续加工和加工后的表面整理处理。
这种工艺可以提高轴的精度和平衡性,减少轴在使用过程中的振动和噪音,从而延长轴的使用寿命。
总结:对于轴的制造,锻造工序和热处理工艺的质量关系到轴的性能和使用寿命。
制造工艺的优化和控制,可以提高轴的品质和可靠性。
hzr702锻件热处理工艺标准
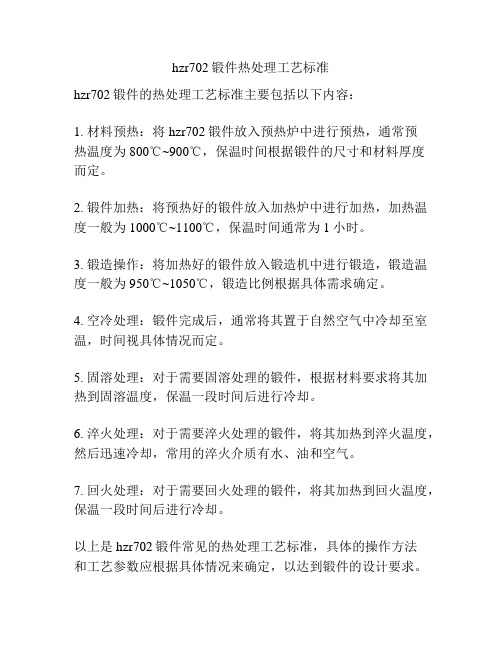
hzr702锻件热处理工艺标准
hzr702锻件的热处理工艺标准主要包括以下内容:
1. 材料预热:将hzr702锻件放入预热炉中进行预热,通常预
热温度为800℃~900℃,保温时间根据锻件的尺寸和材料厚度
而定。
2. 锻件加热:将预热好的锻件放入加热炉中进行加热,加热温度一般为1000℃~1100℃,保温时间通常为1小时。
3. 锻造操作:将加热好的锻件放入锻造机中进行锻造,锻造温度一般为950℃~1050℃,锻造比例根据具体需求确定。
4. 空冷处理:锻件完成后,通常将其置于自然空气中冷却至室温,时间视具体情况而定。
5. 固溶处理:对于需要固溶处理的锻件,根据材料要求将其加热到固溶温度,保温一段时间后进行冷却。
6. 淬火处理:对于需要淬火处理的锻件,将其加热到淬火温度,然后迅速冷却,常用的淬火介质有水、油和空气。
7. 回火处理:对于需要回火处理的锻件,将其加热到回火温度,保温一段时间后进行冷却。
以上是hzr702锻件常见的热处理工艺标准,具体的操作方法
和工艺参数应根据具体情况来确定,以达到锻件的设计要求。
- 1、下载文档前请自行甄别文档内容的完整性,平台不提供额外的编辑、内容补充、找答案等附加服务。
- 2、"仅部分预览"的文档,不可在线预览部分如存在完整性等问题,可反馈申请退款(可完整预览的文档不适用该条件!)。
- 3、如文档侵犯您的权益,请联系客服反馈,我们会尽快为您处理(人工客服工作时间:9:00-18:30)。
目录
1.钢质自由锻件加热工艺规范
2.钢锭(坯)加热规范若干概念
3.加热操作守则
4.锻造操作守则
5.锻件锻后冷却规范
6.锻件锻后炉冷工艺曲线
7.锻件锻后热装炉工艺曲线
8.冷锻件校直前加热、校直后(补焊后)回火工艺曲线
9.锻件各钢种正火(或退火)及高温回火温度表
10.锻件有效截面计算方法
钢质自由锻件加热工艺规范
一.范围:
本规范规定了钢质自由锻件的通用加热技术条件。
本规范适用于碳素钢、合金钢、高合金钢、高温合金钢(铁基、镍基)的冷、热、半热钢锭(坯)的锻造前加热
二.常用钢号分组和始、终锻加热温度范围:
注1:始锻温度为锻前加热允许最高炉温,由于钢锭的铸态初生晶粒加热时过热倾向比同钢号钢坯小,故两者的锻前加热温度相差20℃~30℃;
注2:根据产品的特性、锻件技术条件、变形量等因素,始锻温度可以适当调整;注3:本规范未列入的钢种,可按化学成分相近的钢号确定;
注4:重要的、关键产品的、特殊材质的钢号,其加热工艺曲线由技术部编制;注5:几种不同的钢种,不同尺寸的钢锭(或坯料),在同一加热炉加热时,要以合金成分高的,尺寸大的钢锭(或坯料)为依据编制加热工艺曲线。
三.冷钢坯。
钢锭加热规范:
精品
精品
精品
精品
钢锭(坯)加热规范若干概念
1.钢锭(坯)入炉前的表面温度≥550℃的称为热钢锭,400~550℃的称为半热钢锭(坯),≤400℃的称为冷钢锭。
2.锻件半成品坯料的加热平均直径计算原则:
δ -壁厚 H- 高度或长度 D- 外径
1)实心圆类:当D>H时,按H计算;当D<H时,按D计算。
2)筒类锻坯:H>D 当H>δ时,按1.3δ计算。
3)空心盘(环)类:H<D当H>δ时,按δ计算;当H<δ时,按H计算。
3.为了避免锻件粗晶组织,最后一火的始锻温度可按其剩余锻造比(Y)确定:
Y=1.3~1.6 最高加热温度1050℃
Y<1.3 最高加热温度950℃
4.不同钢种不同规格的坯料同炉加热时,装炉温度和升温速度均按较低的选用,保温时间按较长的选用。
对要求加热温度低或保温时间短的坯料,可先出炉锻造。
注:Y--锻造比
加热操作守则
1.钢锭(坯)装炉前,加热工应校对其冶炼炉号及锭件号,钢锭(坯)重量,尺寸以及钢锭(坯)的状态,并检查其表面质量,清除表面缺陷,不合格严禁装炉。
2.重要的、关键产品的特殊材质的钢号,在进炉前由技术部向操作工进行技术交底。
3.根据装炉实际情况,画好装炉图,记录装炉位置,做好实际操作记录,钢锭(坯)出炉顺序,及返回炉内锻坯位置要记录正确。
4.钢锭(坯)加热过程中必须精心操作,严格控制装炉温度、升温或冷却速度,炉气应保持微正压,炉床上的氧化皮应定期清理。
5.钢锭(坯)完成了加热保温时间之后因故不能出炉锻造时,可将炉温降至900~1050℃保温,若等到可出炉锻造时,则需将钢锭(坯)再加热至锻造温度下保温一段时间后方可出炉锻造。
6.钢锭(坯)经炉内长时间保温之后因故不需再加热时,必须随炉以≤80℃/h的降温速度将钢锭冷至250℃以下方可出炉。
7.加热炉喷嘴要避免火焰直接喷射在钢锭(坯)的表面上,经常检查热电偶、热工仪表,使其正常运行,并维护和保养加热炉设备。
锻造操作守则
1.锻造前应熟悉锻造工艺卡的内容,重要、关键锻件,技术部门需要进行技术交底。
2.锻造生产是集体操作,一定要开好班前会,了解加热情况,做好设备、工具准备工作,做到分工明确,指挥者应对生产的质量和安全负责。
3.在生产中应做到“三勤”:勤量、勤卡、勤查;“四准”:标尺要定准、样棒要划准、卡钳要量准、尺寸要记准。
4.生产时必须按照工艺卡进行锻造,不得任意改动,如工艺卡不合理或因特殊情况不能按照工艺卡执行,应及时向技术部反映,及时解决。
5.锻造指挥者必须认真执行确保锻造工艺卡上各项工艺参数到位、锻造尺寸到位,确保锻件的锻造比(镦粗比、拔长比),重要关键锻件做好生产过程的记录。
6.严格控制终锻温度,特别是关键、重要锻件、高合金钢、高温合金钢。
7.锻件完工后,锻件必须在相当于钢锭的底部端打上钢印(钢号、冶炼炉号和锻件号),钢印必须正确、清楚。
8.料头应用油漆写明分类标记,以便回收回炉。
9.对于关键、重要锻件,或试制新产品钢种的锻件,有关技术人员必须跟班在现场,及时处理可能遇到的问题。
锻件锻后冷却规范
说明:
1.锻件锻后冷却必须按规范执行。
若有特殊情况不能按规范执行须由技术部同意,并有书面意见。
2.沙冷锻件,必须将沙子全部覆盖在锻件上,而不是将锻件置于沙坑中。
3.锻件炉冷要根据不同钢种炉冷曲线工艺规范执行。
4.锻件热装炉是按锻件锻后热处理曲线工艺规范执行(锻件锻后正火、回火或退火)。
5.钢锭或钢坯冶炼工艺是采用EF+LF+VD或VODC方法。
锻件锻后冷却规范按截面尺寸向下调低一档。
锻件锻后炉冷工艺曲线
一.一般锻件锻后炉冷工艺曲线Ⅰ:
按锻件锻后冷却规范的炉冷钢号确定保温时间(Ⅰ):
1.Ⅱ类钢号炉冷保温时间按有效截面尺寸计算:1.5~2h/100mm;
2.Ⅲ类钢号炉冷保温时间按有效截面尺寸计算:2.5~3h/100mm;
3.Ⅳ类钢号炉冷保温时间按有效截面尺寸计算:4~5h/100mm。
二.重要锻件、有特殊要求的锻件锻后炉冷工艺曲线Ⅱ:
按锻件锻后冷却规范的炉冷钢号确定保温时间:
1.630~660℃保温时间(Ⅲ)均按炉冷工艺曲线Ⅰ执行;
2.630~660℃保温时间(Ⅰ)均按保温时间2h计算;
3.280~320℃过冷保温时间(Ⅱ)按630~660℃保温时间(Ⅲ)的1/2计算。
锻件锻后热装炉热处理工艺曲线
一.一般锻件锻后热装炉——正火+回火热处理工艺曲线:
1.锻件锻后热装炉进行正火+回火处理的正火温度、高温回火温度查表确定;
2.640~660℃保温时间(Ⅰ)按2-3h 保温时间计算;
3.正火温度保温时间(Ⅱ)按有效截面尺寸计算:1~1.5h/100mm ;
4.350~400℃过冷保温时间(Ⅲ)按有效截面尺寸计算:0.5~1h/100mm ;
5.高温回火保温时间(Ⅳ)按有效截面尺寸: Ⅱ类钢号高温回火保温时间1.5~2h/100mm, Ⅲ类钢号高温回火保温时间2.5~3.5h/100mm , Ⅳ类钢号高温回火保温时间4~5h/100mm 。
二.滚珠轴承钢、冷轧辊钢锻后热装炉球化退火工艺曲线:
1.630~650℃保温时间(Ⅰ)按3-4h 保温时间计算;
450~550 640~660
正火温度
均 热
均 热
空冷
冷却
保 温 (Ⅰ) 保 温 (Ⅱ)
保 温 (Ⅳ)
待 料
≤80℃
~60
℃/h
80℃ ~60 ℃/h
350~400
保 温 (Ⅲ)
高温回火温度
60℃ ~40
℃/h
炉冷
400
40 ~20℃/h
250~150出炉
℃
t(h)
450~550 630~650
780~800
均
热 均 热
炉冷
保 温 (Ⅰ)
保 温 (Ⅱ)
保 温 (Ⅲ)
待 料
≤80
~60 ℃/h
≤80℃ ~60℃/h
400~450
700~720(滚珠钢)
650~670(冷轧辊钢)
40~20℃/h
400
≤150℃出炉
℃
0 t(h)
200~150℃/h
2.780~800℃保温时间(Ⅱ)按有效截面尺寸计算:1.5h/mm;
3.700~720℃(650~670℃)保温时间(Ⅲ)按有效截面尺寸计算:2h/mm。
冷锻件校直前加热、校直(补焊)后回火工艺曲线
1.550~650℃保温时间(Ⅰ)按有效截面尺寸计算:1~1.5h/100mm;
2.550~650℃保温时间(Ⅱ)按有效截面尺寸计算:2~2.5h/100mm。
各钢种正火(或退火)及高温回火温度(℃)
.。