铜冶炼工艺素材
铸造用纯铜及铜合金的熔炼工艺

铸造用纯铜及铜合金的熔炼工艺铸造用纯铜及铜合金的熔炼工艺[文摘]详细介绍了铸造用纯铜、青铜、黄铜等主要铜合金的熔炼工艺,并提出了实际生产中应注意的问题,供同行参考。
铸造用纯铜和铜合金是重要的有色金属,在实际生产中应用广泛。
常用的铜合金根据成分不同主要分为两类,即铸造黄铜和铸造青铜。
无论是砂型铸造还是熔模铸造,熔炼都是铸造生产的关键环节。
各种铜合金的熔炼有相似之处,也有不同之处。
在多年的生产实践中,我们总结了纯铜和铜合金,主要是青铜和黄铜的冶炼工艺经验,供相关人员参考。
一、纯铜冶炼冶炼设备用于中频感应炉、热电偶、钢包和石墨桔灾害等。
(1)将柑橘灾害预热至暗红色,在灾害底部加入一层厚度约30-50毫米的干木炭或覆盖剂(60%硼砂和137%碎玻璃),依次加入剩余的碎料、废料和棒料,最后加入纯铜(2)中加入的合金元素可在炉台上预热,严禁向液态金属中加入冷料。
在整个熔化过程中,应频繁移动炉料以防止桥接。
(3)合金完全熔化后,当温度达到1200-1220℃时,加入占合金液重量0.3-0.4%的磷铜进行脱氧,磷与氧化亚铜发生后续反应产生的P2O5气体从合金中逸出,磷酸铜会浮在液面上,通过去渣去除,达到脱氧的目的此外,脱氧过程中需要连续搅拌。
最后,炉渣被剥离并从熔炉中排出。
合金液的浇注温度一般为1100-1200℃以锌为主要合金元素的黄铜铜基合金的熔炼是黄铜,它分为普通黄铜和特种黄铜两种类型普通黄铜是由铜和锌组成的二元合金,主要用于压力加工。
在普通黄铜的基础上加入其他合金元素,如硅、铝、锰、铅、铁和镍,就成了特殊的黄铜。
铸造黄铜主要是特殊的黄铜。
1、合金成分和金属配料要求为铜合金化学成分,由于主要成分变化范围大,所以在配料计算过程中,应根据其性能要求,选择合适的配料合金的化学成分应符合GB1176-1987。
几种常用的黄铜熔炼配料的化学成分应符合表1,炉料应干燥干净。
应进行喷砂处理,以清除任何污垢和铁锈。
2,负担比根据一般的配料惯例,新的配料组成应占配料总重量的30%以上,而返料负担应在70%以下。
铜的加工冶炼工艺流程

铜的加工冶炼工艺流程3.1.1 原材料(1)铜精矿在自然界中自然铜存量极少,一般多以金属共生矿的形态存在。
铜矿石中常伴生有多种重金属和稀有金属,如金、银、砷、锑、铋、硒、铅、碲、钴、镍、钼等。
根据铜化合物的性质,铜矿物可分为自然铜、硫化矿和氧化矿三种类型,主要以硫化矿和氧化矿,特别是硫化矿分布最广,目前世界钢产量的90%左右来自硫化矿。
铜矿石经选矿富集获得精矿,常见为褐色、灰色、黑褐色、黄绿色,成粉状,粒度一般小于0.074mm。
含铜量13-30%,按行业标准YS/T 318-1997《铜精矿》的规定,其化学成分和产品分类如表1。
(2)未精炼铜按国家标准GB/T 11086-1989《铜及铜合金术语》规定,未精炼铜包括冰铜、黑铜、沉淀铜和粗铜。
冰铜主要由硫化亚铜和硫化亚铁组成的中间产品,黑铜通常用彭风炉熔炼废杂铜或氧化铜矿石而产生的含杂质较多的铜,铜含量一般为60%-85%。
沉淀铜通常用铁从含铜的溶液中置换,沉淀而获得的铜和氧化铜的不纯混合物,干量计算铜含量一般约50%-85%。
粗铜是用转炉吹炼冰铜而产生的纯度不高的铜,粗铜中铜的含量一般约为98%,本标准中规定的未精炼铜,主要指的是粗铜。
粗铜按行业标准YS/T 70-1993《粗铜》的规定,按化学成分分为三个品级,见表2。
表1 铜精矿的化学成分及分类表2 粗铜的化学成分铜精矿的检验方法:铜矿水分含量的测定按GB 14263-1993《散装浮选铜精矿取样、制样方法》中的规定进行,铜精矿化学成分的测定按GB3884-2000《铜精矿化学分析方法》的规定进行。
(3)电解用铜阳极电解用铜阳极的化学成分见表3。
表3(4)铜废碎料铜废碎料涉及的范围较广,包括紫铜、黄铜、青铜、白铜的废杂料,本标准规定的铜废碎料仅指紫杂铜。
紫杂铜为铜制品所产生的各类废料、废件。
如废旧电缆、紫铜管、棒、板、块、带及带薄镀层的上述材料和其它非合金类铜废料等。
有以下5种分类及规格:第1类:(a)紫铜管、棒、板、块、带,表面干净,无油泥和其它沾附、夹杂。
铜的冶炼等资料

TC/RC(Treatment and refining charges for Processing concentrates),可以翻译为将铜精矿转化为精铜的处理和精炼费用。
TC就是处理费(Treatment charges)或粗炼费,而RC就是精炼费(Refining charges)。
TC/RC是矿产商和贸易商向冶炼厂支付的、将铜精矿加工成精铜的费用。
TC以美元/吨铜精矿报价,而RC以美分/磅精铜报价。
将两者结合为一个数字,可以将TC化为美分/磅来报价,也可以将RC化为美元/吨报价,然后直接相加。
以TC为例来说,TC除以22.046221化为美分/磅,除以0.3(一般TC/RC的作价都是基于含铜量30%的铜精矿),除以0.965(假如96.5%的回收率)。
这种计算方法可简化为“TC费用/6.38”,然后将得到的数字与RC费用相加即可得到综合的TC/RC费用。
由于矿石品位和回收率不同,要根据具体情况来定,所以并无固定的公式。
TC/RC费用明显低于冶炼商的成本,冶炼商还是愿意购买铜精矿冶炼加工的原因:1.炼一吨铜可生产3吨左右的硫酸,硫酸吨成本在200-300元左右,因此当硫酸价格高企时,尽管加工费低冶炼商仍然愿意冶炼加工。
2.在铜精矿中不仅含有铜,还含有金银等一些贵重金属,而这些金属除黄金以外都是不计价的(黄金计价部分也比实际含量低),这对冶炼商来说是一笔额外的收入,可以弥补加工费上的亏损。
TC/RC谈判介绍:2003年,铜陵有色、云铜集团、江铜集团等国内同业巨头发起成立了中国铜原料联合谈判组(China Smelters Purchase Team,简称CSPT小组),代表中国铜冶炼商与国外铜精矿供应商进行谈判,集中向国际市场采购铜精矿,以获取更高的加工费,目前这个联盟已涵盖业内九大铜企。
每季度CSPT 的会员会召开一次经理会议,以此来确定现货买卖的价格底线,每年年底,CSPT小组将与各矿业巨头进行下年度铜精矿加工费的谈判,CSPT小组主要进行协调,具体谈判是国内铜企与外国矿企一对一进行的,但事先CSPT小组内部会确定个大致底价和谈判原则。
铜冶炼工艺(3篇)

第1篇一、引言铜是人类历史上最早使用的金属之一,具有优良的导电性、导热性、耐腐蚀性和可塑性。
随着科技的进步和工业的发展,铜在各个领域的应用越来越广泛。
铜冶炼工艺是指从铜矿石中提取铜金属的一系列物理和化学过程。
本文将详细介绍铜冶炼工艺的原理、流程以及主要设备。
二、铜矿石的类型铜矿石主要分为两大类:硫化铜矿石和氧化铜矿石。
硫化铜矿石主要含有黄铜矿(CuFeS2)、辉铜矿(Cu2S)等硫化物,氧化铜矿石主要含有赤铜矿(Cu2O)、孔雀石(CuCO3·Cu(OH)2)等氧化物。
三、铜冶炼工艺流程1. 铜矿石破碎与磨矿铜矿石破碎与磨矿是将铜矿石从原生矿石中分离出来的第一步。
通过破碎机将矿石破碎成一定粒度,再通过磨矿机将矿石磨成细粉,以利于后续的浮选和冶炼。
2. 浮选浮选是将铜矿石中的硫化物和氧化物进行分离的过程。
将磨好的矿石加入浮选剂,通过调整pH值和搅拌,使硫化物与水形成泡沫,从而实现铜矿物与其他矿物的分离。
3. 精选精选是将浮选得到的铜精矿进行进一步处理,以提高铜的品位。
精选方法有火法精选、湿法精选等。
4. 炼铜炼铜是将精选后的铜精矿进行熔炼,提取铜金属。
炼铜方法主要有火法炼铜、湿法炼铜等。
(1)火法炼铜火法炼铜是将铜精矿在高温下进行熔炼,使铜与硫反应生成硫化铜,然后通过吹炼氧化硫化铜,使铜转化为氧化铜。
火法炼铜主要包括熔炼、吹炼、精炼等过程。
熔炼:将铜精矿加入熔炼炉中,加入助熔剂(如石灰石)和燃料(如焦炭),在高温下熔炼,使铜精矿中的硫化物转化为硫化铜。
吹炼:将熔炼得到的熔融硫化铜吹入转炉中,通过吹入空气,使硫化铜氧化成氧化铜,同时将硫氧化成二氧化硫气体排出。
精炼:将吹炼得到的氧化铜熔融,加入氧化剂(如氧气)和还原剂(如碳),使氧化铜还原成铜金属,同时将杂质氧化去除。
(2)湿法炼铜湿法炼铜是将铜精矿经过溶解、氧化、结晶等过程,提取铜金属。
湿法炼铜主要包括浸出、氧化、结晶、电解等过程。
浸出:将铜精矿加入浸出槽中,加入浸出剂(如硫酸、硝酸)和氧化剂(如氧气、空气),使铜精矿中的铜溶解于浸出剂中。
铜冶炼工艺介绍范文

铜冶炼工艺介绍范文首先是矿石制备。
在矿石制备过程中,铜矿石会经过破碎、磨矿和浮选等处理,以获得适合熔炼的原料。
矿石制备的目的是将矿石中的有用成分与废石分离,使得有用成分更容易被提取出来。
接下来是熔炼。
在熔炼过程中,破碎磨矿后的矿石会被送入高温的炉中,与熔剂一同熔化。
熔剂的作用是降低熔化温度,促使矿石中的铜元素与其他杂质分离,形成铜水。
熔炼过程中,熔融的矿石中的杂质会上浮,在炉内形成炉渣,而铜水则会沉淀在炉底。
炼煅是铜冶炼过程中的一个重要步骤。
在炼煅过程中,铜水会被转移至特殊设计的反射炉中进行煅烧。
煅烧的目的是将铜水中的杂质进一步除去,并熔化成为更纯净的铜锭。
在炼煅过程中,炼煅炉内会加入一定的氧气,以加速杂质的氧化和挥发。
精炼是铜冶炼工艺的最后一步。
在精炼过程中,经过炼煅得到的铜锭会继续进行精细处理,以获得更高纯度的铜产品。
精炼过程一般包括电解精炼和火法精炼等几种方法。
电解精炼是利用电解的原理将铜锭置于电解槽中,通过电解液中的电流作用将杂质阳极溶解,而纯铜则沉积在阴极上。
火法精炼则是将铜锭熔化后,通过反复加热、冷却和冶炼的过程,去除残留的杂质。
总之,铜冶炼工艺是将铜矿石提炼出铜元素并进行精细处理的一系列工艺过程。
矿石制备、熔炼、炼煅和精炼是铜冶炼过程中的主要步骤。
每个步骤都有其独特的工艺和设备,以确保最终提取出的铜产品具有高纯度和良好的品质。
铜冶炼工艺在各个行业中都有广泛应用,对于满足社会各方面的铜需求起到至关重要的作用。
铜冶炼的工艺流程及原理
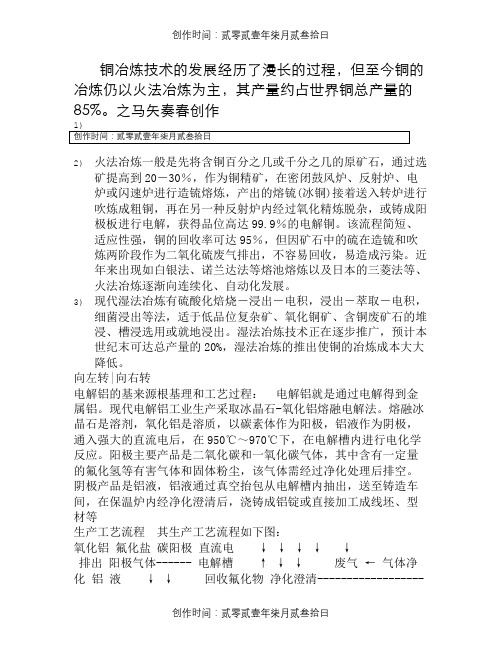
铜冶炼技术的发展经历了漫长的过程,但至今铜的冶炼仍以火法冶炼为主,其产量约占世界铜总产量的85%。
之马矢奏春创作2)火法冶炼一般是先将含铜百分之几或千分之几的原矿石,通过选矿提高到20-30%,作为铜精矿,在密闭鼓风炉、反射炉、电炉或闪速炉进行造锍熔炼,产出的熔锍(冰铜)接着送入转炉进行吹炼成粗铜,再在另一种反射炉内经过氧化精炼脱杂,或铸成阳极板进行电解,获得品位高达99.9%的电解铜。
该流程简短、适应性强,铜的回收率可达95%,但因矿石中的硫在造锍和吹炼两阶段作为二氧化硫废气排出,不容易回收,易造成污染。
近年来出现如白银法、诺兰达法等熔池熔炼以及日本的三菱法等、火法冶炼逐渐向连续化、自动化发展。
3)现代湿法冶炼有硫酸化焙烧-浸出-电积,浸出-萃取-电积,细菌浸出等法,适于低品位复杂矿、氧化铜矿、含铜废矿石的堆浸、槽浸选用或就地浸出。
湿法冶炼技术正在逐步推广,预计本世纪末可达总产量的20%,湿法冶炼的推出使铜的冶炼成本大大降低。
向左转|向右转电解铝的基来源根基理和工艺过程:电解铝就是通过电解得到金属铝。
现代电解铝工业生产采取冰晶石-氧化铝熔融电解法。
熔融冰晶石是溶剂,氧化铝是溶质,以碳素体作为阳极,铝液作为阴极,通入强大的直流电后,在950℃~970℃下,在电解槽内进行电化学反应。
阳极主要产品是二氧化碳和一氧化碳气体,其中含有一定量的氟化氢等有害气体和固体粉尘,该气体需经过净化处理后排空。
阴极产品是铝液,铝液通过真空抬包从电解槽内抽出,送至铸造车间,在保温炉内经净化澄清后,浇铸成铝锭或直接加工成线坯、型材等生产工艺流程其生产工艺流程如下图:氧化铝氟化盐碳阳极直流电↓ ↓ ↓ ↓ ↓排出阳极气体------ 电解槽↑ ↓ ↓ 废气← 气体净化铝液↓ ↓ 回收氟化物净化澄清----------------------- ↓ ↓ ↓ 返回电解槽浇注轧制或铸造↓ ↓ 铝锭线坯或型材方程电解铝就是通过电解得到的铝.重要通过这个方程进行:2Al2O3==4Al+3O2。
铜冶炼

2、铜的性质
• 物理性质:具有良好的延展性,导电性, 导热性。 • 化学性质:铜相对比较稳定,不溶于稀硫 酸和盐酸,氧化剂的存在能导致其溶解。 • 用途:黄铜-铜锌合金,青铜-铜锡合金, 白铜-铜镍合金,通常把黄铜、白铜以外 的铜基合金都称为青铜。重要的战略物资
二、炼铜的原料
三、艺流程
火法炼铜原则工艺流程图
七、铜的电解精炼
• 设备:电解槽 • 作用:进一步出去杂质并回收有价金属 • 产品:阴极铜或叫电解铜、阳极泥、电解 液 • 技术经济指标:电流密度、电流效率、直 收率、电解总回收率、硫酸消耗等
四、冰铜
• • • • 反射炉熔炼 电炉熔炼 密闭鼓风炉熔炼 闪速炉熔炼
五、冰铜的转炉吹炼
• • • • 设备:转炉 作用:将冰铜吹炼成粗铜 产品:粗铜、转炉渣、烟尘和烟气等 技术经济指标: 送风时率 生产率 炉子寿命 铜的直收率
六、粗铜的火法精练
• 设备:反射炉 • 作用:把粗铜中的杂质出去。并把火法精炼铜铸成阳极 • 产品:火法精炼铜 火法精炼炉渣 • 技术经济指标: 单位生产率 燃料消耗 还原剂消耗 空气消耗 铜的直收率
铜冶炼
一、概述
1、铜的生产发展
铜的出现使人类由石器时代进入时期 商殷时期青铜的冶炼就已经达到了很高的水 平,发明了胆水(硫酸铜溶液)浸铜法 北宋末年铜的生产量已达到2000T 乾隆年间铜的生产达万吨以上 1911年我国开始采用鼓风炉炼铜 解放以后各种铜的冶炼技术得到了快速发展 --回收烟气制酸、反射炉的改进、闪速炉的采 用等。
铜冶炼 工艺

铜冶炼工艺铜是我国文化遗产中使用最广泛的金属之一,其在人类历史中应用已有数千年的历史。
目前,铜的产量约占全球金属产量的 1/3 左右,其中矿石铜约占产量的 70% 左右,废铜约占 30% 左右。
铜的优良性能使得它得到广泛应用,例如用于电线、管道、制酸、制造自行车、汽车、火车、飞机、船舶、家电等设备和机械件等。
铜的产量与品质受到各种因素的影响,其中最关键的因素之一就是铜的冶炼技术和生产工艺。
铜的冶炼工艺可以分为多个阶段,通常包括挖掘矿石、粉碎、选矿、冶炼、炼铜,铜的产量和质量取决于每个阶段的技术和工艺。
铜矿通常以硫化矿的形式存在于地下,其含量一般在 2%-3% 左右。
因此在冶炼铜之前需要将地下矿石挖掘出来。
首先需要在地面上建造一系列金属结构,例如运输带、露天开采设备和排水设备等,以便将挖掘出来的矿石从地下输送到地面上进行处理。
在挖掘出来的矿石经过初步分选和粉碎之后,需要对其进行选矿处理,以去除掉非铜矿物和其他杂质,获得含铜较多的矿石。
选矿可采用不同的方法,其中包括重砂选、气浮选、泡沫浮选等方法。
这些方法的目的是通过物理和化学方式,将含铜矿石从其他矿物中分离出来。
选矿过程中获得的含铜矿石经过多次粉碎和筛选之后,需要将其送进冶炼炉中。
常用的冶金炉有三种类型:闪速炉、电炉和转炉。
闪速炉是最常见的冶炼设备,它不仅可以冶炼铜,还可以冶炼其他金属。
炉内需要加入大量的煤和氧气,以便将炉内铜矿石加热到足够高的温度,使铜矿石中的铜被氧化并变成铜氧化物。
这个过程中需添加熔剂来降低熔点,加速熔化,一般使用碳包裹铝的方案来达到此目的。
接下来,铜氧化物与硫化物反应,产生了二氧化硫和铜。
这个过程是一个放热反应,因此需要控制炉子的温度和通入氧气的量,以避免产生过量的二氧化硫和产生副产物。
冶炼完成后,铜和其他杂质分离,生成高纯度铜。
高纯度铜的生产过程中涉及到多个工艺,依次包括冷却、烧结、电解和精炼等步骤。
冷却和烧结是将铜矿石熔化之后冷却,形成固态块状的铜的过程。
- 1、下载文档前请自行甄别文档内容的完整性,平台不提供额外的编辑、内容补充、找答案等附加服务。
- 2、"仅部分预览"的文档,不可在线预览部分如存在完整性等问题,可反馈申请退款(可完整预览的文档不适用该条件!)。
- 3、如文档侵犯您的权益,请联系客服反馈,我们会尽快为您处理(人工客服工作时间:9:00-18:30)。
1、金属铜的物理性质
铜是一种化学元素,它的化学符 号是Cu,它的原子序数是29,是一种 过渡金属。 铜呈紫红色光泽的金属, 密度8.92克/立方厘米。熔点 1083.4±0.2℃,沸点2567℃。常见化 合价+1和+2。电离能7.726电子伏特。 铜是人类发现最早的金属之一, 最好的纯金属之一,稍硬、极坚韧、 耐磨损。还有很好的延展性。导热和导电性能较好。铜和它的一些合金有 较好的耐腐蚀能力,在干燥的空气里很稳定。但在潮湿的空气里在其表面 可以生成一层绿色的碱式碳酸铜Cu2(OH)2CO3,这叫铜绿。可溶于硝酸 和热浓硫酸,略溶于盐酸。容易被碱侵蚀
奥托昆普法
炼铜工艺分类
现代火法炼铜工艺从大的方面可分为两类: 即漂浮熔炼和熔池熔炼。 漂浮状态熔炼是将几乎彻底干燥的精矿与空 气或富氧空气一起喷入炉子空间,使硫化物在漂 浮状态下进行氧化反应,可充分利用粉状物料的 巨大表面积,加速完成初步造锍和造渣过程。此 法熔炼强度大,设备能力大,节能,产出的烟气 SO2浓度高。工业上已经应用的有闪速熔炼法、 基夫赛特法等。
闪速熔炼流程图
诺兰达炉流程图
奥斯麦特流程图
双闪工艺流程图
再生铜的流程图
六.我公司富氧底吹连续吹炼工艺解读
底吹炼铜法是具有中国知识产权的一种炼铜工艺。采用一个 卧式的转炉,通过底部的氧枪将富氧空气吹入炉内,进行强 化熔炼,富氧浓度达75%,实现完全自热熔炼,不用配煤。 从投产后运营的情况来看,底吹炼铜法在工艺上有着突出的 特点:原料适应性强、备料简单、精矿不用干燥和制粒、富 氧浓度高、炉体热损失少(炉体无铜水套)、熔池反应速度 快、氧枪寿命长、易操作、烟尘率低、环保条件好和投资省 等。特别是富氧空气直接送到铜锍层反应,不易形成泡沫渣, 安全性高;单炉完成铜锍和渣的分离,不需设沉降电炉, Fe/SiO2高(1.8~2.0),渣量少,熔炼渣经渣选矿,渣尾 矿含Cu~0.35%,铜回收高,>98.5%;同时底吹熔炼还具 有脱除杂质高,贵金属富集率高等优点。
工艺流程图
设备连接图
连吹流程图
底吹熔炼流程图
主要工艺过程
火法区域的工艺流程按作业性质可分为:
精矿仓及配料系统、铜锍破碎及上料系 统、底吹熔炼系统、底吹吹炼系统、阳 极炉及浇铸系统、环集烟气及阳极炉烟 气脱硫系统等。
火法系统效果图
原料卸矿、储存配料及上料系统
精矿仓配料及原料输送系统处理精矿量1424t/d。精矿仓可储存精矿 时间为50天。精矿仓中的各种铜精矿利用抓斗起重机抓配 成成分均匀的 混合铜精矿、混合铜精矿、渣精矿、石英石分别通过抓斗桥式起重机、 圆盘给料机和定量给料机经胶带输送机送至熔炼厂房,返回烟尘经双螺 旋喂料机和加湿搅拌器。吹炼用石英石和部分冷料经1#、2#胶带输送机 送到4#胶带输送机。3、4#胶带输送机共用一个通廊,并经过转运站转 运至5、6#胶带输送机上,然后运往底吹熔炼厂房。 考虑到冬季极端寒冷天气的情况,本项目设计一个精矿解冻库, 采用蒸汽辅助热风进行解冻,将车皮上冻结的精矿在解冻库解冻 后再运往精矿仓。 熔炼系统对精矿配料及上料系统的要求: (1)上料必须连续稳定。 (2)配料、上料的计量设备要精确。 (3)配送到熔炼系统的物料粒度、水分含量要符合熔炼系统的要求
铜锍破碎、储存及配料
熔炼炉产出的铜锍经缓冷后,倒入破碎场进行三级破碎 破碎流程为:液压打渣机(400mm以下)→装载机→ 中式板矿给料机→1号颚式破碎机→鳞板输送机→2号颚式破 碎机→胶带输送机→卸料小车→铜锍仓 破碎后的铜锍粒径在25mm以下。吹炼渣和精炼渣也通 过该系统破碎后由汽车运至精矿仓的返料仓。 吹炼所需的块煤、石英石也储存在铜锍仓内,铜锍仓设 有抓斗桥式起重机,将铜锍、块煤、石英石分别抓至各自中 间配料仓中。配料区配置有4台定量给料机,两台用于铜锍 的配料;两台用于石英石、块煤的配料;配料后的物料通过 两台胶带输送机运输至熔炼主厂房吹炼工段。
火法熔炼步骤
熔炼:主要是造锍熔炼,其目的是铜精矿中的部分铁和其他金属氧化, 并与脉石和熔剂等造渣除去,产出适合吹炼所需要的冰铜。 吹炼:目的是进一步脱除冰铜中的硫、铁等杂质,回收精矿中的硫,获 取粗铜。 火法精炼:是利用杂质对氧的亲和力大于铜,而其又不溶于铜液等性质, 通过氧化造渣或挥发除去,获得纯度较高的阳极铜。 现代铜精矿冶金的通常步骤和工艺流程如下:
闪速熔炼 工艺
奥托昆普闪速熔炼是采用富氧空气或723~1273K的 热风作为氧化气体。在反应塔顶部设置了下喷型精 矿喷嘴。干燥的精矿和熔剂与富氧空气或热风高速 喷入反应塔内,在塔内呈悬浮状态。物料在向下运 动过程中,与气流中的氧发生氧化反应,放出大量 的热,使反应塔中的温度维持在1673K以上。在高 温下物料迅速反应(2~3s),产生的熔体沉降到沉淀 池内,完成造冰铜和造渣反应,并进行澄清分离。
步骤:铜精矿(含铜13-30%)→冰铜(含铜40——75%)→粗铜(含 铜98.5%)→阳极铜(含铜99.5%)→电解铜(含铜为99.99%)
工艺流程:铜精矿→熔炼→铜锍→吹炼→粗铜→火法精炼→阳极铜→电 解精炼→阴极铜
原则流程图
五、当今铜精矿火法冶金技术概述
当今火法冶金技术正朝着:短流程连续
4
2、铜的基本用途
在有色金属中,铜的产量和耗用量仅次于铝,居第 二位。在电器、输电和电子工业中用量最大,据统计, 世界上生产的铜,近一半消耗在电器工业中。军事上用 铜制造各种子弹、炮弹、舰艇冷凝管和热交换器以及各 咱仪表的弹性元件等。还可用来制作轴承、轴瓦、油管、 阀门、泵体,以及高压蒸汽设备、医疗器械、光学仪器、 装饰材料及金属艺术品和各种日用器具等。
铜 及 铜 合 金 在 电 气 、 机 械 制 造 行 业 、 航 空 及 军 工 业 的 应 用
6
三、炼铜原料概述
炼铜原料概述 生产电解铜(阴极铜)的原料分为铜精矿和废杂铜。用 铜精矿和废杂铜生产电解铜的比例约为7:3,铜精矿依然 是当今生产电解铜的主要原料。 铜精矿:在自然界中自然铜的含量极少,一般都以金属 共生矿的形态存在。铜矿石中常伴生有多种重金属和稀 有金属,如金、银、砷、锑、铋、硒、铅、钴、镍、钼 等。根据铜化合物的性质,铜矿物可分为自然铜、硫化 矿和氧化矿三种类型,主要以硫化矿和氧化矿,特别是 硫化矿分布最广,目前电解铜的90%左右来自硫化矿。 金银等贵金属常和铜共生。铜矿石经采矿和选矿富集获 得铜精矿,含铜13—30%。
炼铜、高富氧、底能耗、高效率、低碳冶金、 清洁生产、自动化、信息化、智能化方向发 展。
硫化铜精矿火法工艺熔炼方法 熔池熔炼方法 现代炼铜方法 漂浮熔炼方法 基夫赛特法
71
诺兰达法 瓦纽科夫法 白银法 奥斯麦特法 三菱法 闪速熔炼法 印柯法
工艺流程总述
我公司火法冶炼工艺采用富氧底吹造锍熔炼、铜锍底吹 吹炼、粗铜回转式阳极炉精炼工艺。工艺过程为湿精矿加入 氧气底吹熔炼炉自热熔炼产出72%的铜锍。经冷却破碎后的 铜锍由加料系统加入到吹炼炉中吹炼成粗铜,液态粗铜加入 到回转式阳极炉精炼并浇铸产出阳极送电解精炼。主要设备 有Φ4.8×20m氧气底吹炉一台,Φ4.4×20m 底吹连续吹炼 炉1台,Φ4.0×12.5m阳极炉2台。 液态熔炼渣和液态转炉 渣送缓冷渣场缓冷后送炉渣选矿车间用浮选法回收铜,产出 的渣精矿返回熔炼炉,渣尾矿外卖。熔炼炉和吹炼炉产出的 高温烟气经余热锅炉回收余热(产生的蒸汽用于发电),再 经电收尘器收尘后送硫酸车间制酸。阳极炉氧化期烟气经降 温除尘后送制酸系统,还原期含二氧化硫很少,经降温除尘 后和全厂环保通风的气体一起进行脱硫,脱硫装置采用活性 焦脱硫吸附解析装置回收二氧化硫,并将二氧化硫送制酸, 脱硫后的烟气通过120m的环保烟囱排放。
79.9
57.5 68.2 36.2 25.5
5.8-6.1
4.05 3.77 2.0-2.2 2.29
灰黑色
亮绿色 亮蓝色 蓝绿色 蓝色
矿物
四、铜精矿冶炼方法概述
铜冶金方法是指由铜精矿获取金属铜(火精铜或电 解铜)所采取的工艺技术途径和手段。铜精矿生产 电解铜的冶炼方法分为两大类:火法冶金和湿法冶 金。目前精炼铜产量的85%以上是用火法冶金从硫 化铜精矿和再生铜中回收的。 火法冶金是指在高温下应用冶金炉把铜精矿中的大 量脉石分离开,脱除各种杂质元素,提取纯金属铜 的方法。火法炼铜工艺一般都分为三段,第一段是 造锍熔炼,由铜精矿炼成含铜40-75%的铜锍(或称 冰铜),第二段是将铜锍炼成含铜98%以上的粗铜, 第三段是将粗铜精炼成阳极铜。
红色
灰黑色 红蓝色 黄色 红蓝色 灰黑色 灰黑色
硫化 矿物
黄铜矿 斑铜矿 硫砷铜矿 黝铜矿
铜的主要矿物
赤铜矿 Cu2O 88.8 7.14 红色
黑铜矿
氧化 孔雀石 蓝铜矿 硅孔雀石 胆矾
CuO
CuCO3· Cu(OH)2 2CuCO3· Cu(OH)2 CuSiO3· 2H2O CuSO4· 5H2O
铜的主要矿物
矿物 类别 矿物 名称 化学分子式 %Cu 密度/ g· cm-3 颜色
自然 矿物
自然铜
辉铜矿 铜蓝
Cu
Cu2S CuS CuFeS2 Cu4FeS4 Cu3AsS4 (Cu,Fe)12Sb4S13
100
79.8 66.7 34.6 63.5 49.0 25.0
8.9
5.5-5.8 4.6-4.7 4.1-4.3 5.06 4.45 4.6-5.1
工艺指标
火法冶炼系统的生产规模、产品、原料、燃料及辅助材料
1)、生产规模及产品 本项目规模为:年处理47万吨混合铜精矿(干基) 火法冶炼的产品:铜阳极板,产量为126722.58t/a,含铜99.0%,含金4.95g/t,含银 522.65g/t。 2)原料 原料为铜精矿。 3)燃料 (1)天然气 氧气底吹熔炼炉、底吹连续吹炼炉烘炉和保温采用天然气作为燃料。回转式阳极炉的烘 炉、保温和生产采用天然气为燃料,回转式阳极精炼炉还原期采用天然气作为还原剂。粗 铜排放溜槽和阳极铜浇铸溜槽的保温、浇铸中间包和浇铸包的烘烤等也采用天然气。 (2)块煤 底吹熔炼炉在精矿发生较大变化或调整渣型时,跟根据需要加入块煤。熔炼所需的块 煤,用汽车运至冶炼厂精矿仓储存。底吹吹炼炉为控制渣中Fe3O4的含量,也需配入少量 块煤。吹炼所需的 块煤,储存在主厂房吹炼炉顶应急块煤仓中。 本项目块煤用量约为2610 t/a,粒度要求不大于15mm 4)熔剂 底吹熔炼炉和吹炼炉采用石英石熔剂造硅渣。石英石外购,厂内不设熔剂破碎设施。本 项目石英石用量约为47043 t/a。 5)氧气 氧气底吹熔炼炉和底吹连续吹炼炉均采用富氧熔炼和吹炼,阳极炉采用稀氧燃烧技术, 熔炼用氧气量880848×103 Nm3/a,压力0.8Mpa;吹炼用氧量24225×103 Nm3/a,压力1.2 Mpa;精炼用氧5187×103 Nm3/a, 压力0.8Mpa。 6)耐火砖 氧气底吹熔炼炉和底吹连续吹炼炉、阳极炉和溜槽的内衬均为耐火材料砌筑。耐火材料由 厂方按照要求的数量、规格和类型,运至耐火材料库。 本项目耐火材料用量约为1450 t/