作业计划与排序
机械制造行业中的流水作业排序问题-文档资料
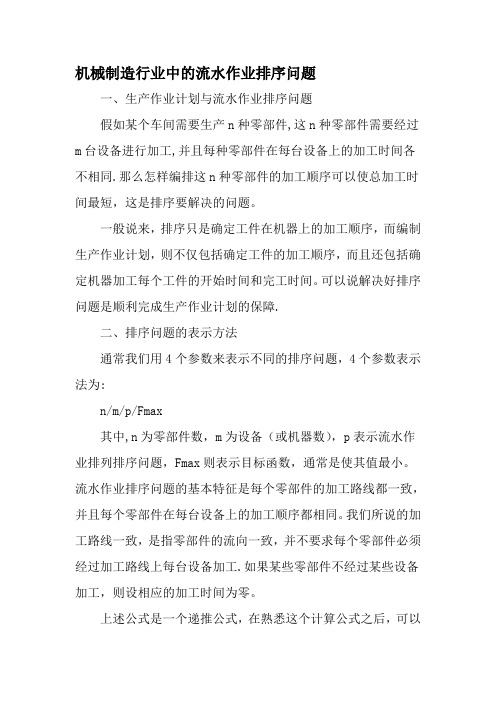
机械制造行业中的流水作业排序问题一、生产作业计划与流水作业排序问题假如某个车间需要生产n种零部件,这n种零部件需要经过m台设备进行加工,并且每种零部件在每台设备上的加工时间各不相同.那么怎样编排这n种零部件的加工顺序可以使总加工时间最短,这是排序要解决的问题。
一般说来,排序只是确定工件在机器上的加工顺序,而编制生产作业计划,则不仅包括确定工件的加工顺序,而且还包括确定机器加工每个工件的开始时间和完工时间。
可以说解决好排序问题是顺利完成生产作业计划的保障.二、排序问题的表示方法通常我们用4个参数来表示不同的排序问题,4个参数表示法为:n/m/p/Fmax其中,n为零部件数,m为设备(或机器数),p表示流水作业排列排序问题,Fmax则表示目标函数,通常是使其值最小。
流水作业排序问题的基本特征是每个零部件的加工路线都一致,并且每个零部件在每台设备上的加工顺序都相同。
我们所说的加工路线一致,是指零部件的流向一致,并不要求每个零部件必须经过加工路线上每台设备加工.如果某些零部件不经过某些设备加工,则设相应的加工时间为零。
上述公式是一个递推公式,在熟悉这个计算公式之后,可以直接在矩阵上计算完工时间。
某车间生产的产品符合4/3/p/Fmax问题,其加工时间如下表所示:如果车间按照S=(1,2,3,4)的顺序组织生产,按照上述公式递推,将每个零部件的完工时间标在其加工时间的右上角。
对于第一行第一列,只需要把加工时间的数值作为完工时间标在加工时间的右上角。
对于第一行的其它元素,只需从左到右依次将前一列右上角的数字加上本列的加工时间,将结果填在计算列加工时间的右上角.对于第二行到第m行,第一列的算法相同.只要把上一行右上角的数字和本行的时间相加,将结果填在本行加工时间的右上角;从第2列到第n列,则要从本行前一列右上角和本列上一行右上角数字中取大者,再和本列加工时间相加,将结果填在本列加工时间的右上角。
这样最后一行的最后一列右上角的数字即为Fmax。
生产运作管理教学课件ppt-编制作业计划与作业排序
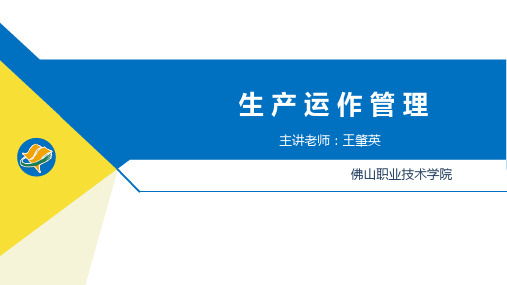
【导入案例解析】
首先,应用在制品定额法确定各个生产车间投入量和出产量 (1)装配1台空调配1件机箱,则装配2万台空调需要机箱数量 Qoj=20000×1 =20000(件); (2)装配车间的机箱的投入量
(件); (3)保证空调整机装配车间需要,机箱车间机箱的出产数量
(件); (4)加工车间机箱的投入数量
60
420
铸造过程
4
40
440
图3-2 连续流水线工作指示图表
生产运作管理
三、大量流水生产作业的期量标准
(2)间断流水线同期化程度不高,需要分工序规定每个工作地的工作时间顺序,确定标准计 划时间,计算工作地看管周期产量。间断流水生产的计划编制方法如下:
第一,确定看管周期。间断流水线中每道工序的节拍与流水线节拍可能不相等,为了使间断流 水生产线有节奏地工作,预先设定一个时间段,使每道工序在该时间段内生产相同数量的产品,在 这个预先设定的时间段内平衡各道工序的生产率达到一致,这个时间段称为看管周期。一般取一个 班、二分之一个班或四分之一个班的时间为看管周期。
生产运作管理
【案例分析】
编制大量生产作业计划考虑的问题及方法。 (1)产品品种单一连续生产,属于流水作业生产; (2)保证生产连续、均衡、稳定,必须规定合理的期量标准; (3)根据需求、期量标准计算出计划期的投入与产出; (4)根据大量流水作业生产连续、均衡、稳定的特点,将投入与产出量按日均匀地分配在计 划期内。
生产运作管理
四、大量流水生产作业计划的编制
式中:Qoi——i车间的产出量 Qij——j车间的投入量 Qsi——i车间外销半成品量 ZI——车间之间库存在制品定额 Z’I——期初预计库存量 QIi——i车间的投入量 Qwi——i车间的废品量 Ze——i车间内部在制品定额 Z’e——i车间内部期初在制品占用量
作业排序与生产作业计划

17.10.2024
6
第一节 作业排序的基本概念
二、假设条件与符号说明
为了便于采用数学模型来分析研究排序问题,做下列假设:
1. 一个工件不能同时在几台不同的机器上被加工。 2. 采取平行移动方式移送被加工的工件。 3. 不允许中断。当一个工件一旦开始加工,必须一直进行到完
工,不得中途停止插入其它工件。 4. 工件在每道工序的加工只在一台机器上进行。 5. 工件数(或批量)、机器数已知,单件加工时间已知, 完
第一节 作业排序的基本概念
一、编制生产作业计划与排序的关系
编制生产作业计划与作业排序不同,排序只是确 定工件在机器上的加工顺序,可以用一组工件的代 号的排列来表示这组工件的加工顺序,而编制生产 作业计划不仅包括确定工件的加工顺序,而且包括 确定机器加工每个工件的开始时间和完成时间。所 以,只有生产作业计划才能指导工人的生产活动。
显然,当ri = 0 时, Fmax = Cm(sn)
在知道了上述计算Fmax 公式后,便可直接在工件加工的 时间矩阵上从左向右计算完工时间。
第二节 流水作业排序问题
例11.1有一个6/4/p/Fmax问题,其加工时间如下表所示。 当按顺序S=(6,1,5,2,4,3)加工时,求Fmax
表11-1 加工时间矩阵
i
1
2
3
4
5
6
Pi1
4
2
3
1
4
2
Pi2
4
5
6
7
4
5
Pi3
5
8
7
5
5
5
Pi4
4
2
4
3
3
1
表11-2 顺序S下的加工时间矩阵
生产与运作管理生产作业计划与排序概述

(一)期量标准概念
为制造对象(产品、部件、零件)在生产过程中的 运动所规定的生产期限(时间)和生产数量的标准。
生产类型 大量生产
不同生产类型的期量标准 期量标准
节拍、流水线工作指示图表、在制品定额
成批生产 单件小批
批量、生产间隔期、生产周期、在制品定额、 提前期
生产周期、提前期
1. 生产周期(T)
检查和控制生产任务计划进度完成情况
生产作业计划的主要决策问题
• 确定批量的大小 • 确定适当的生产顺序 • 安排合理的生产进度日程
• 批量
(1)概念:
批量: 消耗一次准备结束时间所生产的同种产品或
零件的数量,以n记之(即相同产品或零件一次投
入和出产的数量)
生产间隔期: 相邻两批相同产品(零件)投入(或
周转半 前车间期初第 前车间
前车间
成品占 =( 一次出产零件 ÷ 交库间 )× 入库批
用量
入库标准日期 隔日数
量
= (3/5)×50 = 30 (件)
前车间成批入库,后车间整批领用
● 图表
工作日 1 2 3 4 5 6 7 8 910111213141516171819202122232425 1 2 3
解:
工作日 1 2 3 4 5 6 7 8 9 10111213141516171819202122232425 1 2 3
流
最
动 占
大用
占量
用
量
保险储备量
后领 前入
周转半
成品占 =
用量
前车 间批 量
-[
前车间计划最 后车间
后一批零件入 库的标准日期
÷
生产间 隔期
]
生产作业计划与作业排序概论

生产作业计划与作业排序概论生产作业计划和作业排序是生产管理中非常重要的环节,通过合理的计划和排序,可以提高生产效率,降低生产成本,保证产品质量,确保生产进度的顺利进行。
在现代化的生产管理中,生产作业计划和作业排序已经成为不可或缺的一部分。
本文将介绍生产作业计划和作业排序的概念、意义和方法。
生产作业计划的概念和意义生产作业计划是根据生产需求和资源情况,合理安排生产活动的时间、顺序、数量和方法的过程。
通过制定生产计划,可以有效地安排生产活动,使生产过程有序、高效。
生产作业计划的主要目的是保证生产进度的准时、产品质量的稳定和生产成本的最低化。
生产作业计划的意义在于:1.提高生产效率:通过合理的计划,可以提高生产效率,减少空转时间和不必要的等待时间,充分利用生产资源。
2.降低生产成本:通过合理的计划,可以避免资源浪费和重复投入,降低生产成本,提高企业的竞争力。
3.保证产品质量:通过合理的计划,可以确保生产过程中每个环节都按照要求进行,从而保证产品质量稳定。
4.确保生产进度:通过合理的计划,可以提前安排生产活动,确保生产进度的顺利进行,避免延误和返工。
生产作业排序的概念和意义生产作业排序是根据生产作业的性质、优先级和资源限制等因素,合理安排生产作业的顺序和时间的过程。
通过作业排序,可以使生产作业有序、高效地进行,保证生产计划的顺利执行。
生产作业排序的主要目的是提高生产效率、缩短生产周期、降低生产成本。
生产作业排序的意义在于:1.提高生产效率:通过合理的排序,可以减少作业之间的等待时间和传送时间,提高生产效率。
2.缩短生产周期:通过合理的排序,可以优化生产流程,减少生产周期,提高产品的市场竞争力。
3.降低生产成本:通过合理的排序,可以减少不必要的资源浪费和生产停顿,降低生产成本。
4.提高生产计划执行的准确性:通过合理的排序,可以保证生产计划的准时、准确执行,确保产品的交付周期。
生产作业计划和作业排序的方法生产作业计划和作业排序的方法有很多种,根据不同的生产环境和要求,可以采用不同的方法。
生产过程中的物料控制
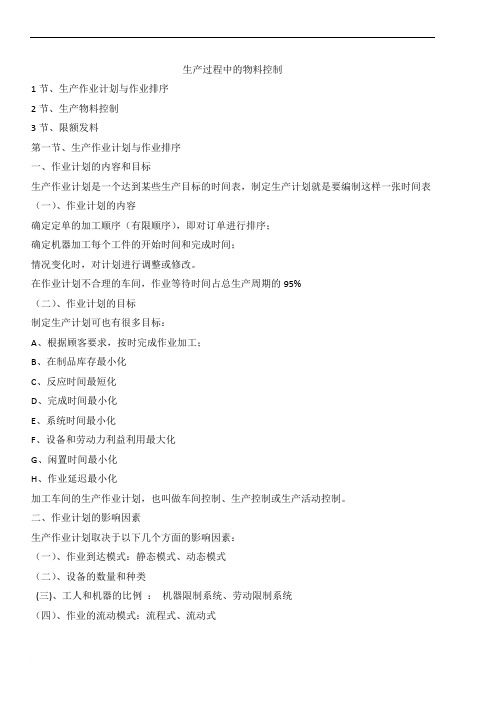
生产过程中的物料控制1节、生产作业计划与作业排序2节、生产物料控制3节、限额发料第一节、生产作业计划与作业排序一、作业计划的内容和目标生产作业计划是一个达到某些生产目标的时间表,制定生产计划就是要编制这样一张时间表(一)、作业计划的内容确定定单的加工顺序(有限顺序),即对订单进行排序;确定机器加工每个工件的开始时间和完成时间;情况变化时,对计划进行调整或修改。
在作业计划不合理的车间,作业等待时间占总生产周期的95%(二)、作业计划的目标制定生产计划可也有很多目标:A、根据顾客要求,按时完成作业加工;B、在制品库存最小化C、反应时间最短化D、完成时间最小化E、系统时间最小化F、设备和劳动力利益利用最大化G、闲置时间最小化H、作业延迟最小化加工车间的生产作业计划,也叫做车间控制、生产控制或生产活动控制。
二、作业计划的影响因素生产作业计划取决于以下几个方面的影响因素:(一)、作业到达模式:静态模式、动态模式(二)、设备的数量和种类(三)、工人和机器的比例:机器限制系统、劳动限制系统(四)、作业的流动模式:流程式、流动式(五)、分配作业的优先规则三、生产控制部门的责任(一)、安排负荷(二)、排序:排序的详细情况可以通过计算机终端发送列表,或者打印出来,或这通过在中央区域张贴工作列表的方式传达给工人(三)、控制:需要随时掌握每项作业的进度情况,直到作业完成。
四、作业排序规则及评估准则(一)、排序规则工件等待:工件的某道工序完成后,下道工序的机器正在加工其他工件,则是要等待一段时间才能开始加工,称为工件等待机器闲置:机器已完成对某个工件的加工,下一个加工工件还未到,称为机器空闲。
良好的排序就是要使工件等待和机器空闲最小化,最常见的排序规则如下:1、先到先服务(FCFS)2、最短加工时间(SPT),这一排序规则的结果是平均流程时间最短,在制品库存减少3、最早交货日期(EDD)4、关键率(CR)关键率,在这一规则下,加工的下一项作业是在所有等待加工的作业中关键率最低的作业,即优先选择临界比最小的工作。
生产管理课件 11作业排序
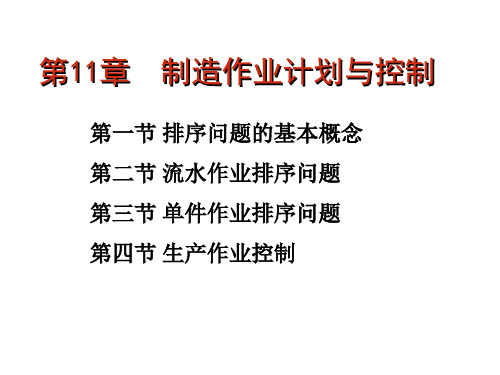
加工周期为46
课堂作业:求Fmax.
表3顺序S下的加工时间矩阵
i P i1 P i2 P i3 P i4
1 2 3 4 56
3
3
3 6 4 10 212 113 316
25 511 415 318 725 631
510 415 520 727 532 436
111 217 323 229 335 137
2、关键工件法
(1)计算每个工件的总加工时间,找出加工时间最长 的工件C,将其作为关键工件;
(2)对于余下的工件若Pi1≤Pim,则按Pi1不减的顺序排 成一个序列Sa,若Pi1>Pim,则按Pim不增的顺序排列成 一个序列Sb。 (3)顺序( Sa,C,Sb)即为所求顺序。
关键工件法求近优解举例
参数表示法:
n /m /P / Fmax所有零件在每台机器上的 加工顺序相同。如在M1上都是第一道工 序,M2上都是第二道工序。
n /m /F / Fmax不同零件在每台机器上的 加工顺序不同。如零件1在M1上不加工, 在M2上才是第一道工序;而零件2在M1上 是第一道工序。
第二节 流水作业排序问题
Johnson法则只是一个充分条件,不是必 要条件。不符合这个法则的加工顺序, 也可能是最优顺序。如对例11-2顺序(2 ,5,6,4,1,3)不符合Johnson法则, 但它也是一个最优顺序
对于3台机器的流水车间排序问题,只有 几种特殊类型的问题找到了有效算法。
对于一般的流水车间排列排序问题,可 以用分支定界法。
③ 若所有零件都已排序,停止。否则, 转步骤①。
例题:求表11-3所示的6/2/F/Fmax问题的最优解。
表11-3加工时间矩阵
05-3 作业计划(排序)-生产计划与控制
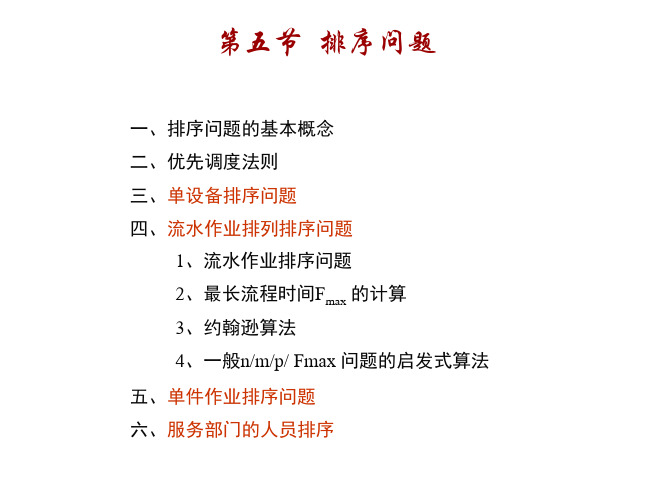
J3 8 2
1 2
8
26 J3
J4
M2 3
J5J4 22
J3 26 28
5
10
15
20
25
30 时间
2、最长流程时间Fmax 的计算
◆ 最长流程时间(加工周期) 从第一个工件在第一台机器开始加工时算起,到最后一个 工件在最后一台机器上完成加工时为止所经过的时间 ◆ 假设所有工件的到达时间都为零 ri= 0, i= 1, 2, ……n Fmax等于排在末位加工的工件在车间的停留时间,也等于 一批工件的最大完工时间Cmax ◆ 设n 个工件的加工顺序为 S= ( S1, S2,……Sn) Si为排第i 位加工的工件的代号
1、名词术语 2、假设条件 3、符号说明 4、排序问题的分类和表示方法 5、排序问题的评价标准(目标函数)
1、名词术语
(1)排序(Sequencing) :确定工件在机器上的加工顺序。 (2)编制作业计划(Scheduling) 确定工件的加工顺序,并确定机器加 工每个工件的开始时间和完成时间 (3)调度(控制)(Controlling) 对生产过程实施控制所采取的行动 •派工(Dispatching)——按作业计划的要求,将具体生产任务安 排到具体的机床上加工 •赶工(Expediting)——在实际进度落后于计划进度时采取的行动 排序的各个名词来自加工制造业,(机器、工件、工序、加工 时间),但此时它们的含义已经扩大了。如机器可以是人、计算机等 服务者。
5、排序问题的评价标准(目标函数)
(1)以按时交货作为目标函数 平均延迟时间 L 平均延误时间 T 最大延误时间Tmax 延误的工件数n (2)以工件的完工时间和工件的流程时间为目标函数 最大完工时间Cmax 最长流程时间Fmax 平均完工时间 C 平均流程时间 F (3)其他目标函数 在制品占用量最小 总调整时间最小 延期罚款最小 生产费用最小 总利润最大 设备利用率最大
- 1、下载文档前请自行甄别文档内容的完整性,平台不提供额外的编辑、内容补充、找答案等附加服务。
- 2、"仅部分预览"的文档,不可在线预览部分如存在完整性等问题,可反馈申请退款(可完整预览的文档不适用该条件!)。
- 3、如文档侵犯您的权益,请联系客服反馈,我们会尽快为您处理(人工客服工作时间:9:00-18:30)。
Operations Scheduling and Sequencing
本章的主要内容
• 作业计划 (Scheduling) • 排序 (Sequencing) • 车间生产控制 ( Shop-Floor Control )
生产管理的计划与控制系统构成
资源计划 Resource Planning 综合生产计划 Production Planning 主生产计划 Master Production Scheduling
三、
排序常用的符号 Ji----工件i,i=1,2,....n di----工件i的交货期 m pij , p ----工件i在机器j Pi----工件i的加工时间, Pi ij j 1 上的加工时间,j=1,…,m
m
Wi----工件i在系统内的等待时间,Wi wij , wij----工件i在 j 1 机器j前的等待时间, j=1,…,m
J3
31 31
J4
1 33
J5
2 32
解:根据SPT原则,得出:
J4 -J5 -J1 -J2 -J3
有关项目的计算:
加工时间 J4 J5
J1 J2 J3 1 2 11 29 31
_
开始时间
0 1 3 14 43
完成时间
1 3 14 43 74
交货期
33 32 61 45 31
延迟
0 0 0 0 43
2 求平均流程时间最短的排序问题
求平均流程时间最短的作业顺序,采用SPT原则。 按工件加工时间的长短,从小到大安排作业。 例:一台加工中心,现有5个工件需要该机器加工。相 关的加工时间和要求完成时间(交货期)如下表所示, 求平均流程时间最短的作业顺序。
J1
加工时间 交货期 11 61
J2
29 45
Ti=max{0, Li}
L i = Ci - d i Li<=0 Li>0
,
工件i的延误时间 按期或完成提前; 延误
目标函数
min Tmax
根据排序目标的不同,可以选择不同的排序规 则,又称为确定零件加工的优先权。
常见的排序规则: SPT---Shortest Process Time, 优先选择加工时间最短的工件 EDD---Earliest Due Date 优先选择交货期紧的工件 FCFS---First Come First Served 按工件到达的先后顺序 CR---Critical Rate 优先选择临界比最小的工件 CR=(交货期-当前日期)/剩余加工时间
[例7-1]:某企业生产1万台130汽车,其中部分零件需要自己生产,每辆汽车需要自 产齿轮 4个、轴 1个。企业的 3个生产车间和 2个在制品库用于生产这两种零件, 排定3个车间的作业计划。按工艺顺序反工序计算
产 产 零 零 每 品 品 件 件 辆 l 2 3 4 5 6 7 8 9 10 11 12 13 14 15 16 17 18 19 20 2l 名 称 A1—001 轴 1 10000 --1000 600 10400 --800 1000 10200 100 1800 600 1l500 500 2000 3000 11000 800 400 300 1l900 130 汽车 10000 台 A1—012 齿 轮 4 40000 --5000 3500 41500 2000 6000 7100 42400 1400 4500 3400 44900 6100 10000 10000 51000 --2500 1500 52000 产 量 编 号 名 称 件 数 出产量 . 废品及损耗 在制品定额 期初预计在制品结存量 投入量(1+2+3-4) 半成品外售量 库存半成品定额 期初预计结存量 出产量(5+6+7-8) 废品及损耗 在制品定额 期初预计在制品结存量 投入量(9+10+11-12) 半成品外售量 库存半成品定额 期初预计结存量 出产量(13+14+15-16) 废品及损耗 在制品定额 期初预计在制品结存量 投入量(17+18+19-20)
一、在制品定额法 • 在制品定额法,是一种利用预先制订的在制品定额, 来协调和规定各车间投入量和出产量的方法。 • 这种方法适用于大批量生产企业。
毛坯库 投入 产出 投入
零件库 产出 投入 产出
毛坯车间
车削车间
磨削车间
计算公式如下: 车削车间的出产量=磨削车间的投入量+零件库半成品外 售量+(零件库半成品定额-期初库存半成品预计结存 量) 车削车间的投入量=车削车间的产量+车削车间计划废品 量+(车削车间内在制品定额-车削车间期初在制品预 计结存量)
四、单台机器排序问题 (n/1/ /B)
n个工件全部经由一台机器处理
1、 常见单台机器排序问题的目标函数 1) 平均流程时间最短 n _ 1 定义: F F 为n个零件经由一台机器的平均流程时间。
n
i 1
i
Fi= Pi+ Wi
目标函数:使平均流程时间最短
2)最大延期量最小
定义: Tmax maxTi 为最大延期量。
计 划 投入 计 划 产出 实 际 出产 累 计 出产
460 408
02-034 齿轮
11872
12572
计 划 投入 计 划 产出 实 际 出产 累 计 出产
1796 1696
1796 1696
1796 1696
1796 1696
… …
… …
… …Biblioteka 其它…………
计 划 投入 计 划 产出 实 际 出产 累 计 出产
二、 排序问题的分类 • 根据机器数的多少 单台机器的排序问题 :多个工件在一台机器上加工 多台机器的排序问题 :多个工件在多台机器上加工 • 根据加工路线的特征(多台机器的排序问题) 单件车间排序 :工件加工路线不同(Job Shop) 流水型排序 : 工件加工路线相同 (Flow Shop) • 根据工件到达系统的情况 静态排序 :排序时工件已全部到达 动态排序 :排序时工件陆续到达 • 根据参数的性质 确定型排序 :加工时间等参数已知 随机型排序 • 根据要实现的目标 单目标排序 :平均流程时间最短或误期工件最少等 多目标排序
作业题
J1 J2 J3 J4 J5
加工时间
交货期
15
21
9
35
11
31
5
17
6
25
分别用EDD规则、SPT规则和CR规则排序,并求出 最大延期量和平均流程时间。
五、 n项任务在两台机器的排序问题
1、两台机器排序问题的含义(n/2/F/Fmax) n个工件都必须经过机器1和机器2的加工,即工艺路线是一致的。
3、计算各车间的计划出产量和投入量 计算公式为: 车间A出产量= 期末车间A出产累计编号-期初车间A出产累计编号 车间A投入量= 期末车间A投入累计编号-期初车间A投入累计编号
第三节
排序的基本概念
一、 排序与编制作业计划的区别 • 排序---确定零部件在一台或一组设备上加工的先后顺序的工作。 • 作业计划---安排零部件的出产数量和投入时间及出产时间。
2、两台机器排序问题的目标
• 两台机器排序的目标是使生产周期Fmax最短。 Fmax 的含义见如下图。
注:(1)按每周7个工作日安排。 (2)本例按日平均投入和出产。
第二节 作业计划的编制方法
• 主生产计划以及物料需求计划中,对产品品种、数量 和交库日期做出了安排,车间生产作业计划是将上述 安排落实到各生产工序(生产地点),同时要考虑生 产过程中的成材率、废品率等影响因素,这些因素在 主生产计划以及物料需求计划中被忽略了。 • 常用的编制车间生产作业计划的方法有三种: 大量生产类型的作业计划 (在制品定额法) 成批生产类型的作业计划 (提前期法----累计编号 法) 单件小批生产类型作业计划 (生产周期法)
加工车间某周车间作业计划--- Job Floor scheduling
零件件 号及名 称 计划出 产 量 (件) 计划投 入 量 (件)
项目
日 历 进 度 (天) 1 2 460 408 3 460 408 4 460 408 …5 … … 6 … … … 7 … … …
01051 轴
2856
3220
Ci----工件i的完成时间, Ci= Pi+ Wi Fi----工件i的流程时间,Fi= Pi+ Wi Li----工件i的延误时间, Li= Ci- di , Li<=0 按期或完成提前; Li>0 延误 Ti----工件i的延期量, Ti=max{0, Li} Ei----工件i提前完成的时间,Li<=0 ,| Li|
[例7-1],齿轮的工艺顺序为毛坯车间---车削车间----磨削车间。 设磨削工序的出产提前期为零(MRP计划入库日期),生产周期 为1天,车削工序和毛坯工序的生产周期分别为 1.5和2天,保险 期均为0.5天,则按反工艺顺序,从计算磨削工序的投入提前期 开始,计算各工序的出产和投入提前期: 磨削工序的投入提前期=0+磨削工序的生产周期=1 车削工序的出产提前期=1+0.5=1.5 车削工序的投入提前期=1.5+1.5=3 毛坯工序的出产提前期=3+0.5=3.5 毛坯工序的投入提前期=3.5+2=5.5
Bill of Material
需求预测
需求市场
物料需求计划 MRP
Inventory status data
能力需求计划
车间生产系统 Shop-floor systems
供应商系统 Vender Systems
采购市场
第一节 作业计划的目的和要求