钢的显微组织评定
渗碳淬火组织评级

生产过程中酸洗法进行磨削烧伤的控制,当出现争议时可再用金相组织 法进行最终的判断
30g/L的硝酸水溶液
酸洗法介绍
溶液配比: 配好三种溶液 1、30g/L 的硝酸水溶液 2、50g/L 的盐酸酒精溶液 3、 50g/L 的氢氧化钠水溶液
酸洗法介绍
• 在酸洗前一定要用酒精或洗洁精去处零件表面的 油污和脏物,并用清水冲洗,确保零件表面非常
干净,这个清洗步骤非常重要,零件表面清洗不 干净会引起误判。
• 根据清水冲洗
水溶液
干净
50g/L 的盐酸 25秒 清水冲洗
酒精溶液
干净
吹干
清水冲洗 30秒 50g/L 的氢氧
况确定;常啮合齿轮1-5级,换档齿轮1-4级。
碳化物评级图
钢件渗碳金相检验
抛光态下的内氧化
腐蚀态下的内氧化
钢件渗碳金相检验
• 非马氏体组织:渗碳淬火件表面层中经常出现连续或不连续的 网状或块状黑色组织,主要由于内氧化而贫合金化元素导致形 成屈氏体类组织,一般规定不超过0.02mm.
• 减少非马氏体组织的措施: • 1)尽可能用低碳烃和高纯度气体做制备渗碳气体的原料气; • 2)尽可能选用含Cr、Ti、V、B元素的钢; • 3)从工艺和设备上采取措施,保证炉气不受空气污染; • 4)尽可能采用快速的淬火冷却介质和冷却方式。
钢件渗碳金相检验
钢件渗碳金相检验
钢件渗碳金相检验
• 适用于渗碳淬硬层有效深度大于0.3mm的汽车齿轮。 • 放大倍数:400X • 检验部位: 同芯部硬度 • 铁素体:1-3级
ASTM E1268 评定显微组织带状物等级或取向的标准实施规范

本标准是以固定代号 E 1268 发布的。其后的数字表示原文本正式通过的年号;在有修订的情况下,为 最后一次修订的年号;圆括号中的数字为最后一次重新确认的年号。上标符号(ε)表示与上次修改或重新 确定的版本有编辑上的变化。
绪论 在金属和合金的树枝晶凝固过程中会发生偏析, 偏析通过后续的变形重新排列。 固态转 变受微观偏析模式的影响, 微观偏析模式导致了分层或带状显微组织的形成。 最常见的呈带 状分布的例子是锻轧后的低碳和低碳合金钢中层状分布的铁素体-珠光体组织,另一些带状 物的例子包括过共析工具钢中的带状碳化物以及热处理合金钢中的带状马氏体。 本标准包括 了叙述带状组织形态、 表征带状物级别的方法以及用来判别热处理样品中带状物之间硬度差 异的显微硬度试验方法。 体视学测量法也可以用来表征非带状但存在第二相粒子的显微组织 沿变形方向的不同级别的取向(伸长)。
度计特别适合于这类测试。
7. 取样和试样 7.1 一般说来,应在最终产品上取样,取样应在所有生产步骤完成之后进行,尤
其是那些会影响带状物特征和级别的生产步骤。 因为带状物等级或取向在产品横 截面内会有所不同,所以检验面应取整个横截面。如果截面尺寸太大以致于不能 取到完整的横截面,那么应在标准规定位置取样,比如表面下、中部(四分之一 处)以及中心处,或者在制造方-购买方协商规定的特定位置。
s =标准偏差(σ)。 t =测定 95%置信区间时测量的视场数与标准偏差的乘积。 95%CI = 95%置信区间。 95%CI = ± ts n
%RA = 相对精度百分数,%。
% RA = 95%CI × 100 X
SB⊥=带状物中心到中心的平均距离。 SB⊥ = 1 N L⊥
SEP1520-1998___钢中碳化物图谱显微检验法.pdf

SEP1520-1998 钢中碳化物图谱系列显微检验法1.检验目的和适用范围1.1根据出现的碳化物特征,采用显微检验的方法对钢(组织)加以评价是适宜的。
本标准为该方法的说明,本标准中附有碳化物的组成和分级图谱系列。
此图谱系列用于所规定的钢及其组织状态。
它是考虑到碳化物形状、结构、尺寸和数量而制定的。
试验是在金相磨片上进行的。
通过在显微镜下观察,与碳化物图谱系列进行比较,检验碳化物状况。
1.2本标准适用于含碳量约为0.1~1.2%,合金元素总含量为5%的钢,通常只用于特殊钢。
本标准不适用于下述的碳化物检验:低碳钢(例如深拉延的钢材)高速工具钢(见钢铁试验标准SEP1615和其他莱氏体钢)1.3仅按协议检验钢和碳化物,并在供货条件中规定全部检验条件(符合本标准规定条件)。
当试验条件未经协议,可采用适当的试验部位进行试验。
1.4根据钢的再加工和使用状况,而确定碳化物的合格界限,不属于标准范围内的规定。
2.试验范围:只要符合质量标准的规定(DIN-标准,钢铁试验标准)本试验范围具有权威性。
若质量标准没有规定则检验批和取样数量,按以下推荐执行:由同一热处理炉次和同一尺寸组成的每炉批取2个试样。
连续炉热处理时(同一冶炼炉号),每5吨盘条或每10吨同一断面的棒材,取1个试样,但每批最少取2个试样。
此外,允许断面相近的钢材,组成一个检验批。
3.取样和试样制备:3.1若无另外协议,取样和试验用金相磨面面积,按下述规定3.1.1取样时,对交货检验用试样应加以标记。
3.1.2检验碳化物特征,除系列6和7碳化物带状检验为纵向磨面外,其它金相试样磨面取样部位为纵向或横向。
只要有可能且有益,每个金相试样磨面面积应为100mm2(标准面积F)。
横向或纵向试样磨面位置,根据不同要求而确定。
图1为圆钢取样位置。
当有待检验的碳化物特征类型,要求一定方向、位置上取样和检验试样面积与标准试样面积不同时,在这种情况下,其具体规定协商确定。
链条原材料及热处理加工的检验和评定标准
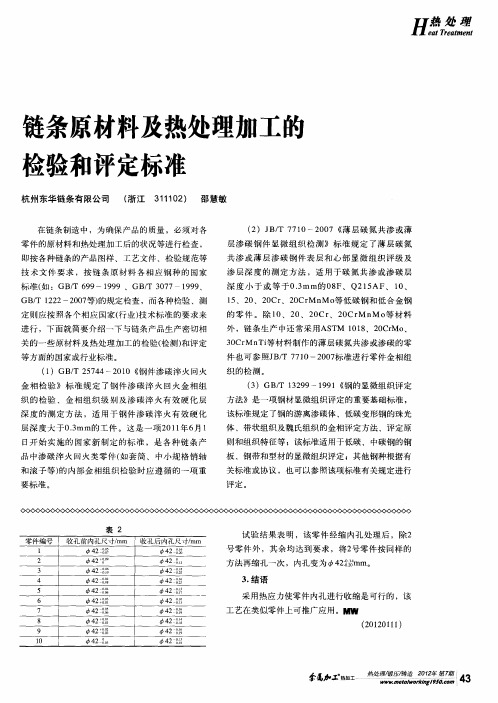
缺陷。根据 供需双方协议 ,也可用作评定其他钢类
低倍 组 织 的缺 陷 。
耐磨性能和整链抗拉强度等性能,通常链条原材料
检验规范 中都对表面脱碳 层规定了深度的要求 ,而 如何测定脱碳层深度则需遵照G / 2 —2 0 标准 BT2 4 0 8
标准适用于渗碳和碳氮共渗淬火硬化 层;并经最终 热处理 后 ,距表面3 于淬火硬化 层深度处硬度值 倍
小于 4 0 V的零 件 。不 能 满足 上 述 条件 的 钢 件 ,应 5H
T 5 7 —2 0 低、 中碳钢球化体评级》 、J / 0 4 0 7 BT 9 1 —2 0 中碳钢与 中碳 合金结构钢马 氏体等 21 08
链条原材料及热处理加工的
检验和评定标准
杭 州东华链 条有限公 司 ( 江 浙 3 1 0 ) 邵 慧敏 1 1 2
在 链 条制 造 中 ,为 确保 产 品的 质 量 ,必须 对 各 零 件 的原 材 料 和 热处 理 加 工 后 的状 况 等 进 行检 查 , 即 按 各种 链 条 的 产 品 图样 、工 艺 文件 、检 验规 范等 技 术 文 件 要 求 ,按 链 条 原 材 料 各 相 应 钢 种 的 国家 标 准 ( :G / 9 —19 、GBT 3 7 —19 、 如 BT69 99 / 0 7 9 9
( )J / 7 0 0 7 薄层碳氮 共渗或薄 2 B T 7 1 —2 0
层 渗 碳 钢 件 显 微 组 织 检 测 ) 准 规 定 了薄 层 碳 氮 )标
共渗或薄 层渗碳 钢件表 层和心部 显微组织 评级及
渗 层 深 度 的 测 定 方 法 ,适 用 于 碳 氮 共 渗 或 渗 碳 层 深 度 小 于 或 等 于 03 .mm的 0 F Q 1 AF 1 、 8 、 2 5 、 0
钢的显微组织评定方法课件

在失效分析中的应用
失效原因分析 通过对失效材料的显微组织进行观察和分析,了解材料的 微观结构和性能变化,找出失效原因,为预防措施提供依 据。
失效模式识别 通过显微组织观察,识别材料的失效模式,如韧性断裂、 脆性断裂、疲劳断裂等,有助于采取相应的改进措施。
失效预防措施 根据显微组织评定的结果,制定针对性的失效预防措施, 如改进工艺参数、调整材料成分、加强产品检测等,提高 产品的可靠性和使用寿命。
渗碳体具有较好的耐腐蚀性,而铁素 体和奥氏体则相对较差。
02
显微组织评定方法
金相显微镜观察法
总结词
金相显微镜观察法是一种常用的显微组织评定方法,通过光 学显微镜观察金属材料的显微组织,分析其结构、形态和分布。
详细描述
金相显微镜观察法利用光学显微镜的高倍率放大能力,观察 金属材料的显微组织,包括晶粒大小、形态、相组成等。通 过对不同区域的组织观察和比较,可以对材料的性能和工艺 条件进行分析和评估。
钢的显微组织评定 方法课件
目 录
• 钢的显微组织基础 • 显微组织评定方法 • 钢的显微组织评定标准 • 钢的显微组织评定实践 • 钢的显微组织评定应用 • 钢的显微组织评定展望
contents
01
钢的显微组织基础
钢的显微组织组成
01
02
03
04
铁素体
一种常见的显微组织,具有较 低的强度和韧性,但良好的塑
04
钢的显微组织评定实践
钢材显微组织的制备
切割钢材样品
使用金相切割机将钢材切割成 适合观察的尺寸,确保样品表
面平整、无划痕。
磨平样品
将切割好的样品进行粗磨和细 磨,去除表面的杂质品
使用抛光机对样品进行抛光, 使表面更加光滑,减少观察时 的干扰。
H13模具钢金相组织分析

热作模具钢H13的显微组织金相分析摘要:按照北美压铸协会提出的优质压铸模H13钢验收标准NADCA# 207-90和H11、H13及改良型钢的显微成分偏析验收参考图谱对H13某国产钢进行显微组织分析,并对其真空淬火显微组织进行研究。
关键词:热作模具钢;热处理;显微组织1前言H13钢在淬硬条件下具有较高韧度,并具有优良的抗热裂能力,是一种强韧兼有的空冷硬化型热作模具用钢。
它适用于制造压铸模、挤压模、热切边模、热锻模的热冲孔模具等。
H13钢在我国为4Cr5MoSiV1钢。
德国的DIN1.2344,瑞典的SS142242,法国的AFNORZ40COV5和日本的JISSKD61与之相类似。
众所周知,影响模具寿命的最重要因素是热作模具钢的质量。
现在,描述热作模具钢的质量主要通过显微组织分析。
评定显微组织的标准广泛采用北美压铸协会模具材料委员会编的《压力铸造模具用高级H13钢的验收标准》NADCA#207-90。
新近研究的显微带状组织验收参考图谱更能说明钢材力学性能和模具寿命的关系。
因而,它们是对材料进行金相评级的重要依据。
本文从这两方面着手对一种国产H13钢进行显微组织分析,并对这种材料的真空淬火显微组织作研究。
2按NADCA的分析按照NADCA#207-90标准,一般试样都在退火态下进行推测。
2.1 材料化学成分:国产H13钢的化学成分分析结果列于表1。
表中还列入ASTMA681(最新修订版)中H13钢和NADCA#207-90中高级H13钢的化学成分,表中列入的4Cr5MoSiV1钢为GB/T1299-2000《合金工具钢》中规定的相当于H13钢的成分。
降低钢中含硫量对提高H13钢的纯净度,从而改善其性能具有重要意义。
文献[3]介绍,硫的质量分数<0.014%时可以大大提高钢件的断裂韧度KIC值。
国外电渣重熔优质H13钢的含硫质量分数控制在0.005%~0.008%范围。
在此,国产电渣重熔钢H13R尚有待提高。
热处理检验方法国家标准
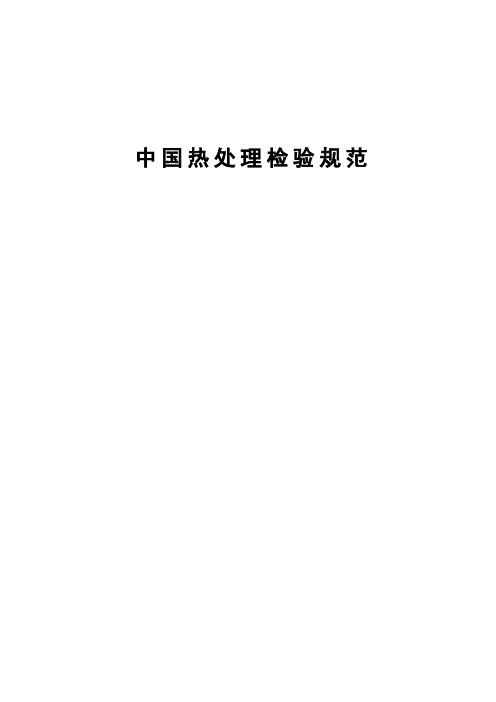
中国热处理检验规范热处理检验方法和规范金属零件的内在质量主要取决于材料和热处理。
因热处理为特种工艺所赋予产品的质量特性往往又室补直观的内在质量,属于“内科”范畴,往往需要通过特殊的仪器(如:各种硬度计、金相显微镜、各种力学性能机)进行检测。
在GB/T19000-ISO9000系列标准中,要求对机械产品零部件在整个热处理过程中一切影响因素实施全面控制,反映原材料及热处理过程控制,质量检验及热处理作业条件(包括生产与检验设备、技术、管理、操作人员素质及管理水平)等各方面均要求控制,才能确保热处理质量。
为此,为了提高我公司热处理产品质量,遵循热处理相关标准,按零件图纸要求严格执行,特制定本规范一、使用范围:本规范适用于零件加工部所有热处理加工零件。
二、硬度检验:通常是根据金属零件工作时所承受的载荷,计算出金属零件上的应力分布,考虑安全系数,提出对材料的强度要求,以强度要求,以强度与硬度的对应关系,确定零件热处理后应具有大硬度值。
为此,硬度时金属零件热处理最重要的质量检验指标,不少零件还时唯一的技术要求。
1、常用硬度检验方法的标准如下:GB230 金属洛氏硬度试验方法GB231 金属布氏硬度试验方法GB1818 金属表面洛氏硬度试验方法GB4340 金属维氏硬度试验方法GB4342 金属显微维氏硬度试验方法GB5030 金属小负荷维氏试验方法2、待检件选取与检验原则如下:为保证零件热处理后达到其图纸技术(或工艺)要求,待检件选取应有代表性,通常从热处理后的零件中选取,能反映零件的工作部位或零件的工作部位硬度的其他部位,对每一个待检件的正时试验点数一般应不少于3个点。
通常连续式加热炉(如网带炉):应在连续生产的网带淬火入回火炉前、回火后入料框前的网带上抽检3-5件/时。
且及时作检验记录。
同时,若发现硬度超差,应及时作检验记录。
同时,若发现硬度越差,应及时进行工艺参数调整,且将前1小时段的零件进行隔离处理(如返工、检)。
金相填空题

金属材料的金相分析填空题(初级)计量技术知识1.国家法定计量单位由国际单位制的计量单位和国家选定的其他计量单位构成。
金属学基础1.构成钢铁材料的主要元素是铁和碳。
2.金属的特性有:不透明、有特殊光泽、有可锻性良好的导电性和导热性、具有正的电阻温度系数。
3.晶格是用来表示晶体中的原子在空间规则排列的框架,又称为空间点阵。
4.晶格是用来表示晶体中的原子在空间规则排列的框架,又称为空间点阵。
5.典型的金属晶体结构类型有三种:体心立方晶格、面心立方晶格、密排六方晶格。
6.典型的金属晶体结构类型有三种:体心立方晶格、面心立方晶格、密排六方晶格。
7.按照合金中组成合金的组元原子的存在方式,合金相可以分成固溶体和金属间化合物两大类。
8.根据溶质原子在基体晶格中所处的位置不同,固溶体可以分为置换固溶体、间隙固溶体两种。
9.金属结晶需能量条件和结构条件。
10. 相是指合金中结构相同、成分和性能均一,并以相界面分开的组成部分。
11.合金相图是表示合金系中合金状态与温度、成分关系的图表。
12.相图是用来表示合金系中合金状态与温度、成份之间关系的。
13.晶体缺陷分点缺陷、线缺陷、面缺陷。
14.通常材料的性能包括物理、化学、力学和工艺四大性能。
15.过冷液体形成固态晶核有均质形核、非均质形核两种。
16.相图是表示合金系中的合金状态与温度、成分之间关系的一种图表。
17.金属传导热量的能力称作导热性,一般用导热系数λ表示。
18.黑色金属:以铁、铬、锰为基体的金属称为黑色金属。
19.合金是金属与金属或非金属元素通过熔炼而获得的一种具有金属特性的物体。
20.孪晶是在一个晶粒中点阵相同,以某一特定晶面孪晶面为界限,两边的点阵呈镜面对称的晶体。
21.根据晶体缺陷的几何形态特征可分为点缺陷、线缺陷和面缺陷。
22.金属结晶是由生核和晶核长大两个基本过程组成的。
23.钢中加入合金元素的目的是①提高机械性能,②改善热处理工艺性能,③获得特殊的物理及化学性能。
- 1、下载文档前请自行甄别文档内容的完整性,平台不提供额外的编辑、内容补充、找答案等附加服务。
- 2、"仅部分预览"的文档,不可在线预览部分如存在完整性等问题,可反馈申请退款(可完整预览的文档不适用该条件!)。
- 3、如文档侵犯您的权益,请联系客服反馈,我们会尽快为您处理(人工客服工作时间:9:00-18:30)。
试样的制备
奥氏体晶粒度的显示
晶粒度的测定方法:
1、比较法
•比较法:通过与标准系列评级图对比来评定平均晶粒度,存 在±0.5级偏差
•适于具有等轴晶粒的再结晶材料或铸态材料
•适合大多工业生产检验,如果第二相(或组元)基本上与基 体晶粒大小相同由岛状或片状组成,或者是第二相质点(晶粒) 的数量少而尺寸又小的,并位于初生晶粒的晶界处
i [3.3115lg(d)] 3.22
取样:沿钢材或零件的轧制或锻造方向通过中心取样;钢坯上
切取的检验面应通过钢材(或钢坯)轴心的纵截面20mm×10mm
钢材外表面到中心的中 通过直径的截面的一半 间位置的部分截面
通过整个直径的截 面,长度保证得到 检验面积
宽度1/4初的全厚度截面
检验面位于宽度1/4和从钢板表面到中心 位置,检验面为钢板厚度的1/2截面e出现粗系的夹杂物,s出现细系的夹杂物 如:B1e, B2.5s
B法:表示给定观察视场数(N)中每类夹杂物及每个宽度系 列夹杂物在给定级别上的视场总数
按照协议规定总级别( itol )或平均级别( imoy )
试验报告:
•非传统类夹杂物按与其形态最接近的A、B、C、D、DS类夹杂物评定
•对于A、B、C类夹杂物,纵向距离d≤40μm,横向距离s≤ 10μm,一条夹杂物
•一个串(条)状夹杂物宽度不同,取最大宽度
A类和C类夹杂物
B类夹杂物
结果表示:
通则:用每个试样的级别以及在此基础上所得的每炉钢每类 和每个宽度系列夹杂物的级别算术平均值表示。
四个系列的标准评级图:
评级图适用范围:
1.1 显微晶粒度的评定:
使用与相应标准系列评级图相同的放大倍数,直接对比。
将检测的晶粒图像与标准系列评级图投影到同一荧屏上, 可提高评级精确度。
当待测晶粒度超过标准系列图片所包括的范围或基准放大 倍数(75、100倍)不能满足需要时,可采用教材中表4-5
宽度和从钢板表面到中心之间的中心位 置,检验面为钢板厚度的1/4截面
夹杂物评定方法:
观察方法:在显微镜下:
实际检验:
A法:检验整个抛光面,对每一类夹杂物,按细系和粗系记 下与所检验面上最恶劣视场相符合的标准图片的级别数
B法:检验整个抛光面,但可以通过研究,减少检验视场数, 对试样做局部检验
二、金属平均晶粒度测定法(GB/T6394-2002)
晶粒度级别指数
晶粒度:指晶粒大小的量度,通常使用长度、面积或体积来 表示不同方法的评定或测量晶粒大小
显微晶粒度级别指数G:N=2G-1 试样在放大100倍下,在 645.16mm2 面积内包含的晶粒个数
宏观晶粒度级别指数Gm :N=2Gm -1 试样在1倍下,在 645.16mm2 面积内包含的晶粒个数
晶粒度报告
(1)铁素体钢,除用渗碳法显示奥氏体晶粒度外,其它方法应 报告如下内容:
若采用其他放大倍数进行评定,将放大倍数M的待测晶粒图 象与基准放大倍数Mb 的系列评级图片进行对比,评出的晶 粒度级别G’ ,其显微晶粒度级别数G为:
G G' Q
Q 6.6439 lg M Mb
1.2宏观晶粒度的评定
•对于特别粗大的晶粒,放大1倍,直接将有代表性的晶粒图 象与系列评级图Ι(非孪晶)和图Ⅱ和图Ⅲ(孪晶)进行比 较评级,宏观晶粒度可用平均晶粒直径或GB/T6349-2002标准 附录中的宏观晶粒度级别Gm 表示。
•当晶粒较小时,选用较高的放大倍数M进行宏观晶粒的评定,
若评出的晶粒度级别数为 ,Gm其' 宏观晶粒度级别数为:
Gm Gm' Qm
Qm 6.6439 lg M
2、面积法
通过计算给定面积网格内的晶粒数来测定晶粒度
基体晶粒边界清晰可见,且第二相(组元)质点(晶粒)主要 存在于基体晶粒之间而不在晶粒内时,
钢的显微组织评 定
一、钢中非金属夹杂物含量的测定
(GB/T10561-2005)
标准适用范围:压缩比大于或等于3的轧制或锻制钢材 原理:将所观察的视场与标准图谱对比,并分别对每类夹杂
物进行评级,标准中的评级图片相当于100倍下纵向抛光面 上的面积为0.5mm2 的正方形视场。 夹杂物分五类: A:硫化物类,较宽范围形态比的单个灰色夹杂物,端部圆角 B:氧化铝类,形态比小,沿轧制方向排成一排 C:硅酸盐类,较宽范围形态比的单个深灰色,端部锐角 D:球状氧化物,带角或圆形,形态比小,无规则分布 DS:单颗粒球状,圆形或近似圆形,直径≥13μm单颗粒夹杂
将已知面积(5000mm2)的圆形测量网格置于晶粒图形之上,选
用网格内至多能截获并不超过100个晶粒(建议50个)的放大
倍数M(网格面积大小以能覆盖基体晶粒为度),然后计算完
全落在测量网格内的晶粒数N内和被网格切割的晶粒数N交,该面
积范围内的晶粒计算为:
N
N内
1 2
N交
1
试样检测面上每平方毫米内晶粒数na: 晶粒度级别指数G:
na
M 2.N A
G 3.321928 lg na 2.954
3、截点法
通过统计给定长度的测量网格上的晶界截点数P来测定晶粒 度。对于非等轴晶粒,截点法即可用于分别测定三个相互垂 直的方向晶粒度,也可计算出总体的平均晶粒度。分直线截 点法和圆截点法。
适用于面积法的条件均适用于截点法
通则:
•每一个观察的视场与标准评级图谱对比,如果一个视场处于两相邻标准图片之 间时,应记录较低的一级。
•对于个别夹杂物或个别夹杂物,长度超过视场的边长(0.710mm),或宽度或直 径大于粗系最大值,作为超尺寸夹杂物评定,并分别记录,纳入该时常视场的 评级
•为提高实际测量的再现性,可采用上图所示的透明网格或轮廓线
每类夹杂物根据非金属夹杂物颗粒宽度的不同分为两个系 列,每个系列由表示夹杂物含量递增的六级图片组成
夹杂物级别评定:
lg(i) [0.5605lg(L)]1.179 lg(i) [0.4626lg(L)] 0.871 lg(i) [0.4807g(L)] 0.904
lg(i) [0.5lg(n)] 0.301