汽车典型零部件用材料的发展途径
乘用车车身零部件轻量化设计典型案例

乘用车车身零部件轻量化设计典型案例随着环境保护意识的提高和汽车工业的快速发展,乘用车的车身零部件轻量化设计成为了汽车制造业的一个重要课题。
轻量化设计不仅可以降低车辆的整体重量,提高燃油经济性,还可以减少对环境的影响。
下面将介绍几个乘用车车身零部件轻量化设计的典型案例。
1. 利用高强度材料:使用高强度的材料可以在不增加重量的情况下提高零部件的强度和刚性。
例如,许多乘用车现在采用了高强度钢材来替代传统的钢材。
高强度钢材可以提供相同强度的零部件,但重量更轻。
此外,还有一些先进的复合材料,如碳纤维增强塑料(CFRP)和铝合金等,也被广泛应用于车身零部件的制造中。
2. 结构优化设计:通过采用结构优化设计方法,可以将零部件的结构进行优化,以减少不必要的材料使用,从而降低整体重量。
例如,在车身的设计过程中,可以使用拓扑优化方法来确定最佳的结构形状,以最小化材料的使用量。
3. 部分集成设计:通过将不同的零部件进行部分集成设计,可以减少连接部件的数量,降低整体重量。
例如,一些车辆现在采用了一体成型的车顶和车身侧板设计,通过减少连接接口,可以减轻车身重量。
4. 利用轻量化技术:现代乘用车越来越多地采用一些先进的轻量化技术来设计车身零部件。
例如,采用铝合金替代传统的钢材可以显著减轻车身重量。
此外,还有一些其他的轻量化技术,如混合材料结构、可变厚度设计和3D打印等,也被广泛应用于乘用车的车身零部件设计中。
总之,乘用车车身零部件轻量化设计是当前汽车制造业的一个重要课题。
通过使用高强度材料、结构优化设计、部分集成设计和轻量化技术等方法,可以实现乘用车的轻量化,降低车辆油耗,减少对环境的影响。
这些典型案例的应用不仅可以提高汽车的性能和节能性,还可以为未来的汽车制造业发展提供借鉴和启示。
第50问:五大工程塑料在汽车领域有哪些应用?

第50问五大工程塑料在汽车领域有哪些应用?工程塑料用于汽车的主要作用是使汽车轻量化,从而达到节油高速的目的。
发达国家将汽车用塑料量作为衡量汽车设计和制造水平高低的一个重要标志,世界上汽车塑料单用量最大的是德国,塑料用量占整体材料的15%。
近年来我国汽车产业发展迅速,目前汽车年产量超过2702万辆,按照国外塑料用量预测,汽车行业年用改性塑料在350万吨以上,这其中工程塑料占了很大一部分比例,五大工程塑料性能特性各不相同,在汽车上的用途也各有偏重。
一、尼龙PA:尼龙主要用于汽车发动机、马达转子及发动机周边部件,主要品种是PA6+GF、PA66+GF、增强阻燃PA6等产品。
(1)在汽车发动机周边部件上的应用:由于发动机周边部件主要是发热和振动部件,其部件所用材料大多数是玻纤增强尼龙。
这是因为尼龙具有较好的综合性能,用玻纤改性后的尼龙,主要性能得到很大的提高,如强度、制品精度、尺寸稳定性等均有很大的提高。
另外,尼龙的品种多,较易回收循环利用,价格相对便宜等,这些因素促成尼龙成为发动机周边部件的理想选择材料。
进气歧管是改性尼龙在汽车中最为典型的应用,1990年德国宝马汽车公司,首先将以玻纤增强尼龙为原料制造的进气歧管应用在六汽缸发动机上;以后美国福特与杜邦公司合作,共同用玻纤增强PA66制造的进气歧管应用在V6发动机上,以后世界各大汽车公司纷纷跟进,改性尼龙进气歧管得到广泛的应用。
(2)在汽车发动机部件上的应用:发动机盖,发动机装饰盖,汽缸头盖等部件一般都用改性尼龙作为首选材料,与金属材质相比,以汽缸头盖为例质量减轻50%,成本降低30%。
除了发动机部件外,汽车的其他受力部件也可使用增强尼龙,如机油滤清器,刮雨器,散热器格栅等。
尼龙的韧性、化学惰性、耐热性和低重量特定是其在汽车配件领域能够替代金属和其它塑料。
通过变化增强等级和聚合物化学性质,树脂生产者可以为指定用途设计配方。
与尼龙相比,热固性聚合物在某些汽车配件领域依然具有相当的竞争力,尤其是在北美。
高分子材料在汽车轻量化中的应用

高分子材料在汽车轻量化中的应用在当今汽车工业的发展中,轻量化已经成为了一个至关重要的课题。
随着环保法规的日益严格和消费者对燃油经济性的更高要求,汽车制造商们纷纷寻求各种方法来减轻车辆的重量,而高分子材料的应用便是其中一项关键的技术手段。
高分子材料,简单来说,就是由大量重复单元组成的大分子化合物。
常见的高分子材料包括塑料、橡胶、纤维等。
这些材料具有许多优异的性能,如重量轻、强度高、耐腐蚀、易于加工成型等,使得它们在汽车轻量化领域中发挥着越来越重要的作用。
首先,塑料在汽车中的应用十分广泛。
汽车内饰件,如仪表盘、门板、座椅靠背等,大量采用了塑料材料。
与传统的金属材料相比,塑料不仅重量轻,还能够通过注塑成型等工艺实现复杂的形状和结构,满足汽车设计的多样化需求。
同时,一些高性能的工程塑料,如聚碳酸酯(PC)、聚酰胺(PA)、聚苯醚(PPO)等,具有出色的机械性能和耐热性能,可以用于制造汽车的发动机周边部件、电子电器部件等。
例如,PC 材料常用于制造汽车灯罩,其良好的透光性和耐冲击性能够保证车灯的照明效果和安全性;PA 材料则可用于制造进气歧管,其耐高温和高强度的特点能够适应发动机舱内的恶劣环境。
橡胶也是汽车中不可或缺的高分子材料之一。
轮胎是橡胶在汽车上最典型的应用。
现代轮胎通常采用合成橡胶,如丁苯橡胶(SBR)、顺丁橡胶(BR)、丁基橡胶(IIR)等,与天然橡胶混合使用,以获得良好的耐磨性、抗老化性和抓地力。
此外,橡胶还用于制造汽车的密封件、减震件等。
密封件能够防止液体和气体的泄漏,保证汽车的正常运行;减震件则可以减少车辆行驶过程中的震动和噪声,提高乘坐舒适性。
纤维增强复合材料是近年来在汽车轻量化领域中发展迅速的一种高分子材料。
这类材料通常由纤维(如碳纤维、玻璃纤维等)和树脂基体(如环氧树脂、不饱和聚酯树脂等)组成。
纤维提供了高强度和高模量,而树脂基体则将纤维粘结在一起,并赋予材料一定的韧性和耐腐蚀性。
碳纤维增强复合材料具有极高的强度和刚度,同时重量非常轻,因此被广泛应用于高端汽车的车身结构件、底盘部件等。
汽车典型零件加工工艺

汽车典型零件加工工艺随着汽车工业的发展,汽车典型零件加工工艺也越来越重要。
汽车典型零件加工工艺是指对汽车零件进行加工和制造的一系列工程技术过程。
本文将介绍汽车典型零件加工工艺的一些常见内容。
一、铸造工艺铸造是汽车典型零件加工工艺中常用的一种方法。
它通过将熔化的金属注入到模具中,待冷却凝固后,得到所需形状的零件。
铸造工艺可以制造出复杂形状的零件,如汽车发动机缸体、曲轴箱等。
常见的铸造工艺包括砂型铸造、压力铸造和失蜡铸造等。
二、加工工艺加工工艺是汽车典型零件加工工艺中最常见的方法之一。
它包括车削、铣削、钻削、磨削等多种加工方式。
通过这些加工工艺,可以对金属材料进行切削、磨削、钻孔等操作,得到所需形状和尺寸的零件。
加工工艺广泛应用于汽车零部件的制造过程中,如发动机曲轴、齿轮、轴承座等。
三、焊接工艺焊接工艺是将不同零件通过加热或压力使其熔合在一起的方法。
在汽车典型零件加工工艺中,焊接工艺常用于连接金属零件,如车身焊接、车架焊接等。
常见的焊接工艺有电弧焊、气体保护焊、激光焊等。
焊接工艺可以使零件连接牢固,提高汽车的结构强度和安全性。
四、涂装工艺涂装工艺是汽车制造过程中不可或缺的一环。
它通过在零件表面涂覆一层颜料或涂料,起到美观、防腐和保护作用。
涂装工艺包括底漆喷涂、面漆喷涂、烤漆等。
涂装工艺在汽车零部件制造中广泛应用,如车身、车门、引擎盖等。
五、装配工艺装配工艺是将各个零件按照一定的顺序和方式组装成完整的汽车的工艺过程。
装配工艺包括零部件的配对、定位、固定等操作。
装配工艺要求精度高,工艺流程清晰,以确保汽车的质量和性能。
常见的装配工艺有机械装配、焊接装配、胶接装配等。
六、检测工艺检测工艺是汽车典型零件加工工艺中不可或缺的环节。
它通过对零件的尺寸、形状、材料等进行检测和测试,以确保零件符合要求。
常见的检测工艺有三坐标测量、硬度测试、超声波探伤等。
检测工艺可以及时发现零件的缺陷和问题,提高汽车的质量和可靠性。
汽车高强度钢材技术的发展
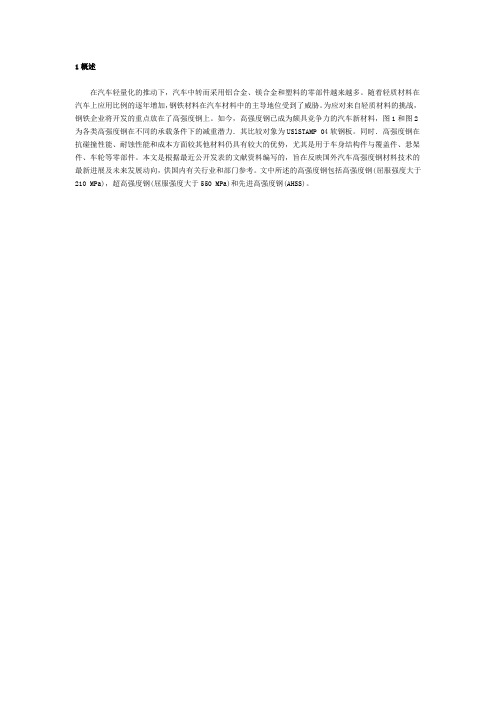
1概述在汽车轻量化的推动下,汽车中转而采用铝合金、镁合金和塑料的零部件越来越多。
随着轻质材料在汽车上应用比例的逐年增加,钢铁材料在汽车材料中的主导地位受到了威胁。
为应对来自轻质材料的挑战,钢铁企业将开发的重点放在了高强度钢上。
如今,高强度钢已成为颇具竞争力的汽车新材料,图1和图2为各类高强度钢在不同的承载条件下的减重潜力.其比较对象为USlSTAMP 04软钢板。
同时.高强度钢在抗碰撞性能、耐蚀性能和成本方面较其他材料仍具有较大的优势,尤其是用于车身结构件与覆盖件、悬架件、车轮等零部件。
本文是根据最近公开发表的文献资料编写的,旨在反映国外汽车高强度钢材料技术的最新进展及未来发展动向,供国内有关行业和部门参考。
文中所述的高强度钢包括高强度钢(屈服强度大于210 MPa),超高强度钢(屈服强度大于550 MPa)和先进高强度钢(AHSS)。
2主要技术进展超轻车身(ULSAB)、超轻覆盖件(ULSAC)、超轻悬架系统(ULSAS)和新概念超轻车身(ULSAB-AVC)等项目的成功实施,验证了高强度钢在减轻汽车自重和改善车辆性能中的有效性。
为了将这些项目所取得的技术成果转化为现实的生产力,近期的高强度钢技术研究,主要集中在支撑技术(Enabling Technologies)上。
2.1若干高强度钢的开发当前正处于新一代高强度钢开发的前夜。
从冶金学的角度看,近几年高强度钢材料的开发,大多只是对原有钢种牌号的补充或性能改善,厚度进一步减薄,材料本身并未取得突破性进展。
开发的难点是要针对不同的零件,力求在产品的强度、塑性和成本之间取得平衡。
SFGHITEN、NANOHITEN、ERW和HISTORY是日本JFE公司最近开发出的几种高强度钢。
其中SFGHITEN为含Nb系列高强度IF钢板,主要应用对象是汽车车身外板,研究用钢的化学成分见表1。
SFGHITEN利用析出的Nb(C,N)微粒和细化晶粒得到强化,其独特之处在于晶界附近存在所谓“无沉淀区”,它降低了材料的屈服强度。
汽车零部件开发流程

汽车零部件开发流程汽车零部件开发过程是一个复杂而精细的过程,需要经历多个阶段,包括需求分析、设计、制造、测试和验证等环节。
以下是汽车零部件开发的典型流程。
首先是需求分析阶段。
在此阶段,开发团队与客户或产品经理进行讨论和交流,明确零部件的功能、性能和技术要求。
同时,对市场需求、竞争状况和法规要求进行调研,确定产品的定位和市场前景。
接下来是设计阶段。
在此阶段,开发团队将根据需求分析阶段的要求,进行零部件的结构设计、工艺设计和材料选择。
设计团队需要采用CAD软件进行三维设计,并进行结构强度和功能仿真分析。
同时,还要考虑生产工艺和成本的因素,以确保设计的可制造性和经济性。
在设计阶段完成后,进入制造阶段。
在此阶段,需要进行样品的制造和试验,包括手工制作样品和进行数控加工。
此外,还需要对零部件进行加工工艺和工艺路线的规划,并制定生产计划。
制造阶段还包括供应商和生产线的选择、工艺能力的评估和生产线的调试。
随后是测试和验证阶段。
在此阶段,需要对零部件进行各种性能和功能测试,包括静态强度测试、动态载荷测试和环境适应性测试等。
测试结果将与需求分析阶段的要求进行对比,以验证产品的设计和制造质量。
同时,还要进行可靠性评估和寿命试验,以确保产品的质量和可靠性。
最后是产品发布阶段。
在通过测试和验证后,产品将进行批量生产,并进行销售和售后服务。
此阶段还包括市场推广、产品宣传和销售团队的培训。
同时,还需要建立售后服务体系,包括维修手册、技术培训和售后支持。
总结来说,汽车零部件的开发流程包括需求分析、设计、制造、测试和验证以及产品发布等多个环节。
每个环节都需要进行细致而科学的规划和执行,以确保产品的质量和市场竞争力。
只有经过全面的开发流程,才能打造出符合市场需求和客户期望的汽车零部件。
报废汽车典型塑料零部件回收利用技术现状

活
中可 以 明显看 出 ,近 法除漆 效果 及处 理能 力都 比较低 , 车 中的 塑料 零部 件 ,已经 增 加 。从 图 1
从 普 通 装 饰 件 发 展 到 结 构 两 年 我 国 轿 车 消 费 量 呈 阶 梯 式 快 产 生 的废 液对环境 危 害较 大。一 些
件 、 功 能 件 ,所 用 的材 料 也 从 普 速 上 升 。 在 销 量 的 不 断 攀 升 的 同 企 业采 用热 解 法 进 行 回收 利 用 , 将 通 塑料 扩 展 到 强 度 更 高 、 冲 击 性 时 ,越 来 越 多 的 汽 车 进 入 报 废 阶 回收 的保 险杠 用于热 解炼 制燃油 或
更 好 的 复 合 材 料 或 塑 料 合 金 。 主 段 。如按每辆汽 车平均耗 用塑料 燃气 ,但是 其热 解后 的残余 产物难 0g 0万 要 的 塑 料 零 部 件 有 保 险 杠 、散 热 6 k 计 ,年均 近5 0 辆报废 汽 车 以处置 ,易产生 二次 污染 。此外 ,
格 栅 、照 明灯 、仪 表 板 ( 副 仪 表 产 生废 旧 塑料 高 达 3 万 t 这 些废 部 分企 业在 回收 的过程 中加 入少量 含 0 。
板) 、座 椅 、车 门 内板 、顶 棚 、杂 『 塑料 如 得不 到妥 善处 理 ,; 污 化 学药 品改性他 用。 1 9 会
收利用的发展方向。
W i h r wig s a ct fn t r l e o r e n c o c l n i me td t r r t fCh n g e n t t e g o n c r i o au a s u c s a d e olgia vr h y r e on n e e i ai o ia, r e o on r c c ig a d u ig o pc l lsi o on n so s a d d a t moblsa c r t h e eo e y l n sn f y ia a t c mp e t f c r e uo n t p c di i c o d wi t e d v lpme t e h n de n ft e Ci lrEc n my t a d o a e y o rc n r . i pe als s t e pr s n ma ds o h a o o h ta v c t d b u ou ty Ths pa an y e h e e t r cu r st a in o e y l g a d u ig o pc l ls i c mp n ns o s a d t mo i s p it g ou e i t n r c ci n sn f y ia a t o o e t fdic r ed auo bl , o ni t h u o n t p c e n t e t n r lms o ia a t mo ie pa t e y l g idu tyan v sa ve o uu e d v l men f x a tp obe fCh n u o t lsi r c ci v c n n s r d gie iw f t r e eop f t o ds ar e u o b lspa t a t e y l g. ic d d a t mo i ls i p r rc ci e c s n
手糊成型工艺典型的产品

手糊成型工艺典型的产品手糊成型是一种常用于制作复杂形状产品的工艺。
这种成型工艺可以使用各种材料,包括橡胶、塑料和复合材料。
手糊成型工艺主要通过手工将材料涂敷在模具上,并使用手工工具将材料均匀压实,形成所需产品的形状。
以下是一些手糊成型工艺典型的产品。
1. 汽车零部件:手糊成型工艺被广泛应用于汽车制造业。
例如,车身外部触感零部件,如车顶、前后保险杠等,通常使用手糊成型工艺制造。
这种工艺能够提供高度的灵活性,以适应不同形状和尺寸的汽车。
2. 船舶零部件:手糊成型工艺也被用于制造船舶零部件。
船舶需要耐腐蚀和耐海水侵蚀的材料,而手糊成型可以使用各种防水材料,如玻璃纤维增强塑料带,来制造这些零部件。
3. 建筑材料:手糊成型工艺可以制造各种建筑材料,如屋顶瓦片、墙板和装饰物品。
这些材料通常需要具有高度的耐久性和耐候性,以承受不同的气候条件和环境。
4. 垃圾桶:手糊成型工艺可以用于制造各种家庭和工业垃圾桶。
这些垃圾桶通常需要具有高度的强度和耐用性,以承受日常使用和多次运输。
5. 电子产品外壳:手糊成型工艺在电子产品制造中也有广泛的应用。
例如,手机和电脑的外壳通常使用塑料等材料通过手糊成型工艺制造。
这种工艺可以制造出符合设计要求的外观和形状的外壳。
6. 运动器材:手糊成型工艺在制造运动器材中也起到重要的作用。
例如,滑雪板、冲浪板和高尔夫球杆等运动器材需要具备一定的强度和耐用性,而手糊成型工艺可以实现这些要求。
7. 实验室设备:手糊成型工艺还广泛应用于制造实验室设备,如实验室仪器的外壳和容器。
这种工艺可以制造出符合特定实验需求的设备,并能够承受实验室环境中的化学腐蚀和温度变化。
总之,手糊成型工艺在许多领域中都有广泛的应用,包括汽车制造、船舶制造、建筑材料、电子产品制造、运动器材制造和实验室设备制造。
这种工艺能够实现复杂形状的制造,并能够灵活适应不同的产品需求。
- 1、下载文档前请自行甄别文档内容的完整性,平台不提供额外的编辑、内容补充、找答案等附加服务。
- 2、"仅部分预览"的文档,不可在线预览部分如存在完整性等问题,可反馈申请退款(可完整预览的文档不适用该条件!)。
- 3、如文档侵犯您的权益,请联系客服反馈,我们会尽快为您处理(人工客服工作时间:9:00-18:30)。
的疲劳抗力,它主要取决于屈服强 度。因此,提高材料的屈服强度, 即提高了零件的疲劳失效抗力,也 就可能减轻零件的质量。然而在高 强度水平下,疲劳抗力的提高需要 足够的韧性予以配合,而且要求材 料中的杂质和夹杂物含量很少。在 过载疲劳条件下,材料的抗过载疲 劳能力,除了应具有高强度之外, 还需要有较高的韧性和延性。在次 载条件下,为了充分发挥材料次载 锻炼的作用,也必须有一定的延性 和韧性配合。
300
600
44.1
70.0
90
150
167
200
表3 几种轻质合金及钢材的强度对比
钢材
Ti合金
10钢
45钢
低碳马氏体
(Ti-6Al-4V) (正火) (调质) (淬火、回火)
980 106.3 327
340 209.0 110
913 205.8 254
1 600 210.0 430
222.7
65.0
延性(塑性)是材料受力断裂 之前发生塑性变形的能力,韧性是 材料断裂之前吸收功(包括弹性变 形功、塑性变形功、断裂功)的 能力。材料具有足够的延性、韧 性是防止制件工作时发生脆断、避
性能
σ t /MPa E/GPa
硬度HBS (σ t /ρ )
/MPa
轻质合金
Mg合金
Al合金
(MB15) (LC6)
各种钢铁材料原剂在不同的成 分、加工处理和显微组织形态的情 况下,其硬度对耐磨性的影响如图 3。图中的耐磨性等于摩擦滑动距离 除以磨耗的体积。从图3看出,普 遍的规律是材料的硬度增高其耐磨 性增大,但当硬度相同时,材料成 分、加工处理工艺和所具备的显微 组织对耐磨性也有明显的影响。对 照图2可知,具有高强度、高韧性的 材料其耐磨性也高。
轴
△△
△
承
△△ △
△△△
疲劳, 屈服及 剪切强 度
△△△
△△△△
疲劳, 耐磨 △ 性,耐 蚀性
材料的发展方向之一。 综上所述,大幅度提高汽车典
型零件材料的强度和韧性,可以提 高所制零件的抗疲劳、抗磨损、抗 塑变、抗断裂能力,也为汽车的轻 量化、安全性提供了基础条件。为 了汽车减振、降噪,汽车重要零件 应广泛使用高强韧性减振材料。
1 汽车典型零件的失效形式 和性能要求
汽车中的典型零件由于服役条 件不同,其失效形式也不尽相同。 几种典型的汽车典型零件的服役条 件、常见失效形式如表1,可以看 出,这些零件的主要失效形式有以 下几类。
(1)疲劳类:如前轴、曲轴、 齿轮、连杆、弹簧等零件,工作时 主要承受交变载荷,其主要失效形 式是疲劳断裂和接触疲劳引起的表 面麻点剥落。这类失效形式占汽车 重要零件失效的绝大多数。解决疲 劳失效的主要途径是提高所用材料
(5)振动、颤动类:汽车是行 走机械,行驶时许多典型零件都在 转动、振动、颤动,并产生噪声, 这将引起能耗增高、环境污染和乘 员的不舒适感,也可因此而使汽车 失效。解决这类问题除了改进汽车 设计之外,主要是广泛使用减振材 料来制造汽车零部件。这也是汽车
2008年第4期
汽 车 工 艺 与 材 料 AT&M
长春工业大学 刘云旭
汽车由十几万个零件组成。其 中,承受载荷、传递功率的典型零 件占汽车总质量的绝大部分,而且 基本上都是由金属材料制成,包括 车身、覆盖件、轴、齿轮、弹簧、 连杆等类零件。因此,这些零件的 轻量化、安全化和节约化是实现汽 车现代化的根本条件,其途径是运 用先进科学技术,充分发挥合金资 源潜力和加工制造过程中能源的潜 力,使所用材料实现高强韧化。这 是汽车现代化和增强竞争能力的必 由之路。为此,本文对汽车典型零 部件的高强韧化进行了探讨。
E/ρ
σ y/ρ
KIC/ρ
G/ρ
σ y/ρ
KIC /ρ
承扭筒状零件 给定T、L、r;t(壁厚)可变
G/ρ
σ y/ρ
KIC /ρ
受弯梁、管类零件 给定S(弯曲力)、L; r可变
承压柱状零件 给定P(压力)、r;t可变
E1/2/ρ E1/2/ρ
σ y 2/3/ρ
KIC 2/3/ρ
承压板状零件 给定P、L、W(宽度);t可变
(2)磨损类:如曲轴、凸轮 轴、齿轮、球头销、气缸等零件, 工作时除应力作用之外,还受到摩 擦的作用,而且摩擦引起的磨损也 可能成为这类零件的失效形式。在 汽车零件中磨损失效占有相当的比 率。解决磨损失效的主要途径是提 高所用材料的耐磨性。一般认为, 材料的耐磨性随着硬度的增高而增 高。但是硬度过高其脆性增大,材 料的破断抗力降低,摩擦时局部材 料会脆裂成磨粒而加速磨损。研究 表明,材料的耐磨性主要受材料的 强度和韧性乘积的影响,实际上以 提高材料的强度为主,并配合以足 够的韧性,则是提高材料耐磨性根 本途径。
性)、韧性以及较小的屈强比。
汽车零件工作时表面受到磨损
目前工程上使用强度高并具有 的零件,一般都承受一定的应力载
较高韧性而且价格较低的材料主要 荷,因此为了减轻零件的质量,也
是钢材。汽车零件可用的钢材类 应使用高强度材料来制造。而且,
型、加工处理和显微组织形态下的 如前所述,提高材料的强度并配合
强度和冲击韧性如
(2)汽车承受重载荷零件用高 强度钢
汽车中承受重载荷的零件需要 断面尺寸较大、质量较重的钢材来 制造,提高所用钢材的强度,在相 同服役条件下,增大钢件承受过载 的能力,可提高制件的安全性和延 长使用寿命。过载条件一定时,则 可减小制件的断面尺寸而减轻自 重。但是大幅度提高强度的同时, 又常常使韧性和延性(塑性)显著 降低。
(4)腐蚀类:如滑动轴承、板 弹簧、螺旋弹簧、排气门等零件, 受到大气、雨水、发动机废气等的 作用,会造成零件表面发生腐蚀和 应力腐蚀,如果腐蚀过度也会导致 零件失效。但是,汽车典型零件中 发生腐蚀和应力腐蚀失效的很少。 解决零件失效问题的主要途径是提 高所用材料对腐蚀介质相应的耐蚀 性或进行表面防蚀处理。
(1)汽车车身用高强度钢板 汽车车身可用的高强度钢板,
除了具有高的强度之外,还要具有 良好的延性和冷塑性加工成形性。 深冲成形、延伸成形和弯曲成形, 都要求钢板具有较高的R值(R=ε w/ ε t,ε w和ε t分别为钢板宽度方向
上的真应变和厚度方向上的真应 变 ) 、 n 值 ( 加 工 硬 化 率 ) 、ε T (总应变率)和低的屈强比(σ y/ σ t)。这类钢板中主要有IF(无间 隙原子)钢、双相(DP)钢、复 相(CP)钢,低碳贝氏体(LCB) 钢、低碳马氏体(LCM)钢和低碳 Si-Mn系TRIP(相变诱发塑性)钢。 这些钢的强度、延性和R值如图1。 可以看出,新钢种如IF钢、超细F晶 钢、低碳贝氏体、马氏体、B+M钢 以及低碳超级贝氏体钢都具有高的 强度和延性,与Al合金、Mg合金等 轻合金相比,作为制造汽车车身用 板材,具有较好的比较优势。
(σ t)和冲击韧性(ak)
适当的韧性是提高耐磨性的基本途 径。由于各种磨损零件承受的应力 性质、大小不同,可以采用不同强 度水平的材料来制造,而通过表面 强化(硬化)来提高耐磨性,但为 了减轻零件质量仍应使用高强度材 料。对于像曲轴、凸轮轴这类承受 应力载荷不大以磨损失效为主并要 求较高刚度的零件,使用高强度材 料后,为了保持零件外观尺寸,可 采用中空的设计来减重。
专 题报道
F
E
A
T
U
R
E
S
表1 典型汽车零件的服役条件和常见失效形式
服役条件
失效形式
零 件 类 型
载荷类型
应力状态
静疲冲
接
拉压弯 扭 切
拉劳击
触
磨温介 损度质
过 振量塑 动变断
形
表尺 脆面寸疲咬腐 断变变劳蚀蚀
化化
腐 蚀 疲 劳
主要失 效指标 抗力
传
动 轴
△△
△△
△
类
△△
△△
弯扭复 合疲劳 强度
齿
(4)汽车典型零件使用高强度 吸振材料
新近研究认为,对于新型结构 材料,除了要求具有高的使用性能 和工艺性能之外,还应具有良好的 吸振性能,这对高速行驶的汽车更 为重要,因为汽车就是在机械振动 状态下运行,机械振动产生噪声, 振幅越大、频率越高,产生的噪 声越大。噪声属于三大公害之一, 近年来世界各国都已用法律或规定 加以限制,振动和噪声不仅污染环 境,影响人的身体健康,而且影响 产品(汽车)的质量,削弱了在国 际上的竞争能力。除了采用机械减 振之外,最好采用承载零件的材料 减振。
(3)过度变形和断裂类:如前 轴、半轴、紧固螺栓、连杆螺栓、 活塞销等零件,工作时承受拉、 弯、压、扭、冲击等载荷,如果所 受应力超过所用材料的强度,则会 引起零件过度变形或断裂而失效。 汽车零件中发生这类失效的比率较 小。解决这类零件失效和减轻这类 零件质量的主要途径是提高所用材 料的抗塑性变形能力和抗脆性破裂 能力。前者是提高屈服强度,后者 是降低脆性、提高延性和韧性。
117.1
204
高碳超级贝氏体钢 (等温处理)
2 200 208.5 58HRC
297
2008年第4期
汽 车 工 艺 与 材 料 AT&M
专 题报道
F
E
A
T
U
R
E
S
下,冲击韧性仍高
于调质钢的水平,
因其具有最佳的强
度与韧性配合,应
成为汽车承载零件
首选材料。
此外,对于承
受不同性质载荷
的零件,可以采用
几种轻质(密度小)材料和钢 材的力学性能及比强度如表3。可
以看出,现代轻质合金的比强度高 于传统使用的正火、调质态低、中 碳钢的水平。但是,随着科技的进 步,钢的强度也在不断的提高,近 期研发的Si-Mn系高碳超级贝氏体钢 的强度已超过2 200 MPa,其比强度 也超过Mg合金、Al合金和Ti合金。 加之钢材的工艺性能优越、成本 (包括价格/比强度)较低,因此钢 材仍然是汽车轻量化的主导材料、 首选材料。