高分子材料成型加工技术的进展
高分子材料成型加工技术的进展分析

高分子材料成型加工技术的进展分析作者:侯春雨来源:《城市建设理论研究》2013年第20期【摘要】随着我国科学技术的不断发展,工业生产领域也有了突飞猛进的发展,而在工业生产领域中,对高分子材料成型加工技术的使用也使得工业生产获得了显著的发展。
本文主要针对高分子材料成型加工技术的进展进行了深入的分析和研究。
【关键字】高分子材料;成型加工技术;进展研究中图分类号:O63 文献标识码:A 文章编号:1前言近些年来,随着科学技术的不断发展,高分子材料在众多领域中被广泛的应用。
高分子材料主要是通过对商品的制造来凸显其价值所在。
就目前而言,高分子材料成型加工技术也越来越受到广泛的关注,因此,要想充分的利用高分子材料,就要对其成型加工进行深入的研究和探讨。
2高分子材料成型加工技术的发展状况近些年来,就高分子材料而言,其合成工业的发展有了很大的突破。
其中取得进步最大的就是造粒用挤出机,通过对其结构的改进,使得其产量有了很大的提高。
在20世纪60年代进行造粒主要采用的是单螺杆的结构挤出机,这样产量就相对较少;到了70年代到80年代的时候,有了一定的改善,主要采用的是连续混炼机和单螺杆挤出机相结合来进行造粒,这时的产量就有了一定的提高;在80年代中期之后,进行造粒主要采用的就是双螺杆挤出机和齿轮泵相结合的模式,这是的产量已经提升很大的一个高度;到了2010年的时候产量已经提升了3亿吨的产量。
除此之外,通过对高分子材料合成技术的应用,可以对树脂的分子结构进行简单明了的控制,因此可以进行大规模的生产运作,并且还可以有效的降低生产成本。
就目前而言,高分子材料的成型加工技术主要追求的就是提高生产率、提高使用性能以及降低生产升本。
而在制作的方面所追求的就是尺寸变小、质量变轻。
在加工成型方面,主要追求的就是研发的周期逐渐变短,而且要注重环保。
3对于高分子材料成型加工技术的研究探析3.1对聚合物的动态反应加工技术的探析聚合物的反应加工技术是通过对双螺杆挤出机的发展基础而逐渐发展起来的。
浅析高分子材料成型加工技术的发展

目标 , 研究 开发 出了结合已成型动态反应技 术的新 型连续化精密光盘注射成型设备 。
三、 高分子材料成型加工技术的发展 走向
近些年来 , 将科技转化 为成果和产业化 的转 型越 来越 受到 国家新型材料科研 中心 的关 注和重视 ,目前我国已经成功完成 了几 个五年计 划 中的一些重 点科技攻关项 目和 国家级的火炬计划预备项 目, 与此同时我 国 还完成了产业化工程的配套项 目数十项, 创 办 的华新 集 团所拥有 自主知识产权 的新技 术和装 备在 国内外 的推广也得 到了业界 的 致好评 。近几年来 ,塑料动态塑化设备 已 经在我国基本普及 , 在 三 十多个省 市及 自 治 区进行 推广应 用, 使用总量超过 了一千 台, 其销售额 已达 数亿 , 部分 的新设备更是销往泰国和荷兰等 国家并产生 了良好的经济与社会效益 。 例如 广东在 2 0 0 0年及其后一年 的两年时间里仅 靠P E电磁动态发泡片材这种制品就为 国家 节省下约一 一 千六百万美元 的外汇 , 其制品厂 的每条生产线一年都可以省下电费近 2 1万 k 。塑料电磁动态注塑机 已将开发完善的五 个规格 系列投入了批量生产并推向市场 ; 塑 料 电磁动 态混炼 挤出机 的其 中 四个规 格 已 经 完成 了中间 阶段的 试验及产业化 的工作 并以投人生产和应用。聚合物新型成型装备 国家工程 研究 中心将技 术和资本相结 合并 引入 了新的管理模式和市场机制 , 以此来进 行 了广州华新科机械有 限公司的重组 , 在近 几年 的销售额意图突破亿元销售额大关 。 综上所述 , 要想促进产业界和科学研究 的有机结合 , 加快我国高分子材料成 型加工 高新技术 及其产 业的发展 步伐和成果 转化 为生产力 的进程 , 就必须要 突破 国外的技术 封锁 防线 , 充分发挥主观能动性掌握有着我 国 自主知识产权 的先进 技术 ,实现质 的跨 越。
基于拉伸流变的高分子材料绿色加工成型新技术

基于拉伸流变的高分子材料绿色加工成型新技术
随着环保意识的不断提高,绿色加工成型技术在高分子材料领域中越来越受到关注。
拉伸流变是一种基于流变学原理的新型加工成型技术,其操作简单、效率高、成型精度高等优点,使其成为高分子材料绿色加工成型的新技术。
拉伸流变技术是通过在高分子材料中施加拉伸力的同时,利用材料的流变特性,在材料内部形成一定的流动状态,从而实现材料的加工成型。
该技术不需要使用任何有害的化学物质或高温高压条件,具有很好的环保性。
在实际应用中,拉伸流变技术可以用于制备各类高分子材料制品,例如薄膜、管材、棒材等。
该技术不仅可以减少制造成本,提高生产效率,还能够大幅降低废品率,实现生产过程的可持续发展。
目前,拉伸流变技术已经在高分子材料领域中得到广泛应用,并成为该领域中的一种重要绿色加工成型技术。
未来,该技术还将继续发展,并在更广泛的领域中得到应用,推动高分子材料绿色加工成型技术的不断进步。
- 1 -。
我国医用高分子材料的发展现状

四、应用场景
1、医疗器械:医用高分子材料被广泛应用于医疗器械的生产,如人工关节、 人工晶体、手术缝合线等。
四、应用场景
2、药物载体:医用高分子材料可以作为药物载体,实现药物的定向传输和控 释,提高药物的治疗效果和降低副作用。
四、应用场景
3、组织工程:医用高分子材料可以作为组织工程的支架材料,辅助机体组织 的再生和修复。
六、总结
六、总结
我国医用高分子材料产业的发展迅速,已经成为全球医用高分子材料的重要 生产国之一。虽然我国在一些关键技术方面与国际先进水平存在差距,但国内企 业正在努力加强技术创新和自主研发,不断提高产品的质量和性能。预计未来几 年,我国医用高分子材料的市场需求将继续增长,同时企业的技术创新和绿色环 保意识也将不断提升。
3、加工成型技术
3、加工成型技术
加工成型技术是医用高分子材料产业的重要组成部分,涉及到产品的形状、 尺寸和性能等方面。我国企业在加工成型技术方面已经有了较为成熟的生产线和 技术人才,但在高端产品的加工成型技术方面仍存在一定差距。
四、应用场景
四、应用场景
医用高分子材料在医疗领域的应用非常广泛,主要包括以下几个方面:
谢谢观看
2、绿色环保
2、绿色环保
随着环保意识的不断提高,医用高分子材料的绿色环保已经成为未来发展的 重要趋势。需要采用环保材料和环保生产工艺,实现医用高分子材料的可降解和 可回收利用,减少对环境的污染。
3、个性化定制
3、个性化定制
随着医疗水平的提高和患者需求的多样化,医用高分子材料的个性化定制已 经成为未来的发展趋势。需要加强技术研发和生产工艺的改进,实现医用高分子 材料的个性化定制,满足不同患者和医疗需求。
一、发展历程
高分子材料的加工成型技术

高分子材料的加工成型技术摘要:在现代社会发展潮流中,高分子材料的成型加工技术受到了社会各界人士的高度关注,且应用范围也在不断的扩展延伸。
鉴于此,深入分析高分子材料的加工成型技术以及应用,可以帮助我国研究成员更好的探究该领域的内容,促使高分子材料成型加工技术与各行业进行充分融合。
关键词:高分子材料;加工成型;技术应用引言随着聚合物在很多重要行业中的应用越来越广泛,在保证其经济性的基础上,我们应该加强聚合物成形工艺的研发,以确保其在生产成本和时间上的良好应用,促进国家的繁荣。
1.高分子材料的概述1.1高分子材料的分类高分子材料有很多种,橡胶,塑料,纤维,粘合剂,涂料等都在这一范畴之中,该种材料在很多领域都有很大的用途。
高分子又称为聚合物质,通过多次使用共价键联,将不计其数的简单相同的结构单位反复组合而形成。
目前,关于聚合物的种类有很多种,根据原料的种类划分,可以将其划分为自然物质和人造物质。
根据物料性质可分为橡胶、纤维、塑料、粘合剂、涂料等;根据用途的不同,可以将其划分为:普通高分子材料、特种高分子材料、功能性高分子材料。
当前,聚合物在建筑、交通、家电、工农业、航空等领域得到了越来越多的应用,并逐渐朝着功能化、智能化、精细化方向发展。
而国内在此领域的发展和科研工作起步较迟,亟需加强技术创新,加强技术人员培训,使聚合物成形工艺水平持续提升,才能走在国际前沿。
1.2高分子材料的成型性能在不同的物理条件下,聚合物的特性差异很大,所以在对聚合物的成形特性进行分析时,必须对聚合物的溶质特性有一定的认识。
已有的实验结果显示,非晶体聚合物的主要形态有玻璃态、高弹态、粘性态三种形态,但多数晶体物质仅有两种形态,即晶态和粘性态。
玻璃态、高弹态和晶体态是物料成形后所采用的形态,而粘流态则是物料在处理时所表现出的形态,不过,也有一些聚合物在高弹状态下完成处理加工作业。
聚合物的制造工艺一般是将聚合物材料制成熔化,放入模具和流动通道中,再经过降温再进行定型,从而使聚合物具有良好的流变性。
高分子材料的合成与加工技术

高分子材料的合成与加工技术高分子材料在现代工业中扮演着重要的角色,它广泛应用于塑料制品、聚合物纤维、复合材料等领域。
高分子材料的合成与加工技术是实现其广泛应用的关键。
在本文中,我们将探讨高分子材料的合成方法和加工技术的发展与应用。
一、高分子材料的合成高分子材料的合成方法主要包括聚合反应和共聚反应。
聚合反应是指通过将单体分子基团进行化学反应,使它们形成长链高分子结构。
常见的聚合反应包括链聚合、环聚合和交联聚合。
链聚合是通过将单体分子中的功能基团进行化学反应,使它们依次连接起来形成高分子链。
环聚合是指通过环状单体分子之间的聚合反应形成高分子环。
交联聚合是指通过将单体分子中的交联剂进行反应,使高分子链之间形成交联结构。
共聚反应是指将两种或多种不同的单体进行聚合反应,形成具有不同结构和性质的高分子材料。
共聚反应可以改变高分子材料的特性,提高其耐热性、耐化学性等。
二、高分子材料的加工技术高分子材料的加工技术主要包括注塑、挤出、吹塑、压延、反应成型等方法。
这些方法可以将高分子材料加工成塑料制品、聚合物纤维和复合材料等产品。
注塑是将高分子材料经过熔融后,通过注射到模具中,在模具中冷却固化成为塑料制品的一种方法。
注塑技术广泛应用于制造各种塑料制品,如玩具、包装材料等。
挤出是将高分子材料经过熔融后,通过挤出机将其挤压成所需的形状的一种方法。
挤出技术用于制造塑料制品、塑料管材等。
吹塑是将高分子材料经过熔融后,通过吹塑机将其吹出成空心物品的一种方法。
吹塑技术广泛应用于生产塑料瓶、塑料容器等。
压延是将高分子材料经过加热软化后,通过压延机将其进行双辊挤压成片状的一种方法。
压延技术用于生产塑料片材、塑料薄膜等。
反应成型是将高分子材料在模具中经过反应后形成所需的形状和结构的一种方法。
反应成型技术可以制备具有特殊性能的高分子材料制品。
三、高分子材料的发展与应用随着科学技术的发展,高分子材料的合成与加工技术也在不断创新和改进。
近年来,研究人员致力于开发环保型高分子材料和高性能高分子材料。
高分子材料成型加工技术研究

料 ;主 要 是橡 胶 、塑 料 、纤 维 、涂 料 、胶 黏 剂和 高分 子 基复 合 材 料 。 高 分子材 料 独特 的结 构和 易 改性 与易 加工特 点 ,使 它具 有其 他材 料 不
可 取代 与不 可比 拟 的优 异性能 ,从 而 广泛运 用 到科 学技 术 、国 防建 设
和 国 民经济 等领 域 ,并 已成 为现 代社 会生 活 中衣 食住 行用 等各 方面 不
可 缺少 的材料 。
1 . 聚合物 动态反应 加工技 术 聚 合物 动态 反应 加工 技术 及 设备 与传统 技 术无 论是 在反 应 加 工原 理还 是设 备 的结构 上 都完全 不 同 ,该技 术是 将 电磁场 引起 的 机械 振动 场 引入聚 合物 反应 挤 出全过 程 ,达 到控 制化 学反 应过 程 、反 应生 成物 的凝 聚态 结构和 反应 制 品的物理 化学 性能 的 目的 [ 3 】 。这项 技 术解 决振 动 力场 下 聚合 反应 加 工过 程 中质 量 、动 量和 能 量传 递 与 平衡 的 难 点 , 从技 术上解 决了 设备结构 集化 的问题 。 2 . 热塑 性弹性 体动态 全硫化 制备技 术
技术 方法 。
1 . 挤 出成 型技术
型 装 备 ,达 到 有效 提高 产 品质量 、节 约能 源 ,降 低消 耗的 目的 。该技 术 避免 了 传统 方式 中 间环节 多 、能耗 大 、周期 时 间长 、成 型前 处 理复 杂 、储运 过程 易受污 染等缺 陷。
3 . 吹塑成 型技术
近些 年来 ,国防 尖端 工业 和航 空工 业 等特殊 领 域的 发展 要求 更 高 性 能 的 聚合 物 材 料 ,开 发研 制 满 足特 定 要 求 的 高聚 合 物 迫 在 眉 睫n I 。
高分子材料成型加工中的自动化生产技术
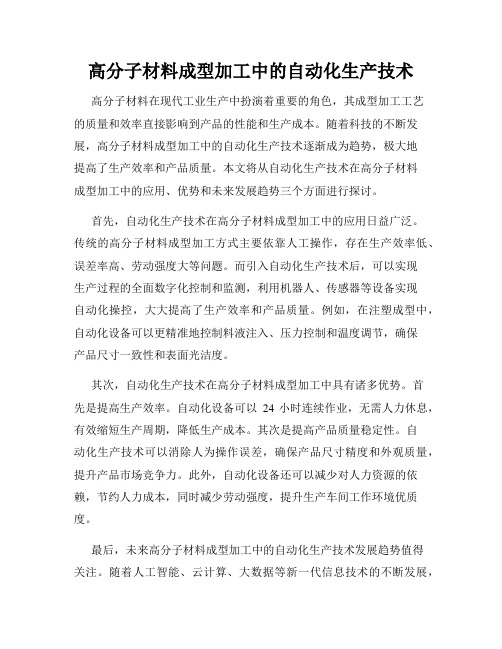
高分子材料成型加工中的自动化生产技术高分子材料在现代工业生产中扮演着重要的角色,其成型加工工艺的质量和效率直接影响到产品的性能和生产成本。
随着科技的不断发展,高分子材料成型加工中的自动化生产技术逐渐成为趋势,极大地提高了生产效率和产品质量。
本文将从自动化生产技术在高分子材料成型加工中的应用、优势和未来发展趋势三个方面进行探讨。
首先,自动化生产技术在高分子材料成型加工中的应用日益广泛。
传统的高分子材料成型加工方式主要依靠人工操作,存在生产效率低、误差率高、劳动强度大等问题。
而引入自动化生产技术后,可以实现生产过程的全面数字化控制和监测,利用机器人、传感器等设备实现自动化操控,大大提高了生产效率和产品质量。
例如,在注塑成型中,自动化设备可以更精准地控制料液注入、压力控制和温度调节,确保产品尺寸一致性和表面光洁度。
其次,自动化生产技术在高分子材料成型加工中具有诸多优势。
首先是提高生产效率。
自动化设备可以24小时连续作业,无需人力休息,有效缩短生产周期,降低生产成本。
其次是提高产品质量稳定性。
自动化生产技术可以消除人为操作误差,确保产品尺寸精度和外观质量,提升产品市场竞争力。
此外,自动化设备还可以减少对人力资源的依赖,节约人力成本,同时减少劳动强度,提升生产车间工作环境优质度。
最后,未来高分子材料成型加工中的自动化生产技术发展趋势值得关注。
随着人工智能、云计算、大数据等新一代信息技术的不断发展,自动化生产设备将变得更加智能化、柔性化和高效化。
例如,智能化的自动化生产线可以实现远程监控和智能诊断,提前发现并排除生产故障,实现生产过程的智能优化。
另外,柔性化的自动化生产设备可以根据不同产品的要求进行快速转换,适应多品种、小批量生产需求。
综上所述,高分子材料成型加工中的自动化生产技术已经成为未来发展的必然趋势,其在提高生产效率、产品质量稳定性和未来发展趋势方面发挥着重要作用。
未来,随着新一代信息技术的不断融合,自动化生产技术将迎来更加广阔的发展空间,为高分子材料产业的可持续发展提供有力支撑。
- 1、下载文档前请自行甄别文档内容的完整性,平台不提供额外的编辑、内容补充、找答案等附加服务。
- 2、"仅部分预览"的文档,不可在线预览部分如存在完整性等问题,可反馈申请退款(可完整预览的文档不适用该条件!)。
- 3、如文档侵犯您的权益,请联系客服反馈,我们会尽快为您处理(人工客服工作时间:9:00-18:30)。
2008年第9期广东化工第35卷总第185期 · 3 ·高分子材料成型加工技术的进展吴刚(广东省石油化工建设工程质量监督站,广东广州 510034)[摘 要]讨论了塑料成型加工技术的现状,介绍了挤出、注塑、吹塑、压延等典型的塑料成型加工工艺原理与技术特点,综述了高分子材料成型加工技术的新进展。
[关键词]塑料;成型;发展[中图分类号]TB324 [文献标识码]A [文章编号]1007-1865(2008)09-0003-04Progress of Plastics Molding TechnologyWu Gang(Guangdong Provincial Petro-chemical Construction Quality Supervision Station, Guangzhou 510034, China)Abstract: The paper introduced the current technology of plastics molding, briefly described the principles and characteristics of the typical processes like extruding, molding, blowing, dusting etc, and the development trend of plastics molding technology was reviewed.Keywords: plastics;molding;development;review随着工业化技术的发展和人民生活水平的提高,人们对塑料产品种类和质量的需求也越来越高。
高分子材料是通过制造成各种制品来实现其使用价值的,因此从应用角度来讲,以对高分子材料赋予形状为主要目的成型加工技术有着重要的意义。
高分子材料的主要成型方法有挤出成型、注射成型、吹塑成型、压延成型等,文章综述了高分子材料成型加工技术的最新进展。
1 挤出成型挤出成型主要是利用螺杆旋转加压方式,连续地将塑化好的成型物料从挤出机的机筒中挤入机头,熔融物料通过机头口模成型为与口模形状相仿的型坯,用牵引装置将成型制品连续地从模具中拉出,同时进行冷却定型,制得所需形状的制品。
挤出成型主要包括加料、塑化、成型、定型等过程。
要获得外观和内在质量均优良的型材制品,是与原材料配方、挤出设备水平、机头模具设计与加工精度、型材断面结构设计及挤出成型工艺条件等分不开的。
挤出成型工艺参数的控制包括成型温度、挤出机工作压力、螺杆转速、挤出速度、牵引速度、排气、加料速度及冷却定型等。
挤出工艺条件又随挤出机的结构、塑料品种、制品类型、产品的质量要求等的不同而改变[1]。
1.1 共挤出技术共挤出技术是用两台或者两台以上单螺杆挤出机或双螺杆挤出机将两种或多种聚合物同时挤出并在一个机头中成型多层板式或片状结构等的一步法加工过程。
共挤出技术避免了传统的高代价且复杂的多步层压或涂层工艺,可容易地成型为具有特殊性能的薄层或超薄层,使之具有着色、遮蔽紫外线、提供阻隔性、控制薄膜表面特性等,也可方便地将各种添加剂如抗结块剂、抗滑移剂和抗静电剂等加入到需要的任何一层。
[收稿日期]2008-05-14[作者简介]吴刚(1956-),男,山东人,本科,高级工程师,主要从事石油化工建设工程质量监督工作。
广东化工 2008年第9期· 4 · 第35卷总第185期按照共挤物料的特性,可将共挤出技术分为软硬共挤、芯部发泡共挤、废料共挤、双色共挤等。
共挤出技术可以在一个工序内完成多层复合制品的挤出成型,绝大多数共挤出复合制品不需要基材和粘合剂,具有生产成本低、工艺简单、能耗低、生产效率高、制品种类多等特点,特别适合于生产复合薄膜、板材、管材等复合制品,是目前多层复合制品最有发展前景的复合成型技术之一,可供共挤出的物料不仅有聚合物,还可以是金属、无机材料等。
共挤出技术是当代广泛应用的先进的聚合物加工方法,共挤出技术已广泛应用于复合管材、复合薄膜、板材、异型材、光纤、电线、电缆等复合制品的生产,随着共挤出技术的发展,其应用领域会进一步拓宽。
多层共挤复合机头是研究和开发的热点,也是共挤复合研究的难点。
开发高效、节能的多层结构单机共挤出设备是共挤出设备的发展趋势[2]。
1.2 挤出注射组合技术挤出和注射成型组合的直接成型技术可将聚合物粉料与磁粉、无机颜料、玻璃纤维等通过双螺杆挤出机混合后直接注塑成型。
其突出优点是可以更加灵活地调节复合物的配方。
省去了造粒、包装、干燥等工序,大幅度地降低了设备费用和减少了生产时间、从而降低了成品的成本。
Krauss Mallei公司推出了型号KMl000-6100IMC的这种组合设备,一个特殊的注射装置与双螺杆挤出机相结合代替了传统的塑化单元,计量器将连续操作的挤出机和间歇操作的成型装置连接在一起。
Husky公司也推出了与阳模相连的Operion Werner & Pfleiderer 40 m双螺杆的挤出注射组合机。
该技术适用于多种材料的成型,即可为单个的聚合物,如ABS、AS、EV A、PA、PC、PE、PET、PBT、POM、PP、PS、PMMA、LCP等;也可为复合材料,如聚合物与玻璃纤维(GF)、CaCO3、云母、滑石粉、硅石、颜料、Fe2O3的混合物;还可为聚合物合金。
如ABS、AS、PS、PVC、SAN合金;PA/HDPE、PBT、PET合金及PC/ABS、PET、PBT合金等。
1.3 成型技术挤胀成型技术是一种塑性成型方法,主要适用于加工细口制件或一些较复杂的中空制品,这些制品通常是采用旋转模塑、注塑或吹塑方法成型的。
其基本过程是:预成型的管坯在组合外力的作用下沿径向外扩张,通过塑性变形形成与模具型腔相一致的制品。
挤胀成型的基本工艺过程为:将管坯放入模具并在管坯内填入胀形介质;对管坯及其内部的胀形介质施加挤压力,使管坯材料在一定的应力状态下变形并流向其径向的模腔自由空间;管坯在胀形介质产生的内压作用下不断变形,得到与模腔形状相同的制件;外力撤消后,胀形介质恢复原状或散开,从制品内部取出[3]。
挤胀成型技术出现于20世纪40年代的金属成型加工领域,虽然没有在塑料加工领域获得广泛的应用,但与常规的塑料成型技术相比,这种方法具有以下特点:成型设备结构相对简单,成型模具的结构简洁;被加工材料不产生相变而且成型过程通常都是在较低温度下进行,能耗低;控制系统比较简单,工艺控制十分灵活,通过控制挤胀行程,利用同一副模具有可能得到不同尺寸的制品;能充分利用挤出制型坯的高生产率和低成本;在生产批量较小的情况下能大幅度降低生产成本。
1.4 反应挤出工艺反应挤出工艺是连续地将单体聚合并对现有聚合物进行改性的一种方法,因可以使聚合物性能多样化、功能化且生产连续、工艺操作简单和经济适用而普遍受到重视。
该工艺的最大特点是将聚合物的改性、合成与聚合物加工这些传统工艺中分开的操作联合起来。
反应挤出成型技术是可以实现高附加值、低成本的新技术,已经引起世界化学和聚合物材料科学与工程界的广泛关注,在工业方面发展很快。
与原有的成型挤出技术相比,有明显的优点:节约加工中的能耗;避免了重复加热;降低了原料成本;在反应挤出阶段,可在生产线上及时调整单体、原料的物性,以保证最终制品的质量。
反应挤出机是反应挤出的主要设备,一般有较长的长径比、多个加料口和特殊的螺杆结构。
它的特点是熔融进料预处理容易;混合分散性和分布性优异;温度控制稳定;可控制整个停留时间分布;可连续加工;未反应的单体和副产品可以除去;具有对后反应的控制能力;可进行粘流熔融输送;可连续制造异型制品。
1.5 固态挤出工艺固态挤出有直接固态挤出和静液压挤出两种方法,是指使聚合物在低于熔点的条件下被挤出口模。
固态挤出一般使用单柱塞挤出机,柱塞式挤出机为间歇性操作。
柱塞得移动产生正向位移和非常高的压力,挤出时口模内的聚合物发生很大的变形,使得分子严重取向,其效果远大于熔融加工,从而使得制品的力学性能大大提高。
2 注射成型技术注射成型技术是目前塑料加工中最普遍的采用的方法之一,可用来生产空间几何形状非常复杂的塑料制件。
由于它具有应用面广、成型周期短、花色品种多、制件尺寸稳定、产品效率高、模具服役条件好、塑料尺寸精密度高、生产操作容易、实现机械化和自动化等诸方面的优点。
因此,在整个塑料制件生产行业中,注射成型占有非常重要的地位。
目前,除了少数几种塑料品种外,几乎所有的塑料(即全部热塑性塑料和部分热固性塑料)都可以采用注塑成型。
注射成型技术的发展主流一般以多种方式的组合为基础,具有如下技术特征:(1)以组合不同材料为特征的注射成型方法,如镶嵌成型、夹心成型、多材质复合成型、多色复合成型2008年第9期广东化工第35卷总第185期 · 5 ·等;(2)以组合惰性气体为特征的注射成型方法,如气体辅助注射成型、微孔泡沫塑料注射成型等;(3)以组成化学反应过程为特征的注射成型方法,如反应注射成型、注射涂装成型等;(4)以组合压缩或压制过程为特征的注射成型方法.如注射压缩成型、注射压制成型、表面贴合成型等;(5)以组合混合混配为特征的注射成型方法,如直接(混配)注射成型等;(6)以组合取向或延伸过程为特征的注射成型方法,如磁场成型、注拉吹成型、剪切场控制取向成型、推拉成型、层间正交成型等;(7)以组合模具移动或加热等过程为特征的注射成型方法,如自切浇口成型、模具滑合成型、热流道模具成型等。
2.1 辅助注塑技术2.1.1 气体辅助注射成型气体辅助注塑GAIM 技术比普通注塑多一个气体注人阶段,由气体推动塑料熔体充满模具型腔。
GAIM具有节省原料、减少合模力、缩短冷却时间、防止制品缩痕、减少内应力、减少或消除制品翘曲、提高制品表面性能、提高生产效率、降低生产成本等优点。
气体辅助注射成型近年来发展较快,国外很多公司相继开发了具有不同特征的新方法,如日本旭化成公司的AGI法、三菱工程塑料公司的CINPRES法及出光石油化学公司的GIM 法等,但各方法的基本原理完全相同。
气体辅助注射成型的工作过程可分为四个阶段:第一阶段为熔体注射,即将熔融的塑料熔体注射到模具型腔中,分为“欠料注射”和“全料注射”。
第二阶段为气体注射,可于注射期的前、中、后期注入气体,气体的压力必须大于塑料熔体的压力以达到使塑件成中空状态。
第三阶段为气体保压当塑件内部被气体充填后,制件在保持气压的情况下冷却,气体由内向外施压使制品外表面紧贴模壁,通过气体二次穿透从内部补充因冷却带来的体积收缩。
第四阶段为制件脱模,随着冷却周期的完成,排出气体,塑件由模腔取出。