焊点可靠性研究
无铅焊点的可靠性及其验证试验

无铅焊点的可靠性及其验证试验编辑: panda-liu无铅焊点的可靠性及其验证试验by John H. Lau Agilent Technologies, Inc. EMA摘要本研究中对RoHS符合产品的可靠性进行了研究,重点是无铅焊点的可靠性。
焊料在电子组装中是一个电的和机械的―胶水‖。
无铅焊料提供的特性是否会让业界在未来一直依赖它?本文无法给出结论!然而,我们试图帮助所有从事这项工作的人更好地理解为什么或应该如何去做,以便他们在未来能够找出答案。
引言R oHS中规定禁止使用铅(Pb),汞(Hg),镉(Cd),六价铬(Cr6+),PBB(多溴联苯),PBDE(多溴二苯醚)等6 种有害物质,实施日期是2006年7月1日。
这意味着,从这天起,所有的EEE(电气、电子设备),除那些豁免的之外[1,2,3],如果他们含有这6种禁用物质,都不能在欧盟市场上销售。
无-X (如无- 铅)的定义是什么?这6种禁用物质在任何一个EEE的均匀材质中所允许的最大浓度值(MCV)已在EU公报上公布,并在2005 年8月18日立法[4]。
它陈述:条款5(1)(a)规定,铅、汞、六价铬、多溴联苯(PBB),多溴二苯醚(PBDE)均匀材质的MCV 为0.1%重量百分比,镉的MCV为0.01%。
简单地讲,以无铅为例,定义为任何一个EEE在所有的(单个的)均匀材质中,铅含量小于0.1wt%。
什么是均匀材料?它定义为不能进一步分解成不同材料的单一材料。
更多的―均匀材料‖解释,请参看[5]。
本文重点仅讨论Pb有害物质。
当今,焊料合金多半使用的是63Sn37Pb,熔点183℃。
不久前,多于1 0 0种无铅焊料合金存在于世,如[6]中表3.1 所示。
然而,今天电子业界主要的无铅焊料是Sn(3-4)wt%Ag(0.5-0.7)wt%Cu (或简称SAC),熔点217 ℃,比铅锡焊料合金的熔点高34℃。
印制电路板组装采用SAC焊料(替代SnPb)时,元件和PCB将承受更高的焊接温度,且他们在成本、性能和可靠性方面有很大的不同[10]。
应用电阻法进行锡基无铅焊点可靠性的研究的开题报告
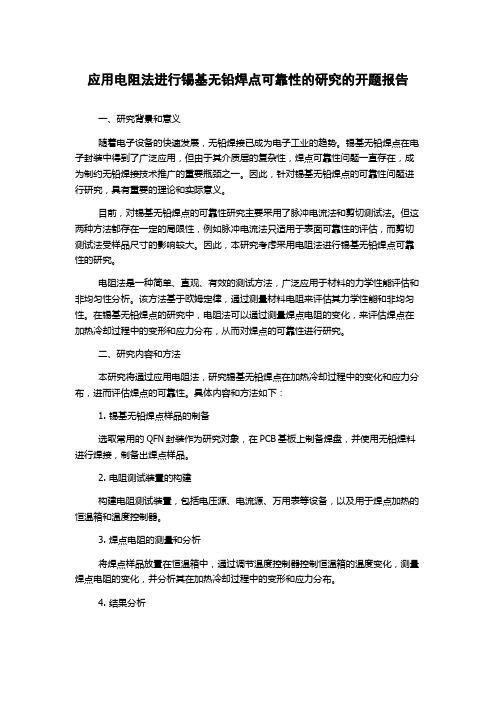
应用电阻法进行锡基无铅焊点可靠性的研究的开题报告一、研究背景和意义随着电子设备的快速发展,无铅焊接已成为电子工业的趋势。
锡基无铅焊点在电子封装中得到了广泛应用,但由于其介质层的复杂性,焊点可靠性问题一直存在,成为制约无铅焊接技术推广的重要瓶颈之一。
因此,针对锡基无铅焊点的可靠性问题进行研究,具有重要的理论和实际意义。
目前,对锡基无铅焊点的可靠性研究主要采用了脉冲电流法和剪切测试法。
但这两种方法都存在一定的局限性,例如脉冲电流法只适用于表面可靠性的评估,而剪切测试法受样品尺寸的影响较大。
因此,本研究考虑采用电阻法进行锡基无铅焊点可靠性的研究。
电阻法是一种简单、直观、有效的测试方法,广泛应用于材料的力学性能评估和非均匀性分析。
该方法基于欧姆定律,通过测量材料电阻来评估其力学性能和非均匀性。
在锡基无铅焊点的研究中,电阻法可以通过测量焊点电阻的变化,来评估焊点在加热冷却过程中的变形和应力分布,从而对焊点的可靠性进行研究。
二、研究内容和方法本研究将通过应用电阻法,研究锡基无铅焊点在加热冷却过程中的变化和应力分布,进而评估焊点的可靠性。
具体内容和方法如下:1. 锡基无铅焊点样品的制备选取常用的QFN封装作为研究对象,在PCB基板上制备焊盘,并使用无铅焊料进行焊接,制备出焊点样品。
2. 电阻测试装置的构建构建电阻测试装置,包括电压源、电流源、万用表等设备,以及用于焊点加热的恒温箱和温度控制器。
3. 焊点电阻的测量和分析将焊点样品放置在恒温箱中,通过调节温度控制器控制恒温箱的温度变化,测量焊点电阻的变化,并分析其在加热冷却过程中的变形和应力分布。
4. 结果分析根据测量结果,分析焊点在加热冷却过程中的变形和应力分布,并评估焊点的可靠性。
同时,与其他测试方法进行比较,验证电阻法在评估焊点可靠性方面的有效性。
三、研究预期成果本研究旨在通过应用电阻法,研究锡基无铅焊点在加热冷却过程中的变化和应力分布,进而评估焊点的可靠性。
QFN器件封装技术及焊点可靠性研究进展

QFN 器件封装技术及焊点可靠性研究进展随着电子设备的不断发展和更新,对器件的封装方式也提出了更高的要求。
传统的DIP(Dual in-line Package)和SOP(Small Outline Package)封装已经不能满足高密度、小体积的产品设计要求,QFN (Quad Flat No-leads)封装因其小尺寸、易于制造和高可靠性的特点受到了广泛的关注和应用。
本文将综述QFN 器件封装技术及其焊点可靠性研究进展。
一、QFN 封装技术的发展QFN 是一种新型的小封装器件,其与SOP 封装相比较,具有尺寸更小,耐机械应力和环境温度变化的能力更强,并且因其无引线封装技术,可以减少因引线老化、断裂导致的坏点率。
随着QFN 应用的不断推进,越来越多的生产厂家开始研究和开发QFN 封装技术。
目前基于QFN 封装技术已经发展出了多种类型,常用的有QFN、DFN、SON 封装。
QFN 封装结构特点QFN 封装结构示意图如下图所示:QFN 封装通常会有金属片和封装耳两个部分。
金属片是做为引子追踪结构,充当芯片和基板的连接。
封装耳的设计旨在增加由于温度差异及机械应力的变化而可能导致的应力释放功能。
同时,又因为QFN 封装表面积小,增加封装耳的数量没有大尺寸封装那么容易。
因此,在QFN 封装中,采用封装耳的技术,但是数量要限制,大约在周边6 个位置左右。
QFN 封装工艺步骤QFN 封装工艺主要包括芯片焊接、烤合、粘接和切割等步骤。
该流程包括如下工艺步骤:Step1:基板清洗基板的清洗是为了去除表面的污垢,确保焊接质量。
Step2:芯片焊接将芯片银浆点焊到基板下面,然后将芯片与基板烤合在一起。
Step3:烤合在热板上,加热芯片和基板,使之彼此结合。
Step4:粘接在芯片上部涂上粘接剂,将芯片贴到基板上。
Step5:切割采用拉丝式切割,即先在芯片上把一定深度的切缝拉开,再用剪刀或切割机进行切割。
以上这些步骤构成了QFN 器件封装过程中的主要流程,总体来说相比传统的SOP 封装方式而言,QFN 封装流程更加的严格,也更加复杂。
LCCC封装器件焊点可靠性研究
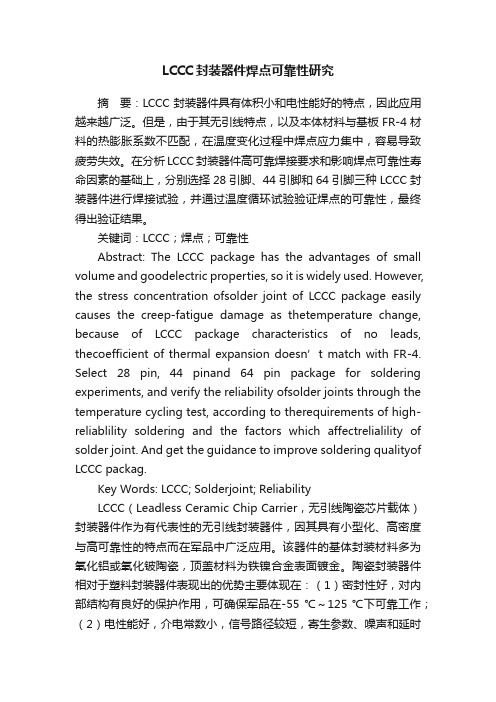
LCCC封装器件焊点可靠性研究摘要:LCCC封装器件具有体积小和电性能好的特点,因此应用越来越广泛。
但是,由于其无引线特点,以及本体材料与基板FR-4材料的热膨胀系数不匹配,在温度变化过程中焊点应力集中,容易导致疲劳失效。
在分析LCCC封装器件高可靠焊接要求和影响焊点可靠性寿命因素的基础上,分别选择28引脚、44引脚和64引脚三种LCCC封装器件进行焊接试验,并通过温度循环试验验证焊点的可靠性,最终得出验证结果。
关键词:LCCC;焊点;可靠性Abstract: The LCCC package has the advantages of small volume and goodelectric properties, so it is widely used. However, the stress concentration ofsolder joint of LCCC package easily causes the creep-fatigue damage as thetemperature change, because of LCCC package characteristics of no leads, theco efficient of thermal expansion doesn’t match with FR-4. Select 28 pin, 44 pinand 64 pin package for soldering experiments, and verify the reliability ofsolder joints through the temperature cycling test, according to therequirements of high-reliablility soldering and the factors which affectrelialility of solder joint. And get the guidance to improve soldering qualityof LCCC packag.Key Words: LCCC; Solderjoint; ReliabilityLCCC(Leadless Ceramic Chip Carrier,无引线陶瓷芯片载体)封装器件作为有代表性的无引线封装器件,因其具有小型化、高密度与高可靠性的特点而在军品中广泛应用。
QFP焊点可靠性研究

Vo1 1 0
.
电
பைடு நூலகம்
子
与
封
装
,
No 1 2
.
ELECTRONI CS & PACKAGI NG
总 第9 2期 21 0 0年 1 2月
封0; 装
组 装 与 测{ 试
QF 点可 靠性 研 究 P焊
邓 小 军
( 锡 创立 达 科 技 有 限 公 司 ,江 苏 无锡 2 4 4 ) 无 1 12
中图分类号 :T 3 59 文献标 识码 : N 0. 4 A
文章编号 :18 .0 0 (0 0 20 0 .4 6 117 2 1 )1.0 80
Ree rho l blyo PS le on sa c nRe a it f i i QF od r it J
DN E GXi - n aj ou
然而铅 对人 体存 在神 经毒性 等 危害 ,对环境 存 在重
金属污染【,使得无铅化的 I ” c引脚焊点研究早在 17 0 9
年 代就 已受到业 界的重视 。
2 Q P焊 点 的 A YS模 型 F NS
塑性 应变 是引起 焊 点材料 失效的 主要原 因 。 由 于 QF P引脚厚度较 大及焊 点对其有 约束性 ,故将其 简化 为平 面应 变 问题 。
rsace o la—e le . h l t riite i fc r hc f tte ea i y fh lejit eerhs fedf e odr T e a i sa n at i a e sh lbl te o ron r s s p sc t n sh ma o w h f c r i i o t sd i et nc p caig acrig osles i f rn e met (n bAg u n t , l l e ne c o i akgn ,cod dr w t d f e tl ns S , , , )ad a owe a ua l r s nt o h ie e P C ri cc t te l t ri o t F l r i i nte met to dr lp mprt e yl g od in, h a is a f e P o ej nw t f i e nme d n emut lt ea r cn n io s p sc t n h Q s d o t h i el h u i ee u c i c t
焊点可靠性研究详解

SMT焊点可靠性研究前言近几年﹐随着支配电子产品飞速发展的高新型微电子组装技术--表面组装技术(SMT)的飞速发展﹐SMT焊点可靠性问题成为普遍关注的焦点问题。
与通孔组装技术THT(Through Hole Technology)相比﹐SMT在焊点结构特征上存在着很大的差异。
THT焊点因为镀通孔内引线和导体铅焊后﹐填缝铅料为焊点提供了主要的机械强度和可靠性﹐镀通孔外缘的铅焊圆角形态不是影响焊点可靠性的主要因素﹐一般只需具有润湿良好的特征就可以被接受。
但在表面组装技术中﹐铅料的填缝尺寸相对较小﹐铅料的圆角(或称边堡)部分在焊点的电气和机械连接中起主要作用﹐焊点的可靠性与THT焊点相比要低得多﹐铅料圆角的凹凸形态将对焊点的可靠性产生重要影响。
另外﹐表面组装技术中大尺寸组件(如陶瓷芯片载体)与印制线路板的热膨胀系数相差较大﹐当温度升高时﹐这种热膨胀差必须全部由焊点来吸收。
如果温度超过铅料的使用温度范围﹐则在焊点处会产生很大的应力最终导致产品失效。
对于小尺寸组件﹐虽然因材料的CTE 失配而引起的焊点应力水平较低﹐但由于SnPb铅料在热循环条件下的粘性行为(蠕变和应力松弛)存在着蠕变损伤失效。
因此﹐焊点可靠性问题尤其是焊点的热循环失效问题是表面组装技术中丞待解决的重大课题。
80年代以来﹐随着电子产品集成水平的提高,各种形式﹑各种尺寸的电子封装器件不断推出﹐使得电子封装产品在设计﹑生产过程中,面临如何合理地选择焊盘图形﹑焊点铅料量以及如何保证焊点质量等问题。
同时﹐迅速变化的市场需求要求封装工艺的设计者们能快速对新产品的性能做出判断﹑对工艺参数的设置做出决策。
目前﹐在表面组装组件的封装和引线设计﹑焊盘图形设计﹑焊点铅料量的选择﹑焊点形态评定等方面尚未能形成合理统一的标准或规则﹐对工艺参数的选择﹑焊点性能的评价局限于通过大量的实验估测。
因此﹐迫切需要寻找一条方便有效的分析焊点可靠性的途径﹐有效地提高表面组装技术的设计﹑工艺水平。
微电子组装焊点可靠性及其铅污染问题的研究的开题报告
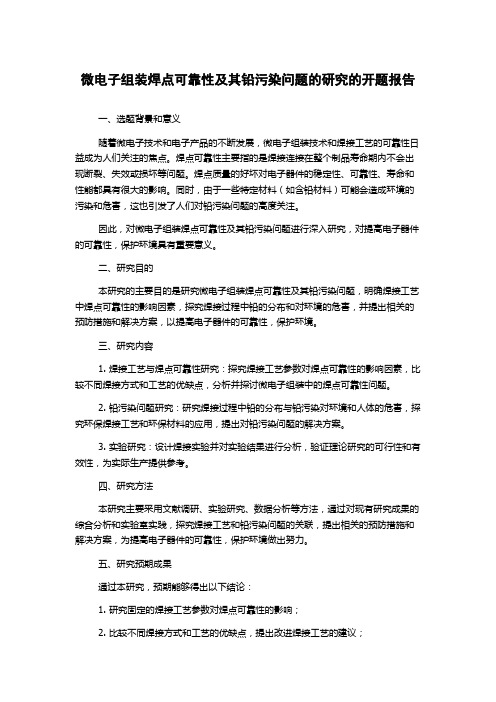
微电子组装焊点可靠性及其铅污染问题的研究的开题报告一、选题背景和意义随着微电子技术和电子产品的不断发展,微电子组装技术和焊接工艺的可靠性日益成为人们关注的焦点。
焊点可靠性主要指的是焊接连接在整个制品寿命期内不会出现断裂、失效或损坏等问题。
焊点质量的好坏对电子器件的稳定性、可靠性、寿命和性能都具有很大的影响。
同时,由于一些特定材料(如含铅材料)可能会造成环境的污染和危害,这也引发了人们对铅污染问题的高度关注。
因此,对微电子组装焊点可靠性及其铅污染问题进行深入研究,对提高电子器件的可靠性,保护环境具有重要意义。
二、研究目的本研究的主要目的是研究微电子组装焊点可靠性及其铅污染问题,明确焊接工艺中焊点可靠性的影响因素,探究焊接过程中铅的分布和对环境的危害,并提出相关的预防措施和解决方案,以提高电子器件的可靠性,保护环境。
三、研究内容1. 焊接工艺与焊点可靠性研究:探究焊接工艺参数对焊点可靠性的影响因素,比较不同焊接方式和工艺的优缺点,分析并探讨微电子组装中的焊点可靠性问题。
2. 铅污染问题研究:研究焊接过程中铅的分布与铅污染对环境和人体的危害,探究环保焊接工艺和环保材料的应用,提出对铅污染问题的解决方案。
3. 实验研究:设计焊接实验并对实验结果进行分析,验证理论研究的可行性和有效性,为实际生产提供参考。
四、研究方法本研究主要采用文献调研、实验研究、数据分析等方法,通过对现有研究成果的综合分析和实验室实践,探究焊接工艺和铅污染问题的关联,提出相关的预防措施和解决方案,为提高电子器件的可靠性,保护环境做出努力。
五、研究预期成果通过本研究,预期能够得出以下结论:1. 研究固定的焊接工艺参数对焊点可靠性的影响;2. 比较不同焊接方式和工艺的优缺点,提出改进焊接工艺的建议;3. 探究焊接过程中铅污染的分布;4. 分析铅污染对环境和人体的危害;5. 探究环保焊接工艺和环保材料的应用,提出对铅污染问题的解决方案。
六、论文框架1. 绪论2. 焊接工艺与焊点可靠性研究3. 铅污染问题研究4. 实验研究5. 结论与展望参考文献。
焊点可靠性分析技术要点
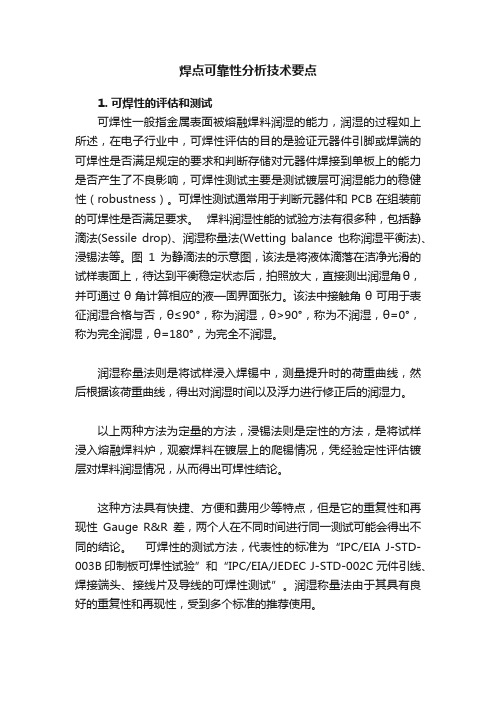
焊点可靠性分析技术要点1. 可焊性的评估和测试可焊性一般指金属表面被熔融焊料润湿的能力,润湿的过程如上所述,在电子行业中,可焊性评估的目的是验证元器件引脚或焊端的可焊性是否满足规定的要求和判断存储对元器件焊接到单板上的能力是否产生了不良影响,可焊性测试主要是测试镀层可润湿能力的稳健性(robustness)。
可焊性测试通常用于判断元器件和PCB在组装前的可焊性是否满足要求。
焊料润湿性能的试验方法有很多种,包括静滴法(Sessile drop)、润湿称量法(Wetting balance也称润湿平衡法)、浸锡法等。
图1为静滴法的示意图,该法是将液体滴落在洁净光滑的试样表面上,待达到平衡稳定状态后,拍照放大,直接测出润湿角θ,并可通过θ角计算相应的液—固界面张力。
该法中接触角θ可用于表征润湿合格与否,θ≤90°,称为润湿,θ>90°,称为不润湿,θ=0°,称为完全润湿,θ=180°,为完全不润湿。
润湿称量法则是将试样浸入焊锡中,测量提升时的荷重曲线,然后根据该荷重曲线,得出对润湿时间以及浮力进行修正后的润湿力。
以上两种方法为定量的方法,浸锡法则是定性的方法,是将试样浸入熔融焊料炉,观察焊料在镀层上的爬锡情况,凭经验定性评估镀层对焊料润湿情况,从而得出可焊性结论。
这种方法具有快捷、方便和费用少等特点,但是它的重复性和再现性Gauge R&R差,两个人在不同时间进行同一测试可能会得出不同的结论。
可焊性的测试方法,代表性的标准为“IPC/EIA J-STD-003B印制板可焊性试验”和“IPC/EIA/JEDEC J-STD-002C元件引线、焊接端头、接线片及导线的可焊性测试”。
润湿称量法由于其具有良好的重复性和再现性,受到多个标准的推荐使用。
影响可焊性的因素很多,主要有:焊料的合金组成、表面镀层(或者表面处理)、温度、助焊剂和时间等。
目前用于电子装配的焊料合金,主要以锡添加其它金属组成,添加的金属类型和量的比例,对润湿性能有很大影响。
- 1、下载文档前请自行甄别文档内容的完整性,平台不提供额外的编辑、内容补充、找答案等附加服务。
- 2、"仅部分预览"的文档,不可在线预览部分如存在完整性等问题,可反馈申请退款(可完整预览的文档不适用该条件!)。
- 3、如文档侵犯您的权益,请联系客服反馈,我们会尽快为您处理(人工客服工作时间:9:00-18:30)。
SMT焊点可靠性研究近几年,随着支配电子产品飞速发展的高新型微电子组装技术--表面组装技术(SMT)的飞速发展,SMT焊点可靠性问题成为普遍关注的焦点问题。
与通孔组装技术THT(Through Hole Technology)相比,SMT在焊点结构特征上存在着很大的差异。
THT焊点因为镀通孔内引线和导体铅焊后,填缝铅料为焊点提供了主要的机械强度和可靠性,镀通孔外缘的铅焊圆角形态不是影响焊点可靠性的主要因素,一般只需具有润湿良好的特征就可以被接受。
但在表面组装技术中,铅料的填缝尺寸相对较小,铅料的圆角(或称边堡)部分在焊点的电气和机械连接中起主要作用,焊点的可靠性与THT焊点相比要低得多,铅料圆角的凹凸形态将对焊点的可靠性产生重要影响。
另外,表面组装技术中大尺寸组件(如陶瓷芯片载体)与印制线路板的热膨胀系数相差较大,当温度升高时,这种热膨胀差必须全部由焊点来吸收。
如果温度超过铅料的使用温度范围,则在焊点处会产生很大的应力最终导致产品失效。
对于小尺寸组件,虽然因材料的CTE 失配而引起的焊点应力水平较低,但由于SnPb铅料在热循环条件下的粘性行为(蠕变和应力松弛)存在着蠕变损伤失效。
因此,焊点可靠性问题尤其是焊点的热循环失效问题是表面组装技术中丞待解决的重大课题。
80年代以来,随着电子产品集成水平的提高,各种形式、各种尺寸的电子封装器件不断推出,使得电子封装产品在设计、生产过程中,面临如何合理地选择焊盘图形、焊点铅料量以及如何保证焊点质量等问题。
同时,迅速变化的市场需求要求封装工艺的设计者们能快速对新产品的性能做出判断、对工艺参数的设置做出决策。
目前,在表面组装组件的封装和引线设计、焊盘图形设计、焊点铅料量的选择、焊点形态评定等方面尚未能形成合理统一的标准或规则,对工艺参数的选择、焊点性能的评价局限于通过大量的实验估测。
因此,迫切需要寻找一条方便有效的分析焊点可靠性的途径,有效地提高表面组装技术的设计、工艺水平。
研究表明,改善焊点形态是提高SMT焊点可靠性的重要途径。
90年代以来,关于焊点形成及焊点可靠性分析理论有大量文献报导。
然而,这些研究工作都是专业学者们针对焊点可靠性分析中的局部问题进行的,尚未形成系统的可靠性分析方法,使其在工程实践中的具体应用受到限制。
因此,基于设计和控制SMT焊点形态是提高SMT焊点可靠性的重要途径的思想,在进一步完善焊点形成及焊点可靠性分析理论基础上,实现了焊点工艺参数设计到焊点形态预测,直至焊点可靠性分析的集成过程,实现SMT焊点形态优化系统,并建立实用化SMT焊点形态优化设计系统,对于减少SMT产品决策实验工作量,提高决策效率和工艺设计水平,保证SMT焊点的可靠性具有重要的技术、经济意义。
1.1SMT及其焊点失效表面组装技术(Surface Mount Technology)简称SMT是通过再流焊、气相焊或波峰焊等软铅焊方法将电子组件贴装在印制板表面或基板上的微电子组装技术。
与传统封装形式相比,SMT具有体积小、重要轻、集成度高、可双面封装、易于实现自动化以及抗电磁干扰能力强等优点。
组装包括芯片内组装(如将芯片封装在基板上成为一个完整的表面组装组件)和芯片外组装(将表面组装组件或单一组件器件封装在印制板上)。
按照封装组件的类型,SMT包括无引线陶瓷芯片载体LCCC,方型扁平封装QFP以及球栅数组BGA等组装形式,如图1所示。
可见,在SMT封装产品中,焊点是关键的组成部分,既要承载电气畅通、又要承载机械连接,因此,提高焊点可靠性是保证SMT产品质量的关键。
SMT可靠性问题主要来自于生产组装过程和服役过程中。
在生产组装过程中,由于焊前准备,焊接过程及焊后检测等设备条件的限制,以及焊接规范选择的人为误差,常造成焊接故障,如虚焊、焊锡短路及曼哈顿现象等,约占SMT产品常见故障的85%,远高于其它故障如器件或印制板故障。
在实际工作中,SMT产品经常处于温度波动的服役环境中,如计算器内电子组装件经常经历通断电,电子组件和PCB板不断被加热和冷却,由于材料间热膨胀系数的差异,在焊点上必然产生热应力,应力的大小和方向会随着温度的变化而变化,而造成焊点的疲劳损伤,SnPb铅料的熔点较低,焊点会产生明显的粘性行为,即蠕变和应力松弛现象,Attarwala等人通过研究SnPb铅料断口形貌得出,失效焊点断口表面主要有表征疲劳断裂的疲劳裂纹和表征蠕变断裂的沿晶裂纹,说明焊点失效为蠕变--疲劳作用的结果。
SMT 焊点在服役条件下的可靠性问题,即在热循环或功率循环中,由于芯片载体与基板之间的热膨胀失配所导致的焊点的蠕变疲劳失效问题,是SMT 领域丞待解决的重要问题,下文所指的SMT焊点可靠性即为SMT焊点在服役条件下的可靠性。
1.2SMT焊点可靠性的影响因素研究表明,SMT焊点可靠性的影响因素主要有以下几个方面:1.材料因素裂纹的起裂与扩展是焊点失效的直接原因。
铅料的微观结构即铅料的组织结构、晶粒尺寸决定着铅料的变形机制、疲劳裂纹扩展机制,从而对焊点的可靠性有决定性影响。
如图2是改变铅料中Sn、Pb的配比所对应的不同铅料中含Sn量的增加,焊点疲劳寿命增加。
适当添加合金元素,如Ag、Sb、Re等可在保证铅料的熔点低、润湿性好,接头强度高等优点的前提下,提高铅料的抗蠕变一疲劳性能,改善焊点可靠性。
另外,由于组件与基板材料CTE不匹配导致焊点在热循环过程中产生应力集中,是导致焊点裂纹的萌生与扩展的本质因素,因此,研制开发展适当的基板材料,减小电子组件与基板的热膨胀系数差异,可抑制焊点的失效。
2.内部缺陷SMT 软铅焊接头因其微小的尺寸,复杂的焊接材料,产生缺陷的几率较大,主要有外观缺陷,如接头外型不良、引线间的桥接、芯吸等,以及内部缺陷,如气孔、有害金属间化合物、虚焊等。
这些缺陷的存在都对焊点的可靠性有致命的影响。
目前存在的焊点缺陷检测方法,很难检测尺寸本来就十分微小的SMT 焊点内部的更加微小的缺陷,因此,关于缺陷对SMT 焊点可靠性影响的理论研究少有文献报导。
哈工大微连接实验室初步研究了不同尺寸球状气孔对接头机械性能的影响,如图3,曲线 1 表示接头外边缘在线的最大应力峰值的变化,曲线2表示气孔周围主应力值的变化,可见,由于气孔的存在,SMT软铅焊接头的机械载强度明显下降。
3.服役条件SMT 产品的可靠性很大程度上决定于服役条件如,环境温度、周期性加载频率等。
Gregory等人模拟焊点热循环的疲劳过程,考察了温度、加载频率对焊点疲劳寿命的影响,结果表明,随着温度的增加,焊点应变范围增加,失效周期数降低。
随着加载频率增加,焊点疲劳寿命降低。
Tien等人的研究表明,焊点高温保温时间短,焊点内的应变恢复的多,将延长焊点疲劳寿命。
保持时间长,由于蠕变的作用,可恢复应变少,增加了焊点内部应变,寿命降低。
4•焊点形态SMT焊点形态即铅料受热熔化以后,沿金属表面润湿铺展冷凝后形成的具有一定几何形状的外观形态,狭义上,即铅料圆角的凹凸形态,研究表明,SMT焊点形态影响焊点机械性能、应力应变及蠕变疲劳寿命等。
如图4是W.M.Sherry等人对841/0非城堡型LCCC焊点的剪切性能在25C进行实验研究的结果。
表明,焊点形态不同,焊点的室温剪切性能不同, B 型焊点的室温剪切性能最好。
M.K.Shah等人假设焊点铅料圆角形态为直线,采用线弹性FEM分析了片式电容焊点在(T=100C)时的热应力。
结果表明,改变铅料圆角的高度、组件与基板的间隙高度以及组件在焊盘上的贴片位置,焊点的应力水平和分布状态不同。
E.Nicewarner对城堡型焊点热循环寿命的试验研究表明,焊点铅料圆角的差异可使焊点热循环寿命的差异达 6 . 5倍。
铅料圆角呈凸形时,焊点热循环寿命较高。
哈尔滨工业大学王国忠等人对同种类型焊点的研究结果为平直型焊点可靠性较好。
而R.W.Korb等人的研究指出,城堡型焊点铅料圆角的高度和长度大致相近时,焊点可靠性最好。
目前,焊点形态对可靠性的影响规律尚不清楚,有待于进一步完善。
1.3SMT焊点形态优化设计在上述影响SMT 焊点可靠性的因素中,焊点的服役条件一般是难以改变的,提高SMT 焊点可靠性主要从减少缺陷,开发新材料,改善焊点形态方面考虑。
其中,减少缺陷的研究因为焊点尺寸非常微小,需要高精度的检测设备,焊点分析的处理工艺复杂,按目前高精密检测仪器发展水平很难进行。
开发新材料即进行新型基板、材料的开发或新的铅料合金的设计,制造工艺复杂、价格昂贵,其实用性受到很大的限制。
而通过合理设计焊点结构参数、改善焊点形态可有效改善焊点的力学性能,从而提高焊点的可靠性。
目前,基于SMT焊点形态的焊点可靠性研究正方兴未艾。
1990年,美国Marquette大学的S.M.Heinrich等人提出了SMT焊点形态优化的计算器辅助设计思想,如图5所示。
设计者首先输入影响焊点形态的有关参数(如铅料量、组件尺寸、焊盘伸出长度以及组件与焊盘的间隙高度等),通过焊点形态预测模型计算出焊点形态,然后利用所得结果进行可靠性(如热循环下的应力、应变等)分析,获得焊点的疲劳寿命,再以焊点疲劳寿命为判断标准,反馈推出最佳的焊点形态,最佳的设计参数。
进行SMT焊点形态优化的计算器辅助设计,可以把关于焊点形成的数值仿真、焊点力学性能的有限元分析以及焊点疲劳寿命预测集成起来,形成一完整的SMT焊点形态优化体系。
应用于SMT工艺生产实践中,可以在产品投入组装前给予合理化建议,大大减少决策过程中的实验工作量,有效提高SMT焊点的可靠性能。
在国内外的有关文献中,尚未见关于SMT焊点形态优化的计算器辅助设计研究的完整报导。
2.1SMT焊点形态预测研究2.1.1SMT焊点形态建模基本方法精确预测焊点形态是SMT组装工艺的一项关键技术。
因为(1)可焊性测试(如润湿平衡实验)与焊点的几何形态密切相关;(2)导致低焊接生产率的接头缺陷,如桥连、断路等决定于焊点的形态;(3)焊点形态对服役条件下焊点的可靠性有重要影响。
焊点形态的研究开始于80年代,主要建模方法为求解边界值问题解法(简BVP,Boundary Volume Problem和数值分析方法。
其中,BVP法通过给定边界值约束条件,建立焊点成形的微分方程,求解出焊点形态。
BVP法预测结果精确,易于考察有关参数对焊点形态的影响规律。
但一般用于焊点形态简单,易于描述为数学微分方程的焊点类型。
数值分析方法,即通过有限元法(简称FEM,Finite Elements Method)求解满足相关约束条件的焊点三相系统能量的最小值,给出焊点形态。
FEM法预测结果是近似解,通过单元类型的选择和数目的增加逐渐精确。
FEM法可用于复杂焊点形态的求解中。
近些年来,随着SMT新型焊点的不断增加,焊点形态预测的研究取得了许多新的进展,BVP法和FEM法广泛应用于焊点二维形态模型、轴对称焊点形态模型及焊点三维形态模型中2.1.2焊点二维形态预测许多关于焊点二维形态的研究文献出现于1986~1993年间,其中,比较有代表性的是美国Marquette大学S.M.Heinrich等人的研究工作。