综述-铝合金疲劳及断口分析
铝合金搅拌摩擦焊接头疲劳断裂行为分析_曹丽杰
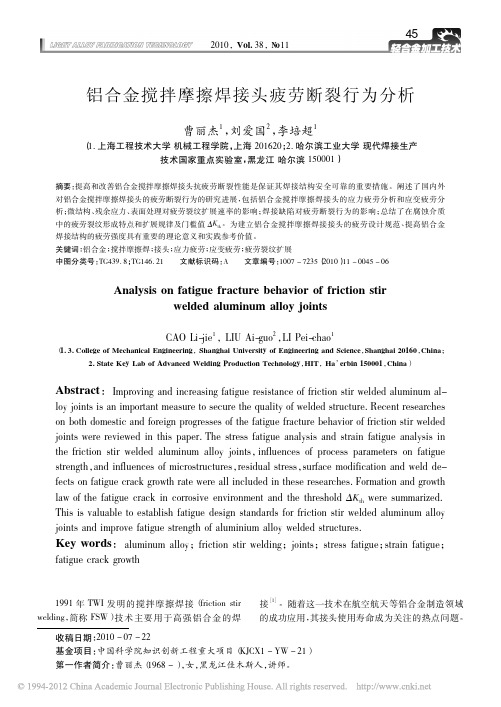
fatigue crack growth
1991 年 TWI 发明的搅拌摩擦焊接 ( friction stir welding,简称 FSW) 技术主要用于高强铝合金的焊
FSW 为固相连接,焊缝中沉淀相大小和聚集程 度影响 FCGRS 和 ΔKth。沉淀相的聚集、滑移逆转和 裂纹偏向提高 ΔKth。对于未时效状态,沉淀相为聚 集态,内部含有微小的 GP 区,裂纹扩展阻力大,ΔKth 也高。疲劳循 环 时 由 于 位 错 对 聚 集 相 的 剪 切,导 致 反向滑移程度增高,循环塑性好。过时效状态下,反 向滑移程度低,大块的非聚集的沉淀相钉扎住位错, 阻止位错反转,循环塑 性 低。因 此,在 过 时 效 状 态 下,或者存在粗大沉淀相时,FCGRS 会增大。此外, 未时效状态下疲劳裂纹的闭合程度大于过时效状态 的 ,其 FCGRS 低于后者的。
低,虽然可以得到良好的焊接接头,但是焊缝底部金
属塑化程度不够,容易出现“吻接”缺陷。
47
2010,Vol. 38,№11
3 铝合金 FSW 接头的疲劳裂纹扩展 速 率 FCGRS ( Fatigue crack growth rates) 和门槛值 ΔKth
为获得缺陷状态下接头的疲劳行为,应用断裂 力学把疲劳 设 计 建 立 在 本 身 存 在 缺 陷 的 基 础 上,按 照裂纹在循环载荷下的扩展规律,估算结构寿命,是 保证结构安全工作的重要途径,同时,也是对传统疲 劳试验分析方法的一个重要补充和发展[9]。FCGRS 是决 定 构 件 疲 劳 行 为 的 一 个 重 要 特 征 参 量,影 响 FSW 接头 FCGRS 的因素有微结构和残余应力、表面 处理方法等。 3. 1 微结构和残余应力对 FCGRS 和 ΔKth的影响
铝合金构件拉伸与疲劳断裂分析
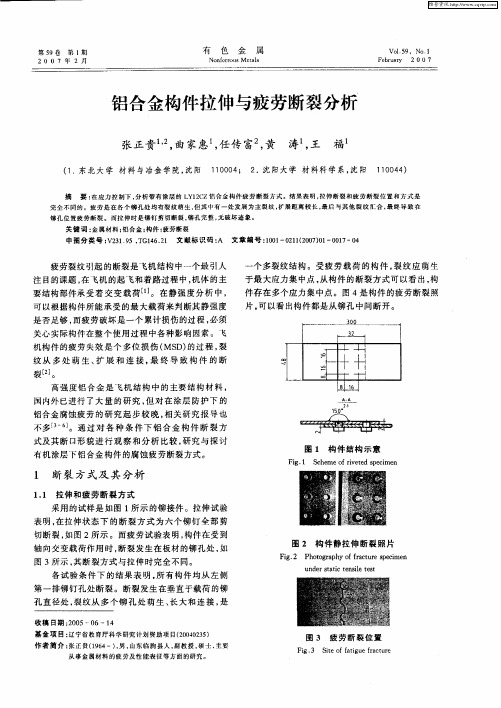
疲劳裂 纹 引起 的断裂 是飞 机 结构 中一个 最 引人 一 个 多裂 纹结 构 。受 疲 劳载 荷 的 构 件 ,裂 纹应 萌生
(4×2—2×1/2×2×1.2)= 16.8r am2。连接 板 在
铆 孔处 的净 截面 积为 S = S总 一S铆孔 = 96—16.8
= 79.2mm2。铆 孔处 材料所 受平 均应 力 d平均=96× 210/79.2=254.5MPa。而 根 据 试 验 的 测 量 结 果 , LY12CZ铝 合 金 的 抗 拉 强 度 为 447.88 MPa,大 于
另一方面在点蚀孔底从沿晶发展的初始裂纹进一步扩展成几条较大的穿晶裂纹随着裂纹的扩展在裂纹尖端处应力继续增大和集中裂纹不断发展在主要受力学因素控制下裂纹向点蚀孔两侧及孔底同时迅速扩展但由于裂纹在厚度方向和轧向上受到的载荷不同在宏观上表现为椭圆形直到与其他裂纹汇合最终导致构件失稳断裂
维普资讯
注 目的课 题 ,在 飞机 的起 飞和 着路 过程 中 ,机体 的主 于 最 大应力集 中点 ,从构件 的 断裂方 式 可以看 出 ,构
要 结构 部件承 受 着 交变 载 荷 … 。在 静 强 度分 析 中 , 可以根 据构件 所能 承受 的最 大载 荷来判 断其静 强度 是 否足 够 ,而疲 劳破 坏是 一个 累计 损伤 的过程 ,必须
摘 要 :在应力控制下 ,分析带有涂层的 LY12CZ铝合金构件疲劳 断裂方式。结果表 明,拉伸断裂和疲 劳断裂位 置和方式是 完 全 不 同 的 。 疲 劳是 在 各 个铆 孔 处 均 有 裂 纹 萌 生 ,但 其 中有 一 处 发 展 为 主 裂 纹 。扩展 距 离 较 长 。最 后 与 其 他 裂 纹 汇合 .最 终 导 致 在 铆孔位置疲劳断裂 。而拉 伸时是 铆钉剪切断裂 ,铆孔完 整,无破坏迹象。
2024铝合金振动疲劳特性及断口分析

2 01 3年 8月
航
空
材
料
学
报
Vo 1 . 3 3,No . 4
Au g us t 2 01 3
J OURNAL OF AE RONAU T I C AL MAT E RI AL S
2 0 2 4铝 合 金 振 动 疲 劳 特 性 及 断 口分 析
初 始 应 力 幅 值 下 的振 动 疲 劳 寿 命 。利 用 体 式 显 微 镜 及 扫 描 电镜 对 疲 劳 断 口进 行 微 观分 析 。 结 果 表 明 : 初 始 应 力 相
同时 , 处 于 共振 状 态 的悬 臂 梁 振 动 疲 劳 寿命 最 长 , 瞬 断 区面 积 最 小 。微 观 分 析 表 明 , 疲 劳 裂 纹 源 萌 生 于 材 料 表 面 的 最大应力 区 , 在裂纹源区有明显的放射状条纹 、 贝壳线和大量刻面 ; 在疲 劳 裂 纹 扩 展 区 , 除疲劳条带外 , 还 观 察 到 大 量 的二 次 疲 劳 裂 纹 ; 疲劳瞬断区则由大量韧窝构成 , 表 现 出典 型 的 韧 性 断 裂 特 征 。 微 观 分 析 可 知 合 金 内强 化 相 颗 粒 对 疲 劳裂 纹扩 展 有 明显 的 阻 碍作 用 。 关键词 : 2 0 2 4铝 合 金 ; 振动疲劳 ; 固有频率 ; 疲劳断 口
的抗 振 动断裂性 能 ; 陈 国平 等分 析 了梁 结 构振 动 疲 劳过 程 中 , 呼 吸式 疲 劳 裂 纹 的扩 展 特 性 ; 李 静
等 系统 研究 了某 型航空 发动 机叶 片 的振 动疲 劳寿命
问题 。在疲 劳寿命 预 估 方 面 , 施 荣 明等 研 究 了振
研究了 T C 6钛 合金 组织 对 振 动疲 劳 的影 响¨ , 蔡 建
分析铸造Al合金热疲劳开裂的形成机理及对策

分析铸造Al合金热疲劳开裂的形成机理及对策铸造Al合金热疲劳开裂是一种严重的质量问题,对于铸件的可靠性和使用寿命具有重大影响。
本文将分析铸造Al合金热疲劳开裂的形成机理,并提出相应的对策。
一、铸造Al合金热疲劳开裂的形成机理铸造Al合金在高温下容易发生热疲劳开裂,其形成机理主要包括以下几个方面:1.热应力效应:在高温下,铸件内部由于温度梯度和热膨胀不均等原因,会产生较大的热应力,导致铸件出现应力集中区域。
当热应力超过铸件材料的承载能力时,就会引起裂纹的产生和扩展。
2.晶界氧化:在高温下,铸造Al合金晶界处容易发生氧化反应,形成氧化物。
这些氧化物会引起晶界强化和晶界脆化,导致晶界疲劳裂纹的形成和扩展。
3.热疲劳循环加载:在高温下,铸造Al合金受到热循环加载,即温度的周期性升降,这会导致铸件内部的应力不断变化,并最终引起热疲劳开裂。
二、对铸造Al合金热疲劳开裂的对策为了解决铸造Al合金热疲劳开裂的问题,可以采取以下对策措施:1.合理设计铸件结构:在铸件设计过程中,应考虑到热应力的分布情况,避免在铸件中出现应力集中区域。
合理设计铸件结构可以减少热应力的积累,降低开裂的概率。
2.优化铸造工艺参数:在铸造过程中,应优化浇注温度、浇注速度、冷却速率等工艺参数,以减少热应力和晶界氧化的产生。
合理的铸造工艺参数可以改善铸件的热疲劳性能,降低开裂风险。
3.合理选择合金元素:合金元素的添加可以改善铸造Al合金的热疲劳性能。
例如,添加少量的镁元素可以提高铝合金的热塑性和热疲劳强度,降低热疲劳开裂的风险。
4.热处理优化:通过合理的热处理工艺,可以改善铸造Al合金的晶界结构,减少晶界氧化和晶界脆化的发生。
同时,热处理还可以通过调整组织结构,提高材料的抗热疲劳性能。
5.应力消除处理:在铸造Al合金后,可以进行应力消除处理,通过加热和冷却过程调整铸件的内部应力分布,降低开裂的风险。
6.增加铸件表面保护层:在高温环境下,为铸件增加一层保护层,可以减少铸件的氧化反应,延缓晶界氧化的发生。
铝合金疲劳断裂的断口特征
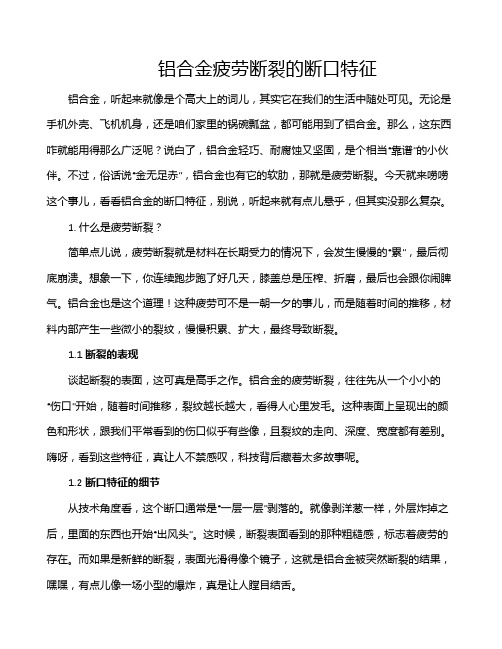
铝合金疲劳断裂的断口特征铝合金,听起来就像是个高大上的词儿,其实它在我们的生活中随处可见。
无论是手机外壳、飞机机身,还是咱们家里的锅碗瓢盆,都可能用到了铝合金。
那么,这东西咋就能用得那么广泛呢?说白了,铝合金轻巧、耐腐蚀又坚固,是个相当“靠谱”的小伙伴。
不过,俗话说“金无足赤”,铝合金也有它的软肋,那就是疲劳断裂。
今天就来唠唠这个事儿,看看铝合金的断口特征,别说,听起来就有点儿悬乎,但其实没那么复杂。
1. 什么是疲劳断裂?简单点儿说,疲劳断裂就是材料在长期受力的情况下,会发生慢慢的“累”,最后彻底崩溃。
想象一下,你连续跑步跑了好几天,膝盖总是压榨、折磨,最后也会跟你闹脾气。
铝合金也是这个道理!这种疲劳可不是一朝一夕的事儿,而是随着时间的推移,材料内部产生一些微小的裂纹,慢慢积累、扩大,最终导致断裂。
1.1 断裂的表现谈起断裂的表面,这可真是高手之作。
铝合金的疲劳断裂,往往先从一个小小的“伤口”开始,随着时间推移,裂纹越长越大,看得人心里发毛。
这种表面上呈现出的颜色和形状,跟我们平常看到的伤口似乎有些像,且裂纹的走向、深度、宽度都有差别。
嗨呀,看到这些特征,真让人不禁感叹,科技背后藏着太多故事呢。
1.2 断口特征的细节从技术角度看,这个断口通常是“一层一层”剥落的。
就像剥洋葱一样,外层炸掉之后,里面的东西也开始“出风头”。
这时候,断裂表面看到的那种粗糙感,标志着疲劳的存在。
而如果是新鲜的断裂,表面光滑得像个镜子,这就是铝合金被突然断裂的结果,嘿嘿,有点儿像一场小型的爆炸,真是让人瞠目结舌。
2. 为什么铝合金会疲劳断裂?哎,生活不易,材料也一样难。
铝合金疲劳断裂,最主要的原因就是各种应力。
不管是咱们日常使用中产生的静态应力,还是偶尔的冲击,时间久了,铝合金就像人一样,受不了的。
尤其在一些高强度环境下,铝合金真的容易变成“脆弱的小白兔”,到最后一触即发,炸成碎片。
2.1 环境因素的干扰别小看了环境因素,温度、湿度甚至是化学物质都能给铝合金带来“小麻烦”。
铸造A356铝合金的拉伸性能及其断口分析
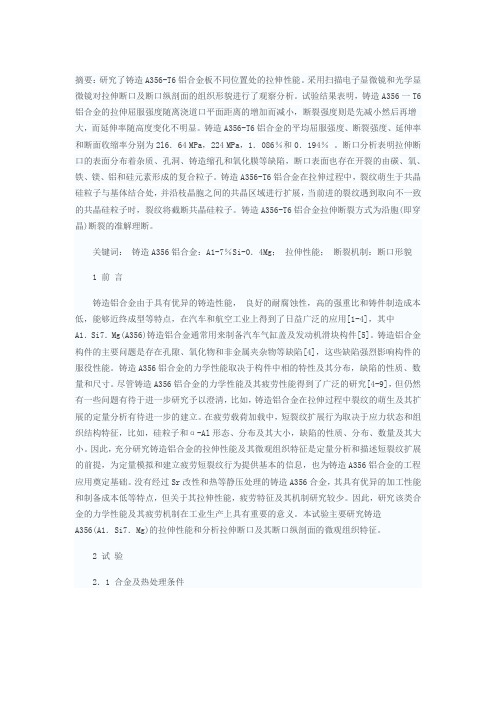
摘要:研究了铸造A356-T6铝合金板不同位置处的拉伸性能。
采用扫描电子显微镜和光学显微镜对拉伸断口及断口纵剖面的组织形貌进行了观察分析。
试验结果表明,铸造A356一T6铝合金的拉伸屈服强度随离浇道口平面距离的增加而减小,断裂强度则是先减小然后再增大,而延伸率随高度变化不明显。
铸造A356-T6铝合金的平均屈服强度、断裂强度、延伸率和断面收缩率分别为2l6.64 MPa,224 MPa,1.086%和0.194%。
断口分析表明拉伸断口的表面分布着杂质、孔洞、铸造缩孔和氧化膜等缺陷,断口表面也存在开裂的由碳、氧、铁、镁、铝和硅元素形成的复合粒子。
铸造A356-T6铝合金在拉伸过程中,裂纹萌生于共晶硅粒子与基体结合处,并沿枝晶胞之间的共晶区域进行扩展,当前进的裂纹遇到取向不一致的共晶硅粒子时,裂纹将截断共晶硅粒子。
铸造A356-T6铝合金拉伸断裂方式为沿胞(即穿晶)断裂的准解理断。
关键词:铸造A356铝合金:A1-7%Si-0.4Mg;拉伸性能;断裂机制:断口形貌1 前言铸造铝合金由于具有优异的铸造性能,良好的耐腐蚀性,高的强重比和铸件制造成本低,能够近终成型等特点,在汽车和航空工业上得到了日益广泛的应用[1-4],其中A1.Si7.Mg(A356)铸造铝合金通常用来制备汽车气缸盖及发动机滑块构件[5]。
铸造铝合金构件的主要问题是存在孔隙、氧化物和非金属夹杂物等缺陷[4],这些缺陷强烈影响构件的服役性能。
铸造A356铝合金的力学性能取决于构件中相的特性及其分布,缺陷的性质、数量和尺寸。
尽管铸造A356铝合金的力学性能及其疲劳性能得到了广泛的研究[4-9],但仍然有一些问题有待于进一步研究予以澄清,比如,铸造铝合金在拉伸过程中裂纹的萌生及其扩展的定量分析有待进一步的建立。
在疲劳载荷加载中,短裂纹扩展行为取决于应力状态和组织结构特征,比如,硅粒子和α-Al形态、分布及其大小,缺陷的性质、分布、数量及其大小。
车体结构铝合金焊接接头疲劳性能研究

车体结构铝合金焊接接头疲劳性能研究摘要:铝合金是一种以铝为主要材料,混合其他合金元素的轻金属材料,该材料在工业生产中较为常见。
铝具有较强的可焊性,和塑造性,也具备导电和导热性能,在交通运输中应用较为广泛。
本文以车体结构,铝合金焊接接头疲劳性能为研究内容,对车体结构焊接中,铝合金接头的疲劳性能影响因素进行简单的分析,并着重对焊缝质量的影响因素作了详细的论述,希望对相关行业者有所帮助。
关键词:铝合金;焊接缺陷;焊接接头;疲劳性能引言:因为铝合金材料本身的理化性质、力学特性和工艺特性都很好,因此,在航空领域,工业领域以及交通领域中应用都比较广泛。
铝合金材质较轻,还具备耐腐蚀,耐磨等特点,用这种材料制造车体的主要结构,符合生产需求。
车体结构的焊接过程,会因为材质受到焊接技术,焊接方法以及焊接材料等影响,促使焊接接头的负载发生变化。
根据其焊接接头疲劳性的研究,能够妥善地找出最佳的焊接方法,匹配最合适的焊接技术,以此来完成车体的焊接工作,确保整体车体结构的稳定性。
一、影响铝合金焊接接头的疲劳性能因素分析由于铝合金本身具有轻量化、高密封等优点,在目前阶段,它基本上已经成为汽车,有轨电车等车体制造材料。
然而,由于铝合金具有高热、高膨胀系数等特性,因此,在进行焊接的时候,因为焊接方法和焊接工艺不匹配会发生一定的问题。
在焊接之后,极易出现结构变形,并且变形量很大,这对铝合金车体的生产质量造成了很大的影响。
铝合金焊接过程中会施加一些外力作用,造成接头缺陷,也就是疲劳破坏。
主要包括了裂纹、气孔、未焊透等情况,这些都是影响铝合金抗疲劳性能的重要因素。
气孔缺陷较为常见,因为在金属凝固的过程中,内部的气体没有及时溢出,形成了气孔,分布在焊缝的周围。
气孔存在对于接头的抗疲劳性的影响主要和气孔宏观尺寸有关,当气孔直径小于0.5 mm时,对接头疲劳性的影响不大。
若气孔大于0.8 mm,则疲劳性与余高保持类似,气孔长度为1.2-1.8 mm时,应力较集中,在气孔处发生断裂。
综述-铝合金疲劳及断口分析报告
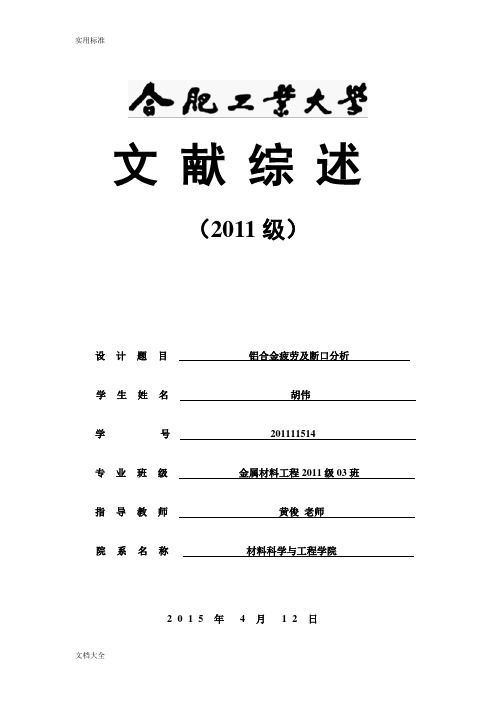
文献综述(2011级)设计题目铝合金疲劳及断口分析学生姓名胡伟学号*********专业班级金属材料工程2011级03班指导教师黄俊老师院系名称材料科学与工程学院2015年4月12日铝合金疲劳及断口分析1 绪论1.1 引言7系铝合金包括Al-Zn-Mg 系和Al-Zn-Mg-Cu 系合金,此类合金具有密度低、比强度高、良好的加工性能及优良的焊接性能等一系列优点。
随着应用在铝合金上的热处理工艺及微合金化技术的不断改进,其力学性能被大幅度强化,综合性能也得到了全面提升。
在航空航天、建筑、车辆、、桥梁、工兵装备和大型压力容器等方面都得到了广泛的应用。
现代工业的飞速发展,对7 系铝合金的强度、韧性以及抗应力腐蚀性能等提出了更高的要求。
但是,存在另外一个现象,在各行各业的领域中,铝合金设备偶尔会出现难以察觉的断裂,在断裂之前很难甚至无法察觉到一点塑性变形。
这种断裂形式,对人身以及财产安全造成了不可挽回的损失。
经过大量实验表明,这些断裂是由于材料的疲劳引起,材料在交变载荷的长期作用下,表面或者内部,尤其是内部会产生微观裂纹。
本文主要研究铝合金疲劳引起的裂纹以及疲劳断口分析,此类研究对于日后的生产安全,有重大意义。
1.2 7系铝合金的发展历史在20世纪20年代,德国的科学家研制出Al-Zn-Mg系合金,由于该合金抗应力腐蚀性能太差,并未得到产业内应用。
在20世纪30年代初一直到二战结束期间,各个国家在研究中发现,Cu元素可以提高铝合金的抗应力腐蚀性能。
在此,开发了大量Al-Zn-Mg 系合金,因此忽视了对Al-Zn-Mg 系合金的研究。
德、美、苏、法等国在Al-Zn-Mg-Cu 系合金基础上成功地开发了7075 、B93 和D。
T。
D683 等合金。
目前正广泛应用在航空航天事业上,但是强度、韧性、抗应力腐蚀性能三者之间未能实现最佳组合状态。
20世纪50年代,德国科学家公布了具有优良焊接性能的合金AlZnMg1 和AlZnMg2,引起了人们对Al-Zn-Mg系合金的重视。
- 1、下载文档前请自行甄别文档内容的完整性,平台不提供额外的编辑、内容补充、找答案等附加服务。
- 2、"仅部分预览"的文档,不可在线预览部分如存在完整性等问题,可反馈申请退款(可完整预览的文档不适用该条件!)。
- 3、如文档侵犯您的权益,请联系客服反馈,我们会尽快为您处理(人工客服工作时间:9:00-18:30)。
文献综述(2011级)设计题目铝合金疲劳及断口分析学生胡伟学号201111514专业班级金属材料工程2011级03班指导教师黄俊老师院系名称材料科学与工程学院2015年4月12日铝合金疲劳及断口分析1 绪论1.1 引言7系铝合金包括Al-Zn-Mg 系和Al-Zn-Mg-Cu 系合金,此类合金具有密度低、比强度高、良好的加工性能及优良的焊接性能等一系列优点。
随着应用在铝合金上的热处理工艺及微合金化技术的不断改进,其力学性能被大幅度强化,综合性能也得到了全面提升。
在航空航天、建筑、车辆、、桥梁、工兵装备和大型压力容器等方面都得到了广泛的应用。
现代工业的飞速发展,对7 系铝合金的强度、韧性以及抗应力腐蚀性能等提出了更高的要求。
但是,存在另外一个现象,在各行各业的领域中,铝合金设备偶尔会出现难以察觉的断裂,在断裂之前很难甚至无法察觉到一点塑性变形。
这种断裂形式,对人身以及财产安全造成了不可挽回的损失。
经过大量实验表明,这些断裂是由于材料的疲劳引起,材料在交变载荷的长期作用下,表面或者部,尤其是部会产生微观裂纹。
本文主要研究铝合金疲劳引起的裂纹以及疲劳断口分析,此类研究对于日后的生产安全,有重大意义。
1.2 7系铝合金的发展历史在20世纪20年代,德国的科学家研制出Al-Zn-Mg系合金,由于该合金抗应力腐蚀性能太差,并未得到产业应用。
在20世纪30年代初一直到二战结束期间,各个国家在研究中发现,Cu元素可以提高铝合金的抗应力腐蚀性能。
在此,开发了大量Al-Zn-Mg 系合金,因此忽视了对Al-Zn-Mg 系合金的研究。
德、美、、法等国在Al-Zn-Mg-Cu 系合金基础上成功地开发了7075 、B93 和D。
T。
D683 等合金。
目前正广泛应用在航空航天事业上,但是强度、韧性、抗应力腐蚀性能三者之间未能实现最佳组合状态。
20世纪50年代,德国科学家公布了具有优良焊接性能的合金AlZnMg1 和AlZnMg2,引起了人们对Al-Zn-Mg系合金的重视。
在此段时间,美国学者在AlZnMg1 合金的基础上,加入了Zr、Mn、Cr 等元素,研制出了7004和7005合金,具有优良焊接性和抗应力腐蚀性能,广泛应用于焊接行业。
唯一不足的是,工艺性能较差。
日本科学家尝试降低合金中Mg含量,提高Zn/Mg值,研制出了ZK60和ZK61合金,使合金的焊接性和工艺性能提高,但是降低了很大的强度。
同时期,前联也研制出了1915、1933合金,强度也是偏低。
为了克服强度低的缺点,20世纪70年代又研制出7020合金,具有高强度,焊接性好的性能。
以后,人们把注意力集中在了Al-Zn-Mg 系铝合金上。
20世纪80年代初,美国科学家先后在7075合金的基础上,为了解决实际生产中抗应力腐蚀敏感性较高的问题,以及满足某些特殊需要,调整了部分合金元素的含量,发展了许多新型合金。
相比之下,国对7系铝合金的研究起步较晚,在20实际80年代,由东北和研究院研制Al-Zn-Mg 系铝合金。
目前主要有7050、7075、7175等合金产品。
20 世纪90 年代中期,航空材料研究所采用常规半连续铸造法试制出7A55 超高强铝合金,近几年又研制出强度更高的7A60 合金。
而在Al2Zn2Mg 系铝合金的研制上,国基本都是仿制,很少自行开发。
1.3 铝合金疲劳的分类1.3.1 疲劳的定义疲劳断裂是由于交变载荷、应力下引起的延时断裂,其断裂应力水平往往低于材料的抗拉强度σb,有时甚至低于屈服强度σs。
一般情况下,疲劳破坏不发生明显的塑性变形,其变形主要是脆性断裂,是一种没有预兆、十分危险的破坏形式,难以检测、预防。
铝合金的疲劳,按疲劳破坏原因可分为三类:热疲劳、腐蚀疲劳和机械疲劳。
1.3.2热疲劳铝合金的热疲劳是在交变应力和热应力共同作用下产生的疲劳破坏。
外部约束和部约束是产生热疲劳的两个必要条件,外部约束即阻碍材料自由膨胀,部约束即产生温度梯度,使材料膨胀,但由于约束从而产生热应力与热应变,经过一定的循环次数,导致裂纹的萌生、扩展。
文孝等研究了LD8铝合金的同相和异相热疲劳特性,应用弹塑性断裂力学方法对不同状态下热疲劳寿命进行了探讨。
1.3.3腐蚀疲劳长期在化工行业使用或者海水中使用的金属材料,处于腐蚀的环境中,此外还承受交变载荷作用,与正常环境下的金属材料相比,腐蚀性环境和交变载荷同时作用,会显著降低材料的疲劳性能,从而产生构件的破坏,以至于最终断裂。
宫玉辉等研究了不同腐蚀环境对7475-T7351铝合金疲劳性能及裂纹扩展速率的影响,发现腐蚀环境对裂纹扩展有较明显的加速作用,但不同环境腐蚀和不同温度对材料的低周疲劳性能影响不大。
王成等将不同浓度硅酸钠添加到铝合金中,发现其可以抑制铝合金的点蚀、减少裂纹源,提高铝合金在氯化钠溶液中抗点蚀的能力及腐蚀疲劳寿命,但对铝合金的腐蚀疲劳裂纹的扩展无法抑制。
1.3.4机械疲劳机械零部件在外加应力或者应变作用下将会产生机械疲劳,经长时间工作后,即使所受应力小于材料屈服点,仍然会产生裂纹,或者产生断裂。
在循环应力水平较低时,弹性应变起主导作用,此时疲劳寿命较长,称之为高周疲劳,也称应力疲劳;在循环应力水平较高时,塑性应变起主导作用,此时疲劳寿命较短,称之为低周疲劳,也称塑性疲劳。
睿等对2024-T3铝合金孔板进行了高低周复合疲劳试验,研究发现随着高低周循环次数增大,复合疲劳寿命有显著的降低,并建立了高低周循环次数和应力幅比与高低周复合疲劳寿命之间的关系式,但其只考虑了载荷循环次数对疲劳的影响,没有全面综合其他影响疲劳寿命的因素。
1.4 疲劳破坏过程及机理金属设备疲劳过程的开始,即疲劳裂纹的萌生称为疲劳源。
疲劳源是材料微观组织永久损伤的核心,当裂纹开始萌生后,逐渐长大并与其它裂纹合并,然后形成肉眼可见的宏观裂纹,称为主裂纹,此时裂纹萌生阶段结束。
之后,进入裂纹扩展阶段,首先开始稳定扩展,裂纹达到临街尺寸后,随着进一步的交变应力、应变作用下,金属材料无法承受,裂纹开始突然间失稳,材料瞬间产生破坏,发生断裂。
简而言之,疲劳破坏过程分为:裂纹萌生,裂纹扩展和失稳断裂三个阶段。
每个阶段具体如下:裂纹萌生:由于应力集中,疲劳裂纹首先起源于材料部微观结构最薄弱的额区域,或者应力较高的区域。
裂纹萌生初期,长度小于0。
05mm~0。
1mm,此裂纹称为疲劳裂纹核。
随着疲劳进行,微观裂纹逐渐发展成宏观裂纹,肉眼可见。
铝合金材料疲劳裂纹萌生主要部位有滑移带、晶界、相界面三种裂纹扩展:疲劳裂纹萌生结束后,将进入裂纹扩展阶段。
此阶段又分为两个部分,首先是裂纹沿主滑移系,以纯剪切方式向扩展,扩展速率极低,其延伸围在几个晶粒长度之间。
其次,在晶界的阻碍作用下,使扩展方向逐渐垂直于主应力即拉应力方向,并形成疲劳条纹或称为疲劳辉纹,一条辉纹就是一次循环的结果。
第一阶段的裂纹扩展速度慢,长度小,所以该阶段的形貌特征并不明显。
而第二阶段的穿晶扩展,其扩展速率随循环周次增加而增大,扩展程度也较为明显,多数材料的第二阶段可用电子显微镜观察到疲劳条纹,有些甚至能用肉眼观察到。
不同材料的疲劳条纹各不相同,形貌也是种类繁多,有与裂纹扩展方向垂直略呈弯曲并相互行的沟槽状花样,有断口比较平滑而且分布有贝纹或海滩花样,有时则呈现以源区为中心的放射线,疲劳条纹是疲劳断口最有代表性的特征。
一般情况下,疲劳裂纹扩展区在整个断口所占面积较大。
疲劳裂纹扩展阶段是材料整个疲劳寿命的主要组成部分。
不同铝合金材料裂纹扩展的两个阶段也有不同的寿命,在材料表面光滑试件中,第一阶段的扩展时间占整个疲劳寿命的绝大部分;而在有缺口的试件中,第一阶段几乎可以忽略,第二阶段的传播是整个疲劳裂纹扩展的寿命。
裂纹失稳:疲劳裂纹扩展到一定长度即临界长度时,材料表面不足以承受外部载荷,在下一次加载中将发生失稳扩展,导致快速断裂。
这一阶段是构件寿命的最后阶段,失稳扩展到断裂这一短暂过程对于构件寿命的贡献是可以忽略的,裂纹最后失稳快速扩展所形成的断口区域称为瞬断区,材料性质不同,断口相貌也截然不同。
1.5 疲劳寿命的影响因素1.5.1材料因疲劳特性与合金成分有关,成分决定了合金组织以及强化效果;同时,合金的显微组织也冶金过程中的缺陷也对合金疲劳有很大程度的影响,裂纹源可能由夹杂物,晶粒大小,晶粒偏析,晶界疏松引起。
涛等研究了Al-Si系铸造铝合金疲劳性能,发现铸造过程难以避免的孔洞及Si颗粒大小、形貌均对铸造铝合金材料疲劳裂纹的萌生有重要影响;Zhai[7]通过对铝锂合金疲劳性能各向异性的研究发现,在轧制方向强度低,疲劳性能也最差,疲劳裂纹多沿方向萌生,而在厚度方向强度较高,鲜见裂纹的萌生,疲劳性能也自然最佳;时效处理是改善铝合金性能的有效途径,由于其改变了合金微观组织结构,自然也对合金疲劳特性影响颇大;Sharma等通过对不同时效处理后的AA 2219 铝合金进行疲劳试验,结果表明自然时效及欠时效处理后的合金疲劳性能较好,鲜见疲劳裂纹的萌生;而峰时效和过时效处理后的合金,其多出萌生疲劳裂纹切裂纹扩展速率较高,疲劳性能不佳。
1.5.2构件状态合金的疲劳特性也跟表面粗糙度、材料尺寸、几何形状。
表面凹凸。
壁厚均匀性有关。
Suraratchai等对影响铝合金疲劳寿命的因素进行了研究,其对合金表面粗糙度进行了有限元分析,结果表明由于材料表面凹凸不平而引起的应力集中,是损害疲劳寿命的源头;肖骥研究了7475铝合金板材的疲劳性能,在疲劳试验中表现最好的T-L平面上的试件进行了喷丸处理,结果发现,经过喷丸处理之后,并不是一定提高了试件的疲劳强度,在喷丸处理的过程中,在引入残余压应力的同时,也破坏了试件表面的平整度。
残余压应力将提高试件的疲劳强度,而过高的粗糙度,将使试件表面很容易成为裂纹源。
1.5.3工作条件载荷的大小和加载方式及加载频率是合金材料疲劳寿命的决定性因素。
岗等研究了2E12铝合金在不同应力水平下的疲劳性能及疲劳裂纹扩展速率,结果表明缺口的存在降低了疲劳强度,随着应力比的提高,疲劳强度也大幅度改善;蹇海根等通过金相、电镜扫描显微技术对比了不同应力下铝合金的疲劳断口显微组织,发现疲劳裂纹萌生处与材料表面的距离随加载应力升高而减小,加载应力越高,疲劳源区面积越小,裂纹扩展区的疲劳辉纹间距越大,且随着应力的增大,断口上疲劳裂纹扩展区的面积减小,瞬断区的面积增大。
同时材料寿命也受工作环境如温度、周边介质等因素影响。
Gasqueres等[13]通过对AA 2024铝合金疲劳裂纹扩展规律的研究发现,正常室温下,疲劳裂纹扩展进入第二阶段后,将环境温度调至223 K,裂纹长大又转为第一阶段的扩展规律,而且此时裂纹的扩展受到温度和气压的共同影响。
铝合金疲劳特性的影响因素很多,从单一或几个因素的考虑对铝合金材料疲劳寿命进行研究并不准确,建立相应的科学模型,综合考虑所有因素从而精确地预测材料的疲劳寿命是需要进一步深入研究的重点。