离心风机CFD模拟及改进
离心风机流道设计及优化研究

离心风机流道设计及优化研究离心风机是目前常见的一种用于通风、排风、送风等工程领域的设备,其核心部件——流道设计和优化,对于风机的性能和效率具有重要影响。
在本文中,将探讨离心风机流道设计及优化的相关内容,并介绍一些常见的优化方法和技术。
一、离心风机流道设计的重要性在离心风机中,流道是将进入的气体引导并加速到风机出口的关键部分,其设计直接影响到风机的性能和效率。
合理的流道设计能够改善气体的流动情况,提高风机的压力能力和送风量,从而达到更高的效率和能耗降低。
而不合理的流道设计可能会导致流动不均匀、能量损失过多等问题,降低风机的性能。
二、离心风机流道设计的要点1. 流道截面设计:离心风机的流道截面形状对于气体流动的扩张和压力变化起着重要作用。
合理的截面设计应考虑流体的流动特性和气体性质,使得气体能够顺利地通过截面,避免过度扩张和收缩,从而减少气流的阻力和能量损失。
2. 纵向流道设计:纵向流道的设计主要考虑气流的加速和扩张,在保持流态稳定的前提下,提高风机的压力能力。
通过合理的纵向流道设计,可以使气流在流道内部能够顺利加速,并尽量减少阻力和湍流的产生,从而最大程度地提高离心风机的效率。
3. 流道表面光滑度:流道表面的光滑度对气流的流动阻力和损耗有着重要影响。
光滑的表面能够减少摩擦阻力,提高流道的效率。
因此,在流道设计中,应注意流道表面的加工工艺和涂层材料的选用,以保证流道表面的光滑度和微粗糙度控制在合理范围内。
三、离心风机流道优化的方法和技术1. 数值模拟与仿真:利用计算流体力学(CFD)方法,对离心风机的流场进行数值模拟和仿真分析,可以得到流道内气流的速度、压力等分布情况,进而评估不同设计方案的性能。
这种方法不仅能够快速进行流道设计的优化,还能够为流道的改进提供有效的思路和参考。
2. 正交试验设计:利用正交试验设计方法,对流道的关键参数进行多因素、多水平的试验,以寻找最佳的参数组合,优化流道设计。
通过实验数据的统计分析,可以确定不同参数对流场的影响程度和相互关系,为进一步的优化提供依据。
基于CFD的风力发电机械结构模拟与优化

基于CFD的风力发电机械结构模拟与优化一、引言随着环境保护意识的不断增强,清洁能源的重要性日益凸显。
风力发电作为一种可再生能源形式,通过利用风能将其转化为电能,成为当前最为广泛应用的清洁能源之一。
然而,在风力发电领域中,机械结构的设计和优化至关重要。
本文将介绍一种基于计算流体力学(CFD)的风力发电机械结构模拟与优化方法。
二、风力发电机械结构概述风力发电机械结构主要由风轮、发电机和传动装置组成。
风轮是将风能转化为机械转动能的关键部件,其叶片的设计和布局直接影响能量捕捉效率。
发电机则是将机械能转化为电能的关键装置,其输出功率受到多种因素的影响,如转速和负载等。
传动装置则用于将风轮的机械转动能顺利传递给发电机,同时调节转速以适应不同风速条件。
三、基于CFD的风轮流场模拟CFD是一种基于数值计算的流体力学模拟方法,能够模拟和分析流体在不同条件下的流动行为。
在风力发电机械结构中,风轮的设计和优化是重中之重。
通过CFD技术,可以对风轮的流场进行详细模拟,并优化叶片的设计。
首先,在风轮模拟中,需要确定合适的边界条件和穿越网格。
利用风洞试验得到的风速分布和风向数据,可以作为CFD模拟的边界条件。
然后,在计算网格中划分三维空间,以模拟风轮的流动行为。
接下来,进行CFD模拟计算,得到风轮的叶片表面压力分布、气流速度矢量图等重要参数。
通过分析这些参数,可以确定风轮在不同工况下的叶片受力情况和能量捕获效率。
最后,通过CFD优化算法,根据所得到的模拟结果,调整风轮的叶片设计进行优化。
例如,可以通过改变叶片的形状、切割角度、长度等参数,来提高风轮的整体效率。
CFD模拟和优化算法的迭代过程,能够帮助工程师们快速找到最优的叶片设计方案。
四、基于CFD的发电机分析与优化除了风轮的优化外,风力发电机械结构中的发电机也需要进行分析和优化。
发电机的转速、负载和温度等因素,直接影响发电效率和安全性。
通过CFD模拟,我们可以模拟发电机的热流场分布和温度变化。
离心风机算例分析CFD
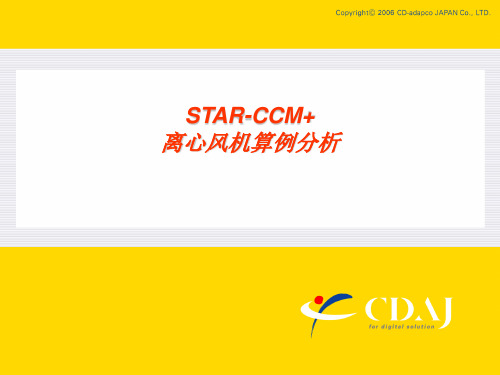
可见Байду номын сангаасBody 1 是 MRF面
Body 2 是 蜗壳和拉伸区域 Body 3 是 挡板 Body 4 是 叶片
重命名:取合适的 “Region名” 和 “Boundary名” 将 baffle 和 blade 这两个Region合并为一个Region,并命名这个Region为rotating
Boundary shell 是一个整体的面,查看shell Region的特征线, 准备将整体的面劈开,分开入口出口、拉伸区域、蜗壳
设定Under relaxation factor 为 0.4 设定Convergence Tolerance 为 0.1 0.2 0.05 0.7 0.1
设定迭代步数 1000
点击
开始计算
当计算不稳定,或者残差震荡时,适当减小松弛因子和容差,增加迭代步数,继续计算 (本例在1000步、3500步处减小了松弛因子和容差)
wrap后缝隙闭合
将Import删除,以Wrapped Surface作为下一步操作的面
更改Mesh 1的网格方案为Surface Remesher,Polyhedral Mesher
将Region mrf与Region pipe合并, 合并后 mrf 成为Region pipe中的一个Boundary 将网格方案从None改为Mesh 1
保持原缝隙处的特征线会给Remesh造成困难
重新抓 rotating blade的特征线 将 blade 和 baffle 合并,成为 blade
以60度角重新抓blade的特征线
Remesh参数的设定:Base Size设定为20mm blade尺度设定为2mm ~ 10mm 点击 生成 Remesh的面网格和 Poly 体网 格
螺杆空压机用多翼离心风机气动性能改进

螺杆空压机用多翼离心风机气动性能改进摘要:多翼离心风机以其体积小、结构紧凑、大流量系数、高压力系数及低噪声等特点在国民经济建设及人们日常生活中的使用范围与使用量越来越多,如空调、仪器设备的通风散热、厨房吸油烟机等,并在很多特殊使用场合下被公认为是一种最理想的风源设备,与人们的日常生活息息相关。
本文通过CFD技术,开展多翼离心风机气动特性研究,在保证安装接口以及散热能力不变的前提下,对各部件关键参数进行优化,改善风机气动性能,降低风量,从而提升整个冷却模块的散热效率。
关键词:多翼离心风机;数值模拟;气动性能;出口均匀性引言多翼离心风机因其整体尺寸小、流量系数大和噪声低等优点被广泛应用于吸油烟机和空调等各类通风换气设备中。
作为换气系统中重要的动力源,多翼式离心风机也是整个系统主要的噪声源。
其中,叶轮是离心风机中的旋转部件,对风机中的能量转换和传递起着重要作用,结构优良的叶轮对整个风机的性能至关重要。
目前国内外学者对叶轮的优化主要以提高风机的性能为目标,对叶轮的主要结构参数如叶片的型线,进出口安装角,进口集流器,蜗舌结构,叶轮与蜗壳的相对安装位置进行改进,每个参数的变化都会对风机的气动性能和噪声特性产生较大的影响。
1计算模型及方法1.1计算模型及网格划分多翼离心风机包括集流器、叶轮、蜗壳、扩压器。
模型计算域包括进口计算域、叶轮计算域、蜗壳计算域、扩压器及出口计算域,出口计算域做适当延伸。
同时保留蜗壳进风口处电机轴,提高计算精度。
出口计算域采用六面体网格,其余计算域采用四面体网格,叶轮区域网格适当加密。
根据湍流模型近壁面方程的要求,进行网格划分,总网格数约5.3×107。
1.2数值模拟方法叶轮区域采用旋转坐标系,并给定旋转速度1500r/min,其余采用静止坐标系。
各计算域间通过设置Interface插值。
设置叶轮所有叶片表面、轮盘表面以及电机轴外表面为旋转壁面,给定相应旋转速度。
风机进口采用压力进口边界条件,设置进口总压为0Pa(G),风机出口采用压力出口边界条件,设置出口静压为0Pa(G)。
基于CFD的风力发电机组优化设计
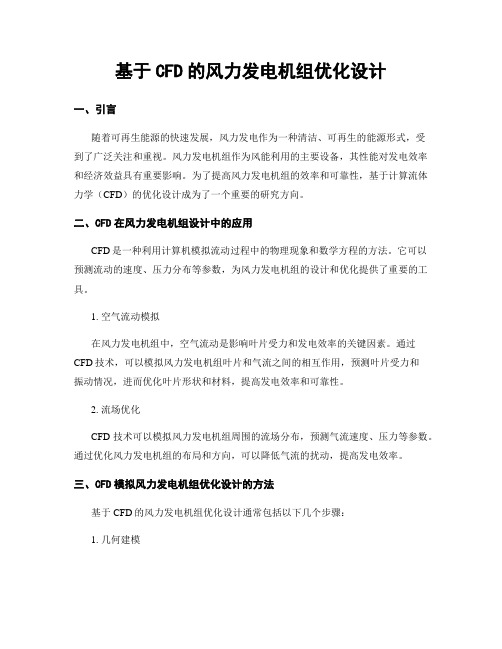
基于CFD的风力发电机组优化设计一、引言随着可再生能源的快速发展,风力发电作为一种清洁、可再生的能源形式,受到了广泛关注和重视。
风力发电机组作为风能利用的主要设备,其性能对发电效率和经济效益具有重要影响。
为了提高风力发电机组的效率和可靠性,基于计算流体力学(CFD)的优化设计成为了一个重要的研究方向。
二、CFD在风力发电机组设计中的应用CFD是一种利用计算机模拟流动过程中的物理现象和数学方程的方法。
它可以预测流动的速度、压力分布等参数,为风力发电机组的设计和优化提供了重要的工具。
1. 空气流动模拟在风力发电机组中,空气流动是影响叶片受力和发电效率的关键因素。
通过CFD技术,可以模拟风力发电机组叶片和气流之间的相互作用,预测叶片受力和振动情况,进而优化叶片形状和材料,提高发电效率和可靠性。
2. 流场优化CFD技术可以模拟风力发电机组周围的流场分布,预测气流速度、压力等参数。
通过优化风力发电机组的布局和方向,可以降低气流的扰动,提高发电效率。
三、CFD模拟风力发电机组优化设计的方法基于CFD的风力发电机组优化设计通常包括以下几个步骤:1. 几何建模首先,需要对风力发电机组的几何形状进行建模。
通过CAD软件或者其他建模工具,将发电机组的外形、叶片、塔筒等部件建立为三维模型。
2. 网格划分在CFD模拟中,需要将风力发电机组的模型划分为网格。
网格划分的好坏会直接影响模拟结果的准确性和计算效率。
通过合理划分网格,可以提高模拟的精度,同时控制计算资源的消耗。
3. 定义边界条件和物理模型在进行模拟之前,需要通过定义边界条件和选择适当的物理模型来规定模拟参数。
边界条件包括风速、气温、湍流强度等;物理模型则包括流体运动的方程、湍流模型等。
4. 求解流动场在CFD模拟中,通过求解Navier-Stokes方程组来计算流动场的速度、压力分布等参数。
根据模拟结果,可以获得叶片受力、振动情况等重要信息。
5. 优化设计基于CFD模拟结果,可以通过修改风力发电机组的几何形状、布局等进行优化设计。
离心式高温风机的性能优化与改进

离心式高温风机的性能优化与改进离心式高温风机是一种广泛应用于工业生产环境中的重要设备,它能够提供大量的气流和压力,用于通风、冷却、排尘等工艺过程。
然而,传统的离心式高温风机在运行过程中存在一些性能上的局限,如效率不高、噪音大、能耗过高等问题。
本文将讨论如何对离心式高温风机进行性能优化与改进,以提高其效率、降低噪音和能耗。
首先,要优化离心式高温风机的性能,可以从设计上入手。
传统的离心式风机通常采用的是单级或多级风叶设计,而在高温环境下,风叶的受热和热膨胀会对其性能造成不利影响。
因此,可以考虑采用复合材料或陶瓷材料制造风叶,以提高其耐高温性和稳定性。
此外,通过优化风叶的几何形状和布置方式,可以改善风叶的流动特性,提高风机的效率和稳定性。
其次,为了降低离心式高温风机的噪音水平,可以采用一系列噪音控制措施。
首先,对风机进行有效隔音,可以通过在风机外壳和进出风口处加装噪音吸音材料,减少噪音的传播和辐射。
其次,可以设计合理的进出风道布局,以减少气流的阻力和湍流噪音。
此外,还可以通过减少旋转部件的摩擦和振动,如增加轴承和减震装置的数量和质量,来降低噪音的产生和传播。
最后,为了改进离心式高温风机的能耗问题,可以从系统运行和控制上入手。
首先,可以利用变频器控制风机运行的转速,根据实际需求进行调节,以降低风机的运行能耗。
其次,可以通过优化风机系统的布置和连接方式,减少气流的泄漏和损失。
同时,还可以结合智能控制技术,利用传感器和自动化控制系统,实现风机的智能调节和优化运行,提高能源利用效率。
总之,离心式高温风机的性能优化与改进是一个多方面的课题,需要从设计、噪音控制和能耗等多个方面进行综合考虑。
只有通过对风机的结构和控制系统进行改进和优化,才能提高其效率和稳定性,降低噪音和能耗。
同时,还需要不断引入新的材料和技术,以适应不同高温环境下的需求。
通过持续的创新和改进,离心式高温风机的性能将得到进一步提升,为工业生产提供更可靠和高效的通风和冷却设备。
离心式高温风机的数字化设计与仿真分析

离心式高温风机的数字化设计与仿真分析离心式高温风机是一种常用于高温环境下的送风设备,具有很高的工作效率和可靠性。
为了进一步提高离心式高温风机的设计效率和减少开发成本,数字化设计与仿真分析成为了必不可少的工具。
本文将探讨离心式高温风机的数字化设计与仿真分析的关键步骤和方法。
首先,数字化设计是指利用计算机辅助设计软件对离心式高温风机进行几何参数设计和流体分析的过程。
在数字化设计的过程中,需要收集离心式高温风机的设计要求和工作条件,例如流量需求、压力需求和工作温度等。
根据这些要求,可以确定离心式高温风机的几何参数,例如叶轮的型状、尺寸和叶片数等。
在数字化设计的过程中,需要借助计算机辅助设计软件进行几何参数的优化。
常用的软件包括CATIA、SolidWorks和AutoCAD等。
这些软件不仅能够快速构建离心式高温风机的三维模型,还能够对模型进行参数化设计,实现快速设计和修改。
通过数字化设计,可以减少人力成本和设计周期,并且提高设计的精度和一致性。
在数字化设计完成后,需要进行离心式高温风机的流体分析。
流体分析是指利用计算流体力学(CFD)软件对离心式高温风机内部的流场进行模拟和预测的过程。
通过流体分析,可以评估离心式高温风机在不同工况下的性能和效率。
例如,可以预测风机的风量、风压和效率等。
在流体分析的过程中,需要将离心式高温风机的三维模型导入到CFD软件中,并设定相应的边界条件和求解器选项。
常用的CFD软件包括ANSYS Fluent、STAR-CCM+和OpenFOAM等。
这些软件能够对离心式高温风机的流动过程进行模拟,得到流速、压力和温度等变量的分布情况。
通过流体分析的结果,可以判断离心式高温风机的性能是否满足设计要求,并对离心式高温风机的几何参数进行优化。
例如,可以调整叶轮的叶片形状和角度,以提高风机的效率和压能。
同时,还可以优化离心式高温风机的进出口通道,减小流场的损失和湍流程度。
除了数字化设计和仿真分析,离心式高温风机的设计还需要考虑材料和制造工艺等因素。
基于CFD的多翼离心换气扇整流罩的改进设计

基于CFD的多翼离心换气扇整流罩的改进设计
谢军龙;许范;钟小普;尹巧朵;舒朝晖
【期刊名称】《流体机械》
【年(卷),期】2012(040)012
【摘要】基于CFD数值模拟软件对一前弯多翼离心换气扇的整流罩进行了改进设计.结果表明:换气扇的全压随整流罩弧形高度的增大而提高,随弧度半径的增大而降低;与原模型相比,整流罩改进后的换气扇全压提高了8%.在叶轮的前盘位置附近处,存在着明显的回流现象,在整流罩内的边缘处也有漩涡现象.改进后的漩涡较原模型有明显的改善,气流流过叶片后,动压值显著增大,静压值变化不明显,当气流离开叶轮进入蜗壳后,静压值沿蜗壳径向方向,呈现明显的增大趋势.
【总页数】4页(P15-18)
【作者】谢军龙;许范;钟小普;尹巧朵;舒朝晖
【作者单位】华中科技大学,湖北武汉,430074
【正文语种】中文
【中图分类】TH43
【相关文献】
1.基于CFD的内附翼无人机的气动设计与验证 [J], 许雪梅;张洁;华杰;;;
2.基于CFD流场分析的船用离心泵r性能改进方法 [J], 黎南;张欣
3.基于CFD仿真的列供离心风机风道分析与改进 [J], 吴飞;庞博;冯崎源
4.CFD分析概述及在离心泵改进设计中的应用 [J], 蒙盛吉
5.基于CFD的内附翼无人机的气动设计与验证 [J], 许雪梅;张洁;华杰
因版权原因,仅展示原文概要,查看原文内容请购买。
- 1、下载文档前请自行甄别文档内容的完整性,平台不提供额外的编辑、内容补充、找答案等附加服务。
- 2、"仅部分预览"的文档,不可在线预览部分如存在完整性等问题,可反馈申请退款(可完整预览的文档不适用该条件!)。
- 3、如文档侵犯您的权益,请联系客服反馈,我们会尽快为您处理(人工客服工作时间:9:00-18:30)。
2005 Fluent 中国用户大会论文集由于CFD计算可以相对准确地给出流体流动的细节,如速度场、压力场、温度场等特性,因而不仅可以准确预测流体产品的整体性能,而且很容易从对流场的分析中发现产品和工程设计中的问题,所以在国外已经逐步得到广泛的应用。
另外,跨学科组合优化设计方法也已经成为复杂叶轮产品的设计平台。
如今,CFD技术运用于风机的实例在我国已不少见,但由于计算机计算能力的限制,模型过于简单。
如单独一个离心叶轮的流道或单独算一个蜗壳;或运用一个流道与蜗壳迭代计算的方法研究风机内部流动,上述模型均忽略了由于蜗壳型线的非对称而导致叶轮各叶道流动呈现的非对称流动特征,而且从离心风机通道内流场分析来看,各部件间的相互影响很严重,所以,必须充分考虑它们之间的相互影响,不能孤立地分别研究[2]。
本文应用Fluent流动分析软件,计算某型号离心通风机全流场,详细得到通风机内部流场流动情况,并根据气动流场,对叶轮前盘形状和蜗壳出口部位等进行优化设计,同时,运用多学科优化平台软件OPTIMUS集成流体计算软件FLUENT,优化计算通风机进口型线,比较集成优化型线与单独用Fluent反复计算的结果,两者基本接近,说明集成优化是可信的。
将流动区域分为三部分:通风机进口部分、叶轮和蜗壳。
进口部分和蜗壳是静止元件,叶轮转动,采用gambit进行参数化建模。
整个通风机的网格数为80 万,网格采用四面体和六面体混合的非结构网格技术。
气体在通风机内流动时,它的气动性能在很大程度上由它本身的造型决定。
由于流道形状、哥氏力和粘性力的影响,通风机内的气体流动十分复杂。
一般认为气流在叶轮内的相对运动和在静止元件内的绝对运动为定常流,而且通风机内的气体压强变化不大,可忽略气体的压缩性。
因此,通风机内的流动是三维、定常、不可压缩流动。
求解相对稳定的、三维不可压缩雷诺平均N-S方程,湍流模型采用标准的εκ?两方程模型,采用一阶迎风格式离散方程,用SIMPLE方法求解控制方程。
在OPTIMUS提供的优化算法中,采用序列二次规划算法。
3 数值计算结果与分析 3.1原通风机建模及数值模拟原有离心通风机存在风量不足、风压不均匀等问题,所以首先对原通风机模型进行数值模拟,分析其内部气流流动状况,找出问题所在。
图 1 原通风机子午面的速度分布表2 原通风机回转面的速度分布叶轮出口部位的速度分布很不均匀,在叶轮前半部分,叶轮不出风反而进风,所以此处有较多逆流存在。
观察叶轮子午面上速度分布如图1所示,可以看到叶轮出口明显的逆流现象。
风机出风口有较多逆流现象,如图2所示。
通过上述流场仿真计算,可以确定原通风机的气动性能很不好。
分析气动流场,认为性能差的原因主要基于三个方面:1叶片进口部位缺乏导流部分,气体流动的流线不能折转,所以造成叶片前半部分压强低,产生逆流。
由于叶轮出口有较多逆流,导致进入蜗壳的气流速度不均匀。
2原模型叶轮采用前向叶片,叶轮的前盘采用平前盘。
平前盘制造简单,但对气流的流动情况有不良影响[3]。
3通风机蜗壳出口的面积过大,所以在蜗壳出口处压力过低而产生较多的逆流。
3.2通风机改型优化计算优化是对通风机改型以得到较好气动性能的过程。
针对原通风机模型气动流场中存在的问题,在结构上作一些相应修改。
3.2.1 改进模型A 针对原通风机模型计算中存在的叶片前半部分逆流现象严重的问题,将叶轮前盘改为弧线型,使计算结果改善。
但由于将叶轮的前盘改为弧形,而使叶轮出口宽度减小,所以为了不降低流量,将叶轮的轴向尺寸增加。
叶轮出口宽度增加到252mm。
如此改动后,叶轮沿子午面速度分布如图3所示。
改为弧形前盘,对气流进行导流,则气动性能改善。
与原模型相比,通风机的出口风压增加24.9%,出口流量增加17%,轴功率增加9.4%,效率增加7.6%。
2005 Fluent 中国用户大会论文集90 气动性能有所改善,但轴功率增加。
通过观察通风机内部气流的流动情况,叶轮进口部位的流动得到好转,但蜗壳出口部位的流动仍然不好,蜗壳出口仍然存在着逆流现象。
3.2.2 改进模型B 在模型A的基础上,把蜗壳出口部位的尺寸减小,消除了蜗壳出口逆流的现象。
蜗壳出口截面的位置没有改变,但尺寸减小。
出口风量有所减小,但转矩减小,轴功率减小,出口总压增加,效率提高。
可见气动特性有很大的提高。
原蜗壳模型改进模型B 图3 蜗壳改动前后z=-0.2 压力分布蜗壳出口改动之后,出口截面尺寸减小,质量流量有所下降,但蜗壳出口逆流面减少,效率提高7.4%,轴功率减小12%。
说明改动使通风机内部的气动流场得到较大改善。
3.2.3 改进模型C 离心式通风机的空气动力特性除了取决于叶轮内部的结构之外,还与通风机的进口形状密切相关,进口又称为集风器,其形状对风机的性能有很大的影响。
在改进模型B的基础上,进一步改善叶轮进口的流动情况。
对进口管道处做成缩放型,从而与叶轮轮盖处的曲线对接,使流动平缓地从轴向转向径向使进口气流缓慢从轴向向径向过渡。
通风机网格数130万。
通过多次改变进气管形状计算,最终得到较好模型。
改进模型的气动性能大为改善,通风机出口总压增加14.1%,出口流量增加6.9%,效率提高8.21%,轴功率增加0.1%。
所以通风机进口部位型线对气流的导向作用非常关键。
若把物体制成流线型,可使边界层的分离点后移,甚至不发生分离,阻力系数大大减小。
在此,一方面减小阻力,另一方面对气流流动起导向作用,使叶轮进口速度分布均匀,流动状况好转。
2005 Fluent 中国用户大会论文集91 图 4 改进模型C沿叶轮子午面速度分布图5 改进模型C回转面速度分布图6 通风机内部气流运动轨迹在子午平面上,流动被很好的导向。
由于蜗壳的存在,使得每一个流道内的速度和压力分布是非对称的。
表一模型改进性能参数一览表出口总压(Pa) 出口流量(kg/s) 转矩(N·m) 轴功率(W) 效率原始模型2014 5.294 122.7 38033.4 22.9% 改进模型A 2515.9 6.193 134.3 41600 30.5% 改进模型B 2951.5 5.746 117.9 36539 37. 9% 改进模型C 3368.8 6.141 118.1 3660746.1% 通过上述通风机结构的改变,多方案比较,改型后的叶轮气动性能改善。
叶轮出口和蜗壳出口没有逆流,出口流量均匀。
出风量和风压有所提高,效率提高,轴功率基本小于或等于原模型的轴功率。
与原模型相比,通风机的出口流量增加16%,出口总压增加67.3%,轴功率下降3.8%,效率增加23.2%。
4 基于OPTIMUS与FLUENT 的离心通风机进口优化在数值化的今天,新产品的开发周期越来越短,产品的成本需要大幅降低,而产品的外延性以及拓展空间又需要极大的扩展,这就需要广泛地采用优化技术进行产品设计。
通过数值模拟通常能够得到一些比较满意的设计方案,但远远不是最佳方案。
CFD已完全具备求解用户设定的一个确定问题的能力,但是工业界对优化设计有越来越强的需求。
目前设计—分析—修改设计—分析的过程仍然是不连续的、孤立的、人工干预的,而非自动的。
虽然分析人2005 Fluent 中国用户大会论文集92 员可以不厌其烦地在屏幕前一次次修改设计参数以寻找最理想方案,但缩短开发周期的压力通常要求分秒必争,人们可能没有更多的时间对数据参数进行手工调整。
最优化技术引入使人们从繁重的凑试工作中解脱出来,同时使设计水平也达到一个新的高度。
多学科多目标优化软件Optimus,具有强大的集成优化能力,可以集成多种CAE/CAD软件。
它可以自动调度通用的流体分析、结构分析软件并由用户设置其它约束条件来完成一个特定优化问题的自动求解过程,使人工的干预降低到最低限度。
这样得到的优化结果是符合目标函数的最佳设计。
根据目标进行设计的理念,彻底颠覆了传统的工程设计过程,从所希望的目标开始,然后定义达到目标所需的设计参数。
本文运用多学科优化平台软件OPTIMUS集成流体计算软件FLUENT6.1和GAMBIT2.1对通风机进口进行优化计算,优化设计建立在仿真分析的基础上。
一个典型的优化过程通常需要经过以下的步骤来完成:(1)参数化建模,利用Fluent软件的参数化建模功能把将要参与优化的数据(设计变量)定义为模型参数,为以后软件修正模型提供可能。
(2) 求解,对参数化模型流场进行数值仿真,把状态参数(约束条件)和目标函数(优化目标)提取出来供优化处理器进行优化参数评价。
(3)优化参数评价,优化处理器根据本次循环提供的优化参数(设计变量、目标函数)与上次循环提供的优化参数作比较之后确定该次循环目标函数是否达到了最小,或者是否达到最优,如果最优,完成迭代,推出优化循环圈,否则,进行下步。
根据已完成的优化循环和当前优化变量的状态修正设计变量,重新投入循环。
通过设计实验方法(DOE)对响应空间作初步的探索,然后对其进行优化计算。
DOE是一种设计空间探索技术,用来对设计空间进行初步探索,可以减小优化问题的计算规模,本例通过对DOE 结果分析,可以看出,只有减小截面尺寸的分析是有效的,因此把变量的变化范围缩小,提高计算效率,减少计算时间。
OPTIMUS中提供了局部优化算法如梯度算法、序列二次规划算法,全局搜索算法如自适应遗传算法、模拟退火法等[4] 。
本例采用了序列二次规划算法,在设定的空间内进行了7次迭代,图7为离心风机的效率随迭代次数变化。
横坐标为迭代次数,纵坐标为风机效率。
图7 优化迭代效率曲线通过对通风机入口优化,在对原通风机模型改动很小的情况下,可以有效提高通风机的性能,出口总压、流量等指标都有很大的提高,效率提高11.41%图8中的左边圆锥形进口为原模型的进口,右边为优化计算得到的进口形状。
通过优化,可以有效改善入口流场的流动,减少不必要的能量损失,明显提高通风机的性能。
优化结果形状与本文3.2.3提供的数值仿真优化模型进口形状基本一致。
人工重复每一个中间态的设计分析工作最终求得一个优化解的过程是漫长和昂贵的,采用OPTIMUS可以提高效率,节省时间,尽快得到问题的最优解。
2005 Fluent 中国用户大会论文集93 图8 优化前后进口形状5总结根据上述对离心通风机内部三维粘性流场进行数值模拟及其改进设计,可以得出如下结论: 1 通过对原离心通风机内部三维粘性流场进行数值模拟,认为该风机气动流场性能比较差,效率只有22.2%.。
主要原因是: (1)叶轮叶片进口缺乏导流部分,所以造成叶片前半部分压强低,产生逆流。
由于叶轮出口有较多逆流,从而导致蜗壳入口流动有逆流,进入蜗壳的气流速度不均匀,恶化了气流在蜗壳内的流动。
(2)原模型叶轮采用前向叶片,叶轮的前盘采用平前盘。