铰刀设计原则及铰孔失效模式分析
铰刀使用中常见的八种问题

铰刀使用中常见八大问题的解决在铰孔加工过程中,经常出现孔径超差、内孔表面粗糙度值高等诸多问题。
问题产生的原因如下:一、孔径增大,误差大铰刀外径尺寸设计值偏大或铰刀刃口有毛刺;切削速度过高;进给量不当或加工余量过大;铰刀主偏角过大;铰刀弯曲;铰刀刃口上粘附着切屑瘤;刃磨时铰刀刃口摆差超差;切削液选择不合适;安装铰刀时锥柄表面油污未擦干净或锥面有磕碰伤;锥柄的扁尾偏位装入机床主轴后锥柄圆锥干涉;主轴弯曲或主轴轴承过松或损坏;铰刀浮动不灵活;与工件不同轴;手铰孔时两手用力不均匀,使铰刀左右晃动。
二、孔径缩小铰刀外径尺寸设计值偏小;切削速度过低;进给量过大;铰刀主偏角过小;切削液选择不合适;刃磨时铰刀磨损部分未磨掉,弹性恢复使孔径缩小;铰钢件时,余量太大或铰刀不锋利,易产生弹性恢复,使孔径缩小;内孔不圆,孔径不合格。
三、铰出的内孔不圆铰刀过长,刚性不足,铰削时产生振动;铰刀主偏角过小;铰刀刃带窄;铰孔余量偏;内孔表面有缺口、交叉孔;孔表面有砂眼、气孔;主轴轴承松动,无导向套,或铰刀与导向套配合间隙过大;由于薄壁工件装夹过紧,卸下后工件变形。
四、孔的内表面有明显的棱面铰孔余量过大;铰刀切削部分后角过大;铰刀刃带过宽;工件表面有气孔、砂眼;主轴摆差过大。
五、内孔表面粗糙度值高切削速度过高;切削液选择不合适;铰刀主偏角过大,铰刀刃口不在同一圆周上;铰孔余量太大;铰孔余量不均匀或太小,局部表面未铰到;铰刀切削部分摆差超差、刃口不锋利,表面粗糙;铰刀刃带过宽;铰孔时排屑不畅;铰刀过度磨损;铰刀碰伤,刃口留有毛刺或崩刃;刃口有积屑瘤;由于材料关系,不适用于零度前角或负前角铰刀。
六、铰刀的使用寿命低铰刀材料不合适;铰刀在刃磨时烧伤;切削液选择不合适,切削液未能顺利地流动切削处;铰刀刃磨后表面粗糙度值太高。
七、铰出的孔位置精度超差导向套磨损;导向套底端距工件太远;导向套长度短、精度差;主轴轴承松动。
铰刀刀齿崩刃铰孔余量过大;工件材料硬度过高;切削刃摆差过大,切削负荷不均匀;铰刀主偏角太小,使切削宽度增大;铰深孔或盲孔时,切屑太多,又未及时清除;刃磨时刀齿已磨裂。
金属铝件铰孔分析
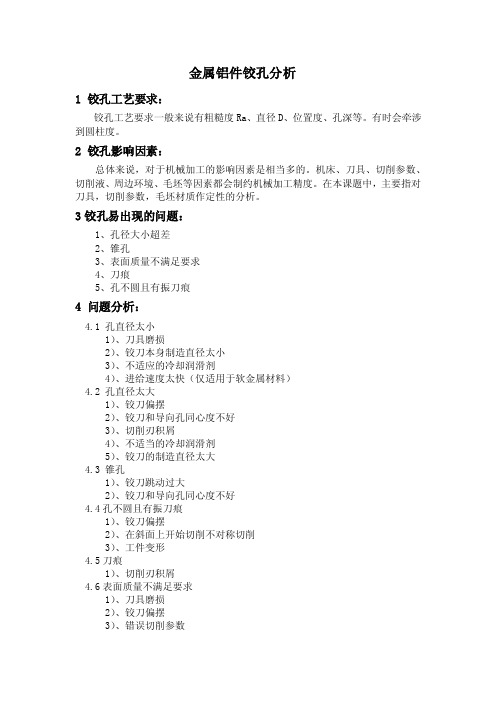
金属铝件铰孔分析1 铰孔工艺要求:铰孔工艺要求一般来说有粗糙度Ra、直径D、位置度、孔深等。
有时会牵涉到圆柱度。
2 铰孔影响因素:总体来说,对于机械加工的影响因素是相当多的。
机床、刀具、切削参数、切削液、周边环境、毛坯等因素都会制约机械加工精度。
在本课题中,主要指对刀具,切削参数,毛坯材质作定性的分析。
3铰孔易出现的问题:1、孔径大小超差2、锥孔3、表面质量不满足要求4、刀痕5、孔不圆且有振刀痕4 问题分析:4.1 孔直径太小1)、刀具磨损2)、铰刀本身制造直径太小3)、不适应的冷却润滑剂4)、进给速度太快(仅适用于软金属材料)4.2 孔直径太大1)、铰刀偏摆2)、铰刀和导向孔同心度不好3)、切削刃积屑4)、不适当的冷却润滑剂5)、铰刀的制造直径太大4.3 锥孔1)、铰刀跳动过大2)、铰刀和导向孔同心度不好4.4孔不圆且有振刀痕1)、铰刀偏摆2)、在斜面上开始切削不对称切削3)、工件变形4.5刀痕1)、切削刃积屑4.6表面质量不满足要求1)、刀具磨损2)、铰刀偏摆3)、错误切削参数4)、排屑不良5 刀具:刀具方面主要牵涉到材质,几何形状,刀具角度等方面。
下面将逐个分析各个因素。
5.1 材质铝件铰孔,一般采用硬质合金、涂层硬质合金、PCD铰刀。
一般来说在加工铝件中问题最大的积屑瘤的问题。
积屑瘤的产生会导致孔径变大,粗糙度超差等负面影响。
从整体上来说PCD铰刀可以使用较高的线速度,能有效避免积屑瘤的产生。
但如果硬质合金刀具设计合理的话,也能加工出很好的精度。
特别是涂层刀具的使用,正确的选用相应的涂层不仅可以达到精度要求,刀具的耐磨性和化学性能稳定,耐热耐氧化,摩擦因素小和热导率低等优点。
但涂层刀片锋利程度不如未涂层刀具,因为刀具涂层时对刃口要做钝化处理。
刃口锋利也可以有效阻止积屑瘤的形成,所以加工铝合金刀具一般不涂层。
5.2 设计及几何尺寸刀具的几何尺寸,如切削刃的前角、后角、主(副)偏角、刃倾角。
铰孔加工质量控制
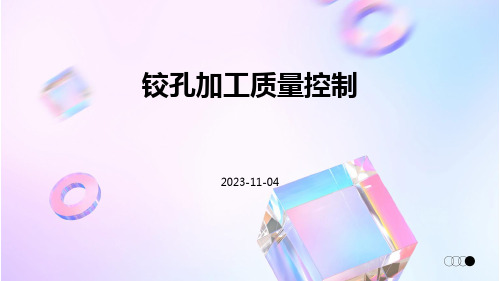
感谢您的观看
THANKS
高质量的铰孔加工能够提高产品的性能和可靠性,减少故障和维修成本。
铰孔加工质量对于产品的装配和使用也具有重要影响,低质量的铰孔可能导致装 配困难、噪音、振动和早期失效等问题。
影响铰孔加工质量的因素
刀具因素
包括刀具材料、刀具磨损、刀具几何参数 等。
机床因素
包括机床精度、机床刚性、机床振动等。
工艺因素
包括铰孔前的预加工、铰孔方法、铰孔余 量、冷却液等。
铰孔加工质量控制
2023-11-04
目 录
• 铰孔加工质量概述 • 铰孔加工质量策划 • 铰孔加工质量控制措施 • 铰孔加工质量检验与评估 • 铰孔加工质量控制应用案例
01
铰孔加工质量概述
铰孔加工质量的定义与重要性
铰孔加工质量是指孔的几何精度、表面粗糙度和孔的形状、位置精度等指标的总 和。这些指标对于产品的性能、寿命和互换性具有重要影响。
2
对质量控制计划进行细化,明确责任人、时间 节点和具体措施,确保计划的可行性和可操作 性。
3
在计划执行过程中,根据实际情况对质量控制 计划进行调整和优化,以满足实际需求。
确定铰孔加工质量控制方案
根据铰孔加工的质量目标和质量 控制计划,确定相应的质量控制
方案。
方案应包括对原材料的质量控制 、设备精度和稳定性的保证、工 艺流程的优化、检验标准的制定
详细描述
在铰孔加工过程中,应选择具有良好冷却性能和润滑性能的 切削液。同时,应确保切削液的流量和压力适中,以充分冷 却刀具和工件。
铰孔加工参数优化
总结词
铰孔加工参数的优化对铰孔加工质量影响较大,需要合理选择主轴转速、进给速度和切削深度等参数 。
详细描述
铰刀

2
铰刀的主要用途
➢经过绞刀加工后的孔可以获得精确的尺寸和形状。 ➢铰刀用于铰削工件上已钻削(或扩孔)加工后的孔,主要 是为了提高孔的加工精度,降低其表面的粗糙度,是用于孔 的精加工和半精加工的刀具,加工余量一般很小。
7
铰刀的分类
01 手 用 铰 刀 02 机 用 铰 刀
8
手用铰刀
手用铰刀概念 顾名思义,手用铰刀就是用于手用铰孔的刀具。手用
铰刀用于铰削工件上已钻削(或扩孔)加工后的孔,主要 是为了提高孔的加工精度,降低其表面的粗糙度,是用于 孔的精加工和半精加工的刀具,加工余量一般很小。 铰削精度
手用铰刀铰削精度为H7、H8、H9内孔。
4
铰刀的齿数及齿槽
• 铰刀的齿数影响铰孔精度、表面粗糙度、容屑空间和刀齿 强度。其值一般按铰刀直径和工件材料确定。铰刀直径较 大时,可取较多齿数;加工韧性材料时,齿数应取少些; 加工脆性材料时,齿数可取多些。为了便于测量铰刀直径, 齿数应取偶数。在常用直径do=8~40mm范围内,一般取齿 数 =4~8个。
机用铰刀的分类
锥柄机用 铰刀
浮动铰刀
套氏机用 铰刀
01
02
03
04
05
06
直柄机用 铰刀
锥度铰 刀
可调节铰 刀
12
机用铰刀-直柄机用铰刀
直柄机用铰刀概念:
直柄机用铰刀用于在机床上铰削一定精度的配合孔,
对孔进行半精加工及精加工,也可以拥有磨孔前和研孔前
的预加工。
直柄机用铰刀用途:
铰孔

使铰刀温度升高
5.余量太多 1.铰刀刀刃不锋利及刀刃上有崩 口、毛刺 表面粗糙 2.余量过大或过小 度差 3.切削速度太高,产生积屑瘤 4.切削液选择不当
2.留适当的铰削余量
3.降低切削速度,用油石把积屑瘤从刀刃上磨去 4.合理选择切削液
10
(1)柄部
用来夹持和传递转矩。(见图)
(2)工作部分 由引导部分l1、切削部分l2、修光部分l3、和 倒锥l4组成。(见图)
1)引导部分 铰刀开始进入孔内时的导向部分。
2)切削部分 担负主要切削工作,铰削时定心好,切屑薄。 3)修光部分 有棱边,起定向、碾光孔壁、控制铰刀直径和 便于测量等作用。 4)倒锥部分 减小铰刀与孔壁之间的摩擦,还可防止产生喇 叭孔和孔径扩大。
③将内孔擦净后,检查孔径尺寸。 2)铰不通孔(见图) ①注意铰削深度,及时退刀。 ②中途退刀几次清除切屑。 注:铰钢件,新刀加乳化液,旧刀加切削油;铰铸件,新 刀加煤油,旧刀不加。
8
二、铰孔方法
9
三、铰孔废品分析
铰孔时产生废品的原因及预防方法
废品种类 产生原因 1.铰刀直径太大 2.铰刀刃口径向振摆过大 孔径扩大 3.尾座偏,铰刀与孔中心不重合 4.切削速度太高,产生积屑瘤和 预防方法 1.仔细测量尺寸,根据孔径尺寸要求,研磨铰刀 2.重新修磨铰刀刃口 3.校正尾座,使其对中,最好采用浮动套筒 4.降低切削速度,加充分的切削液 5.正确选择铰削余量 1.重新刃磨,表面粗糙度要低,刃磨后保管好, 不许碰毛
铰孔前的内孔表面粗糙度不得大于Ra6.3µ m。
2、铰孔方法
(1)准备工作 1)找正尾座中心。
2)固定尾座,尾座套筒伸出50~60mm。
3)选好铰刀。
7
二、铰孔方法
浅谈铰孔的方法_技巧及应用
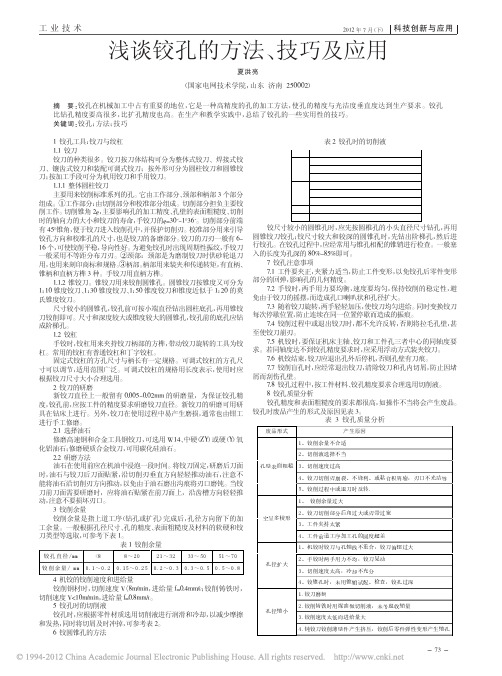
浅谈铰孔的方法、 技巧及应用
夏洪亮
(国家电网技术学院, 山东 济南 250002 )
摘 要 :铰孔在机械加工中占有重要的地位, 它是一种高精度的孔的加工方法, 使孔的精度与光洁度垂直度达到生产要求 。铰孔 比钻孔精度要高很多, 比扩孔精度也高。在生产和教学实践中, 总结了铰孔的一些实用性的技巧。 关键词 :铰孔; 方法; 技巧
4 机铰的铰削速度和进给量 铰削钢材时, 切削速度 V 〈8m/min, 进给量 f=0.4mm/r; 铰削铸铁时, 切削速度 V<10m/min, 进给量 f=0.8mm/r。 5 铰孔时的切削液 铰孔时, 应根据零件材质选用切削液进行润滑和冷却, 以减少摩擦 和发热, 同时将切屑及时冲掉, 可参考表 2。 6 铰圆锥孔的方法
2012 年 7 月 (下 )
科技创新与应用
Hale Waihona Puke 表 2 铰孔时的切削液78%9:;<= >
KLMN
?@AB>%
CD
EFGHIJ EFOPEQRE0STUV W : X0YZ[+ \]>
0hi> = = 0h| =
^
:_^‘ab+ cd I+efg@ j0:+k‘jlmn op+ 0q
1 铰孔工具: 铰刀与绞杠 1.1 铰刀 铰刀的种类很多。铰刀按刀体结构可分为整体式铰刀、焊接式铰 刀、镶齿式铰刀和装配可调式铰刀;按外形可分为圆柱铰刀和圆锥铰 刀; 按加工手段可分为机用铰刀和手用铰刀。 1.1.1 整体圆柱铰刀 它由工作部分、 颈部和柄部 3 个部分 主要用来铰削标准系列的孔。 组成。①工作部分: 由切削部分和校准部分组成。切削部分担负主要铰 切削锥角 2¢, 主要影响孔的加工精度、 孔壁的表面粗糙度、 切削 削工作。 时的轴向力的大小和铰刀的寿命, 手铰刀的¢=30'~1°36'。切削部分前端 有 45°锥角, 便于铰刀进入铰削孔中, 并保护切削刃。 校准部分用来引导 铰孔方向和校准孔的尺寸, 也是铰刀的备磨部分。 铰刀的刀刃一般有 6~ 16 个, 可使铰削平稳, 导向性好。 为避免铰孔时出现周期性振纹, 手铰刀 一般采用不等距分布刀刃。②颈部:颈部是为磨制铰刀时供砂轮退刀 ③柄部。 柄部用来装夹和传递转矩, 有直柄、 用, 也用来刻印商标和规格。 锥柄和直柄方榫 3 种。手铰刀用直柄方榫。 1.1.2 锥铰刀。锥铰刀用来铰削圆锥孔。圆锥铰刀按锥度又可分为 1: 10 锥度铰刀、 1: 30 锥度铰刀、 1: 50 锥度铰刀和锥度近似于 1: 20 的莫 氏锥度铰刀。 尺寸较小的圆锥孔, 铰孔前可按小端直径钻出圆柱底孔, 再用锥铰 刀铰削即可。尺寸和深度较大或锥度较大的圆锥孔, 铰孔前的底孔应钻 成阶梯孔。 1.2 铰杠 手铰时, 铰杠用来夹持铰刀柄部的方榫, 带动铰刀旋转的工具为铰 杠。常用的铰杠有普通铰杠和丁字铰杠。 固定式铰杠的方孔尺寸与柄长有一定规格。可调式铰杠的方孔尺 寸可以调节, 适用范围广泛。可调式铰杠的规格用长度表示, 使用时应 根据铰刀尺寸大小合理选用。 2 铰刀的研磨 新铰刀直径上一般留有 0.005~0.02mm 的研磨量,为保证铰孔精 度, 铰孔前, 应按工件的精度要求研磨铰刀直径。新铰刀的研磨可用研 铰刀在使用过程中易产生磨损, 通常也由钳工 具在钻床上进行。另外, 进行手工修磨。 2.1 选择油石 修磨高速钢和合金工具钢铰刀, 可选用 W14、 中硬 (ZY ) 或硬 (Y ) 氧 化铝油石; 修磨硬质合金铰刀, 可用碳化硅油石。 2.2 研磨方法 油石在使用前应在机油中浸泡一段时间。 将铰刀固定, 研磨后刀面 时, 油石与铰刀后刀面贴紧, 沿切削刃垂直方向轻轻推动油石, 注意不 能将油石沿切削刃方向推动, 以免由于油石磨出沟痕将刃口磨钝。当铰 刀前刀面需要研磨时,应将油石贴紧在前刀面上,沿齿槽方向轻轻推 动, 注意不要损坏刃口。 3 铰削余量 铰削余量是指上道工序 (钻孔或扩孔 ) 完成后, 孔径方向留下的加 工余量。一般根据孔径尺寸、 孔的精度、 表面粗糙度及材料的软硬和铰 刀类型等选取, 可参考下表 1。 表 1 铰削余量
铰孔质量的判别及其解决措施

铰孔质量的判别及其解决措施铰孔是半精加工基础上进行的一种精加工。
一般铰孔的尺寸公差等级可达IT8~IT7,表面粗糙度R。
值可达~。
在实际加工中,常见的铰孔质量问题有表面粗糙度和尺寸精度差,孔口呈喇叭状等。
现分析其产生原因和改进方法。
1 表面粗糙度差的原因及其对策铰削速度过大铰削用量各要素对铰孔的表面粗糙度均有影响,其中以铰削速度影响最大,如用高速钢铰刀铰孔,要获得较好的粗糙度µ;m,对中碳钢工件来说,铰削速度不应超过5m/min,因为此时不易产生积屑瘤,且速度也不高;而铰削铸铁时,因切屑断为粒状,不会形成积屑瘤,故速度可以提高到8~10m/min。
如果采用硬质合金铰刀,铰削速度可提高到90~130m/min,但应修整铰刀的某些角度,以避免出现打刀现象。
铰削余量不适当,进给量过大一般铰削余量为~,对于较大直径的孔,余量不能大于,否则表面粗糙度很差。
故余量过大时可采取粗铰和精铰分开,以保证技术要求。
余量过小,不能正常切削也会使表面粗糙度差。
铰孔的粗糙度Ra值随进给量的增加而增大,但进给量过小时,会导致径向摩擦力的增大,引起铰刀颤动,使孔的表面变粗糙。
所以,如用标准高速钢铰刀加工钢件,要得到表面粗糙度µ;m,则进给量不能超过r,对于铸铁件,可增加至r。
铰刀刀刃不锋利,刃带粗糙一般标准铰刀均未经研磨,影响铰孔的表面粗糙度,因此必须对新铰刀进行研磨。
研磨时要注意铰刀的切削部分与校准部分的交界处,因为内孔最后在这里成形,刀具的粗糙度也在该处被反映到铰孔的内壁。
所以研磨铰刀时,应特别注意用油石将该处轻轻地仔细研磨、抛光,使切削部分与校准部分的交接处圆滑过渡。
经研磨的铰刀,切削刃后刀面刃带粗糙度得到改善,切削部分与校准部分交界处的粗糙度也得到改善,实际上是改善了铰刀本身的粗糙度,故有利于改善铰孔的表面粗糙度。
铰孔时未使用润滑液或使用不当的润滑液铰孔时未用润滑液,则铰刀工作部分的后刀面与孔壁会发生干摩擦,使孔的表面粗糙度差。
解析硬质合金铰刀铰孔无规则收缩_龚小冬

# !" ! " " # 年 第 $% 期 ! ! !" " # $ % & ’ & ( )" $ * "" $ ’
冷加工
( 收稿日期:&))-)’&- )
( 广东! "#$%%% ) ! 李苏营
更大的进给速度以及防止断续切削时切削刃的破坏。 ( & ) 为了避免振动和切断面不平,将刀具磨成如图 % 所示的形状。这样在切削时,刀刃是逐渐切入工件的, 因此受力平稳、连续性好;同时由于刀刃的受力情况如 图 & 所示,沿工件的轴向分力 +% 与 +& 因大小相等方向 相反而相互抵消,因此不会出现普通切断刀易产生振动 的现象。
############################################ !" 解决的办法
针对主要原因,在铰刀加工工艺上采取措施: ( % ) 刀体材料选用 16370,使其焊刀片后仍保持一 定的硬度。 ( & ) 铰刀设计上尽量选用较薄的刀片,刀齿稍浅, 齿槽角度稍小,使齿背尽量加厚,且铰刀外径按孔的最 大极限尺寸设计。焊刀片时,铜焊尽量焊薄焊实在。 ( + ) 铰刀加工工艺在粗磨刀齿外圆时,留精磨量 )" %( 2 )" &,,,然后工具磨用死支片支撑前刀面,粗磨 后角为 %(* 2 %-* ,留圆柱刃带 )" (,, 左右 ( 每齿刃带 宽窄必须一致,否则容易产生跳动误差) 。刃带太窄不 便测量,刃带太宽又不易消除 “ 让刀” 。精磨外圆到最 后尺寸接近时千万不能急,多光整一会,就能避免 塌 陷,第三点是主要环节。 我们用前面所提到的前导向细长杆复合铰刀,试加 工几件,到生产线试用后,效果很好,孔的尺寸与铰刀 的外径完全吻合,孔的圆度和表面粗糙度质量都大幅提 高。我们将所有的硬质合金铰刀都按此加工,取得了同 样的效果。现在,我厂的硬质合金铰刀不再为尺寸和铰 孔质量而烦恼,节省了大量调刀时间、研磨工作和刀具 损耗,为工厂生产经营做出了不可磨灭的贡献。愿我们 的努力也能为我国的机械加工业进步有所帮助。
- 1、下载文档前请自行甄别文档内容的完整性,平台不提供额外的编辑、内容补充、找答案等附加服务。
- 2、"仅部分预览"的文档,不可在线预览部分如存在完整性等问题,可反馈申请退款(可完整预览的文档不适用该条件!)。
- 3、如文档侵犯您的权益,请联系客服反馈,我们会尽快为您处理(人工客服工作时间:9:00-18:30)。
铰刀设计原则及铰孔失效模式分析
在机械加工中,铰孔是用铰刀从工件切除微量金属层,以提高孔的尺寸精度和表面质量的加工方法,是普遍应用的孔的精加工方法之一。
因为铰刀的齿数较多,导向性能好,心部的直径大,刀具的刚性好,加工余量小,可以获得IT9-IT7级直径尺寸精度,内孔表面粗糙度可控制在Ra1.6~0.8mm之间甚至更好。
下面简述一下铰刀的基础知识:
一、铰刀直径及公差的确定原则:
在铰孔加工中,铰刀的直径与公差直接影响到被加工孔的尺寸精度、铰刀的制造成本与使用寿命。
确定铰刀的直径公差应考虑被加工孔的公差Δ、铰孔时的扩张量P或收缩量P1、铰刀使用所需的磨损备磨量H和铰刀本身的制造公差G,见下图所示。
以上计算方法可为按被加工孔的尺寸精度来设计或研磨铰刀提供参考。
为满足工艺要求,一般要先试铰,根据试铰情况来修正计算出的公差带,再确定铰刀实际尺寸及公差,投入使用。
但铰孔时还受机床主轴径向跳动、铰刀的安装偏差、铰刀各刀齿的径向跳动、冷却液、切削用量等因素的影响,使铰出孔的直径往往会“扩张”现象,此时铰刀的直径按下式确定: domax=dwmax-Pmax (1); domin=dwmax-Pmax-G (2);dof=dwmin-Pmin (3).
公式中 do---铰刀直径(mm); dw---工件孔径(mm) ; dof---铰刀报废尺寸(mm); P---铰刀扩张量,一般选取0.003~0.02mm;G---铰刀的制造公差。
在铰削时,也会发生铰出的孔径小于铰刀校准部分实际直径,即产生孔的“收缩”现象,
例如用很小的切削锥的铰刀加工薄壁的韧性材料或用硬质合金铰刀高速铰孔时,铰后孔因弹性恢复而缩小。
此时铰刀直径应按下式确定:
domax=dwmax+P1min (4); domin=dwmax-G (5);dof=dwmin+P1max (6).
公式中P1---孔径收缩量,一般选取0.005~0.02mm。
铰刀磨损储备量H按下式确定:
铰孔后有扩张时 H=domin-dof=domin-dwmin-Pmin (7);
铰孔后有收缩时 H=domin-dof=domin-dwmin-P1max (8)。
二、影响铰刀铰孔质量的主要因素:
(一)铰刀几何参数。
铰孔质量的好坏取决于铰刀本身的精度和表面粗糙度。
因此,铰刀几何参数的合理选择,决定了被铰孔加工质量的好坏。
1--是铰刀直径。
它是根据被加工孔的公称尺寸和公差以及在铰削过程中被加工孔的扩张量或收缩量决定的。
2--是铰刀的齿数。
一般,铰刀的齿数愈多,铰孔的精度就越高,表面粗糙度值就越低,同时,分布在每个切削刃上的负荷也就小,有利于减少铰刀的磨损。
但齿数增多后却降低了刀齿强度,减小了容屑槽。
在切削时,切屑就不容易排出。
特别是铰深孔和切削余量大时,因容屑槽被切屑堵塞,切削液流不进去,致使铰刀和工件因产生热量而变形,影响加工质量。
铰刀的齿数一般都选用偶数。
3--是切削锥角。
它主要是根据不同的加工材料和铰刀的类型来加以选择。
4--是前角。
由于铰削的余量较小,切削仅在刀尖处进行,与刀齿的前倾面很少接触,故前角可以为零,但在铰削塑性较大的材料时,为避免切屑粘滞在刀刃上,前角应取大一些。
5--是后角。
铰刀的后角大,虽然可以提高切削刃的锐利程度,却降低了刀齿强度,在切削过程中容易产生震动和磨损,铰刀直径也随之减小,使铰孔直径达不到要求。
6--是刃带宽度。
它主要是引导铰刀方向和光整孔壁,同时也为了便于测量铰刀的直径。
铰刀的齿数越多刃带的积累宽度也大。
因此有利于孔壁降低表面粗糙度值,铰刀的直径也不容易变小。
但铰刀刃带较宽或积累宽度值过大时,会增加摩擦力矩和切削热,对孔壁的挤压比较严重,容易将孔径涨大,一般选择铰刀的刃带不超过0.25mm。
7--是铰刀的倒锥量。
磨倒锥量是为了避免铰刀校准部分后面摩擦孔壁。
(二)铰削用量。
对铰孔而言,铰削用量是很重要的。
它对铰削过程中的摩擦切削力,
切削热以及切屑瘤的形成和加工精度、表面粗糙度都有极大的影响,因此一定要合理加以选择使用。
1--是铰削余量。
铰削余量不宜留得太大或太小。
因为铰削余量留得太小,铰削时不易校正上道工序残留的变形和去掉表面残留的缺陷,使铰孔质量达不到要求。
若所留的铰削余量太大,势必加大每一个刀齿的切削负荷,破坏了铰削过程中的稳定性,且增加了切削热,使铰刀的直径胀大,孔径也随之扩张,切屑的形成必然呈撕裂状态,造成加工表面粗糙。
2--是机铰的切削速度和进给量。
铰削速度和进给量要根据加工材料合理选择。
进给量不能选得太小,太小时切削厚度可能小于切削刀齿的小圆半径。
铰削余量、切削速度、进给量这三个要素是相互影响,当铰削余量较大时,切削速度,进给量就不能选得过高;反之,如果切削速度和进给量选取较小值时,则可适当提高切削速度。
当然,为了更好地控制铰孔加工质量,除了铰刀几何参数及铰削用量外,可在铰削过程中,采用合理的切削液来排屑和冷却。
三、铰孔失效模式分析及解决措施:
当然,在日常生产中出现加工质量问题是很难全面控制和预防的,只有从“人、机、料、法、环、测”全方位分析,找出问题的根本原因,一定会逐步解决。