聚合物合成工艺-第四章
第四章:自由基聚合方法

→ 2SO4·
B. 水溶性氧化 —还原引发剂
例 过硫酸盐 - 亚硫酸盐
_ 2 S2O8
+ SO3
_ 2
→
_ 2 SO4
+
SO4· +
_ ·SO3
过氧化氢 - 亚铁盐 H2O2 +Fe2+ → OH + HO· + Fe3+
_
(3)乳化剂
乳化剂在乳液聚合中的作用:
a. 降低体系的表面张力使单体形成细小液滴; b. 形成胶束,增溶单体
产物特点与用途 纺丝液 配制纺丝液 制备聚乙烯醇、 维纶的原料
丙烯腈 氧-还体系 醋酸乙烯酯 丙烯酸酯类 丁二烯 AIBN BPO 配位催化剂 BuLi BF3
涂料、粘合剂
顺丁橡胶 低顺式聚丁二烯
异丁烯
异丁烷
阳离子聚合
粘合剂、密封剂
聚醋酸乙烯酯(PVAc)和聚乙烯醇(PVA)
醋酸乙烯酯,甲醇(乙醇)溶液,BPO;65‐70 ℃,溶剂回 流带走聚合热;利用向溶剂的链转移控制分子 量,单体浓度
9
体积收缩:100%聚合时的体积收缩 1 1 ΔVmax w 0 ( ) dm dp
60oC: dm=0.89g/mL; dp=1.18g/ml, ∆Vmax =27mL,V0 =w/dm =112mL
体积收缩百分数= 27/112 =24%
20oC: dm=0.94g/mL; dp=1.208g/mL,∆Vmax =25.7mL 体积收缩百分数=25.7/102=25.2%
不足 反应热难导出、易局部过热、自动加速严重。 措施 降低反应温度,分段聚合,强化传热
8
3、应用实例 有机玻璃:PMMA
聚合实施方法

聚合实施方法第四章聚合实施方法4.1.本体聚合一.定义:不加其它介质,只有单体本身在印发剂、光、热辐射的作用下进行的聚合。
二.配方组成:单体+引发剂(或用光、热辐射引发)+(助剂,如少量颜料、增塑剂、润滑剂、分子量调节剂)三.分类:1.根据单体和聚合体的互溶情况分为均相和非均相两种。
均相本体聚合,是指聚合物溶于单体,在聚合过程中物料逐渐变稠,始终成为均一相态,最后变成硬块。
St、MMA的本体聚合就属均相本体聚合。
非均相本体聚合是单体聚合后新生成的聚合物不溶于单体中,从而沉淀下来成为异相,即非均相氯乙烯的本体聚合。
2.按参加反应的单体的相态分为气相和液相两种。
气相本体聚合最为成熟的是高压聚乙烯的生产。
典型的液相本体聚合有St、MMA 的本体聚合。
四.优缺点1.优点:生产流程短、设备少,易于连续化、生产能力大、产品纯度高、透明性好,此法适用于生产板材或其它型材。
2.缺点:①反应热大,不易排出,危险性大②由于反应体系粘度大,分子扩散困难,所以形成的聚合物分子量分布变宽。
五.聚合机理:遵循自由基聚合一般机理,提高反应速率时,往往分子量降低。
六.意义理论上:由于其组成简单、影响因素少,特别适用于实验室研究。
如:a.单体聚合能力的初步鉴定b.动力学研究c.竞聚率测定d.少量聚合物的试制实际生产上:许多单体均可采用本体聚合方法,不论是气体、液体或固体。
七.生产工艺特征关键是反应热的排出,△H=55~95KJ∕mol20%以下,体系粘度小,散热无困难30%以上,粘度大,散热不易,加上凝胶效应,放热更高,如果散热不良,轻者,造成局部过热,分子量分布变宽,影响产品质量;重者,温度失调,引起短聚,为解决此问题,在工艺和设备的设计上采取了多种措施:〈1〉使反应进行到一定转化率就分离出聚合物。
〈2〉采用较低的反应温度、较低浓度的引发剂进行聚合。
〈3〉将聚合分布进行,控制转化率“自动加速效应”,使放热均匀。
〈4〉强化聚合设备的传热。
聚合物合成工艺第四章
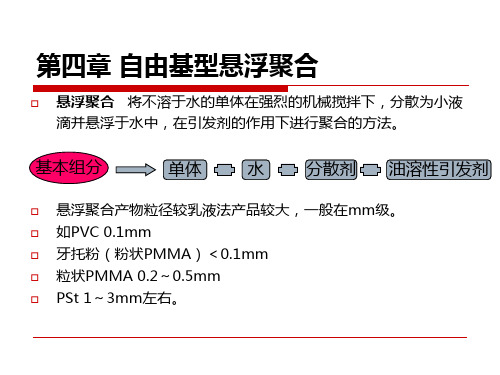
主要质量指标
a.pH值 6~8 b.外观 无肉眼可见悬浮物 c.硬度 ≤5(或Ca2+、Mg2+等离子含量达标)
4.3.2.2分散剂及其种类
B.无机粉末
非水溶性超细无机粉末
MgCO3 CaCO3 BaCO3 滑石粉
Ca3(PO4)2 SiO2
分散作用机理 吸附在液滴的表面形成隔离层,起到分
散的作用。 在一定范围内,粒径越细,颗粒越规整,粒径越均匀,
其分散效果越好。 可将两种无机物同时加入反应体系中,现场合成沉淀物
以获得高分散性的无机粉末。 热稳定性好,可在150℃以上的温度下使用,且可以被酸
第四章 自由基型悬浮聚合
悬浮聚合 将不溶于水的单体在强烈的机械搅拌下,分散为小液 滴并悬浮于水中,在引发剂的作用下进行聚合的方法。
基本组分
单体
水
分散剂 油溶性引发剂
悬浮聚合产物粒径较乳液法产品较大,一般在mm级。 如PVC 0.1mm 牙托粉(粉状PMMA)<0.1mm 粒状PMMA 0.2~0.5mm PSt 1~3mm左右。
A.水溶性聚合物
合成聚合物 半合成聚合物 天然聚合物(已较少采用)
半合成聚合物
主要为纤维素的醚类改性物 甲基纤维素(MC) 羟乙基纤维素(HEC) 羟丙基纤维素(HPC) 乙基羟乙基纤维素(EHEC)
4.3.2.2分散剂及其种类
合成聚合物
①PVA 主要的规格有1788(DP1700~2000,醇解度
4.1.3悬浮聚合的优缺点
缺点
难以实现连续化生产:聚合过程中分散问题在连续聚合中较难
聚合物合成工艺
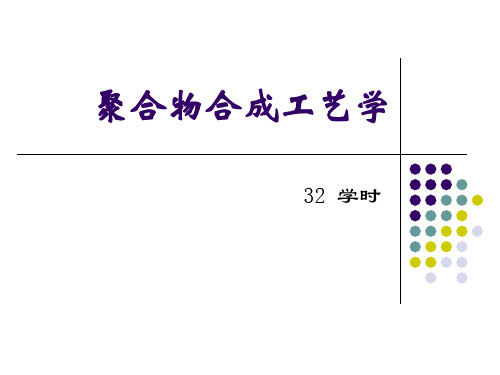
植物、农副产品 糠醛、纤维素脂、纤维素醚等。
2.2.3 中国资源情况展望
煤炭资源丰富 石化基地:大型乙烯装置
第3章 自由基聚合生产工艺
本体聚合 乳液聚合 悬浮聚合 溶液聚合
3.1 自由基聚合工艺基础和本体聚合生产工艺
3.1.1 自由基聚合工艺基础
自由基聚合引发剂
1.特点:产品不能精制提纯,因此,对聚合反应工艺条件和设备 要求很严格;同一套装置要求生产不同牌号的产品。
2.聚合实施方法 自由基聚合:本体、乳液、悬浮、溶液 离子与配位聚合:本体、溶液
3.聚合反应的操作方式 间歇聚合:分批生产,适于小批量生产; 连续聚合:自动化程度高,质量稳定,适合大批量生产。
4.聚合反应器 管式、塔式、釜式、特殊形式 反应热排除方式:夹套冷却、内冷管冷却、反应物料部分闪蒸、反 应介质预冷、回流冷凝器冷却等。 搅拌器形式:平桨式、旋桨式、涡轮式、锚式、螺带式
1.3.5 聚合物后处理过程
后处理过程主要是脱除水分和有机溶剂的干燥过程。 1 合成树脂:采用气流干燥、沸腾干燥;干燥后得到的粉
状树脂,一般要添加稳定剂、润滑剂等添加剂,经混 炼、造粒制得粒状料(PVC除外)。 2 合成橡胶:采用箱式干燥机、挤压膨胀干燥机干燥。干 燥后进入压块机压制成25kg大块。
3.3.2 聚合工艺
常用釜式反应器、半连续操作。
3.3.3 后处理
聚合物溶液:脱除单体,浓缩或稀释至要求的固含量。 固体聚合物:真空蒸发脱单体、有机溶剂; 水溶液:干燥机脱水。
▲3.4 乳液聚合生产工艺
▲应用:合成树脂如PVC、聚醋酸乙烯、聚丙烯酸酯等; 合成橡胶如SBR、NBR、CR。
▲特点: 优点:聚合反应热清除较容易; 反应体系粘度低; 分散体系的稳定性优良,可连续操作; 产品乳液可直接用作涂料、粘合剂、表面处理剂。 缺点:分离过程较复杂,产生大量废水,直接干燥能耗大; 聚合物杂质含量较高。
聚合物合成工艺学每章节后面的思考题

第一章课后思考题(聚合物合成工艺学)1.简述高分子化合物的生产过程?答:(1)原料准备与精制过程:包括单体、溶剂、去离子水等原料的贮存、洗涤、精制、干燥、调整浓度等过程相设备。
(2)催化剂(引发剂)配制过程:包括聚合用催化剂、引发剂和助剂的制造、溶解、贮存、调整浓度等过程与设备。
(3)聚合反应过程:包括聚合和以聚合釜为中心的有关热交换设备及反应物料输送过程与设备。
(4)分离过程:包括未反应单体的回收、脱除溶剂、催化剂,脱除低聚物等过程与设备。
(5)聚合物后处理过程:包括聚合物的输送、干燥、造粒、均匀化、贮存、包装等过程与设备。
(6)回收过程:主要是未反应单体和溶剂的回收与精制过程及设备。
此外三废处理和公用工程如供电、供气、供水等设备。
2.比较连续生产和间歇生产工艺特点?答:连续生产:优点:聚合反应条件稳定,容易实现操作过程中的自动化;若条件一致,则产品质量规格稳定;设备密闭,减少污染;适合大规模生产;劳动生产率高,成本较低。
缺点:不便于小批量生产某牌号产品。
间歇生产:优点:反应条件以控制;物料在聚合反应器内停留时间相同;便于改变工艺条件。
缺点:不易实现操作过程的全部自动化;必须按配方规定的顺序进行;不适合大规模生产,生产能力低。
3.合成橡胶和合成树脂在生产过程中的那两个过程?试比较他们在这两个生产过程上的主要差别是什么?答:主要差别是分离过程和聚合物后处理过程;分离过程:合成橡胶:不能用第二种溶剂以分离合成橡胶,其分离方法是将高粘度橡胶溶液喷入沸腾的水中,同时进行强烈搅拌,未反应的单体和溶剂与一部分水蒸气被蒸出,合成橡胶则以直径10~20mm左右的胶粒析出,且悬浮于水中,经过滤洗涤得到胶粒;合成树脂:将合成树脂溶液逐渐加入第二种非溶剂中,而此溶剂是可以与原来的容剂混溶的,再沉淀釜中搅拌则合成树脂呈粉末状固体析出,如果通过细孔进入沉淀用溶剂中,则生成纤维状产品。
后处理过程:合成橡胶:采用箱式干燥机活挤压膨胀干燥机进行干燥;合成树脂:用加热的空气作为载热体进行气流干燥,含有机溶剂时,用加热的氮气进行干燥。
聚合物合成工艺习题集

聚合物合成工艺习题集“聚合物合成原理及工艺学”习题集第一章绪论1.试述高分子合成工艺学的主要任务。
2.简述高分子材料的主要类型,主要品种以及发展方向。
3.用方块图表示高分子合成材料的生产过程,说明每一步骤的主要特点及意义。
4.如何评价生产工艺合理及先进性。
5.开发新产品或新工艺的步骤和需注意的问题有哪些?第二章生产单体的原料路线1.简述高分子合成材料的基本原料(即三烯、三苯、乙炔)的来源。
2.简述石油裂解制烯烃的工艺过程。
3.如何由石油原料制得芳烃?并写出其中的主要化学反应及工艺过程。
4.画出C4馏分中制取丁二烯的流程简图,并说明采用两次萃取精馏及简单精馏的目的。
5.简述从三烯(乙烯、丙烯、丁二烯)、三苯(苯、甲苯、二甲苯),乙炔出发制备高分子材料的主要单体合成路线(可用方程式或图表表示,并注明基本工艺条件)。
6.如何由煤炭路线及石油化工路线生产氯乙烯单体?7.简述苯乙烯的生产方法。
8.乙烯氯氧化法生产氯乙烯所采用的一步法、二步法及三步法三种方法之主要差别是什么?9.试述合成高分子材料所用单体的主要性能,在贮存、运输过程中以及在使用时应注意哪些问题?10.论述乙烯产量与高分子合成工艺的关系。
第三章自游基本体聚合生产工艺1.自由基聚合过程中反应速度和聚合物分子量与哪些因素有关?工艺过程中如何调节?2.自由基聚合所用引发剂有哪些类型,它们各有什么特点?3.引发剂的分解速率与哪些因素有关?引发剂的半衰期的含义是什么?生产中有何作用?4.引发剂的选择主要根据哪些因素考虑?为什么?5.举例说明在自由基聚合过程中,调节剂,阻聚剂,缓聚剂的作用。
6.为什么溶剂分子的Cs值比调节剂分子的Cs小的多,而对聚合物分子量的影响往往比调节剂大的多?7.以苯乙烯的本体聚合为例,说明本体聚合的特点。
8.根据合成高压聚乙烯的工艺条件和工艺过程特点,组织高压聚乙烯的生产工艺流程,并划出流程示意图。
9. 高压聚乙烯分子结构特点是怎样形成的,对聚合物的加工及性能有何影响。
第四章 自由基悬浮聚合原理及生产工艺课件

高聚物合成工艺 2
(1)均相悬浮聚合 如果聚合物溶于其单体中,则聚合物是透明的小珠,
该种悬浮聚合称为均相悬浮聚合或称珠状聚合。如苯乙
烯的悬浮聚合和甲基丙烯酸甲酯的悬浮聚合等为均相悬
浮聚合。
(2)非均相悬浮聚合 如果聚合物不溶于其单体中.聚合物将以不透明的小
在高分子合成工业生产中常用提高聚合温度的办法使 剩余单体加速聚合,以达到较高的转化率。 通常,当转化率达到90%以上时立即终止反应,回收未 反应的单体,此时,不能靠延长聚合时间来提高转化率, 如果用延长聚合时间的办法来提高转化率将使设备利用 率降低,这是不经济的。
高聚物合成工艺 15
4.聚合装置 (1)聚合釜的传热
高聚物合成工艺 16
⑤在夹套中安装螺旋导流板,其中通冷却水。冷却水不 走短路,当冷却水流速提高10倍以上时,水对釜的给热 系数则可提高8倍以上。 (2)搅拌
搅拌在悬浮聚合中能影响聚合物粒子形态、大小及粒 度分布。搅拌使单体分散为液滴,搅拌叶片的旋转对液 滴所产生的剪切力的大小,决定了单体液滴的大小。剪 切力越大,所形成的液滴越小。搅拌还可以使釜内各部 分温度均一,物料充分混合,从而保证产品的质量。
氯乙烯聚合热比较大,为了合成某一牌号的树脂必须 严格控制聚合温度,温度波动范围不超过±0.2℃。
导出反应釜中聚合热的方法:将反应釜设计为瘦高型, 提高夹套冷却面积,大型反应釜设有可水冷的挡板,反 应釜上安装回流冷凝装置,为了提高传热效率,工业上 采用经冷冻剂冷却的低温水(9℃~12℃或更低)进行冷却。
悬浮聚合用聚合釜一般是带有夹套和搅拌的立式聚合 釜。夹套能帮助聚合过程中产生的大量的聚合热及时、 有效的传出釜外。近年来,聚合釜向大容积方向发展, 但釜的容积增大,其单位容积的传热面积减小。
聚合物合成工艺

第一章绪论4. 20世纪50年代,谁发现了可用于高密度聚乙烯和立构规整聚丙烯的合成催化剂?这些催化剂的基本成分是什么?5. 21世纪高分子科学与工程学科的重要发展方向是什么?6. 简要说明聚合物合成的生产步骤。
第二章合成聚合物的原料路线4. 石脑油的裂解-催化重整可以获得哪些重要芳烃原材料?其中的加氢工艺是为了除去哪些有害物质?5. 什么是C4馏分?如何通过C4馏分制备1,3-丁二烯?10. 从动、植物体内获得的原料路线有哪些?你认为哪些原料路线具有很好的前景。
第三章自由基本体聚合过程及合成工艺17. 用过氧化二苯甲酰作引发剂,苯乙烯在60℃进行本体聚合,试计算正常引发反应、向引发剂转移反应、向单体转移反应三部分在聚合度倒数中各占多少百分比?对聚合度各有什么影响,计算时选用下列数据:[I]=0.04mol/L,f=0.8,k d=2.0×10-6s-1,k p=176L/mol·s,k t=3.6×107 L/mol·s,ρ(60℃)=0.887g/mL,C I=0.05,C M=0.85×10-4。
18. 为了改进聚氯乙烯的性能,常将氯乙烯(M1)与醋酸乙烯(M2)共聚得到以氯乙烯为主的氯醋共聚物。
已知在60℃下上述共聚体系的r1=1.68, r2=0.23,试具体说明要合成含氯乙烯质量分数为80%的组成均匀的氯醋共聚物应采用何种聚合工艺?第四章自由基溶液聚合过程及合成工艺9. 苯乙烯在60℃以过氧化二叔丁基为引发剂,苯为溶剂进行自由基溶液聚合。
当苯乙烯的浓度为1mol/L,引发剂浓度为0.0lmol/L时,引发剂分解和形成聚合物的初速率分别为4×1011mol/(L·s)和1.5×10-7mol/(L·s)。
试根据计算判断在低转化率下,在上述聚合反应中链终止的主要方式,以及每一个由过氧化物引发的链自由基平均转移几次后失去活性?已知在该温度下C M=8.0×10-5,C I=3.2×10-4,C S=2.3×10-6,苯乙烯的密度为0.887g/mL,苯的密度为0.839g/mL,设苯乙烯体系为理想溶液。
- 1、下载文档前请自行甄别文档内容的完整性,平台不提供额外的编辑、内容补充、找答案等附加服务。
- 2、"仅部分预览"的文档,不可在线预览部分如存在完整性等问题,可反馈申请退款(可完整预览的文档不适用该条件!)。
- 3、如文档侵犯您的权益,请联系客服反馈,我们会尽快为您处理(人工客服工作时间:9:00-18:30)。
合成聚合物 半合成聚合物 天然聚合物(已较少采用)
半合成聚合物
主要为纤维素的醚类改性物 甲基纤维素(MC) 羟乙基纤维素(HEC) 羟丙基纤维素(HPC) 乙基羟乙基纤维素(EHEC)
4.3.2.2分散剂及其种类
合成聚合物
①PVA 主要的规格有1788(DP1700~2000,醇解度
性越高。 反应温度波动<±0.2℃。
除起始阶段物料温度逐渐升高外, 当达到设定的反应温度后就维持一 条近似水平的直线,直到反应结束
曲线b
夹套温度控制曲线-曲线c
反应的温度控制主要依 靠夹套温度的控制来实 现!
夹套温度控制曲线总体 呈现先高后低,反应后 期又逐渐升高的特点
为什么会有这种变化?
B.无机粉末
非水溶性超细无机粉末
MgCO3 CaCO3 BaCO3 滑石粉
Ca3(PO4)2 SiO2
分散作用机理 吸附在液滴的表面形成隔离层,起到分
散的作用。 在一定范围内,粒径越细,颗粒越规整,粒径越均匀,
其分散效果越好。 可将两种无机物同时加入反应体系中,现场合成沉淀物
以获得高分散性的无机粉末。 热稳定性好,可在150℃以上的温度下使用,且可以被酸
能力,以维持反应温度的稳定。
夹套温度控制曲线-曲线c
反应后期反应热减少
当转化率≥80%后,单 体数量明显减少,聚合 反应速度逐渐下降。 这时反应热逐渐减少, 夹套温度开始升高,并 逐渐接近物料反应温度。
4.1.3悬浮聚合的优缺点
缺点
难以实现连续化生产:聚合过程中分散问题在连续聚合中较难
解决。
三废排放量比本体法要高。
产品的纯度比本体法要低。
典型流程
离心
单体
+水
+分散体系 聚合 回收 固液分离 干燥
+引发剂
筛分 产品
4.3悬浮聚合组分及要求
单体相 包括单体和助剂 单体 要求具有一定的纯度,且不溶于水(否则成为溶液聚合),
脱单体
室温下为气态的单体 减压蒸出(闪蒸)
室温下为液态的单体 与水的共沸蒸出(汽提)
单体毒性大的还需进一步进行汽提(在水蒸汽的作用下, 进一步脱除单体、减少残留)。
工艺过程与设备
固液分离
颗粒较大的珠状紧密型树脂 过滤分离
疏松型粉末或颗粒
离心(机)分离。
干燥
珠状颗粒因为含有的只是表面游离水,易于干燥:气流 干燥器
洗净。 制备高透明性树脂时应避免使用(以防少量的分散剂包
裹进树脂内部,影响透明度)。
悬浮聚合中的成珠过程示意图
搅拌
不稳定的 分散状态
搅拌
无机物的分散作用
稳定的分 散状态
粘合 分散
有机物的分散作用
4.3.2.2分散剂及其种类
C.助分散剂
—表面活性剂
降低表面张力,起调整颗粒形态和粒径的作用
用量一般较少,为0.001~0.01%(wt ratio),否则易 产生乳化现象。
水在反应过程中主要起分散介质和传热介质的作用,作为分散介 质,其纯度对反应过程和产品品质有重要影响,主要的是水中含 有的各种离子和机械杂质,使用时需净化,接近“纯水”。
主要质量指标
a.pH值 6~8 b.外观 无肉眼可见悬浮物 c.硬度 ≤5(或Ca2+、Mg2+等离子含量达标)
4.3.2.2分散剂及其种类
图9-31,张慰盛版)。
4.6.3 PVC的悬浮聚合生产工艺
主要原材料
单体-VC 纯度99.98%以上 去离子水 pH5~8.5 分散剂 分为主、辅分散剂 主分散剂 控制颗粒的大小,即粒径,主要采用
PVA或纤维素的醚类(HEC、HEPC等) 辅助分散剂 是用来调整或控制产物的孔隙率(吸
反应结束的物料应进行“单体剥离”操作或称之为 “汽提”。
方法是自反应釜送入将物料附有搅拌装置的贮槽中初 步脱除单体;然后送入单体剥离塔(又称汽提塔,图938),用直接蒸汽吹除残留单体。
汽
提
塔
结
构
示
意
筛板塔
图
“鱼眼”的控制
“鱼眼” 主要是在水相中聚合而成的聚合物。 因其表面无分散剂和乳化剂,故颗粒密实,内部孔
隙率低,不易塑化,在加工制品中呈现为“白点”。 防止“鱼眼”形成的办法就是在水相中减少VC 的存
在和防止它的聚合。具体的方法有:
A.改进配方 B.加水相阻聚剂(如Goodrich公司的NaBH4-硼氢
化钠等)
C.选择新型链转移剂并保持器壁的清洁,减少物料
黏釜的发生。
防粘釜技术*
反应过程中,聚合物由于物理和化学原因附着于釜壁或搅拌器 上,先形成薄层覆盖物,然后变成沙粒状沉积物,逐渐脱落进 入水中,形成鱼眼。 粘釜物影响传热和控制,进而影响生产和产品质量。
分散剂以及除引发剂以外的各种助剂,经计量后加入聚 合釜中,然后加入计量的氯乙烯单体。升温到规定的温 度,加入引发剂,聚合反应随即开始。根据所生产的牌 号不同,控制不同的反应温度。 由于VC聚合时对温度比较敏感(温度影响链转移和孔隙 率),反应温度控制严格。一般控制反应温度的波动不 超过±0.2℃。
间提高的幅度偏小 故这时应予以终止(加阻聚剂或降温皆可)。
4.5工艺过程与设备
聚合设备
多为反应釜 提高产量的主要措施是提高反应器的容积 装置大型化带来的问题 单位体积的传热面积减小,传热问题 以VC悬浮聚合用14m3反应釜的单位体积传热面积为
1.93m2/m3 ,35m3反应釜的单位体积传热面积减少为 1.41m2/m3,减少了27%,明显减少 因此,必需采取一些措施。
4.4悬浮聚合的工艺控制
4.4.1单体纯度(略)
4.4.2水油比(液固比)
水油比大 传热好,反应易控制,设备利用率低 水油比小 易出现放热集中现象,设备利用程度提高,反应
难以控制。 通常的配比 1~2.5:1 VC悬浮聚合 1.5~2.5:1 St低温聚合 1.4~1.6:1 St高温聚合 2.8~3:1
防黏釜剂 苯胺、蒽醌类染料的混合溶液。
4.6.3.2配方
生产中的配方很多,大体如下 水:VC =1.1:1~1.4;
引发剂:VC=0. 04~0.05:1; 分散剂:水=0.05~0.30:1。 书中(P47)表4-1也给出了大致的配方
生产流程与流程图
(流程图见P48,图4-1) PVC的悬浮法生产流程比较简单。首先,将去离子水、
第四章 自由基型悬浮聚合
悬浮聚合 将不溶于水的单体在强烈的机械搅拌下,分散为小液 滴并悬浮于水中,在引发剂的作用下进行聚合的方法。
基本组分
单体
水
分散剂 油溶性引发剂
悬浮聚合产物粒径较乳液法产品较大,一般在mm级。 如PVC 0.1mm 牙托粉(粉状PMMA)<0.1mm 粒状PMMA 0.2~0.5mm PSt 1~3mm左右。
4.4悬浮聚合的工艺控制
4.4.3聚合温度
对下列参数等有重要影响
反应速率 产物分子量 产物的微观结构 反应过程 分散剂的分散效果
聚合温度是反应控制的重要因素,必需严格控制。
4.4悬浮聚合的工艺控制
4.4.4聚合时间 一般控制在单体转化率为90%左右,以此作为反应时
间控制的主要决定因素。因为: 转化率超过90%以后,反应的速率明显下降 继续延长反应时间来提高转化率,相对来说,单位时
防粘釜方法 提高反应釜器壁的表面光洁度(如釜内壁、温度计套、挡板等
处)
水相阻聚剂 喷涂防黏釜剂涂层 用热水加热代替蒸汽加热
PVC悬浮聚合工艺自动控制曲线与分析
1)PVC 悬浮聚合 控制曲线
压力曲线-曲线a
投料后进行升温,釜内温度升 高,导致VC单体的压力上升
达设定温度后,温度要求恒定,强化传热与传质的措施反应釜内部增加带夹套的折流挡板,以尽可能增
加传热面积
改进搅拌器的结构,增加釜内的扰动,改进传热
效果
调节气体的蒸发速度 借助物料的体外循环带出
部分热量
强化反应釜夹套的传热效果 如在夹套内增设
喷嘴、扰流挡板等扰流结构
工艺过程与设备
4.5.3后处理
主要为脱单体+(汽提)+固液分离+干燥
油率),其成分为乳化剂,如脱水山梨醇单月桂酸 酯。
主要原材料(续)
引发剂
主要为偶氮类或过氧类,根据牌号和厂家不同,品种区
别较大。
AIVN
LPO
常用引发剂
IPP
终止剂 自由基捕捉剂,如双酚A、叔丁基邻苯二酚、丙
酮缩胺基硫脲(ATSC)。
链转移剂 硫醇类,如巯基乙醇
抗鱼眼剂 苯甲醚的叔丁基、羟基衍生物
悬浮聚合是聚合物生产中的重要方法之一。 主要的悬浮法产品 PVC PSt PMMA PTFE 大量的接枝改性聚合物
4.1.3悬浮聚合的优缺点
优点
总体上与乳液法相近。 工艺流程较短,设备要求相对简单。 反应过程较易控制:反应体系中含有大量的水作为介质,
体系的黏度较低,反应产生的热量易于除去。 树脂的纯度比乳液法高。 三废排放量比乳液法低。
釜内压力相对恒定(~1MPa)
反应后期(单体转化率≥70%), 游离液态单体量急剧减少,反
应釜内的压力开始下降
当游离液态单体消失时,压力 明显下降(~0.6MPa)。
曲线a
反应温度控制曲线-曲线b
产品聚合度与反应温度密切相关 不同反应温度下,链转移反应程度
不同,产品的聚合度不同。 温度是PVC生产中工艺控制的关键 反应温度波动越小,产品质量稳定
以便反应热通过夹套排出。
夹套温度控制曲线-曲线c
自动加速阶段 PVC树脂不溶于单体
聚自 反
VC,但可吸收单体达27%(质量),形 升 合 动 应
成粘性凝胶,然后聚合反应在凝胶内