废丙酮溶媒回收课题设计
丙酮溶剂的回收利用与工艺改进

2019年第10期广东化工第46卷总第396期·95·丙酮溶剂的回收利用与工艺改进姜凯,姚宏,周真龙,郁卫飞*(中国工程物理研究院化工材料研究所,四川绵阳621999)[摘要]针对本单位合成工艺中洗涤用丙酮溶剂,进行了常压蒸馏方法的循环回收利用工艺开发。
采用分段蒸馏方式,有效避免了蒸馏工艺中出现丙酮爆沸的风险;采用蒸汽阀开闭自动控制的方式,有效控制加热温度,有效避免触发超温报警;采取每次蒸馏前排放底部残存液,及70℃阈值时排空废弃液的方式,避免堵塞底阀的风险;本工艺经实验室、小试和中试,均获得合格产品,具有技术可行性。
本工艺经改进应用,安全可行,历年的丙酮回收率稳定在85%,具有较好的经济效益和社会效益。
[关键词]丙酮;分段蒸馏;循环回收利用[中图分类号]TQ[文献标识码]A[文章编号]1007-1865(2019)10-0095-02Recycling Process and its Improvement of Acetone SolventJiang Kai,Yao Hong,Zhou Zhenlong,Yu Weifei*(Institute of Chemical Materrials,China Academy of Engineering Physics,Mianyang621999,China)Abstract:Acetone solvent as washing agent within our synthetic production line was concerned and its recycling process was developed with atmospheric distillation method.Here,segmented distillation was employed to eliminate intense boiling of acetone effectively,automation of steam valve latch-release manner was introduced to eliminate over-temperature alarm entirely and control heating temperature precisely,discharge of bottom residue before distillation and drain of reactor while reaching of70℃threshold should be effective to avoid bottom valve block.The recycling process was attempted for lab-scale,bench-scale,and pilot scale production and lead to qualified product totally,which revealed technical feasibility of the process.The recycling process was applied to show efficient safety, acetone recovery rate high up to85%,and preferable economic and social benefit.Keywords:acetone solvent;segmented distillation;recycling process丙酮是一种优良的有机溶剂,广泛应用于医药、化工、轻工等领域。
化工原理之废丙酮溶媒回收过程填料精馏塔设计
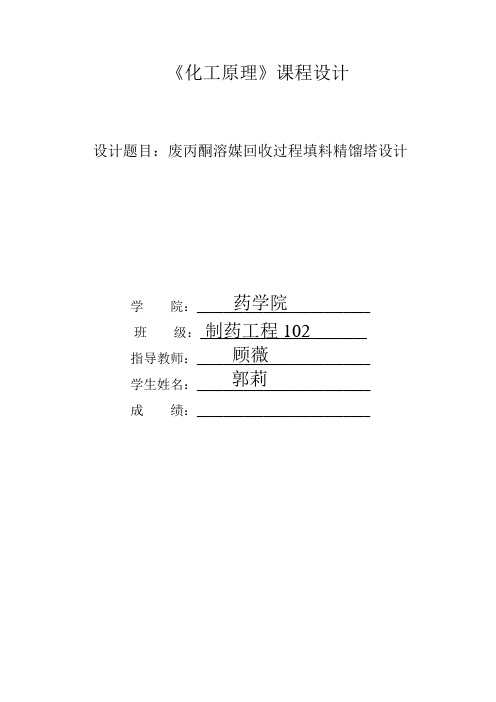
设计题目:废丙酮溶媒回收过程填料精馏塔设计学 院:__________________________ 班 级:_________________________ 指导教师:__________________________ 学生姓名:__________________________成 绩:__________________________药学院 制药工程102 郭莉 顾薇《化工原理》课程设计任务书一、设计题目废丙酮溶媒回收过程填料精馏塔设计本设计项目是根据生产实际情况提出的二、设计任务及条件1、原料液组成组分组成(质量%)丙酮75水252、分离要求产品中水分含量≤0.2%(质量%)残液中丙酮含量≤0.5%(质量%)3、处理能力8.5废丙酮溶媒处理量___________吨/天(每天按24小时计)4、设计条件操作方式:连续精馏操作压力:常压进料状态:饱和液体进料回流比:根据设计经验自行确定塔填料:金属环聚鞍填料,填料规格自选塔顶冷凝器:全凝器三、设计计算内容1、物料衡算2、填料精馏塔计算⑴操作条件的确定⑵塔径的确定⑶填料层高度的确定⑷填料层压降的计算⑸液体分布器设计计算⑹接管管径的计算3、冷凝器和再沸器的计算与选型4、填料精馏塔设计图5、废丙酮溶媒回收过程工艺流程图目录一、前言1.项目来源及开发意义2.精馏塔的选择依据2.1塔型2.2填料类型二、工艺设计要求三、工艺过程设计计算1.物料衡算2.填料精馏塔计算3.冷凝器和再废器计算与选择四、问题讨论五、求塔板数图六、生产工艺流程图七、填料精馏塔设计条件图八、液体分布器图参考文献前言在制药化工生产中,常采用精馏的方式对液体混合物进行分离和提纯。
精馏是利用液体混合物中各组分挥发度的不同并借助于多次部分汽化和部分冷凝达到轻重组分分离的方法。
丙酮~水是工业上最常见的溶剂,也是非常重要的化工原料之一,是无色、无毒、无致癌性、污染性和腐蚀性小的液体混合物。
化工原理课程设计--废丙酮溶媒回收过程填料精馏塔设计
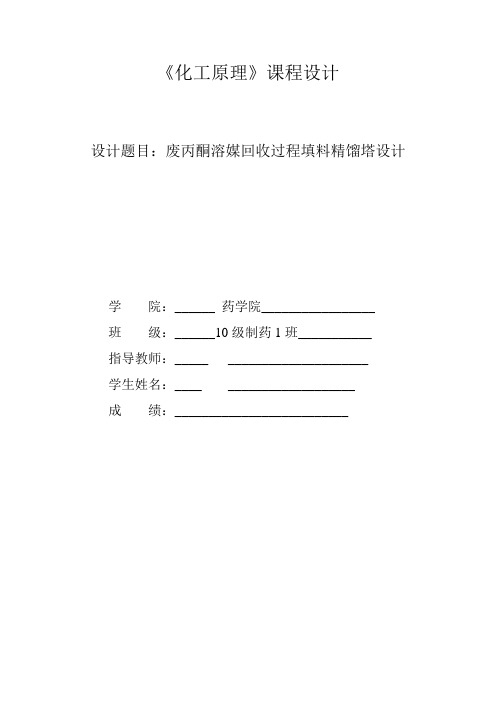
《化工原理》课程设计设计题目:废丙酮溶媒回收过程填料精馏塔设计学院:______ 药学院_________________班级:______10级制药1班___________指导教师:_____ _____________________学生姓名:____ ___________________成绩:__________________________一、前言 (3)1.1项目来源及开发意义 (3)1.2精馏塔的选择依据 (3)1.2.1塔型 (3)1.2.2填料类型 (4)二、设计工艺要求 (4)2.1进料要求 (4)2.2分离要求 (4)2.3塔顶冷凝器设计要求 (4)2.4塔釜再沸器设计要求 (5)2.5液体分布器设计要求 (5)2.6接管管径设计要求 (5)三、工艺过程设计计算 (5)3.1物料横算——确定塔顶、塔釜、进料流量及摩尔分率 (5)3.1.1塔顶、塔釜、进料摩尔分率 (5)3.1.2原料液及塔顶、塔底产品的平均摩尔质量 (5)3.1.3物料衡算 (6)3.2填料精馏塔计算 (6)3.2.1操作条件的计算 (6)3.2.2塔径的确定——D=83.2.3填料层高度的确定 (13)3.2.4填料层压降的计算 (13)3.2.5液体分布器设计计算 (14)3.2.6接管管径的确定 (14)3.3冷凝器和再沸器的计算与选型 (16)3.3.1冷凝器 (16)3.3.2再沸器 (17)四.设计方案讨论 (18)一、前言塔设备是化工、石油等工业中广泛使用的重要生产设备,用以实现蒸馏的塔设备称为蒸馏塔,这类塔设备的基本功能在于提供气、液两相充分接触的机会,使质、热两种传递过程能够迅速有效地进行,还要能使接触之后的气液两相及时分开,互不夹带。
根据塔内气液接触部件的结构形式,可将塔设备分为两大类:板式塔和填料塔。
板式塔内沿塔高度装有若干层塔板,液体靠重力作用由顶部逐板流向塔釜,并在各块板面上形成流动的液层,气体靠压强差推动,由塔底向上依次穿过各塔板上的液层而流向塔顶。
一种用于头孢合成中丙酮废液的回收装置
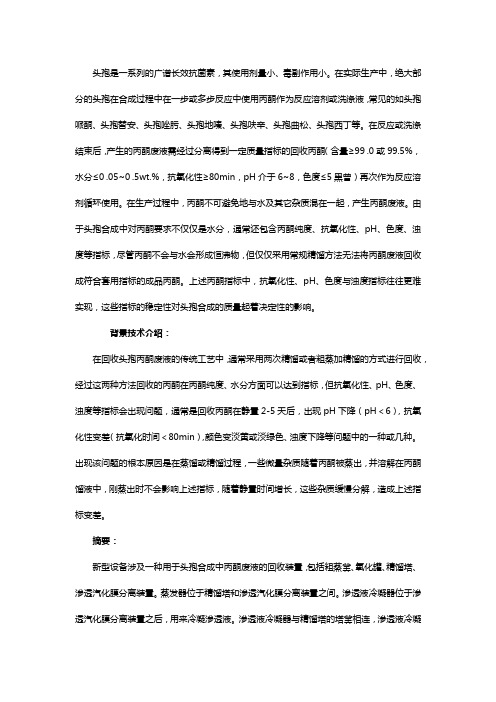
头孢是一系列的广谱长效抗菌素,其使用剂量小、毒副作用小。
在实际生产中,绝大部分的头孢在合成过程中在一步或多步反应中使用丙酮作为反应溶剂或洗涤液,常见的如头孢哌酮、头孢替安、头孢唑肟、头孢地嗪、头孢呋辛、头孢曲松、头孢西丁等。
在反应或洗涤结束后,产生的丙酮废液需经过分离得到一定质量指标的回收丙酮(含量≥99 .0或99.5%,水分≤0 .05~0 .5wt.%,抗氧化性≥80min,pH介于6~8,色度≤5黑曾)再次作为反应溶剂循环使用。
在生产过程中,丙酮不可避免地与水及其它杂质混在一起,产生丙酮废液。
由于头孢合成中对丙酮要求不仅仅是水分,通常还包含丙酮纯度、抗氧化性、pH、色度、浊度等指标,尽管丙酮不会与水会形成恒沸物,但仅仅采用常规精馏方法无法将丙酮废液回收成符合套用指标的成品丙酮。
上述丙酮指标中,抗氧化性、pH、色度与浊度指标往往更难实现,这些指标的稳定性对头孢合成的质量起着决定性的影响。
背景技术介绍:在回收头孢丙酮废液的传统工艺中,通常采用两次精馏或者粗蒸加精馏的方式进行回收,经过这两种方法回收的丙酮在丙酮纯度、水分方面可以达到指标,但抗氧化性、pH、色度、浊度等指标会出现问题,通常是回收丙酮在静置2-5天后,出现pH下降(pH<6),抗氧化性变差(抗氧化时间<80min),颜色变淡黄或淡绿色、浊度下降等问题中的一种或几种。
出现该问题的根本原因是在蒸馏或精馏过程,一些微量杂质随着丙酮被蒸出,并溶解在丙酮馏液中,刚蒸出时不会影响上述指标,随着静置时间增长,这些杂质缓慢分解,造成上述指标变差。
摘要:新型设备涉及一种用于头孢合成中丙酮废液的回收装置,包括粗蒸釜、氧化罐、精馏塔、渗透汽化膜分离装置。
蒸发器位于精馏塔和渗透汽化膜分离装置之间。
渗透液冷凝器位于渗透汽化膜分离装置之后,用来冷凝渗透液。
渗透液冷凝器与精馏塔的塔釜相连,渗透液冷凝后返回精馏塔塔釜回收其中的丙酮。
本装置工艺过程简单,回收过程中,回收率高,丙酮成品质量高,安全系数高,运行能耗低。
丙酮-水的填料塔分离 毕业设计论文

精馏塔的工艺条件及有关物性数据目录1. 设计方案简介 (1)1.1设计的方案 (1)1.2设计工艺 (1)1.3设计内容 (1)2. 工艺计算 (1)2.1 .1水和丙酮物性数据 (1)2.1.2全塔物料衡算 (2)2.1.3塔板数的确定 (2)2 .1.4 精馏塔的工艺条件及有关物性数据的计算 (2)2.2 填料塔的工艺尺寸的计算 (3)2.2.1 塔径的计算 (3)2.2.2塔高的计算 (5)2.2.3 塔板压降计算 (7)2.2.4塔板负荷性能图 (8)3. 辅助设备的计算及选型 (8)3.1 填料支承设备 (9)3.2填料压紧装置 (9)3.3液体再分布装置 (9)4. 设计一览表 (9)5. 后记 (10)6. 参考文献 (10)7. 主要符号说明 (10)8. 附图(工艺流程简图、主体设备设计条件图)1.设计方案简介1.1设计的方案在抗生素类药物生产过程中,需要用丙酮溶媒洗涤晶体,洗涤过滤后产生废丙酮溶媒,其组成为含丙酮__50%__、水___50%__(质量分数)。
为使废丙酮溶媒重复使用,拟建立一套板式精馏塔,以对废丙酮溶媒进行精馏。
得到含水量≤0.5%的丙酮溶液;或者丙酮回收率为98%。
设计要求废丙酮溶媒的处理量为__31000__吨/年,塔底废水中丙酮含量≤__0.05%__(质量分数)。
1.2设计工艺生产能力:31000吨/年(料液)年工作日:300天原料组成:50%丙酮,50%水(质量分率,下同)产品组成:馏出液 99.5%丙酮,釜液0.5%丙酮操作压力:塔顶压强为常压进料温度:泡点进料状况:泡点加热方式:直接蒸汽加热回流比:自选1.3设计内容1、确定精馏装置流程,绘出流程示意图。
2、工艺参数的确定基础数据的查取及估算,工艺过程的物料衡算及热量衡算,理论塔板数,塔板效率,实际塔板数等。
3、主要设备的工艺尺寸计算板间距,塔径,塔高,溢流装置,塔盘布置等。
4、流体力学计算流体力学验算,操作负荷性能图及操作弹性。
天津大学废丙酮溶媒回收过程填料精馏塔设计
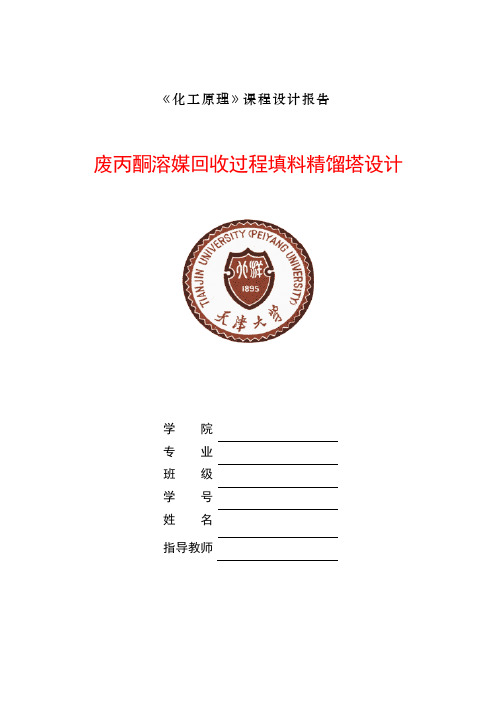
《化工原理》课程设计报告废丙酮溶媒回收过程填料精馏塔设计学院专业班级学号姓名指导教师目录一、课题的来源及意义1.1课题的来源 (2)1.2课题的意义 (2)1.3方法的依据 (2)二、工艺设计要求 (3)三、工艺过程设计计算3.1物料衡算 (3)3.2精馏塔设计计算3.2.1操作条件的确定 (4)3.2.2塔径计算 (11)3.2.3填料层高度计算 (16)3.2.4 填料层压降计算 (18)3.2.5液体分布器计算 (18)3.2.6接管管径计算 (19)3.3冷凝器与再沸器计算与选型3.3.1冷凝器的计算与选型 (20)3.3.2再沸器的计算与选型 (21)四、问题讨论 (23)五、生产工艺流程简图(附图) (27)六、填料精馏塔设计条件图(附图) (28)一、课题的来源及意义1.1课题的来源废丙酮溶媒来自于抗生素类药物“盐酸四环素”的生产过程。
1.2课题的意义:1)回收废丙酮溶媒母液中的丙酮循环利用可以降低生产成本,具有很高的经济效益。
2)回收废丙酮溶媒可以减少环境污染,具有一定的社会效益。
1.3方法的选择:丙酮和水二元物系,在常压下水的沸点100℃,丙酮沸点56.2℃,其沸点相差43.8℃。
由于沸点相差较大,故可以选用精馏操作。
为了提高生产能力,降低操作费用,宜选用连续精馏的操作方式。
精馏塔可以分为板式塔和填料塔。
与板式塔相比,填料塔具有如下特点:1)生产能力大;2)分离效率高;3)压力降小;4)持液量小;5)操作弹性大。
故选用填料塔进行分离。
丙酮—水物系分离的难易程度适中,气液负荷适中,设计中选用金属环矩鞍填料。
丙酮在常压下的沸点为56.2℃,故可采用常压操作,用30℃的循环水进行冷凝。
塔顶蒸汽采用全凝器冷凝,冷凝液在泡点下一部分回流,一部分经产品冷却器冷凝后送至储槽。
塔釜选用再沸器进行间接加热。
综上,此任务选择在填料塔中进行,采用常压连续精馏的方法完成。
四环素碱丁醇水 25% 丙酮溶媒丙酮 99.8%水 0.2%精制丙酮 75%废丙酮溶媒回收丙酮的流程是:二、工艺设计要求2.1原料液组成:2.2分离要求:产品中水分含量 ≤ 0.2% (质量%) 釜残液中丙酮含量 ≤ 0.5%2.3处理能力:废丙酮溶媒处理量14吨 / 天(每天按24小时计)。
废丙酮的回收工艺
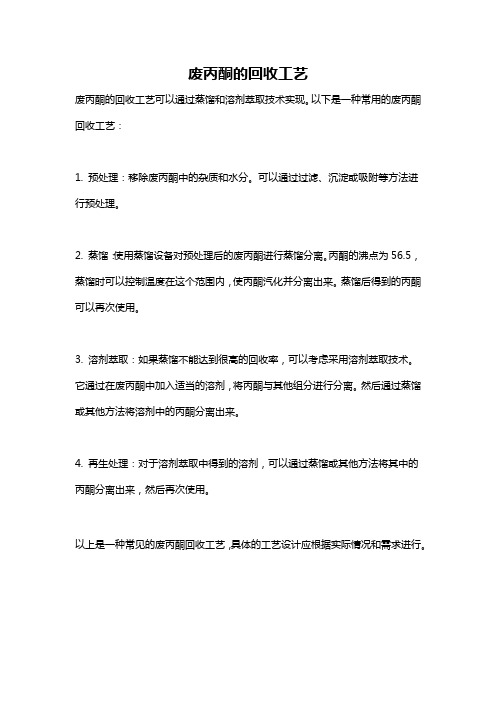
废丙酮的回收工艺
废丙酮的回收工艺可以通过蒸馏和溶剂萃取技术实现。
以下是一种常用的废丙酮回收工艺:
1. 预处理:移除废丙酮中的杂质和水分。
可以通过过滤、沉淀或吸附等方法进行预处理。
2. 蒸馏:使用蒸馏设备对预处理后的废丙酮进行蒸馏分离。
丙酮的沸点为56.5,蒸馏时可以控制温度在这个范围内,使丙酮汽化并分离出来。
蒸馏后得到的丙酮可以再次使用。
3. 溶剂萃取:如果蒸馏不能达到很高的回收率,可以考虑采用溶剂萃取技术。
它通过在废丙酮中加入适当的溶剂,将丙酮与其他组分进行分离。
然后通过蒸馏或其他方法将溶剂中的丙酮分离出来。
4. 再生处理:对于溶剂萃取中得到的溶剂,可以通过蒸馏或其他方法将其中的丙酮分离出来,然后再次使用。
以上是一种常见的废丙酮回收工艺,具体的工艺设计应根据实际情况和需求进行。
年处理1万吨丙酮溶媒回收工艺设计
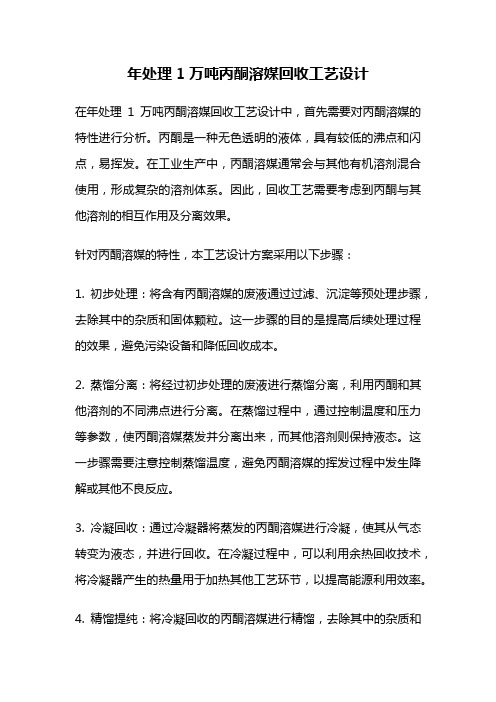
年处理1万吨丙酮溶媒回收工艺设计在年处理1万吨丙酮溶媒回收工艺设计中,首先需要对丙酮溶媒的特性进行分析。
丙酮是一种无色透明的液体,具有较低的沸点和闪点,易挥发。
在工业生产中,丙酮溶媒通常会与其他有机溶剂混合使用,形成复杂的溶剂体系。
因此,回收工艺需要考虑到丙酮与其他溶剂的相互作用及分离效果。
针对丙酮溶媒的特性,本工艺设计方案采用以下步骤:1. 初步处理:将含有丙酮溶媒的废液通过过滤、沉淀等预处理步骤,去除其中的杂质和固体颗粒。
这一步骤的目的是提高后续处理过程的效果,避免污染设备和降低回收成本。
2. 蒸馏分离:将经过初步处理的废液进行蒸馏分离,利用丙酮和其他溶剂的不同沸点进行分离。
在蒸馏过程中,通过控制温度和压力等参数,使丙酮溶媒蒸发并分离出来,而其他溶剂则保持液态。
这一步骤需要注意控制蒸馏温度,避免丙酮溶媒的挥发过程中发生降解或其他不良反应。
3. 冷凝回收:通过冷凝器将蒸发的丙酮溶媒进行冷凝,使其从气态转变为液态,并进行回收。
在冷凝过程中,可以利用余热回收技术,将冷凝器产生的热量用于加热其他工艺环节,以提高能源利用效率。
4. 精馏提纯:将冷凝回收的丙酮溶媒进行精馏,去除其中的杂质和其他残留物。
精馏过程可以通过多级蒸馏塔进行,使得丙酮溶媒得以进一步提纯。
在精馏过程中,可以采用不同的分馏剂和操作条件,以提高分离效果和产品质量。
5. 余热回收:在整个回收工艺中,可以采用余热回收技术,将产生的热量用于加热蒸馏塔、冷凝器等设备,以降低能耗。
余热回收可以通过换热器和热交换设备实现,同时也可以减少对外部能源的依赖。
通过以上工艺设计方案,可以实现对年处理1万吨丙酮溶媒的高效回收。
该工艺具有以下优点:回收率高、能耗低、操作简便、产品质量稳定。
同时,该工艺还可根据实际情况进行调整和优化,以满足不同规模和需求的生产工艺。
年处理1万吨丙酮溶媒回收工艺设计方案能够有效解决丙酮溶媒的回收和资源利用问题,具有重要的经济和环境意义。
- 1、下载文档前请自行甄别文档内容的完整性,平台不提供额外的编辑、内容补充、找答案等附加服务。
- 2、"仅部分预览"的文档,不可在线预览部分如存在完整性等问题,可反馈申请退款(可完整预览的文档不适用该条件!)。
- 3、如文档侵犯您的权益,请联系客服反馈,我们会尽快为您处理(人工客服工作时间:9:00-18:30)。
正文部分:第一部分:前言本次课程设计的题目为“废丙酮溶媒回收过程填料精馏塔设计”。
废丙酮溶媒来自于抗生素类药物“盐酸四环素”的生产过程,在二次操作中用丙酮来溶解和洗涤粗晶体,再通过结晶和过滤得到产品盐酸四环素晶体和废丙酮溶媒。
在废溶媒中丙酮含量颇高,故可以通过精馏操作来回收丙酮以重复利用,这样做既可以降低生产成本,又可以减少环境污染,不但具有很好的经济效益,而且可以获得可观的环境效益和社会效益,可谓一举多得。
盐酸四环素生产过程如下图所示。
第二部分:工艺设计要求原料液组成为丙酮为75%,水为25%(质量分数,下同),分离要求为产品中水分含量不高于0.2%,釜残液中丙酮含量不高于0.5%,废丙酮溶酶的处理量为16吨/每天(一天按24小时计算),设计条件为常压下连续精馏,进料状态为饱和液体进料,回流比自定,填料塔填料为金属环矩鞍,规格自选,计算所需物性数据可通过化工设计手册查询。
第三部分:工艺设计计算过程1物料衡算由废丙酮溶酶的处理量为16吨/每天可得,进料流股16666.7/24F kg h ==,由原料液组成为丙酮为75%,水为25%可得,进料中丙酮的摩尔分数为10.75/58.080.48180.75/58.080.25/18x ==+,水的摩尔分数为20.25/180.51820.75/58.080.25/18x ==+,可得进料的平均摩尔质量为11220.481858.080.51821837.31F M x M x M =+=⨯+⨯= /g mol ,则有进料流股的摩尔流量为666.717.86/37.31F kmol h ==。
由总衡算式可得F D W =+,由丙酮衡算式可得0.750.9980.005F D W =+,代入数值可得:500.19/D kg h =,166.51/W kg h =,同理亦可求得塔顶流股和塔底流股中丙酮和水各自的摩尔分数以及平均摩尔质量,结果见下表:2 填料塔设计计算2.1操作条件确定(操作温度计算)由设计要求可知,该精馏塔为常压操作,操作压力为101.325Kpa ,即760mm Hg 柱,所以求出操作温度即可,而操作温度包括进料温度F t ,塔顶温度D t ,以及塔釜温度W t ,可用试差法计算。
计算过程如下:进料温度F t :假设初值为t=72.5oC ,由安东尼方程可得:12940.46exp[]exp[16.6513]1283.53273.1572.5273.1535.93oB A mmHg tC p =-=-=+-+-23816.44exp[]exp[18.3036]260.28273.1572.5273.1546.13o B A mmHg t C p =-=-=+-+-,则111283.531.689760o k p p===,22260.280.342760o k pp===,可得:1111.6890.48180.8137y k x ==⨯=,2220.3420.51820.1775y k x ==⨯=,则有1210.00884y y δ=--=>0.0005,故不符合误差精度,需重新计算,设t=72.77o C ,同理可得1y =0.8204,2y =0.1795,可得1210.0001y y δ=--=<0.0005,故进料温度为72.77oC 。
塔顶温度D t :假设初值为t=57.0oC ,由安东尼方程可得:12940.46e x p []e x p [16.6513]778.38273.1557.0273.1535.93oB A m m H g tC p=-=-=+-+- 23816.44exp[]exp[18.3036]129.85273.1557.0273.1546.13o B A mmHg t C p =-=-=+-+-, 则11778.38 1.024760o k p p===,22129.850.171760o k p p===,可得:1110.99350.97001.024y x k ===,2220.00650.03800.171y x k ===,则有1210.0080.0005x x δ=--=-<-,不符合要求,故需重新计算,设t=57.23o C ,同理可得1x =0.9625,2x =0.0376,可得1210.0001x x δ=--=-,符合精度要求,故塔顶温度为57.23oC 。
塔底温度W t :假设初值为100oC ,由安东尼方程可得:12940.46exp[]exp[16.6513]2783.85273.15100.0273.1535.93oB A mmHg tC p =-=-=+-+-23816.44exp[]exp[18.3036]759.94273.15100.0273.1546.13o B A mmHg t C p =-=-=+-+-则112783.853.663760o k p p===,22759.940.9999760o k p p===,可得:111 3.6630.001550.0057y k x ==⨯=,2220.99990.998450.9984y k x ==⨯=,则有1210.0040.0005y y δ=--=-<-,不符合要求,需重新计算,设t=99.88o C ,同理可得1y =0.00566,2y =0.9941,可得1210.00023y y δ=--=,符合精度要求,故塔底温度为99.88oC 。
综上,有精馏塔操作条件如下表所示:2.2塔径计算2.2.1最小回流比及操作回流比确定由丙酮—水汽液平衡数据可得体系的汽液平衡曲线(见下图),可知该曲线非正常曲线,故可通过作图法做切线由切线斜率求得最小回流比min R ,进而求得min 1.3R R =。
具体作图步骤为:首先由汽液平衡数据描点做圆滑曲线并作对角线,然后做直线x=0.9935并标出与对角线交点A ,再过A 点做汽液平衡曲线的切线,如图所示,最后解得切线斜率并求出min R 。
通过作图法可得斜率k=0.697,则有m i nm i n 0.6971R k R ==+,解得min 2.3R =,则m i n 1.3 2.99R R ==。
2.2.2精馏塔气液相负荷计算精馏段,有(1)(2.991)8.6534.51/1995.57/V R D kmol h kg h =+=+⨯==,2.998.6525.86/1495.43/L RD kmol h kg h ==⨯==,提馏段,有/(1)34.51/1287V V q F V k m o l h k g=--===,/17.8625.8643.72/1631.19/L L F kmol h kg h =+=+==,2.2.3精馏塔塔径计算精馏塔塔径计算的基本公式为:i D =3600ms VVM V ρ=,而(0.50.85)F u u =--,F u 可通过埃克特关联图查得。
但是精馏段和提馏段需分别计算,然后加以圆整,若相差较大应采用变径塔,相差不大可统一圆整至规范值。
精馏段塔径计算:1495.4L w k g h =,1995.57/V w kg h=,32.133/V mpkg m nRTρ==,3792.38/L i i x kg m ρρ==∑,则0.50.0389V LV L w w ρρ⎛⎫= ⎪⎝⎭,埃克特关联图可知纵坐标为0.192,故20.20.192V L L u gρφψμρ⎛⎫= ⎪⎝⎭,其中170φ=(取25DN =),29841.242792.38H O L ρψρ===,29.81/g m s =,0.3214L i i x μμ==∑,可得2.039F u m s=,取.7Fu u m s==,又334.51.820.29/3632.1m s V VM V m s ρ⨯===⨯,故0.482i D m ===。
提馏段塔径计算:/1631.19/L w k g h =,/1287.57/V w kg h =,/31.314/V mpkg m nRT ρ==,/3839/i i L x kg m ρρ==∑,则////0.50.05VL V L w w ρρ⎛⎫= ⎪ ⎪⎝⎭,查图得纵坐标为0.18,故//20.20.18V L Lu gρφψμρ⎛⎫= ⎪ ⎪⎝⎭,其中2980 1.168839H O L ρψρ===,0.491L i i x μμ==∑,可得 2.559/F u m s =,取0.61.5354F u u m s ==,又有334.5137.310.2722/36003600 1.314m s V VM V m s ρ⨯===⨯,故0.475i D m ===。
故精馏段和提馏段塔径分别为482mm 和475mm ,相差不大,可圆整为500mm ,即精馏塔塔径为500mm 。
2.2.4对塔径进行校核,包括泛点率校核和最小液体喷淋密度校核等。
2.2.4.1泛点率校核:精馏段:2440.25991.324/0.25s V u m s D ππ⨯===⨯,故 1.3240.6492.039F u u ==,符合要求, 提溜段:2440.27221.386/0.25s V u m s D ππ⨯===⨯,可得 1.3860.5422.559F u u ==,合乎要求。
2.2.4.2最小液体喷淋密度校核:设计要求有()min 0.03W L =,25DN =有185a =,故()min min 5.55W U L a =⨯=,精馏段有min 1495.43792.389.610.250.25U U π==>⨯,提馏段有min1631.198399.900.250.25U U π==>⨯,故液体喷淋密度校核合乎要求。
2.2.4.3/D d 校核:25DN =,故500/20825D d ==>,符合要求。
综上所述,可得精馏塔塔径为500mm 。
2.2.5填料层高度计算2.2.5.1理论板数和进料位置的确定理论板数和进料位置通过简捷算法即吉利兰图法获得。
在该丙酮—水体系中,由前面数据可求得体系的平均相对挥发度784.45/131.272775.22/756.691294.19/263.284.85243α++==,则m i n1lg []116.279lg W DD Wx x x x N α-⨯-=-=,而m i n 2.992.30.172912.991R R R --==++,查吉利兰图可得min0.472N N N -=+,故可得13.62N =。
求进料位置,min1lg[]11 2.23lg D FD F x x x x N α-⨯-=-=,横坐标不变,故仍有/min/0.472N N N -=+,求得/ 5.98N =,故总理论板数为14,加料板为6(自上向下)。