钢制车轮行业状况分析
2024年镁合金轮毂市场发展现状

镁合金轮毂市场发展现状1. 引言镁合金轮毂作为一种重要的汽车零部件,具有重量轻、强度高、耐腐蚀等优点,在汽车制造业得到了广泛应用。
本文旨在探讨当前镁合金轮毂市场的发展现状,分析市场规模、发展趋势和主要的影响因素。
2. 市场规模根据市场研究数据,镁合金轮毂市场在近几年保持了快速增长的势头。
目前全球镁合金轮毂市场规模已达到 X 亿美元,预计未来几年将继续保持较高的增长率。
3. 市场发展趋势3.1 技术升级随着汽车工业的发展,对轮毂产品的要求也在不断提高。
未来,镁合金轮毂市场将面临技术升级的需求,包括提高强度、减少重量、改善表面处理等方面。
这将推动镁合金轮毂市场进一步发展。
3.2 新能源汽车市场的崛起新能源汽车市场的迅速崛起也影响着镁合金轮毂市场的发展。
新能源汽车对轮毂的需求更为苛刻,要求轮毂具备更高的强度和更轻的重量。
因此,随着新能源汽车市场的扩大,镁合金轮毂市场也将迎来更大的发展机遇。
3.3 环保意识的增强近年来,环保意识逐渐提高,对于汽车的环保性能要求越来越高。
镁合金轮毂具有较低的碳排放量,逐渐成为环保理念推动下的首选。
因此,环保意识的增强也将促进镁合金轮毂市场的发展。
4. 市场竞争格局目前,镁合金轮毂市场竞争激烈,市场上存在许多厂家和品牌。
主要的竞争策略包括产品质量和性能的改进、价格的竞争以及品牌宣传和营销活动等。
在市场竞争格局中,部分知名品牌厂商占据主导地位,但也有一些中小企业通过技术创新和差异化经营取得了一定的竞争优势。
5. 市场挑战与机遇虽然镁合金轮毂市场前景广阔,但也面临一些挑战。
其中主要包括原材料价格波动、生产成本增加和竞争压力加大等。
然而,对于抓住市场机遇和应对市场挑战,企业可以通过技术创新、产品优化和市场定位等方式来提高竞争力,并取得更好的市场表现。
6. 总结镁合金轮毂市场作为汽车零部件市场的重要组成部分,具有广阔的发展前景。
在技术升级、新能源汽车市场崛起和环保意识增强的推动下,镁合金轮毂市场将保持快速增长。
钢制车轮行业投资与发展前景分析
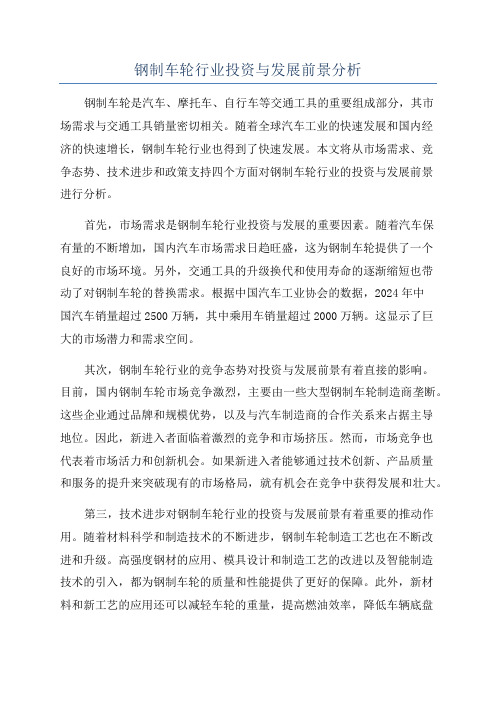
钢制车轮行业投资与发展前景分析钢制车轮是汽车、摩托车、自行车等交通工具的重要组成部分,其市场需求与交通工具销量密切相关。
随着全球汽车工业的快速发展和国内经济的快速增长,钢制车轮行业也得到了快速发展。
本文将从市场需求、竞争态势、技术进步和政策支持四个方面对钢制车轮行业的投资与发展前景进行分析。
首先,市场需求是钢制车轮行业投资与发展的重要因素。
随着汽车保有量的不断增加,国内汽车市场需求日趋旺盛,这为钢制车轮提供了一个良好的市场环境。
另外,交通工具的升级换代和使用寿命的逐渐缩短也带动了对钢制车轮的替换需求。
根据中国汽车工业协会的数据,2024年中国汽车销量超过2500万辆,其中乘用车销量超过2000万辆。
这显示了巨大的市场潜力和需求空间。
其次,钢制车轮行业的竞争态势对投资与发展前景有着直接的影响。
目前,国内钢制车轮市场竞争激烈,主要由一些大型钢制车轮制造商垄断。
这些企业通过品牌和规模优势,以及与汽车制造商的合作关系来占据主导地位。
因此,新进入者面临着激烈的竞争和市场挤压。
然而,市场竞争也代表着市场活力和创新机会。
如果新进入者能够通过技术创新、产品质量和服务的提升来突破现有的市场格局,就有机会在竞争中获得发展和壮大。
第三,技术进步对钢制车轮行业的投资与发展前景有着重要的推动作用。
随着材料科学和制造技术的不断进步,钢制车轮制造工艺也在不断改进和升级。
高强度钢材的应用、模具设计和制造工艺的改进以及智能制造技术的引入,都为钢制车轮的质量和性能提供了更好的保障。
此外,新材料和新工艺的应用还可以减轻车轮的重量,提高燃油效率,降低车辆底盘质量,同时也能提升乘坐舒适度和通过能力。
因此,钢制车轮行业的投资和发展将会得到技术进步的推动,从而获得更多的发展机遇和市场份额。
最后,政策支持也是钢制车轮行业投资与发展前景的重要因素。
国家在产业政策、质量标准和环保要求上给予了一定的支持和指导。
例如,《汽车轮辋及其附件产品质量安全基本要求》和《汽车轮辋及其附件定点生产企业准入资格管理规定》等文件明确了钢制车轮的生产标准和准入要求。
我国胎圈钢丝行业概况研究

我国胎圈钢丝行业概况研究(一)行业发展概况1、轮胎行业概况(1)轮胎行业简介世界轮胎工业发展至今已有160多年历史。
作为汽车工业的上游行业,轮胎产业随着汽车工业的发展而持续发展,新车市场的发展与汽车保有量的不断增加,为轮胎产业的发展提供了原动力。
从全球市场看,目前世界轮胎产业已发展成为一个规模庞大、高度发达的产业,并已进入相对稳定的发展时期。
世界轮胎行业高度集中度,根据美国《轮胎商业》统计的2016 年度全球轮胎75 强排行榜,销售额超过百亿美元的企业有普利司通、米其林、固特异和大陆4 家,2015 年合计销售额717.55 亿美元,占全球轮胎销售额1,601.35 亿美元的44.81%。
这些主要厂商具备雄厚的资金实力和研发能力,引领着世界轮胎行业的发展方向。
中国轮胎工业发展迅速。
在1950 年前,轮胎年产量不足3 万条;到1980 年,轮胎产量已达到1,146 万条;2005 年,中国轮胎产量达到2.5 亿条,超过美国的2.28 亿条,成为世界第一轮胎生产大国。
如今,我国已经成为全球轮胎最大的消耗国,也是最大轮胎生产国和出口国。
我国轮胎企业的国际地位也在逐年上升。
2006 年全球轮胎75 强排名中,中国大陆有17 家企业上榜;2016 年度全球轮胎75 强排名中,中国大陆有30 家企业上榜,其中排名最高的中策橡胶位列第10 名。
国家有关部门近年来出台了一系列的方针政策,为轮胎工业的发展指明了方向。
2010 年9 月,国家工业和信息化部出台了“轮胎产业政策”,“促进资源向优势企业集中,促进企业向集团化发展,提高产业集中度,优化组织结构;引导生产企业集聚发展,优化布局结构;加快淘汰落后生产能力,推动产品结构调整和优化升级……鼓励轮胎生产企业提高自主研发能力,加大研发投入,开展技术创新,实施品牌战略,提高产品技术水平,提高企业核心竞争力”,并从产品调整、技术政策、配套条件建设等方面提出指导意见。
我国轮胎企业自主创新意识逐步增强,产学研合作愈发活跃。
汽车行业用钢发展历程及现状

汽车行业用钢发展历程及现状随着工业革命的到来,汽车行业迅猛发展,而钢材作为一种重要的材料,在汽车制造中起到了举足轻重的作用。
本文将从汽车行业用钢的发展历程和现状两个方面进行探讨。
一、发展历程自汽车问世以来,钢材作为主要的结构材料广泛应用于汽车制造中。
早期的汽车主要采用铸铁和木材,但铸铁重量大、生产成本高,而且容易生锈;木材则不足以满足汽车的高强度和安全要求。
因此,逐渐发展出了以钢材为主的汽车制造工艺。
20世纪初,钢铁工业的迅猛发展为汽车行业提供了坚实的基础。
随着冷轧带钢、汽车用高强度钢的涌现,汽车重量得以大幅降低,同时还提升了汽车的安全性和燃油效率。
在20世纪30年代,汽车行业普遍开始采用冷轧带钢制作车身,为汽车的轻量化发展奠定了基础。
20世纪80年代,汽车行业迎来了进一步的发展。
高性能钢材的研发和应用使得汽车的安全性、耐久性和可靠性得到了极大提升。
此外,新材料的应用也为汽车产品提供了更多的选择,汽车行业开始逐渐采用铝合金、高强度钢、复合材料等新材料。
这些新材料不仅具有良好的机械性能,还能够降低车身重量,提高燃油效率。
二、现状分析当前,全球汽车行业已经进入了一个全新的发展阶段。
为了应对全球气候变化和环境污染问题,各国政府陆续出台了严格的排放标准和能源消耗限制,这对汽车行业用钢提出了新的要求。
首先,轻量化仍然是汽车行业用钢的主要发展趋势。
汽车制造商通过采用高强度钢材、铝合金和复合材料等轻量化材料来降低车身重量,提高燃油效率和减少排放。
其次,钢材的材质优化成为新的研究热点。
汽车行业要求钢材在保证强度和安全性的基础上,还要具备良好的可塑性和韧性。
因此,汽车用钢的研发中,注重材质优化,以满足汽车行业对不同零部件的要求。
此外,随着新能源汽车的快速发展,汽车行业用钢也面临着新的挑战与机遇。
电动汽车对车身结构和用钢材料的要求不同于传统燃油车,需要更高的强度和轻量化材料,以满足电动汽车高性能的要求。
综上所述,汽车行业用钢经历了漫长的发展历程,从最初的铸铁和木材到现在的冷轧带钢、高强度钢和新材料的应用,不断追求轻量化、高强度和高安全性。
汽车钢制车轮行业的现状和趋势
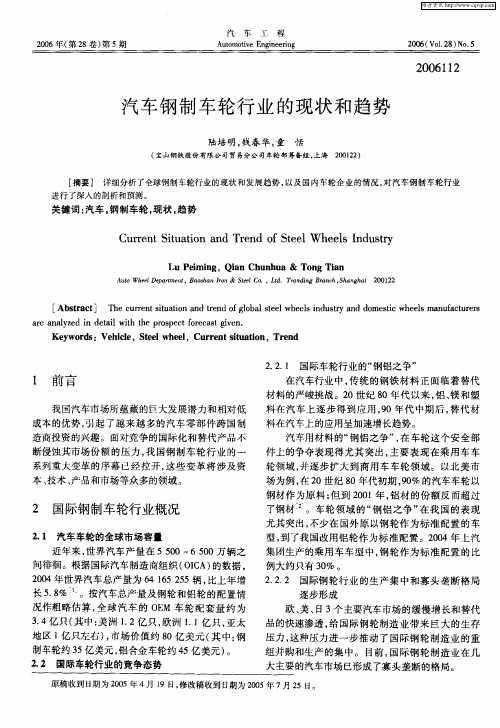
况作粗略估算 , 全球 汽车 的 O M 车 轮配套量 约为 E 34亿只( . 其中: 美洲 12亿 只, . 欧洲 11 . 亿只 , 亚太
地区 1 亿只左右 ) 市场价值约 8 , 0亿美元 ( 中: 其 钢 制车轮约 3 亿美元 , 5 铝合金 车轮约 4 5亿美元) 。 22 国际车轮行业的竞争态势 .
2 国际钢制车轮行业概况
21 汽车车轮的全球市场容量 .
近年 来 , 界 汽车 产 量 在 550—650万 辆 之 世 0 0
间徘徊。根据国际汽车制造商组织 ( IA 的数据 , OC ) 2 0 年世界汽车总产量为 6 6 5 04 41525辆 , 比上年增 长 5 8 。按汽车总产量及钢轮和铝轮的配置情 .%
在汽车行业中 , 传统 的钢铁材料正面临着替代 材料的严峻挑战。2 0世纪 8 0年代 以来 , 、 和塑 铝 镁
料在汽车上逐步得到应用 ,0年 代中期后 , 9 替代材 料在汽车上的应用呈加速增长趋势 。
汽车用材料的“ 钢铝之争” 在车轮这个 安全部 , 件上的争夺表现得尤其突出, 主要表现在乘用车 车 轮领域 , 并逐步扩大到商用车车轮领域。以北美市 场为例 , 2 在 0世纪 8 0年代初期 , % 的汽车车轮以 9 0 钢材作为原料 ; 但到 2 0 年 , 0 1 铝材的份额反而超过 了钢材 。 。车轮领域 的“ 钢铝 之争” 在我 国的表现 尤其突出, 不少在 国外原 以钢轮作 为标准 配置的车 型, 到了我国改用铝轮作 为标 准配置 。20 年 上汽 04 集团生产的乘用车车型 中, 钢轮作 为标 准配置 的 比 例大约只有 3 %。 0 2 22 国际钢轮行业 的生产集 中和寡头垄 断格局 .. 逐步 形成 欧、 、 美 日3个主要汽车市场 的缓慢增 长和替代 品的快速渗透 , 国际钢轮制造业带来 巨大的生存 给 压力 , 这种压力进一步推动了 国际钢轮制造业 的重 组并购和生产的集中。 目前 , 国际钢轮制造业 在几 大主要的汽车市场已形成了寡头垄断的格局。
轮胎行业报告数据分析(3篇)
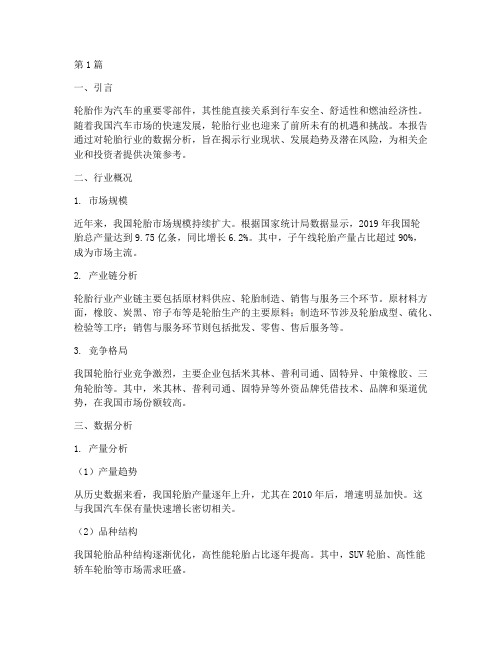
第1篇一、引言轮胎作为汽车的重要零部件,其性能直接关系到行车安全、舒适性和燃油经济性。
随着我国汽车市场的快速发展,轮胎行业也迎来了前所未有的机遇和挑战。
本报告通过对轮胎行业的数据分析,旨在揭示行业现状、发展趋势及潜在风险,为相关企业和投资者提供决策参考。
二、行业概况1. 市场规模近年来,我国轮胎市场规模持续扩大。
根据国家统计局数据显示,2019年我国轮胎总产量达到9.75亿条,同比增长6.2%。
其中,子午线轮胎产量占比超过90%,成为市场主流。
2. 产业链分析轮胎行业产业链主要包括原材料供应、轮胎制造、销售与服务三个环节。
原材料方面,橡胶、炭黑、帘子布等是轮胎生产的主要原料;制造环节涉及轮胎成型、硫化、检验等工序;销售与服务环节则包括批发、零售、售后服务等。
3. 竞争格局我国轮胎行业竞争激烈,主要企业包括米其林、普利司通、固特异、中策橡胶、三角轮胎等。
其中,米其林、普利司通、固特异等外资品牌凭借技术、品牌和渠道优势,在我国市场份额较高。
三、数据分析1. 产量分析(1)产量趋势从历史数据来看,我国轮胎产量逐年上升,尤其在2010年后,增速明显加快。
这与我国汽车保有量快速增长密切相关。
(2)品种结构我国轮胎品种结构逐渐优化,高性能轮胎占比逐年提高。
其中,SUV轮胎、高性能轿车轮胎等市场需求旺盛。
2. 出口分析(1)出口趋势近年来,我国轮胎出口量保持稳定增长。
2019年,我国轮胎出口量达到1.25亿条,同比增长6.2%。
(2)出口地区我国轮胎出口市场主要集中在亚洲、欧洲、美洲等地区。
其中,亚洲市场占比最高,达到50%以上。
3. 价格分析(1)价格走势近年来,我国轮胎价格波动较大。
受原材料成本、汇率等因素影响,轮胎价格呈现周期性波动。
(2)价格结构我国轮胎价格结构呈两头高中间低的态势。
高端轮胎价格较高,低端轮胎价格较低,中端轮胎价格相对稳定。
4. 品牌分析(1)品牌集中度我国轮胎行业品牌集中度较高,前五大企业市场份额超过50%。
火车车轮材料

火车车轮材料火车车轮是火车的重要部件,其材料选择直接关系到火车的安全运行和使用寿命。
目前,火车车轮主要采用的材料有钢轮和复合材料两种类型。
本文将从材料特性、优缺点和应用范围等方面对这两种材料进行比较分析,以期为相关领域的研究和生产提供参考。
首先,钢轮是目前火车车轮的主要材料之一。
钢轮具有高强度、硬度和耐磨性,能够承受火车运行时的巨大载荷和高速摩擦。
此外,钢轮的加工工艺成熟,生产成本相对较低,易于维护和更换。
因此,在传统的火车车轮应用中,钢轮仍然占据主导地位。
然而,钢轮也存在一些缺点。
首先,由于钢轮的密度较大,其重量相对较重,因此会增加火车的整体重量,增加能耗和运行成本。
其次,钢轮在高速运行时容易产生疲劳裂纹和断裂现象,对火车的安全性造成一定影响。
此外,钢轮的振动和噪音较大,也会影响火车的乘坐舒适度和周围环境。
相比之下,复合材料车轮作为新型材料,具有一定的优势。
首先,复合材料轮具有较低的密度和重量,能够有效减轻火车整体重量,降低能耗和运行成本。
其次,复合材料轮的疲劳性能和耐磨性能较好,能够有效延长使用寿命,提高火车的安全性和可靠性。
此外,复合材料轮的振动和噪音较小,能够改善火车的乘坐舒适度和周围环境。
然而,复合材料轮也存在一些问题。
首先,复合材料的生产工艺和技术要求较高,生产成本相对较高,且目前市场上的复合材料轮的规模化生产还存在一定难度。
其次,复合材料轮的研发和应用还需要进一步完善,尤其是在复合材料的可靠性、耐久性和环境适应性等方面还存在一定挑战。
综上所述,钢轮和复合材料轮各有优劣。
在实际应用中,需要根据具体的使用环境、运行条件和经济成本等因素来选择合适的车轮材料。
未来,随着科学技术的不断进步和复合材料技术的不断成熟,相信复合材料车轮将会在火车领域得到更广泛的应用和推广。
同时,钢轮作为传统材料也将在新技术的推动下不断提升和改进,以满足火车运输的需求。
希望本文对相关领域的研究和生产提供一定的参考和帮助。
中国轮胎行业竞争现状的五力分析

中国轮胎行业竞争现状的五力分析本文由gewenqian贡献中国轮胎行业竞争现状的五力分析中国轮胎行业存在着激烈的竞争状态。
中国轮胎行业已经走过了一条比较长的发展道路,在中国360家轮胎企业中,有竞争的企业并不多,主要为国有企业和外资企业,而大多数是规模小、技术水平低、工艺装备差的小企业,这是我国轮胎工业的一大弊病。
总体而言中国轮胎行业现在处于一种战国混战的阶段。
大部分企业属于小企业,能在中国轮胎行业立稳根基的企业并不多。
中国轮胎业五种竞争力量的分析如下。
一、新进入者进入壁垒越高,原有厂商的盈利能力越强。
轮胎行业除了有高额的资本成本外,进入壁垒突出表现在技术壁垒和规模经济上。
1.轮胎行业的技术壁垒日益增高。
进入21世纪,世界轮胎工业创新与变革浪潮一浪接着一浪。
如米其林C3M技术、固特异IMPACT技术、普利司通BIRD技术、大陆MMP技术、倍耐力MIRS技术、三海CCC技术、横滨/东洋不二精工轮胎新工法等。
这些技术使轮胎行业开拓了全新的视野,预示着“轮胎后工业化时代”的来临。
已有轮胎厂商在研发上所做的努力,形成了非常高的进入技术壁垒。
2.轮胎行业的规模经济明显。
轮胎工业是一个技术密集、资金密集、劳动密集型产业,轮胎生产具有固定资产投资大、单个产品价格低的特点,产量越大,单位产品所分摊的固定成本就越低,规模经济就越明显。
由于生产规模不大,我国轮胎生产企业在具有劳动力成本优势的情况下生产成本仍然高于国外企业的根本原因。
,2006年,普利司通、米其林、固特异三巨头的销售收入分别为194亿美元、193亿美元和180亿美元,加起来占全球轮胎总销售收入的50.4%。
而这三家公司在它们各自的国内市场占有率则高达80%,而且这种趋势还在进一步扩大。
由于规模经济效应存在,轮胎企业生产规模越大,竞争优势也就越明显,由此也导致了行业集中度不断提高,寡头垄断特征明显。
二、供应方分析据“中国汽车报”报道,在2008年国内天然橡胶产量将增加百分之八,达到六十五点零万吨。
- 1、下载文档前请自行甄别文档内容的完整性,平台不提供额外的编辑、内容补充、找答案等附加服务。
- 2、"仅部分预览"的文档,不可在线预览部分如存在完整性等问题,可反馈申请退款(可完整预览的文档不适用该条件!)。
- 3、如文档侵犯您的权益,请联系客服反馈,我们会尽快为您处理(人工客服工作时间:9:00-18:30)。
钢制车轮行业状况分析车轮是汽车重要的安全部件之一。
中国汽车工业的发展为中国汽车钢制车轮行业提供了契机。
但是,由于历史原因,中国的钢制车轮企业散乱、技术装备水平落后、自主开发能力弱的局面并没有改变。
本文具体分析了全球钢制车轮工业的现状和发展趋势,以及中国本地车轮企业情况,对汽车钢制车轮行业进行了深入的剖析和猜测。
1 前言中国汽车市场所蕴藏的巨大发展潜力和相对低成本的优势,引起了越来越多的汽车零部件跨国制造商对中国投资的爱好。
面对竞争的国际化和替代产品不断侵蚀其市场份额的压力,中国钢制车轮行业的一系列重大变革的序幕已经拉开,这些变革将涉及资本、技术、产品和市场等众多的领域。
本文从世界车轮行业的总体态势入手,分析了国际车轮企业间的竞争状态,钢轮和铝轮的竞争,钢轮技术的发展等情况,描述目前国内钢轮行业和企业现状并猜测了未来发展的趋势。
2 国际钢制车轮行业概况2.1 汽车车轮的全球市场容量近年来,世界汽车产量在5500-6500万辆之间徘徊。
2004年,世界汽车总产量为6461.6万辆。
按照世界汽车总产量及钢轮和铝轮的配置情况作粗略的估算,全球汽车的OEM车轮配套量约为3.4亿只(其中:美洲1.2亿只,欧洲1.1亿只,亚太地区1亿只左右),市场价值约80亿美元(其中:钢制车轮约35亿美元,铝合金车轮约45亿美元)。
2.2 国际车轮行业的竞争态势2.2.1 国际车轮行业的“钢铝之争”在汽车行业中,传统的钢铁材料正面临着替代材料的严重挑战。
上世纪80年代以来,铝、镁和塑料在汽车上逐步得到应用,90年代中期后,替代材料在汽车上的应用呈加速度趋势。
汽车用材料的“钢铝之争”,在车轮这个安全部件方面的争夺表现的尤其突出,主战场在乘用车车轮领域,并开始逐步扩大到商用车车轮领域。
上世纪80年代初期,全球90%的汽车车轮以钢材作为原料;但到2003年,铝轮的份额窜升至60%。
中国的情况更糟糕一些,部分在国外原以钢轮作为标准配置的车型,到了中国改用铝轮作为标准配置。
以上汽集团为例,2004年上汽集团车型的钢轮配置比例大约只有30%,1/5的轿车配置钢轮,4/5的轿车配置铝轮。
1997年,JD Power Associates的调查研究表明,1997年欧洲主要汽车制造商以钢轮作为标准配置的比重大约77%,北美平均约65%,日本平均约60%。
仅仅两年后,英国一家研究机构的具体调查结果认为,1999年在英国市场销售的汽车中,钢轮作为标准配置的车型只占46%。
2.2.2 国际钢轮行业的生产集中和寡头垄断格局逐步形成欧、美、日三个主要汽车市场的缓慢增长和替代品的快速渗透的不利因素,给国际钢轮制造业带来巨大的生存压力。
这种压力,推动了国际钢轮制造业的重组并购和生产的集中。
目前,国际钢轮制造业在几大主要的汽车市场已形成了“三足鼎立”的寡头垄断格局:北美钢制车轮市场基本上由Hayes Lemmerz International,ArvinMeritor和Accuride三个制造商所瓜分;而日本市场则基本由Topy,Central MotWheel和Ring Techs瓜分。
在欧洲市场,Hayes Lemmerz Internationa,Michelin Wheel Division和Magnetto Wheels三个集团分享了绝大部分的钢轮市场份额:●欧洲乘用车钢制车轮市场:前三家制造商的生产集中度达到74%。
市场份额排名依次为:Hayes Lemmerz Internation占28%,Magnetto Wheels占24%,Michelin Wheel Division占20%,Captive占12%,Sudrad占3%,其他制造商合计占11%。
●欧洲卡、客车钢制车轮市场:前三家制造商的生产集中度高达99%。
三家企业的市场份额及排名依次为:Michelin Wheel Division占36%,Hayes Lemmerz International占35%,Magnetto Wheels占17%。
(注:Sudrad为德国Mefro集团的全资子公司。
2005年3月,Micheline集团公布将其车轮业务全部出售给Mefro集团,从而使Mefro集团成为欧洲最大的车轮生产商之一。
)2.2.3国际钢轮行业的全球化布局和跨洲际联盟的产生国际车轮制造集团,普遍实行了全球化的发展战略。
全球化发展的典型是Hayes Lemmerz International。
该公司于1997年由美国的Hayes公司和德国的Lemmerz公司合并而成,目前在全球拥有22个车轮制造厂,分布于美国、墨西哥、巴西、德国、意大利、比利时、捷克、土耳其、印度、泰国和南非,各种车轮的年生产能力达到6310万只,2003年,其车轮业务的销售收入达12.28亿美元。
面对Hayes Lemmerz International公司咄咄逼人的攻势,在本世纪初,国际车轮行业出现了两个重要的“欧、美、日”跨洲际联盟:A. Magnetto Wheels(欧洲)、Accurid(美国)和Topy(日本)的联盟。
该联盟的车轮年产量达到5300万只。
Magnetto Wheels与Accurid在2000年9月公布建成战略联盟,2001年7月又与Topy签订了联盟协议。
B. Michelin(欧洲)、ArvinMeritor(美国)和Ring Techs(日本)的联盟。
该联盟的钢轮年产量约为4700万只。
三家公司在2002年5月结盟。
国际车轮行业跨洲际联盟的合作领域主要是在技术和市场的层面,包括共享新技术,建立全球性的供给网络等等,也出现了资本纽带关系,比如Magnetto Wheels在2002年6月接管了DUNLOP和TOPY公司在英国的一家乘用车车轮厂89%的股权,TOPY保留11%股份。
2.2.4 国际钢轮行业的最新技术发展和重新夺回失去的市场在过去20年中,钢轮份额下跌,业内人士将其归结为外观、重量、性能等因素,其中,外观是最重要的因素。
钢材的特性和制造工艺决定了钢轮难以做到铸造铝轮那样的结构和外形多样化。
但是,在成本和安全性方面,钢轮却具有非常显着的优势。
最近几年来,国际钢轮制造业在钢铁行业和机械制造行业的协助下,在技术方面进行一系列的革新,取得了突破性的进展具备了与铝轮进行全面抗衡的能力;同时,国际汽车业在巨大的成本压力之下开始重新评估钢轮和铝轮的价值。
值得重视的是,近年来,美国三大汽车公司将不少畅销车型的标准配置由铝轮调整为钢轮,比如:DaimlerChrysler公司2000年后陆续推出的皮卡Dodge Ram 1500/2500/3500已将钢轮成为标准配置;Ford公司的F-150 Lariat 皮卡和Lincoln NavigatSUV,采用了Accuride公司和Lacks合作的新技术钢轮;Nissan在北美销售的皮卡Titan,采用了TOPY生产的深冲压高张力钢板车轮;2004年GM底特律生产基地公布其原计划配置的200万只铝轮将用高强度钢材制造的钢轮替代。
这对国际钢轮业是一个非常大的鼓舞。
国际钢轮行业重新获得其失去的市场,主要的砝码包括:●新材料:微合金钢HSLA,双相钢(DP)和贝氏体钢(Bainitic Steel)等高强度和先进高强度钢种成功开发并逐步应用到制造车轮。
为车轮减轻重量和更加大胆的款式设计创造了必要的条件。
●新工艺:近年来,国际车轮行业与国际车轮设备制造商紧密合作研究发展了旋压生产工艺,应到卡客车的轮幅生产和乘用车的轮辋生产。
无内胎卡客车车轮的轮辐生产使用旋压工艺已经非常普遍。
乘用车轮辋生产也开始使用旋压工艺(图1),当然,这种工艺总体上处在进一步完善的阶段,其不足是装备的投入比较大,效率有待提高。
Magnetto Wheels的法国工厂和Hayes Lemmerz International 的西班牙工厂开始投入小批量生产(主要应用在一些新的大规格的车轮,如直径17”和18”);日本Topy和美国ArvinMeritor也宣称已经把握这项技术。
乘用车车轮轮辋采用旋压工艺、轮幅采用高强度钢材DP600的组合,与传统的材料和工艺相比,可使车轮重量减轻20%,达到与铝轮差不多的重量水平,甚至还低一些。
●新款式:除了材料和工艺革新之外,国际钢轮业在钢轮的外观方面也进行了一系列的开拓,开发了包括半表面车轮、全表面车轮等新车轮。
在款式和轻量化方面的突破是大通风孔(HVA)等款式的车轮,其外观看上去与铝轮差不多,且可有灵活的组合,非凡在穿上外衣(如不锈钢、铝合金、各种颜色的塑料盖等)时的变化可以更多。
Magnetto Wheels,Hayes Lemmerz International,ArvinMerit,Topy等均开发了类似的车轮品种。
Magnetto Wheels还在研发更加轻量化的“三明治”夹层结构的车轮。
当然使用冲压和焊接工艺制造的钢制车轮在细处无法完全与铸造的铝轮相匹敌,但用来取代一些中低端的铝轮,成本优势明显(每个车轮约可降低15美元,每辆整车可以节省60美元,这对OEM采购部门来说是无法忽视的)。
需要说明的是,钢轮使用的模具技术要求高、开发周期长、成本高,轮幅多工位模具成本约30-50万美元一套,需要有大批量的生产来消化,其经济规模大约在30-40万件/年,即6-8万辆整车的配套。
●新工具:近年来CAD/CAM/CAE等设计、模拟和仿真工具取得很大的发展并应用到了国际车轮行业。
借此可以有更加精确和快速的设计,均一性和尺寸精度方面得到大幅度提高。
Hayes Lemmerz International宣称通过利用这些手段,车轮的尺寸精度与5年前相比提高了25-30%。
在生产过程中,在线和离线的质量控制仪器和装备开始普遍应用到国际车轮集团的生产过程中,使车轮的质量得到进一步的控制,目前欧洲车轮行业的PPM水平已经达到100左右的水平。
2.2.5 钢铁业涉足汽车车轮制造业目前,全球钢轮OEM市场钢材消耗量大约为每年400万吨,其中轿车车轮的钢材消耗量约150万吨。
在中国,2004年钢轮行业总体钢材消耗量大约为36万吨,其中乘用车车轮的钢材消耗量大约10万吨。
根据中国汽车行业的发展前景猜测,到2010年,预计全国车轮行业OEM钢材用量可达60万吨,其中,乘用车车轮用钢30万吨,卡客车车轮用钢量30万吨。
汽车车轮作为一个细分市场,钢铝材料的激烈竞争,已经引起世界钢铁业的关注。
在过去的20多年中,钢材的份额从90%下跌到40-50%,对世界钢铁业造成了一定程度的伤害。
针对这种状况,美国钢铁工业协会AISI发起了一个叫做“Wheel Task Force”的活动,全面地推广和协助钢轮企业更多地使用高强度和先进高强度钢材,其邀请的成员包括北美三大汽车集团、北美主要车轮制造商、钢制车轮设备制造商、涂料公司、车轮设计机构等。