9600Kw6轴电力机车牵引电机球铁端盖无冒口铸造工艺应用
六轴9600kW货运电力机车车体研究

终 点 时 最 大 不 超 过 33 0k 0 N。
( )动 态吸收 能力最 少不低 于 4 0k 。 3 5 J 钩缓 系统选 用 了小 间隙的 1 A 型 E级钢 车钩 和大 3 容量 的 QKX 0 1 0型 弹性胶 泥缓 冲器 。
1 0k / 2 i h速 度 等 级 6轴 9 6 0 k 货 运 机 车 是 我 n 0 W
前 窗 等 附 属 部 件 , 图 2所 不 。 如
国 目前 单 轴 功 率 最 大 的 重 载 货 运 机 车 , 车 体 能 在 其 4 ℃ 时使 用 , 承 受 30 0 k 的压 缩 载 荷 和 25 0 0 能 0 N 0 k 的拉 伸载 荷 。以株 洲 电力 机 车有 限公 司 HX 1 N D B车 体 为例 , 1 0k h速度 等 级六 轴 96 0k 货运 机 车 对 2 m/ 0 W 车 体进 行介 绍 。 车 体是 电力 机 车的 主要机 械部 件 之 一 , 整个 车 体 是 以底 架 、 侧墙 、 机室 等组 焊成 一个 整 体 承载 结 构 , 图 司 如
图 2 H 。 B机 车 车 体 X 1
图 3 车 体 纵 向 力传 递
黄 成 荣 ( 9 6 ) , 苏 阜 宁 人 , 究 员 ( 稿 日期 :0 0 0 ~ 2 ) 1 6一 男 江 研 收 2 1 4 7
2
铁 道 机 车 车 辆
第 3 卷 O
式 , 部 由钢板 及钢 板压型件 组焊 而成 的焊接结 构 。底 全 架采用 了贯通式 中央 纵 梁 的框 架结 构 , 由牵 引梁 、 它 枕
图 1 车 体 承 载 结 构
211261552_运行10_年的牵引电机铝端盖性能评估

文章编号:2095-6835(2023)10-0090-03运行10年的牵引电机铝端盖性能评估廉永峰,吕志成,范小晶,姬晓峰(中车永济电机有限公司,陕西西安710000)摘要:为评估已运行10年的牵引电机铝制端盖相关性能状况,通过新旧件力学性能对比、疲劳极限对比、S-N曲线对比,确定该铝端盖性能状况,同时针对试验结果存在问题进行残余应力检测。
研究结论可为后续牵引电机铝制端盖运行提供数据支持,对类似产品的相关研究具有参考意义。
关键词:牵引电机;铝端盖;S-N曲线;残余应力中图分类号:U279文献标志码:A DOI:10.15913/ki.kjycx.2023.10.026随着中国铁路行业的快速发展,列车的行驶速度越来越快,车辆逐渐向轻量化方向发展。
牵引电机为满足轻量化要求,传动端、非传动端结构一般采用铝端盖和锻钢轴承室结构。
在前期设计及试验验证中,已对该结构的力学性能进行仿真分析并进行模拟长寿命试验,满足服役期间的可靠性及安全性要求。
但该类铝制部件长期运行后是否可靠、性能是否发生变化、是否存在潜在风险仍是需要关注的问题。
这些问题是决定牵引电机在全寿命周期内、在检修周期内能否继续可靠运行的关键。
目前,牵引电机在运行两三年后需进行检修,对牵引电机轴承进行更换,对其他部件进行相关检测及更换。
由于牵引电机传动端、非传动端盖为铝制部件,仅能对尺寸及关键部位进行探伤,无法评估其整体性能。
在该部件运行10年后是否能满足后续运行要求、性能是否发生变化,这些问题需进行相关研究。
1检测项目为评估铝端盖相关性能,主要通过对新造部件与服役10年的部件进行性能对比,性能对比涉及成品部件材料自身的力学性能检测、疲劳极限测定、S-N曲线测定及残余应力测试。
成品材料自身的力学性能检测,主要指标为抗拉强度R m、规定塑性延伸强度R p0.2、断后伸长率A(%)、断面收缩率Z(%)。
疲劳极限为在交变循环大至无限次(该铝制部件采用循环次数为107)所承受的最大应力值,疲劳极限的测试采用升降法。
机车轴箱体外端盖螺栓拧紧工艺研究
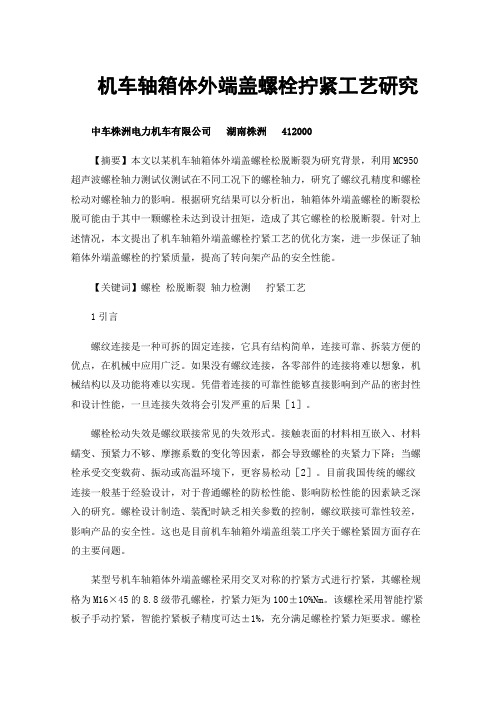
机车轴箱体外端盖螺栓拧紧工艺研究中车株洲电力机车有限公司湖南株洲 412000【摘要】本文以某机车轴箱体外端盖螺栓松脱断裂为研究背景,利用MC950超声波螺栓轴力测试仪测试在不同工况下的螺栓轴力,研究了螺纹孔精度和螺栓松动对螺栓轴力的影响。
根据研究结果可以分析出,轴箱体外端盖螺栓的断裂松脱可能由于其中一颗螺栓未达到设计扭矩,造成了其它螺栓的松脱断裂。
针对上述情况,本文提出了机车轴箱外端盖螺栓拧紧工艺的优化方案,进一步保证了轴箱体外端盖螺栓的拧紧质量,提高了转向架产品的安全性能。
【关键词】螺栓松脱断裂轴力检测拧紧工艺1引言螺纹连接是一种可拆的固定连接,它具有结构简单,连接可靠、拆装方便的优点,在机械中应用广泛。
如果没有螺纹连接,各零部件的连接将难以想象,机械结构以及功能将难以实现。
凭借着连接的可靠性能够直接影响到产品的密封性和设计性能,一旦连接失效将会引发严重的后果[1]。
螺栓松动失效是螺纹联接常见的失效形式。
接触表面的材料相互嵌入、材料蠕变、预紧力不够、摩擦系数的变化等因素,都会导致螺栓的夹紧力下降;当螺栓承受交变载荷、振动或高温环境下,更容易松动[2]。
目前我国传统的螺纹连接一般基于经验设计,对于普通螺栓的防松性能、影响防松性能的因素缺乏深入的研究。
螺栓设计制造、装配时缺乏相关参数的控制,螺纹联接可靠性较差,影响产品的安全性。
这也是目前机车轴箱外端盖组装工序关于螺栓紧固方面存在的主要问题。
某型号机车轴箱体外端盖螺栓采用交叉对称的拧紧方式进行拧紧,其螺栓规格为M16×45的8.8级带孔螺栓,拧紧力矩为100±10%Nm。
该螺栓采用智能拧紧板子手动拧紧,智能拧紧板子精度可达±1%,充分满足螺栓拧紧力矩要求。
螺栓拧紧时与弹垫配合,螺纹部分不涂抹螺纹紧固胶和润滑脂。
在6颗轴箱体外端盖螺栓拧紧后,使用镀锌铁丝两两相串并成“8”字形绞紧防松。
为了分析该轴箱体外端盖螺栓断裂松脱的原因,本文以某型号机车外端盖螺栓松脱轴箱体为研究对象,利用超声波螺栓轴力测试仪,分析螺纹孔精度和螺栓松动对螺栓轴力的影响。
基于数值模拟的160km动力车牵引座铸造工艺研究

使用性能。
本文采用ProCAST 铸造模拟软件,对牵引座进行流场和温度场的计算,分析铸件的凝固过程,依据模拟结果提出改进措施,优化铸件工艺,大大缩短了试制生产周期,最终获得质量合格的铸件。
图1 牵引座铸造缺陷1. 牵引座的技术要求及原铸造工艺160km 动力集中动车组牵引座(以下简称牵引座)铸件结构如图2a 所示,该铸件为壁厚均匀的中型铸件,品质要求满足T B/T 2942—2015标准,铸件质量为110kg ,材质为E 级钢,化学成分为:w C ≤0.32%、w Si ≤1.50%、w M n ≤1.85%、w P ≤0.035%、w S ≤0.035%、w C r =0.30%~0.60%、w N i =0.35%~0.60%,CE ≤0.88%。
加工面内部超声波检测,非加工面磁力检。
根据技术条件要求,选择碱性酚醛树脂砂造型,中频炉熔炼钢液,3t 底注式钢包浇注。
经查阅相关资料,反复研究对比,提出如图2b 所示工艺设计方案。
2. 牵引座实体建模及模拟参数选择应用C AT I A 软件对牵引座进行实体建模,铸造工艺实体模型如图2所示,铸件及浇冒口系统采用相同的网格尺寸,网格尺寸取10mm ×10mm ×10mm ,最终铸件划分网格总数为1226453个,其中本体网格数65380个,合金总网格数为1161073个。
在模拟过程中,热物理参数的选择合理与否,对模拟计算的准确性有着决定性影响。
模拟时,采用ProCAST 模拟软件数据库中E 级钢,该钢种液相线温度、固相线温度、热辐射系数、液相收缩率,各种物性参数齐全,有效保证了模拟的精度。
浇注工艺参数:根据相关文献及生产条件计算所得浇注温度为1580℃,牵引座浇注时间30s ,铸型初始温度20℃。
3. 数值模拟结果分析(1)流动过程计算结果 使用Procast 模拟软件对原铸造工艺进行铸造模拟,观察分析流动过程模拟结果。
流动过程温度场反映金属液在铸造型腔中流动时的温度变化过程,根据流动过程温度场可以发现铸件充型过程中可能产生的缺陷。
HXD1C型机车牵引电机球墨铸铁端盖铸造工艺研究
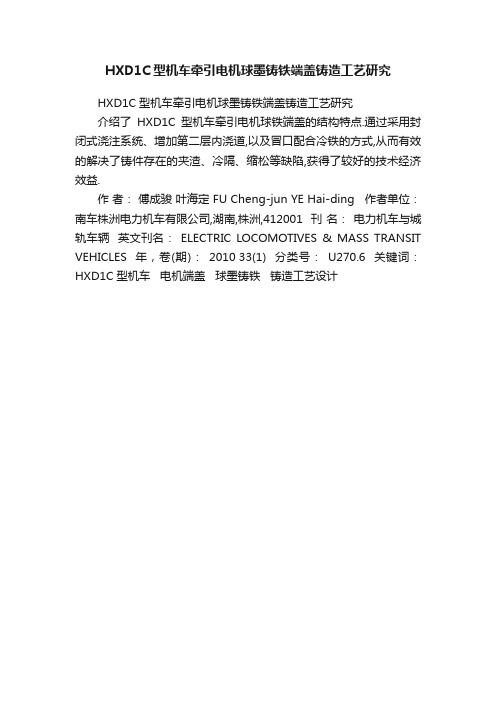
HXD1C型机车牵引电机球墨铸铁端盖铸造工艺研究
HXD1C型机车牵引电机球墨铸铁端盖铸造工艺研究
介绍了HXD1C型机车牵引电机球铁端盖的结构特点.通过采用封闭式浇注系统、增加第二层内浇道,以及冒口配合冷铁的方式,从而有效的解决了铸件存在的夹渣、冷隔、缩松等缺陷,获得了较好的技术经济效益.
作者:傅成骏叶海定 FU Cheng-jun YE Hai-ding 作者单位:南车株洲电力机车有限公司,湖南,株洲,412001 刊名:电力机车与城轨车辆英文刊名:ELECTRIC LOCOMOTIVES & MASS TRANSIT VEHICLES 年,卷(期):2010 33(1) 分类号:U270.6 关键词:HXD1C型机车电机端盖球墨铸铁铸造工艺设计。
发热保温冒口在铁路机车轴箱体上的应用

W ANG F e n g , CHEN Ka i , WU J i a n - mi n
Ke y wo r d s: e x o t h e r mi e - i n s u l a t i n g r i s e r ; l o c o mo t i v e; a x l e h o u s i n g h o d y
1 应用 背景
笔者公司为铁路机车铸钢件生产企业 , 铸钢 件生产量大 , 产品种类多 , 质量要求很高 , 以前产
u s e d i n t h e o r i g i n a l c a s t i n g me t h o d a n d a s t h e r e s u l t . t h e X— r a y d e t e c t i o n s h o we d t h a t a b o u t 6 % c a s t i n g s h a v i n g s h r i n k a g e d e f e c t s h i g h e r t h a n I I I g r a d e . Af t e r c h a n g i n g t h e c o l d is r e r s i n t o t h e e x o t h e r mi c — i n s u l a t i n g r i s e r s , t h e x — r a y d e t e c t i o n r e s u l t o f 3 6 0 0 p c s o f c a s t i n g s s h o we d t h a t t h e c a s t i n g s h a v i n g s h in r k a g e d e f e c t s h i g h e r t h a n I I I g r a d e h a s b e e n r e d u c e d t o 1 . 5 %. P r o d u c t i o n r e s u l t s h o we d t h a t u s i n g e x o t h e r mi c i r s e r s i n c r e a s e d t h e f e e d i n g e f f e c t o f r i s e r s , e f f e c t i v e l y e l i mi n a t e d s h in r k a g e d e f e c t s o f c a s t i n g s , a s we l l a s r e d u c e d p r o d u c t i v e c o s t a n d i n c r e a s e d e c o n o mi c e ic f i e n c y .
分析机车电机盖的铸造工艺优化途径
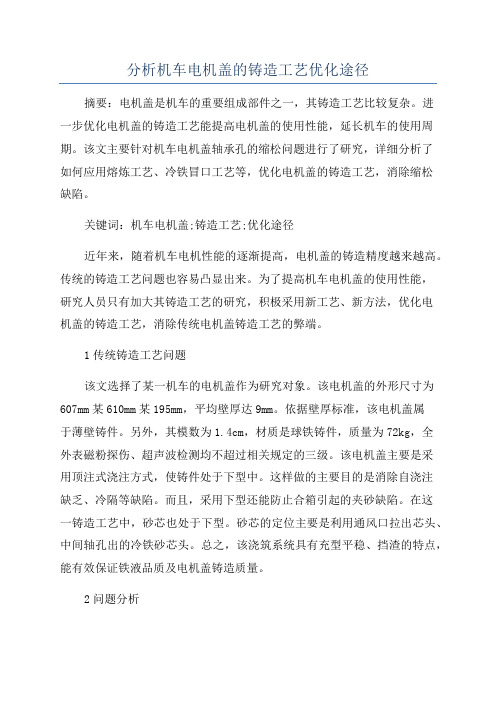
分析机车电机盖的铸造工艺优化途径摘要:电机盖是机车的重要组成部件之一,其铸造工艺比较复杂。
进一步优化电机盖的铸造工艺能提高电机盖的使用性能,延长机车的使用周期。
该文主要针对机车电机盖轴承孔的缩松问题进行了研究,详细分析了如何应用熔炼工艺、冷铁冒口工艺等,优化电机盖的铸造工艺,消除缩松缺陷。
关键词:机车电机盖;铸造工艺;优化途径近年来,随着机车电机性能的逐渐提高,电机盖的铸造精度越来越高。
传统的铸造工艺问题也容易凸显出来。
为了提高机车电机盖的使用性能,研究人员只有加大其铸造工艺的研究,积极采用新工艺、新方法,优化电机盖的铸造工艺,消除传统电机盖铸造工艺的弊端。
1传统铸造工艺问题该文选择了某一机车的电机盖作为研究对象。
该电机盖的外形尺寸为607mm某610mm某195mm,平均壁厚达9mm。
依据壁厚标准,该电机盖属于薄壁铸件。
另外,其模数为1.4cm,材质是球铁铸件,质量为72kg,全外表磁粉探伤、超声波检测均不超过相关规定的三级。
该电机盖主要是采用顶注式浇注方式,使铸件处于下型中。
这样做的主要目的是消除自浇注缺乏、冷隔等缺陷。
而且,采用下型还能防止合箱引起的夹砂缺陷。
在这一铸造工艺中,砂芯也处于下型。
砂芯的定位主要是利用通风口拉出芯头、中间轴孔出的冷铁砂芯头。
总之,该浇筑系统具有充型平稳、挡渣的特点,能有效保证铁液品质及电机盖铸造质量。
2问题分析首先,铸件的工艺实施多是由机械完成,不存在实施缺陷。
其次,从铸件熔炼过程考虑。
该电机盖的铁液熔炼温度、出炉温度、浇注温度等均处于标准范围内。
显然,熔炼过程并无过失。
再者,从其中化学元素的占比考虑。
在对铸件的化学成分、石墨检测过后发现其出碳量在4.48%时,也就是在标准范围内时,铸件的缩松缺陷比较少,且铸件球化效果也非常好。
显然,这也并非是化学成分造成的铸件缩松。
最后,从冷铁、冒口的设计方面考虑。
上文中已经描述出了其设计、摆放情况。
对此,我们可利用代数计算软件Magmaoft对其凝固过程进行模拟、分析。
HXD2C型机车6A系统牵引电机非齿端轴承温升报警探讨(论文)

HXD2C型机车6A系统牵引电机非齿端轴承温升报警探讨(论文)HXD2C型机车6A系统牵引电机非齿端轴承温升报警探讨** (**铁路局 **机务段 ** 471002)摘要:针对HXD2C型机车运用中出现的6A系统(机车车载安全防护系统)2/3/4/5轴牵引电机非齿端轴承温升报警情况的原因进行分析,结合牵引电机结构及其通风冷却系统特点,提出故障处理方案及预防措施。
关键词:HXD2C型机车;6A系统;牵引电机轴承;温升报警;预防措施;HXD2C型机车自20__年8月陆续调拨我段使用以来,发生多起6A系统(机车车载安全防护系统)报2/3/4/5轴牵引电机非齿端轴承温升报警故障。
根据我段统计,自20__年8月到11月间,HXD2C型机车6A系统报牵引电机非齿端轴承温升报警189台次,占6A系统报警信息的36%,且多次因该故障扣临修,但经我段检修车间顶轮检测及电机厂家、唐智公司检查确认,牵引电机轴承并无异常,由此严重影响我段机车检修效率及机车供应。
1.HXD2C型机车驱动装置及故障诊断介绍 1.1 HXD2C型机车驱动装置特点配属我段HXD2C型机车采用永济电机厂YJ90A型牵引电机。
该电机为三相六极鼠笼式异步电机,以鼻式悬挂方式安装在机车转向架上。
电机传动端采用NU2322圆柱滚子轴承,采用机车齿轮箱内的齿轮油作为润滑剂润滑;非传动端采用NJ2218+HJ2218圆柱滚子轴承,采用MOBILI THSHC100润滑脂润滑。
电机采用轴向强迫通风冷却方式,冷却风从传动端的进风口进入,经由定子铁心通风孔、转子铁心通风孔、定转子间的气隙后,从非传动端轴向出风口排出;同时,从传动端进风口进入的冷却风,通过传动端端盖上的三个通风孔,使齿轮箱内的齿轮油具有流向电机传动端轴承的压力,从而提高传动端轴承的润滑效果。
1.2 HXD2C型机车牵引电机通风冷却系统 HXD2C型机车牵引电机通风系统采用独立通风方式,在机车机械间内前后斜对称各布置两台牵引电动机通风机。
- 1、下载文档前请自行甄别文档内容的完整性,平台不提供额外的编辑、内容补充、找答案等附加服务。
- 2、"仅部分预览"的文档,不可在线预览部分如存在完整性等问题,可反馈申请退款(可完整预览的文档不适用该条件!)。
- 3、如文档侵犯您的权益,请联系客服反馈,我们会尽快为您处理(人工客服工作时间:9:00-18:30)。
9600kw6轴电力机车牵引电机球铁端盖铸造工艺研究
摘要:用传统铸造工艺生产电机端盖球铁件,其方案为铸件厚大部位朝上,并在其上设施顶缩颈冒口,底注式浇注工艺。
实践表明用这种工艺,铸件厚大部位易产生缩孔、缩松。
通过对缩松、缩孔产生机理分析,将铸件最厚部位朝下,设置顶注式浇注系统,用浇注系统当冒口来补缩铸件的早期液态收缩。
凝固中后期利用石墨化膨胀,抵消液态收缩,实现了无冒口铸造,获得致密无缺陷铸件。
端盖球铁件无冒口铸造的条件为,铸件最大模数必须大于2.28cm ,这样石墨化膨胀充分,可弥补铸件凝固期间的液态收缩。
关键词: 电机端盖 球墨铸铁 无冒口铸造工艺
9600Kw6轴电力机车是株洲电力机车有限公司自主研发的新一代大功率交流传动牵引电力机车。
牵引电机是整个电力机车的心脏,它的质量优劣关系到是整个机车的运行安全。
端盖是牵引电机上的一个重要球铁铸件,
该铸件要承受着电机传动载荷,同时还要求具有减振功效,力学性能要求零下40度的冲击值达12 J ,同时,检查要求极高,不但要做表面磁粉,而且要拍X 光片,不允许有任何缺陷,铸件出现缺陷,不得焊补,只得做报废处理。
笔者
在端盖球墨铸铁件的铸造工艺设计上做了深入研究,探讨了端盖球铁铸件产生缩孔、缩松的机理,运用均衡凝固理论,实现了球铁铸件无冒口铸造,批量生产的端盖球铁件,经X 光片检查,件件致密,均未发现缩孔、缩松缺陷。
1、铸件结构与技术条件
端盖铸件,其结构尺寸见图1。
材质为QT400-18L ,毛坯重81kg 。
其化学性能、力学性能标准见表1和表2。
此铸件为端盖类铸件常见结构,该零件轴承室部位承受重载荷,内部质量要求高,射线探伤为1级。
局部尺寸如图2 ,铸件平均壁厚为12mm ,经计算,铸件最大模数为M=1.81cm 。
、 传统铸造工艺方案 2.1 工艺设计及结果
采用传统的球墨铸铁铸造工艺设计,即厚大部位朝上,便于设置顶缩颈冒口和集渣;整个铸件均放在上箱,避免了吊芯,方便了造型操作;底注式浇注系统,便于铁水平稳上升和型腔中气体的排出,端盖铸造工艺设计方案见图2所示。
表1 球铁化学成分%
图1 端盖铸件结构
为了保证铁液平衡而快速充型和减少对铸型的冲击,采用半封闭式浇注系统,各浇道比为∑F 直∶∑F 横∶∑F 内=1∶1.2∶0.5,各浇道尺寸如下:直浇道φ70mm ;横浇道 42/50×50(高)两道:内浇道 55 /60×10mm (高)四道。
浇注系统填充校核,横浇道充满有余,浇注系统具有挡渣能力。
端盖球铁样件浇注、经打磨后,做射线探伤发现,铸件厚大部位及冒口根部处存在缩孔、缩松缺陷。
经进一步破坏性加工验证,缺陷具体位置为厚大部位或拐角处,如图3、图4所示。
2.3 改进工艺设计及结果
并使热节转移至冒口颈部,能凝固,最终使铸件在冒口根部产生缩松。
位的结构来看,铸件热节被拐角分成两部分,在不利于自补和冒口补缩的不良温度场[2]。
基于以上分析,对原铸造工艺设计方案做两项改进:一是减小冒口颈尺寸;二是在厚大部位增加一圈外冷铁,调整温度场。
改进后的端盖铸造工艺设计方案见图5所示。
用改进铸造工艺方案进行了端盖批量生产,铸件经射线探伤,铸件以前存在的缩松缺陷消除了,但缩孔缺陷仍然存在,见图6所示。
量生产后,部分产品发现了气孔,且因气孔导致的废品率偏高。
分析原因,冷铁处理不到位,其表面氧化、是造成气孔的原因之一。
在大批量生产的条件下,冷铁表面质量不易控制,加冷铁不能完全消除缩孔,而且会带来气孔缺陷,此工艺方案仍然不能完全满足质量要求。
2.2 缺陷产生机理分析
铸件锥形体薄壁,散热面积也大,模数小,凝固时间短,所形成的石墨球没有充分时间长大,石墨化
膨胀量不足以完全抵消液态收缩。
在锥形体的顶部则是铸件的最厚部位,它相当于一个大冒口,凝固时间长,其中的铁液可直接补缩锥形体的液态收缩-石墨化膨胀叠加后剩余的体积亏缺。
由于冒口颈过小,凝固“冻结”过早,当厚大部位体积亏缺需要冒口补缩时,已无法从冒口中得到液态铁水,因此留下了缩孔。
3、无冒口铸造工艺方案
图4 端盖铸件顶面冒口颈下的缩孔
图6 端盖铸件冒口下的缩孔 图5 端盖铸造工艺设计改进方案示意图
3.1铸造工艺设计及结果
改变原端盖铸件铸造工艺分型方案,将整个铸件置于下箱,铸件最厚的部位放在最低位置,该厚大部位的模数M 为1.81cm 。
根据均衡凝固顶注优先的原则[1]
,铸件上不设冒口,浇注系统采用顶注式,并且兼作冒口。
铁水可通过顶注式浇注系统,经薄壁处补缩处于铸件最低、最厚部位的凝固早期液态收缩,其余液态收缩则依靠该部位石墨化膨胀来抵消。
铸造工艺方案如如图6所示。
浇注样件后,经过破坏性
加工,铸件厚大部位拐角处仍有一部位存在缩孔、缩松缺陷,级别为2级。
(同原方案)。
3.2 缺陷产生原因及解决措施
尽管用浇注系统通过锥形体薄壁能够补缩底部厚大部位早期液态收缩,但该部位石墨化膨胀的体积与铸件液态收缩的体积仍然有一定的差距,有可能处在临界状态。
该部位的模数为1.81cm ,要实现球墨铸铁件的无冒口铸造,铸件的模数须大于 工 艺方案。
方案一是将铸件拐角处拉平,见图7所示,调整后铸件模数
M=2.28cm ;方案二是将铸件拐角处拉平,局部尺寸增大,见图8所示,调整后铸件模数M=2.45cm 。
3.3 生产验证
用改进后的两种铸造工艺设计方案,进行了端盖球铁件
浇注试验。
铸件经射线探伤及破坏性加工检验,均无缩孔、缩松、气孔缺陷。
最后选定方案一,投入了批量生产,共浇注端盖球铁件30余件,经射线探伤检验,件件无缺陷,合格率达100%。
2 结论
1) 端盖球铁件的厚大部朝上,采用底注式浇注系统,会造成厚大部位形成事实上的“顶冒口”,它将补缩低于它的铸
件薄壁锥形体的液态收缩。
顶冒口颈太小,过早“冻结“,铸件厚大部位补缩薄壁锥形体所造成的液态铁水体积亏缺,得不到冒口有效补充。
石墨化膨胀体积一定,无法完全补偿,形成缩孔、缩松在所难免了。
通过加顶冒口的体积来解决缩孔、缩松缺陷是不经济的。
2) 将端盖球铁件厚大部位朝下,采用顶注式浇注系统,则可实现球铁无冒口铸造。
浇注系统内的铁水温度高,可以补缩包括底部厚大部位的真个铸件的早期液态收缩。
当补缩通道凝固后,厚大部位的液态收缩,通过其石墨化膨胀来抵消。
2.4 端盖铸件实现无冒口铸造的关键条件是,铸件模数须大于2.28cm ,只有这样才能使石墨化膨胀充分,膨胀体积大,抵消液态收缩的作用也最强。
参考文献:
[1]魏兵,袁森,张卫华.铸件均衡凝固技术及其应用[M] .北京:机械工业出版社,1998.
[2]钱进.调整温度场消除球铁件缩松缺陷[J] .现代铸铁,2003,(4):39~41.
[3]张宴,张允华,高明兰,等.对工艺因素影响中小球墨铸铁件缩松缺陷的认识[J] .铸造,2006,(9):959~960.。