秦京输油管道腐蚀机理分析及腐蚀检测
油田输油管道腐蚀检测技术研究与应用
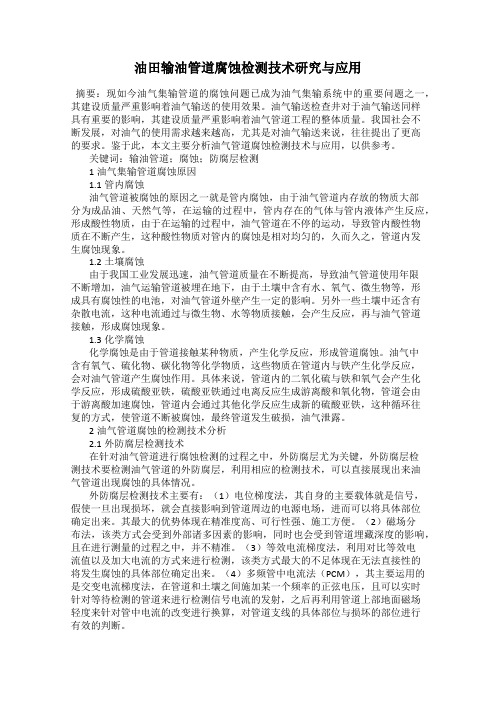
油田输油管道腐蚀检测技术研究与应用摘要:现如今油气集输管道的腐蚀问题已成为油气集输系统中的重要问题之一,其建设质量严重影响着油气输送的使用效果。
油气输送检查井对于油气输送同样具有重要的影响,其建设质量严重影响着油气管道工程的整体质量。
我国社会不断发展,对油气的使用需求越来越高,尤其是对油气输送来说,往往提出了更高的要求。
鉴于此,本文主要分析油气管道腐蚀检测技术与应用,以供参考。
关键词:输油管道;腐蚀;防腐层检测1油气集输管道腐蚀原因1.1管内腐蚀油气管道被腐蚀的原因之一就是管内腐蚀,由于油气管道内存放的物质大部分为成品油、天然气等,在运输的过程中,管内存在的气体与管内液体产生反应,形成酸性物质,由于在运输的过程中,油气管道在不停的运动,导致管内酸性物质在不断产生,这种酸性物质对管内的腐蚀是相对均匀的,久而久之,管道内发生腐蚀现象。
1.2土壤腐蚀由于我国工业发展迅速,油气管道质量在不断提高,导致油气管道使用年限不断增加,油气运输管道被埋在地下,由于土壤中含有水、氧气、微生物等,形成具有腐蚀性的电池,对油气管道外壁产生一定的影响。
另外一些土壤中还含有杂散电流,这种电流通过与微生物、水等物质接触,会产生反应,再与油气管道接触,形成腐蚀现象。
1.3化学腐蚀化学腐蚀是由于管道接触某种物质,产生化学反应,形成管道腐蚀。
油气中含有氧气、硫化物、碳化物等化学物质,这些物质在管道内与铁产生化学反应,会对油气管道产生腐蚀作用。
具体来说,管道内的二氧化硫与铁和氧气会产生化学反应,形成硫酸亚铁,硫酸亚铁通过电离反应生成游离酸和氧化物,管道会由于游离酸加速腐蚀,管道内会通过其他化学反应生成新的硫酸亚铁,这种循环往复的方式,使管道不断被腐蚀,最终管道发生破损,油气泄露。
2油气管道腐蚀的检测技术分析2.1外防腐层检测技术在针对油气管道进行腐蚀检测的过程之中,外防腐层尤为关键,外防腐层检测技术要检测油气管道的外防腐层,利用相应的检测技术,可以直接展现出来油气管道出现腐蚀的具体情况。
秦京线输油管道土壤腐蚀的模糊综合评判_范强
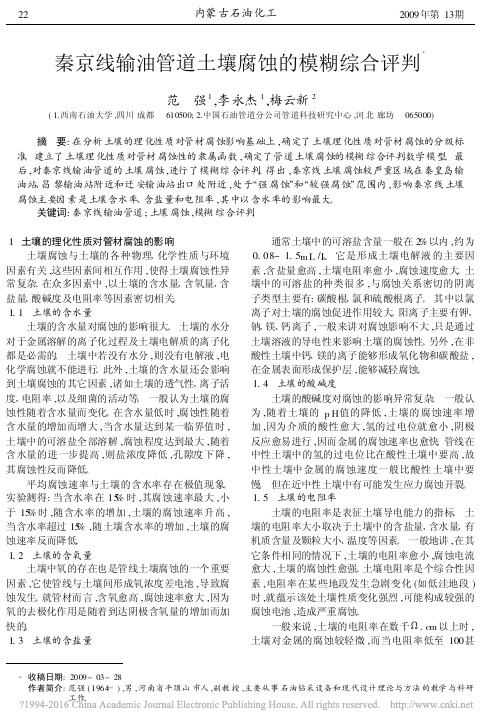
值等各种环境因素 ,按照一定的方法计算出相关的 评价总分 ,再按评价总分或有关指数判断土壤的腐
蚀性。 但由于影响土壤腐蚀的大多数因素具有不确
定性和不精确性 , 即既有随机性 ,又大多 属于模糊
平均腐蚀速率与土壤的含水率存在极值现象。 实验测得: 当含水率在 15% 时 ,其腐蚀速率最大 ,小 于 15% 时 ,随含水率的增加 ,土壤的腐蚀速率升高 , 当含水率超过 15% ,随土壤含水率的增加 ,土壤的腐 蚀速率反而降低。 1. 2 土壤的含氧量
土壤中氧的存在也是管线土壤腐蚀的一个重要
因素 ,它使管线与土壤间形成氧浓度差电池 ,导致腐 蚀发生。就管材而言 ,含氧愈高 ,腐蚀速率愈大 ,因为 氧的去极化作用是随着到达阴极含氧量的增加而加
弱 - - - 强 - - - 中等 强
0. 33
8 66# - 67# ( 41) 秦京 线昌黎站 较弱
弱
强 弱 中等 弱
0. 444
9 106# - 107# ( 6) 秦京 线迁安站 中等
弱 - - - 较强 中 等 中等 0. 581
10 145# - 100M 秦京 线迁安站
弱
弱 - - - 强 较弱 弱
秦京线
弱 - -- - -- 弱 强 弱
0. 53
19 36# ( 东 )
秦京线
弱 - - - - - - 中等 强 强
0. 33
20 36# ( 东 )
秦京线
弱 - -- - -- 强 强 强
0. 6- -- 弱 强 弱
0. 53
22 迁安出 口处
秦京线
弱 - - - - - - 中等 强 强
快的。 1. 3 土壤的含盐量
通常土壤中的可溶盐含量一般在 2% 以内 ,约为 0. 08- 1. 5m L /L。 它是形成土壤电解液 的主要因 素 ,含盐量愈高 ,土壤电阻率愈小 ,腐蚀速度愈大。土 壤中的可溶盐的种类很多 ,与腐蚀关系密切的阴离 子类型主要有: 碳酸根、氯和硫酸根离子。 其中以氯 离子对土壤的腐蚀促进作用较大。阳离子主要有钾、 钠、镁、钙离子 ,一般来讲对腐蚀影响不大 ,只是通过 土壤溶液的导电性来影响土壤的腐蚀性。另外 ,在非 酸性土壤中钙、镁的离子能够形成氧化物和碳酸盐 , 在金属表面形成保护层 ,能够减轻腐蚀。 1. 4 土壤的酸碱度
油管道的腐蚀原因和防腐措施探讨

油管道的腐蚀原因和防腐措施探讨油管道的腐蚀原因可以分为两大类,一类是外部腐蚀,一类是内部腐蚀。
外部腐蚀往往是由环境因素引起的,如土壤湿度、土壤化学成分、气候条件和地质条件等。
这些因素会导致外部腐蚀物质如水、氧和酸等接触到管道表面,从而引发腐蚀。
内部腐蚀则主要是由输送的流体中含有的腐蚀性成分引起的,如硫化氢、二氧化碳和酸性化学物质等。
这些物质会损害管道内壁,从而导致内部腐蚀。
为了防止油管道的腐蚀,各种防腐措施被采用。
其中,常见的方法包括防腐涂层、防腐油漆、防腐土壤覆盖、防腐电流和防腐合金等。
防腐涂层是油管道最常见的防腐措施之一、它通过在管道表面涂覆一层特殊的涂料,形成一个防护层,隔绝了外部环境和管道金属之间的接触。
防腐涂层可以选择各种合适的材料,如环氧树脂、聚乙烯和聚胺脂等。
这些涂料具有耐腐蚀、耐磨损和耐高温的特性,能有效地阻止腐蚀物质对管道的侵蚀。
防腐油漆是一种在管道表面形成的一层薄膜,类似于防腐涂层。
它通常是一种油基或溶剂基的液体材料,可以通过喷涂或刷涂的方式施工在油管道表面。
防腐油漆具有极强的抗腐蚀性能,可以防止外部环境对管道金属的侵蚀。
防腐土壤覆盖是防止外部腐蚀的一种重要措施。
在安装油管道时,通常会在管道下方铺设一层特殊材料的土壤,称为防腐土壤。
这种土壤富含抗腐蚀物质,可以隔离管道与环境的接触,减少腐蚀的风险。
防腐电流是一种通过施加外部电流来保护管道免受腐蚀的方法。
它利用电流作用于管道表面形成一层保护膜,阻碍腐蚀物质的侵蚀。
这是一种被广泛应用的技术,特别适用于埋地管道。
防腐合金也是一种有效的防腐措施。
通过添加抗腐蚀元素如钼、铬和镍等,可以增强管道金属的抗腐蚀性能。
这些元素能够与腐蚀物质产生化学反应,形成物理上的屏障,阻止腐蚀的发生。
总之,油管道的腐蚀原因多种多样,需采取一系列的防腐措施来保护管道的完整性和安全性。
防腐涂层、防腐油漆、防腐土壤覆盖、防腐电流和防腐合金等都是常见的防腐措施。
通过对不同情况的综合考虑和合理选择,可以有效地减少腐蚀对油管道的影响,确保其长期安全运营。
某油田输油管道腐蚀检测结果分析
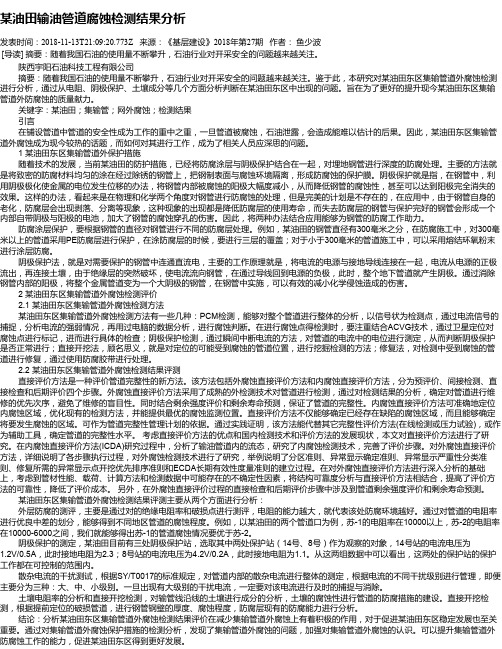
某油田输油管道腐蚀检测结果分析发表时间:2018-11-13T21:09:20.773Z 来源:《基层建设》2018年第27期作者:鱼少波[导读] 摘要:随着我国石油的使用量不断攀升,石油行业对开采安全的问题越来越关注。
陕西宇阳石油科技工程有限公司摘要:随着我国石油的使用量不断攀升,石油行业对开采安全的问题越来越关注。
鉴于此,本研究对某油田东区集输管道外腐蚀检测进行分析,通过从电阻、阴极保护、土壤成分等几个方面分析判断在某油田东区中出现的问题。
旨在为了更好的提升现今某油田东区集输管道外防腐蚀的质量献力。
关键字:某油田;集输管;网外腐蚀;检测结果引言在铺设管道中管道的安全性成为工作的重中之重,一旦管道被腐蚀,石油泄露,会造成能难以估计的后果。
因此,某油田东区集输管道外腐蚀成为现今较热的话题,而如何对其进行工作,成为了相关人员应深思的问题。
1 某油田东区集输管道外保护措施随着技术的发展,当前某油田的防护措施,已经将防腐涂层与阴极保护结合在一起,对埋地钢管进行深度的防腐处理。
主要的方法就是将致密的防腐材料均匀的涂在经过除锈的钢管上,把钢制表面与腐蚀环境隔离,形成防腐蚀的保护膜。
阴极保护就是指,在钢管中,利用阴极极化使金属的电位发生位移的办法,将钢管内部被腐蚀的阳极大幅度减小,从而降低钢管的腐蚀性,甚至可以达到阳极完全消失的效果。
这样的办法,看起来是在物理和化学两个角度对钢管进行防腐蚀的处理,但是完美的计划是不存在的,在应用中,由于钢管自身的老化,防腐层会出现剥落、分离等现象,这种现象的出现都是降低防腐层的使用寿命,而失去防腐层的钢管与保护完好的钢管会形成一个内部自带阴极与阳极的电池,加大了钢管的腐蚀穿孔的伤害。
因此,将两种办法结合应用能够为钢管的防腐工作助力。
防腐涂层保护,要根据钢管的直径对钢管进行不同的防腐层处理。
例如,某油田的钢管直径有300毫米之分,在防腐施工中,对300毫米以上的管道采用PE防腐层进行保护,在涂防腐层的时候,要进行三层的覆盖;对于小于300毫米的管道施工中,可以采用熔结环氧粉末进行涂层防腐。
油田集输管道腐蚀检测与防护措施研究
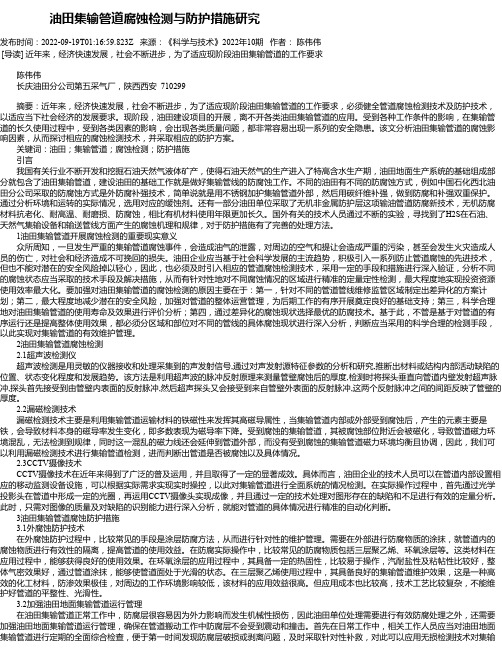
油田集输管道腐蚀检测与防护措施研究发布时间:2022-09-19T01:16:59.823Z 来源:《科学与技术》2022年10期作者:陈伟伟[导读] 近年来,经济快速发展,社会不断进步,为了适应现阶段油田集输管道的工作要求陈伟伟长庆油田分公司第五采气厂,陕西西安 710299摘要:近年来,经济快速发展,社会不断进步,为了适应现阶段油田集输管道的工作要求,必须健全管道腐蚀检测技术及防护技术,以适应当下社会经济的发展要求。
现阶段,油田建设项目的开展,离不开各类油田集输管道的应用。
受到各种工作条件的影响,在集输管道的长久使用过程中,受到各类因素的影响,会出现各类质量问题,都非常容易出现一系列的安全隐患。
该文分析油田集输管道的腐蚀影响因素,从而探讨相应的腐蚀检测技术,并采取相应的防护方案。
关键词:油田;集输管道;腐蚀检测;防护措施引言我国有关行业不断开发和挖掘石油天然气液体矿产,使得石油天然气的生产进入了特高含水生产期,油田地面生产系统的基础组成部分就包含了油田集输管道,建设油田的基础工作就是做好集输管线的防腐蚀工作。
不同的油田有不同的防腐蚀方式,例如中国石化西北油田分公司采取的防腐蚀方式是外防腐补强技术,简单说就是用不锈钢加护集输管道外部,然后用碳纤维补强,做到防腐和补强双重保护。
通过分析环境和运转的实际情况,选用对应的缓蚀剂。
还有一部分油田单位采取了无机非金属防护层这项输油管道防腐新技术,无机防腐材料抗老化、耐高温、耐磨损、防腐蚀,相比有机材料使用年限更加长久。
国外有关的技术人员通过不断的实验,寻找到了H2S在石油、天然气集输设备和输送管线方面产生的腐蚀机理和规律,对于防护措施有了完善的处理方法。
1油田集输管道开展腐蚀检测的重要现实意义众所周知,一旦发生严重的集输管道腐蚀事件,会造成油气的泄露,对周边的空气和提让会造成严重的污染,甚至会发生火灾造成人员的伤亡,对社会和经济造成不可挽回的损失。
油田企业应当基于社会科学发展的主流趋势,积极引入一系列防止管道腐蚀的先进技术,但也不能对潜在的安全风险掉以轻心,因此,也必须及时引入相应的管道腐蚀检测技术,采用一定的手段和措施进行深入验证,分析不同的腐蚀状态应当采取的技术手段及解决措施,从而有针对性地对不同腐蚀情况的区域进行精准的定量定性检测,最大程度地实现投资资源使用效率最大化。
输油管道的腐蚀原因分析及防护研究
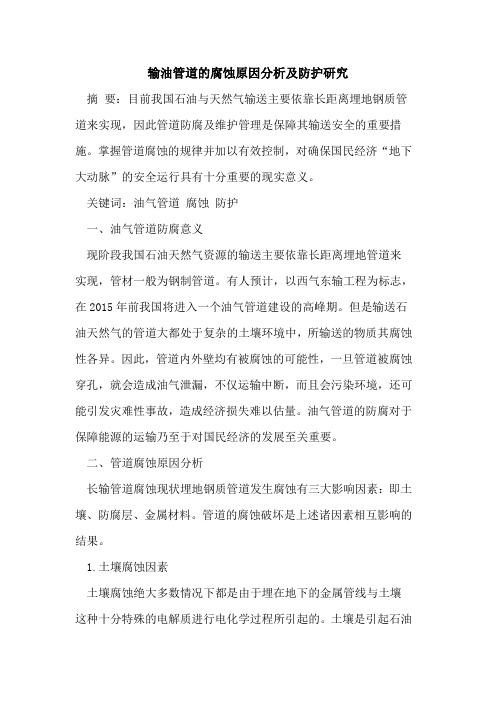
输油管道的腐蚀原因分析及防护研究摘要:目前我国石油与天然气输送主要依靠长距离埋地钢质管道来实现,因此管道防腐及维护管理是保障其输送安全的重要措施。
掌握管道腐蚀的规律并加以有效控制,对确保国民经济“地下大动脉”的安全运行具有十分重要的现实意义。
关键词:油气管道腐蚀防护一、油气管道防腐意义现阶段我国石油天然气资源的输送主要依靠长距离埋地管道来实现,管材一般为钢制管道。
有人预计,以西气东输工程为标志,在2015年前我国将进入一个油气管道建设的高峰期。
但是输送石油天然气的管道大都处于复杂的土壤环境中,所输送的物质其腐蚀性各异。
因此,管道内外壁均有被腐蚀的可能性,一旦管道被腐蚀穿孔,就会造成油气泄漏,不仅运输中断,而且会污染环境,还可能引发灾难性事故,造成经济损失难以估量。
油气管道的防腐对于保障能源的运输乃至于对国民经济的发展至关重要。
二、管道腐蚀原因分析长输管道腐蚀现状埋地钢质管道发生腐蚀有三大影响因素:即土壤、防腐层、金属材料。
管道的腐蚀破坏是上述诸因素相互影响的结果。
1.土壤腐蚀因素土壤腐蚀绝大多数情况下都是由于埋在地下的金属管线与土壤这种十分特殊的电解质进行电化学过程所引起的。
土壤是引起石油长输管线外(壁)腐蚀破坏的主要原因。
土壤是一个由气、液、固组成的多相体系,其透气性和含水性构成了埋地金属的电化学腐蚀环境,且大多数属于氧去极化腐蚀,只有在强酸性土壤中,才会发生氢去极化腐蚀。
其电极反应为:阳极反应:金属溶解并放出电子:fe→fe2++2e阴极反应:介质中的离子吸收电子的还原过程:2h++2e→h2↑(强酸性介质中)o2+4h++4e→2h2o(酸性介质中)o2+2h2o+4e→4oh(-中、碱性介质中)在土壤腐蚀中,阴、阳极过程受土壤结构及湿度的影响极大。
若土壤疏松、干燥,则阳极过程不易进行因为这时缺乏使金属成为水化离子的必要的水分,而氧的渗透和流动比较容易,即阴极反应容易进行。
整个腐蚀过程受阳极控制;而在潮湿的粘性土壤中,氧的渗透和流动速度均较小,但水分充足,所以腐蚀过程主要受阴极过程控制。
典型输油生产事故案例及分析

典型输油生产事故案例及分析案例1、1977年7月29日,秦京线进行正输时,上级调度通知秦皇岛管理处、北京管理处调度,秦京线11:00全线停止正输,12:00由石楼站启泵反输。
北京管理处调度接到调度令后,认为白天电压低,要求推迟到20:00启泵反输。
由于问题没有落实,秦京线11:00没有停止正输。
但是石楼泵站职工认为12:00启泵反输,积极作了准备,站领导请示北京处调度同意,于11:45通知操作工关闭秦京来油阀门,造成秦京线憋压达到5.4Mpa,将石楼站反输泵房过滤器憋漏,三组换热器垫子憋刺。
由于当班工人及时发现采取泄压,避免了一场恶性事故发生。
案情分析:该事故发生的关键点在于石楼站领导请示北京处调度要关闭秦京来油阀门时,北京处调度没有请示上级调度或和秦皇岛处调度落实是否秦京线已停输完毕,必须双方确认后方可执行操作;其次,秦皇岛管理处、北京管理处调度对上级调度令有疑异,应对上级调度提出,上级调度给予明确答复,做好记录,按上级调度令执行;三,石楼站操作工在关闭秦京来油阀门过程中,如有专人监视进站压力变化,发现压力异常升高,停止关阀并紧急打开该阀,事故可终止。
案例2、1980年2月15日晚,秦京线滦河东阀室,自1995年投运后(阀室压盖垫子使用的是石棉垫,耐压不耐油),经过5年运行,老化突然刺油,使迁安泵站出站压力下降。
迁安泵站向管理处调度汇报检查原因,处调度误判断是提温后结蜡情况好转,未能进一步检查原因和进行过细参数分析,直至社员报告阀门漏油后,才采取措施处理。
由于延误了发现漏油时间,结果造成跑油480吨。
案情分析:该事故发生的关键点在于阀室压盖垫子使用的石棉垫老化;但管理处调度判断失误造成事态扩大。
一般管道漏油计算机显示压力历史曲线有以下3种情况:停输再启动、提量、提温运行后,管道内原油结蜡情况逐步好转,由于腐蚀等原因造成的小的渗漏,这两种情况通过压力参数变化很难确定是那种,一般压力历史曲线都出现图A情况,遇到这种曲线,没有把握确定,只能安排人员巡线,该种情况,一般基于“负压波”原理的泄漏检测软件也很难准确判断;原油管道出现较大量的泄漏或者盗油造成跑油,一般压力历史曲线出现图B情况,该种情况,一般基于“负压波”原理的泄漏检测软件能够较准确判断漏油点,确定漏油点位置后,调度人员立即通知巡线人员对该位置巡线,并根据经验扩大巡线范围;管道被打孔盗油成功,一般压力历史曲线出现图C情况,与图B情况明显不同的就是压力下降一段时间(取决于盗油现场压力、被盗原油量等,一般持续10-20分钟)后,盗油分子装完一车,关闭盗油阀门,压力又回升至正常运行压力。
油气管道腐蚀机理及措施分析
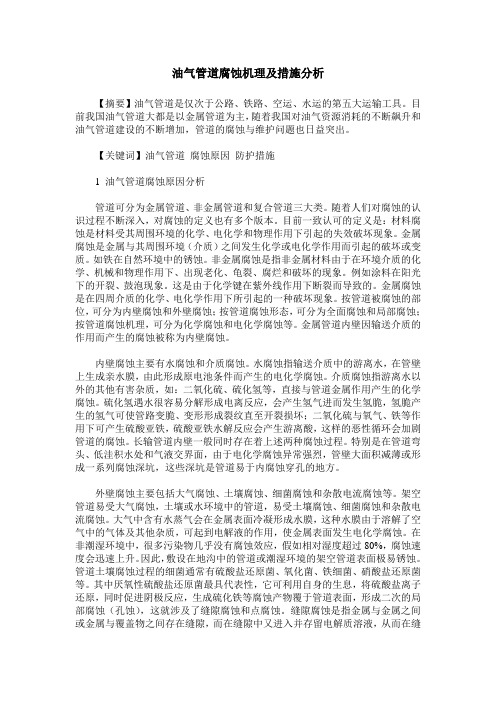
油气管道腐蚀机理及措施分析【摘要】油气管道是仅次于公路、铁路、空运、水运的第五大运输工具。
目前我国油气管道大都是以金属管道为主,随着我国对油气资源消耗的不断飙升和油气管道建设的不断增加,管道的腐蚀与维护问题也日益突出。
【关键词】油气管道腐蚀原因防护措施1 油气管道腐蚀原因分析管道可分为金属管道、非金属管道和复合管道三大类。
随着人们对腐蚀的认识过程不断深入,对腐蚀的定义也有多个版本。
目前一致认可的定义是:材料腐蚀是材料受其周围环境的化学、电化学和物理作用下引起的失效破坏现象。
金属腐蚀是金属与其周围环境(介质)之间发生化学或电化学作用而引起的破坏或变质。
如铁在自然环境中的锈蚀。
非金属腐蚀是指非金属材料由于在环境介质的化学、机械和物理作用下、出现老化、龟裂、腐烂和破坏的现象。
例如涂料在阳光下的开裂、鼓泡现象。
这是由于化学键在紫外线作用下断裂而导致的。
金属腐蚀是在四周介质的化学、电化学作用下所引起的一种破坏现象。
按管道被腐蚀的部位,可分为内壁腐蚀和外壁腐蚀;按管道腐蚀形态,可分为全面腐蚀和局部腐蚀;按管道腐蚀机理,可分为化学腐蚀和电化学腐蚀等。
金属管道内壁因输送介质的作用而产生的腐蚀被称为内壁腐蚀。
内壁腐蚀主要有水腐蚀和介质腐蚀。
水腐蚀指输送介质中的游离水,在管壁上生成亲水膜,由此形成原电池条件而产生的电化学腐蚀。
介质腐蚀指游离水以外的其他有害杂质,如:二氧化硫、硫化氢等,直接与管道金属作用产生的化学腐蚀。
硫化氢遇水很容易分解形成电离反应,会产生氢气进而发生氢脆,氢脆产生的氢气可使管路变脆、变形形成裂纹直至开裂损坏;二氧化硫与氧气、铁等作用下可产生硫酸亚铁,硫酸亚铁水解反应会产生游离酸,这样的恶性循环会加剧管道的腐蚀。
长输管道内壁一般同时存在着上述两种腐蚀过程。
特别是在管道弯头、低洼积水处和气液交界面,由于电化学腐蚀异常强烈,管壁大面积减薄或形成一系列腐蚀深坑,这些深坑是管道易于内腐蚀穿孔的地方。
外壁腐蚀主要包括大气腐蚀、土壤腐蚀、细菌腐蚀和杂散电流腐蚀等。
- 1、下载文档前请自行甄别文档内容的完整性,平台不提供额外的编辑、内容补充、找答案等附加服务。
- 2、"仅部分预览"的文档,不可在线预览部分如存在完整性等问题,可反馈申请退款(可完整预览的文档不适用该条件!)。
- 3、如文档侵犯您的权益,请联系客服反馈,我们会尽快为您处理(人工客服工作时间:9:00-18:30)。
陷是否危害管道的安全可靠性 ,并对缺陷的形成 、发 展 、结构失效过程及后果做出科学判断 ,避免不必要 的经济损失 。
(3) 加大管道的资金投入 ,尤其是“三穿”管段 , 对严重缺陷管段进行维修 。
(4) 在对防腐层进行大修时 ,应对焊缝进行检测 和评估 ,有针对性地开展维修 。
(收稿日期 :2006208221) 编辑 :吕 彦
将内外检测技术有机结合 ,用防腐层外检测结 果判断防腐层绝缘电阻率低 、有破损的点 ,初步判断 可能发生或已经发生的腐蚀 ;用内检测结果判断腐 蚀点的尺寸 、深度和形状 ,两者相对照 ,选择绝缘层 电阻率低而且有内外腐蚀发生的点进行防腐层大 修 ,可以为安全评价提供全面的基础数据资料 。
(2) 对秦京输油管道进行安全风险评估 ,确定缺
主题词 输油 管道 腐蚀 原因 分析 检测
一 、秦京管道腐蚀机理分析
秦京输油管道自 1975 年建成投产至今已经运 行了 30 多年 ,管道全长 348 km ,外防腐层采用石油 沥青 , 目前已经有多处出现老化龟裂 , 管体多处 腐蚀 。
1 、 土壤的细菌腐蚀 土壤中的细菌 (微生物) 参与金属腐蚀 ,主要有 硫酸盐还原菌 、中性硫化菌 、酸性硫化菌和铁细菌 等 。当植物的根系穿透管道防腐层时 ,这些细菌直 接作用在金属表面 ,加快了管体腐蚀 。丰润至宝坻 输油站间有一大片芦苇荡 ,管体发生腐蚀则是芦苇 根穿透了防腐层所致 。
456
20~30
948
1 908
29
35
30~40
275
514
10
16
40~50
137
209
3
4
50~60
74
119
© 1994-2010 China Academic Journal Electronic Publishing House. All rights reserved.
中 。该管道在建设时 ,受当时技术水平及检测技术 小裂纹时 ,此处形成阳极区域 ,而其它大部分防腐层
限制 ,存在着很多施工缺陷 ,其中管道斜口对接等部 状况良好则形成阴极区域 ,这样就会形成了大阴极 、
位是应力集中的地方 ;管道经过华北地区地震断裂 小阳极 ,造成防腐层破裂点流失的电流密度大 ,加速
·38 ·
油 气 储 运 2008 年
由表 1 看出 ,中轻度腐蚀点较多 ,这些点都是管 道安全运行的隐患 。图 1~图 4 为秦京输油管道各 段金属腐蚀点数量分布图 ,图 5 为管道金属腐蚀点 数量沿环向 (时钟位置) 分布情况 。表 2 为管道“三 穿”地段的腐蚀情况 ,其中 L 为正常壁厚的 25 %以 下的金属损失 ; M 为正常壁厚的 25 %~50 %之间的 金属损失 ; S 为正常壁厚的 50 %以上的金属损失 。
· 3 6 · 油 气 储 运
2008 年
防腐保温
秦京输油管道腐蚀机理分析及腐蚀检测
王书浩 3 孟力沛 肖 铭 康利红 宋建河
王英臣
(中国石油管道公司秦京输油气分公司)
(中国石油管道公司济南输油分公司)
王书浩 孟力沛等 :秦京输油管道腐蚀机理分析及腐蚀检测 ,油气储运 ,2008 ,27 (2) 36~39 。
·39 ·
Байду номын сангаас
表 2 管道“三穿”地段的腐蚀数据
腐蚀特征
腐蚀数量 (个)
腐蚀特征
腐蚀数量 (个)
L
4 269
M
157
S
6
本次检测共发现超过管道外径 3 %的变形点 38 处 ,其中秦皇岛 —迁安站 18 处 , 迁安 —宝坻站 11 处 ,宝坻 —房山站 6 处 ,房山 —凤凰亭 3 处 。
《油气储运》投稿要求
(1) 内容 与油气 (包括原油 、成品油 、天然气 、 液化气 、煤气 、浆体及其他介质) 储运工程有关的科 技文章 ,具备科学性 、创新性和实用性 ,篇幅不超过 8 000 字 (含图表) 。
(2) 标题 标题应高度概括地反映文章的主题 , 字数不超过 20 个 。
(3) 摘要 来稿须附 300 字左右的中文摘要及 相应的英文摘要 。
1991 年 ,秦京输油管道曾经做过一次系统的防 腐层外检测 ,对土壤的理化性质进行了分析 ,检测出 了管道外防腐层的绝缘电阻率 ,经过开挖验证发现 , 电阻率低于 2 000 Ω ·m2 的管段发生了管道外防腐 层老化龟裂 ,导致管道本体腐蚀 。对此 ,有针对性地 选择了管道外防腐层大修地段 ,同时对管道腐蚀点 按照相关标准的要求进行了补强处理 ,个别地段更 换了管段 ,提高了管道的运行安全系数 。
3 、 管道应力腐蚀和疲劳腐蚀 秦京输油管道在高温 、高压工况下运行 ,工艺流
渐降低 。加剂浓度为 15 mg/ kg 时 ,在汽油中获得 的减阻效果略低于柴油 ,原因为汽油在管道中流动 时 ,过高的雷诺数导致部分减阻剂分子链遭剪切降 解而失去减阻作用 。
(3) 减阻剂在经过广元 —成都段 294 km 的沿 程管壁摩阻剪切 、湍流剪切及江油局部摩阻剪切后 , 广元 —成都站间平均减阻率仍然保持在 80 %以上 , 表明其良好的抗管壁摩阻剪切 、湍流剪切以及局部 摩阻剪切性能 。但充分溶解在管输油品中的减阻剂 经过成都过滤器和泵剪切以后 ,则完全失去减阻作
© 1994-2010 China Academic Journal Electronic Publishing House. All rights reserved.
第 27 卷第 2 期 王书浩等 :秦京输油管道腐蚀机理分析及腐蚀检测
带 ,20 世纪 70 年代末曾经历了唐山大地震 ,造成滦 了腐蚀 。
河管道断裂 ,其他个别管段也产生了扭曲 、位移 ,致
使管道应力分布发生了很大的变化 。另外 ,该管道 已经处于疲劳期 ,各种性能指标都有所下降 ,在迁安
二 、管道防腐层外检测
输油站出站段固定墩位置曾因应力集中 ,以及频繁 的工艺流程倒换产生了腐蚀疲劳 ,从而造成了管道 腐蚀穿孔 。
(3) 杂散电流集中的区域 。 (4) 有金属套管处 。金属套管对管道阴极保护 产生了屏蔽 ,阻碍了保护电流的正常分布 ,易造成 腐蚀 。 (5) 管道“三穿”处 。“三穿”施工难度较大 ,技术 上有缺陷 ,管道投入运行后又难以维护 。
五 、管道防腐层大修的建议
(1) 防腐层外检测结果只是判断外防腐层性能 的一个依据 。但外检测技术尚存在死角 ,例如在检 测穿越河流段时 ,因信号衰减程度大 ,而无法进行准 确判断 ,甚至个别段落无接收信号 ; 在高压电线附 近 ,因干扰信号强 ,用选频变频法也无法对管道防腐 层状况进行检测 。内检测结果可以确认管道的内 、 外腐蚀点 ,甚至可以确认腐蚀点的形状 、面积和深 度 ,但是不能定量评价外防腐层的性能 。
4 、 杂散电流腐蚀 电气化铁路 、高压输电线 、多种用电设备接地等 杂散分布的电流都可视为杂散电流 。大地中杂散电 流造成的地电位差可达几伏甚至几十伏 ,对埋地管 道干扰强烈 。秦京输油管道沿线的铁路已改造为电 气化铁路 ,杂散电流对管道产生的腐蚀影响日益明 显 ,应当引起高度重视 。 5 、 金属材料不均匀性腐蚀 管体材料存在不均匀性 ,即表明存在着电位差 , 改造后的管道的金属材料与原管材金属在成分上存 在着差异 ,即产生了电位差 。在管道防腐层大修过 程中 ,曾发现个别管段腐蚀严重 ,而其他相邻管道却 保护得很好 ,周边也无其他影响因素 ,初步判断是管 道材质本身不均匀造成的 。另外 ,由于个别管段改
3 066000 ,河北省秦皇岛市海港区文化路 307 号 ;电话 : (0335) 3856424 。
© 1994-2010 China Academic Journal Electronic Publishing House. All rights reserved.
用 ,说明其无法经受过滤器和泵等的强剪切 。 (4) 试验中 ,除柴油在成县有分输之外 ,其余试
验均为没有分输情况下的试验结果 。由于管道实际 运行时分输时间较长 ,因此将更容易实现较高的管 道输量 ,而管道最大输量的获得是减阻剂和最优管 道运行工况共同作用的结果 。
(收稿日期 :2007201204) 编辑 :孟凡强
通过检测管道的防腐层 、阴极保护等电法保护 、 管道周边腐蚀环境 、土壤的理化性质等状况可以判 断管道所面临的主要腐蚀威胁 。在内检测技术推广 之前 ,主要采用选频变频法来测量防腐层绝缘电阻 率 ,通过绝缘电阻率的检测结果来判断外防腐层性 能 ,在不开挖的情况下 ,可以对防腐层老化及破损点 进行准确定位 ,并对防腐层缺陷的尺寸 、数量进行综 合统计 、评价 ,制定防腐层的治理方案 。
2 、 土壤氧气浓度差腐蚀 埋地管道因土壤密度不同 ,导致管道周围氧气
浓度存在差异 ,氧气浓度差是引起管道局部发生腐 蚀的主要因素之一 ,其作用机理为 ,由于输送介质中 氧的含量不同 ,氧浓度差产生电位差 ,贫氧区的管道 电极电位较负 ,则构成电池的阳极而加速腐蚀 ;富氧 区的管道电极电位较正 ,则构成电池的阴极 ,从而减 缓腐蚀 。对于大口径管道而言 ,由于管道顶部土壤 较干燥 ,透气性良好 ,而管道底部较潮湿 ,透气性差 , 因此管道底部的对地电位低于管道顶部的电位 ,底 部形成了阳极区域而发生腐蚀 ,管道腐蚀多发生在 管道的 2~4 点钟和 8~10 点钟位置 。
年 ,对秦京输油管道进行了内腐蚀检测 ,检测结果表 明 ,管道腐蚀严重 ,尤其是迁安 —宝坻站区间和石燕 线 ,具体数据见表 1 。
表 1 秦京输油管道内检测结果
壁厚损失 %
各站间管道的金属腐蚀点数量 (个)
秦皇岛 —迁安 迁安 —宝坻
宝坻 —房山 房山 —凤凰亭
0~20
16 244
38 078
687
第 27 卷第 2 期 王书浩等 :秦京输油管道腐蚀机理分析及腐蚀检测