铰孔工艺
钻孔、铰孔、镗孔
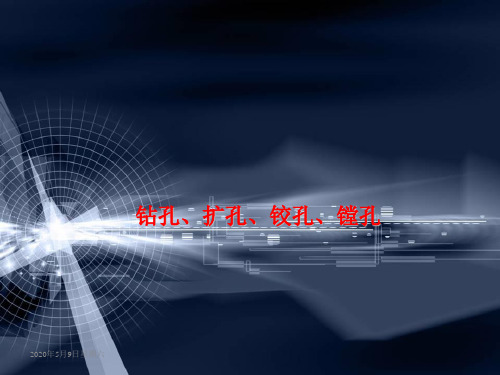
图 9-1 麻花钻头的结构
2015年4月15日星期三
2)中心钻 中心钻用于孔加工的预制精确定位,引导麻花钻进行孔加工,可以减小 误差。中心钻有A型和B型两种型式。A型是不带护锥的中心钻,B型是带护锥 的中心钻。加工直径d=1~10 mm的中心孔时,通常采用不带护锥的中心钻,即 A型。A型中心孔只有60°锥孔;工序较长、精度要求较高的工件,一般采用 带护锥的中心钻,即B型。B型中心孔外端有120°锥面,又称保护锥面,用以 保护60°锥孔的外缘不被碰坏。
0.8μ m。另外,孔距精度可控制在0.05 mm左右。
2015年4月15日星期三
镗刀、镗刀柄和镗刀盘 1.镗刀
镗孔所用的刀具称为镗刀,常用的有整体式镗刀和机械固定式 镗刀。
图 9-9 整体式镗刀和机械固定式镗刀
2015年4月15日星期三
所谓双刃镗刀,是指两端都有切削刃的镗刀。如图9-10所示 为浮动式镗刀,多用于孔的精加工,当精镗时,镗刀块通过作用 在两端的切削刃上大小相等、方向相反的切削抗力,保持自身的 平衡状态,实现自动定心。
成普通孔的精加工。 铰孔的主要工艺要求如下: (1)用铰刀铰孔可以使孔的精度达到IT9~IT7。 (2)用铰刀铰孔可以使孔的表面粗糙度值达到Ra3.2~0.8μ m。
2015年4月15日星期三
铰刀
铰刀分为手用铰刀和机用铰刀两种,其结构如图9-8所示。铰刀由 工作部分、颈部和柄部三部分组成。铰刀的工作部分包括最前端的 45°倒角,45°倒角部分便于铰削开始时将铰刀引导入孔中,并起保
2015年4月15日星期三
(3)用测量法对刀。如图9-18(b)所示,用深度千分尺测量时,A面 到心轴柱面的距离和B面到心轴柱面的距离分别为图样尺寸S3、S4减去心轴 半径。若测量值与计算值不符,则调整工作台位置直至相符为止。 (4)用试镗和测量相结合法对刀。对刀时,首先将铣床主轴轴线与工 件上孔的轴线大致对准,粗镗一刀,然后把孔的实际测量尺寸S7、孔壁到A 基准面的实测尺寸S5、孔壁到B基准面的实测尺寸S6分别与计算值相比较, 再根据误差值调整工作台,使孔的轴线对准镗刀柄的旋转轴线。
数控铣床及加工中心编程与应用项目5铰孔加工

项目5铰孔加工5.1知识准备5.1.1铰孔加工铰孔是利用铰刀从工件孔壁上切除微量金属层,以提高其尺寸精度和表面粗糙度值的加工方法。
铰孔往往作为中小孔钻、扩后的精加工,也可以用于磨孔或研孔前的预加工。
铰孔精度可达到IT9~IT7级,表面粗糙度值R a为1.6~0.8μm,适用于孔的半精加工及精加工。
直径在80mmm以内的孔可以采用铰孔;直径较大的孔多采用精镗加工。
对于小于12mmm 的孔,由于镗孔非常困难,一般先用中心钻定位,然后钻孔(扩孔)、最后铰孔,以保证孔的加工精度。
铰孔不能修正孔的直线度和孔的位置度误差,因此铰孔前孔的直线度和孔的位置精度应符合要求。
一般来说,对于IT8级精度的孔,只要铰削一次就能达到要求;IT7级精度的孔应铰两次,先用小于孔径0.05~0.02mm的铰刀粗铰一次,再用符合孔径公差的铰刀精铰一次。
铰一般孔时,采用直齿铰刀即可;铰不连续孔时,则应采用螺旋齿铰刀;铰通孔时应选用左旋铰刀,切屑向前排出;铰不通孔时,选用右旋铰刀,以使切屑向后排出,但应注意防止“自动进刀”现象引起的振动。
1.铰刀的结构铰刀是对中小直径孔进行半精加工和精加工的刀具,刀具齿数多,槽底直径大、导向性及刚性好。
铰削时,铰刀从工件的孔壁上切除微量的金属层,使被加工孔的精度和表面质量得到提高。
根据铰刀的结构不同,可分为圆柱孔铰刀和锥孔铰刀;根据铰刀制造材料不同可分为高速钢铰刀和硬质合金铰刀。
铰刀的结构如图5-1所示,它是由工作部分、颈部和柄部三部分组成,工作部分包括导锥、切削部分和校准部分。
图5-1 铰刀2.铰刀的装夹铰削的功能是提高孔的尺寸精度和表面质量,而不能提高孔的直线度和孔的位置精度。
铰孔时要求铰刀与机床主轴要有很好的同轴度要求。
采用刚性装夹并不理想,若同轴度误差大,则会出现孔不圆、喇叭口、扩张量大等现象。
因此最好采用浮动装夹装置。
机床或夹具只传递运动和动力,而依靠铰刀的校准部分自我导向。
3.铰削的工艺特点(1)因为采用浮动装夹,铰孔的精度和表面粗糙度主要不是取决于机床的精度,而取决于铰刀的精度、铰刀的安装方式、加工余量、切削用量和切削液等条件。
铰孔加工中的工艺参数
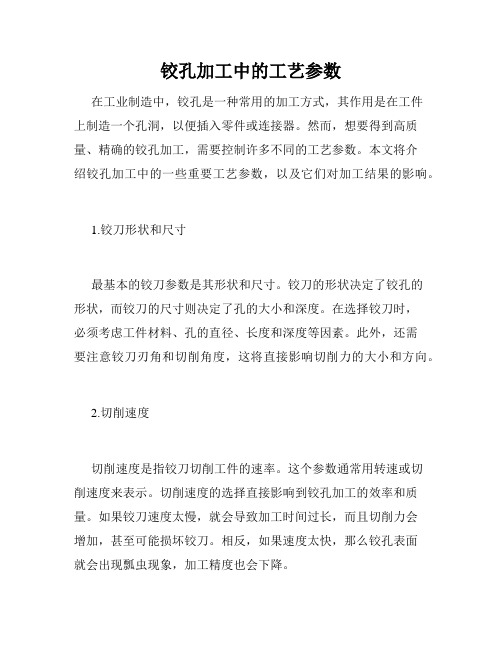
铰孔加工中的工艺参数在工业制造中,铰孔是一种常用的加工方式,其作用是在工件上制造一个孔洞,以便插入零件或连接器。
然而,想要得到高质量、精确的铰孔加工,需要控制许多不同的工艺参数。
本文将介绍铰孔加工中的一些重要工艺参数,以及它们对加工结果的影响。
1.铰刀形状和尺寸最基本的铰刀参数是其形状和尺寸。
铰刀的形状决定了铰孔的形状,而铰刀的尺寸则决定了孔的大小和深度。
在选择铰刀时,必须考虑工件材料、孔的直径、长度和深度等因素。
此外,还需要注意铰刀刃角和切削角度,这将直接影响切削力的大小和方向。
2.切削速度切削速度是指铰刀切削工件的速率。
这个参数通常用转速或切削速度来表示。
切削速度的选择直接影响到铰孔加工的效率和质量。
如果铰刀速度太慢,就会导致加工时间过长,而且切削力会增加,甚至可能损坏铰刀。
相反,如果速度太快,那么铰孔表面就会出现瓢虫现象,加工精度也会下降。
3.进给速度进给速度决定了铰刀在加工过程中每分钟进给的距离。
进给速度与切削速度一样重要,它对加工质量和效率都有影响。
如果进给速度太低,就会导致加工过程中铰孔表面不平滑,甚至出现切削刃痕。
另一方面,如果进给速度过高,则会导致铰刀磨损加速,加工过程中会产生过多的热量,甚至会损坏工件。
4.铰孔深度铰孔深度是铰孔加工的另一个重要参数。
在选择铰刀时,需要根据加工要求确定所需的孔深度,并确保铰孔的深度符合工程要求。
如果铰孔深度过浅,就会导致安装的零件不牢固,而深度过深则会加大工件成本和加工难度。
5.预冲长度预冲长度是指在实际切削铰孔之前,铰刀先在工件上移动的长度。
预冲长度的主要作用是使铰孔与工件表面完全接触,这有利于减少切削刃痕和杂散毛刺等不良现象。
预冲长度的选择应当依据工件材料、孔的直径和深度来确定,并参考铰刀的切削特性和工艺细节。
6.冷却液在铰孔加工过程中,冷却液的选择和使用也是至关重要的工艺参数。
冷却液通过冷却切削区域,降低加工温度,减少摩擦和磨损,并清洗切屑和切屑。
钻孔扩孔及铰孔工艺知识

钻孔(扩孔与铰孔)工艺知识各样部件的孔加工,除掉一部分由车、镗、铣等机床达成外,很大一部分是由钳工利用钻床和钻孔工具(钻头、扩孔钻、铰刀等)达成的。
钳工加工孔的方法一般指钻孔、扩孔和铰孔。
用钻头在实体资料上加工孔叫钻孔。
在钻床上钻孔时,一般状况下,钻头应同时达成两个运动;主运动,即钻头绕轴线的旋转运动(切削运动);协助运动,即钻头沿着轴线方向对着工件的直线运动(进给运动),钻孔时,主要因为钻头构造上存在的弊端,影响加工质量,加工精度一般在IT10级以下,表面粗拙度为μm左右、属粗加工。
一、钻床常用的钻床有台式钻床、立式钻床和摇臂钻床三种,手电钻也是常用的钻孔工具。
台式钻床简称台钻,是一种在工作台上作用的小型钻床,其钻孔直径一般在13mm以下。
台钻型号示例:Z 4 0 1 2主参数:最大钻孔直径型号代号:台式钻床类型代号:钻床因为加工的孔径较小,故台钻的主轴转速一般较高,最高转速可高达近万转/分,最低亦在400转/分左右。
主轴的转速可用改变三角胶带在带轮上的地点来调理。
台钻的主轴进给由转动进给手柄实现。
在进行钻孔前,需依据工件高低调整好工作台与主轴架间的距离,并锁紧固定(联合挂图与实物解说示范)。
台钻小巧灵巧,使用方便,构造简单,主要用于加工小型工件上的各样小孔。
它在仪表制造、钳工和装置顶用得许多。
立式台钻简称立钻。
这种钻床的规格用最大钻孔直径表示。
与台钻对比,立钻刚性好、功率大,因此同意钻削较大的孔,生产率较高,加工精度也较高。
立钻合用于单件、小批量生产中加工中、小型部件。
摇臂钻床它有一个能绕立柱旋转的摇臂、摇臂带着主轴箱可沿立柱垂直移动,同时主轴箱还可以摇臂上作横向挪动。
所以操作时能很方便地调整刀具的地点,以瞄准被加工孔的中心,而不需挪动工件来进行加工。
摇臂钻床合用于一些粗笨的大工件以及多孔工件的加工。
二、钻头钻头是钻孔用的刀削工具,常用高速钢制造,工作部分经热办理淬硬至62~65HRC。
一般钻头由柄部、颈部及工作部分构成(实物与挂图)。
铰孔的工艺

铰孔的工艺铰孔是一种常用的加工工艺,用于制造零件的孔加工。
它是通过铰刀在工件上进行旋转运动,以削除工件上的金属材料,最终形成所需的孔形状和尺寸。
铰孔工艺主要包括以下几个方面:工具选择、加工参数、加工步骤和注意事项。
首先,工具选择是铰孔工艺中非常重要的一步。
常见的铰刀有手动铰刀、机械铰刀和数控铰刀。
手动铰刀适用于简单的孔加工,操作简单方便;机械铰刀适用于批量生产,能够提高工作效率;数控铰刀适用于复杂的孔加工,可以实现高精度的加工。
其次,加工参数也是铰孔工艺中需要注意的一个方面。
首先是转速,一般根据工件材料和孔径大小选择合适的转速,以保证加工效果和工具寿命。
其次是进给速度,进给速度过快容易造成毛刺和刀具损坏,进给速度过慢则会影响加工效率。
最后是切削深度,切削深度应根据工件的强度和刚度选取适当的值,以避免过大的切削力和振动。
加工步骤是铰孔工艺中需要严格按照规定执行的步骤。
首先是确定铰刀的位置和夹持工件。
工件应安装牢固,以免产生振动和偏差。
然后是设置加工参数,包括转速、进给速度和切削深度。
接下来是进行试切,通过试切来调整和校准加工参数,确定最佳的加工条件。
最后是正式加工,进行铰孔操作,及时清理切屑和冷却润滑。
最后,铰孔工艺中还需要注意一些事项。
首先是要选择合适的冷却润滑剂,以降低切削温度和减少刀具磨损。
其次是要保持切削刃的锋利度,定期检查和更换刀具,以保证加工质量。
另外,需要注意加工过程中的安全问题,采取必要的防护措施,避免事故发生。
总之,铰孔是一种常用的加工工艺,通过选择合适的工具、设置有效的加工参数、执行正确的加工步骤和注意事项,可以保证加工质量和效率。
同时,铰孔工艺也需要根据具体的情况进行调整和优化,以满足不同零件的加工需求。
车工工艺教学课件任务三 铰孔

。
任务三 铰孔
一、基础知识
• 4.铰刀尺寸的选择
– 根据经验,铰刀公差通常按照下面的方案来确定。 – 上偏差=2/3被加工孔公差 – 下偏差=1/3被加工孔公差 – 例如,被铰孔尺寸及公差为。
– 在选择铰刀时,其基本尺寸为30 mm。
• 7.铰孔时的冷却和润滑
– 在铰孔时,常常根据不同的被加工材料选取不同的切削液。 – (1)钢件和韧性材料:乳化液、极压乳化液。 – (2)铸铁件、脆性材料:煤油、煤油与矿物油的混合油。 – (3)青铜或铝合金:2号锭子油或煤油。
任务三 铰孔
一、基础知识
• 6.铰削余量的确定
– 铰孔时,应该合理确定加工余量,余量太小时,前一道工序留下的 加工痕迹不能被完全去除,表面粗糙度高。余量太大时,切屑填塞 在铰刀齿槽中,影响切削液进入切削区。
– 而进给量可以选择较大数值,铰钢件时,可取f=0.2~1.0 mm/r, 铰铸铁和有色金属时,进给量还可以再大一些,可取f=0.4~ 1.5 mm/r。
– 吃刀深度ap通常取铰孔余量的一半。
任务三 铰孔
一、基础知识
• 6.铰削余量的确定
– 铰孔时,应该合理确定加工余量,余量太小时,前一道工序留下的 加工痕迹不能被完全去除,表面粗糙度高。余量太大时,切屑填塞 在铰刀齿槽中,影响切削液进入切削区。
任务三 铰孔
一、基础知识
• 铰孔是使用铰刀从工件孔壁上切除微量金属层,以提高其尺 寸精度并减小表面粗糙度的孔加工方法,是重要的孔精加工 方法 。
• 铰孔不能校正预制孔的位置误差。铰孔前一般要经过半精车 孔或扩孔,这一方面可以消除孔的垂直度误差,另一方面可 以使铰孔时余量均匀,可以获得光洁的表面。
车工工艺与技能训练11 加工方法(铰孔)[1]
项目三 车削套类零件
3.3 套类工件的加工方法
五、铰孔 3.铰孔方法 机用铰刀在车床上铰削时,先把铰刀装夹在尾座套筒中或浮动 套筒中(使用浮动套筒可以 不找正),并把尾座移向工件,用手慢慢转动尾座手轮均匀进给来实 现铰削。 手铰时,切削速度低,切削温度也低,不产生积屑瘤,刀具尺 寸变化小,所以手铰比机铰质量高,但手铰只适用于单件小批量生产 中铰通孔。 铰削时,切削速度愈低,表面粗糙度值 愈小,一般最好小于5 m/min。进给量取大些,一般可取0.2 mm/r~l mm/r。
2018年10月23日星期
项目三 车削套类零件
机器是由若干零件按一定的装配关系组合而成。套类零件主要作为旋转 零件的支承,在工作中承受轴向力和径向力。例如车床主轴的轴承孔、尾座 套筒孔、齿轮、带轮孔等。 本项目的学习,要注重与生产实践相结合,增强感性积累和生产知识储 备,图物对照,有效学习,掌握套类零件加工的工艺方法和基本技能。 本项目按如下顺序讨论: 3.1 3.2 3.3 3.4 3.5 3.6 套类工件简介 套类工件的装夹 套类工件的加工方法 套类工件的测量 技能训练 套类工件的质量分析
项目三 车削套类零件
3.3 套类工件的加工方法
六、车削沟槽 2.车端面沟槽 (2)车T形槽 车T形槽比较复杂,可以先用端面直槽刀车出直槽 (图3-30a),再用弯头右车槽刀车外侧沟槽(图3-30b),最后用弯头 左车槽刀车内侧沟槽(图3-30c)。 为了避免弯头刀与直槽侧面圆弧相碰,应将弯头刀侧面磨成圆弧 形。主刀刃的宽度应等于槽宽a,L应小于b,否则弯头刀无法进入槽 内。 (3)车燕尾槽 燕尾槽的车削方法与T形槽相似,也是采用三把刀 分三步车出(图3-31)。
壁、保证铰刀直径和便于测量等作用。倒锥部分是为了减少铰刀与工件
加工中心铰孔的方法技巧
加工中心铰孔的方法技巧
加工中心铰孔是一种常用的加工方法,下面是一些常用的方法和技巧:
1. 选择合适的刀具:根据工件材料的硬度和形状,选择合适的铰刀。
通常使用硬质合金铰刀,能够提供更好的切削质量和寿命。
2. 铰孔前的工件准备:将工件固定在加工中心上,并确保工件表面光洁,并且没有任何杂质。
合适的刀具和夹具夹紧力度也要得当,以确保铰孔的精度和质量。
3. 铰刀进给量控制:通过合适的进给量控制,可以保证铰孔的质量和精度。
进给量太大可能导致刀具损坏或工件表面质量不佳,进给量太小则可能导致切削效率低下。
4. 切削速度控制:根据工件材料的硬度和形状,选择合适的切削速度。
切削速度过高可能导致刀具磨损过快,切削速度过低则可能导致铰孔质量不佳。
5. 切削润滑:使用适当的切削润滑剂可以降低刀具和工件的摩擦,提高切削质量和工具寿命。
选择合适的切削润滑剂并按照规定的用量进行涂抹。
6. 切削过程监控:在加工过程中,及时监控刀具和工件的状态,如果发现异常情况,及时进行调整或更换刀具。
7. 铰孔之后的后续工艺:铰孔完成后,可能需要进行清洁、测量和其他后续处理工艺。
根据具体情况进行相应的处理。
(完整版)铰孔方法
铰孔工艺及方法一、铰孔简介1、铰孔是对已经粗加工的孔进行精加工的一种方法。
2、主要目的:纠正上一道工序残留的变形、刀痕,提高孔的精度,多用于紧配螺栓装配前对螺栓孔的修整。
3、铰孔后的精度一般应该达到IT9~IT7级,不应该低于车床加工后的精度。
4、铰刀的种类:手用和机用。
机用较少使用,船厂多数使用手用铰刀,包括:整体式铰刀、手用可调式圆柱铰刀、整体式圆锥铰刀。
目前8200HP轴系、舵系安装中多使用的为手用可调式圆柱铰刀。
二、铰孔时余量的选择1、铰孔时应考虑孔的直径的大小、材料软硬、尺寸精度要求、表面粗糙度、铰刀类型。
2、铰削余量太大,铰孔不光,铰刀磨损很快。
铰削余量太小,无法达到铰孔目的,影响铰孔质量。
3、余量选择孔径小于5mm,余量10到20丝;孔径5到20mm,余量20到30丝;孔径21到32mm,余量30丝;33到50mm,余量半毫米;大于50的孔径,大多留有1毫米以上余量。
像8200HP的齿轮箱底座孔的铰配中,钻孔后的铰配余量在半毫米。
三、铰孔时需要用到切削液1、切削液目的:清除切屑和降低温度,提高孔的光洁度。
2、钢质材料:一般的乳化液;铰孔要求较高时可用机油或液压油。
3、铸铁材料:不用。
煤油可能会引起孔径缩小。
4、铜:一般乳化液稍微稀释。
5、铝:煤油。
四、铰孔具体操作1、准备:(1)孔径测量:卡尺测量孔径,根据铰削余量与精度要求选择合适尺寸的铰刀,一般选用可调式铰刀。
(2)工具:铰刀、手电、破布、扳手(用于转动铰刀或调节铰刀进给量,并根据铰刀后柄合理选择)、切削液、毛刷。
也可以在铰孔前根据所铰孔的位置及立体空间,自行制作扳手,方便操作便于保证精度。
2、方法:(1)调节铰刀:刀体前端靠近刀头部位螺母松开,调节刀体后端朝向刀柄位置螺母,增大或减小进给量。
刀体越靠近刀头位置,进给量越大。
可以边调节边插进孔内进行试验,以铰刀刀体插入孔内大约一半位置为最理想。
进给量调节好后锁紧上下螺母。
一般情况下,每次的进给量逐步减小,最后一刀完成后可达到铰孔的光洁度和精度要求。
掌握铰孔的加工工艺与编程
THANKS FOR WATCHING
感谢您的观看
问题原因
刀具材料选择不当、刀具结构不合理、切削参数设置不当、加工环 境恶劣等。
解决方案
选择高性能刀具材料、优化刀具结构、合理设置切削参数、改善加 工环境等。
预防措施
加强刀具使用前的检查,避免使用有裂纹或损伤的刀具。同时,合理 安排加工顺序,避免刀具在加工过程中受到过大的冲击和振动。
07 实际操作注意事项与安全 规范
选用具有良好冷却、润滑和防锈性能 的冷却液,以减少刀具磨损、降低加 工温度和防止孔壁表面锈蚀。
供给方式优化
根据加工条件和要求,选择合适的冷 却液供给方式,如喷淋、浸泡等,以 确保冷却液充分覆盖刀具和工件表面 。
工艺参数调整策略
初始参数设定
根据经验或参考类似加工案例, 设定初始的切削速度、进给量和
背吃刀量等参数。
预防措施
定期检查铰刀磨损情况,及时更换磨损严重的铰 刀。
表面粗糙度不达标改善措施
问题原因
铰刀刃口不锋利、铰削速 度过低、进给量不稳定、 铰孔余量过大等。
解决方案
修磨或更换铰刀、提高铰 削速度、稳定进给量、控 制铰孔余量等。
预防措施
加强铰刀的日常维护和保 养,保持刃口锋利。
刀具断裂或磨损过快预防策略
操作前准备工作检查清单
01
检查机床各部位是否完好无 损,如有异常应及时报告维 修人员进行维修或更换。
02
确认刀具、夹具、量具等是 否齐全、完好,并按照工艺 要求正确安装和调整。
03
检查加工工件是否符合图 纸要求,如有缺陷或变形 应及时处理或更换。
04
清洁工作区域,保持整 洁,避免杂物或油污对 加工过程造成干扰。
- 1、下载文档前请自行甄别文档内容的完整性,平台不提供额外的编辑、内容补充、找答案等附加服务。
- 2、"仅部分预览"的文档,不可在线预览部分如存在完整性等问题,可反馈申请退款(可完整预览的文档不适用该条件!)。
- 3、如文档侵犯您的权益,请联系客服反馈,我们会尽快为您处理(人工客服工作时间:9:00-18:30)。
6.6 铰孔工艺、编程材料: 45#钢,正火处理图6-6-1圆周均布孔加工零件6.6.1 铰孔加工工艺1.铰孔加工概述钻孔是在实体材料中钻出一个孔,而铰孔是扩大一个已经存在的孔。
铰孔和钻孔、扩孔一样都是由刀具本身的尺寸来保证被加工孔的尺寸的,但铰孔的质量要高得多。
铰孔时,铰刀从工件孔壁上切除微量金属层,以提高其尺寸精度和减小其表面粗糙度值,铰孔是孔的精加工方法之一,常用作直径不很大、硬度不太高的工件孔的精加工,也可用于磨孔或研孔前的预加工。
机铰生产率高,劳动强度小,适宜于大批大量生产。
铰孔加工精度可达IT9~IT7级,表面粗糙度一般达Ra1.6~0.8μm。
这是由于铰孔所用的铰刀结构特殊,加工余量小,并用很低的切削速度工作的缘故。
直径在100 mm以内的孔可以采用铰孔,孔径大于100 mm时,多用精镗代替铰孔。
在镗床上铰孔时,孔的加工顺序一般为:钻(或扩)孔一镗孔一铰孔。
对于直径小于12 mm的孔,由于孔小镗孔非常困难,一般先用中心钻定位,然后钻孔、扩孔,最后铰孔,这样才能保证孔的直线度和同轴度。
如图6-6-1所示的工件,加工6×φ20H7均布孔,孔面有Ra1.6的表面质量要求,适合用铰孔方法进行孔的精加工。
一般来说,对于IT8级精度的孔,只要铰削一次就能达到要求;IT7级精度的孔应铰两次,先用小于孔径0.05~0.2 mm的铰刀粗铰一次,再用符合孔径公差的铰刀精铰一次;IT6级精度的孔则应铰削三次。
铰孔对于纠正孔的位置误差的能力很差,因此,孔的有关位置精度应由铰孔前的预加工工序予以保证,在铰削前孔的预加工,应先进行减少和消除位置误差。
如,对于同轴度和位置公差有较高要求的孔,首先使用中心钻或点钻加工,然后钻孔,接着是粗镗,最后才由铰刀完成加工。
另外铰孔前,孔的表面粗糙度应小于Ra3.2μm 。
铰孔操作需要使用冷却液,以得到较好的表面质量并在加工中帮助排屑。
切削中并不会产生大量的热,所以选用标准的冷却液即可。
2.铰刀及选用⑴ 铰刀结构在加工中心上铰孔时,多采用通用的标准机用铰刀。
通用标准铰刀,有直柄、锥柄和套式三种。
直柄铰刀直径为φ6mm ~φ20mm ,小孔直柄铰刀直径为φ1 mm ~φ6mm ,锥柄铰刀直径为φ10mm ~φ32mm ,套式铰刀直径为φ25mm ~φ80mm 。
分H7、H8、H9三种精度等级如图6-6-2(a ),整体式铰刀工作部分包括切削部分与校准部分。
铰刀刀头开始部分,称为刀头倒角或“引导锥”,方便刀具进入一个没有倒角的孔。
一些铰刀在刀头设计一段锥形切削刃,为刀具切削部分,承担主要的切削工作,其切削半锥角较小,一般为10~150,因此,铰削时定心好,切屑薄。
校准部分的作用是校正孔径、修光孔壁和导向。
校准部分包括圆柱部分和倒锥部分。
圆柱部分保证铰刀直径和便于测量。
刀体后半部分呈倒锥形可以减小铰刀与孔壁的摩擦。
⑵ 铰刀直径尺寸的确定铰孔的精度主要决定于铰刀的尺寸精度。
由于新的标准圆柱铰刀,直径上留在研磨余量,且其表面粗糙度也较差,所以在铰削IT8级精度以上孔时,应先将铰刀的直径研磨到所需的尺寸精度。
由于铰孔后,孔径会扩张或缩小,目前对孔的扩张或缩小量尚无统一规定,一般铰刀的直径多采用经验数值:铰刀直径的基本尺寸=孔的基本尺寸; 上偏差=2/3被加工孔的直径公差; 下偏差=1/3被加工孔的直径公差; 例如:铰削φ20H7(021.00)的孔,则选用的铰刀直径:铰刀基本尺寸=φ20 mm上偏差=2/3×0.021 mm=0.014 1 mm 下偏差=1/3×0.021 mm=0.007 mm所以选用的铰刀直径尺寸为φ20014.0007.0++mm 。
⑶ 铰刀齿数确定铰刀是多刃刀具,铰刀齿数取决于孔径及加工精度,标准铰刀有4~12齿。
齿数过多,刀具的制造刃磨较困难,在刀具直径一定时,刀齿的强度会降低,容屑空间小,由此造成切屑堵塞和划伤孔壁甚至蹦刃。
齿数过少,则铰削时的稳定性差,刀齿的切削负荷增大,且容易产生几何形状误差。
铰刀齿数可参照表6-6-1选择。
表6-6-1铰刀齿数选择铰刀直径/mm1.5~3 3~14 14~40 >40 齿 数一般加工精度4468高加工精度6810~12铰刀的刀齿又分为直齿和螺旋齿两种。
螺旋齿铰刀带有左旋的螺旋槽,这种设计适合于加工通孔,在切削过程中左旋螺旋槽“迫使”切屑往孔底移动并进入空区。
不过它不适合盲孔加工。
⑷ 铰刀材料确定铰刀材料通常是高速钢、钴合金或带焊接硬质合金刀尖的硬质合金刀具。
硬质合金铰刀耐磨性较好;高速钢铰刀较经济实用,耐磨性较差。
3.铰削用量的选用⑴ 铰削余量铰削余量是留作铰削加工的切深的大小。
通常要进行铰孔余量比扩孔或镗孔的余量要小,铰削余量太大会增大切削压力而损坏铰刀,导致加工表面粗糙度很差。
余量过大时可采取粗铰和精铰分开,以保证技术要求。
另一方面,如果毛坯余量太小会使铰刀过早磨损,不能正常切削,也会使表面粗糙度差。
一般铰削余量为0.1~0.25mm ,对于较大直径的孔,余量不能大于0.3mm 。
有一种经验建议留出铰刀直径1~3%大小的厚度作为铰削余量(直径值),如,Φ20的铰刀加Φ19.6左右的孔直径比较合适:20-(20×2/100)=19.6对于硬材料和一些航空材料,铰孔余量通常取得更小。
⑵铰孔的进给率铰孔的进给率比钻孔要大,通常为它的2~3倍。
取较高进给率的目的是使铰刀切削材料而不是摩擦材料。
但铰孔的粗糙度Ra值随进给量的增加而增大。
进给量过小时,会导致刀具径向摩擦力的增大,铰刀会迅速磨损引起铰刀颤动,使孔的表面变粗糙。
标准高速钢铰刀加工钢件,要得到表面粗糙度Ra0.63,则进给量不能超过0.5mm/r,对于铸铁件,可增加至0.85mm/r。
⑶铰孔操作的主轴转速铰削用量各要素对铰孔的表面粗糙度均有影响,其中以铰削速度影响最大,如用高速钢铰刀铰孔,要获得较好的粗糙度Ra0.63;m,对中碳钢工件来说,铰削速度不应超过5m/min,因为此时不易产生积屑瘤,且速度也不高;而铰削铸铁时,因切屑断为粒状,不会形成积屑瘤,故速度可以提高到8~10m/min。
通常铰孔的主轴转速可选为同材料上钻孔主轴转速的2/3。
例如,如果钻孔主轴转速为500r/min,那么铰孔主轴转速定为它的2/3比较合理:500×0.660=330r/min4.适合于铰孔切削循环通常铰孔的步骤和其他操作一样。
加工盲孔时,先采用钻削然后铰孔,但是在钻孔过程中必然会在孔内留下一些碎屑影响铰孔的正常操作。
因此在铰孔之前,应用M00停止程序,允许操作图6-6-3 G85固定循环路线者除去所有的碎屑。
铰孔编程也需要用到固定循环。
实际上并没有直接定义的铰孔循环。
Fanuc控制系统中比较合适的循环为G85,该循环可实现进给运动“进”和进给运动“出”,且两种运动的进给率相同。
G85固定循环路线如图6-6-3所示。
6.6.2 铰孔工艺编程实例1.工件孔加工任务如图6-6-1零件,毛坯尺寸:90×90×42,材料为45钢,正火处理,已在普通铣床上完成90×90侧面轮廓和基本定位面底平面加工,上表面留下了2㎜的余量,现需要加工:1)铣削上表面,保证尺寸30,上表面达到Ra3.2的表面质量要求;2)6×φ20H7圆周均布通孔加工,孔面达到Ra1.6的表面质量要求。
2.工件坐标系设定:如图6-6-4,工件长、宽向设计基准分别在左右、前后的对称面,设定X、Y向工件零点在工件对称中心,Z向零点设在距底面30㎜上表面。
3.上表面加工工艺分析:上表面加工参考平面铣削工艺。
4.圆周均布通孔加工方法选择选用钻→扩→铰的加工方法加工φ20H7,加工步骤及刀具选择如下:①引正孔:φ4中心钻钻引正孔;②钻孔:φ18麻花钻头钻通孔;③扩孔:φ19.8扩孔钻扩孔,半精加工;④孔口倒角:φ30点钻(钻尖90°)⑤铰孔:φ20H7机用铰刀铰孔精加工。
5.孔加工循环的选择:底孔加工前的中心钻加工中心孔用G82孔加工循环,麻花钻头钻6×φ18mm孔和扩孔钻直径19.8mm用G81孔加工循环,最后机用铰刀铰直径20mm孔应用G84孔加工循环。
6.各孔X、Y位置坐标值:如表6-6-2所示,各孔X、Y位置坐标值有直角坐标、极坐标两种表示法:表6-6-21 2 3 4 5 6直角坐标X=30cos30°Y=30sin30°X=30cos90°Y=30sin90°X=30cos150°Y=30sin150°X=30cos210°Y=30sin210°X=30cos270°Y=30sin270°X=30cos330°Y=30sin330°极坐标X=30Y=30 X=30Y=90X=30Y=150X=30Y=210X=30Y=270X=30Y=330显然当多孔在XY平面内圆周分布时,用极坐标的方法表示点位较直角坐标表示法方便。
7.孔加工循环的高度平面选择图6-6-4工件工件坐标系Z向R面高度:上表面上方50㎜。
初始平面高度:上表面上方5㎜。
孔底高度:引正孔钻至Z-5;φ18麻花钻钻孔深至Z-45;扩φ19.8孔深至Z-40;倒角至Z-11;铰孔深至Z-40。
8.切削用量的计算零件材料为45钢,机用铰刀材料为高速钢,直径20mm,进给量0.8mm/r,转速100 r/min,切削液为30%菜油加70%肥皂水。
其它刀具切削用量参考表6-6-3工序卡9.工序卡表6-6-3工序卡10.孔加工编程加工程序编制如下:主程序:O6600;主程序号G54 G21 G90 G94 G17 T01 初始化设置,同时T01刀准备T01 M98 P8888;调用换刀子程序,T01刀装上主轴M98 P6601;调用T01刀加工程序O6601T02 M98 P8888;调用换刀子程序,T02刀装上主轴M98 P6602;调用T02刀加工程序O6602子程序:O6601(T01铣平面)G00 X120 .0Y-5.0 S318 M03;G43 G0 Z50.0 H01;G0 Z-5.0 M08;G1 X-120 F550;G00 Z50.0;M99O6602(T02中心钻钻引正孔)S1200 M03G43 Z50.0 H02 M08G17G16G99 G82 X30 Y30 R5.0 Z-5.0 P100 F100. M98P6607G15M99O6603(T03麻花钻头钻通孔)S550 M03G43 Z50.0 H03 M08G17G16 G99 G81 X30 Y30 R5.0 Z-45. F80.M98P6607G15M99O6604(T04φ19.8扩孔钻扩孔,半精加工)S300 M03G43 Z50.0 H04 M08G17G16G99 G81X30Y30 R5.0 Z-40.0 F150.M98 P6607G15M99O6605(T05孔口倒角)S300 M03G43 Z50.0 H05 M08G17G16G99 G82X30Y30 R5.0 Z-11.0 P100 F50. M98P6607G15M99T03 M98 P8888;调用换刀子程序,T03装上主轴M98 P6603;调用T03刀加工程序O6603T04 M98 P8888;调用换刀子程序,T04刀装上主轴M98 P06604;调用T04刀加工程序O6604T05 M98 P8888;调用换刀子程序,T05装上主轴M98 P6605;调用T05刀加工程序O6605T06 M98 P8888;调用换刀子程序,T06装上主轴M98 P6606;调用T06刀加工程序O6606G91 G28 Z0 回到机床Z向零点M05;主轴停转M30;。