3工件的装夹及铣削方法
第二章工件装夹和机床夹具
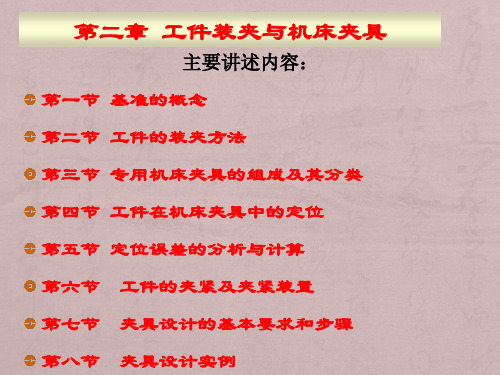
第四节 工件在机床夹具中的定位
例2.在圆柱体上钻孔,保证孔尺寸及与外圆柱的同轴度。
第四节 工件在机床夹具中的定位
影响加工要求的自由度,必须限制;不影响加工要求
的自由度可限制,可不限制。
例及与3.图底示面,的在平一行工度件两上项铣要通求槽,。必为须保限证制尺Z寸, X6,0Y00.20mm
为保证尺寸30±0·1mm及槽侧面与B面的平行度,必须限制
第三节 专用机床夹具的组成及其分类
第三节 专用机床夹具的组成及其分类
2.夹紧元件或夹紧装置 夹紧工件,并使其在加工时在外 力作用下仍然保持工件在夹具中 正确位置的元件或装置称为夹紧 元件或夹紧装置。它一般由动力 装置(如气缸、油缸等)、中间 传力机构(如杠杆、螺纹传动副、 斜楔、凸轮等)和夹紧元件(如 卡爪、压板、压块等)组成。
X
,Leabharlann Z两个自由度,至于 Y 则可限制可不限制。
图1-12
第四节 工件在机床夹具中的定位
5.正确处理过定位: 1) 改变定位元件的结构避免过定位
如图示,把长圆柱销改成短圆柱销,即可避免了过定位。
第四节 工件在机床夹具中的定位
2. 去掉多余的定位支承,消除过定位
如图示,定位支承销3重复限制了Y 把定位支承销3撤消,
第二章 工件装夹与机床夹具
主要讲述内容: 第一节 基准的概念 第二节 工件的装夹方法 第三节 专用机床夹具的组成及其分类 第四节 工件在机床夹具中的定位 第五节 定位误差的分析与计算 第六节 工件的夹紧及夹紧装置 第七节 夹具设计的基本要求和步骤 第八节 夹具设计实例
第一节 基准的概念
一、基本概念: 1. 定位:
图1-7
第四节 工件在机床夹具中的定位
数控铣削加工工艺范围及铣削方式

数控铣削加工工艺范围及铣削方式铣削是铣刀旋转作主运动,工件或铣刀作进给运动的切削加工方法。
铣削的主要工作及刀具与工件的运动形式如图所示。
在铣削过程中,根据铣床,铣刀及运动形式的不同可将铣削分为如下几种:(1)根据铣床分类根据铣床的结构将铣削方式分为立铣和卧铣.由于数控铣削一个工序中一般要加工多个表面,所以常见的数控铣床多为立式铣床。
(2)根据铣刀分类根据铣刀切削刃的形式和方位将铣削方式分为周铣和端铣.用分布于铣刀圆柱面上的刀齿铣削工作表面,称为周铣,如图6—2(a)所示;用分布于铣刀端平面上的刀齿进行铣削称为端铣,如图6—2(b)所示。
图中平行于铣刀轴线测量的切削层参数ap为背吃刀量.垂直于铣刀轴线测量的切削层参数ac为切削宽度,fz是每齿进给量.单独的周铣和端铣主要用于加工平面类零件,数控铣削中常用周、端铣组合加工曲面和型腔。
(3)根据铣刀和工件的运动形式公类根据铣刀和工作的相对运动将铣削方式分为顺铣和逆铣。
铣削时,铣刀切出工件时的切削速度方向与工件的进给方向相同,称为顺铣如图(6—3)a 所示;铣削时,铣刀切入工件时的切削速度方向与工件进给方向相反,称为逆铣,如图(6-3)b所示。
顺铣与逆铣比较:顺铣加工可以提高铣刀耐用度2~3倍,工件表面粗糙度值较小,尤其在铣削难加工材料时,效果更加明显。
铣床工作台的纵向进给运动一般由丝杠和螺母来实现,采用顺铣法加工时,对普通铣床首先要求铣床有消除进给丝杠螺母副间隙的装置,避免工作台窜动;其次要求毛坯表面没有破皮,工艺系统有足够的刚度。
如果具备这样的条件,应当优先考虑采用顺铣,否则应采用逆铣.目前生产中采用逆铣加工方式的比较多。
数控铣床采用无间隙的滚球丝杠传动,因此数控铣床均可采用顺铣加工.数控铣削主要特点(1)生产率高(2)可选用不同的铣削方式(3)断续切削(4)半封闭切削数控铣削主要加工对象(1)平面类零件加工面平行或垂直水平面,或加工面与水平面的夹角为定角的零件为平面类零件.目前,在数控铣床上加工的绝大多数零件属于平面类零件。
高速铣削薄壁件的工件装夹方法

高速铣削薄壁件的工件装夹方法F技术前沿高速铣削薄壁件的工件装夹方法■文/同济大学机械工程学院李沪曾纪多斌在航空航天,汽车电子电器等工业领域,越来越多地使用薄壁结构件(以下简称薄壁件).在保证刚度,强度,抗断裂能力等要求条件下.尽可能减轻零部件重量.并减少零件总数和装配工作.薄壁件材料切除率高达9O%以上.需要努力控制加工变形和提高效率.对机械加工提出了高新技术要求.高速铣削作为当今世界先进制造技术之一,很适合于加工薄壁件.为控制加工变形.除进行工艺优化外.还需要合理选择工件装夹方法.本文以下就这一主题进行探讨.1.薄壁结构件的装夹在实验室工作实践中.尝试采用通用压板.磁体吸附和真空吸盘等不同方法装夹薄壁件.都取得良好效果.下面分别展开讨论.1.1通用压板图1中三连波导薄壁件外形尺寸为791×157×32mm.长,宽与厚度尺寸相差不算特别悬殊.最小壁厚为2mm.工件刚度不是很小.经过分析比较和试验.在毛坯两侧面沿长度方向铣削高10mm.深3mm的工艺通槽后.从毛坯两侧用4块压板伸人工艺通槽压紧.结果证明装夹变形小.实用方便.此处的装夹要点是压板的数量和在机床工作台面上围绕毛坯的作用点分布,还有夹紧力的大小.一般地说. 压板数量应当适中.作用点分布位置需要均匀错开. 夹紧力尽可能小些.?112.第04期数控机床市场图1通用压板装夹三连波导薄壁件如果薄壁件的长,宽尺寸大且接近.而厚度很小时.采用通用压板装夹会有问题.其一.工件毛坯侧面高度不足没有铣削工艺槽的余地.只能用压板直接压住上表面.容易留下压痕.特别是当工件材料较软时.此时压板还会妨碍走刀加工.其二.压板压紧后.毛坯中间部位容易发生弹性变形而如图2拱起,影响加工精度甚至加工的顺利进行,加工完成后工件难免发生较大翘曲变形.拱起高度血广~向一.图2通用压板装夹造成毛坯拱起变形可见.通用压板主要用于厚度和刚度不很小的薄壁件装夹.1.2磁铁吸附如果需要加工厚度为1mm左右的有色金属薄板件,通用压板和电磁工作台装夹都无法采用,不妨考虑磁铁吸附的装夹方法.用永磁铁通过磁力吸附作用将此类薄板件压紧在导磁的工作台面上.该方法广泛应用于电子元器件领域,解决刚性低,工艺要求苛刻的轻小,超薄有色金属零件的装夹问题.磁铁吸附装夹夹紧力分布均匀,夹紧可靠,工件变形小,一般不会在工件表面产生压痕.磁铁形状简单,便于保管,还可以组合起来用于装夹形状复杂的薄板件.图3所示铝合金薄壁件上有12条直槽,槽壁和槽底厚度均为1mm,毛坯原始厚度1O.25mm.高速铣削加工时采用了通用压板和磁铁吸附结合的装夹方法. 起先.在毛坯四周每边铣出两个用于搭压板的工艺槽,尺寸为20X5X5mm.通用压板压紧后,开始铣削中间2条直槽.加工完成后把工业用强磁铁放入槽内,利用磁铁与工作台面问的磁力作用,使工件底面与工作台面紧密接触.接着,从中间向两边依次铣削直槽,每次左右对称各1条,加工完成后即放入磁铁,直至12条槽内都有了磁铁.最后,拆去工件四周的8块压板,仅利用磁铁吸力夹紧工件,再完成工件外轮廓的铣削加工,可以避免压板妨碍走刀加工.图3铝合金直槽腔薄壁件磁铁吸附装夹效率较低,增加了数控编程和加工时需要考虑的问题,在通用机械制造领域内适合于作为临时替代或补充的装夹方法.1.3真空吸盘随着科学技术的发展进步,有色金属和非金属材料在制造业中的应用日趋广泛.机械加工中遇到越来越多薄,脆,无导磁性的扁平工件,往往不能够采用传统方法装夹固定.2O世纪9O年代以来,真空吸盘夹具逐渐进入机械加工领域.最初,它在电子行F业中获得较多应用,而后推广到汽车,包装,木工,金属加工等行业中.真空吸盘夹紧力分布均匀,大小一致.没有机械夹紧件,不会造成工件局部变形,不影响工件表面质量.它不需要装夹辅具.使用方便,可减少装夹辅助时间,提高效率.这些优点,使它十分适合于装夹薄壁件.根据真空的产生方法,真空吸盘可分压缩空气原理和真空泵原理两大类.1.3.1压缩空气原理图4表示压缩空气产生真空的原理.压缩空气从阀ElA送入,经阀ElB由阀ElC流出.阀ElB截面积比阀ElA小,空气流速在B处远高于A处.由伯努利方程可知B处气压较低而产生强的抽吸能力,带走阀ElD处的气体形成真空.这就是作为真空源的真空发生器的原理.它工作时不需要润滑,是清洁的工艺装备.真空发生器分单级和多级两类,后者效率高,在消耗等量压缩空气条件下,抽气量达到前者的若干倍.图4压缩空气产生真空原理图5真空发生器真空吸盘夹具第o4期数控机床市场?113?技术箭图5真空吸盘夹具采用真空发生器作为真空源,吸盘金属工作台面用于支承工件,吸口分布均匀,采用中等硬度橡胶条密封,工件定位吸紧可靠.1.3.2真空泵原理与真空发生器相比,真空泵能够达到的真空度高,抽吸效率高.达到同样真空度的时间短.按其基本原理,真空泵可分为压缩型和吸附型两类.最常见的压缩型真空泵采用机械工作原理,借助机构的循环运动周期性地改变泵内容积空间,压缩其中的气体排出泵外,并阻止外界气体倒流回泵内.通过不断抽吸与泵相连的密闭空间内的气体并排出泵外,可以很快地获得真空.吸附型真空泵利用各种物理表面或化学吸气剂,在封闭的空间中将气体分子吸附在固体表面上或变为固体,例如吸附泵,溅射离子泵,钛升华泵及低温泵.图6和图7显示实验室与某外资企业共同研发的一套真空夹具系统.图6用电化铝材料制成的网格真空工作台尺寸为610X610X28mm,重图6密封胶条嵌入网格真空台面图7真空夹具系统气路部分?114?第04期数控机床市场量<15kg,用通用压板固定在5轴联动高速铣削加工中心的圆工作台上.网格真空台面经特殊处理摩擦增大,不平度不超过0.O2mm,扁平薄板工件安放其上,加工后形状误差≤0.O2mm.台面上纵横各有22道5X5mm的通槽,用于根据薄壁件面积大小嵌入密封胶条,围出一块面积略小的吸附区域.实践表明正确选用密封胶条的材料,硬度,弹性,截面形状,制造精度等,对于保证工件装夹的定位精度和吸紧,保证系统的长期正常工作运转,具有决定意义.图7气路部分中,左侧水隔离器通过黑色塑料管与网格真空工作台相连,用于过滤沉淀穿越密封胶条而漏入的少量切屑,冷却润滑液等杂质,以隔离保护图右侧昂贵的真空泵,首先使之能够长期正常运转.压缩型真空泵最大抽吸能力为7.6m3/h,可在2s内使系统达到85%的相对真空度.即入=O.85.图中间黑色的手动滑阀.用于控制网格真空台面处于吸紧工作或者放松暂停状态.真空夹具其实是利用工件上下两面的气体压力差压紧工件.若F1和F2分别为工件上,下两表面所受大气压力和吸盘内残余气体压力,则压力差AF=F1一F2=P0XA1一(1一入)XP0XA2其中标准大气压P0=1O1325Pa,A1为大气压力作用面积也即工件上表面面积,A2为密封胶条围出的吸附区域中的吸口面积.如果工件材料为铝合金,则图6中网格台面与它的静摩擦系数≥065.在扁平薄板件上下表面尺寸与工作台网格台面相同的条件下,A1=590X 590:0.3481m,A2=20X5X[[590+(590—20X5)]=0.108m2,得△F=101325X0.3481一(1—0.85)X101325X01O833630N,静摩擦力fmax≥0.65X33630—21860N,工件自重对其影响忽略不计.当A1减小至1/8时,粗略估算假设A2以相同比例减小,则AF一4200N和fmax一2730N.在实验室高速铣削铝合金时,切削分力FX,FY,FZ均小于300N,即Fz远小于AF,Fx与Fy的矢量和远小于fmax, 所以该夹具系统夹紧可靠.真空夹具系统能够比较理想地满足装夹无导磁性的薄壁件尤其是扁平薄板件的要求,工件变形小,装夹快捷,方便,但是价格高.2.结论本文介绍了在实验室工作实践中.通用压板磁体吸附和真空吸盘三种装夹薄壁件的不同方法.其中,通用压板简单,通用,价格低,但适合装夹厚度和刚度不很小的薄壁件,容易产生压痕.磁铁本身也简单,不过一般仅作为临时替代或补充的装夹方法且使用过程中需要多次操作不够方便.真空夹具系统适用性广,工件装夹可靠,变形小,操作方便,但需要定制系统,使用中有消耗成本高需要考虑其经济性例如工件有一定批量.参考文献[1]李沪曾,王逸,张冲等.薄壁整体结构件的高速铣削.同济大学(自然科学版),2007.35(4):522[2]张秋源,李汛波,罗世勇.利用钐钻永磁体的夹具设计.工具技术,2006(2):38[3]陆宏,真空夹具及其应用.仪表技术与传感器,1993(3):17[4]滕红华.真空吸盘吸持物体的动力学分析.包装工程,2004(2):68,83[5]郭维强,蒲如平,韩秀杰等.真空发生器抽吸机理与性能的分析研究.真空,2003(6):54[6]李泽,刘俊杰.罗茨真空泵及其使用.四川科学技术出版社,1985[7]D.Cheng,符锡理.用低温吸附泵获得低压强.导弹与航天运载技术,1992(4):18.[8]SchmalZ(中国)有限公司.VacuumclampingtechnologyforcNcmachinetOOlS,2006.{L第04期数控机床市场?115?。
加工中心常用的30种装夹方法
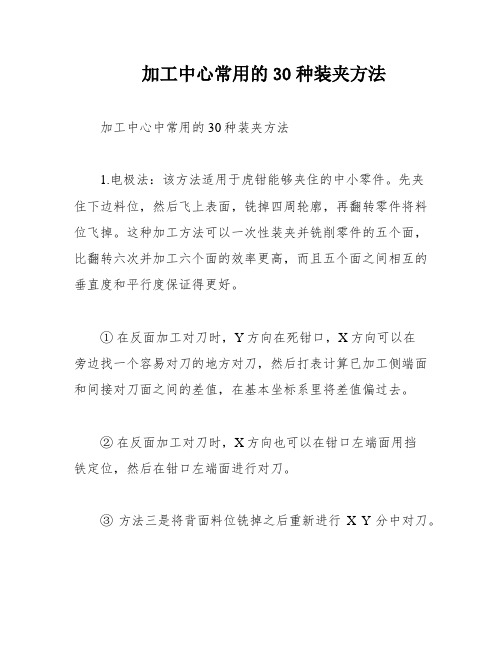
加工中心常用的30种装夹方法加工中心中常用的30种装夹方法1.电极法:该方法适用于虎钳能够夹住的中小零件。
先夹住下边料位,然后飞上表面,铣掉四周轮廓,再翻转零件将料位飞掉。
这种加工方法可以一次性装夹并铣削零件的五个面,比翻转六次并加工六个面的效率更高,而且五个面之间相互的垂直度和平行度保证得更好。
①在反面加工对刀时,Y方向在死钳口,X方向可以在旁边找一个容易对刀的地方对刀,然后打表计算已加工侧端面和间接对刀面之间的差值,在基本坐标系里将差值偏过去。
②在反面加工对刀时,X方向也可以在钳口左端面用挡铁定位,然后在钳口左端面进行对刀。
③方法三是将背面料位铣掉之后重新进行X Y分中对刀。
④在主轴上吸百分表,回转一周就像一个分中棒,左右已加工端面压表一样,这样可以精确地分出X向的中心。
2.正反面掏料法:这种方法适用于加工中心和车床,避免了常规装夹力造成的薄壁变形。
该方法适用于拉伸轮廓类零件和不容易用常规方法装夹的薄壁零件,而且要求厚度方向有料位,宽度方向有足够的压板位置。
1)先飞上表面,只沿外轮廓走刀,再飞上表面把毛刺翻下来。
2)然后翻转工件,沿截面走刀,将截面料位掏掉,剩下0.1的正反面连接厚度,手工去除多余的料块。
3.换压板法:当零件比较大时,可以采用交替换压板的方法飞上表面。
4.中间锁螺栓铣四周,换压板铣内腔:针对铣框类薄板零件,由于这类零件中间的料容易拱起,因此需要采用中间锁螺丝的方法。
5.层叠法:适用于薄板类零件,厚度只有0.5-1mm,可以再加一块薄铝板压上去铣,最后换一下压板铣掉连接筋。
6.中间锁沉头螺栓:飞上表面,铣四周轮廓。
7.倒掉法:从背面加工装板,锁紧拉住工件。
8.侧顶法:1)当侧面大于45度时,可以采用压板顶紧的方法飞上表面。
2)当侧面有螺丝时,可以采用螺丝顶紧的方法。
3)可以铣放置零件的长方形工装槽,然后在侧面用螺丝顶紧。
9.工艺搭台法:适用于异形、避开无法常规装夹易变形的支架类零件或薄壁盘类零件。
CNC操作指引(最新)
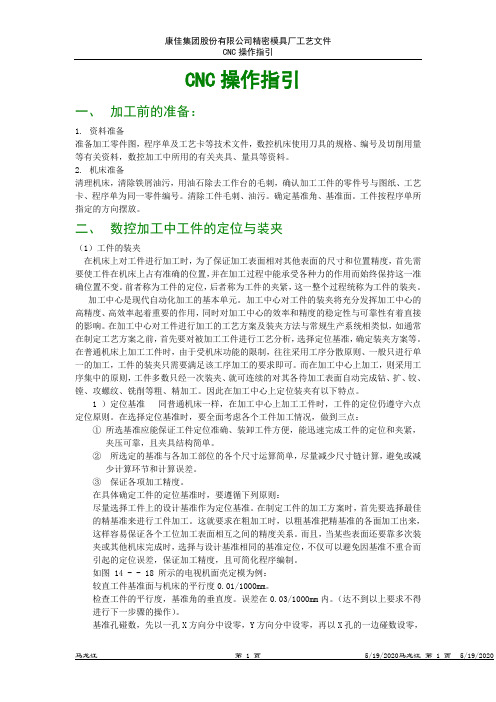
CNC操作指引一、加工前的准备:1.资料准备准备加工零件图,程序单及工艺卡等技术文件,数控机床使用刀具的规格、编号及切削用量等有关资料,数控加工中所用的有关夹具、量具等资料。
2.机床准备清理机床,清除铁屑油污,用油石除去工作台的毛刺,确认加工工件的零件号与图纸、工艺卡、程序单为同一零件编号。
清除工件毛刺、油污。
确定基准角、基准面。
工件按程序单所指定的方向摆放。
二、数控加工中工件的定位与装夹(1)工件的装夹在机床上对工件进行加工时,为了保证加工表面相对其他表面的尺寸和位置精度,首先需要使工件在机床上占有准确的位置,并在加工过程中能承受各种力的作用而始终保持这一准确位置不变。
前者称为工件的定位,后者称为工件的夹紧,这一整个过程统称为工件的装夹。
加工中心是现代自动化加工的基本单元。
加工中心对工件的装夹将充分发挥加工中心的高精度、高效率起着重要的作用,同时对加工中心的效率和精度的稳定性与可靠性有着直接的影响。
在加工中心对工件进行加工的工艺方案及装夹方法与常规生产系统相类似,如通常在制定工艺方案之前,首先要对被加工工件进行工艺分析,选择定位基准,确定装夹方案等。
在普通机床上加工工件时,由于受机床功能的限制,往往采用工序分散原则、一般只进行单一的加工,工件的装夹只需要满足该工序加工的要求即可。
而在加工中心上加工,则采用工序集中的原则,工件多数只经一次装夹、就可连续的对其各待加工表面自动完成钻、扩、铰、镗、攻螺纹、铣削等粗、精加工。
因此在加工中心上定位装夹有以下特点。
1 )定位基准同普通机床一样,在加工中心上加工工件时,工件的定位仍遵守六点定位原则。
在选择定位基准时,要全面考虑各个工件加工情况,做到三点:①所选基准应能保证工件定位准确、装卸工件方便,能迅速完成工件的定位和夹紧,夹压可靠,且夹具结构简单。
②所选定的基准与各加工部位的各个尺寸运算简单,尽量减少尺寸链计算,避免或减少计算环节和计算误差。
③保证各项加工精度。
铣削的工件安装方法
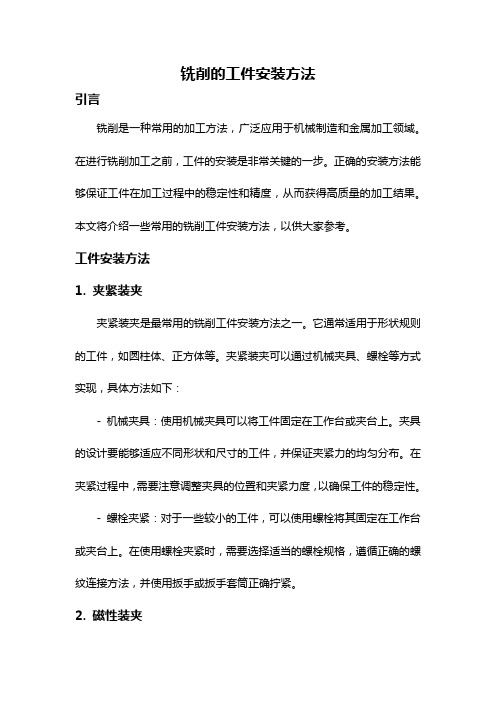
铣削的工件安装方法引言铣削是一种常用的加工方法,广泛应用于机械制造和金属加工领域。
在进行铣削加工之前,工件的安装是非常关键的一步。
正确的安装方法能够保证工件在加工过程中的稳定性和精度,从而获得高质量的加工结果。
本文将介绍一些常用的铣削工件安装方法,以供大家参考。
工件安装方法1. 夹紧装夹夹紧装夹是最常用的铣削工件安装方法之一。
它通常适用于形状规则的工件,如圆柱体、正方体等。
夹紧装夹可以通过机械夹具、螺栓等方式实现,具体方法如下:- 机械夹具:使用机械夹具可以将工件固定在工作台或夹台上。
夹具的设计要能够适应不同形状和尺寸的工件,并保证夹紧力的均匀分布。
在夹紧过程中,需要注意调整夹具的位置和夹紧力度,以确保工件的稳定性。
- 螺栓夹紧:对于一些较小的工件,可以使用螺栓将其固定在工作台或夹台上。
在使用螺栓夹紧时,需要选择适当的螺栓规格,遵循正确的螺纹连接方法,并使用扳手或扳手套筒正确拧紧。
2. 磁性装夹磁性装夹是一种非接触式的工件安装方法,适用于某些不适合夹紧的工件。
这种方法利用磁性力将工件固定在工作台上,具有快速、方便、灵活等优点。
具体方法如下:- 磁台:使用磁台可以产生一定的磁力,将工件吸附在工作台上。
磁台的选型要与工件的磁性相匹配,以确保工件能够稳定地固定在工作台上。
在使用磁台时,还需注意工件表面的平整度和清洁度,以确保充分的吸附力。
3. 急速接口急速接口是一种专门设计用于快速更换工件的安装方法。
它主要应用于多品种、小批量的生产环境中,能够大大提高工作效率。
具体方法如下:- 急速接口装夹:使用急速接口装夹系统,可以实现工件的快速安装和卸载。
这种系统通常由快速接头、定位销、夹具等组成。
在安装时,只需将工件与接头对应插入,然后通过夹具固定即可。
在卸载时,只需释放夹具,即可快速卸载工件。
结论工件的安装是铣削加工中非常重要的一步。
正确的安装方法能够保证工件的稳定性和加工精度,产生高质量的加工结果。
本文介绍了夹紧装夹、磁性装夹和急速接口等常用的铣削工件安装方法。
机加工工艺--机加工加工方法

4. 钻削的应用
钻孔主要用于粗加工。如螺钉孔、油孔、内螺纹底孔等。 单件、小批生产中、小型工件上的小孔(D<13mm),
常用台式钻床加工。 中、小型工件上较大的孔(D<50mm),常用立式钻床加工。
大型工件上的孔,则采用摇臂钻床加工。
回转体工件上的孔,多在车床上加工。
二、扩孔和铰孔
1. 扩孔 用扩孔钻对工件上已有的孔进行扩大加工。
ae
ae
端铣法可以通过 调整铣刀和工件 的相对位置,调 节刀齿切入和切 出时的切削厚度, 从而达到改善铣 削过程的目的。
铣削工艺特点及应用
1. 铣削特点
1)生产率高(多齿刀具、速度高); 2)散热条件好; 3)容易产生振动。
2. 铣削的应用
主要加工平面。同时可加工沟槽、成形面、切断等。
§5
磨削加工
第二章 切削加工方法
§1 车削加工
车削 — 用车刀在车床上加工工件的工艺过程。 加工精度:IT8~IT7,表面粗糙度:Ra=1.6~6.3um 主运动 — 工件的旋转运动。 进给运动 — 刀具的直线运动。
所以:车削加工适宜各种回转体表面的加工。
普通车床 — 适于各种中、小 型轴、盘、套类零件的单件、 小批量生产。 转塔式六角车床 — 适于加工 零件尺寸较小、形状较复杂的 中、小型轴、盘、套类零件。 立式车床 — 适于直径较大、 长度较短的重型零件。 (L/D=0.3~0.8) 数控车床 — 适于多品种、 小批量生产复杂形状的零件。
内圆磨与铰孔和拉孔相比较:
① 可以加工淬硬工件的孔; ② 不仅能保证孔本身的尺寸精度和表面质量,还可以提 高孔的位置精度和形状精度。 ③ 生产率低比铰孔低,比拉孔更低。
磨孔一般仅用于淬硬工件孔的精加工。
通用铣床的操作方法
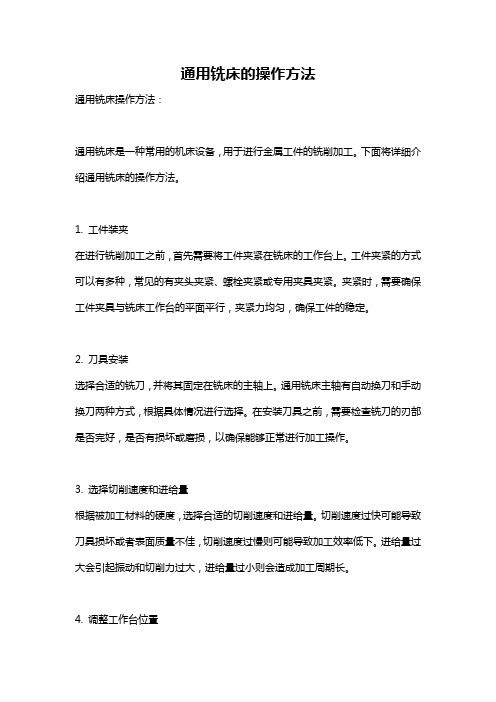
通用铣床的操作方法通用铣床操作方法:通用铣床是一种常用的机床设备,用于进行金属工件的铣削加工。
下面将详细介绍通用铣床的操作方法。
1. 工件装夹在进行铣削加工之前,首先需要将工件夹紧在铣床的工作台上。
工件夹紧的方式可以有多种,常见的有夹头夹紧、螺栓夹紧或专用夹具夹紧。
夹紧时,需要确保工件夹具与铣床工作台的平面平行,夹紧力均匀,确保工件的稳定。
2. 刀具安装选择合适的铣刀,并将其固定在铣床的主轴上。
通用铣床主轴有自动换刀和手动换刀两种方式,根据具体情况进行选择。
在安装刀具之前,需要检查铣刀的刃部是否完好,是否有损坏或磨损,以确保能够正常进行加工操作。
3. 选择切削速度和进给量根据被加工材料的硬度,选择合适的切削速度和进给量。
切削速度过快可能导致刀具损坏或者表面质量不佳,切削速度过慢则可能导致加工效率低下。
进给量过大会引起振动和切削力过大,进给量过小则会造成加工周期长。
4. 调整工作台位置根据需要的加工位置,通过手动或自动控制方式,调整铣床的工作台位置。
工作台的上下、前后和左右移动,可以通过控制手柄或操作面板上的按钮进行调整。
5. 开关机床在进行加工操作前,需要打开铣床的电源开关,并确保各个部件运转正常。
在开机之前,需要检查机床上的刀具、夹具以及工件是否安装稳定,并且没有任何杂物。
在关闭铣床之前,需要先停止铣刀的转动,并将工作台和刀具回到初始位置。
6. 执行加工操作根据加工需求,通过手动或自动的方式,将刀具和工作台移动到开始加工的位置。
开启铣刀,同时控制工作台沿着所需的路径进行移动,以进行切削加工。
在进行加工过程中,需要不断检查加工质量和刀具状态,及时调整切削参数和加工路径。
7. 加工结束和清理当加工任务完成后,需要关闭铣床的电源开关,并将刀具和工作台回到初始位置。
然后,将工件从夹具上取下,并进行测量和检查,以确保加工质量。
最后,清理铣床的切屑和废液,以保持机床和工作环境的整洁。
需要注意的是,在进行通用铣床操作时,要遵循以下安全规范:1. 穿戴好防护装备,如手套、护目镜和工作服,以避免受伤。
- 1、下载文档前请自行甄别文档内容的完整性,平台不提供额外的编辑、内容补充、找答案等附加服务。
- 2、"仅部分预览"的文档,不可在线预览部分如存在完整性等问题,可反馈申请退款(可完整预览的文档不适用该条件!)。
- 3、如文档侵犯您的权益,请联系客服反馈,我们会尽快为您处理(人工客服工作时间:9:00-18:30)。
2)、不对称端铣 如图3-1(b) 、(c)所示,用面铣刀铣削平面时, 工件铣削层宽度在铣刀中心两边不相等的 铣削方式,称为不对称端铣。
图3-1 对称铣削与不对称铣削 (a)对称铣削;(b)非对称逆铣;(c)非对称顺铣
• 不对称端铣时,当进刀部分大于出刀部分时称 为逆铣。如图3-1(b) 所示;反之称为顺铣,如图 3-1(c)所示。顺铣时,同样有可能拉动工件台, 造成严重后果,故一般不采用。端铣时,垂直 铣削力的大小和方向与切削方式无关。另外用 端铣法逆铣时,刀齿开始切入时的切周厚度较 薄,切削刃受到的冲击较小,并且切削刃开始 切入时无滑动阶段,故可提高铣刀的寿命。用 端铣法作顺铣时的优点是切削在切离工件时较 薄,所以切屑容易去掉,切削刃切入时切屑较 厚,不致在冷硬层中挤刮,尤其对容易产生冷 硬现象的材料,如不锈钢,则更为明显。
(3)端铣时刀齿有主、副切削刃同时工作, 主切削刃切去大部分余量,副切削刃起修 光作用,齿刃负荷分配合理,刀具寿命较 长,且加工面的表面粗糙度值也较小;而 周铣时只有圆周上的主切削刃工作,不但 无法消除已加工表面的残留面积,而且铣 刀装夹后的径向跳动了会反映到工件表面 上。
(4)面铣刀便于镶装硬质合金刀片进行高速 铣削和阶梯铣削,生产效率高,铣削质量 也较好;而圆柱铣刀镶装硬质合金刀片比 较困难。
• (5)铣削宽度较大的工件时,圆柱铣刀一 般要接刀铣削,故留有接刀痕迹;在端面 铣削时,则可用盘形面铣刀一次铣出工件 全宽度。
• (6)圆柱铣刀可采用大刃倾角,以充分发 挥刃倾角在铣削过程中的作用,对铣削难 加工材料(如不锈钢、耐热合金等)有一 定效果。
• 综上所述,一般情况下,端铣时的生产效 率和铣削质量都比周铣时高。所以铣平面 时,应尽可能采用端铣。但是要具体情况 具体分析,目前工厂中卧式铣床使用得很 普遍,这是因为它的万能性好,便于实现 组合铣削,以提高铣削效率。此外,在铣 削韧性很大的不锈钢等材料时,也可考虑 采用大螺旋角铣刀进行周铣
4、端铣时的顺铣与逆铣
端铣时,根据铣刀和工件的相对位置不同, 可分为对称铣削和不对称铣削。 1)、对称铣削 图3-1(a)所示为用面铣刀铣平面时,铣刀处于 工件铣削层宽度中间位置的铣削方式,称 为对称端铣。
• 若用纵向工作台进给作对称铣削,工件的 削层宽度铣刀轴线的两边各占一半。左半 部为进刀部分,是逆铣,右半部分为出刀 部分,是顺铣。使作用在工件上的纵向分 力在中分线两边大小相等,方向相反,所 以工作台在进给方向不会产生突然拉动现 象。但是,此时作用在工作台横向进给方 向上的分力较大,会使工作台沿横向产生 突然拉动,因此铣削前必须紧固横向工作 台。基于上述原因,用面铣刀进行对称铣 削时,只适用于加工工短而宽或较厚的工 件,不宜铣削狭长或较薄的工件。
一、工件在平口钳中的装夹 对于中小尺寸、形状简单的工件,一般 装夹在平口钳中。为了保证平口钳在铣床 工件台上的正确位置,应当把平口钳底面 的定向键靠紧在台面当中T形槽的一个侧面。 如果没有定向槽或者是具有回转刻度盘的 平口钳,则可用直角尺或者划针来校正虎 钳的固定钳口。对于安装精度要求比较高 的场合,可使用百分表校正。
• 在平口钳中装夹工件时,工件放置的位置 要适当,既要夹得紧,以要使工件在加工 中稳定,并且要防止工件被夹变形。
• 工件装夹时要注意以下几点:
1、平口钳一定要加紧 2、工件要在平口钳敲紧 3、一定要放垫铁 4、垫铁以及钳口要刷干净
三、讲解铣削方法: 周铣和端铣 1、周铣。 周铣是用铣刀周边齿刃进行的铣削。周 铣平面时平面度的好坏,主要取决于铣刀 的面柱素线是否直,因此在精铣平面时, 铣刀的圆柱度一定要好。
• 平口钳的定位面是导轨面和固定钳口,在 平口钳中装夹工件时,必须使工件的基准 面贴紧这两个面。对于较薄的工件,可在 工件下面垫上经过磨削的平行垫铁。在夹 紧工件时,要用铜棒或者榔头柄轻轻敲打 工件,使工件的下面贴紧。
• 如果工件上用平口钳平紧的两个面,一个 是已加工的面,另一个是毛坯面,为了保 证铣出的平面与已加工面垂直,可使已加 工面和固定钳口接触,并在活动钳口和毛 坯面之间垫一根圆棒或者一块撑板
2、端铣。 端铣是用铣刀端面齿刃进行的铣削。用端 铣铣出的平面Байду номын сангаас其平面度的好坏,主要取 决于铣床主轴轴线与进给方向的垂直度。
3、周铣和端铣的比较 (1)面铣刀的装夹刚度较好,铣削时振动小; 而圆柱铣刀刀杆较长,轴径较小,容易产 生弯曲变形及振动。
(2)端铣时同时工作的齿数比周铣多,工作 较平稳。这时因为端铣时刀齿在铣削层宽 度的范围内工作,而周铣时刀齿仅在铣削 层深度的范围内工作,一般情况下铣削层 宽度要比铣削层深度大得多,所以面铣刀 和工件的接触面较大,同时工作的齿数多, 铣削力波动小。为减少周铣时的振动,可 选择大螺旋角铣刀来弥补这一缺点。