失效模式与效应分析(FMEA)
失效模式与效应分析

上失效模式与效应分析(failure modes and effects analysis, FMEA)¾又名:潜在失效模式与效应分析(PotentialfaiIUre modes and effects analysis),失效模式、影响与危害性分析(failure modes, effects, and criticality analysis, FMECA)A概述失效模式与效应分析(FMEA)是一步步地识别在设计、生产或装配过程以及最终产品和服务中全部可能失效的一种方法。
“失效模式”意思是可能产生某些失效的方式或模式。
失效是任何的错误或者缺陷,尤其是那些影响顾客的、潜在的或实际的。
“效应分析”指的是争论这些失效的后果或效应。
这些失效依据他们结果的严峻性、发生的频率以及被检测到的简洁度优先排序。
FMEA的目的是从有最高的、优先级的开头来实行行动消退或者削减失效。
FMEA通常把当前有关失效的学问以及所实行的行动文档化,用于持续的改进。
FMEA用于设计中预防失效的发生,之后又用于正在进行的过程操作中的掌握。
抱负地说, FMFA 开头于产品的概念设计阶段,贯穿于产品或服务的整个生命期中。
FMEA在19世纪40年月最早被应用于美国的军队中,然后在航空和自动化行业得到进一步的进展应用。
一些行业已经把FMEA的标准正规化,下面是一个综述。
在实行FMEA过程之前,需通过其他的参考资料和培训,从而学习更多关于组织和行业的标准和具体的方法。
>适用场合•当一个产品或服务正在被设计或者重复设计时,在QFD之后或者在设计完成之后;•当以全新的方式应用现有的过程、产品或服务时;•在形成新的或改进过程的掌握方法以前;•当对现有的过程、产品或服务方案改进的时候;•当分析现有的过程、产品或者服务失效缘由时;•贯穿于过程、产品或者服务的生命期中定期进行检查。
>实施步骤这只是一个也许的过程,具体的细节则随着组织或行业的标准而有所变化。
设备潜在失效模式及效应分析

设备潜在失效模式及效应分析设备潜在失效模式及效应分析(FMEA)是一种系统性的方法,用于识别设备潜在的失效模式及其可能的影响。
这种方法可以帮助组织预测设备可能出现的问题,从而采取预防性措施来避免这些问题的发生。
在进行设备潜在失效模式及效应分析时,首先需要确定设备要分析的功能或特性。
然后,对于每一个功能或特性,需要识别所有可能的失效模式。
失效模式是指设备在执行其功能或特性时可能发生的故障方式。
一旦失效模式被确定,下一步就是对每种失效模式进行评估,确定其可能的影响。
这些影响可以涉及到安全、质量、生产效率、环境和成本等方面。
通过对失效模式和其影响进行分析,可以确定哪些失效模式是最严重的,从而可以优先采取措施来预防或减轻这些失效的影响。
设备潜在失效模式及效应分析对于预测设备可能出现的故障非常有益。
通过这种分析,组织可以采取有效的措施来避免或减少设备故障可能造成的负面影响。
这不仅可以提高设备的可靠性和可用性,还可以降低维护成本,提高生产效率,保护员工安全,保护环境等。
总之,设备潜在失效模式及效应分析是一种重要的工具,可以帮助组织预测设备可能的故障,并制定相应的预防措施。
这种分析方法不仅可以提高设备的可靠性和可用性,还可以降低维护成本,提高生产效率,保护员工安全和环境等方面都具有重要作用。
设备潜在失效模式及效应分析(FMEA)是一种系统性的方法,用于识别设备潜在的失效模式及其可能的影响。
这种方法可以帮助组织预测设备可能出现的问题,从而采取预防性措施来避免这些问题的发生。
在进行设备潜在失效模式及效应分析时,首先需要确定设备要分析的功能或特性。
然后,对于每一个功能或特性,需要识别所有可能的失效模式。
失效模式是指设备在执行其功能或特性时可能发生的故障方式。
失效模式的识别可以通过对设备的历史数据、技术文档、专家意见等进行调研,以找出设备可能存在的各种故障情况。
一旦失效模式被确定,下一步就是对每种失效模式进行评估,确定其可能的影响。
失效模式和效果分析FMEA在制药行业的应用教材

失效模式和效果分析FMEA在制药行业的应用教材失效模式与效应分析(Failure Mode and Effects Analysis, FMEA)是一种常用的质量管理工具,它可以帮助制药行业发现潜在的问题,预防和减少产品质量问题的发生,从而提高产品质量和安全性。
本文将探讨FMEA在制药行业的应用,并分析其效果。
FMEA的基本原理是通过识别潜在的失效模式,并分析这些失效模式可能引起的效应,进而制定合适的预防和纠正措施。
在制药行业,FMEA通常用于产品开发、生产过程和设备维护等环节。
下面将详细介绍FMEA在这些环节的应用。
首先,FMEA在制药产品开发阶段起到了重要的作用。
制药产品的设计失效可能导致产品质量问题和安全隐患。
通过应用FMEA,可以对设计过程中潜在的失效模式进行识别和评估,并制定相应的改进方案。
例如,通过对产品配方进行FMEA分析,可以找出可能导致配方不稳定的因素,如不合适的原材料、配方比例不当等。
这样可以在产品设计阶段及时进行调整,避免质量问题的发生。
其次,FMEA在制药生产过程中的应用也十分重要。
生产过程中的失效可能导致产品质量不稳定和生产效率降低。
通过应用FMEA,可以识别和评估生产过程中的潜在失效模式,并设计相应的控制措施。
例如,在制药生产过程中,可能存在温度控制失效、搅拌不均匀等问题。
通过应用FMEA,可以定位这些问题的发生原因,并制定相应的控制措施,比如使用更精确的温度控制设备、改进搅拌工艺等。
此外,FMEA还可以应用于制药设备的维护管理。
设备故障可能导致生产中断和质量问题。
通过应用FMEA,可以识别设备故障的潜在失效模式,并制定相应的预防和纠正措施。
例如,对于关键设备,可以制定定期保养计划,定期更换易损件,增加备件库存等。
通过这些措施,可以降低设备故障的概率,保证生产的稳定性和质量。
FMEA作为一种质量管理工具,在制药行业的应用具有一定的优势和效果。
首先,通过FMEA可以对潜在的失效模式进行全面、系统的分析。
失效分析基本常识以及操作流程

失效分析基本常识以及操作流程失效分析是一种通过分析和探究事物、系统或过程发生失效的原因和机制的方法。
它可以帮助我们识别并改进潜在的问题,以提高系统的可靠性和性能。
以下是关于失效分析的基本常识与操作流程。
一、失效分析的基本常识1.失效模式与效应分析(FMEA):FMEA是一种通过分析预测和评估失效模式及其严重性、发生概率和检测能力的方法。
它可以在设计、生产和使用阶段预防或减少失效。
2.失效树分析(FTA):FTA是一种通过将失效进行因果关系的图形化表示来分析系统失效的方法。
它能够帮助确定导致一些具体失效的事件链。
3.事故树分析(ETA):ETA是一种通过将事故及其后果进行因果关系的图形化表示来分析事故发生的方法。
它可以帮助识别和评估事故的潜在原因及其对系统的影响。
4.失效模式、原因和影响分析(FMEDA):FMEDA是一种通过分析失效模式、失效原因和失效影响的方法来评估系统的可靠性。
它通常用于评估硬件系统。
5.人因分析:人因分析是一种通过分析人因相关的错误、失误和措施来评估和改进工作系统和流程的方法。
它可以帮助减少人为失误和提高操作效率。
二、失效分析的操作流程1.确定分析目标:确定需要进行失效分析的系统、产品或过程,并明确分析的目标和范围。
例如,是为了解决一个特定的问题,还是为了提高整体系统的可靠性等。
2.收集相关数据:收集和整理与失效有关的数据和信息,包括过去的失效记录、测量数据、使用情况等。
这些数据将为后续的分析提供基础。
3.选择适当的工具和方法:根据分析的目标和需要,选择适合的失效分析方法和工具,如FMEA、FTA、ETA等。
有时需要结合多种方法进行分析。
4.定义失效模式与效应:识别和描述可能的失效模式及其对系统的影响。
这包括对失效模式的描述和分类,以及对失效的严重性进行评估。
5.分析失效原因:通过追溯失效模式,分析导致失效发生的可能原因和机制。
这包括对失效原因的分类和评估,以及确定潜在缺陷和改进点。
风险评估技术-失效模式和效应分析(FMEA)及失效模式、效应和危害度分析(FMECA)

失效模式和效应分析(FMEA及失效模式、效应和危害度分析(FMECA)1 概述失效模式和效应分析(Failure Mode and Effect Analysis ,简称FMEA)是用来识别组件或系统未能达到其设计意图的方法。
FMEA 用于识别:•系统各部分所有潜在的失效模式(失效模式是被观察到的是失误或操作不当);•这些故障对系统的影响;• 故障原因;• 如何避免故障及 /或减弱故障对系统的影响。
失效模式、效应和危害度分析(Failure Mode and Effect and Criticality Analysis ,简称 FMECA)拓展了 FMEA 的使用范围。
根据其重要性和危害程度,FMECA 可对每种被识别的失效模式进行排序。
这种分析通常是定性或半定量的,但是使用实际故障率也可以定量化。
2 用途FMEA 有几种应用:用于部件和产品的设计(或产品) FM EA ;用于系统的系统FMEA ;用于制造和组装过程的过程 FMEA ;服务FMEA和软件FMEA。
FMEA/ FMECA 可以在系统的设计、制造或运行过程中使用。
然而,为了提高可靠性,改进在设计阶段更容易实施。
FMEA/ FMECA 也适用于过程和程序。
例如,它被用来识别潜在医疗保健系统中的错误和维修程序中的失败。
FMEA/FMECA 可用来:•协助挑选具有高可靠性的替代性设计方案;•确保所有的失效模式及其对运行成功的影响得到分析;•列出潜在的故障并识别其影响的严重性;•为测试及维修工作的规划提供依据;• 为定量的可靠性及可用性分析提供依据。
它大多用于实体系统中的组件故障,但是也可以用来识别人为失效模式及影响。
FMEA 及 FMECA 可以为其他分析技术,例如定性及定量的故障树分析提供输入数据。
3 输入数据FMEA 及 FMECA 需要有关系统组件足够详细的信息,以便对各组件出现故障的方式进行有意义的分析。
信息可能包括:• 正在分析的系统及系统组件的图形,或者过程步骤的流程图;• 了解过程中每一步或系统组成部分的功能;• 可能影响运行的过程及环境参数的详细信息;• 对特定故障结果的了解;• 有关故障的历史信息,包括现有的故障率数据。
失效模式与效应分析在护理风险
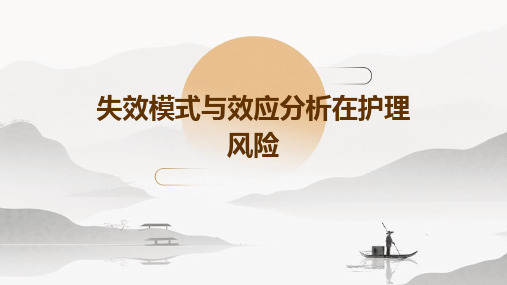
将识别出的失效模式记录在专门的表格或数据库中,以便后续分析 和改进。
风险优先级评估
评估失效模式的风险
01
根据失效模式的发生频率、严重程度和可检测性等指标,评估
每个失效模式的风险等级。
确定优先改进目标
02
根据风险评估结果,确定需要优先改进的失效模式,为制定改
进措施提供依据。
制定风险控制计划
实施难度
FMEA需要多部门合作和大量资源投入,实施起 来可能面临一定的困难。
更新需求
随着医疗技术的不断发展和护理实践的改进, FMEA需要不断更新和调整。
未来发展方向
智能化分析
利用人工智能和大数据技术,对海量数据进行挖掘和分析,提高 FMEA的准确性和效率。
跨学科合作
加强与其他学科领域的合作,共同研究护理风险的防控策略,提高 护理质量。
案例二:老年患者护理风险
总结词
老年患者由于身体机能下降,容易发生跌倒、压疮等护理风险。FMEA可以帮助识别和评估这些风险 ,从而采取有效的措施来降低风险。
详细描述
老年患者护理风险的失效模式包括地面湿滑、床边无护栏、缺乏合适的坐便器等。通过FMEA分析, 可以评估这些风险的发生可能性和严重程度。针对这些风险,可以采取相应的措施,如加强地面清洁 、安装床边护栏、提供合适的坐便器等,以降低风险。
提高护理质量
通过分析和改进护理过程中的失效 模式,FMEA有助于提高护理质量, 提升患者的满意度和信任度。
FMEA的发展历程
起源
FMEA起源于20世纪40年代的军事行 业,后来被广泛应用于航空、汽车和 医疗领域。
在护理领域的应用
发展和改进
随着医疗技术的不断发展和患者需求 的提高,FMEA在护理领域的应用也 在不断发展和改进,以适应新的挑战 和需求。
失效模式与效应分析 (FMEA)
失效模式與效應分析 (FMEA)何謂「FMEA、FMECA」?FMECA 是兩種分析技術的總稱:1.FMEA﹝故障型式及其影響分析﹞2.CA﹝Criticality Analysis, 嚴重度分析﹞與失誤樹分析一樣,故障型式影響及嚴重度分析﹝failure modes, effects and criticality analysis, 簡稱 FMECA﹞,首先在美國國防科技中研究發展,且在國防部各機構中普遍應用﹝DOD, 1980﹞,後來漸應用於工業界。
在核能、化工、石化、海上鑽油等高風險工業中,自不例外。
工業界的設計工程師與可靠度﹝Reliability﹞工程師常運用 FMECA 以預測複雜的產品的可靠度,預估一件產品的零件在某特定的時間及情況下,如何失去其功能,故障的次數是多少,故障之後對其他零件或對整個系統會產生怎樣的影響等。
FMECA 的功用不止於可靠度一端,其分析所得的資料,尚可作下列用途:1.協助評估所設計的裝置,如複聯系統﹝Redundancy﹞、故障偵測,以及fail-safe 特性等。
2.對測試、採購﹝Procurement﹞、檢查、改善措施等提供先後順序的參考資料。
3.提供失誤隔絕﹝Fault isolation﹞及維護性﹝Maintainability﹞分析的參考資料。
4.提供系統安全分析﹝如失誤樹分析﹞所需的硬體資料。
FMECA 可在系統週期的任一階段中,依計劃內容之需要,以不同深淺程度實施,但在設計階段的初期,一旦所需的設備確定之後,即應實施。
FMECA 的對象是系統或子系統中的零組件,尤其對於複雜的系統中的設備零件,最能發揮其故障針砭的功效,此為其他系統安全分析技術不能望其項背之處。
但因其分析對象大多限於硬體,故對於人為因素和作業環境因素較少納入分析考慮範圍。
因此,如能將 FMECA 與失誤樹分析合併使用,必更能瞭解整個作業系統的危害,進而防範事故生。
摘於【環安 Q&A】。
失效模式与效应分析在护理风险PPT课件(精选)
失效模式与效应分析在护理风险PPT课件(精选)失效模式与效应分析在护理风险PPT课件(精选)失效模式与效应分析(Failure Mode and Effects Analysis, FMEA)是一种用于识别和评估系统、设备或过程中潜在失效的方法。
在护理领域中,FMEA被广泛应用于识别护理过程中潜在的风险和错误,以便采取相应措施预防风险事件的发生。
本PPT课件将介绍失效模式与效应分析在护理风险管理中的应用,并提供一些精选案例。
第一部分:什么是失效模式与效应分析(FMEA)失效模式与效应分析是一种结构化的方法,用于识别和评估潜在失效对系统或过程的影响。
该方法通过系统性分析可能的失效模式,评估其严重性以及对其他环节的影响,从而确定采取的控制措施和风险管理策略。
FMEA通常由跨专业的团队共同进行,以获得全面准确的分析结果。
第二部分:FMEA在护理风险管理中的应用2.1 护理风险管理的背景和意义护理风险管理是为了提供安全有效的护理而采取的一系列策略和措施。
在日常护理实践中,存在着各种风险和误差,例如药物错误、手术事故、设备故障等。
通过采用FMEA方法,护理团队可以识别和分析这些潜在的失效模式,制定相应的预防措施,降低患者遭受伤害的风险。
2.2 FMEA的基本步骤(1)确定目标:明确进行FMEA的目的和范围。
(2)建立团队:组建跨专业的团队,包括护士、医生、护理管理人员等。
(3)流程分析:详细描述护理过程中的每个步骤和环节。
(4)识别失效模式:分析每个步骤中可能发生的失效模式。
(5)评估严重性与频率:评估每个失效模式的严重性和发生频率。
(6)确定控制措施:制定相应的控制措施,包括预防和纠正措施。
(7)执行措施:在实际护理过程中执行制定的措施,并追踪效果。
(8)持续改进:根据实际效果,对措施进行评估和改进。
第三部分:护理风险管理中的FMEA案例3.1 药物错误防范以护理过程中的药物错误为例,通过FMEA的方法,可以识别出引发药物错误的失效模式,如医嘱错误、药物相互作用等。
潜在失效模式与效应分析
潜在失效模式与效应分析潜在失效模式与效应分析(Failure Mode and Effects Analysis,FMEA)是一种常用于产品设计与制造过程中的质量管理工具,用于识别和分析可能的失效模式和其对产品或系统性能的潜在影响,从而采取相应的改进措施以提高产品的可靠性和安全性。
FMEA包括三个关键步骤:识别潜在失效模式、分析失效效应和确定风险优先级。
首先,团队通过对产品或系统进行系统性分析,并结合以往经验,识别出所有可能的失效模式。
这些失效模式可能发生在产品的各个环节,如设计、制造、装配、运输和使用等。
然后,团队对每个失效模式进行评估,分析失效效应。
失效效应可能包括对产品功能、性能、可靠性和安全性的影响。
最后,根据失效模式和效应的严重性和概率,确定风险优先级,以便制定相应的改进措施。
FMEA的核心目标是预防失效,并通过优先处理潜在的高风险失效来提高产品质量和可靠性。
通过分析失效模式和其效应,可以识别导致失效的根本原因,并采取相应的纠正和预防措施。
FMEA可以帮助团队更好地理解产品的设计和制造过程中的潜在问题,并预测可能的质量和安全风险,从而减少后续的成本和不良后果。
FMEA也有助于团队提高对产品的理解和共识。
在FMEA过程中,团队成员就产品的设计和制造问题展开讨论,共同评估潜在的失效模式和其效应,并制定改进措施。
通过这些讨论,团队可以发现和纠正潜在的问题,并提高各部门之间的沟通和合作。
FMEA的应用领域广泛,适用于各类产品和系统的设计和制造过程。
例如,汽车制造业常用FMEA来识别和纠正潜在的设计和制造缺陷,提高汽车的质量和安全性。
医疗设备制造商也使用FMEA来评估产品的安全性和性能,减少医疗事故的风险。
此外,航空航天、电子、化工等行业也都广泛应用FMEA来提高产品的可靠性和安全性。
总之,潜在失效模式与效应分析(FMEA)是一种非常有用的质量管理工具,通过识别和分析潜在的失效模式和其效应,帮助团队预防失效、提高产品的可靠性和安全性。
FMEA失效模式及效应分析介绍
FMEA失效模式及效应分析介绍FMEA(Failure Mode and Effects Analysis)是一种用于识别、评估和减轻系统、产品或过程中可能的失效模式及其可能的效应的工具和方法。
它的目标是通过提前识别和纠正潜在的问题,从而提高系统的可靠性和安全性。
FMEA通常由一个跨职能的团队进行,包括设计工程师、工艺工程师、质量控制人员等。
这个团队将系统、产品或过程分解成多个组成部分,然后针对每个部分,逐个分析其可能的失效模式以及这些失效模式可能引起的效应。
在进行FMEA之前,团队首先需要定义一个适当的评估标准,用于对失效模式和效应进行风险评估。
评估标准通常包括失效的概率、严重性和可能性等方面。
然后,通过对每个失效模式和效应进行评估,确定其风险等级。
常用的评估方法包括风险矩阵、风险优先级数等。
FMEA的关键步骤包括:1.确定分析的范围:确定要进行FMEA的系统、产品或过程的范围,并明确所有相关的组成部分。
2.分析失效模式:对每个组成部分,团队成员进行头脑风暴,识别可能的失效模式。
失效模式是指一个组成部分不能正常工作或无法满足指定要求的一种方式。
3.分析失效效应:对于每个失效模式,分析团队评估其可能引起的效应,包括对系统性能、安全性和可靠性的影响。
这些效应需要根据评估标准进行量化或定性评估。
4.评估风险等级:通过将失效模式和效应的概率、严重性和可能性等因素综合考虑,评估每个失效模式和效应的风险等级。
这有助于团队确定哪些失效模式和效应应优先处理。
5.提出改进措施:根据风险等级,团队制定相应的改进计划。
这可以包括重新设计、改变制造流程、增加可靠性测试等措施,以降低失效模式和效应的风险。
FMEA的优点在于:1.提前识别风险:通过系统的、结构化的方法,FMEA能够识别并提前预测系统或产品中的潜在问题,从而及早采取措施来减轻或消除这些风险。
2.优化设计:通过对失效模式和效应的分析,FMEA可以帮助设计团队发现并改进设计中的潜在问题,从而提高系统的可靠性和性能。
- 1、下载文档前请自行甄别文档内容的完整性,平台不提供额外的编辑、内容补充、找答案等附加服务。
- 2、"仅部分预览"的文档,不可在线预览部分如存在完整性等问题,可反馈申请退款(可完整预览的文档不适用该条件!)。
- 3、如文档侵犯您的权益,请联系客服反馈,我们会尽快为您处理(人工客服工作时间:9:00-18:30)。
Failure Mode & Effects Analysis
1. FMEA 簡介(續)
消除
減少
減少
保存
全風險
剩余風險
損失管制程序圖
1) 消除,管制及減低風險的工作不只是工程部門的責任,更是
每一個部門甚至是每一個人的工作職責.
2) 風險允許存在, 但必須降低及控制在一定范圍之內.
3) FMEA就是通過風險評估與計算來確認FMEA的執行效果.
1957工程手冊中正式列出 FMEA程序
Nation Aeronautics and Space Administration(NASA)
Chrysler,Ford, G.M. ASQC,AIAG
Defense Department
International Electrical Commission(IEC)
1960成功地應用於航太計劃
1974出版Mil-STD-1629 FMECA 1980出版Mil-STD-1629A FMECA 1985出版IEC812 FMEA
10
Failure Mode & Effects Analysis
4. FMEA是持續改善手法之一
先期產品品質規劃(APQP)系統由設計,制造及顧客三大部份組成. 顧客是整個系統中的關鍵: 顧客的心聲,即是顧客的需求及期望.將 顧客的需求及期望和其他關鍵要求輸入於設計及制造系統中,應用 各種技術如制造設計(Design for Manufacturing),裝配設計 (Design for Assembly),價值工程(Value Engineering),實驗設計 ,電腦輔助設計(CAD),電腦輔助工程(CAE),可靠度工程計劃法 (Reliability Engineering Plans)等方法,制造出顧客可以接受, 甚至可超越顧客期望的產品或服務.
2. FMEA 定義及評價
第三: 主要特征(Major)
FMEA的評定指標迅速回饋到制程, 可立即正確地改善品質 問題.此指標也提供問題來源及關于品質方面,顧客不滿意 的定性及定量說明, 諸如下列所示:
1.長期信賴性測試 2.稽核
6.檢驗研究 7.保證(里程,壽命)資料分析
3.制程良品率檢討及分析 8.供應商審核分析
4.客戶問卷調查
9.顧客抱怨分析
5.產品驗收測試
9
Failure Mode & Effects Analysis
3. FMEA淵源
Grumman Aircraft Co統 失效分析
Boeing & Martin Marietta Aerospace Company
客戶需求及其他可取得資訊. 2) 使用統計推論,數學模式,模擬分析,同步工程及可靠度工程
等. 使用FMEA並不意謂這種方法比其他手法更好,或是更準確.如果正 確及時的使用,FMEA方法會更準確,更正確及更有效率.
6
Failure Mode & Effects Analysis
2. FMEA 定義及評價
3
Failure Mode & Effects Analysis
1. FMEA 簡介(續)
FMEA成功關鍵: 時間性 FMEA是“事前行為”, 而非“事後行為”. 即事 先(APQP)花費時間很好的進行FMEA,能容易,低成 本地對產品或制程進行修改,從而減少或消除因 修改帶來更大損失的機會. FMEA是一個相互作用的過程, 永無止境.
2. FMEA 定義及評價
第二: 重要特性(Significant) 顧客及供應商共同制定或顧客指定或設計/制程工程 師制定.
e.g: 尺寸,速度,溫度,壓力,等等. 設計FMEA及制程FMEA的內容必須用於確認重要的產品 ,制程或服務特性.所有的重要特性應於可行性研究中 就設計好.
8
Failure Mode & Effects Analysis
5
Failure Mode & Effects Analysis
2. FMEA 定義及評價
FMEA是一種工程技術用以定義,確認,及消除在系統,設計,制程及 服務還沒有到達顧客前已知的或潛在的失效,問題,錯誤,等等. FMEA定義失效的方法一般有兩種 1) 使用歷史數據,針對類似產品經驗,服務,保證數據,顧客抱怨,
2
Failure Mode & Effects Analysis
1. FMEA 簡介(續)
FMEA定義: 潛在失效模式及效應分析(Potential Failure Mold and Effects Analysis), 是產品品 質持續改善及提升的分析工具之一,它貫穿於產品 設計開發到制程改善及產品變更的整個過程. FMEA 不同於 8-discipline, 它是一種先期改善行為(預 防性), 而後者只是一種錯誤矯正行為(事後型). 通過FMEA的執行和落實,可減少很多設計&生產過程 中的失敗及矯正成本.
Failure Mode & Effects Analysis
(先期)失效模式與效應分析
(Potential )Failure Mode &Effects Analysis
----務實篇
1
Failure Mode & Effects Analysis
1. FMEA 簡介
因應日益增加的快速變動,任何個人或企業必須追 求技術及品質的提升以改善產品與服務. 這需要 不同程度的改變.改變同時也伴隨不確定之風險. 公司或企業為了生存及永續發展必須思考如何預 防或消除風險. “風險”一詞在FMEA中被廣泛運 用.
FMEA是早期預防失效及錯誤發生的最重要且最有效的,避 免流漏失效,錯誤流到顧客手上的最好的方法之一.
第一: 良好的FMEA必須具備:
1.確認已知及潛在失效模式 2.確認每一失效模式的效應和原因 3.依據風險優先指數(嚴重度,發生率,難檢度) 4.提供問題跟催及矯正行動
7
Failure Mode & Effects Analysis
11
Failure Mode & Effects Analysis
4. FMEA是持續改善手法之一
系統/設計及制程FMEA是以顧客為依歸, 顧客就是FMEA的導師(客 戶導向),指引著FMEA的方法做法及方向. FMEA的過程必須匯集全力用以減少產品設計及制程過程的風險,方 能生產合乎顧客需求超越顧客期望的產品,達到以客為尊的目的. Note: 1. 顧客= 外部客戶 + 內部客戶 即在 FMEA制作過程中應