磁控溅射和电弧离子镀技术和应用介绍
磁控溅射的原理及应用

磁控溅射的原理及应用1. 什么是磁控溅射磁控溅射是一种常用的薄膜沉积技术,通过利用磁场将材料原子或离子从靶材表面释放出来,形成一个薄膜层,沉积在基底表面上的一种方法。
这种方法可以在真空环境中进行,可以用于各种材料包括金属、合金、氧化物等。
2. 磁控溅射的原理磁控溅射的原理基于带电粒子在磁场中的运动规律。
溅射系统通常由一个靶材和一个基底组成,它们被放置在真空室中。
磁控溅射的过程包括以下几个步骤:1.靶材表面被离子轰击,其中的原子或离子被释放出来。
2.磁场控制离子在真空室中的运动轨迹。
3.基底表面上的原子或离子吸附并形成一个薄膜层。
这个过程中,磁场是十分重要的。
磁场会引导离子沿着特定的轨迹运动,使得离子沉积在基底的特定位置上。
磁场还可以控制离子的能量和方向,从而影响薄膜的性质和微结构。
3. 磁控溅射的应用磁控溅射是一种多功能的薄膜沉积技术,广泛应用于各种领域。
3.1 表面涂层磁控溅射可以用于向基底表面沉积各种薄膜层。
这些薄膜层可以具有不同的功能,如防腐、耐磨、导电等。
它们可以用于改善材料的性能和外观。
3.2 光学薄膜磁控溅射可以制备高质量的光学薄膜。
这些薄膜可以应用于光学器件,如镜片、滤光片、反射镜等。
因为磁控溅射是在真空环境中进行的,所以这些光学薄膜可以具有良好的光学性能。
3.3 金属薄膜磁控溅射可以制备金属薄膜。
这些薄膜可以具有高导电性和优良的机械性能,可用于电子器件、导电材料等领域。
3.4 磁性材料磁控溅射还可以制备磁性材料薄膜。
这些薄膜可以具有特定的磁性性能,如高矫顽力、高饱和磁感应强度等。
它们可以应用于磁存储器件、传感器等领域。
4. 总结磁控溅射是一种重要的薄膜沉积技术,通过利用磁场控制离子运动和沉积位置,可以制备各种功能薄膜。
它在表面涂层、光学薄膜、金属薄膜和磁性材料等领域有着广泛的应用。
磁控溅射技术的发展,为材料科学和工程领域提供了新的可能性,为各种应用提供了高性能的薄膜材料。
电弧离子镀和磁控溅射

电弧离子镀和磁控溅射
电弧离子镀和磁控溅射都是制备薄膜或涂层的方法,有各自的原理和优缺点。
电弧离子镀的原理是引弧,其与电焊时的引弧类似。
其优点是离化率高(可达100%),沉积速率大,轰击剧烈,膜层致密与基片结合好。
磁控溅射的原理是在真空室内加入正交(有例外)的电磁场,空间中的电子在电磁场的作用下不断做螺旋线运动,电子运动撞击空间中稀有气体粒子(一般氮气、氩气),使其离化,离化了的粒子又会产生运动着的电子,继续撞击其他稀有气体粒子,于是电子越来越多,形成电子云环绕在阳离子周围,构成等离子体,阳离子在电场力的作用下轰击靶材(靶材接负压),溅射出靶材离子,在基片上沉积。
磁控溅射相比于蒸镀,能精准控制膜层厚度,沉积薄膜的致密度有所加强,既可以沉积金属膜层,也可以沉积非金属膜层、化合物膜层。
总的来说,电弧离子镀和磁控溅射在应用上都可以用来制备薄膜或涂层,都有各自的优点和适用范围。
磁控溅射技术的原理及应用

磁控溅射技术的原理及应用1. 磁控溅射技术简介磁控溅射技术是一种常用的薄膜沉积技术,通过将金属靶材溅射生成粒子或原子,在表面形成均匀且致密的薄膜覆盖层。
磁控溅射技术具有高效、环保、可控厚度等特点,广泛应用于材料科学、半导体制造、光学镀膜等领域。
2. 磁控溅射技术的原理磁控溅射技术基于电离溅射原理,通过磁场控制靶材离子的行为,使其垂直击打到靶材表面,从而产生溅射现象。
主要的原理包括以下几个方面:•靶材电离:在磁控溅射设备中,将靶材通电,使其产生离子。
电离的方式包括直流电离、射频电离等,通过电离可使靶材中的金属原子或粒子脱离束缚并形成等离子体。
•磁场控制:通过磁铁或电磁铁产生磁场,使得等离子体中的离子在磁场的作用下呈现螺旋轨道运动。
磁场对离子运动的控制可改变其飞行路径,使其垂直击打到靶材表面,并增加溅射效率。
•沉积膜形成:靶材表面被离子击打后,产生大量的金属原子或粒子,它们在靶材表面扩散并沉积形成均匀的薄膜。
溅射过程中的离子能量、离子束流密度等参数的调控可以影响薄膜的组成、结构和性能。
3. 磁控溅射技术的应用磁控溅射技术具有广泛的应用领域和潜力,主要包括以下几个方面:3.1 材料科学•薄膜制备:磁控溅射技术可以制备各种材料的薄膜,如金属薄膜、氧化物薄膜、氮化物薄膜等。
这些薄膜具有良好的致密性和附着力,在材料科学领域中起着重要作用。
•合金制备:通过磁控溅射技术,可以将两种或多种材料溅射在一起,制备出各种复合材料或合金。
这些合金具有独特的力学、电磁等性能,广泛应用于航空航天、汽车制造等领域。
3.2 半导体制造•集成电路制备:磁控溅射技术可以制备半导体材料的薄膜,作为集成电路的关键材料。
薄膜的制备过程中可以调控其成分和结构,从而改变其电学、光学等性能,满足集成电路的需求。
•光罩制备:在半导体工艺中,磁控溅射技术还可以制备光罩。
光罩是半导体制造中的重要工艺设备,用于制作集成电路的图案,对半导体工艺的精度和稳定性要求非常高。
磁控溅射镀膜
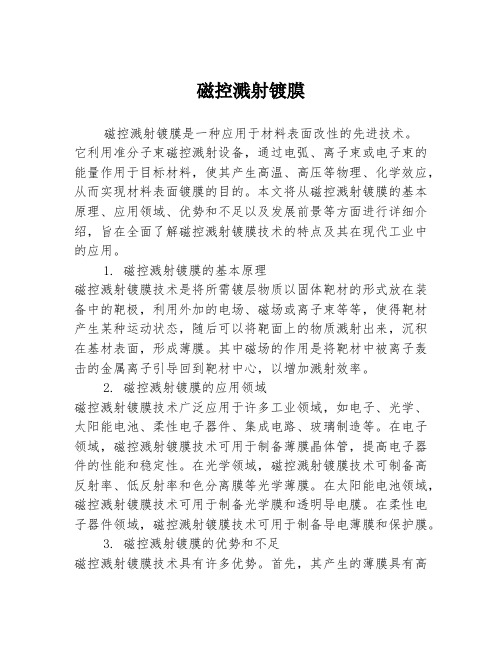
磁控溅射镀膜磁控溅射镀膜是一种应用于材料表面改性的先进技术。
它利用准分子束磁控溅射设备,通过电弧、离子束或电子束的能量作用于目标材料,使其产生高温、高压等物理、化学效应,从而实现材料表面镀膜的目的。
本文将从磁控溅射镀膜的基本原理、应用领域、优势和不足以及发展前景等方面进行详细介绍,旨在全面了解磁控溅射镀膜技术的特点及其在现代工业中的应用。
1. 磁控溅射镀膜的基本原理磁控溅射镀膜技术是将所需镀层物质以固体靶材的形式放在装备中的靶极,利用外加的电场、磁场或离子束等等,使得靶材产生某种运动状态,随后可以将靶面上的物质溅射出来,沉积在基材表面,形成薄膜。
其中磁场的作用是将靶材中被离子轰击的金属离子引导回到靶材中心,以增加溅射效率。
2. 磁控溅射镀膜的应用领域磁控溅射镀膜技术广泛应用于许多工业领域,如电子、光学、太阳能电池、柔性电子器件、集成电路、玻璃制造等。
在电子领域,磁控溅射镀膜技术可用于制备薄膜晶体管,提高电子器件的性能和稳定性。
在光学领域,磁控溅射镀膜技术可制备高反射率、低反射率和色分离膜等光学薄膜。
在太阳能电池领域,磁控溅射镀膜技术可用于制备光学膜和透明导电膜。
在柔性电子器件领域,磁控溅射镀膜技术可用于制备导电薄膜和保护膜。
3. 磁控溅射镀膜的优势和不足磁控溅射镀膜技术具有许多优势。
首先,其产生的薄膜具有高质量、高致密性和良好的附着力。
其次,磁控溅射镀膜过程中无需加热基材,可避免基材变形和热损伤。
此外,磁控溅射镀膜技术具有膜层成分可调、薄膜复杂结构可控等特点。
然而,磁控溅射镀膜技术也存在不足之处。
一方面,磁控溅射镀膜设备体积较大、成本较高,且对真空度要求较高。
另一方面,由于目前磁控溅射镀膜技术仍处于发展阶段,其在大尺寸薄膜制备和高速镀膜方面还存在一定限制。
4. 磁控溅射镀膜的未来发展随着科学技术的不断进步,磁控溅射镀膜技术将进一步得到发展和完善。
一方面,磁控溅射镀膜技术将在薄膜成分调控和复杂结构薄膜制备方面取得更大突破,以满足不同行业对薄膜材料的需求。
磁控溅射镀膜技术综合介绍
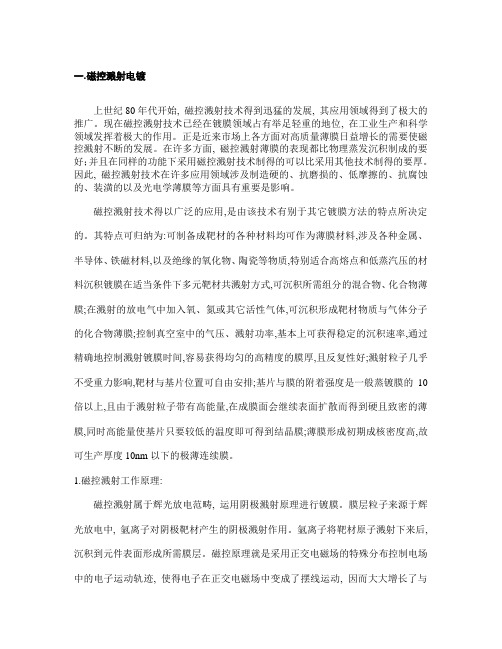
一.磁控溅射电镀上世纪80年代开始, 磁控溅射技术得到迅猛的发展, 其应用领域得到了极大的推广。
现在磁控溅射技术已经在镀膜领域占有举足轻重的地位, 在工业生产和科学领域发挥着极大的作用。
正是近来市场上各方面对高质量薄膜日益增长的需要使磁控溅射不断的发展。
在许多方面, 磁控溅射薄膜的表现都比物理蒸发沉积制成的要好;并且在同样的功能下采用磁控溅射技术制得的可以比采用其他技术制得的要厚。
因此, 磁控溅射技术在许多应用领域涉及制造硬的、抗磨损的、低摩擦的、抗腐蚀的、装潢的以及光电学薄膜等方面具有重要是影响。
磁控溅射技术得以广泛的应用,是由该技术有别于其它镀膜方法的特点所决定的。
其特点可归纳为:可制备成靶材的各种材料均可作为薄膜材料,涉及各种金属、半导体、铁磁材料,以及绝缘的氧化物、陶瓷等物质,特别适合高熔点和低蒸汽压的材料沉积镀膜在适当条件下多元靶材共溅射方式,可沉积所需组分的混合物、化合物薄膜;在溅射的放电气中加入氧、氮或其它活性气体,可沉积形成靶材物质与气体分子的化合物薄膜;控制真空室中的气压、溅射功率,基本上可获得稳定的沉积速率,通过精确地控制溅射镀膜时间,容易获得均匀的高精度的膜厚,且反复性好;溅射粒子几乎不受重力影响,靶材与基片位置可自由安排;基片与膜的附着强度是一般蒸镀膜的10倍以上,且由于溅射粒子带有高能量,在成膜面会继续表面扩散而得到硬且致密的薄膜,同时高能量使基片只要较低的温度即可得到结晶膜;薄膜形成初期成核密度高,故可生产厚度10nm以下的极薄连续膜。
1.磁控溅射工作原理:磁控溅射属于辉光放电范畴, 运用阴极溅射原理进行镀膜。
膜层粒子来源于辉光放电中, 氩离子对阴极靶材产生的阴极溅射作用。
氩离子将靶材原子溅射下来后,沉积到元件表面形成所需膜层。
磁控原理就是采用正交电磁场的特殊分布控制电场中的电子运动轨迹, 使得电子在正交电磁场中变成了摆线运动, 因而大大增长了与气体分子碰撞的几率。
用高能粒子(大多数是由电场加速的气体正离子)撞击固体表面(靶), 使固体原子(分子)从表面射出的现象称为溅射。
无靶直流磁控溅射技术在电镀领域中的应用
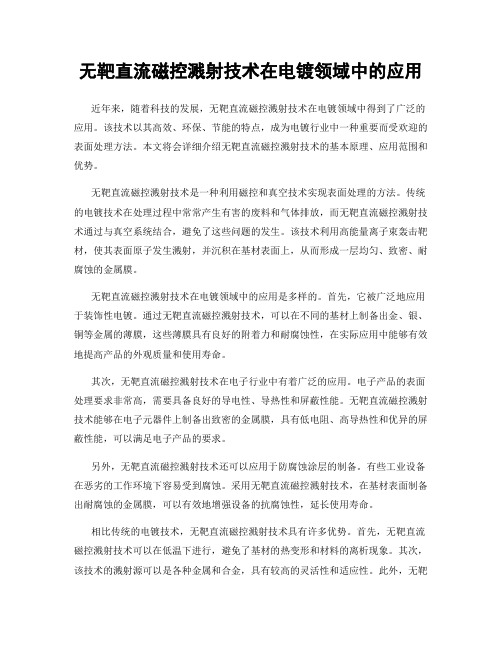
无靶直流磁控溅射技术在电镀领域中的应用近年来,随着科技的发展,无靶直流磁控溅射技术在电镀领域中得到了广泛的应用。
该技术以其高效、环保、节能的特点,成为电镀行业中一种重要而受欢迎的表面处理方法。
本文将会详细介绍无靶直流磁控溅射技术的基本原理、应用范围和优势。
无靶直流磁控溅射技术是一种利用磁控和真空技术实现表面处理的方法。
传统的电镀技术在处理过程中常常产生有害的废料和气体排放,而无靶直流磁控溅射技术通过与真空系统结合,避免了这些问题的发生。
该技术利用高能量离子束轰击靶材,使其表面原子发生溅射,并沉积在基材表面上,从而形成一层均匀、致密、耐腐蚀的金属膜。
无靶直流磁控溅射技术在电镀领域中的应用是多样的。
首先,它被广泛地应用于装饰性电镀。
通过无靶直流磁控溅射技术,可以在不同的基材上制备出金、银、铜等金属的薄膜,这些薄膜具有良好的附着力和耐腐蚀性,在实际应用中能够有效地提高产品的外观质量和使用寿命。
其次,无靶直流磁控溅射技术在电子行业中有着广泛的应用。
电子产品的表面处理要求非常高,需要具备良好的导电性、导热性和屏蔽性能。
无靶直流磁控溅射技术能够在电子元器件上制备出致密的金属膜,具有低电阻、高导热性和优异的屏蔽性能,可以满足电子产品的要求。
另外,无靶直流磁控溅射技术还可以应用于防腐蚀涂层的制备。
有些工业设备在恶劣的工作环境下容易受到腐蚀。
采用无靶直流磁控溅射技术,在基材表面制备出耐腐蚀的金属膜,可以有效地增强设备的抗腐蚀性,延长使用寿命。
相比传统的电镀技术,无靶直流磁控溅射技术具有许多优势。
首先,无靶直流磁控溅射技术可以在低温下进行,避免了基材的热变形和材料的离析现象。
其次,该技术的溅射源可以是各种金属和合金,具有较高的灵活性和适应性。
此外,无靶直流磁控溅射技术的工艺稳定性好,制备的金属膜均匀且致密,具有较高的附着力和耐腐蚀性。
在实际应用中,我们还需要注意到一些问题。
首先,无靶直流磁控溅射技术需要较为复杂的设备和专业的操作技术,因此在使用时需要具备相关的知识和经验。
多弧离子镀磁控溅射复合沉积

多弧离子镀磁控溅射复合沉积
多弧离子镀磁控溅射复合沉积是一种先进的表面处理技术,常用于制备功能性薄膜材料。
其工艺过程包括离子镀、磁控溅射和复合沉积三个步骤。
在离子镀步骤中,将基片作为阴极放置在离子源中,通过电弧放电或射频加热使金属阳极材料释放离子。
离子在离子源内被加速并排列成束,然后通过减速器进入装置的真空室。
离子束在进入真空室后会被聚焦并沉积在基片表面,形成均匀的金属薄膜。
这一步骤可以提高基片表面的粗糙度和增加表面活性位点数量。
在磁控溅射步骤中,将基片作为靶材放置在溅射室中,真空室内注入惰性气体(如氩气)。
通过电弧放电或射频放电,使靶材表面产生高温等离子体,使靶材表面的原子或分子离开靶材并冲击基片表面。
这个过程可以形成一层均匀致密的薄膜,增加基片表面的硬度和抗腐蚀性能。
复合沉积步骤是将离子镀和磁控溅射两个步骤结合起来,以更好地改善薄膜的性能。
通常先进行离子镀步骤,增加基片表面的活性位点数量,然后再进行磁控溅射步骤,形成一层均匀的薄膜。
这种复合沉积可以延长薄膜的使用寿命,提高其机械强度和耐磨性。
多弧离子镀磁控溅射复合沉积技术具有较高的沉积速率、良好的薄膜质量和复杂化学成分的调控能力。
它广泛应用于光学薄
膜、电子薄膜、功能性涂层等领域,如太阳能电池、显示器件和传感器等。
磁控溅射离子镀

磁控溅射离子镀磁控溅射离子镀随着科技的不断发展,材料表面处理技术也越来越受到人们的关注。
其中,磁控溅射离子镀技术是一种非常先进的表面处理方法。
本文将从原理、工艺、应用等方面详细介绍磁控溅射离子镀技术。
一、磁控溅射离子镀技术的原理磁控溅射离子镀技术是一种利用磁场控制离子运动的表面处理技术。
其主要原理是:在真空环境下,将制品作为阴极,利用高速电子轰击产生的离子在磁场作用下被聚集和加速,从而沉积在制品表面形成薄膜。
这种薄膜具有高硬度、高耐磨、耐腐蚀性好、不易脱落等优点。
二、磁控溅射离子镀技术的工艺流程1. 处理前的准备工作要先将制品表面进行清洗,去除表面的油污、灰尘等。
2. 真空排气将加工件、目标和溅射室等装置放置在真空室内,打开真空系统进行排气,直至达到所需真空度。
3. 溅射物的加热将制品和目标加热至一定温度,使其表面温度达到一定的范围,有助于提高溅射效率和薄膜质量。
4. 溅射室充气将惰性气体注入溅射室中作为离子的载体,从而形成离子束。
5. 磁场建立通过磁铁制成的磁场使得离子束向阴极开展自动运动,溅射出的物质在阴极表面沉积形成一层薄膜。
6. 增加反应气体通过向溅射过程通入反应气体,使沉积物质形成化学反应并调控膜层成分。
7. 薄膜形成及整体清洗经过多次溅射后,薄膜形成,清洗处理后即可使用。
三、磁控溅射离子镀技术的应用磁控溅射离子镀技术在工业界有着广泛应用,主要应用于以下领域:1. 电子工业用于制造电子元器件、半导体器件和显示器件中的各种金属及合金薄膜。
2. 光学工业制造反射膜、半反射膜、介质膜和滤光片等。
3. 机械工业制造模具、刀具、轴承、涡轮叶片等。
4. 生物医学制造医疗器械、人工关节、高品质耗材。
总之,磁控溅射离子镀技术具有高效、高质、低污染的特点,在工业生产中的应用越来越广泛。
- 1、下载文档前请自行甄别文档内容的完整性,平台不提供额外的编辑、内容补充、找答案等附加服务。
- 2、"仅部分预览"的文档,不可在线预览部分如存在完整性等问题,可反馈申请退款(可完整预览的文档不适用该条件!)。
- 3、如文档侵犯您的权益,请联系客服反馈,我们会尽快为您处理(人工客服工作时间:9:00-18:30)。
产生大颗粒喷射主要根源
1、弧斑随机运动速度慢 2、弧斑自身电磁产生的磁收缩力 3、放电离子轰击形成的反作用力
大颗粒,行业难题!
电弧离子镀大颗粒问题的解决
电弧离子镀的改进 磁过滤
磁镜过滤方法: –通过磁场对电子运动的控制实现 对等离子体的控制; –可以显著降低薄膜中的大颗粒; –沉积效率降低明显、束径受磁镜 限制;
电弧离子镀的历史
19世纪,美国发明家爱迪生提出利用真空电弧进行 镀膜的设想,并申请了美国专利;
20世纪50年代B.Vodra, H. Wroe等在真空冶炼时明确指 出真空电弧完全可以用于表面薄膜的沉积制备;
20世纪60年代日本真空技术研究所利用真空 交流电弧沉 积金属薄膜;
20世纪70年代苏联购买了日本的技术,发展了电弧离子 镀技术;
磁控溅射的应用--超硬涂层
用TiN,TiC等超硬镀层涂覆刀具、模具等表面, 摩擦系数小,化学稳定性好,具有优良的耐热、 耐磨、抗氧化、耐冲击等性能,既可以提高刀具、 模具等的工作特性,又可以提高使用寿命,一般 可使刀具寿命提高3~10倍。
磁控溅射的应用--固体润滑薄膜
• 在高温、超高真空、射线辐照等特殊条件下工作 的机械部件不能用润滑油,只有用软金属或层状 物质等固体润滑剂。
制集成电路的鉭膜,首次实现溅射镀膜产业化; 1970年圆柱磁控溅射阴极获得工业应用; 1980年前后,提出脉冲单靶磁控溅射、中频单靶磁控溅射,
发展为中频双靶磁控溅射; 1986年Kirchhoff 等申请双靶磁控溅射方法的专利; 1986年Window发明了非平衡溅射,有广阔的应用前景 1994年德国Leybold的孪生靶系统正式投入生产;
circular trajectory
TMF=0 G
TMF=10 G TMF=20 G
TMF=30 G
弧
弧
斑
斑
尺
速
寸
度
TMF=0 G
TMF=15 G
TMF=30 G
轴对称磁场对弧斑运动的影响
电弧离子镀大颗粒问题的解决
电弧离子镀的改进 轴对称磁场
TMF=0 G
TMF=15 G
TMF=30 G
锥形坑
平整下凹
薄膜/涂层制备技术 (磁控溅射和电弧离子镀)及应用
雷浩
薄膜/涂层的概念与特点
概念:薄膜/涂层是一类用特殊方法获得的,依 靠基体支撑并具有与基体不同的结构和性能的 二维材料。薄膜(Films):厚度 < 1m,如光电功 能薄膜等;涂层(Coatings):厚度 ≥ 1m,如硬质 涂层、防护涂层等。
20世纪80年代美国多弧公司购买了苏联技术,实现了产 业化,并在西方得到了迅速发展;
20世纪80年代后,我国引进了大量设备和技术。此后, 该技术得到了迅速发展。
电弧离子镀的设备
真空电弧蒸发源及电弧离子镀设备
电弧离子镀常用的弧源和靶材结构
轴向磁场控制的圆形小弧源
俄罗斯弧源
可控电弧蒸发源 柱状弧源 矩形平面大弧源
电弧离子镀大颗粒问题的解决
电弧离子镀的改进 双层挡板屏蔽
(a)
靶材
基板
(b)
10m
双层挡板
特点:
–物理屏蔽;
10m
–沉积速率降低;
电弧离子镀大颗粒问题的解决
电弧离子镀的改进 轴对称磁场
Transverse magnetic field, Gs
Normal magnetic field, Gs
Distance from center, cm Distance from center, cm
电弧离子镀的应用--装饰镀膜
电弧离子镀的应用--装饰镀膜
电弧离子镀的应用--刀模具表面强化
电弧离子镀的应用--刀模具表面强化
电弧离子镀的应用--刀模具表面强化
电弧离子镀的应用--刀模具表面强化
谢谢!!
50
弧斑运动对靶材刻蚀利用率的影响
电弧离子镀大颗粒问题的解决
电弧离子镀的改进 动态拱形磁场
磁场位形
拱形磁场位形随电流比的变化
动态拱形磁场控制的离子镀弧源设计
电弧离子镀大颗粒问题的解决
永磁铁
电磁线圈
传统弧源(轴对称磁场)
俄罗斯弧源(纵向磁场)
静态/准静态磁场
电弧离子镀大颗粒问题的解决
解决大颗粒喷射的新思路 弧斑运动速度和分布 磁场位形设计
• 常用的固体润滑剂有软金属(Au,Ag,Pb,Sn等), 层状物质(MoS2,WS2,石墨,CaF2,云母等), 高分子材料(尼龙、聚四氟乙烯等)等。
• 其中溅射法制取MoS2膜及聚四氟乙烯膜十分有效。
磁控溅射的应用--透明导电薄膜
• 厚度:几十~几百纳米 • 透明性:与玻璃接近 • 导电性:与金属接近 • 种类:
氧化铟锡 (ITO); 掺铝氧化锌 (ZAO); ITO/Ag/ITO; TiO2/Ag/TiO2; ITO/ZnO;SiO2/ITO
磁控溅射的应用--透明导电薄膜
液晶显示器 触摸屏
太阳能电池
磁控溅射的应用--透明导电薄膜
有机/柔性电致发光器件(OLED)
磁控溅射的应用--透明导电薄膜
除霜防雾
等等离离子子体体 靶靶材材
NN 靶SS材 NN
优点:稳定性、重复性、均匀性、低温
种类:化合物、合金、梯度膜、多层膜
磁控溅射的靶材
磁控溅射镀膜设备与等离子体
磁控溅射的应用
溅射薄膜按其不同的功能和应用可大致分 为机械功能膜和物理功能膜两大类。前者 包括耐磨、减摩、耐热、抗蚀等表面强化 薄膜材料、固体润滑薄膜材料;后者包括 电、磁、声、光等功能薄膜材料等。
磁控溅射的种类
成膜条件:1、靶材 2、Ar 3、周围的真空环境
反应类型
非反应溅射
电源类型 反应溅射
直流磁控溅射 中频磁控溅射 射频磁控溅射
磁控溅射的种类
• 传统磁控溅射
电电流流密密度度>~ 5m01.1mAmA/Ac/mc/cmm222
• 非平衡磁控溅射
S
S
基基靶板板材
等离子体
等基离板子体
• 闭合场非平衡磁控溅射
磁控溅射的历史
1842年Grove发现阴极溅射现象; 1877年将二极溅射技术用于镀制反射镜; 二十世纪三十年代采用二极溅射技术镀制金膜作为导电
底层以后出现射频溅射、三极溅射和磁控溅射; 1936年和1940年Penning相继发明圆柱和圆筒磁控溅射
阴极; 1963年美国贝尔实验室采用10米的连续溅射镀膜装置镀
磁场约束遮挡过滤: –等离子体发射方向与镀膜方向垂直; –束径不受限制,但沉积率比较低;
电弧离子镀大颗粒问题的解决
电弧离子镀的改进 脉冲偏压
–通过对基片施加脉冲偏压减少等 离子体中的颗粒沉积;
原理:利用等离子体尘埃带负电 的特点,通过脉冲偏压的动态等 离子体壳层控制尘埃颗粒沉积;
特点: –沉积效率降低比较小; –可以实现化合物的低温沉积; –可以改善薄膜的力学性能; –特别大的颗粒过滤效果不理想;
旋转磁场 弯曲磁场 轴对称磁场 拱形磁场 尖角磁场
+
= 动态磁场
磁场位形 横向分量 纵向分量
创新点:1. 弧源头 2.弧斑运动速度提高 3. 纵/横向磁场均匀分布
电弧离子镀大颗粒问题的解决
多极磁芯
难点: 1. 线包的发热 2. 磁芯耐涡流损耗
传统弧源
新型弧源
电弧离子镀大颗粒问题的解决
电弧离子镀的改进 旋转横向磁场
概念:利用气体放电产生的正离子在电场作用下轰击作为 阴极的靶,使靶材中的原子(或分子)逸出并沉积到基板 表面上形成所需要的膜。在阴极靶面上造一个正交的磁场, 使得电离的几率增加,就成为了磁控溅射。
磁控溅射的特点
优点: 涂层致密质量好;可控制涂层厚度;电子对于衬底 的轰击能量小;可获得理想纳米涂层;原子沉积 缺点: 沉积速度较慢;需要高真空状态;方向性较强
保温、隔热
磁控溅射的应用--透明导电薄膜
电磁屏蔽
雷达隐身
电弧离子镀(Arc Ion Plating)的介绍
电弧离子镀 (Arc Ion Plating, AIP)或称之为阴极真 空弧沉积(Cathodic vacuum Arc Deposition, CAD), 是在真空环境下利用电弧放电 蒸发作为镀料粒子源 实现离子镀的一种方法,是离化率最高的离子镀形式。
脉冲弧源
电弧离子镀的设备
国产
俄罗斯
欧洲
电弧离子镀的设备
国产
电弧离子镀的工艺问题
电弧离子镀工艺的几个问题:
大颗粒的喷射 靶材利用率 放电稳定性
大颗粒的排除 沉积速率 沉积均匀性
弧斑运动的控制
轴对称磁场 动态可控磁场
磁场 旋转磁场
等离子体传输的控制
磁场增强 磁过滤
电弧离子镀的大颗粒问题
薄膜/涂层的种类及应用
• 电子工业:电极、电阻膜、电介质膜、绝缘膜、 透明导电膜、超导膜等。
• 光学工业:荧光膜、反射膜、增透膜、干涉膜 等。
• 机械工业:硬化膜、耐热膜、耐腐蚀膜等。 • 能源工业:聚热膜、防反射膜、透射膜等。 • 传感器:热敏、气敏、压敏、氧气传感器、红
外线传感器等。 • 其它:装饰膜等。
热 蒸 发
磁 控 溅 射
电 弧 离 子 镀
物理气相沉积(PVD)
定义:薄膜材料通过物理方法输运到基体表面 代表技术:蒸发镀膜、溅射沉积、电弧离子镀、 离子束辅助沉积、脉冲激光沉积、离子束沉积、 团簇沉积等。 技术特点:沉积温度低、工作气压比较低
磁控溅射 (Magnetron Sputtering)的介绍
电弧源:靶(导电材料)+约束磁场+弧电极+触发电极 优点:沉积速度快;膜基结合力高;薄膜致密度高; 绕镀性好等。