pdc钻头分析
PDC钻头稳定性分析
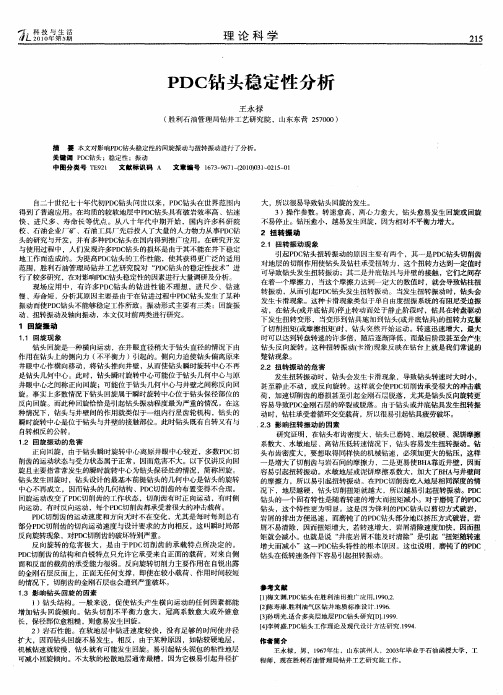
【1 2陈寿康 . 利油气 区钻井 地质标 准 没计.96 胜 19 . 【] 明光 . 合多夹层 地层 P C 3 孙 适 D 钻头 研究[】 99 D. 9 . 1 【1 4李树盛 .D 钻头 工作理论 及现代 设计方 法研究 . 9. P C 1 4 9
作者 简 介
王永 禄 ,男 ,16 年生 ,山东滨 州人 ,2 0 年毕业 于石 油函授大 学 ,工 97 03
13 影 响钻 头 回 旋 的 因 素 . 1 )钻头结构 。一般来说 ,促 使钻头产生横 向运动 的任 何因素都能
研究证明 , 在钻头布齿密度大 、 钻头 已磨钝 、 地层较硬、泥饼摩擦 系数大 、水敏地层 、高钻压低转速情况下 , 钻头容易发生扭转振动。钻 头布齿密度大 ,要想取得 同样快的机械钻速 ,必须加更 大的钻压 ,这样 是增大 了切削齿与岩石 间的摩擦力 ,二是更易使B A靠近井壁 ,因而 H 容易引起扭转振动。水敏地层或泥饼摩擦 系数大 ,加大 了B- 与井壁问 IA I 的摩擦力 ,所以易引起扭转振动。在P C D 切削齿 吃人地层相同深度的情 况下 ,地层越硬 ,钻头切削扭矩 就越大 ,所 以越易引起扭转振 动。P DC 钻头 的一个 固有特性是随着转速的增大而扭矩减小。对于磨钝 了的P DC 钻头 ,这个特性更为明显 。这是 因为锋利 的P C D 钻头以剪切方式破岩 , 岩屑 的排 出方便迅速 ,而磨 钝了的P C D 钻头部分地 以挤压方式破岩,岩 屑不易清除 ,因而扭矩增大 ,若转速增大 ,岩屑清除速度加快 ,因而扭 矩就会减小。也就是说 “ 井底岩屑不能及 时清除”是引起 “ 扭矩随转速 增大而减小 ”这一P c D 钻头特性 的根本 原因。这也说 明 , 磨钝 了的P C D 钻头在低转速条件下容易引起扭转振动。
pdc钻头

PDC钻头1. 简介PDC钻头是一种常用于石油钻井的钻探工具。
PDC钻头由多个聚晶体金刚石(Polycrystalline Diamond Compact)切削元件组成,被广泛应用于地层钻探、岩石切割和石油开采中。
本文将介绍PDC钻头的结构、原理以及应用领域。
2. 结构PDC钻头主要由刀翼、钻头体和连接部分组成。
2.1 刀翼刀翼是PDC钻头的重要组成部分,通常由金刚石切削元件制成。
刀翼的数量、形状和布局对钻头的钻井性能和钻孔质量起着重要作用。
刀翼一般采用均匀分布的方式,以保证钻头在钻井过程中的均匀磨损。
2.2 钻头体钻头体是连接刀翼和连接部分的主要结构,通常由钢铁材料制成。
钻头体的设计需要考虑到钻井环境、井眼尺寸和钻头的稳定性等因素。
钻头体一般具有良好的强度和刚度,以确保钻头在高强度的钻井过程中不会发生变形或破损。
2.3 连接部分连接部分是将钻头与钻杆连接在一起的部分,通常采用标准的API连接方式。
连接部分需要具有良好的密封性和承载能力,以确保钻头和钻杆之间的传递力矩和转速。
3. 原理PDC钻头通过刀翼上的金刚石切削元件对地层进行切削和磨损,从而实现钻井的目的。
PDC钻头利用金刚石的高硬度和强大的切削能力,能够在岩石中快速切削并形成孔道。
PDC钻头的切削原理主要有两种:剪切和破碎。
3.1 剪切剪切是PDC钻头常用的切削方式之一。
当PDC钻头旋转时,刀翼上的金刚石切削元件与地层接触,通过相对运动切削地层。
金刚石的高硬度和切削元件的锋利边缘使得PDC钻头能够在地层中形成清晰而平滑的孔道。
3.2 破碎破碎是PDC钻头另一种常用的切削方式。
当地层硬度较高时,剪切切削效果可能不佳。
此时,PDC钻头通过施加较大的冲击力将地层破碎,进而形成孔道。
4. 应用领域PDC钻头广泛应用于石油、天然气和水井钻探领域。
其高效的切削能力和稳定的性能使其成为钻井操作中的重要工具。
4.1 石油钻井在石油钻井中,PDC钻头常用于垂直井、水平井和定向井的钻铤作业。
PDC钻头钻井泥包原因及控制对策

PDC钻头钻井泥包原因及控制对策摘要:为了解决PDC钻肉钻井过程中产生泥包的问题,保障钻井作业的顺利进行,本文首先对PDC钻头钻井泥包产生的原因进行了分析,从作业流程到钻头材料,逐一进行了探讨,并提出了相应的控制措施。
关键词:PDC钻头;钻井泥包;控制措施引言:近年来,我国对能源的需求越来越高,页岩油气等非常规油气资源的开发陆续被提上日程,PDC钻头经过长时间的发展,现在已经成为钻井行业提速增效的重要工具,而因为开采环境的原因,经常会出现钻头泥包,大大降低了开采效率,所以对PDC钻头钻井泥包的产生原因及控制处理显得十分重要。
一、PDC钻头钻井泥包原因分析(一)钻井液性能原因在开展钻井作业过程中,钻头是其中的重要组成部分,还有一种物质也是十分重要的,那就是钻井液,它可以在岩层和钻头之间起到润滑的作用,还可以将多余的废屑带出地面,因为钻井液的类型不同,其中含有的成分也不同,润滑性及密度差异较大,密度较大的钻井液失水性很严重,各种杂质会很容易粘附在钻井壁上,形成泥包,随着钻井作业进行,就会依附到钻头上形成钻头泥包,润滑性过低也会导致大量泥岩颗粒吸附到钻头上,这是引发钻头钻井泥包的主要原因。
(二)钻井工程技术问题钻井作业过程的技术问题也不容小觑,为了提高工作效率,钻头的转速会越来越快,过快的钻头转速虽然加快了作业进程,但是大量碎屑无法及时排出,排出量跟不上作业量,钻头压力是影响钻头速度的重要因素,最佳条件下,钻速和钻压是成正比的,但是由于地质因素,有的岩层过软,而钻压过大、没有匀速送钻等操作会造成钻速过快或过慢,都会使钻头与地层接触过多而产生钻头泥包。
操作不当也会导致钻井液吸附废料能力下降,大量的碎屑会滞留在井壁处,形成泥堆,久而久之就会形成泥包,当钻头触及比较松软的土层时,泥包受到挤压,就会沾到井壁上去。
还有在下钻作业时,没有下入套管,钻头刮蹭到井壁上的泥包,也会形成钻头泥包。
(三)钻头类型及尺寸不合理在开展钻井作业时,也需要慎重选择钻头类型及尺寸,不同钻头的种类其结构是不同的,首先PDC钻头的结构会影响水力对其清洗的效果,比如散步式布齿和浅锥轮廓的钻头,水力冲洗的效果不明显,切削齿侧倾角较小的钻头,不易于碎屑的排出,钻头水眼的位置如果与喷射角度对不上,会在井底处形成钻井液涡流,使得钻头的刀片和切削齿得不到清洗,碎屑堆积就会产生泥包现象,钻头喷嘴太小,排量不够,废屑没有及时排出也会造成堆积。
pdc钻头分析
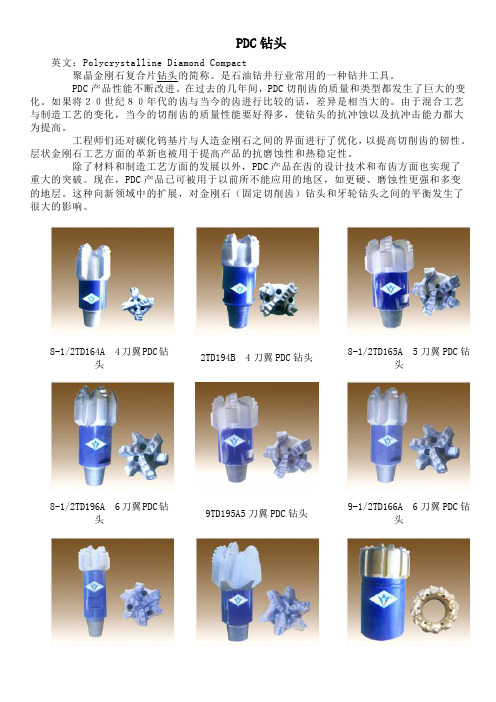
PDC钻头英文:Polycrystalline Diamond Compact聚晶金刚石复合片钻头的简称。
是石油钻井行业常用的一种钻井工具。
PDC产品性能不断改进。
在过去的几年间,PDC切削齿的质量和类型都发生了巨大的变化。
如果将20世纪80年代的齿与当今的齿进行比较的话,差异是相当大的。
由于混合工艺与制造工艺的变化,当今的切削齿的质量性能要好得多,使钻头的抗冲蚀以及抗冲击能力都大为提高。
工程师们还对碳化钨基片与人造金刚石之间的界面进行了优化,以提高切削齿的韧性。
层状金刚石工艺方面的革新也被用于提高产品的抗磨蚀性和热稳定性。
除了材料和制造工艺方面的发展以外,PDC产品在齿的设计技术和布齿方面也实现了重大的突破。
现在,PDC产品已可被用于以前所不能应用的地区,如更硬、磨蚀性更强和多变的地层。
这种向新领域中的扩展,对金刚石(固定切削齿)钻头和牙轮钻头之间的平衡发生了很大的影响。
8-1/2TD164A 4刀翼PDC钻头2TD194B 4刀翼PDC钻头8-1/2TD165A 5刀翼PDC钻头8-1/2TD196A 6刀翼PDC钻头9TD195A5刀翼PDC钻头9-1/2TD166A 6刀翼PDC钻头最初,PDC 钻头只能被用于软页岩地层中,原因是硬的夹层会损坏钻头。
但由于新技术的出现以及结构的变化,目前PDC 钻头已能够用于钻硬夹层和长段的硬岩地层了。
PDC 钻头正越来越多地为人们所选用,特别是随着PDC 齿质量的不断提高,这种情况越发凸显。
由于钻头设计和齿的改进,PDC 钻头的可定向性也随之提高,这进一步削弱了过去在马达钻井中牙轮钻头的优势。
目前,PDC 钻头每天都在许多地层的钻井应用中排挤掉牙轮钻头的市场。
PDC 钻头厚层砾岩钻进技术探索与实践:为了降低海上钻井作业成本、提高作业效率,开发了PDC 钻头厚层砾岩钻进技术.在保持普通PDC 钻头快速切削性能的基础上,通过优选新型高强度PDC 切削 齿、改进钻头切削结构提高钻头的整体强度,通过采用后倾角渐变、力平衡设计、加强切削齿保护等方法提高钻头的稳定性,并且在使用中通过优化钻具组合、采用 合理的钻井参数和"中低排量-中低转速-中高钻压"的平稳钻进模式预防PDC 钻头在砾岩段的先期破坏,有效延长了钻头在砾岩钻进中的寿命.应用该技术实现 了用PDC 钻头在辽东湾一次性钻穿馆陶组和东营组上部疏松地层中垂厚近80 m 的砾岩段,有的井钻穿砾岩段后又直接钻下部中硬地层至完钻井深.采用PDC 钻头厚层砾岩钻进技术,可以大量节省海上钻井作业时间,显著降低钻井费用.PDC 钻头工程技术措施石油钻井装备:1)、首先做好PDC 钻头的选型工作,钻头水眼、流道设计应利于排屑;2)、下入PDC 钻头之前,应充分循环泥浆,清洗井眼,防止起钻后滞留在井眼内的钻屑继续水化分散;3)、下钻时钻头不断刮削井壁,井壁上的泥饼或滞留于井内的钻屑会在钻头下堆积,到一定程度便会压实在钻头上,那么下钻中途进行循环,将钻头 冲洗干净也是有其必要的;4)、下钻过程中还应适当控制速度,防止钻头突然冲入砂桥,钻进一堆烂泥中;另外如果速度恰当,PDC 钻头会顺着上一只钻头所钻的螺旋形井眼轨道行 进,而不是在井壁上划拉下大量泥饼。
pdc钻头名词解释
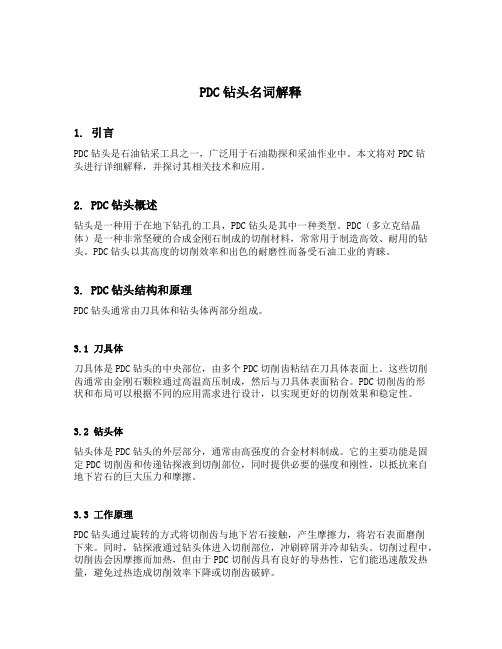
PDC钻头名词解释1. 引言PDC钻头是石油钻采工具之一,广泛用于石油勘探和采油作业中。
本文将对PDC钻头进行详细解释,并探讨其相关技术和应用。
2. PDC钻头概述钻头是一种用于在地下钻孔的工具,PDC钻头是其中一种类型。
PDC(多立克结晶体)是一种非常坚硬的合成金刚石制成的切削材料,常常用于制造高效、耐用的钻头。
PDC钻头以其高度的切削效率和出色的耐磨性而备受石油工业的青睐。
3. PDC钻头结构和原理PDC钻头通常由刀具体和钻头体两部分组成。
3.1 刀具体刀具体是PDC钻头的中央部位,由多个PDC切削齿粘结在刀具体表面上。
这些切削齿通常由金刚石颗粒通过高温高压制成,然后与刀具体表面粘合。
PDC切削齿的形状和布局可以根据不同的应用需求进行设计,以实现更好的切削效果和稳定性。
3.2 钻头体钻头体是PDC钻头的外层部分,通常由高强度的合金材料制成。
它的主要功能是固定PDC切削齿和传递钻探液到切削部位,同时提供必要的强度和刚性,以抵抗来自地下岩石的巨大压力和摩擦。
3.3 工作原理PDC钻头通过旋转的方式将切削齿与地下岩石接触,产生摩擦力,将岩石表面磨削下来。
同时,钻探液通过钻头体进入切削部位,冲刷碎屑并冷却钻头。
切削过程中,切削齿会因摩擦而加热,但由于PDC切削齿具有良好的导热性,它们能迅速散发热量,避免过热造成切削效率下降或切削齿破碎。
4. PDC钻头的优势相比传统的钻头类型,PDC钻头具有许多优势。
4.1 高效切削PDC钻头采用多个粘合在刀具体上的PDC切削齿,这种设计可以实现高效的切削,快速消耗岩石表面,提高钻探效率。
4.2 耐磨性强PDC切削齿具有良好的耐磨性,能够承受长时间的高强度切削,减少了频繁更换切削齿的需要,提高了钻头的使用寿命。
4.3 高度稳定PDC钻头的切削齿布局和形状经过精心设计,可以实现平衡切削力和稳定性。
它们减少了钻头的震动和偏离轨迹的可能性,确保了钻孔的准确度和质量。
4.4 适应多种地质环境PDC钻头可以适应各种地质环境,如软土、硬岩、砾石等。
pdc钻头的原理与应用

PDC钻头的原理与应用1. 简介PDC钻头是一种新型的刀具,它采用多个聚晶金刚石(Polycrystalline Diamond Compact,PDC)片嵌入钢体基体制成,广泛用于石油勘探和开发领域。
本文将介绍PDC钻头的原理和应用。
2. PDC钻头的原理PDC钻头的原理是将多个聚晶金刚石片嵌入钢体基体制成,利用聚晶金刚石的高硬度和耐磨性,以及钢体基体的韧性和强度,实现高效的钻井作业。
PDC钻头的原理主要包括以下几个方面:2.1 聚晶金刚石片PDC钻头采用的聚晶金刚石片由多个金刚石颗粒和金属结合剂组成,具有高硬度、耐磨性好等特点。
聚晶金刚石片通过特定的制备工艺,使得每个金刚石颗粒都与周围的颗粒紧密结合,形成一个整体。
2.2 钢体基体钢体基体是PDC钻头的主体部分,它由高强度的钢材制成。
钢体基体承载着聚晶金刚石片,并且通过特定的工艺将聚晶金刚石片与钢体基体紧密结合,形成一个整体结构。
钢体基体具有良好的韧性和强度,能够有效地传递钻井力,同时保护聚晶金刚石片。
2.3 刀具形态PDC钻头的刀具形态通常有平面PDC钻头、锥度PDC钻头和斜面PDC钻头等。
不同形态的刀具适用于不同的地质条件和钻井需求。
例如,平面PDC钻头适用于较硬的地质层,而锥度PDC钻头适用于软、粉状的地质层。
2.4 作用原理PDC钻头在钻井作业中,通过旋转和下压力来完成钻井作业。
当PDC钻头旋转时,聚晶金刚石片切削岩石,同时钢体基体提供支撑和切削力。
通过连续的旋转和下压力,PDC钻头可以持续地切削岩石,实现高效的钻井作业。
3. PDC钻头的应用PDC钻头由于其优良的性能,在石油勘探和开发领域得到了广泛的应用。
主要应用于以下几个方面:3.1 石油勘探PDC钻头可以在石油勘探中使用,用于钻取各种类型的地层。
由于其高硬度和耐磨性,PDC钻头可以有效地切削各种岩石,包括硬质岩石和软质岩石。
在石油勘探中,PDC钻头可以提高钻探的效率,减少钻井时间,降低勘探成本。
pdc钻头工作原理
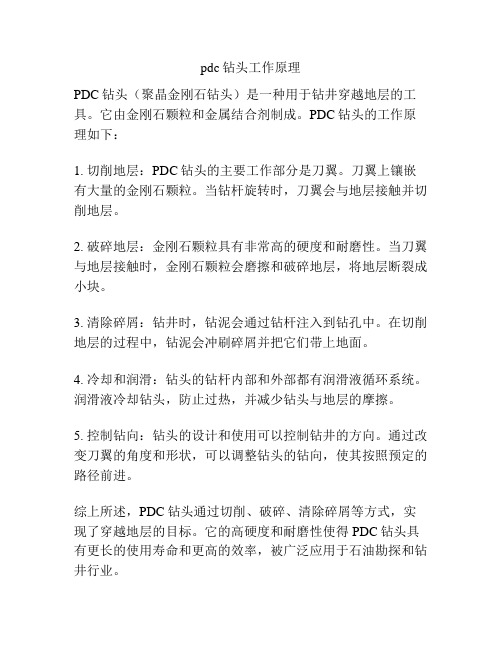
pdc钻头工作原理
PDC钻头(聚晶金刚石钻头)是一种用于钻井穿越地层的工具。
它由金刚石颗粒和金属结合剂制成。
PDC钻头的工作原理如下:
1. 切削地层:PDC钻头的主要工作部分是刀翼。
刀翼上镶嵌有大量的金刚石颗粒。
当钻杆旋转时,刀翼会与地层接触并切削地层。
2. 破碎地层:金刚石颗粒具有非常高的硬度和耐磨性。
当刀翼与地层接触时,金刚石颗粒会磨擦和破碎地层,将地层断裂成小块。
3. 清除碎屑:钻井时,钻泥会通过钻杆注入到钻孔中。
在切削地层的过程中,钻泥会冲刷碎屑并把它们带上地面。
4. 冷却和润滑:钻头的钻杆内部和外部都有润滑液循环系统。
润滑液冷却钻头,防止过热,并减少钻头与地层的摩擦。
5. 控制钻向:钻头的设计和使用可以控制钻井的方向。
通过改变刀翼的角度和形状,可以调整钻头的钻向,使其按照预定的路径前进。
综上所述,PDC钻头通过切削、破碎、清除碎屑等方式,实现了穿越地层的目标。
它的高硬度和耐磨性使得PDC钻头具有更长的使用寿命和更高的效率,被广泛应用于石油勘探和钻井行业。
PDC钻头泥包现象的研究与分析

PDC钻头泥包现象的研究与分析随着钻井提速的需求,钻井现场更多地使用PDC钻头,显著提高钻井效率,减少起下钻,避免掉钻头等事故,降低成本。
但在应用中经常有PDC钻头泥包的现象,泥包是制约PDC钻头使用和提高机械钻速的主要问题。
本文在分析泥包原因的基础上,从泥浆性能、钻井参数、现场操作等方面结合施工井钻头泥包现象,对PDC钻头泥包进行了分析,提出预防PDC钻头泥包的技术措施,有助于解决PDC钻头泥包的问题。
标签:PDC钻头;泥包;粘度;切力;劣质固相1PDC钻头结构及布齿方式1.1 PDC钻头结构PDC钻头是以聚晶金刚石复合片(PDC)作为切削刃的钻头,主要由钻头体、聚晶金刚石复合片切削齿、水力结构等部分组成。
其中钻头冠部是其工作面,其工作面的几何形状影响钻头的稳定性、井底清洗、钻头磨损及钻头各部位载荷分布。
钻头工作面形状一般包括内锥、顶部、侧面、肩部及保径五个基本要素。
1.2 布齿方式PDC钻头布齿方式有三种:刮刀式布齿,单齿式布齿,组合式切削齿。
刮刀式布齿方式的特点是将切削齿沿着从钻头中心附近到保径部位的直线(或接近于直线的曲线)布置在胎体刮刀上,在适当的位置布置喷嘴(或水眼),每个喷嘴或水眼起到冷却或清洗一个或两个刮刀片上的切削齿的作用。
采用这种方式布齿的PDC钻头具有整体强度高、抗冲击能力强、易于清洗和冷却、排屑好、抗泥包能力强的特点,在黏性或软地层中应使用这种布齿方式的PDC钻头。
单齿式布齿方式是将切削齿一个一个地单独布置在钻头工作面上,在适当的地方布置喷嘴或水眼,钻井液从喷嘴流出后,切削齿收到清洗及冷却,当同时也起到阻流与分配液流的作用。
这种结构的布齿区域大、布齿密度高,可以提供钻头的使用寿命,但水力控制能力低,容易在黏性地层泥包。
组合式切削齒的布置采用直线刮刀和单齿式相结合的方式,在适当的地方布置水眼或喷嘴,这种布齿方式具有较好的清洗、冷却和排屑能力,布齿密度较高。
这种布齿方式的钻头多用于中等硬度地层。
- 1、下载文档前请自行甄别文档内容的完整性,平台不提供额外的编辑、内容补充、找答案等附加服务。
- 2、"仅部分预览"的文档,不可在线预览部分如存在完整性等问题,可反馈申请退款(可完整预览的文档不适用该条件!)。
- 3、如文档侵犯您的权益,请联系客服反馈,我们会尽快为您处理(人工客服工作时间:9:00-18:30)。
PDC钻头英文:Polycrystalline Diamond Compact聚晶金刚石复合片钻头的简称。
是石油钻井行业常用的一种钻井工具。
PDC产品性能不断改进。
在过去的几年间,PDC切削齿的质量和类型都发生了巨大的变化。
如果将20世纪80年代的齿与当今的齿进行比较的话,差异是相当大的。
由于混合工艺与制造工艺的变化,当今的切削齿的质量性能要好得多,使钻头的抗冲蚀以及抗冲击能力都大为提高。
工程师们还对碳化钨基片与人造金刚石之间的界面进行了优化,以提高切削齿的韧性。
层状金刚石工艺方面的革新也被用于提高产品的抗磨蚀性和热稳定性。
除了材料和制造工艺方面的发展以外,PDC产品在齿的设计技术和布齿方面也实现了重大的突破。
现在,PDC产品已可被用于以前所不能应用的地区,如更硬、磨蚀性更强和多变的地层。
这种向新领域中的扩展,对金刚石(固定切削齿)钻头和牙轮钻头之间的平衡发生了很大的影响。
8-1/2TD164A 4刀翼PDC钻头2TD194B 4刀翼PDC钻头8-1/2TD165A 5刀翼PDC钻头8-1/2TD196A 6刀翼PDC钻头9TD195A5刀翼PDC钻头9-1/2TD166A 6刀翼PDC钻头最初,PDC 钻头只能被用于软页岩地层中,原因是硬的夹层会损坏钻头。
但由于新技术的出现以及结构的变化,目前PDC 钻头已能够用于钻硬夹层和长段的硬岩地层了。
PDC 钻头正越来越多地为人们所选用,特别是随着PDC 齿质量的不断提高,这种情况越发凸显。
由于钻头设计和齿的改进,PDC 钻头的可定向性也随之提高,这进一步削弱了过去在马达钻井中牙轮钻头的优势。
目前,PDC 钻头每天都在许多地层的钻井应用中排挤掉牙轮钻头的市场。
PDC 钻头厚层砾岩钻进技术探索与实践:为了降低海上钻井作业成本、提高作业效率,开发了PDC 钻头厚层砾岩钻进技术.在保持普通PDC 钻头快速切削性能的基础上,通过优选新型高强度PDC 切削 齿、改进钻头切削结构提高钻头的整体强度,通过采用后倾角渐变、力平衡设计、加强切削齿保护等方法提高钻头的稳定性,并且在使用中通过优化钻具组合、采用 合理的钻井参数和"中低排量-中低转速-中高钻压"的平稳钻进模式预防PDC 钻头在砾岩段的先期破坏,有效延长了钻头在砾岩钻进中的寿命.应用该技术实现 了用PDC 钻头在辽东湾一次性钻穿馆陶组和东营组上部疏松地层中垂厚近80 m 的砾岩段,有的井钻穿砾岩段后又直接钻下部中硬地层至完钻井深.采用PDC 钻头厚层砾岩钻进技术,可以大量节省海上钻井作业时间,显著降低钻井费用.PDC 钻头工程技术措施石油钻井装备:1)、首先做好PDC 钻头的选型工作,钻头水眼、流道设计应利于排屑;2)、下入PDC 钻头之前,应充分循环泥浆,清洗井眼,防止起钻后滞留在井眼内的钻屑继续水化分散;3)、下钻时钻头不断刮削井壁,井壁上的泥饼或滞留于井内的钻屑会在钻头下堆积,到一定程度便会压实在钻头上,那么下钻中途进行循环,将钻头 冲洗干净也是有其必要的;4)、下钻过程中还应适当控制速度,防止钻头突然冲入砂桥,钻进一堆烂泥中;另外如果速度恰当,PDC 钻头会顺着上一只钻头所钻的螺旋形井眼轨道行 进,而不是在井壁上划拉下大量泥饼。
5)、每次下钻到底时必须先开泵,尽量提高排量充分冲洗井底和钻头,等排量满足要求后再轻压旋转钻进0.5-1m ,这也是PDC 钻头造型的要求。
6)、下入PDC 前先短起下钻,对井壁泥饼进行刮削、挤压,将厚泥饼拉薄、压实,尽量保证井眼畅通、消除阻卡;在钻头泥包高发区,如果采用了所有方法 也无法避免PDC 钻头泥包,那么先使用牙轮通一趟井就成了必要手段7)、尽量采用大排量钻进,保证PDC 钻头的充分清洗与冷却;8)、在软泥岩中钻进,应尽量采用低钻压、高转速、大排量,没有必要盲目使用高钻压去追求那仅高一小点的钻速,那只是牙轮钻头的使用方式;9)、操作要精细,送钻加压一定要均匀,不能忽大忽小。
*牙轮钻头在使用中的结构特点牙轮钻头在使用中具有良好的结构特点,下面简单的介绍一下牙轮钻头的结构特点:1、牙轮钻头采用浮动轴承结构,浮动元件由高强度、高弹性、高耐温性、高耐磨性特点的新材料制 成,表面经固体润滑剂处理。
在降低轴承副相对线速度的同时,减少摩擦面温升,能有效提高高钻压或高转速钻井工艺条件下的轴承寿命和轴承可靠性。
2、镶齿钻头采用高强度高韧性硬质合金齿,优化设计的齿排数、齿数、露齿高度和独特的合金齿外形,充分发挥 了镶齿钻头高耐磨性和优异的切削能力。
钢齿钻头齿面敷焊新型耐磨材料,在保持钢齿钻头高机械钻速的同时,提高了钻头切削齿寿命。
3、牙轮钻头中的钢球锁紧牙轮,适应高转速,能够在使用中提高工作效率。
4、采用可限制压差并防止钻井液进入润滑系统的全橡胶储油囊,为轴承系统提供了良好的润滑保证。
5、采用可耐250°C 高温、抗磨损的新型润滑脂。
6TD136A 6刀翼PDC 钻头 12-1/4TD166A 6刀翼PDC钻头 8-1/2TD13A6、采用高精度的金属密封。
金属密封由一副精心设计加工的金属密封环作为轴承轴向动密封,两个高弹性的橡胶供能圈分别位于牙掌和牙轮密封区域内作为静密封,优化的密封压缩量确保了两个金属环密封表面始终保持良好接触。
钻头的选型及分类一、金刚石钻头(一)金刚石材料钻头的特点((与牙轮钻头相比)(1)金刚石材料钻头是一体性钻头,可以使用高的转速,适合于和高转速的井下动力钻具一起使用,取得高的效益;在定向钻井过程中,它可以承受较大的侧向载荷而不发生井下事故,适合于定向钻井;(2)金刚石材料耐磨且寿命长,适合于深井及研磨性地层使用;(3)在地温较高的情况下,牙轮钻头的轴承密封易失效,使用金刚石材料钻头则不会出现此问题;in)的井眼钻井中,牙轮钻头的轴承由于空间尺寸的限制,强度受到影(4)在小于165.1 mm(61/2响,性能不能保证,而金刚石材料钻头则不会出现问题,因而小井眼钻井宜使用金刚石材料钻头;(5)金刚石材料钻头的钻压低于牙轮钻头,因而在钻压受到限制(如防斜钻进)的情况下应使用金刚石材料钻头;(6)金刚石材料钻头结构设计灵活,简单,能满足非标准的异形尺寸井眼的钻井需要;(7)金刚石材料钻头中的PDC钻头是一种切削型钻头,切削齿具有自锐优点,破碎岩石时无牙轮钻头的压持作用,切削齿切削时的切削面积较大,是一种高效钻头;(8)金刚石材料钻头工作时必须保证充分的清洗与冷却;(9)金刚石材料钻头抗冲击性载荷性能较差;(10)金刚石材料钻头价格较高。
(二)金刚石材料钻头选型(适应的地层)TSP钻头适合于在具有研磨性的中等至硬地层钻井。
PDC钻头适用于软到中等硬度地层,但是PDC钻头钻进的地层必须是均质地层,以避免冲击载荷,含砾石的地层不能使用PDC钻头。
二、牙轮钻头的选型及分类法(一)牙轮钻头选型的原则及应考虑的问题(1)地层的软硬程度和研磨性。
(2)钻进井段的深浅。
(3)易斜地层。
(4)软硬交错地层。
选用的钻头对所要钻的地层是否适合,要通过实践的检验才能下结论。
对于同一地层使用过的几种类型的钻头,在保证井身质量的前提下,一般以“每米成本”作为评价钻头选型是否合理的标准。
(1)国产牙轮钻头型号表示方法如下in(215.9 mm)的镶齿滑动密封轴承喷射式三牙轮钻头的型号为:例:用于中硬地层、直径为81/281/×HP5或215.9×HP5。
2(2)IADC牙轮钻头分类方法及编号IADC规定,每一类钻头用四位字码进行分类及编号,各字码的意义如下:第一位字码为系列代号,用数字1~8分别表示八个系列,表示钻头牙齿特征及所适用的地层:1一铣齿,低抗压强度高可钻性的软地层;2一铣齿,高抗压强度的中到中硬地层;3一铣齿,中等研磨性或研磨性的硬地层;4一镶齿,低抗压强度高可钻性的软地层;5一镶齿,低抗压强度的软到中硬地层;6一镶齿,高抗压强度的中硬地层;7一镶齿,中等研磨性或研磨性的硬地层;8一镶齿,高研磨性的极硬地层。
第二位字码为岩性级别代号,用数字1~4分别表示在第一位数码表示的钻头所适用的地层中再依次从软到硬分为四个等级。
第三位字码为钻头结构特征代号,用数字1~9计九个数字表示,其中1~7表示钻头轴承及保径特征,8与9留待未来的新结构特征钻头用。
1~7表示的意义如下:1一非密封滚动轴承;2一空气清洗、冷却,滚动轴承;3—滚动轴承,保径;4—滚动、密封轴承;5一滚动、密封轴承,保径;6一滑动、密封轴承;7一滑动、密封轴承,保径。
第四位字码为钻头附加结构特征代号,用以表示前面三位数字无法表达的特征,用英文字母表示。
目前,IADC已定义了11个特征,用下列字母表示:A一空气冷却;C一中心喷嘴;D一定向钻井;E一加长喷嘴;G一附加保径/钻头体保护;J一喷嘴偏射;R一加强焊缝(用于顿钻);S一标准铣齿;X一楔形镶齿;。
R一圆锥形镶齿;Z一其他形状镶齿。
有些钻头,其结构可能兼有多种附加结构特征,则应选择一个主要的特征符号表示。
钻头的合理使用一、金刚石钻头操作规程1.下井前准备。
(1)井下情况正常,起下钻畅通无阻。
(2)井底干净,无金属落物。
(3)钻井液符合钻井设计要求,净化设备运转正常。
(4)用好钻杆滤清器,其最大孔径应小于钻头最小喷嘴的直径。
2.下钻。
(1)钻头螺纹要涂好标准的润滑脂,上卸钻头要用钻头装卸器。
(2)钻头人井要扶正、慢放。
至防喷器时更要找中,防止碰坏PDC切削齿。
通过阻流环位置时,尤其要减慢下放速度,注意防碰。
l(3)下钻遇阻划眼时,划眼钻压应控制在20千牛以下(钻头直径小于215.5mm时,要低于10千牛),转速低于50转/分。
严禁大段划眼和不循环钻井液划眼。
(4)下钻接近井底时应提前开泵。
钻头离井底0.5m以上,应缓慢上下活动和转动钻具,充分循环钻井液。
待井底清洁后,校正指重表。
待泵压正常后方可井底造型。
3.井底造型。
确认钻头接触井底后,采用50转/分左右的转速和5~20千牛的钻压参数磨合井底,进尺0.5~1.0米。
4.钻井(1)钻速试验。
井底造型后,可在推荐钻井参数范围内,选用不同的钻压转速进行钻速试验,直到找到一个最优钻速为止。
正常钻进时若遇地层变化,可再做钻速试验。
(2)钻速试验完毕,即可按最优参数正常钻进。
钻进中要确保排量满足要求,送钻均匀。
枉钻遇泥岩井段时,钻速会明显下降,这时司钻要耐心,并可适当提高钻压,降低转速,但钻压也不宜过大,一般提高10~30千牛为宜。
若钻遇硬夹层发生轻微蹩钻现象时,可适当降低钻压,同时降低钻速,等钻穿后再采用正常参数钻进。
(3)每钻进300~400米要进行一次短起下钻(双心PDC钻头除外),以防止起钻拔活塞。
(4)钻头使用到后期,PDC切削齿的磨损平面加大,降低了PDC切削齿切入地层的深度,因此可适当提高钻压以维持较高的机械钻速。