阴极铜生产工艺技术标准(自用)
(技术规范标准)阴极铜生产工艺技术标准(自用)
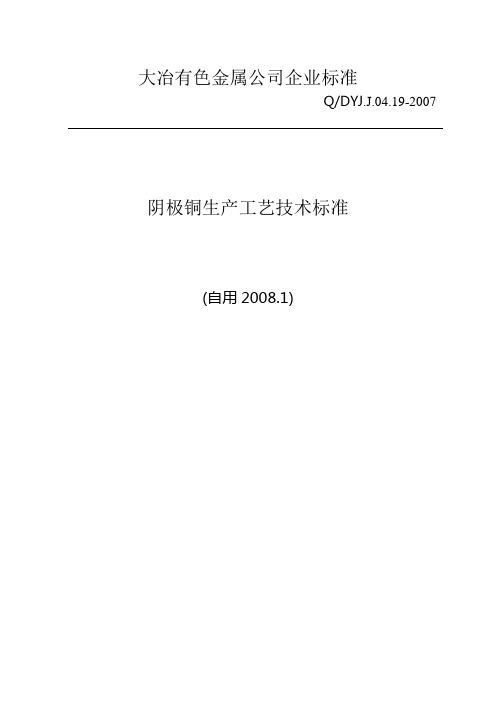
生产槽:Cu40~55H2SO4160~200Cl-0.01~0.09
As≤12 Sb≤1Bi≤0.5Ni≤15
种板槽:Cu38-55H2SO4160~200Cl-0.001~0.02
As≤12Sb≤1Ni≤12Bi≤0.35
平均槽电压:生产槽≤0.37V种板槽≤0.45V
电流密度230~300A/m2
2.4水
a)生活水:符合生活饮用水水质卫生规范(卫法监发[2001]161号)。
b)生产水:符合GB50050-95水质控制标准。
2.5 硫酸:工业纯,符合GB534规定,其中H2SO4≥98%
2.6盐酸:工业纯,符合GB320规定,其中HCl≥31%
2.7明胶:工业纯,其中H2O≤16%,粒度≥6mm
不定期
渣铜精矿
Cu、S、H20
1次/批
粗铜
Cu、Au、Ag、Ni、Se、Te、Bi、Sb、As、Pb、Zn、Fe
不定期
阳极铜
1次/炉
不定期
阴极铜
Se、Te、Bi、Cr、Mn、Sb、Cd、As、P、Pb、S、Sn、Ni、Fe、Si、Zn、Co、Ag、Cu
1批/系
中
间
物
料
转炉渣
Cu、SiO2、Fe
1次/炉
不定期
电解液
Cu、H2SO4、Cl-
1次/班
Pb、Zn、Ni、Bi、Fe、Cd、As、Sb
1次/周
硫酸铜
CuSO4·5H2O、游离酸、水不溶物
1次/批
粗硫酸镍
Ni
不定期
净化后液
Cu、Ni、As、Sb、Bi、H2SO4
1次/周
液空、液氧
乙炔
1次/小时
阴极铜生产工艺技术标准

阴极铜生产工艺技术标准引言阴极铜是一种重要的金属材料,在电子、通信、电力和建筑等领域有广泛的应用。
阴极铜的质量和性能直接影响到最终产品的质量。
因此,制定阴极铜生产工艺技术标准对于保证产品质量、提高生产效率具有重要意义。
本文档旨在提供阴极铜生产工艺技术标准的指导,包括原料准备、工艺流程、工艺参数等方面的要求。
1. 原料准备阴极铜生产过程中所使用的原料应符合以下要求:•铜源:使用高纯度电解铜作为铜源。
•补剂:根据工艺需要,选用适当补剂进行添加,如铁、镍、锡等。
2. 工艺流程阴极铜的生产工艺流程应包括以下几个主要步骤:2.1. 净化铜源使用电解铜作为主要原料时,应先进行铜源净化,以去除杂质和不纯物质。
具体净化步骤如下:1.采用酸洗方法,将铜源浸泡在稀盐酸中,去除铜表面的氧化皮和杂质。
2.用水冲洗铜源,去除酸洗残留物。
3.在碱性溶液中浸泡铜源,帮助去除冷冲孔和油脂等表面污染。
4.最后用纯水冲洗,确保铜源的纯净度。
2.2. 电解制备阴极铜电解制备阴极铜是主要的生产工艺步骤,具体流程如下:1.准备电解槽:选择合适的电解槽,并根据工艺要求调整槽液的组成和温度。
2.安装阳极和阴极:将净化后的铜源做为阴极,阳极使用铅。
3.填充电解槽:将电解槽填满电解液,液面应保持在适当位置。
4.启动电流:逐步增加电流强度,直到达到设定值。
5.电解反应:在设定电流和时间下,铜离子在电解中还原并沉积在阴极上,形成阴极铜。
6.分离阴极铜:根据生产需要,定期停止电解反应,将阴极铜从阴极上取下。
7.清洗和处理阴极铜:对取下的阴极铜进行清洗和处理,以去除表面污染,并得到纯净的阴极铜产品。
2.3. 后续处理根据生产需要,还可以对阴极铜进行进一步的处理,如除氧、除杂、静电除尘等,以提高产品质量。
3. 工艺参数要求阴极铜生产过程中的一些工艺参数需符合以下要求:1.电流密度:根据生产设备和工艺要求,设定适当的电流密度范围,以保证电解反应效果和阴极铜质量。
粗铜和阴极铜标准

粗铜和阴极铜标准粗铜标准本标准规定了粗铜的产品分类、技术要求、试验方法、检验规则及标志、包装、运输和贮存。
有色金属行业标准粗铜(YS/T 70—93)1 主题内容与适用范围本标准规定了粗铜的产品分类、技术要求、试验方法、检验规则及标志、包装、运输和贮存。
本标准适用于转炉及其他方法所生产的粗铜,供精炼用。
本标准的有关条款也适用于阳极铜。
2 引用标准GB 5120 粗铜化学分析方法3 产品分类粗铜按化学成分分为3个牌号:Cu99.30C、Cu99.00C、Cu97.50C。
4 技术要求4.1 化学成分4.1.1 粗铜的化学成分应符合下表的规定。
4.1.2 粗铜中金、银含量不作规定,但需按批进行分析,报出分析结果。
如有特殊情况,供需双方可协商解决。
4.2 表面质量4.2.1 粗铜锭的边缘及表面不得有易脱落的飞边、毛刺等。
4.2.2 表面和断面不得有炉渣和夹杂物。
4.2.3 浇铸面铜峰高度不大于100mm。
4.3 每个粗铜锭重量为500~800kg。
锭的长度不大于800mm,宽度不大于500mm。
如合同中注明时,也可供应其他规格的铜锭。
5 试验方法5.1 化学成分的仲裁分析方法按GB5120的规定进行。
5.2 表面质量用目视检查。
6 检验规则6.1 检查和验收6.1.1 粗铜应由供方技术监督部门进行检验,保证产品质量符合本标准的规定,并填写质量证明书。
6.1.2 需方对收到的产品及小样按本标准的规定进行检验。
如检验结果与所附的质量证明书不符时,应在收到小样之日起二个月内向供方提出,由供需双方协商解决。
如需仲裁,仲裁取样在需方由供需双方共同进行,样品交由双方共同认可的单位分析,以仲裁分析结果为准。
6.2 组批粗铜应成批提交检验,每批由同一炉次且形状大致相同的产品组成。
6.3 检验项目每批粗铜锭应进行化学成分及表面质量的检验。
6.4 化学成分仲裁取样、制样6.4.1 仲裁取样6.4.1.1 每批粗铜随机抽取粗铜锭,小于30t时,取样锭数不少于3锭;大于30t 时,取样锭数不小于5锭。
阴极铜的生产工艺流程
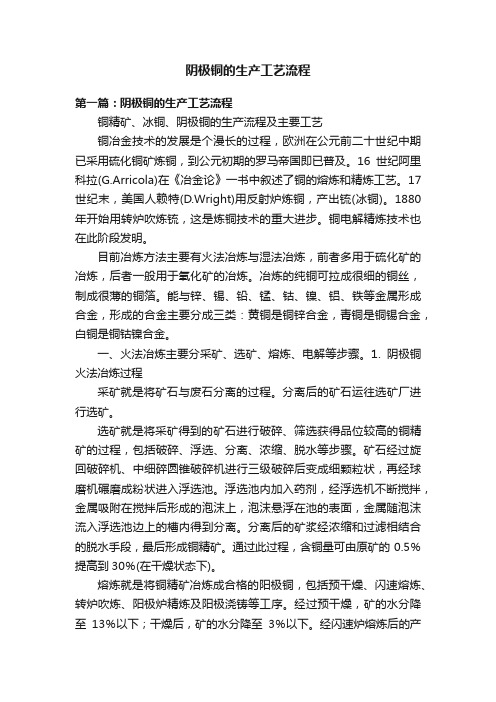
阴极铜的生产工艺流程第一篇:阴极铜的生产工艺流程铜精矿、冰铜、阴极铜的生产流程及主要工艺铜冶金技术的发展是个漫长的过程,欧洲在公元前二十世纪中期已采用硫化铜矿炼铜,到公元初期的罗马帝国即已普及。
16世纪阿里科拉(G.Arricola)在《冶金论》一书中叙述了铜的熔炼和精炼工艺。
17世纪末,美国人赖特(D.Wright)用反射炉炼铜,产出锍(冰铜)。
1880年开始用转炉吹炼锍,这是炼铜技术的重大进步。
铜电解精炼技术也在此阶段发明。
目前冶炼方法主要有火法冶炼与湿法冶炼,前者多用于硫化矿的冶炼,后者一般用于氧化矿的冶炼。
冶炼的纯铜可拉成很细的铜丝,制成很薄的铜箔。
能与锌、锡、铅、锰、钴、镍、铝、铁等金属形成合金,形成的合金主要分成三类:黄铜是铜锌合金,青铜是铜锡合金,白铜是铜钴镍合金。
一、火法冶炼主要分采矿、选矿、熔炼、电解等步骤。
⒈ 阴极铜火法冶炼过程采矿就是将矿石与废石分离的过程。
分离后的矿石运往选矿厂进行选矿。
选矿就是将采矿得到的矿石进行破碎、筛选获得品位较高的铜精矿的过程,包括破碎、浮选、分离、浓缩、脱水等步骤。
矿石经过旋回破碎机、中细碎圆锥破碎机进行三级破碎后变成细颗粒状,再经球磨机碾磨成粉状进入浮选池。
浮选池内加入药剂,经浮选机不断搅拌,金属吸附在搅拌后形成的泡沫上,泡沫悬浮在池的表面,金属随泡沫流入浮选池边上的槽内得到分离。
分离后的矿浆经浓缩和过滤相结合的脱水手段,最后形成铜精矿。
通过此过程,含铜量可由原矿的0.5%提高到30%(在干燥状态下)。
熔炼就是将铜精矿冶炼成合格的阳极铜,包括预干燥、闪速熔炼、转炉吹炼、阳极炉精炼及阳极浇铸等工序。
经过预干燥,矿的水分降至13%以下;干燥后,矿的水分降至3%以下。
经闪速炉熔炼后的产物称“冰铜”,液体状,铜含量50%--75%,与硫混合。
“冰铜”经转炉吹炼后的产物是“粗铜”,铜含量98.5%左右。
粗铜再经阳极炉精炼并经过圆盘浇铸机浇铸,即形成阳极铜。
阴极铜的生产工艺流程

阴极铜的生产工艺流程下载温馨提示:该文档是我店铺精心编制而成,希望大家下载以后,能够帮助大家解决实际的问题。
文档下载后可定制随意修改,请根据实际需要进行相应的调整和使用,谢谢!并且,本店铺为大家提供各种各样类型的实用资料,如教育随笔、日记赏析、句子摘抄、古诗大全、经典美文、话题作文、工作总结、词语解析、文案摘录、其他资料等等,如想了解不同资料格式和写法,敬请关注!Download tips: This document is carefully compiled by theeditor. I hope that after you download them,they can help yousolve practical problems. The document can be customized andmodified after downloading,please adjust and use it according toactual needs, thank you!In addition, our shop provides you with various types ofpractical materials,such as educational essays, diaryappreciation,sentence excerpts,ancient poems,classic articles,topic composition,work summary,word parsing,copy excerpts,other materials and so on,want to know different data formats andwriting methods,please pay attention!阴极铜的生产工艺流程一、原料准备阶段1. 选择铜矿石:首先需要选择高品质的铜矿石,确保原料的质量。
阴极铜

阴极铜阴极铜将粗铜(含铜99%)预先制成厚板作为阳极,纯铜制成薄片作阴极,以硫酸(H2 SO4)和硫酸铜(CuSO4)的混和液作为电解液。
通电后,铜从阳极溶解成铜离子(Cu)向阴极移动,到达阴极后获得电子而在阴极析出纯铜(亦称电解铜)。
粗铜中杂质如比铜活泼的铁和锌等会随铜一起溶解为离子(Zn和Fe)。
由于这些离子与铜离子相比不易析出,所以电解时只要适当调节电位差即可避免这些离子在阳极上析出。
比铜不活泼的杂质如金和银等沉积在电解槽的底部。
这样生产出来的铜板,称为“电解铜”,质量极高,可以用来制作电气产品。
沉淀在电解槽底部的称为“阳极泥”,里面富含金银,是十分贵重的,取出再加工有极高的经济价值。
中华人民共和国国家标准GB/T 467—1997阴极铜前言本标准是参照ASTMB115-93《阴极铜》对GB467-82《电解铜》进行修订的。
本标准将原GB 467-82 中的电解铜(Cu-1)改名为标准阴极铜(Cu-CATH-2),相当于ASTMB115中的2号阴极铜。
根据国内的实际情况,本标准对标准阴极铜中杂质极限含量的规定,与ASTMB115中的2号阴极铜有以下差别:标准阴极铜的铋含量较高,而铅含量较低;对锌和硫作了规定,而对硒和碲未作规定,ASTMB115与此相反,对硒和碲作了规定,而对锌和硫未作规定。
此外,还将GB/T 13585-92《高纯阴极铜》规定的高纯阴极铜(Cu-CATH-1)纳入了本标准。
GB/T 13585-92是等效采用BS 6017-1989《精炼铜》中的高纯阴极铜制定的,有关技术内容纳入本标准时未作任何修改。
本标准的范围与原标准不同,并将标准名称改为《阴极铜》。
本标准自实施之日起,代替原GB 467-82和GB/T 13585-92,同时GB 466-8 2标准作废。
本标准由中国有色金属工业总公司提出。
本标准由中国有色金属工业总公司标准计量研究所归口。
本标准由上海冶炼厂和中国有色金属工业总公司标准计量研究所负责起草。
湿法冶炼阴极铜生产工艺流程
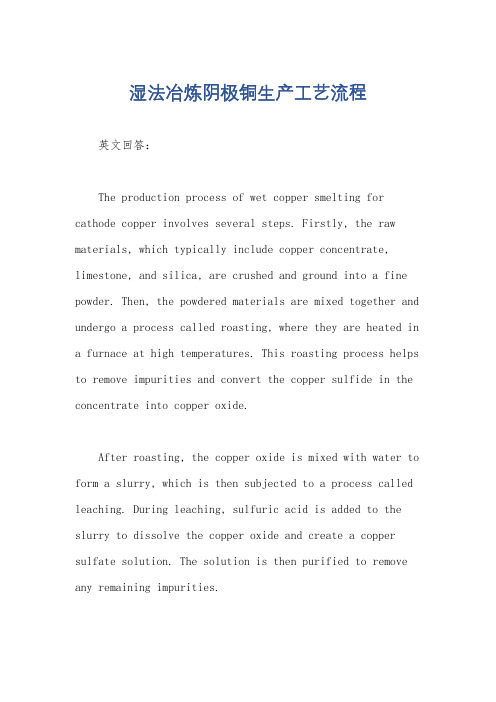
湿法冶炼阴极铜生产工艺流程英文回答:The production process of wet copper smelting for cathode copper involves several steps. Firstly, the raw materials, which typically include copper concentrate, limestone, and silica, are crushed and ground into a fine powder. Then, the powdered materials are mixed together and undergo a process called roasting, where they are heated in a furnace at high temperatures. This roasting process helps to remove impurities and convert the copper sulfide in the concentrate into copper oxide.After roasting, the copper oxide is mixed with water to form a slurry, which is then subjected to a process called leaching. During leaching, sulfuric acid is added to the slurry to dissolve the copper oxide and create a copper sulfate solution. The solution is then purified to remove any remaining impurities.Next, the purified copper sulfate solution is subjected to electrolysis. This involves passing an electric current through the solution, causing the copper ions to migrate towards the cathode, where they are reduced and deposited as pure copper. The anode, typically made of impure copper, dissolves as copper ions are released into the solution to maintain the electrical balance.Once the electrolysis process is complete, the deposited copper on the cathode is removed and processed further to produce cathode copper. This involves melting the copper and casting it into molds to form copper cathodes of a specific shape and size. The cathodes are then inspected for quality and packaged for shipment.中文回答:湿法冶炼阴极铜的生产工艺流程包括几个步骤。
金属公司阴极铜生产工艺技术标准

金属公司阴极铜生产工艺技术标准大冶有色金属公司企业标准Q/DYJ.J.04.19- 阴极铜生产工艺技术标准(自用 .1)-4-10-发布 -4-10实施大冶有色金属公司发布大冶有色金属公司企业标准阴极铜生产工艺技术标准Q/DYJ.J.04.19-1 主题内容与适用范围本标准规定了采用生精矿贫化炉和诺兰达炉熔炼、冰铜转炉吹炼、阳极炉精炼及电解精炼生产阴极铜所需的原料、燃料的要求,主要设备,工艺及操作要点。
本标准适用于公司阴极铜的生产及技术管理。
2原燃料要求2.1 进厂铜精矿a)进口铜精矿:Cu>20.00% Fe >24% S>30% MgO<1%Al2O3<5% Zn<0.6% As<0.1% Sb<0.02%Bi<0.07% F<0.06%b)国内铜精矿: Cu>16.00% S>18% MgO<1%Al2O3<5% Zn<0.6% As<0.1% Sb<0.02%Bi<0.07% F<0.06%2.1 铜精矿a)诺兰达炉混合铜精矿:Cu>20.00% Fe >24% S>23%MgO<1% Al2O3<5% Pb<0.6%Zn<0.6% As<0.1% Sb<0.02%Bi<0.07% F<0.06% H2O 5~9%b)贫化炉混合铜精矿:Cu>16% As<0.1% F<0.06% Bi〈0.1%Sb<0.1% Cd<0.02% MgO<1% Al2O3<1.5%Pb<1% Zn<5%Q/DYJ.J.04.19-Cu/S>0.75 H2O 5~9%2.2 燃料a)粉煤:固定碳>55% 挥发份>25% 灰份<15%水份<1~2% 发热值>2.7×104kJ/kg 粒度-200目>80%b)重油:发热值>3.5×104 kJ/kg含水<5% 含硫<1.0% 粘度<8×10-3m2/s(25℃)c)石油焦:发热值>3.5×104 kJ/kg 粒度<100mmd)天然气: CH4>97%(体积比)2.3 熔剂石英石:SiO2>70% CaO<3% Fe<4% As<0.1%F<0.03% H2O<7% 粒度:诺兰达炉、反射炉<15mm;入转炉8-25mm2.4 水a)生活水:符合生活饮用水水质卫生规范(卫法监发[ ]161号)。
- 1、下载文档前请自行甄别文档内容的完整性,平台不提供额外的编辑、内容补充、找答案等附加服务。
- 2、"仅部分预览"的文档,不可在线预览部分如存在完整性等问题,可反馈申请退款(可完整预览的文档不适用该条件!)。
- 3、如文档侵犯您的权益,请联系客服反馈,我们会尽快为您处理(人工客服工作时间:9:00-18:30)。
大冶有色金属公司企业标准Q/DYJ.J.04.19-2007阴极铜生产工艺技术标准(自用2008.1)2007-4-10-发布 2007-4-10实施大冶有色金属公司发布大冶有色金属公司企业标准阴极铜生产工艺技术标准Q/DYJ.J.04.19-20071 主题内容与适用范围本标准规定了采用生精矿贫化炉和诺兰达炉熔炼、冰铜转炉吹炼、阳极炉精炼及电解精炼生产阴极铜所需的原料、燃料的要求,主要设备,工艺及操作要点。
本标准适用于公司阴极铜的生产及技术管理。
2原燃料要求2.1 进厂铜精矿a)进口铜精矿:Cu>20.00% Fe >24% S>30% MgO<1%Al2O3<5% Zn<0.6% As<0.1% Sb<0.02%Bi<0.07% F<0.06%b)国内铜精矿: Cu>16.00% S>18% MgO<1% Al2O3<5%Zn<0.6% As<0.1% Sb<0.02% Bi<0.07%F<0.06%2.1 铜精矿a)诺兰达炉混合铜精矿:Cu>20.00% Fe >24% S>23%MgO<1% Al2O3<5% Pb<0.6%Zn<0.6% As<0.1% Sb<0.02%Bi<0.07% F<0.06% H2O 5~9%b)贫化炉混合铜精矿:Cu>16% As<0.1% F<0.06% Bi〈0.1%Sb<0.1% Cd<0.02% MgO<1% Al2O3<1.5%Pb<1% Zn<5%Q/DYJ.J.04.19-2007Cu/S>0.75 H2O 5~9%2.2 燃料a)粉煤:固定碳>55% 挥发份>25% 灰份<15%水份<1~2% 发热值>2.7×104 kJ/kg 粒度-200目>80%b)重油:发热值>3.5×104 kJ/kg含水<5% 含硫<1.0% 粘度<8×10-3m2/s(25℃)c)石油焦:发热值>3.5×104 kJ/kg 粒度<100mmd)天然气: CH4>97%(体积比)2.3 熔剂石英石:SiO2>70% CaO<3% Fe<4% As<0.1%F<0.03% H2O<7% 粒度:诺兰达炉、反射炉<15mm;入转炉8-25mm2.4 水a)生活水:符合生活饮用水水质卫生规范(卫法监发[2001]161号)。
b)生产水:符合GB50050-95水质控制标准。
2.5 硫酸:工业纯,符合GB534规定,其中H2SO4≥98%2.6 盐酸:工业纯,符合GB320规定,其中HCl≥31%2.7 明胶:工业纯,其中H2O≤16%,粒度≥6mm2.8 硫脲:工业纯,符合GB17013-88的规定,其中硫脲含量≥98%3 产品质量标准3.1 粗铜:符合国标YS/T70-19933.2 阴极铜:符合国标GBT/467-1997 (T2、T3为纯铜)4 工艺流程4.1 流程简介Q/DYJ.J.04.19-2007将铜精矿、返料、石油焦、熔剂等按入料条件要求进行配料,加入诺兰达炉、贫化炉熔炼,产出冰铜,送转炉吹炼产出粗铜,再送阳极炉精炼产出阳极铜,再经电解精炼产出阴极铜。
诺兰达炉及贫化炉高温烟气经余热锅炉产生蒸汽或发电。
诺兰达炉及转炉含硫烟气送硫酸系统制酸。
4.2工艺流程图冶化工艺流程图Q/DYJ.J.04.19-20074.3 关键过程的确认关键过程:配料过程、诺兰达炉熔炼过程、转炉吹炼过程、阳极炉精炼过程、电解过程关键岗位:配料岗位、诺兰达炉熔炼主控室、转炉炉前岗位、阳极炉炉前岗位、电解电调岗位、电解槽下岗位5主要设备5.1 备料工序鄂式破碎机 450×750mm N=50kw 1台园锥中碎机 KCJI-900 N=40kw 1台(50-86t/h)圆锥细碎机 KCJI-1200 N=60kw 1台球磨机Ф2.2×3.9m N=240Kw 2台回转窑Ф2.2×13.5m 3台Ф3.2×20m 1台10t双梁桥吊 Q=10t L k=22.5m 3台10t双梁桥吊 Q=10t L k=31.5m 3台熔剂抓斗起重机Q=10t L k=22.5m 2台原煤起重机 Q=10t L k=22.5m 2台5.2 熔炼工序贫化炉271m2 1台诺兰达炉Ф4.7×18m 1台Atlas风机 HA9-7 N=1491Kw 1台抛料机 B=500 mm 4台泥炮机 JOY 1台捅风眼机 F-3095-1 1台贫化炉电收尘器YWZ-RS40-2/3 2台650kW离心风机:Y4-73-11ND220 2台诺兰达炉电收尘器:KWZ-RS50- 1/4 2台5.3 转炉吹炼及阳极炉精炼工序转炉Ф3.6×8.8m 3万Nm3/h 0.7Nm3/min.cm2 2台转炉Ф3.66×7.1m 1台转炉Ф4×11.7m 4万Nm3/h 0.61Nm3/min.cm2 2台精炼炉Ф3.6×8.1m 1台精炼炉Ф3.92×9.2m 2台高压鼓风机 3500kW 920m3/min 1台高压鼓风机 1800 kW Q=45000Nm3/h 3.6-3.8万m3/h 3台精炼园盘浇铸机Ф11×20模25t/h 1台双园盘浇铸机双16模 85t/h 1台鼓风机 G9-38-11 Q=44600m3/h 110Kw 2台引风机 Y4-73-11 Q=71000 m3/h 110Kw 2台引风机 Y4-73-11 Q=14000m3/h 1台50t桥式吊车 Q=50/15t L k=22.5m 250Kw 4台5.4 电解工序一系生产槽 3200×1140×1200mm 4.4m3 90 140个阳31/30二系生产槽 3200×1140×1200mm 4.4m3 90 196个阳31/30三系生产槽 4000×1130×1270mm 5.7m3 90 264个阳39/38种板系统 4500×1140×1200mm 6.1m3 110 86个阳37/36一系钛板加热器 PS-J 20m2 3台二系钛板加热器 P3-JHBB型 20m2 3台三系钛板加热器 BRH70 60m2 3台种板加热器 P3-JHBB型 20m2 2台吊车 10t 7台电二小板电解槽 5420×1170×1420mm 9 m3336个阳53/52电二大板电解槽 5420×1410×1720mm 13m3 596个阳48/47电二种板电解槽5420×1410×1720mm 13 m3 50个阳48/47板式换热器 AK20-HGL 20m2 3台板式换热器 BR0.6-0.6-75-1 75m2 2台种板换热器 BR0.3T-0.6-17-E 2台板式换热器 BR0.6-0.8-75-1 75m2 1台板式换热器 S42-IS10 22m2 3台专用行车 26t 3台行车 16t 3台阴极洗涤机组 CATHODE-400 1台阳极洗涤机组 ANODE-250 1台残极洗涤机组 400片/h 1台导电棒机组 1台始极片机组 500片/h 1台过滤机 LAROX LSF-E18/36-AV-2 2台5.5 锅炉工序45t余热锅炉 WGZ45/39-1 1台23t余热锅炉 QCF82/830-23-4.31 1台14.3吨余热锅炉QCF57/800-14.3-3.82 2台汽轮机发电机组N6-35 1套汽轮机发电机组CB3-3.43/0.981/0.49 1套5.6 制氧工序空气过滤器 GL-40000-3 2台空气透平压缩机 DH63-14 2台Q/DYJ.J.04.19-2007空气冷却塔 UF-32000/5.7-Ⅱ 2台分子筛纯化系统 HXK-31500/5.6 2台透平式空气膨胀机 PLPK/72.7/7.6-0.44 4台空分塔 KDON-6000/13000-X 2台氧气透平压缩机 2TY-108.3/4-Ⅰ 2台高压循环水泵 300S58 3台氧气增压压缩机 DW-150/0.07-2 2台硫酸离心鼓风机 AI800-1.28 2台水环式真空泵 2BEC72 4台5.7 渣缓冷工序破碎机 DH300LC-V 1台破碎机 325BL 1台龙门吊 50/10 1台龙门吊 50/15 1台6 监视与测量的要求Q/DYJ.J.04.19-20076.1 阴极铜生产检验流程图说明: ------取样点-------工序6.2 阴极铜生产检测项目表7工艺参数7.1 备料工序干铜精矿:Cu>18% H2O 5%∽9%回转干燥窑处理量:20~45t/h台、80~100t/h台粉煤:含H2O1~2% 粒度-200目>80%原煤处理量:250t/日±贫化炉、诺兰达炉熔剂粒度<8mm熔剂处理量:30~45t/h转炉熔剂粒度:8~25mm7.2 熔炼工序诺兰达炉:冰铜品位60~73%;炉温1160~1230℃;炉渣Fe/SiO21.3~1.8;渣口渣含铜<7%;氧浓<50%;风量>22000m3/h;烟气SO2浓度>7.5%;冰铜面1000~1300mm;总液面< 1750mm;处理量>50~90t/h,石油焦0.5~1.5t/h、石英石2.5t/h±。
贫化炉:耗煤量 7.5~9.0 t/h;炉头温度1380~1500℃;炉尾温度1200~1300℃;炉膛压力4.9~29.4Pa;一次风量18000~24000Nm3/h;二次风量30000~46000Nm3/h (使用富氧操作时:一次风量10000~20000Nm3/h;二次风量26000~40000Nm3/h);烟囱温度≤320℃;处理量>900t/日;冰铜品位>25%;渣含铜≤0.80%、T炉底<640℃。
电收尘:诺兰达炉电收尘进口温度<400℃,负压0~-2000Pa贫化炉电收尘进口温度<400℃,负压0~-2000Pa7.3 转炉吹炼及阳极炉精炼工序转炉吹炼:送风时率≥70%;鼓风压力0.08-0.12Mpa;鼓风量>16000Nm3/h;转炉渣含铜<3%(不含筛炉渣);粗铜含铜≥98.0%;一周期温度<1260℃;二周期温度<1300℃阳极炉精炼:渣率≤4%;天燃气用量≤48 Nm3/t;阳极铜含铜≥98.5%;氧<0.2%;硫≤0.02%小阳极板 780×750mm 设定值±5(根据电解工艺生产需要)大阳极板 1000×960mm 设定值±3(根据电解工艺生产需要)7.4 电解工序阳极同极中心距平均值:小板95mm 大板105mm电解液成份g/l:生产槽:Cu40~55 H2SO4160~200 Cl-0.01~0.09As≤12 Sb≤1 Bi≤0.5 Ni≤15种板槽: Cu38-55 H2SO4160~200 Cl-0.001~0.02As≤12 Sb≤1 Ni≤12 Bi≤0.35平均槽电压:生产槽≤0.37V 种板槽≤0.45V电流密度230~300A/m2电解液温度60~65℃电解液循环量:生产槽20~30l/min 种板槽20~40l/min添加剂:生产系统:明胶40-350g/t.Cu 硫脲20-170g/t.Cu盐酸0~500ml/t.Cu种板系统:明胶800~2500g/t.Cu 硫脲10~60g/t.Cu盐酸0~500ml/t.Cu阳极泥:含铜≤20%,含水≤20%阴阳极周期:电二小板阴极8-9天、阳极16-18天电二大板阴极7-8天、阳极21-24天种板系统阴极24小时、阳极14-16天阴阳极尺寸:小板阳极(780±10)*(755±10)*(35±5)小板阴极(825±15)*(785±10)*(0.3-0.6)Q/DYJ.J.04.19-2007大板阳极(975±10)*(955±10)*(45-50)大板阴极(1030±10)*(986±5)*(0.4-0.8)7.5 锅炉工序除盐水:硬度≤5Epb Na<100ppb SiO2<100ppb导电度<1 0μΩ/cm PH>7供电解蒸汽:< 0.5Mpa供制氧蒸汽: 0.5~0.8Mpa45t锅炉:压力≤3.8Mpa 温度400~450℃水位±50mm最大±100mm23t锅炉:压力≤4.31Mpa 温度254℃水位±50mm最大±100mm14.3t锅炉:压力≤3.82Mpa 温度235℃水位±50mm最大±100mm7.6 制氧工序空压机出口压力 0.45~0.53Mpa进冷箱空气流量 24000~33000Nm3/h空气出空冷塔温度 6~12℃空气出分子筛后二氧化碳含量<0.5ppm产品氧气流量 4500~6300Nm3/h冷凝蒸发器液氧液位 2000~2700mm氧气纯度 99.2~99.6%供氧压力:0.1~0.25Mpa变压吸附制氧系统:产品氧气流量 7000~9000Nm3/h氧气纯度 70~82%7.7 渣缓冷工序水冷时间>36h冷渣块度<350mm8 技术经济指标粗铜冶炼回收率:诺兰达炉≥98.0% 贫化炉≥97.4%诺兰达炉吨铜单耗:直水<3.4t 电<1150kwh 石油焦≤0.05t重油<0.02t 石英石<0.4t 柴油<0.01t 诺兰达炉渣口渣含铜<7%贫化炉吨铜单耗: 直水<8t(取消锅炉后)回水<30t(取消锅炉后)电<380kwh 煤<1t贫化炉渣含铜≤0.8%贫化炉电收尘效率≥97%诺兰达炉电收尘效率≥97%转炉直收率≥88%粗铜单耗:煤单耗(贫化炉)≤1200Kg/t 石油焦单耗(诺兰达炉)≤0.5t 电单耗≤850Kwh/t 水单耗≤45t/t 石英石单耗≤0.2t/t 耐火材料单耗≤14Kg/t阳极铜合格率≥98.5%阳极铜主品位≥98.5%高纯阴极铜产出率≥98%转炉渣含铜≤3%(不含筛炉渣)电解直流电单耗<290kwh/t.Cu电解蒸汽单耗<1t/t.Cu电解硫酸单耗<20kg/t.Cu电流效率≥96%残极率≤19.5%铜冶炼综合能耗≤650Kg标煤/t制氧:电单耗≤750Kwh/KN m3(非送风状态)9 操作要点及人员要求9.1 岗位操作要点:9.1.1 备料工序a)进厂铜精矿严格执行分仓堆放,按配料比配料,做到配料准确,合理用料。