断口分析
金属材料断口分析的步骤与方法
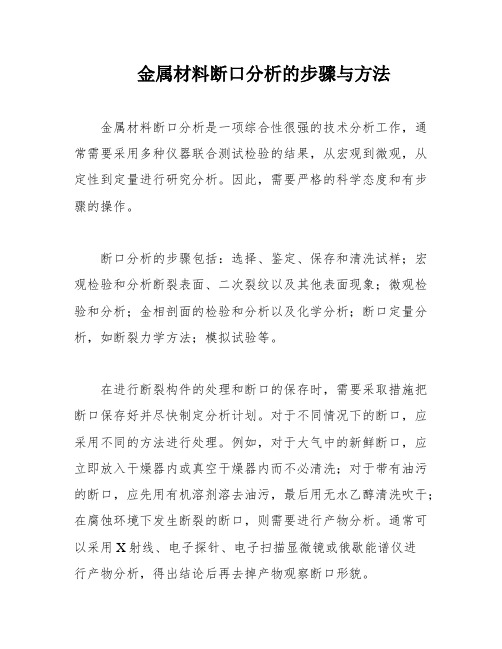
金属材料断口分析的步骤与方法金属材料断口分析是一项综合性很强的技术分析工作,通常需要采用多种仪器联合测试检验的结果,从宏观到微观,从定性到定量进行研究分析。
因此,需要严格的科学态度和有步骤的操作。
断口分析的步骤包括:选择、鉴定、保存和清洗试样;宏观检验和分析断裂表面、二次裂纹以及其他表面现象;微观检验和分析;金相剖面的检验和分析以及化学分析;断口定量分析,如断裂力学方法;模拟试验等。
在进行断裂构件的处理和断口的保存时,需要采取措施把断口保存好并尽快制定分析计划。
对于不同情况下的断口,应采用不同的方法进行处理。
例如,对于大气中的新鲜断口,应立即放入干燥器内或真空干燥器内而不必清洗;对于带有油污的断口,应先用有机溶剂溶去油污,最后用无水乙醇清洗吹干;在腐蚀环境下发生断裂的断口,则需要进行产物分析。
通常可以采用X射线、电子探针、电子扫描显微镜或俄歇能谱仪进行产物分析,得出结论后再去掉产物观察断口形貌。
总之,断口分析是一项重要的金属材料分析技术,需要严格的科学态度和有步骤的操作。
去除腐蚀产物的方法之一是干剥法。
使用醋酸纤维纸(AC纸)进行清理是最有效的方法之一,特别是在断口表面已经受到腐蚀的情况下。
将一条厚度约为1mm的AC纸放入丙酮中泡软,然后放在断口表面上。
在第一张条带的背后衬上一块未软化的AC纸,然后用夹子将复型牢牢地压在断口表面上。
干燥后,使用小镊子将干复型从断口上揭下来。
如果断口非常污染,可以重复操作,直到获得一个洁净无污染的复型为止。
这种方法的一个优点是,它可以将从断口上除去的碎屑保存下来,以供以后鉴定使用。
此外,还可以使用复型法来长期保存断口。
断口表面不能使用酸溶液清洗,因为这会影响断口分析的准确性。
对于在潮湿空气中暴露时间比较长、锈蚀比较严重的断口,以及高温下使用的有高温氧化的断口,一定要去除氧化膜后才能观察,以避免假象。
如果一般有机溶液、超声波洗涤和复型都不能洁净断口表面,可以采用化学清洗。
断口分析

故障件的断口分析在形形色色的故障分析过程中,人们常会瞧到一些损坏零件的断口,但就是人们缺乏“读懂”它的经验,不能从它的断口处判断其损坏的真正原因而贻误了战机。
这里结合整改过程中的一些实例作些介绍,希望能对您有所帮助!对于汽车常用碳素钢与合金钢而言,其常见断口有:1.韧性(塑性)断口:发生明显塑性变形的断裂统称为塑性断裂。
断口形貌为韧性(塑性)断口,断口呈暗灰色没有金属光泽瞧不到颗粒状形貌,断口上有相当大的延伸边缘。
2.疲劳弯曲断口:2-1 在抗拉极限范围内的疲劳弯曲断口:出现典型的疲劳裂纹源区、裂纹扩展区与瞬时断裂区特征(下面将详述)。
2-2 超过抗拉极限范围内的弯曲断口:不具有典型的疲劳断口特征,属于不正常的弯曲断裂。
其断口特征:沿弯曲方向上下呈灰褐色无金属光泽的断层;而内层呈银灰色白亮条状新断口(见图1)。
图13.典型的金属疲劳断口典型的疲劳断口定会出现疲劳裂纹源区、裂纹扩展区与瞬时断裂区三个特征。
断口具有典型的“贝壳状”或称“海滩状”。
3-1 疲劳裂纹源区:就是疲劳裂纹萌生的策源地,它处于机件的表面,形状呈平坦、白亮光滑的半圆或椭圆形,这就是因为疲劳裂纹的扩展过程速度缓慢,裂纹经反复挤压摩擦而形成的。
它所占有的面积较其她两个区要小很多。
疲劳裂纹大多就是因受交变载荷的机件表面有缺陷;譬如裂纹、脱碳、硬伤痕、焊点等缺陷形成应力集中而引起的。
疲劳裂纹点在同一个机件上可能有多处,换句话说可能有多处疲劳裂纹源区,这需要我们去仔细解读疲劳断口。
3-2 疲劳裂纹扩展区:就是形成疲劳裂纹后慢速扩展的区域。
它就是判断疲劳断裂的最重要的特征区。
它以疲劳源区为中心,与裂纹扩展方向垂直呈半圆形或扇形的弧线,也称疲劳弧线呈“贝纹状”。
疲劳弧线就是因机器运转时的负载变化、反复启动与停止而留下的塑性变形痕迹线。
金属材料的塑性好、工作温度高及有腐蚀介质存在时则弧线清晰。
3-3 瞬时断裂区:由于疲劳裂纹不断扩展使机件的有效断面减小,因此应力不断增加直至截面应力达到材料许用应力时,瞬时断裂便发生了。
金属断口分析

断口(断裂)的基本特征与机理
滑移分离
滑移的形式
波状滑移:在晶体材料中不仅有直线型的滑移线或滑移带,
而且有波状的滑移线或滑移带。尤其是体心立方材料,由于它 没有最密排的晶面,所以滑移没有一个确定的晶面,一般可能 在几个较密的低指数面滑移,如{110}、{112}、{123}。而密排 方向是<111>,它便是滑移方向。共有48个滑移系,如果有很
断口(断裂)的基本特征与机理
滑移分离
滑移的形式 滑移碎化:当一个晶粒产生滑移变形时,它受到相邻晶粒的 束缚而阻止该晶粒的滑移,这样滑动的晶粒随着滑移变形量的 增加而产生硬化现象;另一方面这个晶粒边界的应力场将促进 相邻晶粒的滑移。与此同时,这个晶粒开动了更多的滑移系来 反抗相邻晶粒的阻力,由此产生了多重滑移而引起滑移碎化。 扭折带:在晶体材料滑移变形时,有时出现滑移部分的晶体 相对于基体旋转一定的角度,滑移区域内的滑移线成S形弯曲, 称为扭折带。扭折带两端的晶体区域具有不同的去向,但扭折 带平面总是大致垂直于主要参与滑移的方向。
断口分析的作用及意义
断裂失效分析从裂纹和断口的宏观、微 观特征入手,研究断裂过程和形貌特征与 材料性能、显微组织、零件受力状态及环 境条件之间的关系,从而揭示断裂失效的 原因和规律。
断裂力学方法和金属物理方法之间架起 联系的桥梁。
断口(断裂)分类
1.断裂与断口 构件或试样在外力作用下导致裂纹形成扩展 而分裂为两部分(或几部分)的过程称为断 裂。包括裂纹萌生、扩展和最后瞬断三个阶 段。 各阶段的形成机理及其在整个断裂过程中所 占的比例,与构件形状、材料种类、应力大 小与方向、环境条件等因素有关。 断裂形成的断面称为断口。断口上详细记录 了断裂过程中内外因素的变化所留下的痕迹 与特征,是分析断裂机理与原因的重要依据。
断口分析方法

1. 前言
断口是断裂过程的最真实,完整的纪录, 从宏观到微观的断口分析可以揭示断裂过 程中从裂纹的形核,长大到断裂的各个进 程中主断裂面的受力情况,介质环境情况, 材料制造情况,以及损伤过程等. 断口分析的三大作用:1 作为结构材料研 究的重要内容之一,用于研究材料的断裂 机理;2 断裂失效分析; 3 评价材料 .
3. 断口的宏观分析
目的: 分析断裂的起源位置;裂纹的扩展方向; 根据断口变形的情况和断口宏观痕迹大致 判断断裂的性质,受力状况,环境状况, 材料缺陷状况等. 选择取样分析位置,为进一步的断口微观 分析或其他相关检验做准备和指明方向.
判断裂纹源和裂纹扩展方向的原则
在有放射状花样的情况下,放射方向是裂纹扩展方向,沿 反方向可追溯到裂纹源;分叉裂纹分叉方向是裂纹扩展方 向. 弧线形的贝纹状花样是裂纹扩展速度发生变化在断口上留 下的痕迹,一般情况下弧线凸向为裂纹扩展方向; 断口的色泽可资参考,如氧化情况,腐蚀产物的厚度,疲 劳断口的表面磨光情况等等; 对于装备中多个元件发生断裂的情况,主要根据低应力断 裂还是大应力断裂来判断首断件,一般是低应力断裂件为 首断件. 对于韧性断裂,可通过裂纹的走向,鼓包,壁厚减薄情况 等判断起爆点.
断口分析分为宏观断口分析和微观断口分 析两部分,二者必须相互结合.宏观断口 分析主要是用肉眼或借助普通放大镜进行 观察,从而分析裂纹的扩展方向,断裂的 起源位置,断裂过程的载荷情况等断裂的 宏观特征;微观断口分析需要借助光学和 电子显微分析仪器进行观察和分析,通过 对断口的微观形态,结晶学特征,残留元 素成分等理化特征的分析,确定断裂的类 型和断裂的机理.
2. 断口分析样品的制备
取样:最好采用手锯切割试样;采用砂轮切割要 注意避免过热;采用线切割前要对断口进行保 护;人工启开裂纹时最好将试样冷至材料低温脆 性转变温度以下,但之后应及时烘干试样; 除油:一般情况下建议采用汽油或酒精,采用丙 酮则发生二次污染的可能性较大. 除锈:除锈前应对断口进行腐蚀产物等的分析, 以免清洗后损失该方面的信息.根据材料的成份 和锈蚀状态选择清洗液. 对于不能现场取样的断口,可以采用火棉胶复型 等办法得到断口形貌复形,和萃取断口残留物进 行显微分析.采用复型最重要的是避免假象.
金属断口机理及分析

名词解释延性断裂:金属材料在过载负荷的作用下,局部发生明显的宏观塑性变形后断裂。
蠕变:金属长时间在恒应力,恒温作用下,慢慢产生塑性变形的现象。
准解理断裂:断口形态与解理断口相似,但具有较大塑性变形〔变形量大于解理断裂、小于延性断裂〕是一种脆性穿晶断口沿晶断裂:裂纹沿着晶界扩展的方式发生的断裂。
解理断裂:在正应力作用下沿解理面发生的穿晶脆断。
应力腐蚀断裂:拉应力和腐蚀介质联合作用的低应力脆断疲劳辉纹:显微观察疲劳断口时,断口上细小的,相互平行的具有规则间距的,与裂纹扩展方向垂直的显微条纹。
正断:断面取向与最大正应力相垂直〔解理断裂、平面应变条件下的断裂〕韧性:材料从变形到断裂过程中吸收能量的大小,是材料强度和塑性的综合反映。
冲击韧性:冲击过程中材料吸收的功除以断的面积。
位向腐蚀坑技术:利用材料腐蚀后的几何形状与晶面指数之间的关系研究晶体取向,分析断裂机理或断裂过程。
河流把戏:解理台阶及局部塑性变形形成的撕裂脊线所组成的条纹。
其形状类似地图上的河流。
断口萃取复型:利用AC纸将断口上夹杂物或第二相质点萃取下来做电子衍射分析确定这些质点的晶体构造。
氢脆:金属材料由于受到含氢气氛的作用而引起的低应力脆断。
卵形韧窝:大韧窝在长大过程中与小韧窝交截产生的。
等轴韧窝:拉伸正应力作用下形成的圆形微坑。
均匀分布于断口外表,显微洞孔沿空间三维方向均匀长大。
第一章断裂的分类及特点1.根据宏观现象分:脆性断裂和延伸断裂。
脆性断裂裂纹源:材料外表、内部的缺陷、微裂纹;断口:平齐、与正应力相垂直,人字纹或放射花纹。
延性断裂裂纹源:孔穴的形成和合并;断口:三区,无光泽的纤维状,剪切面断裂、与拉伸轴线成45º .2.根据断裂扩展途分:穿晶断裂与沿晶断裂。
穿晶断裂:裂纹穿过晶粒内部、可能为脆性断裂也可能是延性断裂;沿晶断裂:裂纹沿着晶界扩展,多属脆断。
应力腐蚀断口,氢脆断口。
3根据微观断裂的机制上分:韧窝、解理〔及准解理〕、沿晶和疲劳断裂4根据断面的宏观取向与最大正应力的交角分:正断、切断正断:断面取向与最大正应力相垂直〔解理断裂、平面应变条件下的断裂〕切断:断面取向与最大切应力相一致,与最大应力成45º交角〔平面应力条件下的撕裂〕根据裂纹尖端应力分布的不同,主要可分为三类裂纹变形:裂纹张开型、边缘滑开型〔正向滑开型〕、侧向滑开型〔撒开型〕裂纹尺寸与断裂强度的关系Kic:材料的断裂韧性,反映材料抗脆性断裂的物理常量〔不同于应力强度因子,与K准则相似〕:断裂应力〔剩余强度〕 a :裂纹深度〔长度〕Y:形状系数〔与试样几何形状、载荷条件、裂纹位置有关〕脆性材料K准则:KI是由载荷及裂纹体的形状和尺寸决定的量,是表征裂纹尖端应力场强度的计算量;KIC是材料固有的机械性能参量,是表示材料抵抗脆断能力的试验量第二章裂纹源位置的判别方法:T型法〔脆断判别主裂纹〕,分差法〔脆断判别主裂纹〕,变形法〔韧断判别主裂纹〕,氧化法〔环境断裂判别主裂纹〕,贝纹线法〔适用于疲劳断裂判别主裂纹〕。
金属材料断口分析的步骤与方法

金属材料断口分析的步骤与方法断口分析通常是一个从宏观到微观,从定性到定量的分析过程,并且是应用多种仪器联合测试检验的结果,是综合性很强的技术分析工作。
因此需要严格的科学态度,精心地、有步骤地进行研究分析。
断口分析步骤:(1)所有试样的选择、鉴定、保存以及清洗;(2)宏观检验和分析(断裂表面、二次裂纹以及其他的表面现象);(3)微观检验和分析;(4)金相剖面的检验和分析以及化学分析;(5)断口定量分析(断裂力学方法);(6)模拟试验。
1 断裂构件的处理及断口的保存在确定了断裂的金属构件后,就要采取措施把断口保存好,尽快制定分析计划。
通常金属构件的断裂不止一个断口,有时要立即判断主断口有困难,此时应该把所有断件收集好,在收集过程中切勿把断口碰伤或对接,也不要在断口上使用防蚀涂层。
保护和清理断口是断口分析的一个重要前提。
对断口和裂纹轨迹进行充分检查后方可进行清洗。
对于不同情况下的断口应该用不同方法处理:(1)大气中的新鲜断口,应立即放入干燥器内或真空干燥器内而不必清洗。
(2)对于带有油污的断口,首先用汽油,然后用丙酮、三氯甲烷、石油醚及苯等有机溶剂溶去油污,最后用无水乙醇清洗吹干。
当浸没处理还不能去除油污时,可使用蒸汽或超声波方法进一步去除。
(3)在腐蚀环境下发生断裂的断口,通常在断口上覆盖一层腐蚀产物,这层产物对于分析断裂原因是非常有用的,但对断口形貌观察常常带来很大的麻烦。
在这种情况下,需要用综合分析的方法来考虑。
因为有许多腐蚀产物容易水解或分解,因此进行产物分析要抓紧时间,同时不要进行任何清洗和处理。
通常把带有腐蚀产物的断口试样,先用X射线、电子探针、电子扫描显微镜或俄歇能谱仪进行产物分析,得出结论后去掉产物再观察断口形貌。
去掉腐蚀产物有时可采用干剥法。
用醋酸纤维纸(称AC纸,由7%的醋酸纤维素、丙酮溶液制成厚度0.1~1mm的均匀薄膜)复型进行清理是最有效的方法之一,尤其是断口表面已经受到腐蚀的时候。
断口分析报告
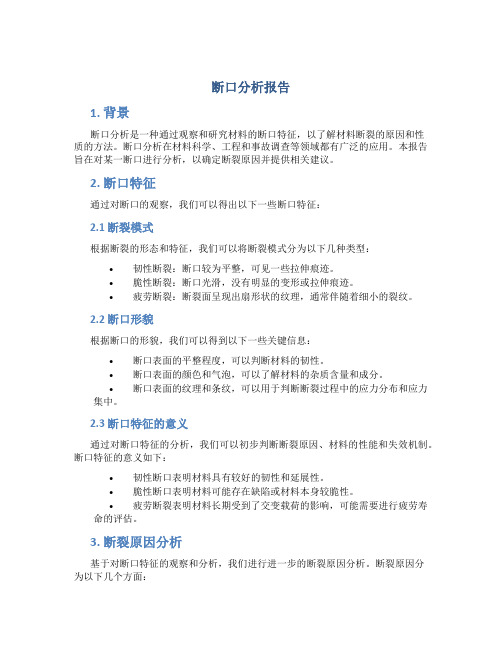
断口分析报告1. 背景断口分析是一种通过观察和研究材料的断口特征,以了解材料断裂的原因和性质的方法。
断口分析在材料科学、工程和事故调查等领域都有广泛的应用。
本报告旨在对某一断口进行分析,以确定断裂原因并提供相关建议。
2. 断口特征通过对断口的观察,我们可以得出以下一些断口特征:2.1 断裂模式根据断裂的形态和特征,我们可以将断裂模式分为以下几种类型:•韧性断裂:断口较为平整,可见一些拉伸痕迹。
•脆性断裂:断口光滑,没有明显的变形或拉伸痕迹。
•疲劳断裂:断裂面呈现出扇形状的纹理,通常伴随着细小的裂纹。
2.2 断口形貌根据断口的形貌,我们可以得到以下一些关键信息:•断口表面的平整程度,可以判断材料的韧性。
•断口表面的颜色和气泡,可以了解材料的杂质含量和成分。
•断口表面的纹理和条纹,可以用于判断断裂过程中的应力分布和应力集中。
2.3 断口特征的意义通过对断口特征的分析,我们可以初步判断断裂原因、材料的性能和失效机制。
断口特征的意义如下:•韧性断口表明材料具有较好的韧性和延展性。
•脆性断口表明材料可能存在缺陷或材料本身较脆性。
•疲劳断裂表明材料长期受到了交变载荷的影响,可能需要进行疲劳寿命的评估。
3. 断裂原因分析基于对断口特征的观察和分析,我们进行进一步的断裂原因分析。
断裂原因分为以下几个方面:3.1 材料缺陷材料缺陷是引起断裂的常见原因之一。
缺陷可以存在于材料的制备、成型和使用过程中。
常见的材料缺陷包括:气孔、夹杂物、夹层等。
通过观察断口特征,我们可以判断是否存在明显的材料缺陷。
3.2 施加载荷材料在受到外部力的作用下可能会发生断裂。
施加在材料上的载荷可能包括拉力、压力、剪切力等。
通过观察断口形貌和纹理,我们可以初步判断受力方向和载荷大小。
3.3 环境因素环境因素也可能对材料的断裂起到一定的影响。
例如,高温、湿度、腐蚀等环境条件可能导致材料的性能变化和失效。
通过分析断口的颜色、气泡等特征,我们可以初步判断是否存在环境因素导致的断裂。
金属材料断口分析-精彩部分

断口分析总结
1 断口微观分析 系统介绍:
2 1,解理与准解 理;
3 2,剪切断裂;
4 3,疲劳断裂;
4,晶间断裂
5等 断口的一般 特征
解理与准解理断裂的断口具有以下之一 的重要特征----解理部分:
解理与准解理断裂的断口具有以下之一 的重要特征----准解理部分:
剪切断裂断口的一般特征
下面介绍:
01
断口微观分析的
系统说明:
02
1解理与准解理;
03
2剪切断裂;
04
3疲劳断裂;
05
4晶间断裂等
断口特征
有关断口分析的 基本概念介绍--10; 冲击断口的宏观 形貌及示意图
V缺口试样
断口
示意图
有关断口分 析的基本概 念介绍---11;
带有中央切口板 试样的反复交变 拉伸的疲劳断口
有关断口分析的基本概念 介绍---12; 弯曲与旋转弯曲疲劳断口
a, Ⅰ; b, Ⅱ; c, Ⅲ;
平面应变和平面应力时断口 有关断口分析的基本概念介 绍---4;
a,平面应变时的断口,正断 型;
b,平面应力时的断口,切断 型;
屈服区大小沿板厚方向改变的情况(穿透裂纹“哑铃状”) 有关断口分析的基本概念介绍---4;
有关断口分析 的基本概念介 绍---5; 静载荷下光滑 圆试样的拉伸 断口宏观形貌 示意图
有关断口分析的基本概 念介绍---6;
静载荷下缺口拉伸试样 断口宏观形貌示意图
有关断口分析的基 本概念介绍---7; 裂纹不对称扩展的 断口形态示意图
有关断口分 析的基本概 念介绍---8; 矩形拉伸试 样的断口形 貌及示意图
有关断口分析的 基本概念介绍--9;
- 1、下载文档前请自行甄别文档内容的完整性,平台不提供额外的编辑、内容补充、找答案等附加服务。
- 2、"仅部分预览"的文档,不可在线预览部分如存在完整性等问题,可反馈申请退款(可完整预览的文档不适用该条件!)。
- 3、如文档侵犯您的权益,请联系客服反馈,我们会尽快为您处理(人工客服工作时间:9:00-18:30)。
故障件的断口分析
在形形色色的故障分析过程中,人们常会看到一些损坏零件的断口,但是人们缺乏“读懂”它的经验,不能从它的断口处判断其损坏的真正原因而贻误了战机。
这里结合整改过程中的一些实例作些介绍,希望能对您有所帮助!
对于汽车常用碳素钢和合金钢而言,其常见断口有:
1.韧性(塑性)断口:发生明显塑性变形的断裂统称为塑性断裂。
断口形貌为韧性(塑性)断口,断口呈暗灰色没有金属光泽看不到颗粒状形貌,断口上有相当大的延伸边缘。
2.疲劳弯曲断口:
2-1 在抗拉极限范围内的疲劳弯曲断口:出现典型的疲劳裂纹源区、裂纹扩展区和瞬时断裂区特征(下面将详
述)。
2-2 超过抗拉极限范围内的弯曲断口:不具有典型的疲劳断口特征,属于不正常的弯曲断裂。
其断口特征:沿
弯曲方向上下呈灰褐色无金属光泽的断层;而内层呈
银灰色白亮条状新断口(见图1)。
图1
3.典型的金属疲劳断口
典型的疲劳断口定会出现疲劳裂纹源区、裂纹扩展区和瞬时断裂区三个特征。
断口具有典型的“贝壳状”或称“海滩状”。
3-1 疲劳裂纹源区:是疲劳裂纹萌生的策源地,它处于机件的表面,形状呈平坦、白亮光滑的半圆或椭圆形,这是因为疲劳裂纹的扩展过程速度缓慢,裂纹经反复挤压摩擦而形成的。
它所占有的面积较其他两个区要小很多。
疲劳裂纹大多是因受交变载荷的机件表面有缺陷;譬如裂纹、脱碳、硬伤痕、焊点等缺陷形成应力集中而引起的。
疲劳裂纹点在同一个机件上可能有多处,换句话说可能有多处疲劳裂纹源区,这需要我们去仔细解读疲劳断口。
3-2 疲劳裂纹扩展区:是形成疲劳裂纹后慢速扩展的区域。
它是判断疲劳断裂的最重要的特征区。
它以疲
劳源区为中心,与裂纹扩展方向垂直呈半圆形或扇
形的弧线,也称疲劳弧线呈“贝纹状”。
疲劳弧线
是因机器运转时的负载变化、反复启动和停止而留
下的塑性变形痕迹线。
金属材料的塑性好、工作温
度高及有腐蚀介质存在时则弧线清晰。
3-3 瞬时断裂区:由于疲劳裂纹不断扩展使机件的有效断面减小,因此应力不断增加直至截面应力达到材
料许用应力时,瞬时断裂便发生了。
材料塑性大时,
断口呈暗灰色纤维状;脆性材料的断口呈结晶状。
小结:
要点:
疲劳宏观断口的特征
断口拥有三个形貌不同的区域:疲劳源、疲劳区、瞬断区。
随材质、应力状态的不同,三个区的大小和位置不同。
1、疲劳裂纹源区
裂纹的萌生地;裂纹处在亚稳扩展过程中。
由于应力交变,断面摩擦而光亮。
加工硬化。
随应力状态及应力大小的不同,可有一个或几个疲劳源。
2、疲劳裂纹扩展区(贝纹区)
断面比较光滑,并分布有贝纹线。
循环应力低,材料韧性好,疲劳区大,贝纹线细、明显。
有时在疲劳区的后部,还可看到沿扩展方向的疲劳台阶(高应力作用)。
3、瞬时断裂区
一般在疲劳源的对侧。
脆性材料为结晶状断口;
韧性材料有放射状纹理,边缘为剪切唇。
范例一:前稳定杆拉杆断头
最近前稳定杆拉杆在市场上出现多次短头现象,见图2
图2
其断口形状见图3.
图3
分析:由于故障里程都很短,理应不属于疲劳断裂的范畴,但从断口来看它更像2-2中所描述的超过抗拉极限
范围内的弯曲断口。
引起此故障的可能因素有二:
1) 在极限载荷下产生的弯曲断裂
2) 材料与工艺上的原因
首先作一简单验算(见图4):
已知:
前稳定杆扭转角刚度
K β=5000 Nm/rad=5000/57.3=87.3Nm/度
稳定杆作用力半径 R=355mm=0.355m
当汽车满载,车轮上下跳动±100mm 时,
稳定杆的工作扭角 β=±7.5°
A=25mm
计算:
稳定杆的交变力矩 M 0= ±K β×β=±87.3×7.5°=±655 Nm
稳定杆端头作用力 N R M F 1844355
.0655±=±=±=
图4
拉杆AA 断面处的弯曲应力σ
233/461001.05.218441
1.01.0cm N a F d M =⨯=⨯⨯==σ 拉杆材料为20号钢,许用应力是σ=45000N/cm 2,在极限状态下就有可能产生断头故障,不过这还要进一步调查分析后才能下结论。
范例二。
球笼驱动轴断裂原因分析
1.问题:08-02-25日一辆下线车在打力矩时在花键轴处断裂(图1)。
2.损坏件断口描述:(见图2)
1)在花键部位被拉断。
2)断口有两个区域,一为暗区(已产生的裂纹断面);
另一为亮区(新拉裂的断面)。
3)在暗区边缘沿花键根部有一明显的淬火裂纹(因它而扩散到整个暗区,形成断裂面)。
4)断口金相颗粒比较细小均匀,说明热处理正常。
图2
3.基本分析
1)暗区系零件中频淬火时,因花键根部出现淬裂导致该区大面积与主体裂开。
2)剩余的亮区部分,在M22×1.5螺旋打力矩时,承受不了强大的轴向拉力而拉断。
4.验证计算
1)已知:材料为55号碳素钢;花键齿的根径D=φ
23mm
螺纹M22×1.5 螺距 t=1.5mm 扭紧力矩 M=217±20 Nm
55号钢的屈服极限为 σs=382 N/mm 2 抗拉强度为σT=647 N/mm 2
螺纹和螺母之间的摩擦系数μ=0.15(钢—钢)
2)验算:
螺母在用M 力矩扭紧时,计入摩擦的影响,所产
生的轴向力Q 可按以下公式计算:
d t t r M M Q πμπ15.02+-=
=+⨯-⨯=22
15.05.15.115.0112370002370002ππQ 125044 N
从断口亮区所占的面积约为A=(0.78×
222)/2=189mm 2
断口的拉应力:
σ=Q/A=125044/189=662 N/mm 2
该值已达到或超过55号钢的抗拉强度[σT ]
=660N/mm 2
必然在打扭矩时被拉断,如果淬火时零件未出
现淬火裂纹,则断口的拉应力σ=330N/mm2,
大大小于55号钢的抗拉强度[σT]
=660N/mm2,因此是安全的。
5.结论:
损坏的样件是由于产生淬火裂纹,从而导致打扭矩时拉断。
摆臂断裂。