第四章 钢显微组织评定(全)
金属材料进厂检验方法
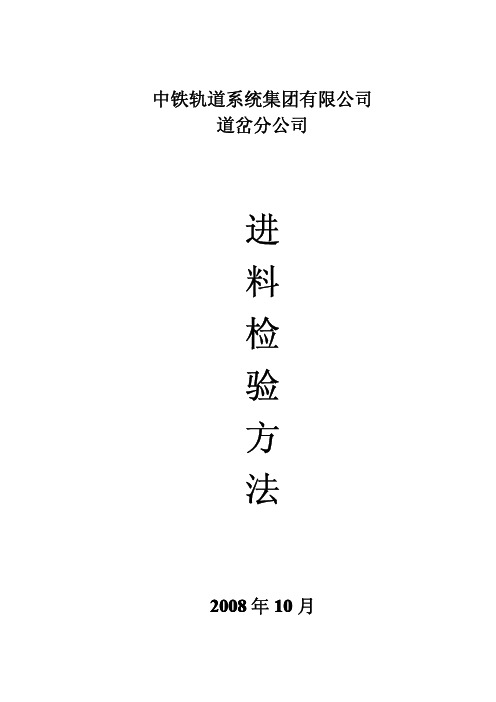
Nb
≤0.010 ≤0.010 0.020~0.050
RE
- -
残留元素上限(%) Cr 0.15 Mo 0.020 Ni 0.10 Cu 0.15 Sn 0.040 Sb 0.020 Ti 0.025 Cu+10Sn 0.35 Cr+Mo+Ni+Cu 0.35
需方要求对成品化学成分进行验证分析时,与表 1.1.2 规定成分范围的偏差值应符 合 GB/T222-2006 钢的成品化学成分允许偏差中表 1 的规定。 对残留元素, 若供方保证 , 可不做检验。 1.1.3 拉伸性能 钢轨的抗拉强度和伸长率应符合表 1.1.3 中规定。
外形、表面质量
验收检验项目
取样部位 图 1.1.1 图 1.1.1 过渡区外 的全断面 图 1.1.1 图 1.1.1 距轨端 300mm 处 全长 全长 - 试验方法 GB/T14203 GB/T228 GB226 GB/T13298 GB224 样板、影像 投影仪 目测 目测 - TB/T2344-2003 43kg/m~75kg/m 热轧钢轨订货 技术条件 检测依据
0.65~0.76 0.71~0.80 0.72~0.80
Si
0.15~0.35 0.50~0.80 0.60~0.90
Mn
1.10~1.40 0.70~1.05 1.00~1.30
P
≤0.030 ≤0.030 ≤0.030
SHale Waihona Puke ≤0.030 ≤0.030 ≤0.030
V
≤0.030 0.040~0.12 ≤0.030
图 1.1.1
普速 43kg/m~75kg/m 理化检验取样位置图
2
中铁轨道系统集团有限公司道岔分公司进料检验方法
钢中非金属夹杂物含量的测定标准评级图显微检验法介绍

钢中非金属夹杂物含量的测定标准评级图显微检验法介绍GB/T 10561—2005—何群雄,孙时秋:介绍了钢中非金属夹杂物含量测定显微检验法的概况,并对国标等同采用国际标准ISO4967:1998后变化的技术内容作了简要说明。
:非金属夹杂物;标准评级图显微检验法 0钢中非金属夹杂物的评定是衡量钢内在质量的一种重要方法,通过该方法的检验能反映钢中非金属夹杂物的含量、沾污度以及类型,为满足产品设计要求或改进生产工艺提供可靠的依据,尤其是非金属夹杂物的显微检验方法,更是各国冶金学家长期研究的课题。
随着显微技术和电子金相技术的不断发展,采用自动图像仪及计算机软件来评定非金属夹杂物的方法已经越来越多的被用于进行科学研究和实际生产检验。
目前美国金属材料协会(ASTM)E4委员会已有3个显微检验方法来评定非金属夹杂物含量的方法标准,即ASTM E45-97《用评级图谱评定非金属夹杂物的人工方法》、ASTM E1122-1986《自动图像分析法检查非金属夹杂物级别的方法》和ASTM E1245-2000《采用自动图像分析法测定钢中非金属夹杂物或第二相含量的方法》。
但是,应用光学显微镜测定钢中非金属夹杂物的标准图谱评级方法,至今还是在被最广泛地采用。
随着钢铁冶金技术的不断发展和对钢铁材料质量的要求不断提高,标准图谱评级的显微方法检验标准也在不断地修改和完善之中,如现行的国际标准ISO4967-1998《用标准图谱评定钢非金属夹杂物的显微方法》和美国ASTME45-97《钢中非金属夹杂物含量测定方法》对标准图谱和评定方法都作了较大的修改和变动,较好地解决了用光学显微镜评定钢中非金属夹杂物评定的一系列问题,使标准图谱的显微评定方法日趋完善。
GB/T10561-1989《钢中非金属夹杂物显微评定方法》标准是我国钢检测领域的一项重要的基础标准,也是钢中非金属夹杂物含量的主要检测方法之一。
该标准已颁布了一项重要的基础标准,也是钢中非金属夹杂物含量的主要检测方法之一。
(完整)合金钢、铸铁、有色金属的显微组织观察与分析
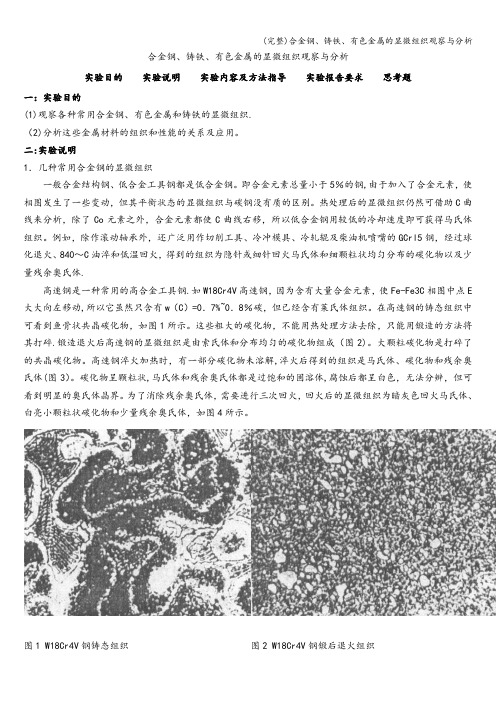
合金钢、铸铁、有色金属的显微组织观察与分析实验目的实验说明实验内容及方法指导实验报告要求思考题一:实验目的(1)观察各种常用合金钢、有色金属和铸铁的显微组织.(2)分析这些金属材料的组织和性能的关系及应用。
二:实验说明1.几种常用合金钢的显微组织一般合金结构钢、低合金工具钢都是低合金钢。
即合金元素总量小于5%的钢,由于加入了合金元素,使相图发生了一些变动,但其平衡状态的显微组织与碳钢没有质的区别。
热处理后的显微组织仍然可借助C曲线来分析,除了Co元素之外,合金元素都使C曲线右移,所以低合金钢用较低的冷却速度即可获得马氏体组织。
例如,除作滚动轴承外,还广泛用作切削工具、冷冲模具、冷轧辊及柴油机喷嘴的GCrl5钢,经过球化退火、840~C油淬和低温回火,得到的组织为隐针或细针回火马氏体和细颗粒状均匀分布的碳化物以及少量残余奥氏体.高速钢是一种常用的高合金工具钢.如W18Cr4V高速钢,因为含有大量合金元素,使Fe-Fe3C相图中点E 大大向左移动,所以它虽然只含有w(C)=0.7%~0.8%碳,但已经含有莱氏体组织。
在高速钢的铸态组织中可看到鱼骨状共晶碳化物,如图1所示。
这些粗大的碳化物,不能用热处理方法去除,只能用锻造的方法将其打碎.锻造退火后高速钢的显微组织是由索氏体和分布均匀的碳化物组成(图2)。
大颗粒碳化物是打碎了的共晶碳化物。
高速钢淬火加热时,有一部分碳化物未溶解,淬火后得到的组织是马氏体、碳化物和残余奥氏体(图3)。
碳化物呈颗粒状,马氏体和残余奥氏体都是过饱和的固溶体,腐蚀后都呈白色,无法分辨,但可看到明显的奥氏体晶界。
为了消除残余奥氏体,需要进行三次回火,回火后的显微组织为暗灰色回火马氏体、白亮小颗粒状碳化物和少量残余奥氏体,如图4所示。
图1 W18Cr4V钢铸态组织图2 W18Cr4V钢锻后退火组织图3 W18Cr4V钢的淬火组织图4 W18CNV钢的淬火回火组织2.铸铁的显微组织依铸铁在结晶过程中石墨化程度不同,可分为白口铸铁、灰口铸铁、麻口铸铁.白口铸铁具有莱氏体组织而没有石墨,碳几乎全部以碳化物形式(Fe3C)存在;灰口铸铁没有莱氏体,而有石墨,即碳部分或全部以自由碳、石墨的形式存在。
钢的显微组织评定方法课件

在失效分析中的应用
失效原因分析 通过对失效材料的显微组织进行观察和分析,了解材料的 微观结构和性能变化,找出失效原因,为预防措施提供依 据。
失效模式识别 通过显微组织观察,识别材料的失效模式,如韧性断裂、 脆性断裂、疲劳断裂等,有助于采取相应的改进措施。
失效预防措施 根据显微组织评定的结果,制定针对性的失效预防措施, 如改进工艺参数、调整材料成分、加强产品检测等,提高 产品的可靠性和使用寿命。
渗碳体具有较好的耐腐蚀性,而铁素 体和奥氏体则相对较差。
02
显微组织评定方法
金相显微镜观察法
总结词
金相显微镜观察法是一种常用的显微组织评定方法,通过光 学显微镜观察金属材料的显微组织,分析其结构、形态和分布。
详细描述
金相显微镜观察法利用光学显微镜的高倍率放大能力,观察 金属材料的显微组织,包括晶粒大小、形态、相组成等。通 过对不同区域的组织观察和比较,可以对材料的性能和工艺 条件进行分析和评估。
钢的显微组织评定 方法课件
目 录
• 钢的显微组织基础 • 显微组织评定方法 • 钢的显微组织评定标准 • 钢的显微组织评定实践 • 钢的显微组织评定应用 • 钢的显微组织评定展望
contents
01
钢的显微组织基础
钢的显微组织组成
01
02
03
04
铁素体
一种常见的显微组织,具有较 低的强度和韧性,但良好的塑
04
钢的显微组织评定实践
钢材显微组织的制备
切割钢材样品
使用金相切割机将钢材切割成 适合观察的尺寸,确保样品表
面平整、无划痕。
磨平样品
将切割好的样品进行粗磨和细 磨,去除表面的杂质品
使用抛光机对样品进行抛光, 使表面更加光滑,减少观察时 的干扰。
第四章 二元合金相图与合金凝固参考答案

第四章二元合金相图与合金凝固一、本章主要内容:相图基本原理:相,相平衡,相律,相图的表示与测定方法,杠杆定律;二元匀晶相图:相图分析,固溶体平衡凝固过程及组织,固溶体的非平衡凝固与微观偏析固溶体的正常凝固过程与宏观偏析:成分过冷,溶质原子再分配,成分过冷的形成及对组织的影响,区域熔炼;二元共晶相图:相图分析,共晶系合金的平衡凝固和组织,共晶组织及形成机理:粗糙—粗糙界面,粗糙—光滑界面,光滑—光滑界面;共晶系非平衡凝固与组织:伪共晶,离异共晶,非平衡共晶;二元包晶相图:相图分析,包晶合金的平衡凝固与组织,包晶反应的应用铸锭:铸锭的三层典型组织,铸锭组织控制,铸锭中的偏析其它二元相图:形成化合物的二元相图,有三相平衡恒温转变的其它二元相图:共析,偏晶,熔晶,包析,合晶,有序、无序转变,磁性转变,同素异晶转变二元相图总结及分析方法二元相图实例:Fe-Fe3C亚稳平衡相图,相图与合金性能的关系相图热力学基础:自由能—成分曲线,异相平衡条件,公切线法则,由成分—自由能曲线绘制二元相图二、1.填空1 相律表达式为___f=C-P+2 ___。
2. 固溶体合金凝固时,除了需要结构起伏和能量起伏外,还要有___成分_______起伏。
3. 按液固界面微观结构,界面可分为____光滑界面_____和_______粗糙界面___。
4. 液态金属凝固时,粗糙界面晶体的长大机制是______垂直长大机制_____,光滑界面晶体的长大机制是____二维平面长大____和_____依靠晶体缺陷长大___。
5 在一般铸造条件下固溶体合金容易产生__枝晶____偏析,用____均匀化退火___热处理方法可以消除。
6 液态金属凝固时,若温度梯度dT/dX>0(正温度梯度下),其固、液界面呈___平直状___状,dT/dX<0时(负温度梯度下),则固、液界面为______树枝___状。
7. 靠近共晶点的亚共晶或过共晶合金,快冷时可能得到全部共晶组织,这称为____伪共晶__。
20钢铁材料渗层深度测定及组织检验
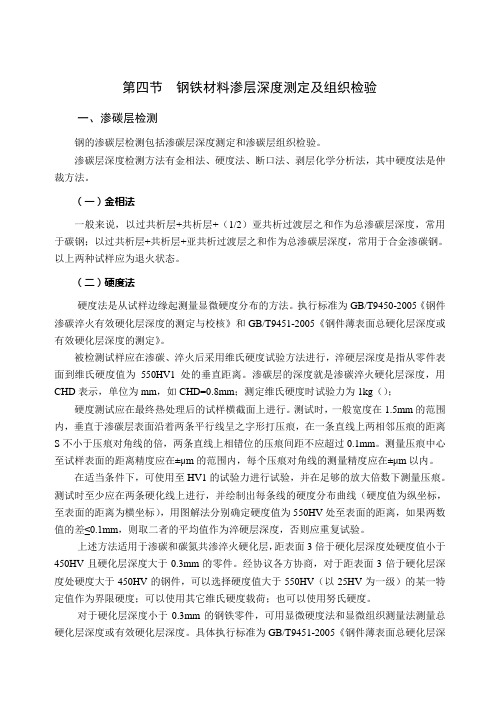
第四节钢铁材料渗层深度测定及组织检验一、渗碳层检测钢的渗碳层检测包括渗碳层深度测定和渗碳层组织检验。
渗碳层深度检测方法有金相法、硬度法、断口法、剥层化学分析法,其中硬度法是仲裁方法。
(一)金相法一般来说,以过共析层+共析层+(1/2)亚共析过渡层之和作为总渗碳层深度,常用于碳钢;以过共析层+共析层+亚共析过渡层之和作为总渗碳层深度,常用于合金渗碳钢。
以上两种试样应为退火状态。
(二)硬度法硬度法是从试样边缘起测量显微硬度分布的方法。
执行标准为GB/T9450-2005《钢件渗碳淬火有效硬化层深度的测定与校核》和GB/T9451-2005《钢件薄表面总硬化层深度或有效硬化层深度的测定》。
被检测试样应在渗碳、淬火后采用维氏硬度试验方法进行,淬硬层深度是指从零件表面到维氏硬度值为550HV1处的垂直距离。
渗碳层的深度就是渗碳淬火硬化层深度,用CHD表示,单位为mm,如CHD=0.8mm;测定维氏硬度时试验力为1kg();硬度测试应在最终热处理后的试样横截面上进行。
测试时,一般宽度在1.5mm的范围内,垂直于渗碳层表面沿着两条平行线呈之字形打压痕,在一条直线上两相邻压痕的距离S不小于压痕对角线的倍,两条直线上相错位的压痕间距不应超过0.1mm。
测量压痕中心至试样表面的距离精度应在±μm的范围内,每个压痕对角线的测量精度应在±μm以内。
在适当条件下,可使用至HV1的试验力进行试验,并在足够的放大倍数下测量压痕。
测试时至少应在两条硬化线上进行,并绘制出每条线的硬度分布曲线(硬度值为纵坐标,至表面的距离为横坐标),用图解法分别确定硬度值为550HV处至表面的距离,如果两数值的差≤0.1mm,则取二者的平均值作为淬硬层深度,否则应重复试验。
上述方法适用于渗碳和碳氮共渗淬火硬化层,距表面3倍于硬化层深度处硬度值小于450HV且硬化层深度大于0.3mm的零件。
经协议各方协商,对于距表面3倍于硬化层深度处硬度大于450HV的钢件,可以选择硬度值大于550HV(以25HV为一级)的某一特定值作为界限硬度;可以使用其它维氏硬度载荷;也可以使用努氏硬度。
焊接金相组织
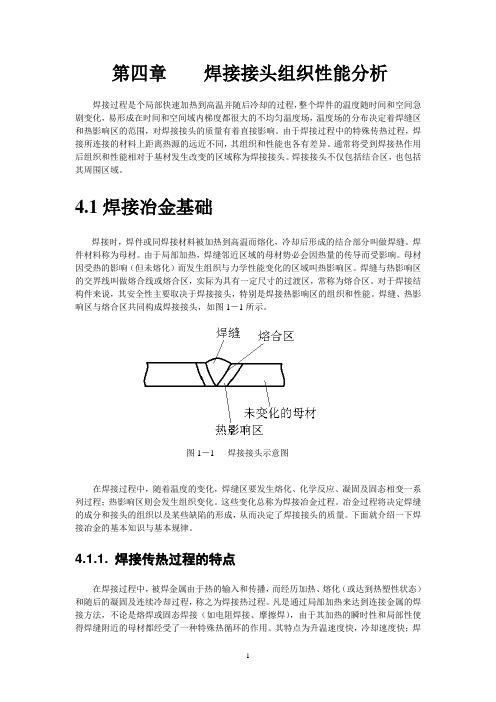
第四章焊接接头组织性能分析焊接过程是个局部快速加热到高温并随后冷却的过程,整个焊件的温度随时间和空间急剧变化,易形成在时间和空间域内梯度都很大的不均匀温度场,温度场的分布决定着焊缝区和热影响区的范围,对焊接接头的质量有着直接影响。
由于焊接过程中的特殊传热过程,焊接所连接的材料上距离热源的远近不同,其组织和性能也各有差异。
通常将受到焊接热作用后组织和性能相对于基材发生改变的区域称为焊接接头。
焊接接头不仅包括结合区,也包括其周围区域。
4.1焊接冶金基础焊接时,焊件或同焊接材料被加热到高温而熔化,冷却后形成的结合部分叫做焊缝。
焊件材料称为母材。
由于局部加热,焊缝邻近区域的母材势必会因热量的传导而受影响。
母材因受热的影响(但未熔化)而发生组织与力学性能变化的区域叫热影响区。
焊缝与热影响区的交界线叫做熔合线或熔合区,实际为具有一定尺寸的过渡区,常称为熔合区。
对于焊接结构件来说,其安全性主要取决于焊接接头,特别是焊接热影响区的组织和性能。
焊缝、热影响区与熔合区共同构成焊接接头,如图1-1所示。
图1-1 焊接接头示意图在焊接过程中,随着温度的变化,焊缝区要发生熔化、化学反应、凝固及固态相变一系列过程;热影响区则会发生组织变化。
这些变化总称为焊接冶金过程。
冶金过程将决定焊缝的成分和接头的组织以及某些缺陷的形成,从而决定了焊接接头的质量。
下面就介绍一下焊接冶金的基本知识与基本规律。
4.1.1. 焊接传热过程的特点在焊接过程中,被焊金属由于热的输入和传播,而经历加热、熔化(或达到热塑性状态)和随后的凝固及连续冷却过程,称之为焊接热过程。
凡是通过局部加热来达到连接金属的焊接方法,不论是熔焊或固态焊接(如电阻焊接、摩擦焊),由于其加热的瞬时性和局部性使得焊缝附近的母材都经受了一种特殊热循环的作用。
其特点为升温速度快,冷却速度快;焊接加热的另一个特点为热场分步极不均匀,紧靠焊缝的高温区内接近熔点,远离焊缝的低温区内接近室温,这一加热特点也造成焊件的温度分布不均匀,并随时间而不断变化,参见图1-2。
第四章 铁碳合金相图
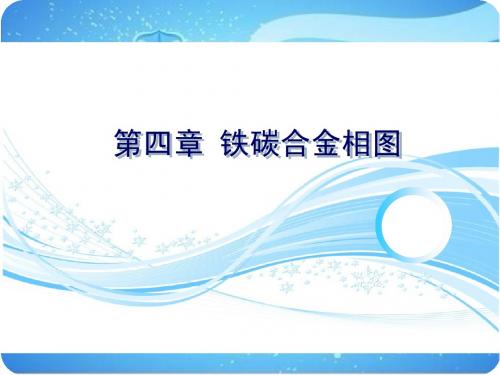
的性能与纯铁相似,硬度低而塑性高,并有铁磁
性。
铁碳合金中的基本相
• 铁素体的力学性能特点是塑性、韧性好,
而强度、硬度低。
• δ=30%~50%,AK=128~160J
σb=180~280MPa,50~80HBS。
铁碳合金中的基本相
• 铁素体的显微组织与纯铁相同,用4%硝酸 酒精溶液浸蚀后,在显微镜下呈现明亮的 多边形等轴晶粒,在亚共析钢中铁素体呈
铁碳合金中的基本相
• 奥氏体的组织与铁素体相似,但晶界较
为平直,且常有孪晶存在。
铁碳合金中的基本相
3、渗碳体(Cementite)
• 渗碳体是铁和碳形成的具有复杂结构的金
属化合物,用化学分子式“Fe3C”表示。它
的碳质量分数wc=6.69%,熔点为1227℃。
• 硬而脆,耐腐蚀。用4%硝酸酒精溶液浸蚀 后,在显微镜下呈白色,如果用4%苦味酸 溶液浸蚀,渗碳体呈暗黑色。
第四章 铁碳合金相图
LOGO
概述
• 钢铁是现代工业中应用最广泛的材料,其 基本组成元素是铁和碳,故称为铁碳合金。 普通碳钢和铸铁就属于铁碳合金的范畴, 而合金钢则是有意加入一些合金元素的铁 碳合金。 • 为了研究铁碳合金的组织和性能以及它们 与成分、温度的关系,就必须学习铁碳合 金相图。
概述
• 铁碳合金相图最早是在1889年测定的,距
• 钢中wc↑,其可焊性↓,故焊接用钢主要是指 低碳 钢和低碳合金钢。
上一级
• (三) 切削加工性能
• 金属的切削加工性能是指金属进行切削 加工时的难易程度。 • 钢的硬度为160~230HBS时,切削加工 性最好。
上一级
ቤተ መጻሕፍቲ ባይዱ
LOGO
水平线ECF为共晶反应线。
- 1、下载文档前请自行甄别文档内容的完整性,平台不提供额外的编辑、内容补充、找答案等附加服务。
- 2、"仅部分预览"的文档,不可在线预览部分如存在完整性等问题,可反馈申请退款(可完整预览的文档不适用该条件!)。
- 3、如文档侵犯您的权益,请联系客服反馈,我们会尽快为您处理(人工客服工作时间:9:00-18:30)。
游离渗碳体评定(400×) (碳的质量分数≤0.15%的退火钢)
评级图:三个系列、六个级别 A系列:铁素体晶粒外围被渗碳体网包围的
比率作为评定原则
B系列:渗碳体颗粒构成单层、双层、多层 不同长度链状和颗粒尺寸的增大为原则
C系列:点状渗碳体向不均匀的带状过渡为 原则
低碳变形钢的珠光体评定(400×)
(GB/T13320-1991)
适用范围 调质处理或正火处理的汽车、拖拉机、通用 机械等结构钢锻件,不适用于锻件脱碳、过 热、过烧等组织的评定。
一、试样的选取(A)截面尺寸 小于40mm, 取整个截面(B)截面尺寸 40-60mm,取中 心试样(C)截面尺寸大于60mm,取边部和中 心试样。
试样的制取:取平行于压力加工方向截面
晶粒延伸度e=n1/n2 e=n1/n2 n1:横向所切 割的晶粒数: n2纵向所切割的晶粒数
测定方法(100×)
比较法:评级图Ⅰ( e=1)、评级图Ⅱ( e=2)、 评级图Ⅲ( e=4)
切割法晶粒度级数 级别数表示:评级图+下标(例如Ⅱ3)
评级图:二个系列、六个级别 A系列:含碳量0.15~0.30% 钢的魏氏织 B系列:含碳量0.31~0.50%钢的魏氏组
织
第四节 钢的脱碳层深度测定方法
(GB/T224-2008)
脱碳层的专业术语
部分脱碳:钢样表层碳含量低于材料规定的含碳 量的下限,但碳含量高于在铁素体中的做大溶解 度。
适用范围
测定钢材及零件的脱碳层深度 完全脱碳与部分脱碳
测定方法
金相法:不同部位的五点脱碳层深度;这些测 量值的平均值为总脱碳层深度
硬度法:用0.49N~4.9N试验力,从表面测至 基体平稳处的距离为总脱碳层深度
化学分析法
碳含量与产品表面距离的关系
不同规格圆钢棒的取样方法
钢中非金属夹杂物显微评定方法
(GB/T10561-2005)
适用范围
适用于经过压缩比大于或等于3的延伸变形(轧制、 锻造、冷拔等)的钢材中非金属夹杂物的显微评定
试样的选取与制备
纵向,面积200mm2
显微评定方法(100X)
评级图:ISO评级图 检验方法:A法、B法 结果表示 试验报告
根据其形态将夹杂物归入五种夹杂物进行评定,但注 明化学特征
例如:球状硫化物Dsulf1.0 球状硫化钙Dcas0.5 串连状氮化钛BTiN1.5
不在同一直线上夹杂物的评定
二条夹杂物纵间距≤40μm、横间距≤10μm应视为一条夹杂物
超大尺寸夹杂物的评定
1)在100×下的 71mm×71mm范围内夹杂物 纳入评级 2)单独指明超大夹杂物的长度或宽度
完全脱碳:钢样表层碳含量低于碳在铁素体中的 做大溶解度。
总脱碳层深度:完全脱碳深度+部分脱碳深度。 有效脱碳层深度:从产品表面到规定的碳含量或
硬度水平的点的距离,规定的碳含量或硬度水平 以不因脱碳而影响使用性能为准(产品规定的碳 含量最小值)。 铁素体脱碳层深度:表面完全脱碳层的深度。
奥氏体钢晶粒度
化学试剂显示法 电解腐蚀显示法
铝及铝合金晶粒度 铜及铜合金晶粒度 镁及镁合金晶粒度 镍及镍合金晶粒度 锌及锌合金晶粒度
晶粒度的测定方法
比较法:通过与标准评级图对比来评定。
评级图四个系列 :无孪晶晶粒100×、有孪晶晶粒 100×、有孪晶晶粒75×、 钢中奥氏体晶粒
不同规格方钢的取样方法
钢板和矩形钢材的取样方法
第五节
中碳钢与中碳合金钢结构钢马 氏体等级
(JB/T9211-2008)
适用范围
中碳钢和中碳合金结构钢整体淬火或淬火后 200℃以下回火的马氏体组织的检验,
标准规定
马氏体的级别1~8级,放大倍数500倍。
第六节
钢质模锻件金相组织评级图与评定 方法
16
38
555
510
25
53
822 <1147 746 <1029 36 <49 76 <107
夹杂物宽度极限值(μm)
类别
细系
粗系
最小宽度(μm) 最大宽度(μm) 最小宽度(μm)
A
2
4
>4
B
2
9
>9
C
2
5
>5
D
3
8
>8
注:D类夹杂物的最大尺寸定义为直径
最大宽度(μm)
12 15 12 13
非传统类夹杂物的评定
D
型
细系
1.5
1.5
1.5
1.5
粗系
1.0
ቤተ መጻሕፍቲ ባይዱ1.0
1.0
1.0
晶粒度: ≥5级
三、扁 钢试样选取:厚度≤30mm,应在1/4扁钢宽度处取纵向剖面试样, 试面的长度约15 mm,宽度约1/4厚度。厚度>30mm,同样在1/4扁钢宽 度处取纵向剖面试样,试面长度约15mm,宽度约1/2厚度。
四、试样的放大倍数为100X,评定的视场为样品中最严重的区域。对于网 状碳化物,要考虑网的变形、完整及网上碳化物的堆积程度。对于带状碳化 物,要考虑带的宽度和带内碳化物的堆积程度。
A类夹杂物级别0.5级的视场数为n1,级别为1的为n2,级别为2.5的为n3…….那 么所有视场评级为:(0.5*n1+1*n2+2.5*n3)/(n1+n2+n3)
GB/T10561-2005标准中夹杂物的评定类 型
A:硫化物类(灰色条状) B:氧化铝类(黑色带角并沿变形方向排成一行——至少 三颗) C:硅酸盐类(深灰色条状) D:球状氧化物类(深灰色) DS:单颗球状氧化物(深灰色——直径≥13μm)
第二节
金属平均晶粒度测定方法
(GB/T6394-2002)
适用范围
测定金属材料晶粒度,以晶粒的几何图形为基础。
试样的制备
在交货状态的材料切取,尺寸:φ10~12mm, 10×10mm
晶粒度的显示方法
铁素体钢的奥氏体晶粒度
渗碳法 网状铁素体法 氧化法 直接淬火法 网状渗碳体法 网状珠光体(托氏体)法
附3(GB/T13305-1991)
奥氏体不锈钢中α相面积含量金相测定方法
α级别 0.5 1.0 1.5 2.0 3.0 4.0
α相面积含量% ≤2 >2~5 >5~8 >8~12 >12~20 >20~35
附4(GB4234-1994) 外科植入物用不锈钢
测定夹杂物和晶粒度要求
夹杂物类 A
B
C
评级图1:中碳结构钢的正火处理锻件(1~8级) 评级图2:低碳低合金钢的正火处理锻件(1~8级) 评级图3:中碳结构钢的调质处理锻件(1~8级) 评级图4:中碳合金结构钢的调质处理锻件(1~8级)
附1
低碳钢冷轧薄板铁素体晶粒度的测
定法
(GB/T4335-1984)
适用 范围
含碳量小于0.2%的低碳(低碳低合金)冷轧薄板的 铁素体晶粒度
实际检验A法:
把抛光后的未经侵蚀的试样置于显微镜下观察,对各类夹杂物按粗系或细 系记下,然后把最恶劣的视场与标准评级图进行比较,相符的即为该试样 夹杂物的级别。 表示:A2;B1e, B2.5s
实际检验B法:
应检验整个抛光面,试样每个视场同标准图片相比较,每类夹杂物按细系 或粗系记录下来与检验视场最符合的级别数。为了使检验费用降到最低, 可以减少检验视场,并使其分布符合一定的方案,然后对试样局部检验。
夹杂物的评级界限:长度、颗数、直径(最小值)
级别(i) A总长度(μm) B总长度(μm) C总长度(μm) D(颗数) DS (直径μm)
0.5 37 1.0 127 1.5 261 2.0 436 2.5 649 3.0 895<
1181
17
18
1
13
77
76
4
19
184
176
9
27
343
320
第一评级图:适用直径、边长或厚度<120mm的热轧、锻制及冷拉钨系高 速钢。
第二评级图:适用直径、边长或厚度<120mm的热轧、锻制及冷拉钨钼系 高速钢、 高温不锈轴承钢
第三评级图:适用直径≥120mm的高速工具钢锻材。 第四评级图:热轧、锻制及冷拉合金工具钢材。 第五评级图:热轧、锻制及冷拉高碳铬不锈轴承钢材 第六评级图:高温轴承钢钢材
带状组织评定
带状贯穿视场的程度、连续性、变形铁素体晶粒的多少为原则( 100×)
A系列:含碳量≤0.15 %钢的带状组织 评级图:三个系列、六个级别 B系列:含碳量0.16~0.30% 钢的带状组
织 C系列:含碳量0.31~0.50%钢的带状组织
魏氏组织的评定(100×)
针状铁素体的数量、尺寸、奥氏体晶粒大小为原则
面积法
截点法
单圆截点法 直线截点法 三圆截点法
报告
第三节 钢的显微组织评定方法
(GB/T13299-1991)
适用范围
低碳、中碳钢的钢板、钢带、和型材的显微组织
试样的制取 评定方法 评定原则
游离渗碳体 低碳变形钢的珠光体 带状组织 魏氏组织
(碳的质量分数≤0.10~0.30%)
评级图:三个系列、六个级别 A系列:含碳量0.10~0.20%冷轧钢,渗碳
体颗粒聚集并趋向带状为原则 B系列:含碳量0.10~0.20%热轧钢中细粒
状珠光体向片状珠光体过渡为原则 C系列:含碳量0.21~0.30%热轧钢细粒状
珠光体向不均匀的珠光体带状过渡为原则
附2 钢的共晶碳化物不均匀度评级法
(GB/T14979-1994)