应用韧性断裂准则预测板料的成形极限图
材料的断裂和韧性PPT课件
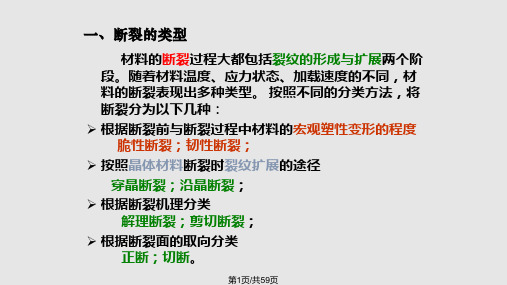
状态有关。其下标表示I型扩展类型,单位为Pa·m1/2。r
为半径向量, 为角坐标。
第30页/共59页
对于裂纹尖端处的一点,即r C,0,于是:
xx yy
KI
2 r
xy 0
(2.12)
在x轴上裂纹尖端的切应力分量为零,拉应力分量最 大,裂纹最易沿x轴方向扩展。
KI Y c KIc (2.14)
当 KI KIc 时,有裂纹,但不会扩展 破损安全
[]
许用应力: []= f / n 或 ys / n f 为断裂强度,ys 为屈服强度,n为安全系数。
缺点
没有抓住断裂的本质,不能防止低应力下的脆性断裂。
第35页/共59页
提出新的设计思想和选材原则,采用一个新的表征材料特征 的临界值:平面应变断裂韧性KIc,它也是一个材料常数,表示 材料抵抗断裂的能力,KIc越高,则断裂应力σc或临界裂纹尺寸 C越大。 根据应力场强度因子K和断裂韧度KIc的相对大小,可以建立裂 纹失稳扩展脆断的断裂K判据,即
一、断裂的类型
材料的断裂过程大都包括裂纹的形成与扩展两个阶 段。随着材料温度、应力状态、加载速度的不同,材 料的断裂表现出多种类型。 按照不同的分类方法,将 断裂分为以下几种: ➢ 根据断裂前与断裂过程中材料的宏观塑性变形的程度
脆性断裂;韧性断裂; ➢ 按照晶体材料断裂时裂纹扩展的途径
穿晶断裂;沿晶断裂; ➢ 根据断裂机理分类
2 r
cos
2
1
sin
2
sin
3
2
xy
KI cos sin cos 3 2 r 2 2 2
ij
KI
2r
一种新的板料成形极限预测判据
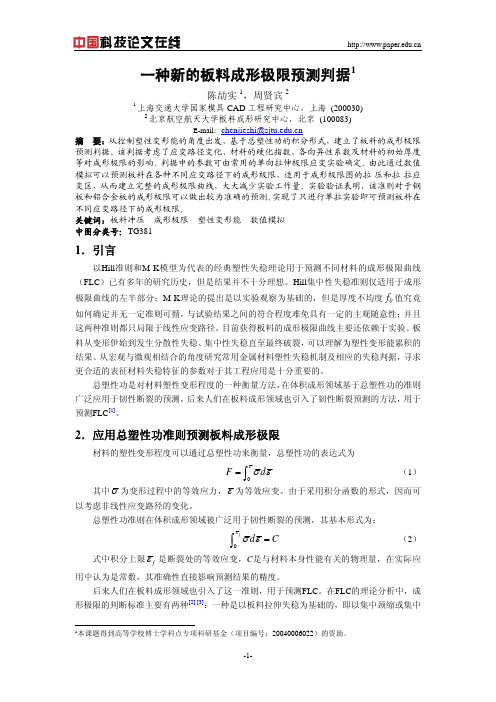
σs
(MPa)
r0
0.72 1.85 0.64
r45
1.21 1.52 0.65
r90
1.03 2.37 0.61
382.8 158.3 155.3
为节省计算时间,根据试件的对称性,只模拟四分之一试件的变形过程(图1) ,板料初 始网格划分为1mm的四边形壳单元。各种应变路径下的加载条件完全相同,板料与凹模以 及压边圈之间的摩擦系数均设为0.12,与凸模之间的摩擦系数为0.05[6],压边力为200kN,凸 模速度为10mm/ms, 模具尺寸与试验设备尺寸相同。 应变路径的变化通过改变试件尺寸来实 现,试件长度均为176mm,宽度从15mm至176mm递增。采用等向强化模型、Barlat89屈服 准则。
∫
εn
0
σ dε = C
(3)
其积分上限 ε n 为与破裂起始部位最接近,但不包含颈缩的椭圆的等效应变。 由于确定与常数C有关的材料参数需要大量的实验数据,而且是统计量,这种预测方法 不便于在工程中应用。在目前的应用中都是采用一些宏观试验数据来确定常数C。 A.M.Goijaerts[4]指出,如果确定常数C的实验加载条件与将要预测的成形过程的加载条件越 相近, 则预测的结果越与实验结果相符。 可是如果用与预测的成形过程完全相同的实验来确 定,这种方法对预测虽然具有很高的精度,但是实验相对很繁琐。目前常用的方法是用拉伸 实验法来确定,通过拉伸试样的极限应变等参数来求得准则中的材料常数。在实际应用中, 通常选取与准则中材料常数个数等同的拉伸变形实验, 并且应力状态不同, 来确定材料常数。 常用的工程方法有:单向拉伸实验,平面应变实验,等双拉实验等。 本文为确定材料常数C,采用了胀形实验中单向拉伸应变路径下的极限应变数据。为了 能够按照材料变形过程中的具体应变路径进行积分,本文采用冲压成形模拟软件Pam-Stamp 进行相同变形过程的数值模拟, 在模拟过程中当试件上第一主应变最大的单元达到此应变值 时,认为此处达到成形极限。然后将此单元的应力应变历史代入公式(3) ,计算材料常数。 采用这种方法确定材料常数的优点是可以按照单元真正的变形路径进行积分, 而不是简单的 假定为线性。 采用NUMISHEET’96[5]中提供的HS钢板、IF钢板和6111-T4铝合金板三种材料的力学性 能参数进行其成形极限实验过程的数值模拟。几种材料的材料力学性能参数见表1。
板料成形中韧性断裂准则应用研究进展

S a g a 0 0 0,Ch n ) h n h i2 0 3 ia
Ab ta t sr c :Thsp p ro e ve dt ep e it n meh d ff r n i i i h e t l o mi g, i a e v r iwe h r dci t o so o mig l t n s e tme a r n o m f whc n l d d f r n i i sr s ig a ,t ema i m o m ig t inn ai ih i cu e o mig l t te sda r m m h x mu f r n hn ig rto,f r n i t o mi g l mi da r m n u tl rc u ec i ra DFC) ig a a d d ci fa t r rt i ( e e .Th n t i p p rp i td o tt a C o l r dc e h s a e on e u h tDF c ud p e it t ef r n i to tls e twihl w lsii l a d me n i a et ec a g f o mi g h o mi gl mi fmea h e t o pa tct wel n a tmet k h h n eo r n y f p t t c o n .W h n a o tn a h i oa c u t n e d p ig FEA o mo e ,DF c u d n to l p l n o ic e n a p t d l C o l o n ya py it n r me t l — a p o c t ul o pe lsi n ls i d ma emo e ,b tt n t p i v re a p o c r a h wi a f lyc u ld ea tca d pa t a g d l u o o ese n e s p r a h. h c To a c r tl r dc o mig l t rt r n t e lc tra e f r n ei s e c si— c u aey p e itf r n i mi ,acie i o r fe tma e ilp ro ma c n e s n ewa n o d s e s be b sd sic e sn h ip n a l e ie n r a i gt eFEA d l c u a y mo e c r c . a Ke r s u t e fa t r rt ra;s e tm ea o mig;fr n i i;f i lm e tme h d ywo d :d ci r cu ec i i l e h e t lfr n o mig l t i t ee n t o m n e
金属塑性成形过程韧性断裂的准则及其数值模拟
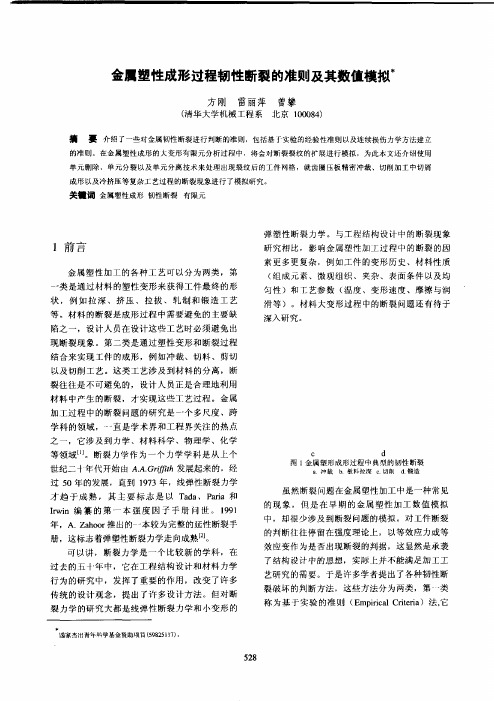
R e r y在1 9 es 9 年提出了三向应力作 i 和Tc l 6 c a ]
用下材料的韧性断裂准则为:
的应用。最后介绍作者对几个典型工艺模拟的结
果。
1 .
2韧性断裂准则
金属在加工过程中发生的断裂大多是韧性断 裂,很少发生脆性断裂。一般认为,金属中的韧
Kc nv 1 8 a a 在 9 年首先提出的另一种分析方 ho 5
法。这种研究方法主要是从细观 ( e s l m s ce oa) 的角度进行研究,对空洞的萌生和扩展角度进
行预测,建立空洞萌生准则。因为韧性断裂的
调整,局部调整还包括单元删除 ( e tn D l o)、 e i
50 3
截
国家杰出青年科学基金资助项目( 851) 5 21 . 9 7
58 2
主要是通过标准的常规实验来获取材料的实验数 据,然后用于对材料成形过程中的韧性断裂的判 断上,它还分二种,即应力、应变和应变能准 则,这类准则的代表是 C cr t a a 准则。 ok fLt m o- h 从所分析的尺度和方法上讲,它属于宏观断裂力 学的范畴。这种方法的缺陷是简单的力学实验条
申
虽然断裂问题在金属塑性加工中是一种常见 的现象,但是在早期的金属塑性加工数值模拟 中,却很少涉及到断裂问题的模拟。对工件断裂 的判断往往停留在强度理论上,以等效应力或等 效应变作为是否出现断裂的判据,这显然是承袭 了结构设计中的思想,实际上并不能满足加工工 艺研究的需要。于是许多学者提出了各种韧性断 裂破坏的判断方法,这些方法分为两类,第 类 称为基于实验的准则 (m i a Cir ) 它 E pi l ea 法, r c r i t
世纪二十年代开始由A .r h .G咖t发展起来的, A 经
成形极限图的测试-应用和可信度分析

1 引言
汽车和摩托车的许多零件如覆盖件 、油箱等都 是用薄钢板冲压成形的 , 在冲压零件的选材和制定 冲压工艺时常常用到成形极限图 。
成形极 限图(Forming Limit Diagrams)也称成 形极限曲线(Forming Limit Curves), 常 用 FL D 或 F LC 表示 。成形极限图是 判断和评定金属薄板成 形性的最为简便和直观的方法 , 是对板材成形性能 的一种定量描述 , 是解决板材冲压问题的一个非常 有效的工具 , 同时也是对冲压工艺成败性的一种判 断曲线 。相对于通常使用的基本成形性能指标(σs , σb 和 δ)及杯突值而言 , 成形极限图可以较好地反
· 498 ·
图 4 成形极限图
图 5 成形极限曲线
说明模拟计算 F LC 具有较高的可信度 。 将极限应 变分布条带的上限连成曲线 , 所得实际测量 F LC 应 变值均大于模拟计算应变值 2 %~ 8 %。 因为实际 测量的极限应变值是板材出现颈缩或破裂附近的应 变 , 在实际使用中不应超过该值 , 所以使用模拟计算 的 F LC 进行冲压零件选材预测是较为安全的 , 模拟 计算 F LC 可以应用于实际分析 。 在使用实际测量 F LC 时 , 如 F LC 为极限应变分布条带的上限 , 选材 预测时应取较大的安全裕度 ;如 F LC 为极限应变分 布条带的平均值 , 选材预测时可取较小的安全裕度 ; 如 F LC 为极限应变分布条带的下限 , 选材预测时所
成形极限图的测试应用和可信度分析形特点的材料性能这是非常重要的问题对多种冷轧钢板的成形极限图进行了测试并与动应变测试分析系统模拟计算的成形极限曲线作了比较应用成形极限图对胀形类和拉深类实物冲压零件进行选材预测对应用成形极限图选材预测的可信度作了分析d0d1胀形状态网格圆的三种畸变状态成形极限图测试原理成形极限图可以用实验测试得到gbt158251995对试验方法作了规定自动应变测试分析系统根据有关的经验公式模拟计算出来实验测试实验测试fl试验时先在试样表面印制标准的圆网格然后将不同宽度的试样分别置于凹模与压边圈之间利用压边力压紧拉深筋以外的试样材料使之不产生材料的流动试样中部在凸模力作用下产生胀形变形并形成凸包见图测量缩颈区或破裂区附近的网格圆长轴和短轴尺寸由此计算金属薄板允许的局部表面极限应变ln100ln100为横向坐标建立表面应变坐标系
韧性断裂PPT课件
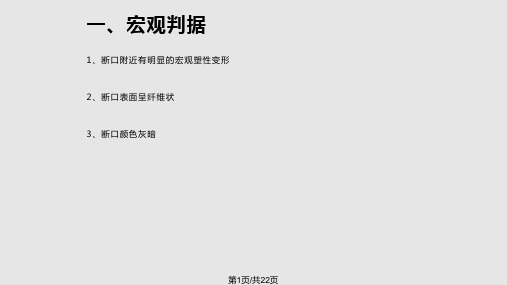
多个微裂纹通过滑移长大、聚集 连接,扩展过程需要消耗大量能 量
宏观:平行于最大剪切应力或垂 直于最大主应力方向 微观:穿晶
通过滑移变形慢速扩展
沿晶分离(可能伴有微量塑性 变形),或沿一定晶面快速劈 开,扩展过程只需要很少能量 宏观:垂直于正应力 微观:沿晶、解理
通过沿晶分离或解理快速扩展
断裂控制因素 应变控制 ε> εf
应力控制 σ> σf
第20页/共22页
项目
断口形态
断口颜色 塑性变形
断裂原因
韧性断裂和脆性断裂的比较
韧性断裂
脆性断裂
宏观:纤维状 微观:蛇形滑移、涟波、延伸、 韧窝
粗糙、灰暗
宏观:放射状(人字纹)、颗粒 状
微观:解理扇形、河流、舌状花 样、沿晶韧窝、岩石状
细瓷状、光亮
伴有大量塑性宏观变形:拉伸— —缩颈,扭转——扭角,冲击— —转角,弯曲——挠度,压缩— —镦粗
2)纤维区是断裂过程中某瞬间的裂纹前沿, 各排纤维的法线方向代表裂纹扩展方向,沿此 方向可以找到冲击力作用点。
3)微观上成撕裂型韧窝,匹配断口上韧窝 弯曲方向相同,且被拉长。
第16页/共22页
4、压缩
1)断口为剪切型。 2)裂纹走向与正应力成45°。 3)微观断口上出现半弧形韧窝,匹配断口 上弯曲方向相反。
过载或强度不足
无宏观塑性变形
材质:白点、分层、夹杂 工艺:过热、过烧、回火脆、焊 接脆、时效脆等 环境:应力腐蚀、氢脆、低温脆 应力:低应力脆断、应力状态过 硬引起的脆断
第21页/共22页
感谢您的观看!
第22页/共22页
不同形状的韧窝 第11页/共22页
无夹杂韧窝
有夹杂韧窝 第12页/共22页
应用韧性断裂准则预测盒形件拉深成形极限
应用韧性断裂准则预测盒形件拉深成形极限
杨玉英;于忠奇;王永志;孙振忠
【期刊名称】《哈尔滨工业大学学报》
【年(卷),期】2004(036)011
【摘要】目前已提出的韧性断裂准则预测板料成形极限,只在简单轴对称件中得到应用.利用作者提出的韧性断裂准则预测了铝合金板LF21,LY21(M)和钢板st17非轴对称的方盒件拉深成形极限,并与成形极限图的预测结果和实验结果进行比较.结果表明,这种方法较好地预测了盒形件拉深成形极限,为预测非轴对称件成形的断裂发生提供了一种有效的方法,也为预测复杂形状零件成形极限奠定了基础.
【总页数】4页(P1507-1510)
【作者】杨玉英;于忠奇;王永志;孙振忠
【作者单位】哈尔滨工业大学,材料科学与工程学院,黑龙江,哈尔滨,150001;哈尔滨工业大学,材料科学与工程学院,黑龙江,哈尔滨,150001;哈尔滨工业大学,材料科学与工程学院,黑龙江,哈尔滨,150001;哈尔滨工业大学,材料科学与工程学院,黑龙江,哈尔滨,150001
【正文语种】中文
【中图分类】TG386
【相关文献】
1.成形极限预测韧性断裂准则及屈服准则的影响 [J], 陈劼实;周贤宾
2.应用专家系统进行盒形件拉深成形极限的分析 [J], 郑晓丹;汪锐;何丹农
3.基于神经网络和遗传算法的板材韧性断裂准则参数优化及成形极限预测 [J], 董国疆;陈志伟;赵长财;李潇逸;杨卓云
4.应用韧性断裂准则预测不同材料的胀形极限 [J], 于忠奇;杨玉英;孙振忠
5.应用韧性断裂准则预测板料的成形极限图 [J], 余心宏;翟妮芝;翟江波
因版权原因,仅展示原文概要,查看原文内容请购买。
abaqus损伤准则总结
abaqus损伤准则总结ABAQUS中有四种初始断裂准则:在⾼应变速率下变形时,有shear failure和tensile failure(旋压⽤不到,不再介绍)对于断裂延性⾦属:可以选⽤A:韧性准则(ductile criteria)和B:剪切准则(shearcriteria)对于缩颈不稳定性可以使⽤(钣⾦):C:FLD、FLSD、M-K以及MSFLD对于铝合⾦、镁合⾦以及⾼强钢在变形过程中会出现不同机制的断裂,可能会将以上准则联合起来进⾏使⽤。
损伤的感念如下图所⽰:1.韧性断裂准则中提供的韧性断裂准则需要输⼊的参数为:1.1ABAQUS断裂应变;应⼒三轴度;应变速率要测量不同应⼒三轴度下的断裂应变需要进⾏⼤量的实验,这是不可取的。
Hooputra et al,2004通过实验和理论推导得到了在定应变速率下,断裂应变和应⼒三轴度的关系:公式中::应⼒三轴度。
即平均应⼒和屈服应⼒的⽐值;为等双轴拉伸时的应⼒三:等双轴拉伸时,断裂时的等效塑性应变,轴度,其值为2/3;为等双轴压缩时的应:等双轴压缩时,断裂时的等效塑性应变,⼒三轴度,其值为-2/3;因此,为了得到断裂时等效塑性应变和应⼒三轴度的关系,只需要求出和参数三个参数即可。
根据⽅程已得到不同应⼒三轴度下的断、裂应变。
、和在⼀个应变速率下只需要三组数据,就可以求出⽅程中的。
帮助⽂件中的建议:ABAQUS==2/3⽅程⼀(是不是:例如在杯突试验中,应⼒三轴度为已知量杯突实验和等双轴拉伸的变形时等效的,杯突实验如何在⾼温下进⾏,能否⽤双向拉伸实验代替?)=此时,通过对进⾏杯突实验的板料印制⽹格,可以得到其成形极限(。
):例如三点弯曲试验中,应⼒三轴度为已知量(印制⽅程⼆=0.57735。
⽹格测量,具体如何测量不是很清楚):例如在单轴拉伸实验中,应⼒三轴度为已知量=0.333⽅程三。
平均应⼒为屈服应⼒的三分之⼀。
SIMUWE论坛中的建议:这个应该通过单轴拉伸实验、压缩实验和纯剪切实验。
板料成形极限理论与实验研究进展
第13卷第5期2006年10月塑性工程学报JOURNALOFPLASTICITYENGINEERINGV01.13No.5Oct.2006板料成形极限理论与实验研究进展*(北京航空航天大学机械工程及自动化学院,北京100083)韩非万敏吴向东摘要:成形极限是板材成形领域中重要的性能指标和工艺参数。
文章在阐述成形极限在板料成形中的意义的基础上,综述并分析了成形极限在理论和实验方面的研究进展。
成形极限图受应变路径的影响,给工业生产应用带来极大不便。
以极限应力构成的成形极限应力图不受应变路径的影响,作为复杂加载路径的成形极限判据更加方便和实用。
FLsD研究与FLD相结合,成为精确地确定破裂判别准则的主要途径之一,是近来研究的热点。
十字形双向拉伸是实现复杂加载路径有效实用的试验方法。
最后对成形极限应力图和十字形双向拉伸试验需要解决的关键问题作了阐述。
关键词:板料成形;成形极限;成形极限应力图;复杂加载路径;十字形双向拉伸试验中图分类号:TG386文献标识码:A文章编号:1007—2012(2006)05—0080一07引言成形极限是板材成形领域中重要的性能指标和工艺参数,反映了板材在塑性失稳前所能取得的最大变形程度。
为确定板材拉伸失稳的成形极限,人们从理论和实验等方面提出了许多研究与评价方法,其中最有现实意义和应用最为广泛的是20世纪60年代由Keelercl]和GOOdwin[2]提出的以极限应变构成的成形极限图(forminglimitdiagram,FLD)的概念。
FLD为方便研究板材成形极限、评价板材成形性能及解决板材成形领域中众多难题提供了技术基础和实用判据。
通常由标准实验确定的FLD都是由线性或近似线性的应变路径得到的。
在实际生产中,应变路径通常偏离线性路径。
因此,由简单应变路径建立的FLD并不能准确预测破裂的发生,必须采用与实际成形相符的复杂应变路径所建立的FLD作为破裂判据。
研究复杂应变路径对FLD的影响规律一直是板料成形领域主要的研究内容[3]。
第7章板料成形性能与成形极限ppt课件
图7-8 网格圆畸变
.
根据测量结果,计算试样表面极限应变。
e1
d1 d0 d0
100
%
e2
d2 d0 d0
100
%
1
ln
d1 d0
ln(1
e1
)
2
ln
d2 d0ຫໍສະໝຸດ ln(1 e2 ).
如图7-9,以表面应变e2(或ε2)为横坐标、表面应变e1〔或ε1〕 为纵坐标,建立表面应变坐标系。在e1-e2坐标系中,习惯将e1 和e2分度比例为1:2,而在ε1-ε2坐标系中两者分度一般相同。 将试验测定表面极限应变量〔e1、e2〕或〔ε1、ε2〕标绘在表 面应变坐标系中。
第7章 板料成形性能与成形极限
.
板料成形性能是指板料对各种成形工 艺的适应能力。
板料成形性能主要包括成形性能、贴 模性能和定形性能。其总体构成所谓综合 成形性能,也叫做广义成形性能。其中成 形性能〔抗破裂性能〕可视为狭义的冲压 成形性能,它是目前生产中作为评定板料 冲压成形性能的主要指标。
.
贴模性能是指板料在冲压成形中取得模具 形状的能力。制件出现折皱、翘曲、塌陷和鼓 起等几何面缺陷均会使贴模性能降低。定形性 能是指制件脱模后保持其在模内既得形状的能 力,故亦称冻结性能。制件出现尺寸误差与形 状误差使定形性降低,回弹是影响板料定形性 的最主要因素。
如图76二维应变坐标系中用不同应变路径下表面极限应变量连成曲线或勾画出条带形区域称为成形极限曲线forminglimitcurve缩写flc极限应变量与极限曲线共同构成成形极限图forminglimitdiagram缩写fld23图76成形极限图fld242成形极限图fld试验将一侧表面制有网格的试样臵于凹模与压边圈之间压紧拉深筋以外的材料试样中部在外力作用下产生变形见图77其表面上的网格圆发生变形当某个局部产生缩颈或破裂时停止试验测量缩颈区或破裂区附近的网格圆长轴和短轴尺寸计算板料允许的局部表面极限主应变量e25图77试验简图26下述两种方法可获得不同应变路径下表面极限主应变
- 1、下载文档前请自行甄别文档内容的完整性,平台不提供额外的编辑、内容补充、找答案等附加服务。
- 2、"仅部分预览"的文档,不可在线预览部分如存在完整性等问题,可反馈申请退款(可完整预览的文档不适用该条件!)。
- 3、如文档侵犯您的权益,请联系客服反馈,我们会尽快为您处理(人工客服工作时间:9:00-18:30)。
F( y - z ) 2 + G( z - x ) 2 + H ( x - y) 2 +
2L
2 yz
+
ቤተ መጻሕፍቲ ባይዱ
2M
2 zx
+
2N
2 xy
-
1=
0
( 7)
式中 x 、 y 、 z # # # 拉伸屈服应力 ( MP a)
xy 、 yz 、 z x # # # 剪切屈服应力 ( M Pa)
F、G、H 、L 、M、N # ## 与屈服应力有关
比值 在整个单向拉伸和平面拉伸测试的过程中可
1
分别表示为:
3 韧性断裂准则及材料常数的确定
引入韧性断裂准则要解决两个问题: 准则的结 构及其常数的确定, 它们直接影响预测和分析结果 的正确性。
冲压时板料变形区处于三向压应力状态, 材料 在狭窄的凸、凹模间隙附近形成了局部的塑性剪切
m = 1 2( 2+ r ) = 2( 2 + r ) ( 单向拉伸) ( 5)
- 应变曲线。两种材料的应力- 应变可分别描述为:
A 5182 O : = 570( 0 0011+ ) 0 21
( 1)
M ild st eel: = 625( 0 0069 + ) 0 23 ( 2)
式中 # # # 等效应力 ( MP a)
# # # 等效应变
表 1 材料拉伸性能
Table 1 Tensile properties of the materials
的异性参数
图 2 各向异性系数对单向拉伸和平面拉伸 应力、应变比的影响
Fig 2 Ef fect of normal anis ot ropy param et er on t he st ress an d st rain rat io of uniaxial t ensil e and plan st rain s tr et chin g
YU Xin hong, ZHAI Ni zhi, ZHAI Jiang bo ( Department of M at erials Science and Eng ineering , N or thwestern P olytechnical U niver sity, Xi an 710072, China)
成形极限图的实验确定方法根据试件受力方式 的不同主要分为两种, 如图 1 所示。一种是使用圆 柱型扁平冲头深拉延的 平板面法![ 5] ( 图 1a) ; 另 一种 是 使用 半 球 型冲 头 胀 形 的 曲 面 法![ 6] ( 图 1b) , 但后者比前者应用更 加广泛。本文 尝试用实 验和模拟相结合的方法获得 F L D, 先通过实验测得 相关的材料参数, 再用软件 EAT / dy naf orm 模拟半 球型冲头胀形 实验, 得到随 时间历史变化 的应力、 应变值, 代入韧性断裂准则找出破裂点, 绘制 F LD 图。
∃f 1+ a m d = C 0
( 3)
2 材料本构关系
测试材料为铝合金板 A5182 O 和 SPCC, 厚度
d= 1 0 m m。表 1 是这两种材料标准单向拉伸测试
测得的材料性能参数, 其值为与扎制方向成 0∀、45∀、
90∀三个方向的平均值。其中强度系数 F、屈服应力
s 、应变硬化指数 n 用来描述材料本构关系, 即应力
带, 经历了弹塑性变形、剧烈的塑性变形和韧性断 裂。从微观角度来说, 材料在大变形下会出现损伤, 伴随着微观空穴的长大和聚合, 直至许多空穴聚集 在一起产生裂纹, 引起韧性断裂。所以, 韧性断裂 准则 也 既 是 一 种 损 伤 断 裂 准 则。 M c Clint ock、 Cockcrof t 和 L atham、Br ozzo 等人都提出了损伤断 裂准则[ 7] , 但这些准则均未考虑金属大变形的影响, 在实际应用中有较大局限性。Oy ane 等[ 8] 考虑到静 水应力可以抑制或加速韧性破坏, 不仅能定量地表 示瞬时的损伤状态, 更体现了加载过程中整个应力 - 应变历史对材料的劣化效应。假定韧性损伤达到 一定值时破裂发生, 提 出了 ( 3) 式 的 Oy ane 损伤 断裂准则, 应用较 广的是其 整化的 ( 4) 式 Oy ane 韧性断裂准则, 本文也 用的是 ( 4) 式 Oy ane 韧性 断裂准则进行成形极限图的预测。
第 32 卷 第 5 期 V ol 32 N o 5
锻压技术
FORGING & STAMPING TECHNOLOGY
2007 年 10 月 Oct. 2007
应用韧性断裂准则预测板料的成形极限图
余心宏* , 翟妮芝, 翟江波
( 西北工业大学 材料科学与工 程学院, 陕西 西安 710072)
摘要: 将 O yan 韧性断裂准则引入数值模拟预 测板料 的成形极 限图 ( FL D) 。讨论了 各向异 性系数 对不同 应变状 态
杨氏 材料 模量/
GP a A5182 O 69 6
强度 系数/ MPa 570
应变硬 各向异 屈服强 拉伸
化指数 性系数 度 s/ 强度/
n
r
MPa MPa
0 21 0 93 135 285
延伸 率/ %
21 9
S PCC 207 625 0 23 1 17 199 346 36 6
∃f m + C1 d = C2 0
( 4)
式中 f # # # 断裂发生处的等效应变 m # # # 静水应力 ( MP a)
C # # # 裂纹出现时的临界损伤值
a、C1 、C2 # # # 材料常数
材料常数至少需要两种应变条件下的破裂应变
才能确定。表 2 是单向拉伸和平面拉伸实验的颈缩 部位测得的断裂应变[ 3, 5] 。
表 2 材料 的断裂应变
Abstract: T o predict the form ing limit diag rams ( FL D) of sheet metals, Oyan ductile fracture crit er io n w as intr oduced into numerical simulatio n. T he inf luence o f nor mal aniso tro pic coefficient on the item in different str ains of the cr iterion w ere discussed and mater ial constants in the cr iterion w ere o btained by testing the fr actur e str ains of uniax ial t ensile and plan str ain st retching . T he fo rming limit w as predicted in t he male punch bulging t est by substituting the v alues o f stress and strain o f every time step o bt ained fro m numer ical simulation into ductile fracture cr iter ion. O yan ductile fractur e cr iterion was applied to predict the FL D of A 5182 O and SP CC. T he results indicate t hat the combinat ion o f ductile fracture cr iterion and numer ical simulat ion can successfully predict the form ing limit diag ram o f sheet metals. Keywords: for ming limit diag ram; duct ile fr act ur e criter ion; numer ical simulation
第5期
余心宏等: 应用韧性断裂准则预测板料的成形极限图
45
图 1 成形极限图实验装置 ( a) In plane 测试装置 ( b) O ut of plane 测试装置 Fig 1 Ex perim ent equipm ent of form ing l imit diagrams ( a) In plane t est ing equipment ( b) Out of plane t esting equipment
图。
关键词: 成形极限图; 韧性断裂准则; 数值模拟
中图分类号: TG386 41
文献标识码: A
文章编号: 1000 3940 ( 2007) 05 0044 04
Predicti on of sheet metal forming limi t diagram by applying ductile fracture criterion
1 引言
板料冲压成形过程是一个涉及材料非线性、几 何非线 性 和 复 杂 接 触 摩 擦状 况 的 大 变 形 力 学 过 程[ 1, 2] , 其变形的复杂 性使得断裂等 板料失效的准 确预测变的困难。断裂预测最常用的是 20 世纪 60 年 代 Keeler 和 Backof en 提 出 的 成 形 极 限 图 ( F L D) 。但想要得到各种板料的成形极限图, 靠人 工实验工作重、耗时长、耗材多、花费高, 且应变 路径是 近 线 性, 与 实 际 生 产 差 异 较 大。 传 统 的 Sw ift 、H il l、M K 沟槽! 以及 S R 理论模型虽然 是板材成形极限预测的有效工具, 但都不能准确预 测塑性差、破裂时无明显颈缩现象的铝合金板。因 此, 需要一种合适的成形极限准则正确分析成形过 程, 而源自于韧性损伤理论的韧性断裂准则正是预 测板料成形极限的一种有效方法。各国学者在各种 假设的基础上已提出多种韧性断裂准则, 其中应用