某商用车白车身结构疲劳寿命分析与优化设计
某商用车白车身结构疲劳寿命分析与优化设计

某商用车白车身结构疲劳寿命分析与优化设计作者:湖南工业李明李源陈斌摘要:本文基于应力分析结果,采用有效的疲劳寿命预估方法,利用专业耐久性疲劳寿命分析系统MSC.Fatigue 对该型商用车白车身进行S-N 全寿命分析,得其疲劳寿命分布与危险点的寿命值。
采用结构优化、合理选材等方法,提高白车身结构的疲劳寿命。
关键词:白车身;有限元;静态分析;疲劳寿命分析;优化前言在车身结构疲劳领域的国内研究中,1994 年,江苏理工大学陈龙在建立了车辆驾驶室疲劳强度计算的力学和数学模型基础上,提出了车辆驾驶室疲劳强度研究方法[1]。
2001 年,清华大学孙凌玉[2]等首次计算机模拟了汽车随机振动过程。
2002 年,上海汇众汽车制造有限公司王成龙[3]等应用FATIGUE 软件的分析,结合疲劳台架试验,探讨了疲劳强度理论在汽车产品零部件疲劳寿命计算中的应用,提出了提高零部件疲劳强度的方法。
2004 年,同济大学汽车学院靳晓雄[4]等人提到进行零部件疲劳寿命预估,精确的有限元模型和可靠的材料疲劳数据是必需的,另外获得准确的实际运行工况下的道路输入载荷也非常关键。
但由于客观条件的限制,国内这方面的研究非常有限,理论分析的多,对局部零部件研究的多,把车身整体作为研究对象的很少。
本文以某型商用车疲劳寿命仿真分析及优化提高为内容,研究中,首先对白车身结构几何进行网格划分;之后使用MSC.Patran/Nastran 对白车身结构进行静态仿真;然后导入MSC.Fatigue 对白车身结构进行疲劳寿命仿真。
在分析的基础上采用结构优化设计的方法优化结构、合理选择材料等,提高白车身结构的静态力学性能与动态疲劳寿命。
1 疲劳寿命计算方法疲劳寿命计算需要载荷的变化历程、结构的几何参数,以及有关的材料性能参数或曲线[4]。
图1为基于有限元分析结果的疲劳寿命分析流程。
图1 基于有限元分析结果的疲劳寿命分析用有限元方法计算疲劳寿命通常分为两步:第一步是计算应力应变响应。
车辆白车身DFMEA分析范例

车身工程中心编制人:新严重度新频度新探测度新风险顺序数1零部件无法安装1车身数据未符合边界要求5按《白车身孔位描述书》和《零部件边界条件确认表》进行数据检查152车身无法焊装、车身运动干涉、车身异响、用户抱怨1三维数据检查未全面检查、运动校核未考虑实车精度、相关零部件未考虑到位5按《白车身自相关检查表》和《车身运动件运动校核检查表》进行数据校核6303整车外观效果差,无法满足客户需求,影响销售4设计间隙、面差不合理;装调不到位;公差分配不合理;定位方式设置不合理6参照相关车型合理设置DTS定义值,合理设置公差,合理设置定位方式6144数模校核,定位方案确定车身4增加模具费用,增加整车成本,影响利润1设计结构时未考虑后期开发车型的共用性5编制车身开发模块化说明,预先设计拓展车型结构方案6305零部件冲压起皱,翻边开裂,尖角争料,产品结构弱,易变形,尖角拉延破裂冲压负角,件拉延开裂,模具上修边刃口强度不足,影响车身性能5冲压SE分析未到位,钣金结构不合理4按《白车身SE审查报告》进行反馈及数模修改,合理设计钣金结构6120SE分析车身/制造6车身焊接操作性差,工人抱怨、生产率低,焊接效果差,影响车身性能5焊装SE分析未到位,钣金结构不合理4按《白车身SE审查报告》进行反馈及数模修改,合理设计钣金结构,合理布置焊点位置及层次2407车身电泳底漆厚度不均匀、部分区域未充分覆盖底漆、车身锈蚀、影响整车寿命5涂装SE分析未到位,钣金结构不合理4按《白车身SE审查报告》进行反馈及数模修改,合理设计钣金结构,保证涂装效果2408总装件无法安装;车身总装操作性差,工人抱怨、生产率低;零部件维修操作性差5总装SE分析未到位未分析可维修性4按《白车身SE审查报告》进行反馈及数模修改,合理设计钣金结构,合理考虑安装操作空间,进行安装虚拟验证2409影响用户乘车舒适性,影响内部载货空间,用户抱怨3未合理设计钣金结构,钣金侵占内部空间6进行CAE分析,在保证车身性能、安装结构的前提下尽量增大内部空间,可对比标杆设计7126初期确定目标值,后期按照执行,尽量加大内部空间车身/整车10影响用户乘车舒适性,影响内部装卸货方便性,用户抱怨3未合理设计钣金结构,未按人机要求设计6按人机要求设计数据,在保证车身性能、安装结构的前提下尽量改善,可对比标杆设计6108方案阶段确定各相关尺寸,保证后期数据满足要求。
基于有限元法的某车型白车身耐久分析

h 乍身的疲 劳 寿命 , 提前 预 测 灯命 较短 的 域 , 以 便 存 试制 样 年 前 就 能进 行 政进 , 以 达 到 降低 新 产
品 的开发 周期 与成 本 的效 I 、 小 义以某 车 型 白车 身 为分 析 刈’ 象, 建 立仃 限 元模 犁 , 通过 惯 性 释 放 方 法 汁钾 : 得 纠心 力分 布 状 况; { 母 利 用 六 分 力测 试技 术 实测 该 在 试验 场
中 图分 类 号 : L J 4 6 1 。 1 文献标识码 : 、 文章编号 : 1 6 7 2 — 4 8 0 1 ( 2 0 l 7 ) 【 ) 1 — 0 7 1 — 0 3
D OI : 1 0 。 1 9 5 0 8 / j . c n k i . 1 6 7 2 - 4 8 0 1 . 2 0 1 7 . 0 1 . 0 2 2
疲 劳耐久技术 , 对 该 车 型 ㈠车 进 行耐 久 分 析 l 1 前有 3 种常 的疲 劳 分 析 力 ‘ 法: 心, J 一 寿命 法 、 应 变一 寿命 法 和线 弹 性 断 裂 力学 法 , 这 些 方 法都 足 以疲 劳 寿命 L j 加 载 循环 次 数之 J 1 i J 的关 系 为基础 的 本 文采 用 应 变一 寿 命 ( E — N) 法, 陔 ‘ 法 因其 能有 效 考虑 到局 部 塑形 变 彤 × 、 f 疲 劳分 析造 成 的影
零 部 件 循 环 应 力或 应 变 的 作 川下 , 局部 位 置会, , l ! 永 久性 累 计损 伤 , 经 过 一定 循 环 次 数后 损 伤 较 大 化 发 展 成 裂纹 或 直 接 断 裂 , 这 个过 程
运 行 的 道路 载荷 谱数 据 , 以此 数据 驱 动 整 乍多体 动 力学 模 型 , 获取 白车身 _ J 硬 点 载筒 谱 ; 然后 结合
车身结构优化设计及其疲劳寿命分析

车身结构优化设计及其疲劳寿命分析一、引言在车辆设计中,车身结构的优化设计及其疲劳寿命分析也是不可或缺的一部分。
做好这方面的工作,不仅可以提高车辆的安全性能和舒适性能,还可以延长车辆的使用寿命,从而更好地保障人们的出行安全和生活质量。
二、车身结构优化设计1.1 意义和目的车身结构的优化设计是指在保证车身强度、刚度和稳定性等性能的基础上,通过调整结构、采用新材料和加工工艺等手段来使车身的重量更轻,噪音更小,乘坐舒适性更好,并提高车辆的综合性能。
1.2 优化设计流程(1)确定系统性能需求:包括车身强度、刚度、稳定性、舒适性、安全性能等。
(2)分析和优化车身结构:采用CAE分析和优化软件对车身结构进行分析,调整结构、减少零部件的数量等以达到重量减轻的目的。
(3)选择合适材料:采用轻量化材料,如高强度钢、铝合金、塑料等材料,以达到减轻重量的目的。
(4)提高加工工艺:采用先进的加工工艺,如冲压成型、喷涂、涂装等,以达到提高制造效率和降低成本的目的。
1.3 实例分析比如,本田公司最近发布了一款新车,其中采用了大量的高强度钢材料,并采用模块化设计,去除了很多零部件,从而在车身稳定性和舒适性上都有所提升,同时重量也有所减轻。
三、疲劳寿命分析2.1 意义和目的车身结构的疲劳寿命分析是指在保证车身结构强度和稳定性的基础上,通过对车身各零部件的疲劳寿命进行分析和评估,预测车身的使用寿命,避免出现裂纹、断裂、变形等现象,保证车辆的安全性能和可靠性能。
2.2 疲劳寿命分析方法(1)有限元法:采用有限元法对车身结构进行疲劳寿命分析,通过对板、梁、节点等部件的应力应变、应变历程和损伤程度等进行分析和评估。
(2)试验法:采用试验方法对车身结构进行疲劳寿命分析,通过对多样化试验来检测车身结构各零部件的疲劳损伤、裂纹、变形等情况,并分析其疲劳寿命。
2.3 实例分析比如,通用汽车公司采用了先进的试验方法和有限元分析方法来研究车身结构的疲劳寿命,通过对车身各零部件的应力分布和疲劳损伤等进行综合评估,提高了车身的疲劳寿命,同时也提高了车辆的安全性和可靠性。
重载机械结构疲劳寿命预测与优化设计

重载机械结构疲劳寿命预测与优化设计随着工程技术的迅猛发展,机械结构的重载问题也日益突出,而疲劳寿命的预测与优化设计成为了重载机械结构设计的重要研究课题。
疲劳寿命预测与优化设计可以有效提高机械结构的安全性和可靠性,延长使用寿命,降低维修成本。
一、重载机械结构的疲劳现象分析在对重载机械结构的疲劳寿命进行预测与优化设计之前,首先需要对疲劳现象进行深入分析。
重载机械结构的疲劳现象主要体现在材料中的断裂疲劳和零件或连接点的破损疲劳两个方面。
断裂疲劳主要是由于结构承受的动态载荷,导致材料中出现微观缺陷引起的。
随着载荷的作用,缺陷会逐渐扩展并最终导致断裂。
而破损疲劳则是由于零件或连接点处的局部应力过大,使得零件或连接点发生塑性变形或断裂。
二、重载机械结构的疲劳寿命预测方法针对重载机械结构的疲劳寿命预测方法,目前主要有两种常用的方法:一种是基于经验公式的方法,另一种则是基于有限元分析的方法。
基于经验公式的方法适用于简单结构的疲劳寿命预测,其核心是根据材料的应力-寿命曲线,结合疲劳强度折减公式,通过计算结构所受到的应力情况,从而得到结构的疲劳寿命。
然而,这种方法在考虑复杂结构的疲劳寿命时存在较大的误差。
基于有限元分析的方法是一种更为精确的疲劳寿命预测方法,它能够考虑结构的非线性和非均匀性,并能够模拟结构在实际工作条件下的受力情况。
该方法通过将结构离散为有限个单元,在不同载荷下进行疲劳寿命分析,从而得到结构的疲劳寿命。
然而,该方法需要精确的材料参数和载荷数据,并且计算量较大。
三、重载机械结构的优化设计方法为了提高重载机械结构的疲劳寿命,优化设计方法成为了必要的手段。
常见的优化设计方法有:材料优化、结构优化和参数优化。
材料优化主要是通过选择高强度、高韧性和耐疲劳的材料,来提高机械结构的疲劳寿命。
同时,合理的热处理工艺也能够增强材料的抗疲劳性能。
结构优化则是通过对结构进行几何形状或材料截面优化,来改善应力分布状态,减小应力集中区域,提高结构的疲劳寿命。
白车身强度分析及优化设计

10.16638/ki.1671-7988.2020.10.054白车身强度分析及优化设计刘小会,杨越(安徽江淮汽车集团股份有限公司技术中心,安徽合肥230001)摘要:文章首先阐述了车身强度分析的目的以及CAE分析的方法,然后分析了基于强度考虑的车身优化设计方法。
以某型汽车C柱区域的强度问题为例,进行了原因分析和方案优化,经CAE分析验证,结果满足要求。
关键词:汽车;强度;CAE 分析;应力中图分类号:U467 文献标识码:B 文章编号:1671-7988(2020)10-181-03The Optimal Design of The White Body StrengthLiu Xiaohui, Y ang Y ue(The technology center of the jiang huai automobile, Anhui Hefei 230001)Abstract: This paper first describes the purpose of the body strength analysis and the method of CAE analysis, then analyzes the body design method based on intensity is considered. Finally, this paper takes the strength of the column with a certain type of car C area problem as example, has carried on the analysis of the causes and scheme optimization, the final CAE analysis verify again, can meet the requirements.Keywords: Automobile; Strength; CAE; StressCLC NO.: U467 Document Code: B Article ID: 1671-7988(2020)10-181-03前言汽车的结构强度主要由车身强度来决定。
汽车底盘结构优化设计与疲劳寿命分析
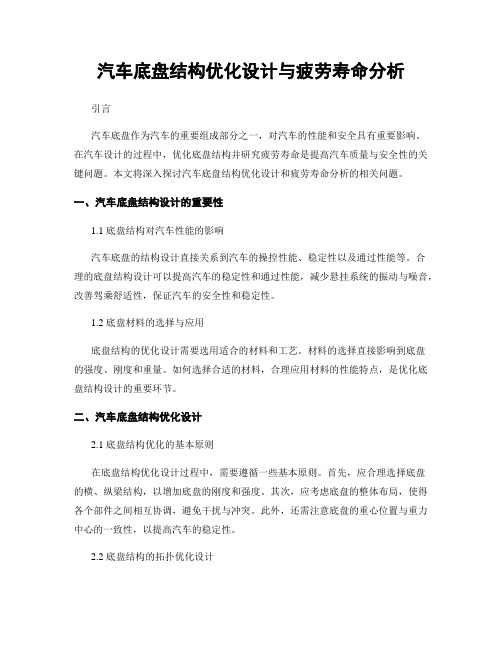
汽车底盘结构优化设计与疲劳寿命分析引言汽车底盘作为汽车的重要组成部分之一,对汽车的性能和安全具有重要影响。
在汽车设计的过程中,优化底盘结构并研究疲劳寿命是提高汽车质量与安全性的关键问题。
本文将深入探讨汽车底盘结构优化设计和疲劳寿命分析的相关问题。
一、汽车底盘结构设计的重要性1.1 底盘结构对汽车性能的影响汽车底盘的结构设计直接关系到汽车的操控性能、稳定性以及通过性能等。
合理的底盘结构设计可以提高汽车的稳定性和通过性能,减少悬挂系统的振动与噪音,改善驾乘舒适性,保证汽车的安全性和稳定性。
1.2 底盘材料的选择与应用底盘结构的优化设计需要选用适合的材料和工艺。
材料的选择直接影响到底盘的强度、刚度和重量。
如何选择合适的材料,合理应用材料的性能特点,是优化底盘结构设计的重要环节。
二、汽车底盘结构优化设计2.1 底盘结构优化的基本原则在底盘结构优化设计过程中,需要遵循一些基本原则。
首先,应合理选择底盘的横、纵梁结构,以增加底盘的刚度和强度。
其次,应考虑底盘的整体布局,使得各个部件之间相互协调,避免干扰与冲突。
此外,还需注意底盘的重心位置与重力中心的一致性,以提高汽车的稳定性。
2.2 底盘结构的拓扑优化设计底盘结构的拓扑优化设计是一种基于构型形式的设计方法,通过调整结构的拓扑布局来达到优化结构的目的。
该方法能有效降低底盘的重量,提高底盘的强度和刚度。
2.3 底盘结构的材料优化设计底盘结构的材料优化设计是指通过选择合适的材料和工艺,使得材料的性能与结构的要求相匹配。
这种设计方法不仅可以降低材料的成本,还可以提高底盘结构的强度和刚度。
三、疲劳寿命分析3.1 疲劳失效的原因和特点疲劳失效是底盘结构在长期使用过程中产生的一种常见失效形式。
它通常由于底盘受到循环加载而引起,其特点是在载荷作用下产生微小的损伤,逐渐发展成微裂纹,最终导致底盘的疲劳破坏。
3.2 底盘疲劳寿命分析方法底盘疲劳寿命分析是对底盘结构进行疲劳耐久性评估的一种重要手段。
某SUV白车身模态分析及优化设计
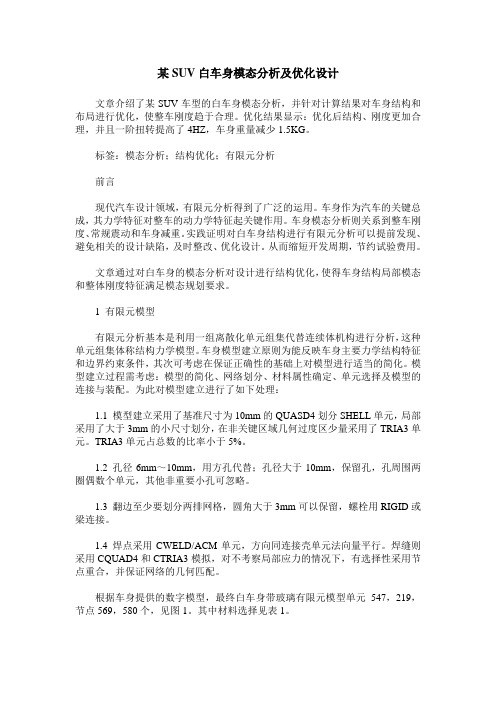
某SUV白车身模态分析及优化设计文章介绍了某SUV车型的白车身模态分析,并针对计算结果对车身结构和布局进行优化,使整车刚度趋于合理。
优化结果显示:优化后结构、刚度更加合理,并且一阶扭转提高了4HZ,车身重量减少1.5KG。
标签:模态分析;结构优化;有限元分析前言现代汽车设计领域,有限元分析得到了广泛的运用。
车身作为汽车的关键总成,其力学特征对整车的动力学特征起关键作用。
车身模态分析则关系到整车刚度、常规震动和车身减重。
实践证明对白车身结构进行有限元分析可以提前发现、避免相关的设计缺陷,及时整改、优化设计。
从而缩短开发周期,节约试验费用。
文章通过对白车身的模态分析对设计进行结构优化,使得车身结构局部模态和整体刚度特征满足模态规划要求。
1 有限元模型有限元分析基本是利用一组离散化单元组集代替连续体机构进行分析,这种单元组集体称结构力学模型。
车身模型建立原则为能反映车身主要力学结构特征和边界约束条件,其次可考虑在保证正确性的基础上对模型进行适当的简化。
模型建立过程需考虑:模型的简化、网络划分、材料属性确定、单元选择及模型的连接与装配。
为此对模型建立进行了如下处理:1.1 模型建立采用了基准尺寸为10mm的QUASD4划分SHELL单元,局部采用了大于3mm的小尺寸划分,在非关键区域几何过度区少量采用了TRIA3单元。
TRIA3单元占总数的比率小于5%。
1.2 孔径6mm~10mm,用方孔代替;孔径大于10mm,保留孔,孔周围两圈偶数个单元,其他非重要小孔可忽略。
1.3 翻边至少要划分两排网格,圆角大于3mm可以保留,螺栓用RIGID或梁连接。
1.4 焊点采用CWELD/ACM单元,方向同连接壳单元法向量平行。
焊缝则采用CQUAD4和CTRIA3模拟,对不考察局部应力的情况下,有选择性采用节点重合,并保证网络的几何匹配。
根据车身提供的数字模型,最终白车身带玻璃有限元模型单元547,219,节点569,580个,见图1。
- 1、下载文档前请自行甄别文档内容的完整性,平台不提供额外的编辑、内容补充、找答案等附加服务。
- 2、"仅部分预览"的文档,不可在线预览部分如存在完整性等问题,可反馈申请退款(可完整预览的文档不适用该条件!)。
- 3、如文档侵犯您的权益,请联系客服反馈,我们会尽快为您处理(人工客服工作时间:9:00-18:30)。
某商用车白车身结构疲劳寿命分析与优化设计李明1李源2陈斌3(1湖南工业大学机械工程学院,湖南株洲,412008;2国防科学技术大学指挥军官基础教育学院,湖南长沙,410072;3 湖南大学汽车车身先进设计制造国家重点实验室,湖南长沙,410082)摘要:本文基于应力分析结果,采用有效的疲劳寿命预估方法,利用专业耐久性疲劳寿命分析系统MSC.Fatigue对该型商用车白车身进行S-N全寿命分析,得其疲劳寿命分布与危险点的寿命值。
采用结构优化、合理选材等方法,提高白车身结构的疲劳寿命。
关键词:白车身;有限元;静态分析;疲劳寿命分析;优化Body-in-white Fatigue Analysis and Optimization Design of theCommercial VehicleLI Ming1, LI Yuan2, CHEN Bin3(1 School of Mechanical Engineering , Hunan University of Technology, Zhuzhou, Hunan 412008, China; 2 College of Basic Education for Officers, National University of Defense Technology, Changsha, Hunan 410072, China;3 State Key Laboratory of Advanced Design and Manufacture for Vehicle Body, Hunan University, Changsha, Hunan 410082,China)Abstract:Based on the results of stress analysis, this paper took the effective way of the fatigue life estimating, used the professional durability fatigue life analysis system MSC. Fatigue, and the S-N life-cycle analysis of the certain type of commercial vehicle body-in-white finite element model, got the distribution of fatigue life and the fatigue life value of the danger points. Finally, by the structural optimization and material selection, writer improved the fatigue life of white body structure.Keywords: B ody-in-white structure, FEM, Static analysis, Fatigue lifetime analysis; Optimization0 前言在车身结构疲劳领域的国内研究中,1994年,江苏理工大学陈龙在建立了车辆驾驶室疲劳强度计算的力学和数学模型基础上,提出了车辆驾驶室疲劳强度研究方法[1]。
2001 年,清华大学孙凌玉[2]等首次计算机模拟了汽车随机振动过程。
2002年,上海汇众汽车制造有限公司王成龙[3]等应用FATIGUE 软件的分析,结合疲劳台架试验,探讨了疲劳强度理论在汽车产品零部件疲劳寿命计算中的应用,提出了提高零部件疲劳强度的方法。
2004年,同济大学汽车学院靳晓雄[4]等人提到进行零部件疲劳寿命预估,精确的有限元模型和可靠的材料疲劳数据是必需的,另外获得准确的实际运行工况下的道路输入载荷也非常关键。
但由于客观条件的限制,国内这方面的研究非常有限,理论分析的多,对局部零部件研究的多,把车身整体作为研究对象的很少。
本文以某型商用车疲劳寿命仿真分析及优化提高为内容,研究中,首先对白车身结构几何进行网格划分;之后使用MSC.Patran/Nastran对白车身结构进行静态仿真;然后导入MSC.Fatigue对白车身结构进行疲劳寿命仿真。
在分析的基础上采用结构优化设计的方法优化结构、合理选择材料等,提高白车身结构的静态力学性能与动态疲劳寿命。
1 疲劳寿命计算方法疲劳寿命计算需要载荷的变化历程、结构的几何参数,以及有关的材料性能参数或曲线[4]。
图1为基于有限元分析结果的疲劳寿命分析流程。
图1 基于有限元分析结果的疲劳寿命分析用有限元方法计算疲劳寿命通常分为两步:第一步是计算应力应变响应。
第二步是结合材料性能参数,应用不同的疲劳损伤模型进行寿命计算。
疲劳寿命的预测精度既依赖于应力应变响应的正确模拟,也依赖于预测模型的合理使用。
本文以材料或零部件的疲劳寿命曲线为基础,S-N方法用名义应力或局部应力预测实际构件的疲劳寿命,可以选择的应力参数有最大主应力、von-Mises 应力、Tresca 应力等。
损伤累积计算可以使用常规的Palmgren-Miner线性法则,能进行Good-man 和Gerber 平均应力修正,也能进行考虑表面加工和表面处理影响的寿命计算。
这一方法对于低应力高周疲劳寿命预测比较有效。
特别是对于一些复杂的零部件或焊接件,直接使用实测的“零部件S-N”曲线通常能获得合理的寿命估计。
2 白车身有限元模型的建立驾驶室白车身含有零件数目众多,并且常含有复杂的曲面,用网格准确描述其几何特征的难度较高,复杂的曲面会产生许多网格上的问题,如单元畸变、网格细小、网格失真等诸多问题。
对数目繁多、曲面复杂的零部件划分高质量的网格工作量大、难度高。
经网格质量检查后,不合格网格数为162个,网格失效百分比为0.0%,整体上网格的形状较为理想,网格质量较高,为计算结果的准确性提供了一个必要条件。
图2为白车身整车的有限元模型。
除此之外,白车身各个部件之间是通过焊接连接起来的,两部件在焊接处具有完全相同的自由度,为刚性连接,可用一维rigid单元模拟表示。
在整个白车身模型中焊点多达上万个,需利用rigid面板在焊点位置逐个施加。
并且焊点与焊点、焊点与约束之间很容易出现过约束的情况。
图3为焊点图。
图2 白车身整车的有限元模型图3为白车身焊点全图商用车静态典型工况为全扭曲工况模拟白车身两前轮同时着地时,主副驾驶员重力、卧铺人员重力以及车身自重对白车身产生静态弯曲作用的情况。
全扭曲工况模拟白车身两前轮均悬空时,主副驾驶座上相对反向的作用力对白车身产生静态全扭曲作用的情况。
此工况下主驾驶座从下至上均布于两个连接座椅的部件上施加了1000N的力,副驾驶座从上至下均布于两个连接座椅的部件上施加了1000N的力。
全扭曲工况两前轮均悬空,车身前端两个与前轮连接位置均无约束;后端两处约束表示车身与车架的连接,同样限制了X、Y、Z三个方向的自由度,约束节点位置固定。
图4为车顶向下视图全扭曲工况载荷与约束在空间上的位置关系。
经Nastran分析后,主后杠仍为主要应力部件,最大应力达403MPa,不仅超过材料屈服极限,而且超过了材料抗拉极限。
图5为全扭曲静态分析的应变云图,最大变形为19.13mm。
图4 全扭曲工况载荷与约束空间上位置关系图5 全扭曲静态分析应变云图3白车身有限元模型的疲劳分析利用上述的加载静态仿真分析的有限元应力结果,设置载荷信息并关联有限元工况,导入MSC.Fatigue中计算。
图6为全曲工况动态疲劳分析寿命云图,与车架的连接处的疲劳寿命达不到107次的应力要求,图7为寿命最差节点列表,可见最差节点在经受7.885E4次应力循环时便产生疲劳破坏,不符合疲劳寿命的要求。
需经过结构优化提高这些节点的疲劳寿命。
图6 全扭曲工况动态疲劳分析寿命云图在车身结构优化改进中,通常采用的方法有改变零件的局部形状尺寸、调整局部零部件的位置、增加加强筋或辅助零件、整体采用较厚的钢板或采用拼焊板材料的方法。
采用改变零件的局部形状尺寸、调整局部零部件的位置要对原有的零部件进行改动,并有可能影响到全车整体的布局,在制造工艺上,有可能要调整模具,成本高,一般不宜采用;增加加强筋或辅助零件、整体采用较厚的钢板的方法,适用于形状并不十分复杂的零部件。
使用拼焊板技术不用改变零部件的位置,根据车身不同部位强度的要求,合理使用一些不同强度的材料,不需要焊接加强筋,减轻车身的质量,减少车身零件的数量,是最优的结构优化方法。
由于拼焊板可以一次成形,减少了大量冲压加工的设备和工序,缩减了模具的安装过程,简化车身制造过程。
经全扭曲工况动态疲劳分析后,白车身的最低疲劳寿命次数为10E+5.88,低于10E+7次,需要进行疲劳寿命的优化。
图8列出了疲劳寿命最差的一些点,显示了疲劳寿命存在问题的区域。
该疲劳寿命问题为局部问题,可对疲劳出现局部疲劳寿命问题的部件更换材料。
图8静态结构优化后疲劳分析寿命云图更换的材料为MANTEN_MSN,其弹性模型为E=2.034E+5,抗拉极限为σb=600MPa,更换材料后,最差寿命点的疲劳寿命从原来的10E+5.8751优化为3×10E+7。
全扭曲工况的动态疲劳寿命得到了改善。
图9 全扭曲工况疲劳寿命材料优化4 小结本论文基于应力分析结果,采用有效的疲劳寿命预估方法,利用专业耐久性疲劳寿命分析系统MSC.Fatigue对该型商用车白车身进行S-N全寿命分析,得其疲劳寿命分布与危险点的寿命值。
采用结构优化、合理选材等方法,提高白车身结构的疲劳寿命。
完成了白车身动态疲劳寿命的优化。
最终优化后,白车身各工况整车的疲劳寿命均修正至107次循环以上。
5 参考文献[1] 陈龙,周孔亢. 车辆驾驶室疲劳强度试验与计算,机械工程学报,1994,30(5):23-29.[2] 孙凌玉,吕振华. 利用计算机仿真技术预测车身零件疲劳寿命,汽车工程,2001,23(6):389-391.[3] 王成龙,张治. 疲劳分析在汽车零部件设计中应用,上海汽车,2002,8:10-13.[4] 彭为,靳晓雄. 基于有限元分析的轿车零件疲劳寿命预测,汽车工程,2004,26(4):507-509.[5] 高云凯. 汽车车身结构分析. 北京:北京理工大学出版社,2005.[6] 谭继锦. 汽车结构有限元分析. 北京:清华大学出版社,2009.。