粉末冶金新技术的研究详解
粉末冶金高速压制技术的原理、特点及其研究进展
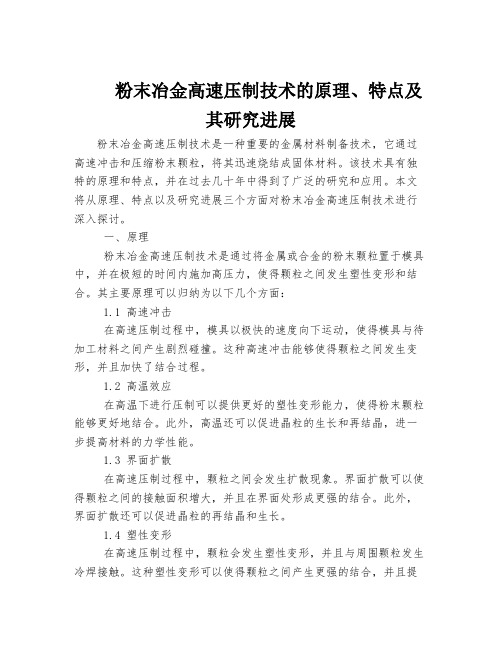
粉末冶金高速压制技术的原理、特点及其研究进展粉末冶金高速压制技术是一种重要的金属材料制备技术,它通过高速冲击和压缩粉末颗粒,将其迅速烧结成固体材料。
该技术具有独特的原理和特点,并在过去几十年中得到了广泛的研究和应用。
本文将从原理、特点以及研究进展三个方面对粉末冶金高速压制技术进行深入探讨。
一、原理粉末冶金高速压制技术是通过将金属或合金的粉末颗粒置于模具中,并在极短的时间内施加高压力,使得颗粒之间发生塑性变形和结合。
其主要原理可以归纳为以下几个方面:1.1 高速冲击在高速压制过程中,模具以极快的速度向下运动,使得模具与待加工材料之间产生剧烈碰撞。
这种高速冲击能够使得颗粒之间发生变形,并且加快了结合过程。
1.2 高温效应在高温下进行压制可以提供更好的塑性变形能力,使得粉末颗粒能够更好地结合。
此外,高温还可以促进晶粒的生长和再结晶,进一步提高材料的力学性能。
1.3 界面扩散在高速压制过程中,颗粒之间会发生扩散现象。
界面扩散可以使得颗粒之间的接触面积增大,并且在界面处形成更强的结合。
此外,界面扩散还可以促进晶粒的再结晶和生长。
1.4 塑性变形在高速压制过程中,颗粒会发生塑性变形,并且与周围颗粒发生冷焊接触。
这种塑性变形可以使得颗粒之间产生更强的结合,并且提高材料的密度和力学性能。
二、特点与传统冶金加工方法相比,粉末冶金高速压制技术具有以下几个特点:2.1 高效快速由于采用了高速冲击和压缩技术,这种方法具有快速、高效的特点。
一般情况下,整个过程只需要几十毫秒到几秒钟即可完成。
2.2 高质量由于采用了高温和高压力的条件,粉末冶金高速压制技术可以获得高密度和均匀的材料。
此外,由于塑性变形和界面扩散的作用,材料的结合强度也得到了显著提高。
2.3 复杂形状粉末冶金高速压制技术可以制备各种复杂形状的金属零件。
由于采用了模具,可以根据需要设计出各种形状和尺寸的零件。
2.4 节约能源与传统冶金加工方法相比,粉末冶金高速压制技术具有节约能源的优势。
粉末冶金新技术

磁压制可达到较高的密度,从而降低烧结收缩
率。目前许多动磁压制的应用已接近工业化 阶段,第一台动磁压制系统已在运行中。
24
二、粉末冶金成型新技术 2.高速压制 瑞典开发出粉末冶的又一次重大技术突破。高速压制采
用液压冲击机,它与传统压制有许多相似之处,但关 键是压制速度比传统快500~1000倍,其压头速度高
定程度的变形)。
这种粉末可用于汽车工业,特别适用于发动机部
件,传动部件及近终形齿轮等。
6
一、制粉新技术 2.软磁金属复合粉制备 目前软磁复合材料已得到广泛应用。它们是在 纯铁粉颗粒上包覆一层氧化物或热固化树脂进行绝 缘而制成的。在低频应用中,采用粗颗粒铁粉与热固 化树脂混合,获得高磁导率与低铁损的材料。高频应 用时,颗粒间需要更有效地进行绝缘,因而粒度要更 小,以进一步减少涡流损失。它可制成各向同性的软 磁复合部件,但不需要高温烧结。粉末晶粒度增大时, 磁导率增大,矫顽力降低。
形性。它是介于金属注射成形与传统模压之间的
一种成形工艺。
32
二、粉末成型新技术 流动温压技术的关键是提高混合粉末的流动性,主
要通过两种方法来实现:
第一种方法是向粉末中加入精细粉末。这种精细 粉末能够填充在大颗粒之间的间隙中,从而提高了混合 粉末的松装密度。 第二种方法是比传统粉末冶金工艺加入更多的粘
创铁基粉末冶金零部件应用新纪元”和“导致粉
末冶金技术革命”的新型成型技术。
28
二、粉末成型新技术 温压技术的特点 :
• 能以较低成本制造出高性能粉末冶金零部件;
• 提高零部件生坯密度和高强度,便于制造形状 复杂以及要求精密的零 部件 ; • 产品密度均匀。
高密度粉末冶金成形方法研究及优化

高密度粉末冶金成形方法研究及优化一、引言高密度粉末冶金成形技术是一种通过在粉末表面施加压力和温度实现金属材料成形的加工工艺。
该技术具有高效率、低成本、高精度、可逆性和可重复性等优点。
因此,在改进传统的金属成形过程以及开发新型金属材料时,高密度粉末冶金成形技术已成为一种备受关注的重要研究领域。
二、高密度粉末冶金成形方法的分类高密度粉末冶金成形技术根据成形前后粉末状况的变化,可分为以下几种方法:1. 等静压成形 (HIP)等静压成形是一种将高密度金属粉末放入成型模具中,先以低压力进行预压,随后在高温和高压力的条件下加以成形的加工方法。
等静压成形方法可以制造出具有高密度和高性能的复杂形状金属零件,如滚轮轴承、配气机构、燃气轮机叶片等等。
2. 烧结成型烧结成型是一种通过在制备过程中在粉末中添加一些粘结剂,使得粉末在高温条件下粘结在一起,然后进行成形的方法。
这种方法可以制造出高精度、高可靠性和抗热性能强的机械结构件和高强度、低密度的材料。
3. 挤压成形挤压成形是一种通过将金属粉末放入旋转式模具中,在模具两端施加压力来实现成形的加工方法。
这种方法较其他成形方式更为简单,适用于制作一些规则结构的中间件、链接件和管道接头。
4. 等离子粉末成形等离子粉末成形是一种将金属粉末喷射到等离子体火焰中进行高温加热,通过表面张力形成液态金属,并恰当地加压形成零件的一种成形工艺。
等离子粉末成形方法操作简单、可加工出具有高密度、高强度和高耐磨性的金属零件。
三、高密度粉末冶金成形方法的优化为了进一步提高高密度粉末冶金成形技术的加工效率、成形质量和材料性能,需要进行相应的优化。
优化方案一:材料的合理选择选择合适的材料是决定高密度粉末冶金成形成功与否的关键因素之一。
高密度粉末冶金成形的理想材料是那些粒度大小适中、形状均匀、流动性能好而且作为粉末冶金材料的化学成分方面相同或相似的金属粉末。
因此,选择质量优良、粘度适中的金属粉末是高密度粉末冶金成形过程中一个非常重要的环节。
《粉末冶金新技术》课件

4 等离子热惯性成形法
利用高速等离子体热传导原理,实现金属粉 末的瞬时烧结成形。
粉末成型技术
1
注射成型法
基于金属、合金或陶瓷粉末制成的糊状物通过注射成型机构,进而制得密实件。
2
热压成型法
将金属或陶瓷粉末放入橡胶模具中,在高温高压条件下进行成型。
3
热等静压成型法
将金属或陶瓷粉末放入模具中,在高温高压条件下进行成型。
2 粉末冶金的未来发展
随着科技的不断进步,粉末冶金技术将继续创新,为各个领域提供更加先进和优质的材 料。
3 粉末冶金的应用前景
粉末冶金材料的应用领域将会进一步拓展,为人类的生活和工业发展带来更多的便利和 创新。
粉末冶金的发展现状
当前,粉末冶金技术已经取得了许多突破,应用范围不断扩大。
粉末制备技术
1 机械合金化法
通过高能球磨等方法,将金属粉末与化合物金属离子,制备溶胶,再通过凝胶 化和烧结得到陶瓷制品。
3 沸腾床法
通过控制气体流动,在高温高压环境下制备 金属和陶瓷的纳米粉末。
《粉末冶金新技术》PPT 课件
粉末冶金新技术是一门前沿的材料学科,通过粉末制备与成型技术,实现材 料的精细化、多功能化和资源节约型制备,在航空、汽车、医疗和化学等领 域有广泛应用。
简介
粉末冶金概述
粉末冶金是一种通过将金属或陶瓷粉末加工、压实、烧结制得密实体材料的方法。
粉末冶金的历史
粉末冶金技术在古代文明中已有应用,如古埃及制造金属器具。
粉末冶金新发展趋势
新材料及制备技术
研发新材料和制备技术,如纳米 材料、复合材料等,推动粉末冶 金技术的发展。
资源节约型粉末冶金技术
开发更加环保、节约资源的粉末 冶金技术,实现可持续发展。
金属粉末冶金在模具制造中的应用研究

金属粉末冶金在模具制造中的应用研究现代制造业的发展离不开高精度模具的应用,而金属粉末冶金技术作为一种先进的制造工艺,已经在模具制造领域发挥了重要作用。
本文将探讨金属粉末冶金在模具制造中的应用研究,包括其原理、优势以及面临的挑战。
一、金属粉末冶金的原理金属粉末冶金是利用金属粉末通过成型、烧结等工艺制备零件的技术。
其基本原理是将金属粉末与其他添加剂按一定比例混合,然后通过压制成型和烧结工艺,使金属粉末颗粒之间发生冶金结合,形成致密的金属零件。
金属粉末冶金技术具有灵活性强、材料利用率高、生产过程环保等优势。
通过调节金属粉末成分和粒度,可以实现不同材料性能的调控和优化。
因此,在模具制造中应用金属粉末冶金技术,可以有效提高模具的材料性能和使用寿命。
二、金属粉末冶金在模具制造中的应用1. 陶瓷模具制造金属粉末冶金技术在陶瓷模具制造中有广泛应用。
传统的陶瓷模具制造过程需要使用粘土等材料,且成本高、制作周期长。
而采用金属粉末冶金技术制造陶瓷模具,不仅可以提高模具的耐磨性和耐腐蚀性,还能够减少生产周期和成本。
2. 超硬模具制造超硬材料如金刚石、立方氮化硼等具有极高的硬度和耐磨性,常用于制造需要高度精密加工的工具。
金属粉末冶金技术可以制备具有高硬度的超硬合金材料,用于制造高效的模具。
这些模具不仅可以提高工具的寿命和加工效率,还可以降低加工过程中的能耗和废料产生。
3. 复合材料模具制造复合材料在航天航空、汽车、电子等行业得到了广泛应用。
而金属粉末冶金技术可以制备具有优良综合性能的复合材料模具,用于制造复杂的复合材料产品。
这些模具可以提供更高的加工精度和复杂度,满足现代工业对产品的多样化需求。
三、金属粉末冶金在模具制造中面临的挑战虽然金属粉末冶金技术在模具制造中具有广泛应用前景,但目前仍面临一些挑战。
首先,金属粉末的成本较高,制造成本较传统工艺高。
随着技术的进步和规模效应的发挥,相信金属粉末冶金技术的成本将会逐渐降低。
铝合金粉末冶金的研究及应用
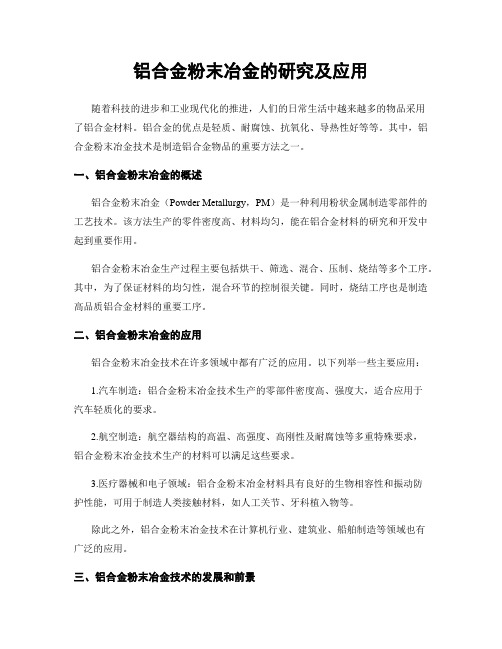
铝合金粉末冶金的研究及应用随着科技的进步和工业现代化的推进,人们的日常生活中越来越多的物品采用了铝合金材料。
铝合金的优点是轻质、耐腐蚀、抗氧化、导热性好等等。
其中,铝合金粉末冶金技术是制造铝合金物品的重要方法之一。
一、铝合金粉末冶金的概述铝合金粉末冶金(Powder Metallurgy,PM)是一种利用粉状金属制造零部件的工艺技术。
该方法生产的零件密度高、材料均匀,能在铝合金材料的研究和开发中起到重要作用。
铝合金粉末冶金生产过程主要包括烘干、筛选、混合、压制、烧结等多个工序。
其中,为了保证材料的均匀性,混合环节的控制很关键。
同时,烧结工序也是制造高品质铝合金材料的重要工序。
二、铝合金粉末冶金的应用铝合金粉末冶金技术在许多领域中都有广泛的应用。
以下列举一些主要应用:1.汽车制造:铝合金粉末冶金技术生产的零部件密度高、强度大,适合应用于汽车轻质化的要求。
2.航空制造:航空器结构的高温、高强度、高刚性及耐腐蚀等多重特殊要求,铝合金粉末冶金技术生产的材料可以满足这些要求。
3.医疗器械和电子领域:铝合金粉末冶金材料具有良好的生物相容性和振动防护性能,可用于制造人类接触材料,如人工关节、牙科植入物等。
除此之外,铝合金粉末冶金技术在计算机行业、建筑业、船舶制造等领域也有广泛的应用。
三、铝合金粉末冶金技术的发展和前景铝合金粉末冶金技术,在其其他领域的应用得到迅速发展和广泛应用的基础上,其研究和应用也逐步升级。
特别是随着高技术和智能化的应用,国内外铝合金粉末冶金技术也进一步提高和发展,成为新材料和科技的重要领域。
在当前的国际环境下,在“新能源、新技术、新材料”的背景下,铝合金粉末冶金技术发展具有广泛而重要的应用前景。
同时,铝合金粉末冶金技术也将成为我国未来工业发展的重要方向。
总之,铝合金粉末冶金技术的研究和应用在现代工业制造中具有重要意义。
随着科技的不断进步,其应用领域也在不断扩展,为我们的生活和经济发展带来更丰富的选择。
纳米粉末冶金制备技术及其在复合材料中的应用研究
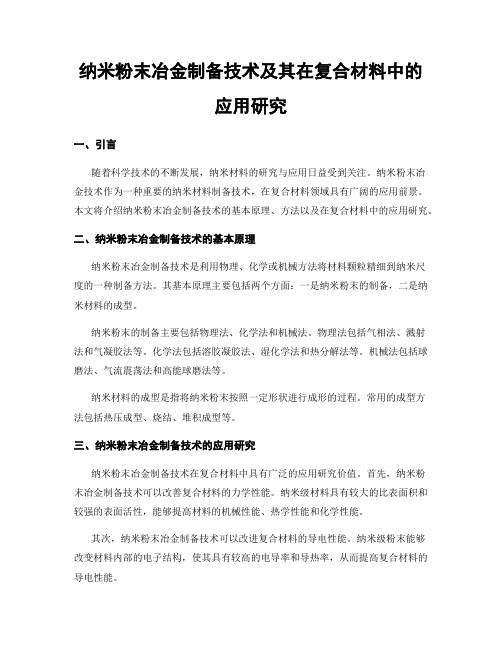
纳米粉末冶金制备技术及其在复合材料中的应用研究一、引言随着科学技术的不断发展,纳米材料的研究与应用日益受到关注。
纳米粉末冶金技术作为一种重要的纳米材料制备技术,在复合材料领域具有广阔的应用前景。
本文将介绍纳米粉末冶金制备技术的基本原理、方法以及在复合材料中的应用研究。
二、纳米粉末冶金制备技术的基本原理纳米粉末冶金制备技术是利用物理、化学或机械方法将材料颗粒精细到纳米尺度的一种制备方法。
其基本原理主要包括两个方面:一是纳米粉末的制备,二是纳米材料的成型。
纳米粉末的制备主要包括物理法、化学法和机械法。
物理法包括气相法、溅射法和气凝胶法等。
化学法包括溶胶凝胶法、湿化学法和热分解法等。
机械法包括球磨法、气流震荡法和高能球磨法等。
纳米材料的成型是指将纳米粉末按照一定形状进行成形的过程。
常用的成型方法包括热压成型、烧结、堆积成型等。
三、纳米粉末冶金制备技术的应用研究纳米粉末冶金制备技术在复合材料中具有广泛的应用研究价值。
首先,纳米粉末冶金制备技术可以改善复合材料的力学性能。
纳米级材料具有较大的比表面积和较强的表面活性,能够提高材料的机械性能、热学性能和化学性能。
其次,纳米粉末冶金制备技术可以改进复合材料的导电性能。
纳米级粉末能够改变材料内部的电子结构,使其具有较高的电导率和导热率,从而提高复合材料的导电性能。
此外,纳米粉末冶金制备技术还可提高复合材料的耐腐蚀性能。
纳米级粉末具有较高的表面能和化学反应活性,可使复合材料形成均匀、致密的氧化层,从而提高材料的耐腐蚀性能。
四、纳米粉末冶金制备技术在复合材料中的应用案例纳米粉末冶金制备技术在复合材料中已经取得了一系列的应用成果。
以纳米陶瓷复合材料为例,通过热压成型技术将纳米陶瓷粉末与金属粉末相结合,可获得高硬度、高抗磨损性能的复合材料。
以纳米金属基复合材料为例,通过球磨法制备纳米级金属粉末,再将其与聚合物基体材料混合,并经过热压成型工艺得到复合材料。
这种纳米金属基复合材料具有良好的导电性能和较高的强度。
《快速凝固-粉末冶金制备块体5083纳米晶铝合金研究》范文

《快速凝固-粉末冶金制备块体5083纳米晶铝合金研究》篇一快速凝固-粉末冶金制备块体5083纳米晶铝合金研究一、引言铝合金作为一种轻质、高强度且耐腐蚀的金属材料,在现代工业和科研领域中得到了广泛的应用。
其中,5083铝合金以其优良的机械性能和加工性能,在航空、汽车、船舶等领域具有重要地位。
然而,传统的铸造方法制备的铝合金往往存在晶粒粗大、力学性能不高等问题。
为了解决这些问题,研究者们开始探索新的制备技术,其中快速凝固/粉末冶金技术因其独特的优势受到了广泛的关注。
本文将重点研究快速凝固/粉末冶金制备块体5083纳米晶铝合金的过程及性能特点。
二、研究内容与方法(一)材料与设备本实验所使用的原材料为5083铝合金粉末,设备主要包括快速凝固设备、粉末冶金设备以及相关的检测设备。
(二)实验方法1. 快速凝固制备纳米晶铝合金粉末:通过快速凝固技术,将5083铝合金粉末在高温下进行熔炼,并迅速冷却,得到纳米晶铝合金粉末。
2. 粉末冶金制备块体:将快速凝固得到的纳米晶铝合金粉末进行压制、烧结等处理,得到块体铝合金材料。
(三)研究内容本实验主要研究快速凝固/粉末冶金制备块体5083纳米晶铝合金的工艺过程及性能特点,包括材料的组织结构、力学性能、耐腐蚀性能等。
三、实验结果与分析(一)组织结构分析通过X射线衍射、扫描电子显微镜等手段对块体5083纳米晶铝合金的组织结构进行分析,发现其晶粒尺寸明显小于传统铸造方法制备的铝合金,具有较高的晶粒密度。
(二)力学性能分析对块体5083纳米晶铝合金进行拉伸、压缩等力学性能测试,发现其具有较高的强度和塑性,与传统铸造方法制备的铝合金相比,具有明显的优势。
(三)耐腐蚀性能分析通过电化学腐蚀等方法对块体5083纳米晶铝合金的耐腐蚀性能进行分析,发现其具有较好的耐腐蚀性能,能够在恶劣的环境中保持良好的性能。
四、讨论与结论(一)讨论快速凝固/粉末冶金技术能够有效地制备出晶粒细小、性能优良的5083纳米晶铝合金。
- 1、下载文档前请自行甄别文档内容的完整性,平台不提供额外的编辑、内容补充、找答案等附加服务。
- 2、"仅部分预览"的文档,不可在线预览部分如存在完整性等问题,可反馈申请退款(可完整预览的文档不适用该条件!)。
- 3、如文档侵犯您的权益,请联系客服反馈,我们会尽快为您处理(人工客服工作时间:9:00-18:30)。
2、MIM工艺特点
2.1MIM工艺与其它加工工艺的对比
粉末冶金新技术
制作人:何志江
-----金属粉末注射成型
(Metal Injection Molding)
主要内容
MIM概述及其发展史 MIM工艺特点
MIM工艺过程 MIM的应用 MIM未来的发展方向
Page 2
1-1、MIM技术概述
什么是粉末注射成型
金属(陶瓷)粉末注射成型技术(Metal Injection Molding,简称MIM技术)是集 塑料成型工艺学、高分子化学、粉末冶金 工艺学和金属材料学等多学科相互渗透与 交叉的产物,利用模具可注射成型坯件并 通过烧结快速制造高密度、高精度、三维 复杂形状的结构零件,能够快速准确的将 设计思想物化为具有一定结构、功能特性 的制品并可直接批量生产出零件,是制造 技术行业一次新的变革。
Page
3
1-1、MIM技术概述
该工艺技术不仅具有常规粉末冶金工艺 工序少、无切削或少切削、经济效益高等 优点,而且克服了传统粉末冶金工艺制品
密度低、材质不均匀、机械性能低、不易 成型薄壁、复杂结构的缺点,特别适合于
大批量生产小型、复杂以及具有特殊要求 的金属零件。
Page
4
1-2、MIM的发展史
Page 8
1-2、MIM发展史
1980年Wiech组建了Witec公司,1982年 Brunswick(布伦瑞克)公司进入MIM行业, 并收购了Witec公司,其后又逐步注册了 Omark工业、Remington军品、Rocky牙科 等子公司。1986年,日。1990年以色列 Metalor2000(美泰乐)公司从Parmatech 公司引进了Wiech工艺技术,建立了MIM生 产线。
Page
14
1-2、MIM发展史
但随着中国工业水平的不断提高和 WTO的加入,国外商品大量涌入中国, 政府对MIM技术的重视 ,以及国内工 程技术人员对MIM技术认知程度的进 一步加深,MIM技术必将在中国得以 迅速发展。 据中国粉末冶金协会预测:1-2年内 我国MIM产品的市场需求量将达8-10 亿元人民币,2015年可望突破20亿元 人民币。
Page 11
1-2、MIM发展史
Marko Maetzig详细分析了欧洲的情 况,欧洲共有120家公司和30家研究机 构从事MIM方面的工作,拥有250台注 射成形机,年消耗1100吨喂料。 欧洲的MIM公司38%来自于传统的陶 瓷行业,27%来自于塑料行业,8%来 自于传统粉末冶金和金属切削加工行 业,5%来自于铸造行业,另有14%为 新成立的公司。
Page 10
1-2、MIM发展史
经过近二十年的发展,2003年全球MIM产 品市场总值达到约10亿美元。 以地域划分,美国占了55%,接下来为欧 洲和日本。目前全世界共有超过500家公司 从事金属注射成形产品的生产和销售工作, 另外还有约40家MIM粉末供应商,20家 MIM喂料供应商。 据统计,全球MIM产业的成形能力已超过 700台注射成形机、500台炉子、300台混 炼机。
Page 13
1-2、MIM发展史
国内状况 中国MIM技术的发展只有二十年左右的时间,技 术的研究始于八十年代末,从事研究开发的单位 不足10家,虽然粘结剂各有不同,但都取得了可 喜的成果,有的已经达到国际先进水平,但在 MIM技术的应用及产业化方面与国外相比存在一 定的差距。原因有以下几个方面: (1)中国1956年才开始粉末冶金的发展,基础 实力薄弱。 (2)机械制造业与发达国家相比落后,工程技术 人员的开发能力不足。 (3)国内技术人员对MIM技术的认识程度不够, 制约了MIM技术的推广
Page 6
1-2、MIM发展史
过去由于缺少合适的粉末及原料价 格太高、知识平台不完善、技术不 成熟、人们了解和市场接受时间不 长、生产(包括模具制造)周期太 长、投资不够等原因,其发展和应 用较为缓慢。
Page 7
1-2、MIM发展史
为解决MIM技术的难点,促进MIM技 术实用化, 80年 代中期美国制 定了一个高 级粉末工计 。 划,研究内 容涵括了与 注射成形有关 的18个课题。 随后日本、德国等也积极开展MIM的 开发研究。
70年代末 80年
代中 期
90年代
Page 5
1-2、MIM发展史
金属注射成形最早可溯源于20世纪20年代 开始的陶瓷火花塞的粉末注射成形制备,随后 的几十年间粉末注射成 形主要集中于陶瓷 注射成形。直到 1979年,由 Wiech等人组建 Parmatech 公司的金属注射成 形产品获得两项 大奖,以及当时Wiech 和Rivers先后获 得专利,粉末注射成形才开始转向以金属注射 成形为主导。
Page 9
1-2、MIM发展史
随着MIM研究的 不断深入以及新型 粘结剂的开发、制粉技术和脱脂工艺 的不断进步, 到90年代初已实 现产业化。 经过20多年 的努力,目 前MIM 已成为 国际粉末冶金 领域发展迅速、 最有前途的一种新型近净成形技术, 被誉 为“国际最热门的金属零部件 成形技术”之一。
.
Page 15
2、MIM工艺特点
粉末注射成型的优点:
能像生产塑料制品一样,一次成形生产形 状复杂的金属、陶瓷等零件部件产品成本 低、光洁度好、精度高(±0.3%~±0.1 %),一般无需后续加工. 产品强度,硬度,延伸率等力学性能高,
耐磨性好,耐疲劳,组织均匀原材料利用 率高,生产自动化程度高,工序简单,可 连续大批量生产无污染,生产过程为清洁 工艺生产
Page 12
1-2、MIM发展史
日本现在共有20~30家MIM公司,日本近 几年MIM市场呈现稳定上升趋势。虽然 2001年较2000年有所下降,但总体而言, 其销售总额呈稳定增长趋势。 据粉末冶金协会粗略统计和预测,全球 MIM产品的销售量正在以每年30%~40% 的速度递增,截止2000年,全球的年平均 销售额为10亿美元,预计到2012年平均年 销售量将超过24亿美元。