中油检测公司+油气管道检测与评价技术
油气管道缺陷无损检测与在线检测诊断技术的探析

油气管道缺陷无损检测与在线检测诊断技术的探析油气管道是石油天然气输送的重要通道,其安全可靠运行对于国家经济发展和能源供应有着重要的意义。
油气管道在长期运输过程中会受到各种外界因素的影响,从而产生各种缺陷。
这些缺陷如果不能及时检测和诊断,将会对管道的安全运行产生不利影响。
油气管道的无损检测和在线检测诊断技术的研究和应用对于保障管道安全运行至关重要。
一、油气管道的缺陷类型油气管道在运输过程中经常受到内部和外部因素的影响,从而产生各种缺陷。
常见的油气管道缺陷类型包括管道腐蚀、裂纹、焊接缺陷、磨损和腐蚀疲劳等。
这些缺陷如果不能及时发现和处理,将会对管道的安全运行产生重大隐患。
二、无损检测技术的应用无损检测技术是一种能够在不破坏被检测物体完整性的前提下检测物体内部结构和缺陷的技术。
针对油气管道的缺陷无损检测技术主要包括超声波检测、X射线探伤、涡流检测、磁粉探伤和电磁无损检测等。
超声波检测是利用超声波在材料内部的传播和反射来检测材料内部结构和缺陷的一种技术。
它可以对管道的厚度、腐蚀、裂纹等缺陷进行精密的检测,准确地确定缺陷的位置和大小。
X射线探伤是利用X射线能够透过材料并被不同程度吸收来检测材料内部结构和缺陷的一种技术。
它适用于检测管道的焊接缺陷、裂纹等。
涡流检测是一种利用涡流感应来检测管道表面裂纹和磨损的无损检测技术。
它具有检测速度快、效率高的特点。
电磁无损检测是一种利用电磁感应原理检测管道缺陷的技术,它可以用于管道的厚度测量和腐蚀检测。
以上这些无损检测技术的应用,为油气管道的安全运行提供了有力的技术支持。
通过无损检测技术可以及时、准确地发现管道的缺陷,从而及时采取修复措施,确保管道的安全运行。
三、在线检测诊断技术的发展随着科技的不断进步,油气管道的在线检测诊断技术也在不断得到发展和完善。
在线检测诊断技术主要包括智能传感器技术、远程监测技术和数据分析技术。
智能传感器技术是利用传感器对管道的各项运行参数和状态进行实时监测和诊断。
管道检测与评价技术知识讲解

7、SY/T 0063-1992 钢管防腐层检漏试验方法
6
8、SY/T 0379-1998 钢质管道煤焦油磁漆外防腐层技术标准 9、SY/T 6063-1994 埋地钢质管道防腐绝缘层电阻率现场测量技术规定 10、SY/T 6597-2004 钢质管道内检测技术规范 11、SY/T 0087-1995 钢质管道及储罐腐蚀与防护调查方法标准 12、SY/T 0443-1998 常压钢制焊接储罐及管道渗透检测技术标准 13、SY/T 4080-1995 管道、储罐渗漏检测方法 14、SY/T 5919-1994 埋地钢质管道干线电法保护技术管理规程 15、Q/SYJS 0054-2005 钢制管道内检测执行技术规范
➢ 检测结果很难用图表形式表示,缺陷的发现需要熟练的
操作技艺。
30
CIPS检测仪
CIPS: close interval potential survey 名称:密间隔电位测试 功能:主要用于测试阴极保护的有效性 检测仪器:加拿大阴极保护公司的DCVG/CIPS检测仪
31
阴极保护测试的传统方法
➢ 在埋地管线的阴极保护系统中,被保护的管道每间隔一定 的距离有一个管地电位的测试桩,是用导线与管体金属连 接,然后引到地面上,并做好与地的绝缘。
b、扩展应用 ➢ 评价防腐(保温)层的电气性能 ➢ 查找牺牲阳极埋设位置 ➢ 阴极保护系统故障检测
PCM管中电流检测仪的特点
防腐层漏点检测
防腐层等级评定
仪器功率强大150W、检测距离大
计算出防腐层绝缘电阻的大小
24
哈得管线外防腐层PCM检测现场
PCM检测结果:
➢ 哈得输油管线老线与新线的防 腐层防腐效果较好。全线的防 腐 层 平 均 电 阻 Rg 大 于 10.2 KΩ•m2 。 根 据 SY/T 00362000 , 煤 焦 油 瓷 漆 的 防 腐 层 绝缘电阻应不小于10 KΩ•m2。 据此标准,防腐层的防腐性能 综合等级可评定为优。
《2024年油气输送管道检测方法及安全评价》范文

《油气输送管道检测方法及安全评价》篇一一、引言随着油气工业的不断发展,油气输送管道的安全问题显得尤为重要。
油气输送管道作为能源运输的重要通道,其安全性和稳定性直接关系到国家经济命脉和人民生命财产安全。
因此,对油气输送管道进行定期检测和安全评价,是保障管道安全运行的重要措施。
本文将介绍油气输送管道的检测方法及安全评价,以期为相关领域的研究和应用提供参考。
二、油气输送管道检测方法(一)常规检测方法1. 视觉检测:通过人工巡检、无人机航测等方式,对管道外观进行检查,包括管道颜色、腐蚀情况、泄漏等。
2. 漏磁检测:利用磁场原理检测管道表面裂纹、凹陷等缺陷。
3. 超声波检测:利用超声波对管道内部进行检测,判断管道内部是否存在腐蚀、结垢等现象。
(二)特殊检测方法1. 智能检测:通过安装传感器等设备,实时监测管道的变形、应力、温度等参数,实现管道的智能监测。
2. 无损检测:采用射线、超声波等无损检测技术,对管道进行全面检测,以发现潜在的安全隐患。
3. 地质雷达检测:利用地质雷达技术对地下管道进行探测,了解管道周围地质环境的变化情况。
三、安全评价(一)定性评价定性评价主要是根据检测结果,对管道的安全状况进行评估。
通过对比管道设计参数、运行参数以及实际检测结果,判断管道是否存在安全隐患。
定性评价的结果通常以文字描述或图表形式呈现。
(二)定量评价定量评价是利用数学模型、软件算法等手段,对管道的安全状况进行量化评估。
通过建立管道的数学模型,分析管道在不同工况下的应力、变形等情况,从而判断管道的安全性能。
定量评价的结果通常以数值形式呈现,为制定针对性的安全措施提供依据。
四、安全措施与建议针对油气输送管道的检测和安全评价结果,提出以下安全措施与建议:1. 定期进行管道检测和安全评价,及时发现并处理潜在的安全隐患。
2. 加强管道巡检力度,提高人工巡检和智能巡检的结合程度,确保及时发现并处理问题。
3. 对老旧、腐蚀严重的管道进行更换或修复,提高管道的整体安全性。
油气集输管道外检测与风险评价要点分析

油气集输管道外检测与风险评价要点分析摘要:油气集输管道式油气输送的主要渠道,广泛应用到了各个油田的区块当中,作为油田生产的保障系统,为油田生产提供了有利条件,对于管道的外检测方法来说,指的是在不开挖的条件下,通过对埋地管道以及覆盖层的评价判断内部管道的腐蚀状况,然后根据实际情况提出有针对性的维护方法,降低各种管道事故发生的概率。
本篇文章就介绍了管道外检测方法以及风险评价的流程、方法和内容,提出了一系列提高外检测效率的方法,保证油田集输管道的安全运行。
关键词:油气集输管道;外检测;风险评价一、埋地管道外检测目前,随着我国油田建设的不断发展,尤其集输管道数量越来越多,随着这些管道使用时间的增加,管道老化问题日益严重,如果不可以对油气管道进行及时的检查,那么很可能发生各种管道事故,严重时会危及到周围群众的生命财产安全。
目前我国的管道检测方法有内检测、外检测和专项检测等等,但是在进行内检测时,由于管内结啦和管线变形极其容易造成管道堵塞,并且清理管道时,管内的原油没有办法存放,使得被油品污染的管道处理难度更大。
并且检测成本较高,而外检测方法可以随时随地检测管道外部的环境,不需要与管道那介质进行直接的接触,可以很大程度上提高检测的效果,是我国油气集输管道检测的常用方法之一。
1.资料调查与数据收集在展开外管保检测时,首先应该收集管道设计、安装和运行的相关资料,统计管道的介质腐蚀性、管道运行年限,判断管道是否适合采用外检测方法。
然后对管道运行的历史数据进行审查分析,记录管道防腐层破损的数量和面积,找出造成管道故障的原因所在。
根据以上测量的信息判断出管线地区等级以及风险管段,为管道的检测提供原始的数据。
除此之外,由于数据收集的完整性和准确性直接影响到检测的效果,因此在数据收集过程当中一定要满足管道分段的最少要求,及时将最新数据保存到管到数据库当中。
2.敷设环境调查辐射环境调查的主要内容指的是调查管道走向、位置以及埋线深度,统计管道周围的人口密度、公路和铁路数量、临近建筑物数量以及土地的地质情况,为后期的管道检测提供环境依据。
《油气输送管道检测方法及安全评价》
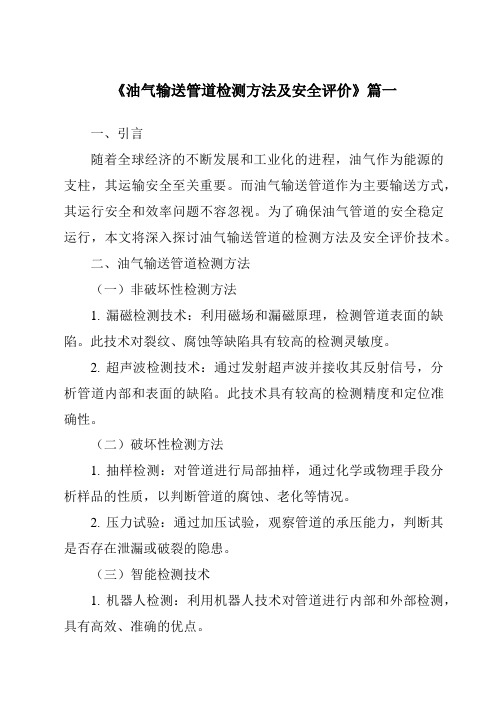
《油气输送管道检测方法及安全评价》篇一一、引言随着全球经济的不断发展和工业化的进程,油气作为能源的支柱,其运输安全至关重要。
而油气输送管道作为主要输送方式,其运行安全和效率问题不容忽视。
为了确保油气管道的安全稳定运行,本文将深入探讨油气输送管道的检测方法及安全评价技术。
二、油气输送管道检测方法(一)非破坏性检测方法1. 漏磁检测技术:利用磁场和漏磁原理,检测管道表面的缺陷。
此技术对裂纹、腐蚀等缺陷具有较高的检测灵敏度。
2. 超声波检测技术:通过发射超声波并接收其反射信号,分析管道内部和表面的缺陷。
此技术具有较高的检测精度和定位准确性。
(二)破坏性检测方法1. 抽样检测:对管道进行局部抽样,通过化学或物理手段分析样品的性质,以判断管道的腐蚀、老化等情况。
2. 压力试验:通过加压试验,观察管道的承压能力,判断其是否存在泄漏或破裂的隐患。
(三)智能检测技术1. 机器人检测:利用机器人技术对管道进行内部和外部检测,具有高效、准确的优点。
2. 无线传感器网络:通过在管道上布置无线传感器,实时监测管道的温度、压力、泄漏等参数,实现远程监控和预警。
三、安全评价技术(一)风险评估风险评估是安全评价的核心,通过对管道的运行环境、设备状况、管理情况等因素进行综合分析,评估管道发生事故的概率和后果严重程度。
常用的风险评估方法包括定性和定量评估。
(二)安全检查表与审核安全检查表是针对管道系统的各个部分和环节,列出可能存在的安全隐患和问题,进行逐项检查和评价。
而安全审核则是对管道的安全管理制度、操作规程等进行审查和评价。
(三)事故后果模拟与分析通过建立事故模型,对可能发生的事故进行模拟和分析,预测事故的发生概率和后果严重程度,为制定安全措施提供依据。
四、综合评价及应对措施综合运用各种检测方法和安全评价技术,对油气输送管道进行全面评价。
针对发现的问题和隐患,制定相应的应对措施,如加强巡检、提高检测频率、修复或更换设备等。
同时,还应加强管道的安全管理,提高员工的安全意识和技能水平,确保管道的安全稳定运行。
油田集输管道检测评价及修复技术导则
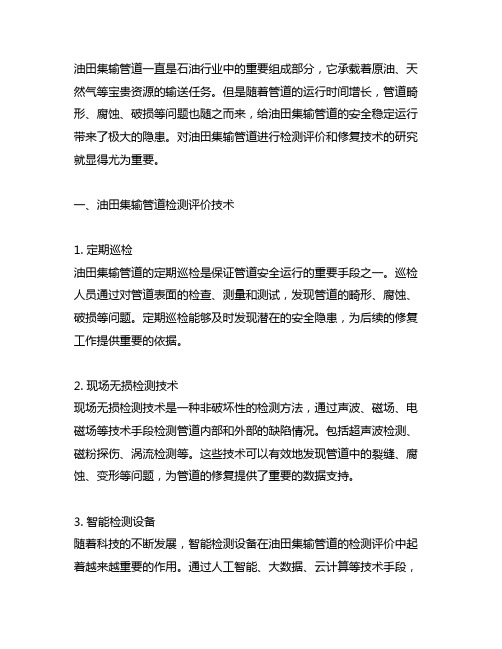
油田集输管道一直是石油行业中的重要组成部分,它承载着原油、天然气等宝贵资源的输送任务。
但是随着管道的运行时间增长,管道畸形、腐蚀、破损等问题也随之而来,给油田集输管道的安全稳定运行带来了极大的隐患。
对油田集输管道进行检测评价和修复技术的研究就显得尤为重要。
一、油田集输管道检测评价技术1. 定期巡检油田集输管道的定期巡检是保证管道安全运行的重要手段之一。
巡检人员通过对管道表面的检查、测量和测试,发现管道的畸形、腐蚀、破损等问题。
定期巡检能够及时发现潜在的安全隐患,为后续的修复工作提供重要的依据。
2. 现场无损检测技术现场无损检测技术是一种非破坏性的检测方法,通过声波、磁场、电磁场等技术手段检测管道内部和外部的缺陷情况。
包括超声波检测、磁粉探伤、涡流检测等。
这些技术可以有效地发现管道中的裂缝、腐蚀、变形等问题,为管道的修复提供了重要的数据支持。
3. 智能检测设备随着科技的不断发展,智能检测设备在油田集输管道的检测评价中起着越来越重要的作用。
通过人工智能、大数据、云计算等技术手段,可以实现对管道的全方位监测和实时预警。
智能检测设备可以大大提高管道检测的效率和准确性,为管道的安全运行提供了强有力的保障。
二、油田集输管道修复技术1. 管道腐蚀修复腐蚀是油田集输管道面临的重要问题,其修复工作至关重要。
常见的修复方法包括焊接修复、涂层修复、局部更换等。
通过对腐蚀部位进行修复,可以使管道重新恢复其强度和密封性。
2. 管道畸形修复管道的畸形会导致管道的受力不均匀,从而影响管道的安全运行。
常用的修复方法包括冷弯修复、热处理修复等。
通过对畸形部位进行修复,可以有效地恢复管道的原有形状和功能。
3. 管道破损修复管道的破损往往是由外部力量导致的,例如机械损伤、地质灾害等。
常见的修复方法包括局部更换、补焊修复等。
通过对破损部位进行修复,可以使管道重新恢复其完整性和稳定性。
三、油田集输管道检测评价及修复技术的发展趋势1. 智能化未来油田集输管道的检测评价和修复技术将趋向智能化,更加依靠人工智能和大数据技术,实现对管道的全方位监测和预警。
油气管道缺陷无损检测与在线检测诊断技术的探析

油气管道缺陷无损检测与在线检测诊断技术的探析油气管道是石油、天然气等能源资源的重要输送通道,对于国家能源安全和经济发展具有重要意义。
油气管道在长期使用过程中难免会出现各种缺陷,这些缺陷可能会导致管道泄漏、爆炸等严重事故,给人民生命财产安全带来巨大风险。
油气管道的无损检测与在线检测诊断技术显得尤为重要。
本文将从油气管道的缺陷特点、无损检测技术及在线检测诊断技术等方面对该问题进行探讨。
一、油气管道缺陷特点油气管道缺陷主要包括内外腐蚀、焊接缺陷、应力腐蚀开裂、管道内结垢等。
这些缺陷在管道长期运行中会逐渐加剧,导致管道壁厚度减薄、管道内部压力承载能力下降,甚至引发管道泄露或爆炸事故。
内外腐蚀是油气管道常见的缺陷,其特点是发展速度缓慢但难以察觉,一旦蔓延到一定程度就会对管道的安全性造成严重影响。
焊接缺陷主要由于焊接时的操作不当、焊缝质量不良等原因导致,这种缺陷在管道使用过程中易发生破裂。
应力腐蚀开裂是由于管道受到应力和介质腐蚀的共同作用引起的,这种缺陷常常发生在管道接头和焊缝处。
管道内结垢会导致介质流通不畅,增加管道的阻力,加剧腐蚀速度,最终导致管道破裂。
由于油气管道运行环境的特殊性,其缺陷检测难度较大,因此需要借助先进的无损检测技术和在线检测诊断技术来保障管道的安全运行。
二、无损检测技术无损检测技术是指在不破坏被测体的情况下对被测体进行检测和评价的技术手段。
在油气管道的无损检测中,常用的技术包括超声波检测、磁粉探伤、液态渗透检测、射线检测等。
超声波检测是常用的一种无损检测技术,其原理是利用超声波在材料中传播的特性来检测材料内部的缺陷。
超声波可以穿透材料并在缺陷处发生反射或衍射,通过接收回波信号来判断缺陷的位置、大小和形状。
磁粉探伤是利用磁粉检测剂在磁场作用下检测材料表面和亚表面的缺陷,其原理是磁粉在磁场下会聚集在缺陷处形成磁粉斑。
液态渗透检测是利用液态渗透剂的渗透性来检测材料表面裂纹、开裂等表面缺陷。
射线检测是利用射线照射被测体,通过检测射线透过被测体后的衰减情况来判断材料的内部缺陷。
《2024年油气输送管道检测方法及安全评价》范文
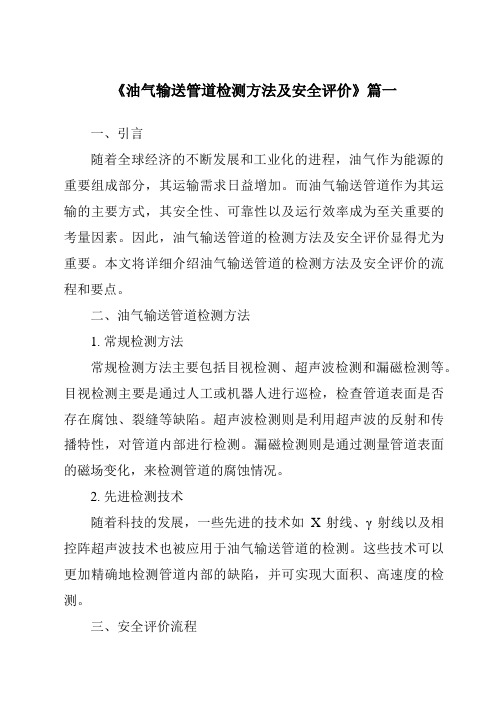
《油气输送管道检测方法及安全评价》篇一一、引言随着全球经济的不断发展和工业化的进程,油气作为能源的重要组成部分,其运输需求日益增加。
而油气输送管道作为其运输的主要方式,其安全性、可靠性以及运行效率成为至关重要的考量因素。
因此,油气输送管道的检测方法及安全评价显得尤为重要。
本文将详细介绍油气输送管道的检测方法及安全评价的流程和要点。
二、油气输送管道检测方法1. 常规检测方法常规检测方法主要包括目视检测、超声波检测和漏磁检测等。
目视检测主要是通过人工或机器人进行巡检,检查管道表面是否存在腐蚀、裂缝等缺陷。
超声波检测则是利用超声波的反射和传播特性,对管道内部进行检测。
漏磁检测则是通过测量管道表面的磁场变化,来检测管道的腐蚀情况。
2. 先进检测技术随着科技的发展,一些先进的技术如X射线、γ射线以及相控阵超声波技术也被应用于油气输送管道的检测。
这些技术可以更加精确地检测管道内部的缺陷,并可实现大面积、高速度的检测。
三、安全评价流程1. 收集数据首先,需要收集管道的基本信息,如管道的材质、规格、运行时间等。
同时,还需要收集管道的检测数据,如腐蚀深度、裂纹长度等。
2. 风险评估根据收集的数据,对管道进行风险评估。
风险评估主要包括对管道的腐蚀、裂纹等缺陷进行定性和定量分析,评估其对管道安全的影响程度。
3. 安全评价根据风险评估的结果,对管道进行安全评价。
安全评价主要包括对管道的整体安全性能进行评价,确定其是否满足运行要求。
四、安全评价要点1. 定期检测与维护定期对油气输送管道进行检测和维护是保证其安全性的重要措施。
通过定期检测,可以及时发现并处理管道的缺陷和问题,防止事故的发生。
2. 科学的风险评估方法科学的风险评估方法是保证安全评价准确性的关键。
应采用先进的风险评估方法和技术,对管道的缺陷和问题进行定性和定量分析,准确评估其对管道安全的影响程度。
3. 综合评价与决策支持综合评价与决策支持是安全评价的重要环节。
- 1、下载文档前请自行甄别文档内容的完整性,平台不提供额外的编辑、内容补充、找答案等附加服务。
- 2、"仅部分预览"的文档,不可在线预览部分如存在完整性等问题,可反馈申请退款(可完整预览的文档不适用该条件!)。
- 3、如文档侵犯您的权益,请联系客服反馈,我们会尽快为您处理(人工客服工作时间:9:00-18:30)。
中油管道检测技术有限责任公司油气管道检测与评价技术中油管道检测技术有限责任公司2017年01月中油管道检测技术有限责任公司ü 中油管道检测技术有限责任公司隶属于中国石油天然气管道局;ü 成立于1992年;ü 国内最早从事管道检测及安全评价的专业化公司;ü 2000年成为国家安监局指定的管道检测单位;ü 2011年获得国家质监总局颁发的综合检验机构甲类资质证书;ü 拥有国家油气管道检测工程实验室。
CPPI综合检验机构甲类资质证书(甲类为国家级)工业清洗A级资质证书质量管理体系及HSE认证国际专业机构认证壳牌及道达尔全球供应商资格及penspen会员资格6检测公司现有外检测设备总览埋地管道外防腐层及阴保检测管道河流穿越埋深检测储罐检测埋地管线防腐蚀层测试仪-DM 存储式杂散电流监测仪-HC069管道电流测绘仪- PCM Plus电火花检漏仪密间隔管地电位检测仪-CIPS土壤电阻测试仪ZC-8储罐底板腐蚀自动扫描绘图系统真空试漏仪声发射系统超声波探伤仪管道河流穿越埋深检测系统—ONEPASS管道河流穿越埋深检测系统—ONEPASS管道河流穿越埋深检测系统—ONEPASS管道河流穿越埋深检测系统—ONEPASS变形检测器高清漏磁检测器2198inch 27310inch 32312inch 35514inch 377 40616inch三轴漏磁检测器验收检测器1686inch 清管器325 1144inch 口径(mm)(inch)42650820inch45718inch 52955922inch检测公司现有内检测设备总览拥有6-56英寸系列智能内检测设备。
61024inch 66026inch 71128inch72081332inch 91436inch 101640inch 121948inch 106742inch 76230inch 86434inch 96538inch 142256inch变形检测器高清漏磁检测器三轴漏磁检测器验收检测器清管器口径(mm)(inch)可变径检测器复合检测器检测公司现有内检测设备总览ü 2009年研制国内首台三轴检测器。
ü 2002年研制国内首台高清检测器。
数据分析专家系统变形分析软件用户化报告软件惯性导航数据处理软件含缺陷管道完整性评价软件管道完整性管理系统检测公司拥有的软件一• 管道检测技术介绍二• 检测在完整性管理中应用三• 管道完整性评价内 容中油管道检测技术有限责任公司一• 管道检测技术介绍二• 检测在完整性管理中应用三• 管道完整性评价内 容外腐蚀、内腐蚀、应力腐蚀裂纹(第三方)施工、打孔盗油(气)、恶意破坏材料缺陷、制造缺陷、焊接缺陷变形滑坡、泥石流、水毁、地质沉降1 埋地管道存在的威胁穿孔泄漏破裂1 埋地管道存在的威胁能源损失污染环境火灾爆炸•••1 埋地管道存在的威胁1 埋地管道存在的威胁管道•威胁•检测•发现缺陷•评价•维修监控•再捡测 人 •各类疾病•仪器检查•发现疾病•会诊•手术或定期检查•再次检查1 埋地管道存在的威胁管道•威胁•检测•发现缺陷•评价•维修监控•再检测 人 •各类疾病•仪器检查•发现疾病•会诊•手术或定期检查•再次检查1 埋地管道存在的威胁管道•威胁•检测•发现缺陷•评价•维修监控•再捡测 人 •各类疾病•仪器检查•发现疾病•会诊•手术或定期检查•再次检查检测及评价技术生命周期内的管道医生2 检测技术检测技术外检测技术内检测技术3 外检测技术1)站场无损检测Ø站场压力容器、储罐腐蚀检测Ø站场生产工艺设施的外部检测Ø站场、阀室内工艺管线的检测2)埋地管道外防腐层状况检测与评估Ø土壤腐蚀性检测Ø杂散电流测试Ø杂散电流干扰电位测试Ø外防腐层破损精确定位Ø外防腐层安全质量状况评估Ø阴极保护系统评价3 外检测技术3)管道河流穿越埋深检测Ø确定管线水平和垂直坐标Ø确定水深及管线在河床下的埋深Ø形成河流穿越段平面图和剖面图4)储罐检测服务Ø提供储罐各部位详细的检测结果Ø提供维修建议Ø储罐综合评价5)管道、储罐阴极保护的设计与安装Ø钢制管道和储罐阴极保护系统检测Ø钢制管道和储罐阴极保护系统现场安装服务4 管道内检测利用管道内运行的可实时采集并记录管道信息的检测器所完成的检测,也称之管道智能检测。
管道可检性收发球筒管道物理特征:三通、弯头、阀门、外部干扰装置等管道运行条件:温度、压力、运行速度卡堵 卡堵 卡堵 卡堵 卡堵 卡堵 卡堵4 管道内检测检测器类型清管器泡沫清管器 皮碗清管器钢刷清管器 磁力清管器变形检测器在役变形检测器投产前验收检测器金属损失检测器漏磁检测器(轴向、横向、旋转)超声检测器裂纹检测器EMAT 超声检测器特殊需求检测器变径检测器复合检测器5 管道检测器分类泡沫清管器•对于长期未进行清管作业或情况较复杂的管道首次进行清管作业,采用该类型清管器。
皮碗清管器•清除一般杂质,并可加装测径板。
钢刷清管器•用来清除附着在管壁上的硬垢,如铁锈、沉积物等杂质。
磁力清管器•主要是将管道中影响漏磁检测的铁磁性杂质清出。
6 主要内检测技术 — 清管管道清管可以有效的清除管道中存在的污物及杂质,提高管道输送效率,确保管道安全运行。
目前使用的高精度多通道变形检测器,可对在役和投产前管道进行变形检测,能检测发现管道凹陷、椭圆度、褶皱及其三维尺寸、位置。
也可检测到管道内径变化、管道附件如,阀门、三通、法兰、弯头、弯管、管道长度及壁厚变化等信息。
•• • •6 主要内检测技术 — 变形检测漏磁检测可实时检测并记录管道金属本体上的金属损失缺陷,包括:腐蚀、机械损伤、制造缺陷、焊缝异常;管道上的附件:套管、补丁、阀门、三通、弯头;管道非正常开孔、管道壁厚变化、焊缝、外接金属物、维修套筒等。
并能确定缺陷、特征的尺寸及精确位置。
腐蚀信号图腐蚀信号图现场开挖图片6 主要内检测技术 — 三轴漏磁检测6 主要内检测技术 —横向励磁检测能够检测出轴向狭长型缺陷,如沟槽、裂纹,是轴向漏磁检测技术的有效补充。
电磁超声裂纹检测技术(EMAT)用于检测输气管道的应力腐蚀裂纹(SCC)。
6 主要内检测技术 — 裂纹检测可变径检测器通过能力较强,能够适应2到3种口径的管道检测。
同时也满足一个检测段中有两种不同口径的变径管道检测。
6 主要内检测技术 — 可变径检测利用压电超声传感器激励、接收超声波信号。
通过分析反射回波信息可以精确的对各种腐蚀、裂纹缺陷进行检测和量化。
优点:主动检测、检测精度高、量化可信度高。
缺点:需要耦合剂、技术难度较高。
6 主要内检测技术 — 压电超声检测复合检测器是指将多种检测功能复合到一台检测器上,如,将三轴漏磁检测、高精度变形检测、管道壁厚测量、管道弯头角度测量等功能进行集成,实现一次检测,获取多种数据。
6 主要内检测技术 — 复合检测搭载在管道内检测器上的惯性测绘单元,结合地面GPS测量坐标,能精确地描绘管道中心线三维走向。
高精度的管道测绘系统6 主要内检测技术 — 走向检测通过使用专业的Mapping数据分析处理软件,对惯性测绘单元获得的角速度、加速度、里程数据进行处理分析,识别出由于环境等因素诱发的管道弯曲变形区域,分析计算管道各点曲率及弯曲应变,这是管道内检测领域开展管道应变分析所采用的一种全新的技术手段。
6 主要内检测技术 — 走向检测中油管道检测技术有限责任公司一• 管道检测技术介绍二• 检测在完整性管理中应用三• 管道完整性评价内 容1 管道内检测数据成果腐蚀信号图腐蚀信号图现场开挖图片1 管道内检测数据成果制造缺陷1 管道内检测数据成果机械损伤1 管道内检测数据成果焊缝异常1 管道内检测数据成果漏磁检测发现的变形1 管道内检测数据成果智能测径发现的变形2 在完整性管理中的贡献完整性管理的重要数据来源金属损失检测:能较全面的检测管道在制管、建造、运营期间产生的缺陷。
裂纹检测:超声波或电磁超声检测技术可以检测管道和焊缝上的裂纹。
智能测径:检测管道中存在的凹陷、褶皱、管体不圆等变形缺陷。
搭载mapping 系统的内检测能够检测或完善管道走向信息。
3 不同阶段的管道内检测投产前检测基线检测再次检测投产前管道变形内检测管道施工建设投产前管道内检测降低管道运营风险投产前管道变形内检测ü凹陷主要位于管道底部,系施工质量控制不严格导致的管底硬物对管道挤压造成的。
ü管道4为途径山区地段的管道,在104公里的管道上检测到深度大于5%OD的凹陷97处,最深的凹陷达到14%OD。
投产前管道变形内检测投产前管道腐蚀检测明确管道存在的附件发现管道制造、施工过程遗留的缺陷查明焊缝缺陷,确认焊缝是否存在问题检测管道存在变形情况是管道施工建设验收的有效补充为管道建立原始数据档案满足管道完整性管理的要求管道投产运营后进行的首次检测称之为基线检测,通过实施基线检测可以:管道基线检测较基线检测,实施再次检测的管道获得的信息更详细,并且通过两检测数据的对比,可以实现:缺陷存在类型确认确认管道中存在的腐蚀缺陷(活性点)确认腐蚀增长速率,制定维修缺陷计划补口、高后果区等区域的缺陷数据对比分析确认新发生的凹陷及缺陷,考虑第三方破坏的影响管道周期性检测中油管道检测技术有限责任公司一• 管道检测技术介绍二• 检测在完整性管理中应用三• 管道完整性评价内 容中油管道检测技术有限责任公司三、管道完整性评价检测技术完整性评价查找缺陷方法 评判缺陷严重性的手段。