制程失效模式与效应分析FMEA的运用
失效模式与效应分析在预防眼科患儿跌倒中的应用效果
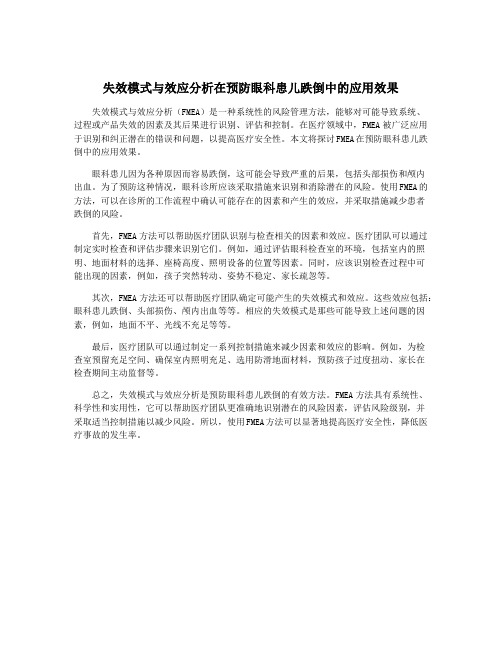
失效模式与效应分析在预防眼科患儿跌倒中的应用效果失效模式与效应分析(FMEA)是一种系统性的风险管理方法,能够对可能导致系统、过程或产品失效的因素及其后果进行识别、评估和控制。
在医疗领域中,FMEA被广泛应用于识别和纠正潜在的错误和问题,以提高医疗安全性。
本文将探讨FMEA在预防眼科患儿跌倒中的应用效果。
眼科患儿因为各种原因而容易跌倒,这可能会导致严重的后果,包括头部损伤和颅内出血。
为了预防这种情况,眼科诊所应该采取措施来识别和消除潜在的风险。
使用FMEA的方法,可以在诊所的工作流程中确认可能存在的因素和产生的效应,并采取措施减少患者跌倒的风险。
首先,FMEA方法可以帮助医疗团队识别与检查相关的因素和效应。
医疗团队可以通过制定实时检查和评估步骤来识别它们。
例如,通过评估眼科检查室的环境,包括室内的照明、地面材料的选择、座椅高度、照明设备的位置等因素。
同时,应该识别检查过程中可能出现的因素,例如,孩子突然转动、姿势不稳定、家长疏忽等。
其次,FMEA方法还可以帮助医疗团队确定可能产生的失效模式和效应。
这些效应包括:眼科患儿跌倒、头部损伤、颅内出血等等。
相应的失效模式是那些可能导致上述问题的因素,例如,地面不平、光线不充足等等。
最后,医疗团队可以通过制定一系列控制措施来减少因素和效应的影响。
例如,为检查室预留充足空间、确保室内照明充足、选用防滑地面材料,预防孩子过度扭动、家长在检查期间主动监督等。
总之,失效模式与效应分析是预防眼科患儿跌倒的有效方法。
FMEA方法具有系统性、科学性和实用性,它可以帮助医疗团队更准确地识别潜在的风险因素,评估风险级别,并采取适当控制措施以减少风险。
所以,使用FMEA方法可以显著地提高医疗安全性,降低医疗事故的发生率。
FMEA失效模式和效应分析

1 of 19項 目:過程責任:生產準備者:部 門:制一部零件號:關鍵日期:FMEA 日期:中心隊員:FMEA 編號: 0606242 of 19項 目:過程責任:生產準備者:部 門:制一部零件號:關鍵日期:FMEA 日期:中心隊員:FMEA 編號: 0606243 of 19項 目:過程責任:生產準備者:部 門:制一部零件號:關鍵日期:FMEA 日期:中心隊員:FMEA 編號: 0606244 of 19項 目:過程責任:生產準備者:部 門:制一部零件號:關鍵日期:FMEA 日期:中心隊員:FMEA 編號: 0606245 of 19項 目:過程責任:生產準備者:部 門:制一部零件號:關鍵日期:FMEA 日期:中心隊員:FMEA 編號: 0606246 of 19項 目:過程責任:生產準備者:部 門:制一部零件號:關鍵日期:FMEA 日期:中心隊員:FMEA 編號: 0606247 of 19項 目:過程責任:生產準備者:部 門:制一部零件號:關鍵日期:FMEA 日期:中心隊員:FMEA 編號: 0606248 of 19項 目:過程責任:生產準備者:部 門:制一部零件號:關鍵日期:FMEA 日期:中心隊員:FMEA 編號: 0606249 of 19項 目:過程責任:生產準備者:部 門:制一部零件號:關鍵日期:FMEA 日期:中心隊員:FMEA 編號: 06062410 of 19項 目:過程責任:生產準備者:部 門:制一部零件號:關鍵日期:FMEA 日期:中心隊員:FMEA 編號: 06062411 of 19項 目:過程責任:生產準備者:部 門:制一部零件號:關鍵日期:FMEA 日期:中心隊員:FMEA 編號: 06062412 of 19項 目:過程責任:生產準備者:部 門:制一部零件號:關鍵日期:FMEA 日期:中心隊員:FMEA 編號: 06062413 of 19項 目:過程責任:生產準備者:部 門:制一部零件號:關鍵日期:FMEA 日期:中心隊員:FMEA 編號: 06062414 of 19項 目:過程責任:生產準備者:部 門:制一部零件號:關鍵日期:FMEA 日期:中心隊員:FMEA 編號: 06062415 of 19項 目:過程責任:生產準備者:部 門:制一部零件號:關鍵日期:FMEA 日期:中心隊員:FMEA 編號: 06062416 of 19項 目:過程責任:生產準備者:部 門:制一部零件號:關鍵日期:FMEA 日期:中心隊員:FMEA 編號: 06062417 of 19項 目:過程責任:生產準備者:部 門:制一部零件號:關鍵日期:FMEA 日期:中心隊員:FMEA 編號: 06062418 of 19項 目:過程責任:生產準備者:部 門:制一部零件號:關鍵日期:FMEA 日期:中心隊員:FMEA 編號: 06062419 of 19項 目:過程責任:生產準備者:部 門:制一部零件號:關鍵日期:FMEA 日期:中心隊員:FMEA 編號: 060624。
失效模式与效应分析程序FMEA资料
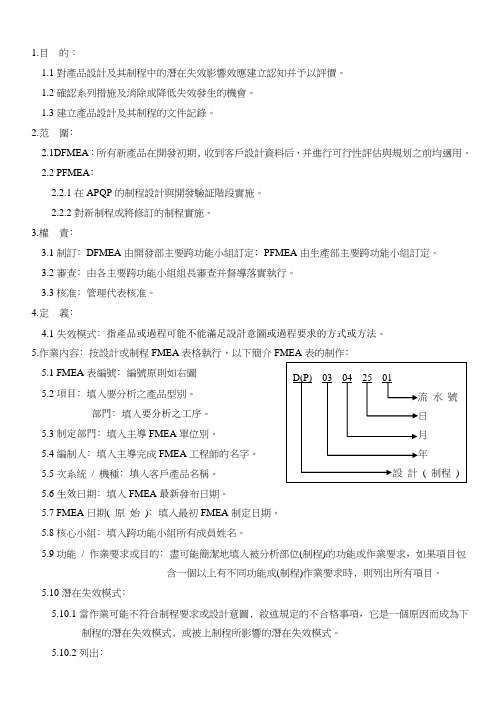
1.目的:1.1對產品設計及其制程中的潛在失效影響效應建立認知并予以評價。
1.2確認系列措施及消除或降低失效發生的機會。
1.3建立產品設計及其制程的文件記錄。
2.范圍﹕2.1DFMEA:所有新產品在開發初期﹐收到客戶設計資料后,并進行可行性評估與規划之前均適用。
2.2 PFMEA﹕2.2.1在APQP的制程設計與開發驗証階段實施。
2.2.2對新制程或將修訂的制程實施。
3.權責﹕3.1制訂﹕DFMEA由開發部主要跨功能小組訂定﹔PFMEA由生產部主要跨功能小組訂定。
3.2審查﹕由各主要跨功能小組組長審查并督導落實執行。
3.3核准﹕管理代表核准。
4.定義﹕4.1失效模式﹕指產品或過程可能不能滿足設計意圖或過程要求的方式或方法。
5.作業內容﹕按設計或制程FMEA表格執行,以下簡介FMEA表的制作﹕5.2項目﹕填入要分析之產品型別。
部門﹕填入要分析之工序。
5.3制定部門﹕填入主導FMEA單位別。
5.4編制人﹕填入主導完成FMEA工程師的名字。
5.5次系統/ 機種﹕填入客戶產品名稱。
5.6生效日期﹕填入FMEA最新發布日期。
5.7 FMEA日期( 原始)﹕填入最初FMEA制定日期。
5.8核心小組﹕填入跨功能小組所有成員姓名。
5.9功能/ 作業要求或目的﹕盡可能簡潔地填入被分析部位(制程)的功能或作業要求,如果項目包含一個以上有不同功能或(制程)作業要求時﹐則列出所有項目。
5.10潛在失效模式﹕5.10.1當作業可能不符合制程要求或設計意圖﹐敘述規定的不合格事項,它是一個原因而成為下制程的潛在失效模式﹐或被上制程所影響的潛在失效模式。
5.10.2列出﹕5.10.2.1每一潛在失效模式假設失效是將發生的﹐但不是必須發生的。
5.10.2.2盡可能敘述失效模式發生于某些作業條件下(如﹕壓力等)和在某些使用條件下(如﹕溫度,高度)。
5.10.2.3一般失效模式含如下各項﹐但不限于此﹕破損、變形、碰傷、錯位、裂紋等。
失效模式和效果分析FMEA在制药行业的应用教材

失效模式和效果分析FMEA在制药行业的应用教材失效模式与效应分析(Failure Mode and Effects Analysis, FMEA)是一种常用的质量管理工具,它可以帮助制药行业发现潜在的问题,预防和减少产品质量问题的发生,从而提高产品质量和安全性。
本文将探讨FMEA在制药行业的应用,并分析其效果。
FMEA的基本原理是通过识别潜在的失效模式,并分析这些失效模式可能引起的效应,进而制定合适的预防和纠正措施。
在制药行业,FMEA通常用于产品开发、生产过程和设备维护等环节。
下面将详细介绍FMEA在这些环节的应用。
首先,FMEA在制药产品开发阶段起到了重要的作用。
制药产品的设计失效可能导致产品质量问题和安全隐患。
通过应用FMEA,可以对设计过程中潜在的失效模式进行识别和评估,并制定相应的改进方案。
例如,通过对产品配方进行FMEA分析,可以找出可能导致配方不稳定的因素,如不合适的原材料、配方比例不当等。
这样可以在产品设计阶段及时进行调整,避免质量问题的发生。
其次,FMEA在制药生产过程中的应用也十分重要。
生产过程中的失效可能导致产品质量不稳定和生产效率降低。
通过应用FMEA,可以识别和评估生产过程中的潜在失效模式,并设计相应的控制措施。
例如,在制药生产过程中,可能存在温度控制失效、搅拌不均匀等问题。
通过应用FMEA,可以定位这些问题的发生原因,并制定相应的控制措施,比如使用更精确的温度控制设备、改进搅拌工艺等。
此外,FMEA还可以应用于制药设备的维护管理。
设备故障可能导致生产中断和质量问题。
通过应用FMEA,可以识别设备故障的潜在失效模式,并制定相应的预防和纠正措施。
例如,对于关键设备,可以制定定期保养计划,定期更换易损件,增加备件库存等。
通过这些措施,可以降低设备故障的概率,保证生产的稳定性和质量。
FMEA作为一种质量管理工具,在制药行业的应用具有一定的优势和效果。
首先,通过FMEA可以对潜在的失效模式进行全面、系统的分析。
风险评估技术-失效模式和效应分析(FMEA)及失效模式、效应和危害度分析(FMECA)

失效模式和效应分析(FMEA及失效模式、效应和危害度分析(FMECA)1 概述失效模式和效应分析(Failure Mode and Effect Analysis ,简称FMEA)是用来识别组件或系统未能达到其设计意图的方法。
FMEA 用于识别:•系统各部分所有潜在的失效模式(失效模式是被观察到的是失误或操作不当);•这些故障对系统的影响;• 故障原因;• 如何避免故障及 /或减弱故障对系统的影响。
失效模式、效应和危害度分析(Failure Mode and Effect and Criticality Analysis ,简称 FMECA)拓展了 FMEA 的使用范围。
根据其重要性和危害程度,FMECA 可对每种被识别的失效模式进行排序。
这种分析通常是定性或半定量的,但是使用实际故障率也可以定量化。
2 用途FMEA 有几种应用:用于部件和产品的设计(或产品) FM EA ;用于系统的系统FMEA ;用于制造和组装过程的过程 FMEA ;服务FMEA和软件FMEA。
FMEA/ FMECA 可以在系统的设计、制造或运行过程中使用。
然而,为了提高可靠性,改进在设计阶段更容易实施。
FMEA/ FMECA 也适用于过程和程序。
例如,它被用来识别潜在医疗保健系统中的错误和维修程序中的失败。
FMEA/FMECA 可用来:•协助挑选具有高可靠性的替代性设计方案;•确保所有的失效模式及其对运行成功的影响得到分析;•列出潜在的故障并识别其影响的严重性;•为测试及维修工作的规划提供依据;• 为定量的可靠性及可用性分析提供依据。
它大多用于实体系统中的组件故障,但是也可以用来识别人为失效模式及影响。
FMEA 及 FMECA 可以为其他分析技术,例如定性及定量的故障树分析提供输入数据。
3 输入数据FMEA 及 FMECA 需要有关系统组件足够详细的信息,以便对各组件出现故障的方式进行有意义的分析。
信息可能包括:• 正在分析的系统及系统组件的图形,或者过程步骤的流程图;• 了解过程中每一步或系统组成部分的功能;• 可能影响运行的过程及环境参数的详细信息;• 对特定故障结果的了解;• 有关故障的历史信息,包括现有的故障率数据。
FMEA失效模式与效应分析

检查并确认顾客需求
仔细考虑什么是 主要关键的过程
使用RPN指针及相关信息 决定关键特性 对关键特性 发展合适的管制机制
仔细考虑 每一阶段之管制计划 prototype pre-launch production
13
一、FMEA 的基本概念
FMEA 之 功 用 阶 段 功 用
1.设计时间
1.发掘所有可能之失效模式
”早知道 ……… 就不会 ”
早知道 作好机场安检 就不会 造成 911美国国难 早知道 改进防洪排水设计 就不会 造成全台大淹水 早知道 不滥垦滥伐 就不会 造成土石流 早知道 作好桥梁维护 就不会 造成高屏大桥倒塌
有些 早知道 是必需的!有些 就不会 是不允许发生的
核能电厂、水库、卫星、飞机…….
9
一、FMEA 的基本概念
有失效 是客户看到 而我们却没见到吗?
客户看的 失效 和我们相同吗?
客户对 失效的看法 和我们相同吗?
想想看 光驱及遥控鼠标 有没有
思考看看为什么? ?
10
一、FMEA 的基本概念
典型车辆工业开发三步骤
APQP Timeline
过程流程图 (包含所有流程) 由APQP程序启动过程 有些要素可能含在 设计FMEA (包含所有流程)
2. 顾客需求 : 可被规范及被量测 思考所需的工具及必备的技术文件 : 3. 产品需求 : QFD、顾客面谈、可靠度需求 比较分析、产品质量信息 4. 制造组装的需求 制程需求
19
20
二、设计 FMEA 填写说明
运用QFD将产品系统架构展开 或设计流程展开并列出功能方块图
系统 次系统
车身 门 窗 内装 外装
3.关键性分析(critical analysis)
FMEA失效模式及效应分析介绍

FMEA失效模式及效应分析介绍FMEA(Failure Mode and Effects Analysis)是一种用于识别、评估和减轻系统、产品或过程中可能的失效模式及其可能的效应的工具和方法。
它的目标是通过提前识别和纠正潜在的问题,从而提高系统的可靠性和安全性。
FMEA通常由一个跨职能的团队进行,包括设计工程师、工艺工程师、质量控制人员等。
这个团队将系统、产品或过程分解成多个组成部分,然后针对每个部分,逐个分析其可能的失效模式以及这些失效模式可能引起的效应。
在进行FMEA之前,团队首先需要定义一个适当的评估标准,用于对失效模式和效应进行风险评估。
评估标准通常包括失效的概率、严重性和可能性等方面。
然后,通过对每个失效模式和效应进行评估,确定其风险等级。
常用的评估方法包括风险矩阵、风险优先级数等。
FMEA的关键步骤包括:1.确定分析的范围:确定要进行FMEA的系统、产品或过程的范围,并明确所有相关的组成部分。
2.分析失效模式:对每个组成部分,团队成员进行头脑风暴,识别可能的失效模式。
失效模式是指一个组成部分不能正常工作或无法满足指定要求的一种方式。
3.分析失效效应:对于每个失效模式,分析团队评估其可能引起的效应,包括对系统性能、安全性和可靠性的影响。
这些效应需要根据评估标准进行量化或定性评估。
4.评估风险等级:通过将失效模式和效应的概率、严重性和可能性等因素综合考虑,评估每个失效模式和效应的风险等级。
这有助于团队确定哪些失效模式和效应应优先处理。
5.提出改进措施:根据风险等级,团队制定相应的改进计划。
这可以包括重新设计、改变制造流程、增加可靠性测试等措施,以降低失效模式和效应的风险。
FMEA的优点在于:1.提前识别风险:通过系统的、结构化的方法,FMEA能够识别并提前预测系统或产品中的潜在问题,从而及早采取措施来减轻或消除这些风险。
2.优化设计:通过对失效模式和效应的分析,FMEA可以帮助设计团队发现并改进设计中的潜在问题,从而提高系统的可靠性和性能。
FMEA失效模式与效应分析

括这个系统作业相关环境的信息(如:定温度、压力、湿度范围)。
如果项目包含一个以上有不同潜在失效模式功能时,则列出所有个 别功能。
第二版2001/11/07 14
设计FMEA填写说明
(10)潜在失效模式 潜在失效模式是零件、子系统、或系统于符合设计意图过程 中可能失效的种类。潜在失效模式也可能是较高阶子系统或系统之 失效原因,或较低阶零组件的失效效应。 列出特别项目和功能的每一潜在失效模式。假设失效是将发 生的,但不是必须发生的。 潜在失效模式仅可能发生于某些作业条件下(如:热、冷、 干、多灰尘的条件)和在某些使用条件下(如:行驶哩数在帄均数 以上、粗糙不帄的地形、仅在市区行驶)。 一般的失效模式包含下列各项,但不限于此:破碎的、变形、 松弛、泄漏、黏着、短路、生锈氧化、龟裂。
第二版2001/11/07 4
FMEA过程顺序
系统有那功能,特征,需要条件? 会有那些错误? 发生错误会有多惨? 那些错误是什么造成的?
发生之频率?
有那些预防和检测?
检测方法能多好程度? 我们能做什么? -设计变更 -过程变更 -特殊控制 -改变标准程序或指南
第二版2001/11/07 5
FMEA之功用
第二版2001/11/07
21
设计FMEA填写说明
(16)现行设计管制 列出利用预防措施、设计验证/确认(DV)、或其它活动,而这些活 动是用来确认对失效模式设计适当,和/或原因/设备均被考虑。目前常 用的管制为一些已被使用或正在使用的相同或类似的设计。(如:道路
测试、设计审查、数学研究、可行性审查、原型测试、车队测试等)。
第二版2001/11/07
2
FMEA的基本概念
1.对失效的产品进行分析,找出零组件之 失效模式,鉴定出它的失效原因,研究 该项失效模式对系统会产生什么影响。
- 1、下载文档前请自行甄别文档内容的完整性,平台不提供额外的编辑、内容补充、找答案等附加服务。
- 2、"仅部分预览"的文档,不可在线预览部分如存在完整性等问题,可反馈申请退款(可完整预览的文档不适用该条件!)。
- 3、如文档侵犯您的权益,请联系客服反馈,我们会尽快为您处理(人工客服工作时间:9:00-18:30)。
PFMEA(简易版)的实施程序说明
1.组成PFMEA团队 :了解客户需求或项目工作内容,组成PFME
团队,建立共同的PFMEA 流程知识,项目目标确认。
例如: 目标在量产前将所有可能发生问题降至0。
2.了解产品特性及制造流程 : 依据过去机种或产品经验考虑可
发生相似问题点,或收集资料参考过去对策加以导入 。
PFMEA(简易版)的实施程序说明
5.针对失效模式研拟对策 :对策导入,需考虑对策防呆,避免
为疏忽造成不良,针对所有不同失效模式实际导入对策,并做对策确 动作。
例如 : 颜色管理,图示…等。
6.对策导入检验 :试产观察追踪对策导入效果。
7.对策重修订及导入 :于各阶段试产时确认所有对策是否有效?
已有预防问题依旧发生时需修改对策。
8.FMEA /PFMEA趋势图 :记录PFMEA 趋势,并 将PFMEA 对
策归档,供日后参考。
9.挑战目标持续改善:若不良问题重复发生,须重新 review及
改对策再导入确认,新产品或流程导入时必须重新考虑PFMEA。
PFMEA的作业方式
分站失效模式矩陣圖
製程失效模式與效應分析表
PFMEA趨勢圖 (T.S.)
产品量产时“ 高质量”及“效 率”
顾客的定义
FMEA :
1.内部顾客: 包括生产、组装等,下制程对上制程都称之为顾客。t;=> SMT
2.外部顾客: 最终的使用者(End user) 。
例如 : 购买昌碩生產之所有产品的消费者 。
FMEA实施流程
组成FMEA团队 搜集资料
失效模式与效应分析的沿革
精神
FMEA是一种结构化、预防性的分析技术,主要有两种分析方法: 第一种为「硬品法」:表列并分析每一硬品的可能失效模式。 第二种为「功能法」:根据物品的输出功能分析造成失效的可能原因
因应适用时机与对象不同,失效模式与效应分析( FMEA )又分为两种
1.DFMEA:Design Failure Mode and Effect Analysis
N-TRN-PDS-130-1
前言
PFMEA三大主轴 : 1. 提升制程能力。 2. 以卓越的制程能力克服设计瓶颈。 3. 创造工程师洞察机先的价值。
PFMEA课程内容
1.课程讲解 : 90分钟。 2.随堂测验(笔试) : 15 分钟(分数比重:30%)。 3.专案实习 : 分组成立项目(15分钟),自授课完毕两周后
缴交PFMEA Report(分数比重:70%)。 4.及格标准 : 75分以上,认证合格,课后成绩将提报
各单位主管,作为考核参考数据。
PFMEA课程大纲
失效模式与效应分析的沿革 DFMEA与PFMEA实施时机及差异 顾客的定义 FMEA实施流程 PFMEA的实施程序(简易版) PFMEA的实施程序说明(简易版) PFMEA的作业方式(简易版) PFMEA实施范例(简易版) PFMEA执行方法(简易版)
失效模式与效应分析的沿革
背景
• 格鲁曼(Grumman)公司在1950年初期,随飞机由螺旋桨(Propeller 推进引擎变为喷射引擎(Jet engine)而开发失效模式、效应与关键 分析(Failure Modes, Effects and Criticality Analysis; FMECA)的 设计分析方法。
步骤1. 制作“PFMEA分站失效模式矩阵图”:
利用此表格,针对产品及制程分站,将所有可能发生质量问题点条列式 盘点出来格式如下所示 :
制程失效模式与效应分析(FMEA)的运用
08年昌硕電子化修改版
讲师: 王进贤 课程时数:81分钟
版本:080401A 講師:王進賢 JOJO W
大纲说明
课程内容
1.前言 2.FMEA课程内容 3.FMEA课程大纲
4.失效模式与效应分析的沿革
5. DFMEA与PFMEA实施时机及差异 6.顾客的定义 7. FMEA实施流程 8. PFMEA(简易版)的实施程序 9. PFMEA(简易版)的实施程序说明 10. PFMEA的作业方式 11. FMEA 风险指数评估(Risk Priority Number; RPN) 12.案例模拟 13. PFMEA重点 14.Q&A and 資料來源
(设计失效模式与效应分析) 。 2.PFMEA:Process Failure Mode and Effect Analysis
(制程失效模式与效应分析)。
DFMEA与PFMEA实施时机及差异 产品研发阶段: 实施DFMEA
针对潜在设计问题事先预测并以解决
产品试产(P/R)前: 完成PFMEA
针对潜在制程问题事先预测并解决
完成FMEA执行计划
分析硬品架构
分析失效原因 分析发生率O
定义系统特性 分析失效模式 分析现有管制方式 分析难检度D
计算关键指数 R.P.N
制程改善
决定关键性失效模式 建议改正行动
撰写报告
分析系统功能
分析失效效应 分析严重度S
失效报告、分析 与改正操作系统
目标设立 阶段 E/R
计划订定阶 段 E/R
例如:收集生產過程中SFIS紀錄的不良资料。
3.找出可能的失效模式: 可分制程及部品特性及可能发生不良问
题作一矩阵图加以盘点(以实际到现场观察为佳),并填入制程失效模 式与效应分析表。例如 : 组装动作<=>刮碰撞伤, M/B<=>短路。
4.找出可能的失效原因:汇总发生的问题,预测新产品及制程可
的失效原因(使用脑力激荡法) 。
PFMEA(简易版)的实施程序
Start
组成PFMEA团队设立目标
了解产品特性及生产流程
找出各种可能失效的模式 / 因子 针对失败模式研拟对策(参照资料)
对策导入检验 NG
各试产阶段确 认对策是否有
效 PFMEA/TROBULE SHOOT
对策重修订及导入 目标检验持续改善
计划执行 阶段 E/R
目标检验 阶段 P/R
• 1960s美国航空太空总署(NASA)执行阿波罗(APOLLO)计划时,即 将可靠度及安全管理订为契约中的重要条款,要求履约对象〔即 合约商〕必须实施FMECA,美国军方也开始使用。
• 1993年美国三大车厂(GM,Ford,Chrysler)在ASQC(美国质量协会) AIAG(汽车工业行动组)协助下完成设计及制程FMEA参考手册。