齿形和齿向修形(K形图)
齿轮修形知识简介

NO.6841 2 3 4 5 6 7齿轮修形可以极大地提高传动精度,并增加齿轮强度。
广义上的齿轮修形有许多类别(齿端修形、齿顶修形、齿根修形、变位、修改压力角),本文将分享答主在精密传动设计中,关于齿轮修形的心得。
(以下将『输出扭矩波动率小』作为『传动精度高』的唯一指标)1. 齿『端』修形(齿向修形)齿『端』修形是最常见(最容易加工)的修形方式,通常是为了帮助装配,和机械设计中多数倒角的作用是一样的,但其实对传动精度和齿轮强度都有影响。
2. 齿『顶』修形(齿顶高系数)齿『顶』修形是所有修形方式中,对传动精度影响(提高)最大的。
我们希望齿轮啮合线是这的形状:红色是啮合线(理想的)但其实是这样的:红色是啮合线(实际的),啮合线只有一部分是“正确”的因为标准齿形中,齿顶被“削”去了一部分,所以渐开线是不完整的,导致主齿轮的齿顶和副齿轮的齿面(从截面上看)是先由点-线接触,再过渡到线-线接触:上图的放大版如果齿顶少“削”一点(齿顶高系数从1 提高至1.3,相应地,齿根高系数从1.25 提高至1.4),渐开线会变得更完整,啮合线也变得从1.25 提高至1.4、),渐开线会变得更完整,啮合线也变得更接近理想的形状:啮合线“正确部分”变长了、“不正确部分”变短了但并不是“削”得越少,传动精度越高,因为齿顶的材料厚度小、应变大,因此在啮合的过程中,渐开线越靠近齿根的部分,啮合精度越高;渐开线越靠近齿顶的部分,啮合精度越低。
不同场景中(主要影响因素是额定扭矩、齿轮模数、齿数、压力齿轮副参数:基于ISO 53:1998轮廓A 齿形、1 模24 齿、20 度压力角、厚度7 mm、10 Nm 输入扭矩、4775 RPM 输入转速、5 kW 输入功率、齿根高系数1.4、无变位、无其他修形、中心矩公差为0、齿厚公差/背隙/齿距误差为0、无摩擦。
此时扭矩波动仅受材料模量和齿形影响。
若齿顶高系数为1,输出扭矩曲线:若齿顶高系数为1.2:旋转角度(齿轮A)[°]扭矩波动范围为(+0.02,-0.12),波峰在C 点左侧、波谷在C 点右侧若齿顶高系数为1.4:旋转角度(齿轮A)[°]输出扭矩波动范围为(+0.01,-0.1),波谷在C 点左侧、波峰在C 点右侧这个例子是(容许范围内)齿顶高系数越大、传动精度越高。
齿轮用K卡图设计及应用

1 .变 速 器 中 K 卡 图 的含 义
以变 速器 1 被动 齿轮 的 K卡 图为 例解 释 K卡 挡 图的含 义 。图 1为 变 速 器 1挡 被 动 齿 轮 的 K卡 图。 在 K卡 图中 ,上半 部分 为 齿 向 图 ,下 半部 分 为齿 廓
图
l
( m) 齿 顶 修 缘 量 ( m ;C 是 m) 齿 廓 总 公 差 ;F 是
' 在 0异 向时则 测量值 = I4 4 4 : _ + 2 I。MW
( 收稿 日期 :2 100 ) 0 12 1
3 .齿廓综合偏差 F 的确 定
根 据设 计精度 ,按 表 2选 择齿 廓 总 公 差 ( 摘
7 0
参露
…
自 D N 9 2 1标准 ) I36T 。
T = 6 aa6/ 2 0 tn 2L () 3
尺寸 计 算 ;C 为 轮 齿 啮 合 刚 度 ,简 化算 法 C =1 7
N( / mm ・ m) 。
( ) 从基 圆至齿 顶 圆的展 开长度 K的计 算公 式 4
K= ( 一 ) r 式 中 ,r 为齿 顶 圆半 径 。 ( ) 从基 圆至有 效 齿 根 圆的展 开 长 度 F的计 算 5
眦
( 1 啮合线 的 倾斜 量 AK 在 基 圆半 径 、齿 顶 1) 圆半 径与 啮合线 组 成 的直 角三 角 形 中 ( 图 3 ,由 见 ) 于 啮合线 发 生 倾 斜 ,O 角 发 生 变 化 ,产 生 了倾 斜 量 /
△ 。
已知有效 齿 顶 圆展 开 长 度 K=4 . II 3 5 I ;有 效齿 YI I
( ) 圆角 R= . 2 mm。 9 005
(0 与最 大 修缘 高度 展 开 长 度 相应 的 齿廓 1)
齿轮的齿形齿向介绍ppt课件
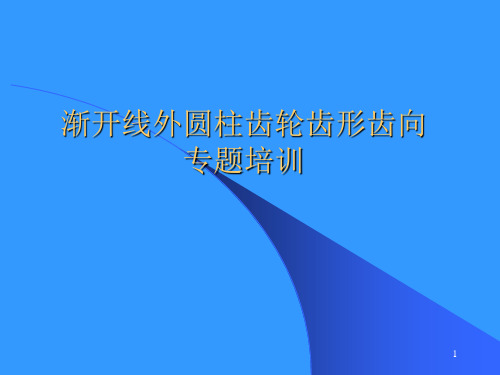
1
培训纲要
一、齿形齿向检测图(WENZEL)详解 二、几种应避免的不良齿形齿向 三、检测、评判齿形齿向时应注意事项 四、各项精度误差对齿轮加工的重要性
2
一、齿形齿向检测图(WENZEL)详解
1、齿形检测图详解(齿形检测图见附图一) 1)齿形图横座标:齿轮渐开线检测点展开角/曲率半径/直径参数 2)齿形图纵座标:检测的计数齿数信息、左右齿面信息、齿形 误差每格数值(比列)、齿形误差。
江齿齿形修形标准对齿轮螺旋角误差正负判定原则与WENZEL判定原则
相同,即为“实体增加减小法”。
15
Cb—齿向鼓形量:齿向中线两点间连线到齿向中线之间的最大距 离,有正、负之分,齿向中线弧高向齿轮实体外偏离为“正”如 图示,反之为“负”即齿向中凹。
16
fsβ—齿向螺旋角误差变动量:齿向螺旋角误差最大值与最小值 之差。该项误差即是我们常讲的齿向乱不乱的问题,在齿向误 差数据表中没有反映,需评判人员计算,从该项误差可以反映 齿轮加工过程中刀具装夹和修磨误差、工装端跳和零件端跳是 否合格。
8
附图二:纵式齿形检测图形
9
2、齿向检测图详解(齿向检测图见附图三、附图四),以附图 三齿向检测图形(纵式)为例:
附图三:(右旋)齿向检测图形(横式)
10
附图四:齿向检测图(纵式)
11
1)齿向图横座标:齿轮宽度方向的检测点长度尺寸,检测时齿 轮放置的下端为0基准(0~B齿宽度)。 2)齿向图纵座标:检测的计数齿数信息、左右齿面信息、齿向 误差每格数值(比列)、齿向误差。
以上具体的各种精度要求见《齿形加工工序齿形检 测评判规定》
谢谢大家! 不当之处敬请指正!
结束 ——
齿轮的参数、代号、图解、计算方法

齿轮几何要素的名称、代号齿顶圆:通过圆柱齿轮轮齿顶部的圆称为齿顶圆,其直径用 d a 表示。
齿根圆:通过圆柱齿轮齿根部的圆称为齿根圆,直径用 d f 表示。
齿顶高:齿顶圆 d a 与分度圆d 之间的径向距离称为齿顶高,用 h a 来表示。
齿根高:齿根圆 d f 与分度圆 d 之间的径向距离称为齿根高,用 h f 表示。
齿顶高与齿根高之和称为齿高,以h 表示,即齿顶圆与齿根圆之间的径向距离。
以上所述的几何要素均与模数 m 、齿数z 有关。
齿形角:两齿轮圆心连线的节点P处,齿廓曲线的公法线(齿廓的受力方向)与两节圆的内公切线(节点P 处的瞬时运动方向)所夹的锐角,称为分度圆齿形角,以α表示,我国采用的齿形角一般为20°。
传动比:符号i ,传动比i 为主动齿轮的转速n 1(r/min )与从动齿轮的转速n 2(r/min )之比,或从动齿轮的齿数与主动齿轮的齿数之比。
即i= n 1/n 2 = z 2/z 1中心距:符号a ,指两圆柱齿轮轴线之间的最短距离,即:a=(d 1+d 2)/2=m(z 1+z 2)/2齿轮几何参数计算压痕法是在被测齿轮的齿顶涂色后,使其在一张纸上滚动,这张纸上就留下了齿顶滚过的痕迹,根据压痕作出齿顶线的延长线及辅助线,然后用量角器测量出齿向角度,该角即为齿轮齿顶处的螺旋角β,然后再根据齿轮其它几何参数,计算出齿轮分度圆处的螺旋角β。
1) 什么是「模数」?模数表示轮齿的大小。
R模数是分度圆齿距与圆周率(π)之比,单位为毫米(mm)。
除模数外,表示轮齿大小的还有CP(周节:Circular pitch)与DP(径节:Diametral pitch)。
【参考】齿距是相邻两齿上相当点间的分度圆弧长。
2) 什么是「分度圆直径」?分度圆直径是齿轮的基准直径。
决定齿轮大小的两大要素是模数和齿数、分度圆直径等于齿数与模数(端面)的乘积。
过去,分度圆直径被称为基准节径。
最近,按ISO标准,统一称为分度圆直径。
渐开线齿轮的齿形齿向修整
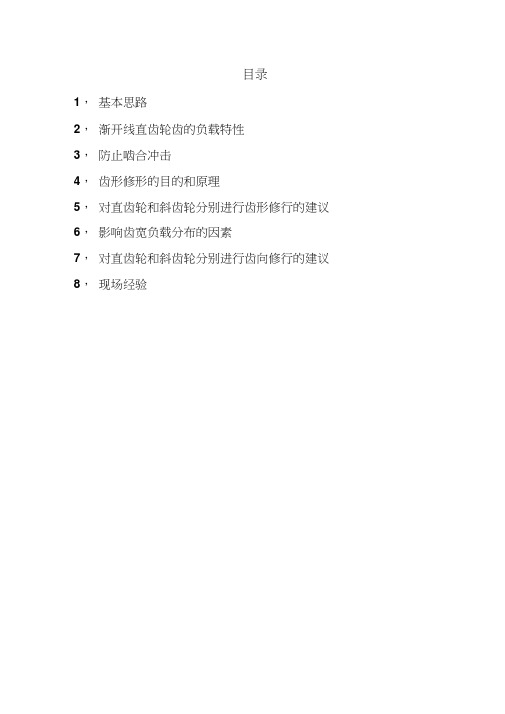
目录1,基本思路2,渐开线直齿轮齿的负载特性3,防止啮合冲击4,齿形修形的目的和原理5,对直齿轮和斜齿轮分别进行齿形修行的建议6,影响齿宽负载分布的因素7,对直齿轮和斜齿轮分别进行齿向修行的建议8,现场经验简介负载齿轮的传动试验研究表明,随着齿轮进入啮合和脱离啮合时,由于角速度脉动的变化而增加了啮合冲击。
啮合冲击,既使是制造很精确的齿轮也是难以避免的,因为这种冲击部分是由齿轮负载时的弹性变形引起的。
啮合冲击的强度决定于负载量以及齿的精确度和壳体内传动齿轮与从动齿轮的相互位置,其他影响因素还有如:节线速度,齿轮惯性矩,齿面质量和润滑情况等。
齿轮间的波动引起齿轮自身和齿轮轴及壳体的振动从而产生噪音。
只有当更高的速度和负载需求及传动噪音要求更高的情况非常紧急时,才能考虑采用通过齿形修行(齿顶,齿根修缘)减小啮合冲击。
一旦实施了热后磨齿,那么就能承载更高的传动负载,在这种情况下就要求进行齿形修行。
但是随着传动负载的增加,对齿向修行(或是鼓形修整)也就有了要求。
以下将对齿向修行做更深的说明。
虽然鼓形修整的主要目的是是齿宽的负载分布均匀,不过设计良好的鼓形修整还可以减小啮合冲击。
换句话说,也就是抵消各种与良好齿轮轴承条件相斥的影响。
两种类型的齿轮修行(齿形和齿向修行)的思路是不相同的。
因此本论文将分别对两种不同的修行模式进行说明。
通常,实际的修行量都比较小,不管是齿顶修缘,齿根修缘还是端面修缘,通常在7.62U到25.4 U之间。
尽管修行量很小,可在修行设计和应用良好的情况下,这一点点的修行可以提高齿面的负载能力。
然而,如果要求进行齿形修行以提高齿面负载力,那么必须修行确保达到最小制造精度。
从振幅的序方面考虑,如果齿形误差接近齿形修行量时,那么对齿轮啮合性能的改善就还有所怀疑,特别是当修行和误差同时出现时。
通常认为,如果要使用齿形和齿向修行的方法增加齿宽负载能力,那么必须确保在振幅上齿形误差比修行量小。
本文给予的建议都是基于专业的斜齿硬化和磨齿经验提出的。
齿轮修形p

整理课件
11
1.2常用修整方法
自从Walker于1938年最早发表的渐开线齿轮轮齿修整的论述开始, 数十年来,人们对齿廓修整得研究从来就没有停止过,已见公开发表的 公式已有数十种,更多的是许多公司作为内部资料未曾公开。
切变形和齿面接触变形等),因此,工作时,原本在常温无载荷状 态下沿齿宽方向均匀接触的状态被改变,载荷沿齿宽方向的分布会 很不均匀,甚至于会严重偏载。 •运转会产生热变形,特别是高速齿轮,温度沿齿宽方向升高且不均匀, 产生螺旋线偏差。 •制造误差,制造产生的螺旋线偏差、箱体轴承孔轴线的平行度偏差、; •箱体、轴、轴承、机架等受力后产生的变形引起轴心偏移,离心力造 成的径向位移等。
整理课件
6
整理课件
7
a)轮端面重合度 εα=1.2,
b) εα=1.8
图3 具有不同大小的单对齿啮合与双对齿啮合区时的名义载荷
整理课件
8
图4
整理课件
9
图4为理论载荷分布图,但是由于啮合点上齿面的接触变形、 齿的剪切变形和弯曲变形等因素的影响,使得在单齿啮合区的 载荷分布有所缓和。整个啮合过程中轮齿承担载荷的幅度大致 为:E点40%,B点从60%急剧跳到100%,BD段为100%,,D 点从100%急剧跳到60%,A点40%。由此可见,轮齿啮合过程 中有明显的载荷突变现象,相应也会引起轮齿弹性变形的明显 变化,引起主从动齿轮的齿距变化,使啮入初始点发生干涉现 象。
对增速传动,因从动小齿轮因温度高,压力角稍小,基齿距稍大, 会加剧轮齿受冲击的倾向。为此,从动小齿轮的齿顶B处,采用偏向 体内的公差带,即加大小齿轮的压力角,减小其基齿距。
齿轮的齿形齿向介绍精选幻灯片
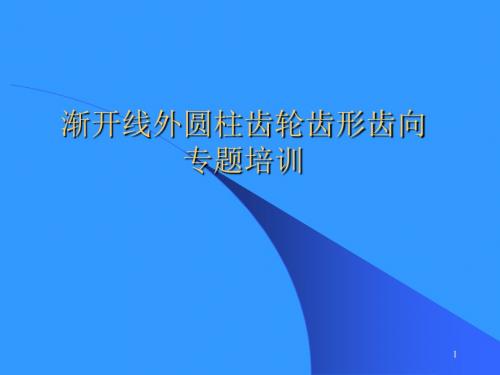
离,有正、负之分,齿向中线弧高向齿轮实体外偏离为“正”如 图示,反之为“负”即齿向中凹。
16
fsβ—齿向螺旋角误差变动量:齿向螺旋角误差最大值与最小值
之差。该项误差即是我们常讲的齿向乱不乱的问题,在齿向误 差数据表中没有反映,需评判人员计算,从该项误差可以反映 齿轮加工过程中刀具装夹和修磨误差、工装端跳和零件端跳是 否合格。
6
ff α——齿形形状误差(齿形波纹度):在齿形评价范围内,包容实际齿形线的两条平 行于齿形中线间的法向距离。
C α——齿形鼓形量:齿形中线两点间连线到齿形中线之间的最大距离,有正负之分, 齿形中线弧高向齿轮实体外偏离为“正”如图示,反之为“负”即齿形中凹,。
7
fsα——齿形压力角误差变动量:齿形压力角误差最大值与最小
附图三:(右旋)齿向检测图形(横式)
10
附图四:齿向检测图(纵式)
11
1)齿向图横座标:齿轮宽度方向的检测点长度尺寸,检测时齿 轮放置的下端为0基准(0~B齿宽度)。 2)齿向图纵座标:检测的计数齿数信息、左右齿面信息、齿向 误差每格数值(比列)、齿向误差。
12
3)齿向误差数据表:在数据表中有Fβ 、fHβ、 f f β 、C β误差数据。以右齿面齿向为例 Fβ——总齿向误差:在齿向评价范围内,包容实际齿向线的两条标准齿向线之间的距离。
从下图可以看出,用本公司评判标准判断出的齿向螺旋角误差,有 一个面就会与WENZEL检测仪评价的正负相反:左旋齿则左齿面相反, 右旋齿则右齿面相反。
江齿齿形修形标准对齿轮螺旋角误差正负判定原则与WENZEL判定原则 15 相同,即为“实体增加减小法”。
Cb—齿向鼓形量:齿向中线两点间连线到齿向中线之间的最大距
ቤተ መጻሕፍቲ ባይዱ
干货齿轮传动系统之齿轮修形原理及应用

⼲货齿轮传动系统之齿轮修形原理及应⽤作者:尚振国,刘辉,谢忠东,武⼒波,王迎春齿轮传动是⼀种应⽤最⼴的机械传动形式,具有传动效率⾼、结构紧凑等特点。
但由于不可避免地存在制造和安装误差,齿轮传动装置的振动和噪声往往较⼤,特别是在⼀些⼤功率传动装置中(如兆⽡级风⼒发电增速器、船⽤齿轮减速器等,以及对舒适性要求较⾼的传动装置中(如汽车变速箱等),振动和噪声问题尤为突出。
齿轮修形是降低齿轮传动装置振动和噪声的⼀种成熟⽽有效的技术,近年来获得了越来越⼴泛的应⽤。
齿轮修形包括齿廓修形和齿向修形,本研究中作者分别介绍了其基本原理以及应⽤情况。
齿廓修形1齿廓修形原理齿轮啮合传动过程中主、被动齿轮的基节必须处处相等,从理论上讲,精确的渐开线刚性齿轮是完全能够实现上述⽬标的。
但实际中的齿轮副均为弹性体,在⼀定啮合⼒作⽤下会产⽣相应的弹性变形,使处于啮合线位置的主动轮和被动轮基节出现变化,不再相等。
如图1(a)所⽰,当齿对2进⼊啮⼊位置时,由于齿对1的变形,主动轮基节Pb1⼩于被动轮基节Pb2,轮齿啮⼊点的啮合⼒骤然增⾼,形成了通常所说的啮⼊冲击。
与此类似,如图1(b)所⽰,在齿对1即将脱离啮合接触时,由于齿对2的变形,Pb1>Pb2,主动轮齿顶将沿被动轮齿根刮⾏,形成通常所说的啮出冲击。
为了消除轮齿啮⼊和啮出冲击,通常采⽤齿廓修形的⽅法,即沿齿⾼⽅向从齿⾯上去除⼀部分材料,从⽽改变齿廓形状,消除齿对在啮⼊、啮出位置的⼏何⼲涉。
图1 齿对在啮⼊、啮出位置的⼏何⼲涉2齿廓修形的效果分析齿廓修形的参数包括修形量、修形长度和修形曲线。
图2为某⼤型风⼒发电齿轮增速箱输出级宽斜齿轮副传动⽰意图,齿轮传动参数见表1。
作者应⽤有限元接触分析技术计算了未修形和不同修形参数下各啮合齿对上载荷分配情况。
在⼩齿轮齿顶修形量为0.025mm,齿根修形量为0.05mm,修形起点为单双齿啮合交替点,修形曲线采⽤⼆次曲线的情况下,各啮合齿对上载荷的分配情况见图3。