异种金属焊缝超声波检测讨论
浅谈异种钢对接焊缝的超声波检测方法
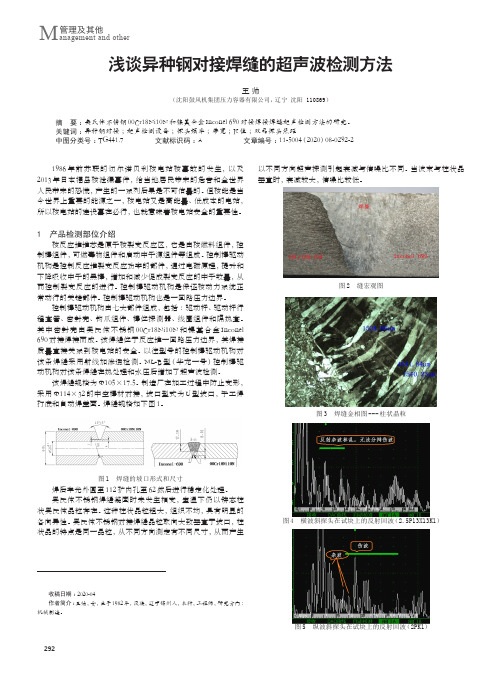
292管理及其他M anagement and other浅谈异种钢对接焊缝的超声波检测方法王 帅(沈阳鼓风机集团压力容器有限公司,辽宁 沈阳 110869)摘 要:奥氏体不锈钢00Cr18Ni10N 和镍基合金Inconel 690对接焊接焊缝超声检测方法的研究。
关键词:异种钢对接;超声检测设备;探头频率;带宽;K 值;双晶探头焦距中图分类号:TG441.7 文献标识码:A 文章编号:11-5004(2020)08-0292-2 收稿日期:2020-04作者简介:王帅,女,生于1982年,汉族,辽宁锦州人,本科,工程师,研究方向:机械制造。
1986年前苏联的切尔诺贝利核电站核事故的发生,以及2013年日本福岛核泄漏事件,给当地居民带来的危害和全世界人民带来的恐慌,产生的一系列后果是不可估量的。
但核能是当今世界上重要的能源之一,核电站又是高能量、低成本的电站,所以核电站的建设事在必行,也就意味着核电站安全的重要性。
1 产品检测部位介绍核反应堆堆芯是原子核裂变反应区,它是由核燃料组件,控制棒组件,可燃毒物组件和启动中子源组件等组成。
控制棒驱动机构是控制反应堆裂变反应功率的部件,通过电磁原理,提升和下降吸收中子的黑棒,增加和减少促成裂变反应的中子数量,从而控制裂变反应的进行。
控制棒驱动机构是保证核动力系统正常动行的关键部件。
控制棒驱动机构也是一回路压力边界。
控制棒驱动机构由七大部件组成,包括:驱动杆、驱动杆行程套管、密封壳、钩爪组件、棒位探测器、线圈组件和隔热套。
其中密封壳由奥氏体不锈钢00Cr18Ni10N 和镍基合金Inconel 690对接焊接而成。
该焊缝位于反应堆一回路压力边界,其焊接质量直接关系到核电站的安全。
以往型号的控制棒驱动机构对该条焊缝采用射线加渗透检测。
ML-B 型(华龙一号)控制棒驱动机构对该条焊缝在热处理和水压后增加了超声波检测。
该焊缝规格为Φ105×17.5。
制造厂在加工过程中防止变形,采用Φ114×32的中空棒材对接,坡口型式为U 型坡口,手工焊打底和自动焊盖面。
钢结构焊缝超声波检测探讨

钢结构焊缝超声波检测探讨摘要:在钢结构焊接过程中,应制定完善的管理方案,针对焊缝进行合理的检测,使用超声波检测方式开展管控活动,在提升钢结构焊缝质量的情况下,优化整体工作模式与体系,充分发挥超声波检测技术的积极作用,为其后续发展夯实基础。
关键词:钢结构;焊缝;超声波检测在钢结构焊缝检测工作中,应合理使用超声波检测方式开展工作,及时发现焊缝的质量问题,采取科学措施解决问题,在提升超声波检测技术应用效果的情况下,优化整体工作模式与机制。
一、钢结构焊缝缺陷类型分析(一)裂纹缺陷分析钢结构焊缝的裂纹缺陷,属于尖锐端头开口位移且存在连续性的断裂的可能,缺陷面呈现锯齿状,属于危险性缺陷。
其形成原因就是在焊接过程中或焊后,焊缝金属或焊缝热影响区出现了收缩的现象,在母材焊接的时候,加热均匀性存在问题,导致出现金属母材结构及应力的发生变化,出现了裂纹的现象。
(二)焊接通透性较差在钢结构焊接管理工作中,坡口位置受到母材熔化的影响,没有提升焊接的通透行,经常会出现焊接问题,无法全面提升整体工作效果。
且在日常管理工作中,没有进行充分的处理,经常会出现熔渣现象或是氧化物清除问题,在一定程度上,会导致焊缝的应用效率降低,如果没有进行科学研究与合理分析,将会影响钢结构焊缝的处理效果,无法满足当前的工作要求。
(四)夹渣问题分析在钢结构焊接的时候,熔池中熔渣没有浮出,还存留在焊缝中,引发焊缝的夹渣问题。
一些熔渣会残留在焊缝金属内,另一些熔渣会溢出焊缝金属表面,对于残留在焊缝金属内的熔渣,无法对其进行彻底的清除处理,甚至出现均匀性问题。
且在焊接工作中,没有及时对焊渣进行处理,焊缝中出现氧化物或是硫化物等夹杂物过量,致使焊缝质量下降,影响整体结构。
(五)气孔方面的缺陷问题对于钢结构焊接工作而言,经常会出现气孔缺陷问题,严重影响整体工作的合理实施。
气孔是在钢结构焊缝中的出现的球状孔洞,是焊缝熔池在冷却过程中,熔化金属结构中会折出气体,没有完全的浮出焊缝表面,凝固在焊接金属内形成的。
浅谈超声波焊缝探伤

浅谈焊缝超声波探伤之现状及提高检测可靠性的措施关键词:焊缝超声波探伤缺陷目前超声波探伤技术已发展成为无损检测的主要方法之一。
但迄今为止,国内外焊缝探伤的工艺、方法及质量标准的制定,往往注重超声波与缺陷的相互作用,而对评定缺陷的信号参数同缺陷实际危害程度的关系重视不够,所以只要求测比较容易测量的缺陷参数而对难以测量的缺陷参数(如壁厚方向的尺寸)则不作要求。
如从检验标准JBll52—8l、GBll345—89到JB4730—94,只对缺陷的当量、缺陷的指标长度、缺陷的定位有要求,而对缺陷的定性,及缺陷壁厚方向尺寸不作强制要求。
验收标准如蒸规、容规及电锅规、焊规只简单提出了验收内容如裂纹、未熔不允许、条渣气孔按尺大小来计,而不对验收标谁的来由及校据作陈述,探伤人员往往缺乏缺陷危害程度的概念,在实际检验中只是流于常规、机械性的操作及僵化的执行标准,不能对缺陷的三性(定量、定位)很好的加以分析判断,准确确定缺陷的危害程度。
本文将针对目前焊缝探伤中易疏忽的几个问题做一些探讨,以提高焊缝探伤的可靠性。
1.表面和近表面缺陷的漏检问题1.1检出率及危害性Ω取值范围在1.01~1.13,而F的取值一般不小于Ω。
由式(1)和(2)对比可知,对同一条裂纹,表面裂纹的等效尺寸至少是深埋时的两倍。
CVDA还明确规定,当缺陷到自由表面的最短表面的最短距离P1<0.4H(H为缺陷最大高度)时,则该缺陷简化为αH+P1的表面缺陷。
由上面CVDA对表面近表面、裂纹的等效尺寸计算可知,表面、近表面缺陷危害程度大,探伤人员应倍加关注。
1.2提高表面、近表面缺陷检出率的措施。
1.2.1焊缝表面的加工近年来制订的一些焊缝超声波探伤新标准采用划检验级别的方法。
作为解决焊缝检出概率的重要措施之一。
如我国的GB11345-89中的C级检验,也规定了焊缝余高要磨平。
但磨平的程度未明确规定:JB4730-94标准(压力容器无损检测标准)也提到了对于要求高的焊缝,根据实际需要可将缝余高磨平以利检测。
焊接接头的超声波检测技术研究
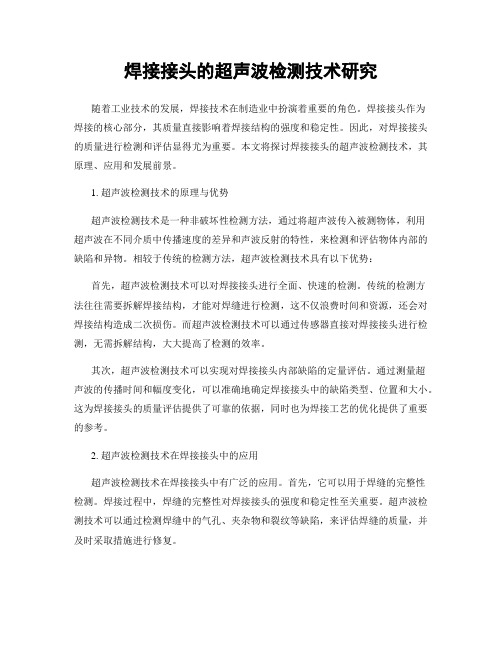
焊接接头的超声波检测技术研究随着工业技术的发展,焊接技术在制造业中扮演着重要的角色。
焊接接头作为焊接的核心部分,其质量直接影响着焊接结构的强度和稳定性。
因此,对焊接接头的质量进行检测和评估显得尤为重要。
本文将探讨焊接接头的超声波检测技术,其原理、应用和发展前景。
1. 超声波检测技术的原理与优势超声波检测技术是一种非破坏性检测方法,通过将超声波传入被测物体,利用超声波在不同介质中传播速度的差异和声波反射的特性,来检测和评估物体内部的缺陷和异物。
相较于传统的检测方法,超声波检测技术具有以下优势:首先,超声波检测技术可以对焊接接头进行全面、快速的检测。
传统的检测方法往往需要拆解焊接结构,才能对焊缝进行检测,这不仅浪费时间和资源,还会对焊接结构造成二次损伤。
而超声波检测技术可以通过传感器直接对焊接接头进行检测,无需拆解结构,大大提高了检测的效率。
其次,超声波检测技术可以实现对焊接接头内部缺陷的定量评估。
通过测量超声波的传播时间和幅度变化,可以准确地确定焊接接头中的缺陷类型、位置和大小。
这为焊接接头的质量评估提供了可靠的依据,同时也为焊接工艺的优化提供了重要的参考。
2. 超声波检测技术在焊接接头中的应用超声波检测技术在焊接接头中有广泛的应用。
首先,它可以用于焊缝的完整性检测。
焊接过程中,焊缝的完整性对焊接接头的强度和稳定性至关重要。
超声波检测技术可以通过检测焊缝中的气孔、夹杂物和裂纹等缺陷,来评估焊缝的质量,并及时采取措施进行修复。
其次,超声波检测技术可以用于焊接接头的质量控制。
在焊接生产过程中,超声波检测技术可以实时监测焊接接头的质量,并及时发现和排除潜在的缺陷。
这有助于提高焊接接头的质量稳定性,减少不合格品的产生,降低生产成本。
此外,超声波检测技术还可以用于焊接接头的损伤评估。
在焊接接头使用过程中,由于外部力的作用或者其他原因,焊接接头可能会出现损伤,如裂纹和疲劳断裂等。
超声波检测技术可以对这些损伤进行定量评估,为维修和更换提供依据。
超声波焊接镍/铝异种金属研究

超声波焊接镍/铝异种金属研究超声波焊接属于压焊,该方法是在静压力作用下利用超声波高频率的弹性机械振动把工件的弹性振动能转变成摩擦功与形变能,对工件进行清理和焊接。
超声波焊接主要用于连接金属材料、半导体材料、塑料和金属陶瓷等。
因为焊接速度快,焊接质量好、密封性好、焊接过程安全稳定等优点,超声波金属焊接在工业上得到了十分广泛的应用。
文章使用超声波焊接金属的方法对镍N4和铝1060焊接,研究了不同的焊接工艺参数对给接头显微组织带来的的影响。
改变焊接时间和焊接压力等焊接工艺参数对镍/铝异种金属进行焊接,最终确定焊接可焊范围为:焊接时间50~110ms,焊接压力0.25MPa~0.35MPa,接延时400ms。
将焊接时间取为50ms、80ms、110ms,焊接压力取为0.25ms、0.3ms、0.35ms,得到9组焊接参数,并分析了各参数下的焊件试样。
对试样进行镶嵌、打磨、抛光以及腐蚀,使其满足观察要求,再对焊件成形进行分析,比较得出最佳的焊接试样。
标签:超声波焊接;镍;铝;显微组织引言随着有色金属应用的日益广泛,其连接技术也随之备受关注。
工业纯镍具有优异的耐腐蚀性,在工业生产中,纯镍主要用来制造不锈钢以及其他抗腐蚀合金,也用来做加氢催化剂以及陶瓷产品、电子线路、玻璃着绿色和制备Ni的化合物等。
所以,优化纯镍材料的焊接工艺、控制焊接缺陷是保证设备制造质量的关键环节。
纯镍的液态凝固过程没有相变,非常容易生成低熔点的共晶体,出现热裂纹等缺陷;在传统焊接过程中,焊接快速冷却凝固过程极易出现裂纹、气孔以及晶粒粗大等缺陷,严重影响焊接接头的耐腐蚀性能与机械性能。
铝的密度小、延展性好,耐蚀、导热以及导电等性能优良,而且在很低的温度下依然能够得到满意的力学性能,在化工、机械、交通、建筑、航空航天、日常生产生活等领域得到了广泛的普及。
铝极易形成致密的Al2O3氧化膜,吸附水分,在传统焊接过程中易造成焊缝夹杂与气孔。
这些都是焊接生产中颇感困难的问题。
异种金属焊缝超声波检测讨论

夹角有关 • 被散射的超声波沿着复杂的路径传播倒探头
时,在显示屏上引起草状回波,使信噪比下降 ,严重时噪声信号会淹没缺陷信号 • 手工PE检测时通常使用双晶纵波斜探头
二、焊缝的特点及对超声波的影响
二、焊缝的特点及对超声波的影响
2.3 对超声波的影响——改变传播方向 • 金属结构的各向异性导致超声波的传播方
三、产品技术要求
对比试块的要求
• 厚度允许误差:——厚度≤50mm的,为±20%;
>50mm的,为±10mm。
——厚度
• 曲率半径:与被检工件偏差±25%
• 人工反射体
——平行于其扫查面的横孔,直径为2mm
——第一个孔低于扫查面10mm
——后备孔深度差最大 20mm
——所有反射体位置应距两端至少各20mm
一一从没有堆焊层的表面,沿方向1~4、9~ 10检验;
——属于原先所用探头盲区区域的补充检验
应采用浅盲区探头沿1、3、9、10方向进行
• 直射纵波扫查有一个面不能接近或要检验有整个精加 工的不锈钢或高镍合金堆焊层的部件时,可以:
向扫查
——从没有堆焊层或可接近的表面沿13方
——属于原先所用探头盲区区域的补充检 验,应采用浅盲区探头从13方向进行
向改变 • 由于母材、隔离层、焊缝的异种界面和焊
缝材料的各向异性的影响,会导致超声波 传播过程中产生声束的偏转
二、焊缝的特点及对超声波的影响
二、焊缝的特点及对超声波的影响
2.4对超声波的影响——频率降低 • 射线检测时射线束穿过工件后线质变硬 • 当超声波探头接收到从缺陷上返回的超声
波时,信号频率通常低于发射时超声波的 频率 • 这是材料对超声波产生低通滤波的影响 • 材料晶粒粗大时,低通滤波效应变大
钢结构焊缝超声波探伤测试存在的问题与管控措施分析
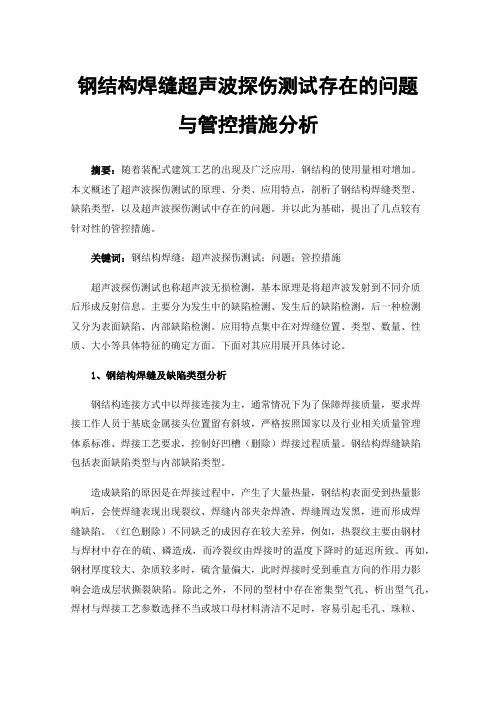
钢结构焊缝超声波探伤测试存在的问题与管控措施分析摘要:随着装配式建筑工艺的出现及广泛应用,钢结构的使用量相对增加。
本文概述了超声波探伤测试的原理、分类、应用特点,剖析了钢结构焊缝类型、缺陷类型,以及超声波探伤测试中存在的问题。
并以此为基础,提出了几点较有针对性的管控措施。
关键词:钢结构焊缝;超声波探伤测试;问题;管控措施超声波探伤测试也称超声波无损检测,基本原理是将超声波发射到不同介质后形成反射信息。
主要分为发生中的缺陷检测、发生后的缺陷检测,后一种检测又分为表面缺陷、内部缺陷检测。
应用特点集中在对焊缝位置、类型、数量、性质、大小等具体特征的确定方面。
下面对其应用展开具体讨论。
1、钢结构焊缝及缺陷类型分析钢结构连接方式中以焊接连接为主,通常情况下为了保障焊接质量,要求焊接工作人员于基底金属接头位置留有斜坡,严格按照国家以及行业相关质量管理体系标准、焊接工艺要求,控制好凹槽(删除)焊接过程质量。
钢结构焊缝缺陷包括表面缺陷类型与内部缺陷类型。
造成缺陷的原因是在焊接过程中,产生了大量热量,钢结构表面受到热量影响后,会使焊缝表现出现裂纹、焊缝内部夹杂焊渣、焊缝周边发黑,进而形成焊缝缺陷。
(红色删除)不同缺乏的成因存在较大差异,例如,热裂纹主要由钢材与焊材中存在的硫、磷造成,而冷裂纹由焊接时的温度下降时的延迟所致。
再如,钢材厚度较大、杂质较多时,硫含量偏大,此时焊接时受到垂直方向的作用力影响会造成层状撕裂缺陷。
除此之外,不同的型材中存在密集型气孔、析出型气孔,焊材与焊接工艺参数选择不当或坡口母材料清洁不足时,容易引起毛孔、珠粒、孔隙度大等缺陷。
其中,表面缺陷主要包括毛孔、焊接珠粒、表面燃烧等等,内部缺陷主要表现为焊接裂缝、焊接孔隙度、焊接泄漏、焊渣夹杂物等。
2、钢结构焊缝超声波探伤测试存在的问题2.1技术方案研发设计水平低目前,在钢结构焊缝无损检测中,超声波探伤测试效果较好,应用相对地普遍。
尤其从2018年开始实施“互联网+”改革后,钢结构焊接施工中进一步强化了对该技术的应用,通过数据采集、传输、存储、抽取、分析、利用等完整的数据化管理方式,扩增了该技术的应用效果。
超声相控阵在异种钢焊缝检测中的应用
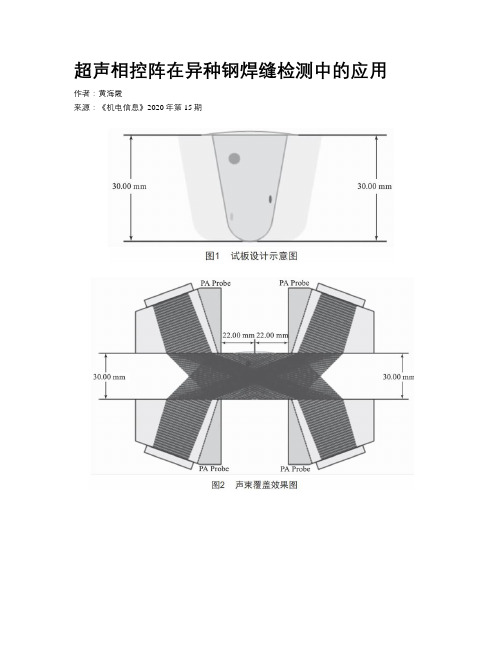
超声相控阵在异种钢焊缝检测中的应用作者:黄海霞来源:《机电信息》2020年第15期摘要:异种钢焊缝深刻影响着整体结构的安全,因此必须对焊接质量进行严格的检测,防止由于缺陷的存在而带来的严重后果。
异种钢焊缝通常具有形状不规则的特点,采用传统的超声波检测技术很难进行准确检测。
超声相控阵由于可以偏转和聚焦,因而在异种钢焊缝检测中得到了广泛的应用。
现通过实验手段对超声相控阵在异种钢焊缝检测中的应用进行了详细探讨,对常见缺陷的超声反射回波进行了分析。
实验结果表明:超声相控检测技术可以较好地满足异种钢焊缝检测的要求。
关键词:超声相控阵;异种钢焊接;焊缝检测0; ; 引言随着各类设备和材料的增加,不同材料之间的组合应用日益普遍,尤其是钢材的对接使用更是常见。
钢材对接会遇到异种钢焊接问题,由于不同种类的钢材料在物理、化学等特性上有明显的区别,二者之间的焊接成为应用的难点之一[1]。
无损检测技术是检测焊缝质量的主要技术,其中超声技术由于环保便捷而成为最主要的无损检测技术之一。
随着技术的发展,焊缝质量检测的要求也在不断提高,超声相控阵的应用更加广泛,并且技术日益成熟。
超声相控阵的出现,使焊缝缺陷可以通过二维成像结果清晰地显示出来,大大提高了检测的效率和可靠性。
本文通过实验手段对超声相控阵在异种钢焊缝检测中的应用进行了详细探讨,具有重要的现实意义。
1; ; 超声相控阵的原理及优势超声检测技术是工业无损检测四大常规技术中的重要一员,超声相控阵则是传统超声波检测技术的进一步发展,它已成为提高无损检测效率和质量的重要手段。
超声检测主要是利用了声波的反射现象进行材料缺陷的识别,是声学领域的重要应用方向。
超声探头中的压电晶片在电场的作用下发出高频振动,振动由探头传播出来后形成超声波,超声波在穿透材料的过程中,一旦遇到不规则的介质,其正常传播就会受到干扰,造成部分声波被吸收或反射回来,探头接收反射或透射的声场后通过仪器显示出来,即可分析出工件内部的缺陷信息[2]。
- 1、下载文档前请自行甄别文档内容的完整性,平台不提供额外的编辑、内容补充、找答案等附加服务。
- 2、"仅部分预览"的文档,不可在线预览部分如存在完整性等问题,可反馈申请退款(可完整预览的文档不适用该条件!)。
- 3、如文档侵犯您的权益,请联系客服反馈,我们会尽快为您处理(人工客服工作时间:9:00-18:30)。
三、产品技术要求
对比试块的要求
• 厚度允许误差:——厚度≤50mm的,为±20%;
>50mm的,为±10mm。
——厚度
• 曲率半径:与被检工件偏差±25%
• 人工反射体
——平行于其扫查面的横孔,直径为2mm
——第一个孔低于扫查面10mm
——后备孔深度差最大 20mm
——所有反射体位置应距两端至少各20mm
三、产品技术要求
• 按照上述要求的探头和扫查方向,用试 块上人工反射体做出基准线(DAC)
• 需记录的最小信号为20%DAC,记录的最 小信号与噪声之间的信噪比要求为3:1
• 即DAC提高14dB(使记录的最小信号达到 基准波幅),再提高9.5 dB(使允许的最大 噪声信号达到基准波幅)
• 此时如果任意的噪声信号均不超过基准 波幅,则检测系统的性能满足要求
二、焊缝的特点及对超声波的影响
针对材质为 ERNiCrFe-7的 异种金属焊 缝,我们制 作了与产品 的焊缝结构 和焊接工艺 相同的试块 进行试验
二、焊缝的特点及对超声波的影响
2.2 对超声波的影响——衰减 • 超声波在传播过程中的衰减主要有散射衰减
和吸收衰减 • 由于异种金属焊缝的介质晶粒较大且具有各
• 上述试验效果主要受聚焦范围和曲率的影响, 自己采购时 ,应明确提出以上参数
四、试验结果
• 针对异种钢奥氏体粗晶焊缝,无论是手动 PE检测,还是自动检测,均需要先进行可探 性试验
• 确定出可探区域后,再对这些区域进行检 测
• 普通的低合金钢和碳钢焊缝检测通常是不 需要进行可探性试验这一步骤的
• 对于这种粗晶焊缝内部质量的控制,主要 还应由射线来保证,超声可以作为辅助的手 段
三、产品技术要求
1)应在同一表面上从焊缝两侧进行扫查(ASME第Ⅴ卷,T441.1.3 )
2)应用斜探头从垂直于焊缝轴线和沿焊缝轴线两个方向进行扫查 ,且应从焊缝两个相对方向及平行于焊缝两个相对方向扫查( ASME第Ⅴ卷,T441.1.4)
3)扫查取向平行于焊缝的反射体时,斜探头应垂直对准焊缝轴线 ,且探头的操作应能使超声波扫过整个焊缝金属(ASME第Ⅴ卷 ,T441.1.5)
四、试验结果
• 探头:06-1486 longwave37° TRL1-Aust 2(15×25)C SA5°,FS-60,OR428AX
• 探头:06-1489 longwave45° TR1.5-Aust 2(15×25)C SA6°,FS-17,OR428AX
• 探头的参数有:频率、晶片数量和尺寸、角度 、聚焦范围、曲率
一一从没有堆焊层的表面,沿方向1~4、9~ 10检验;
——属于原先所用探头盲区区域的补充检验
应采用浅盲区探头沿1、3、9、10方向进行
• 直射纵波扫查有一个面不能接近或要检验有整个精加 工的不锈钢或高镍合金堆焊层的部件时,可以:
向扫查
——从没有堆焊层或可接近的表面沿13方
——属于原先所用探头盲区区域的补充检 验,应采用浅盲区探头从13方向进行
向改变 • 由于母材、隔离层、焊缝的异种界面和焊
缝材料的各向异性的影响,会导致超声波 传播过程中产生声束的偏转
二、焊缝的特点及对超声波的影响
二、焊缝的特点及对超声波的影响
2.4对超声波的影响——频率降低 • 射线检测时射线束穿过工件后线质变硬 • 当超声波探头接收到从缺陷上返回的超声
波时,信号频率通常低于发射时超声波的 频率 • 这是材料对超声波产生低通滤波的影响 • 材料晶粒粗大时,低通滤波效应变大
4.3非相关显示 对于具体的扫查计划、焊缝结构和坡口角度、超声波在
不同材料中传播的声速,存在一些非相关显示,应针对具体
情况进行分析。
四、试验结果
4.3非相关显示——结构引起的
四、试验结果
4.3非相关显示——波型转换
四、试验结果
• 在焊缝两侧的母材进行轴向扫查,由于 声束多是穿过母材,所以信噪比较好
• 探头骑在焊缝上进行周向扫查时,声束 多是穿过焊缝或预堆层,灵敏度和信噪比 较低
• 轴向扫查时,基准Φ2mm横孔时,灵敏度 余量和信噪比没问题,但是提高12dB后有 问题
• 轴向扫查时,基准Φ4.8mm横孔时,灵敏 度余量和信噪比没问题,但是提高23.5dB
二、焊缝的特点及对超声波的影响
• 镍基异种钢焊缝对超声波的衰减很大 • 超声波可探测的最大深度应由试块上最深
的人工孔确定
• 当试块上人工缺陷的深度无法覆盖工件厚 度时,则无法保证工件上未覆盖区域的检 测灵敏度
• 设计试块时应保证人工缺陷的设置覆盖整 个被检工件厚度
二、焊缝的特点及对超声波的影响
2.6镍基焊缝易产生的缺陷(举例)
• 有带表性的是 RPV和SG的安全端焊缝,其 两侧母材分别是碳钢和不锈钢,焊缝由镍 基(或不锈钢)隔离层和镍基(或不锈钢 )焊缝组成
一、异种金属焊缝介绍
SG安全端焊缝
一、异种金属焊缝介绍
反应堆压力容器的安全端
一、异种金属焊缝介绍
RPV 安全端异种金属焊缝
一、异种金属焊缝介绍
• 镍基异种金属焊缝低倍照片如下图所示
四、试验结果
• 使用低频纵波双晶探头,频带宽度较宽 • 检测粗晶焊缝时,应根据实际情况综合多
种因素来识别缺陷,如缺陷的反射波高、 动态波型的稳定程度、B扫描时信号颜色对 比度、分布位置 、密集程度等 • 不同的厂家、焊接工艺、焊缝结构,深度 上和焊缝宽度上的盲区位置都不相同 • 针对各具体情况,试块最好是专用
向异性,会导致严重的散射 • 散射的强弱和超声波声束与晶粒轴线之间的
夹角有关 • 被散射的超声波沿着复杂的路径传播倒探头
时,在显示屏上引起草状回波,使信噪比下降 ,严重时噪声信号会淹没缺陷信号 • 手工PE检测时通常使用双晶纵波斜探头
二、焊缝的特点及对超声波的影响
二、焊缝的特点及对超声波的影响
2.3 对超声波的影响——改变传播方向 • 金属结构的各向异性导致超声波的传播方
三、产品技术要求
3.2ASME标准相关的规定 方法标准:ASME V卷 验收标准:ASME III卷 NB-5000
ASME XI卷IWB-2500。 检验方法:采用直探头、斜探头接触法。
校准方法:对比试块法。
基准灵敏度:在对比试块的横孔(Φ4.8mm),记 录限为基准反射波幅的在提高14dB,信噪比9.5dB
• 需针对具体的焊接工艺与坡口形式去制 作试块
二、焊缝的特点及对超声波的影响
• 由于粗晶结构对超声波的衰减很大,林状 回波的出现也会降低信噪比
• 当超声波穿过异种金属焊缝界面时所产生 的折射会使超声传播路径发生崎变
• 焊缝的粗大晶粒和各向异性也会使超声传 播路径发生崎变
• 这些因素都会给超声检测和缺陷定位造成 困难
二、焊缝的特点及对超声波的影响
2.5对超声波的影响——试块
• 国、内外标准中,要求焊缝试块的厚度与 工件一致,或在一定的偏差范围内
• 试块上人工缺陷的最大深度则小于工件厚 度
• 如在ASME标准中,焊缝试块上横孔的最大 深度位于试块厚度的3/4处
• 这种情况仅适用于被探测材料的衰减系数 较小的情况
四、试验结果
4.1使用常规的手动超声检测方式进行试验
四、试验结果
四、试验结果
第一步,我们首先制作模拟安全端焊缝的探伤试 块,然后制定试验计划。
第二步:选择试验仪器: 所用设备:为CTS-22型超声波探伤仪。 探头:荷兰RTD粗晶焊缝检测用探头。 第三步:在探伤试块上进行可行性探伤试验,确
定探头能覆盖的区域,而且要保证该区域检测 时的信噪比≥6dB。 第四步:第二步与第三步反复进行,确定最好的 试验条件与可探测区域。
4)扫查取向垂直于焊缝的反射体时,斜探头应对准平行于焊缝轴 线的方向,探头的操作应能使超声波扫过整个焊缝金属(ASME 第Ⅴ卷,T441.1.6)
5)一般应用45°、60°、70°三种角度探头进行检测(ASME第Ⅴ 卷,I-20)
6)扫查时,应将增益调整到比起始参考水平至少大一倍的位置, 应当参照起始参考水平做出评定(ASME第Ⅴ卷,T542.7.2.3, T542.7.2.4)
——B1SE:覆盖深度范围10~30mm,内外表面检测 ——SEB2H(或SEB4H):覆盖深度范围0~20mm 内外表面检测 • 37°纵波斜探头: ——Longwave37 °TRL1-Aust 2(15×25) Flat:外表 面周向扫查,覆盖深度范围0~30mm。 ——Longwave37 °TRL1-Aust 2(15×25)IR350AX: 内表面周向扫查,覆盖深度范围0~60mm
• 我们的试验主要以核压力容器安全端镍 基异种钢焊缝为主
一、异种金属焊缝介绍
压力容器的安全端镍基焊缝的特点 有:
• 在焊缝金属凝固期间生成纤维状或树枝 状晶体,焊缝晶粒尺寸大
• 在某一特殊方位上晶体生长占优势,具 有各向异性的特征
• 特别需要强调的是焊接工艺与坡口形式 对镍基焊缝的晶粒组织影响很大
• 如某一反应堆压力容器安全端坡口深度约92mm ,属于大厚度异种金属焊接,须采用窄间隙坡 口。
• 接管与安全端焊缝,焊后收缩应力大,易在镍 基隔离层与内壁不锈钢堆焊接触部位出现裂纹 、未熔合等焊接缺陷,质量难于控制
• 我们了解国内外很多知名企业都在安全端焊接 过程中出现过失误
三、产品技术要求
• 目前世界上核电制造和检测有两个标准体 系:法国RCC-M标准和美国ASME标准
四、试验结果
• 45°纵波斜探头: ——VRY45:外表面轴向扫查,覆盖全部深度范
围;内表面轴向扫查,覆盖深度范围0~60mm; ——VSY45,外表面轴向扫查,覆盖深度范围
0~15mm • 60°纵波斜探头:
——VRY60:内、外表面轴向扫查,覆盖深度范 围0~20mm;内表面周向扫查,覆盖深度范围0~ 20mm ——VSY60,外表面轴向扫查,覆盖深度范围 0~10mm