管壳式换热器
管壳式换热器的工作原理及结构
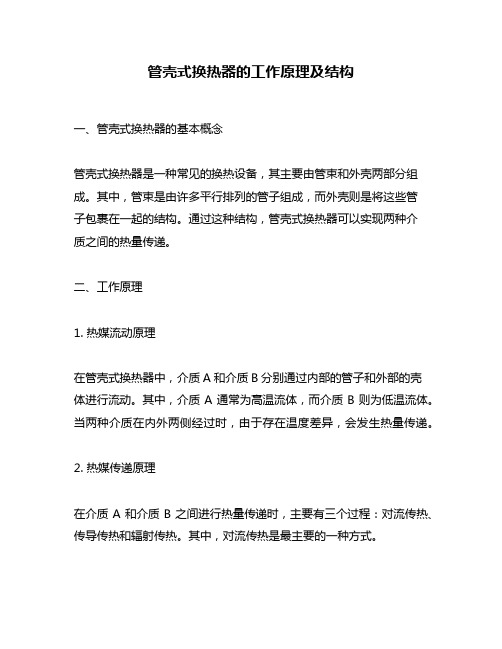
管壳式换热器的工作原理及结构一、管壳式换热器的基本概念管壳式换热器是一种常见的换热设备,其主要由管束和外壳两部分组成。
其中,管束是由许多平行排列的管子组成,而外壳则是将这些管子包裹在一起的结构。
通过这种结构,管壳式换热器可以实现两种介质之间的热量传递。
二、工作原理1. 热媒流动原理在管壳式换热器中,介质A和介质B分别通过内部的管子和外部的壳体进行流动。
其中,介质A通常为高温流体,而介质B则为低温流体。
当两种介质在内外两侧经过时,由于存在温度差异,会发生热量传递。
2. 热媒传递原理在介质A和介质B之间进行热量传递时,主要有三个过程:对流传热、传导传热和辐射传热。
其中,对流传热是最主要的一种方式。
3. 工作过程在工作过程中,高温流体通过内部的管子进入到换热器中,并沿着管子表面流动。
同时,低温流体从外部的壳体进入到换热器中,并沿着管子外表面流动。
在这个过程中,高温流体和低温流体之间进行了热量传递,使得高温流体的温度降低,而低温流体的温度升高。
三、结构特点1. 管束结构管束是管壳式换热器的主要组成部分之一。
在管束中,许多平行排列的管子被固定在两个端盖板上,并通过密封垫圈与外壳连接。
由于管子间距离较小,因此可以有效地增加热量传递面积。
2. 壳体结构外壳是管壳式换热器的另一个重要组成部分。
它通常由两个半球形或长方形壳体组成,并通过法兰连接。
在使用过程中,外壳起到保护内部管束不受损坏的作用。
3. 密封结构为了保证介质A和介质B之间不发生混合,在管壳式换热器中需要设置密封结构。
这种密封结构通常采用密封垫圈或波纹垫片等材料制成,可以有效地防止介质泄漏。
4. 清洗结构由于管壳式换热器在使用过程中会产生一定的污垢和腐蚀物,因此需要定期进行清洗。
为了方便清洗,管壳式换热器通常设置有进出口和排污口等结构。
四、应用领域管壳式换热器广泛应用于化工、石油、制药、食品等领域中。
在这些领域中,管壳式换热器可以实现高效的热量传递,提高生产效率,并减少能源消耗。
管壳式换热器的课程设计
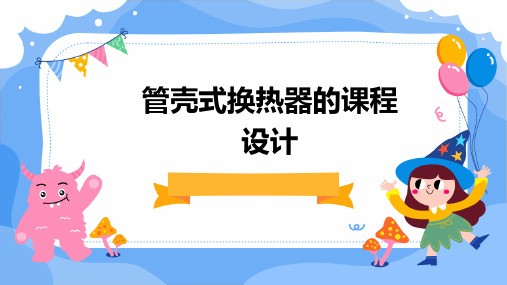
避免选用不合适的材料导致设备损坏 或安全事故;注意材料的兼容性和与 其他材料的接触情况;考虑材料的可 加工性和安装维护的便利性。
04
管壳式换热器的优化设计
传热效率优化
01
传热效率
通过选择合适的材料、优化管程和壳程流体的流速和温度,以及采用强
化传热技术,如增加翅片、改进管子形状等,提高换热器的传热效率。
管件与结构
优化换热器内部的管件和 结构,减少流体流动过程 中的局部阻力,降低压力 损失。
结构强度优化
1 2
应力分析
对换热器进行详细的应力分析,确保其在正常操 作条件下具有足够的结构强度和稳定性。
材料选择
根据使用条件和要求,选择合适的材料和厚度, 以提高换热器的结构强度和耐腐蚀性。
3
支撑与固定
合理设计换热器的支撑和固定结构,以减小应力 集中和振动,提高其结构强度和使用寿命。
新材料与新技术的应用
新型材料
采用高导热性能的复合材料、纳米材料等,提高换热器的传热效率。
新型涂层
利用先进的涂层技术,如陶瓷涂层、金属氧化物涂层等,增强换热器的抗腐蚀和 耐磨性能。
节能减排与环保要求
高效节能
研发低能耗的换热器,优化换热器结构,降低运行过程中的能源消耗。
环保设计
采用无毒、无害的材料,减少换热器对环境的影响,同时对换热器产生的废弃物进行环保处理。
能源与动力工程领域的应用
发电厂
管壳式换热器可用于加热和冷却发电厂中的各种 流体,如锅炉给水、凝结水和冷却水等。
船舶工程
在船舶工程中,管壳式换热器可用于船舶发动机 的冷却和加热,以及生活用水的加热和冷却。
采暖系统
在供暖系统中,管壳式换热器可用于将热量从热 源传递到水中,为建筑物提供热水供暖。
管壳式换热器简介

管壳式换热器由管子,管板和壳体(管箱)组成。
由于管内外流体的温度不同,因之换热器的壳体与管束的温度也不同。
如果两温度相差很大,换热器内将产生很大热应力,导致管子弯曲、断裂,或从管板上拉脱。
因此,当管束与壳体温度差超过50℃时,需采取适当补偿措施,以消除或减少热应力。
根据所采用的补偿措施,管壳式换热器可分为以下几种主要类型:
①固定管板式换热器管束两端的管板(跟管子过盈配合的那块板)与壳体联成一体,结构简单,但只适用于冷热流体温度差不大,且壳程不需机械清洗时的换热操作。
当温度差稍大(相差50度必须)而壳程压力又不太高时,可在壳体上安装有弹性的补偿圈,以减小热应力。
(每个物体都有伸缩性,像水杯,冷热水无影响,但是像这,管程热水要膨胀,壳程冷水要收缩,就需要弹性好的补偿圈)
②浮头(斧头)式换热器(有一块浮头管板就是不固定,有一块固定管板,在固定管板的基础上,只是管程流体到另一端便折流)管束一端的管板可自由浮动,完全消除了热应力;且整个管束可从壳体中抽出,便于机械清洗和检修。
浮头式换热器的应用较广,但结构比较复杂,造价较高。
③U型管式换热器每根换热管皆弯成U形,两端分别固定在同一管板上下两区,借助于管箱内的隔板分成进出口两室。
此种换热器完全消除了热应力,弯曲那端不用膨胀固定,可以伸缩。
消除应力。
结构比浮头式简单,但管程不易清洗(因为弯曲,难冲洗)。
温度应力又称为热应力,它是由于构件受热不均匀而存在着温度差异,各处膨胀变形或收缩变形不一致,相互约束而产生的内应力。
管壳式热交换器
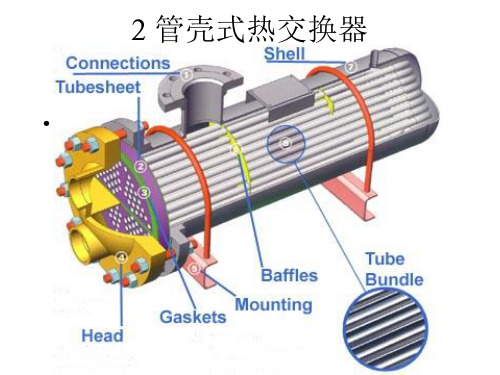
2.5.2 流体温度和终温的确定
• 在换热器设计中加热剂或冷却剂出口温度需由设计 者确定。如冷却水进口温度需依当地条件而定,但 出口温度需通过经济权衡作出选择。在缺水地区可 使出口温度高些,这样操作费用低,但使传热平均 温差下降,需传热面积增加使得投资费用提高,反 之亦然。根据经验一般应使∆tm大于10℃为宜, 此外若工业用水作为冷却剂出口温度不宜过高,因 工业用水中所含的盐类(主要CaCO3,MgCO3,CaSO4、 MgSO4等)的溶解度随温度升高而减小,若出口温度 过高,盐类析出,形成垢层使传热过程恶化,因此 一般出口温度不超过45℃。所以应根据水源条件, 水质情况等加以综合考虑后确定。水源严重缺乏地 区可采用空气作为冷却剂,但使传热系数下降。对 于加热剂可按同样原则选择出口温度
一、管、壳程介质的配置 有利于传热、压力损失小。具体如下: 1、流量小、粘度大的流体走壳程较好。 2、温差较大时,K大的流体走壳程。 3、与外界温差大的流体走管程。 4、饱和蒸汽走壳程。 5、含杂质流体走管程。 6、有毒介质走管程。 7、压降小走壳程。 8、高温、高压、腐蚀性强的流体走管程。
2.5.1 流体在换热器中内的流动 空间选择
管程变化对阻力影响
• 对同一换热器,若由单管程改为两管程, 阻力损失剧增为原来的8倍,而强制对流 传热、湍流条件下的表面传热系数只增 为原来的1.74倍;若由单管程改为四管程, 阻力损失增为原来的64倍,而表面传热 系数只增为原来的3倍。由此可见,在选 择换热器管程数目时,应该兼顾传热与 流体压降两方面的得失。
– 见公式2.21
2.3 管壳式换热器的传热计算
• • • • • 一、热力设计任务 1.合理的参数选择及结构设计 2.传热计算和压降计算 热力设计:设计计算,校核计算。 设计计算:已知传热量Q,换热工质工作 参数(进、出口温度),求F和结构形式。 • 校核计算:已知换热器的具体结构、某 些参数来核定另一参数。
管壳式换热器结构介绍
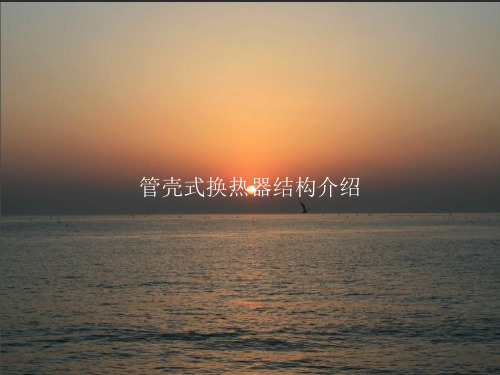
后封头
L型后封头:和A型前封头相同 M型后封头:和B型前封头相同 N型后封头:和N型前封头相同 U型:U型管束,管束可移动,壳侧容易清洗;热膨胀处理优秀,经济无法兰; 缺点是管侧无法清洗,更换管束困难,弯头部位容易冲刷损伤, P型封头和W型封头已经被淘汰,不在使用, S型封头:其尺寸特点是其后封头要比壳体的直径大,优点是可以解决换热 器设计过程中的两个问题,一是可以消除换热器的热应力,二是换热器的管
造遵循标准:国外TEMAASME国内GB151、GB150
换热器封头选取原则
1、管壳侧是否需要清洗; 2、是否需要移动管束; 3、是否需要考虑热膨胀; 前封头类型:A、B、C、D、N 后封头类型:L、M、N、P、S、T、W 后封头又分为固定式、浮头式以及U型管,相对于固定式,浮头式造价更高、 需要更大的壳径、低的换热效果由于泄漏流C的存在,优点则是一端具有自 由度可以处理好热膨胀问题,
温度,
5、设备结构的选择
对于一定的工艺条件,首先应确定设备的形式, 例如选择固定管板形式还是浮头形式等,参
螺纹管性能特点
在管子类型中,螺纹管属于管外扩展表面的类型,在普通换热管外壁轧制成 螺纹状的低翅片,用以增加外侧的传热面积,螺纹管表面积比光管可扩展 1.6-2.7倍,与光管相比,当管外流速一样时,壳程传热热阻可以缩小相应的倍 数,而管内流体因管径的减小,则压力降会略有增大,螺纹管比较适宜于壳
K型壳体:主要用于管程热介质,壳侧蒸发的工况,在废热回收条件下使用,
X型壳体:冷热流体属于错流流动,其优点是压降非常小,当采用其他壳体 发生振动,且通过调整换热器参数无法消除该振动时可以使用此壳体形式,
其不足之处是流体分布不均匀,X型壳体并不经常使用,
在化工工艺手册中,I型壳体类型可EDR软件中的不是同一种壳体,其形式见 I1,它的使用方式仅有一种搭配,就是BIU,U型管换热器,
管壳式换热器
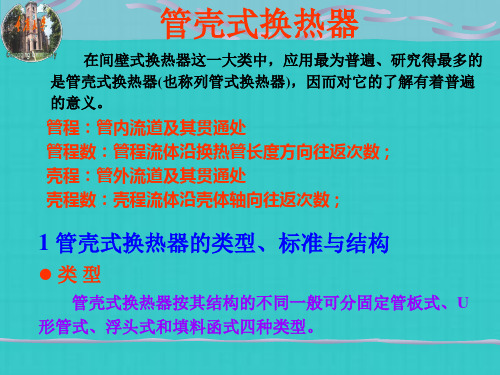
管/壳程设计压力(MPa),压力相等时只写Pt 公称直径(mm),对釜式重沸器用分数表示, 分子为管箱内直径,分母为圆筒内直径
第一个字母代表前端管箱型式,第二个字母代表壳体型式, 第三个字母代表后端结构型式
管壳式换热器的类型、标准与结构
管壳式换热器的类型、标准与结构
粘度在10-3 Pa·s以下的低粘性液体,Ft=0. 应用虎克定律,可分别求出管子所受的压缩力和壳体所受的拉伸力。 拉杆是一根两端皆带螺纹的长杆,一端拧入管板,折流板穿在拉杆上,各折流板之间则以套在拉杆上的定距管来保持板间距离,最后 一块折流板用螺母拧在拉杆上紧固。 折流板泄漏校正系数Rl 折流板厚度:为了防振、并能承受拆换管子时的扭拉作用,折流板须有一定厚度。 旁路挡板的安装:旁路挡板厚度一般与折流板厚度相同,可将它嵌入折流板槽内,并点焊在每块折流板上。 第三个字母代表后端结构型式 管壳式换热器主要组合部件有前端管箱、壳体和后端结构(包括管束)三部分,三部分的不同组合,就形成结构不同的换热器。 当设备上无安装折流板的要求(如冷凝换热)时,应该安装一定数量的支持板,用来支撑换热管,防止它产生过大挠度。 解决方法:在外壳上装设膨胀节,减小但不能完全消除温差热应力,且在多程换热器中,这种方法不能照顾到管子的相对移动。 管壳式换热器的热补偿问题 具有膨胀节的固定管板式换热器 公称直径(mm),对釜式重沸器用分数表示, 14因子来校正,则不论加热或冷却,均可取(mf/mw)0. 此修正项的计算,往往由于壁温未知而要用试算法; 显然,长管不便于拆换和清洗,增加程数则使构造复杂,并在无相变的换热器中引起平均温差的降低。 (3)当管束与壳体的温差太大而产生不同的热膨胀时,常会使管子与管板的接口脱开,从而发生流体的泄漏。 (1)传热面一定时,增加管长可使换热器直径减小,从而使换热器的成本有所降低。 (8) 折流板外缘与壳体内壁之间的泄漏面积Asb 管长应选用标准值:GBl51-1999推荐换热管长度为:l000、1500、2000、2500、3000、4500、6000、7500、9000、12000 mm等
管壳式与板式水水换热器的比较分析
管壳式与板式水水换热器的比较分析管壳式和板式水水换热器是两种常见的换热设备,它们在应用范围、换热效果、维护保养等方面都有不同的特点。
本文将分析对比这两种换热器的优缺点,以帮助读者选择适合自己的换热器。
一、管壳式水水换热器管壳式换热器是由一个管壳和多个外管、内管组成的传热设备。
内管和外管之间的空间中流体进行传热,通常用于高温、高压、高粘度、易腐蚀、易结垢的介质换热。
其优点主要有以下几点:1. 适用范围广:管壳式换热器可以适用于多种工业领域,如化工、石化、制药、航空航天等。
2. 效率高:由于管壳式换热器的传热面积大,因此效率相对较高。
3. 维护保养方便:管壳式换热器可以进行组件化维护,随时更换外管和内管,便于清洗和维护。
但管壳式水水换热器也有其缺点:1. 制作成本高:管壳式换热器的制造成本较高,因为需要制造大量外管和内管。
2. 占用空间大:管壳式换热器由于外形尺寸较大,占用的空间相对较大。
3. 流体压降大:由于管壳式换热器的内部设计,流体的压降大,需要消耗更多的能量。
二、板式水水换热器板式换热器是由多个密封的板组成,板上的通道构成流体的管道,在板上进行传热。
板式换热器通常用于低温、低压、低粘度、不易腐蚀、不易结垢的介质换热。
其优点主要有以下几点:1. 占用空间小:板式换热器通常比管壳式换热器小,占用的空间相对较小。
2. 制作成本低:板式换热器的制造成本相对较低,因为只需要制造少量密封板即可。
3. 传热效果好:由于板式换热器的传热面积大,传热效果好。
但板式换热器也有其缺点:1. 不适用于高温高压:由于板式换热器的密封性不够,不适用于高温、高压介质。
2. 维护保养复杂:由于板式换热器的结构复杂,维护保养需要额外耗费一定的时间和精力。
3. 稳定性差:由于板式换热器板间的连接处容易出现渗漏情况,不够稳定。
综上所述,管壳式水水换热器和板式水水换热器在适用范围、效率、维护保养等方面都有不同的特点。
根据实际需要选择适合自己的换热器是关键。
管壳式换热器原理
管壳式换热器原理嘿,朋友们!今天咱来聊聊管壳式换热器原理,这玩意儿可有意思啦!你可以把管壳式换热器想象成是一个特别的“热魔法盒”。
它有个长长的壳子,就像一个大口袋,里面装着好多管子。
这管子啊,就像是一条条小路,热的流体和冷的流体就沿着这些小路走。
热流体大摇大摆地从一些管子里通过,它身上带着好多热量呢。
而冷流体呢,则在壳子和管子之间的缝隙里悄悄溜达。
这时候神奇的事情就发生啦!热流体的热量就会透过管子壁,传递给冷流体。
哎呀呀,这不就像是热流体很大方地把自己的热量分了一些给冷流体嘛!你说这像不像在一个热闹的集市上,大家互相交换东西?热流体把热量这个“宝贝”给了冷流体,自己慢慢变凉了,冷流体呢,就变得暖和起来了。
这样不就实现了热量的交换嘛!那这其中的原理到底是咋回事呢?其实啊,就是因为有温差呀!热的东西总是想把热量散发出去,冷的东西总是想吸收热量,这是自然规律呀!管壳式换热器就是利用了这个规律,让热流体和冷流体在合适的地方相遇,然后完成热量的传递。
你想想看,要是没有这种换热器,我们的生活得少了多少便利呀!比如在一些工厂里,需要把热量从一个地方转移到另一个地方,要是靠人工去搬,那得累成啥样呀!有了管壳式换热器,就轻松多啦。
而且哦,管壳式换热器还有很多不同的类型呢,就像人有不同的性格一样。
有的适合处理高温的流体,有的适合处理腐蚀性的流体,各有各的特点和用处。
咱再说说它的优点吧。
它结构相对简单,容易制造和维护,这多好呀!就像一个老实可靠的朋友,不会给你找麻烦。
而且它的换热效率也不错呀,可以在很多场合大显身手。
当然啦,它也不是完美无缺的。
它可能会占比较大的空间,有时候还会有一些泄漏的问题。
但这也不能掩盖它的光芒呀!总之呢,管壳式换热器原理虽然看起来有点复杂,但只要你用心去理解,就会发现其实也不难。
它就像我们生活中的一个好帮手,默默地为我们服务着。
让我们的生活变得更加舒适和便利。
所以呀,可别小看了这个“热魔法盒”哦!原创不易,请尊重原创,谢谢!。
管壳式换热器国家标准
管壳式换热器国家标准管壳式换热器是一种常见的热交换设备,广泛应用于化工、石油、电力、制药等领域。
为了确保管壳式换热器的安全性、可靠性和性能,国家制定了一系列的标准,以规范其设计、制造、安装和使用。
本文将对管壳式换热器国家标准进行介绍和解析,以便相关行业从业人员更好地理解和遵守相关标准。
首先,管壳式换热器的国家标准主要包括GB/T151、GB/T251、GB/T351等一系列标准。
这些标准涵盖了管壳式换热器的设计、材料、制造、检验、安装、使用和维护等方面。
其中,GB/T151主要规定了管壳式换热器的基本参数、技术要求和检验方法;GB/T251主要规定了管壳式换热器的材料选用和制造要求;GB/T351主要规定了管壳式换热器的安装、使用和维护要求。
其次,管壳式换热器国家标准的制定是为了保障设备的安全运行和有效利用。
在设计和制造过程中,必须严格按照相关标准的要求进行,确保设备具有良好的耐压性、耐腐蚀性和传热性能。
在安装和使用过程中,必须按照标准规定的程序和方法进行,确保设备能够安全、稳定地运行。
在维护和检修过程中,必须按照标准规定的要求进行,确保设备的性能和使用寿命。
此外,管壳式换热器国家标准的遵守对于相关行业从业人员来说是非常重要的。
只有严格遵守相关标准,才能保证设备的安全性和可靠性。
因此,相关行业从业人员必须深入学习和理解相关标准,严格按照标准要求进行工作,不得有丝毫马虎和疏忽。
总之,管壳式换热器国家标准的制定和遵守对于保障设备的安全运行和有效利用具有重要意义。
相关行业从业人员必须深入学习和理解相关标准,严格按照标准要求进行工作,确保设备的安全性、可靠性和性能。
只有这样,才能更好地推动相关行业的发展,实现设备的长期稳定运行和有效利用。
管壳式换热器 比例
管壳式换热器比例
管壳式换热器是一种常见的热交换设备,用于在两种流体之间传递热量。
它通常由一个管束(管子)和一个外壳组成。
管壳式换热器的比例可以从多个角度来讨论:
1. 效率比例,管壳式换热器的效率是指它实际传递的热量与理论上可以传递的最大热量之间的比率。
提高管壳式换热器的效率可以通过优化设计、改进材料和增加换热面积等方式来实现。
2. 尺寸比例,管壳式换热器的尺寸比例可以指外壳和管束之间的尺寸比例,以及换热面积和整体尺寸之间的比例。
合理的尺寸比例可以影响换热器的性能和成本。
3. 流体比例,在管壳式换热器中,流体的流量比例和流速比例对换热效果有重要影响。
合理的流体比例可以确保充分的热交换,同时避免流体过速或过慢导致的问题。
4. 材料比例,管壳式换热器的材料比例指的是外壳、管束以及密封件等部件的材料选择比例。
选择合适的材料可以确保换热器在不同工况下具有良好的耐腐蚀性和耐高温性能。
综上所述,管壳式换热器的比例涉及到多个方面,包括效率、尺寸、流体和材料等。
在实际应用中,根据具体的工艺要求和换热条件,需要综合考虑这些因素来确定合适的比例关系,以确保换热器的性能和可靠性。
- 1、下载文档前请自行甄别文档内容的完整性,平台不提供额外的编辑、内容补充、找答案等附加服务。
- 2、"仅部分预览"的文档,不可在线预览部分如存在完整性等问题,可反馈申请退款(可完整预览的文档不适用该条件!)。
- 3、如文档侵犯您的权益,请联系客服反馈,我们会尽快为您处理(人工客服工作时间:9:00-18:30)。
应用:
有缝隙腐蚀; 需使用复合管板等的场合
53
6.2.2 管壳式换热器结构
过程设备设计
切除管子端部
54
6.2.2 管壳式换热器结构
过程设备设计
课堂讨论
关于先焊还是先胀的讨论 机械胀接——先焊后胀 液压胀接——先胀后焊
55
过程设备设计
第六章 换热设备
6.1 概述 6.2 管壳式换热器 6.3 传热强化技术
12
14
19
25
32
38
45
57
换热管中心距
16
19
25
32
40
48
57
72
25
6.2.2 管壳式换热器结构
过程设备设计
26
6.2.2 管壳式换热器结构
过程设备设计
二、管板
用来排布换热管;
作用
将管程和壳程流体分开,避免冷、热流体混合; 承受管程、壳程压力和温度的载荷作用。
27
6.2.2 管壳式换热器结构
应用
除较大振动和缝隙腐蚀场合外,该方法应用广泛; 薄管板不能胀,只能焊。
52
6.2.2 管壳式换热器结构
过程设备设计
3.胀焊并用
主要有强度胀+密封焊、强度焊+贴胀、强度焊+强度胀等 不仅能提高连接处的抗疲劳性能, 而且还可消除应力腐蚀和缝隙腐蚀, 提高使用寿命
密封性能要求较高; 承受振动和疲劳载荷;
过程设备设计
1.管板材料
力学性能
介质腐蚀性(及tube-tubesheet间电位差对腐蚀影响)
贵重钢板价格
流体无腐蚀性或有轻微腐蚀性时, 管板采用压力容器用碳素钢或低合金钢板或锻件制造;
腐蚀性较强时,用不锈钢、铜、铝、钛等材料,
为经济考虑,采用复合钢板或堆焊衬里。
28
6.2.2 管壳式换热器结构
过程设备设计
特点
隔板 箱盖
清洗时不要拆除管线; 管板 隔板 (1) 缺点是用材较多。
(2)
(b)
箱盖
40
6.2.2 管壳式换热器结构
过程设备设计
特点
隔板
(1)
管板 隔板
检查、清洗不方便 很少使用
( 2)
)
箱盖
(c)
41
6.2.2 管壳式换热器结构
过程设备设计
特点
隔板
设置多层隔板 的管箱结构
(d)
42
6.2.2 管壳式换热器结构
过程设备设计
四、管束分程 管内流动的流体从管子的一端流到另一端,称为一个管程
换热面积要变大
管数增加
流速下降
管子加长 传热系数下降
多管程
43
6.2.2 管壳式换热器结构
管束分程布置图
2
1 2 1 2 3 4 1 4
过程设备设计
管程数 流动顺序 管箱隔板 介质返回 侧隔板 图序
1
4
2 3 1 2 4 3 2 5 1 6 3 4
优点
结构较浮头式简单,加工制造方便; 节省材料,造价比较低廉; 管束从壳体内可抽出; 管内、管间都能进行清洗,维修方便。
填料处易泄漏。 4MPa 以下,且不适用于易挥发、易燃、 易爆、有毒及贵重介质,使用温度受填 料的物性限制。
缺点 应用
注:填料函式换热器现在已很少采用。
15
6.2.1 基本类型
五、釜式重沸器
过程设备设计
结构 蒸发空间
(f)
管束可以为浮头式、U形管式和固定管板式结构
16
6.2.1 基本类型
过程设备设计
特点
与浮头式、U形管式换热器一样, 清洗维修方便; 可处理不清洁、易结垢介质,能 承受高温、高压(无温差应力)。
17
6.2.2 管壳式换热器结构
过程设备设计
管程
壳程
( a) BEM立 式 固 定 管 板 式 换 热 器
为减少热应力,通常在固定管板式换热器中设置柔性元件 (如膨胀节、挠性管板等),来吸收热膨胀差。
7
6.2.1 基本类型
过程设备设计
二、浮头式
结构
浮头端
浮头端可自由伸缩,无热应力
8
浮头式换热器
9
6.2.1 基本类型
过程设备设计
优点——管间和管内清洗方便,不会产生热应力; 缺点——结构复杂,造价比固定管板式换热器高, 设备笨重,材料消耗量大,且浮头端小盖 在操作中无法检查,制造时对密封要求较 高。 应用——壳体和管束之间壁温差较大或壳程介质易 结垢的场合。
非均匀胀接 方法 均匀胀接
管子硬度一般须低于管板硬度, 若达不到,可进行管头退火处理
47
6.2.2 管壳式换热器结构
过程设备设计
液压胀接
接头
48
6.2.2 管壳式换热器结构
过程设备设计
液压胀接
49
6.2.2 管壳式换热器结构
过程设备设计
机械胀接
50
6.2.2 管壳式换热器结构
过程设备设计
2.强度焊
10
6.2.1 基本类型
过程设备设计
三、U形管式换热器
结构
U形管
( C) BIU U形 管 式 换 热 器
11
U形管式换热器
12
6.2.1 基本类型
过程设备设计
优点
结构比较简单、价格便宜,承压能力强。 受弯管曲率半径限制,布管少; 管束最内层管间距大,管板利用率低; 壳程流体易短路,传热不利。 当管子泄漏损坏时,只有外层U形管可更 换,内层管只能堵死,坏一根U形管相当 于坏两根管,报废率较高。
过程设备设计
优点
——结构简单、紧凑、能承受较高的压力,造价
低,管程清洗方便,管子损坏时易于堵管或更换。
缺点
——当管束与壳体的壁温或材料的线膨胀系数相
差较大时,壳体和管束中将产生较大的热应力。 ——适用于壳侧介质清洁且不易结垢并能进行溶
应用
解清洗,管、壳程两侧温差不大或温差较大但壳 侧压力不高的场合。
过程设备设计
第六章 换热设备
6.1 概述 6.2 管壳式换热器 6.3 传热强化技术
6.2.1 基本类型 6.2.2 管壳式换热器结构
6.2.3 管板设计
6.2.4 膨胀节设计 6.2.5 管束振动和防止
1
过程设备设计
6.2 管壳式换热器
本章 重点
教学重点: 管壳式换热器结构。 教学难点: 管板设计、管束振动。
(c) (c) (c) (c) (c) (c) (c) (c)
(c)
(d) (d) (d) (d) (d) (d) (d) 37
(d) (d)
6.2.2 管壳式换热器结构
过程设备设计
特点
隔板
清洗时要拆除管线; 该结构适用于较清 洁的介质。
箱
(a)
38
换热器管箱
39
6.2.2 管壳式换热器结构
过程设备设计
隔板
隔板 隔板
隔板 箱盖
隔板 箱盖
隔板 隔板 隔板 隔板
隔板 隔板 箱盖 箱盖
隔板 隔板 管板 管板 隔板 管板 (1) 管板 (1) (1) (1)
隔板
(2) (2) (2) (2)
箱盖 箱盖 箱盖 箱盖
(a) (a)
(a) (a) (a) (a)
(a) ( (b) b)
(b) ( b) (b) (b) ( b (b) ) (b)
6.2.1 基本类型 6.2.2 管壳式换热器结构
6.2.3 管板设计
6.2.4 膨胀节设计 6.2.5 管束振动和防止
56
6.2.2 管壳式换热器结构
过程设备设计
6.2.2.2 壳程结构
2
管壳式换热器
3
6.2.1 基本类型
过程设备设计
6.2.1 基本类型 一、固定管板式
二、浮头式
三、U形管式 四、填料函式
五、釜式重沸器
4
6.2.1 基本类型
过程设备设计
一、固定管板式换热器
结构
(Байду номын сангаасa) BEM立 式 固 定 管 板 式 换 热 器
5
双管程固定管板换热器
6
6.2.1 基本类型
6.2.2.2 壳程结构
20
6.2.2 管壳式换热器结构
过程设备设计
一、换热管
光管 1.换热管型式 强化传热管 翅片管(在给热系数低侧)
螺旋槽管
螺纹管
φ19×2、φ25×2.5和φ38×2.5mm无缝钢管
2.换热管尺寸
φ25×2和φ38×2.5mm不锈钢管 标准管长1.5、2.0、3.0、4.5、6.0、9.0m等
21
6.2.2 管壳式换热器结构
过程设备设计
单位体积传热面积增大、结构紧凑、 金属耗量减少、传热系数提高 小管径 阻力大,不便清洗,易结垢堵塞 用于较清洁的流体
大管径
粘性大或污浊的流体
22
6.2.2 管壳式换热器结构
过程设备设计
3.换热管材料
碳素钢 低合金钢
不锈钢
金属材料 铜 铜镍合金 铝合金 钛等
管程
18
6.2.2 管壳式换热器结构
管程——与管束中流体相通的空间 壳程——换热管外面流体及相通空间
过程设备设计
管程
壳程
( a) BEM立 式 固 定 管 板 式 换 热 器
管程
19
6.2.2 管壳式换热器结构
过程设备设计
一、换热管
二、管板
6.2.2.1 管程结构
三、管箱 四、管束分程 五、换热管与管板连接
33
6.2.2 管壳式换热器结构