《金属切削原理》第章[磨削]
《金属切削原理与刀具》知识点总结
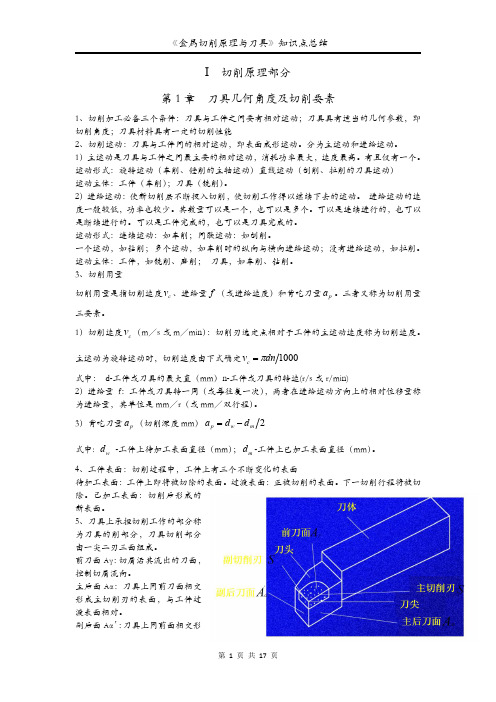
I 切削原理部分第1章刀具几何角度及切削要素1、切削加工必备三个条件:刀具与工件之间要有相对运动;刀具具有适当的几何参数,即切削角度;刀具材料具有一定的切削性能2、切削运动:刀具与工件间的相对运动,即表面成形运动。
分为主运动和进给运动。
1)主运动是刀具与工件之间最主要的相对运动,消耗功率最大,速度最高。
有且仅有一个。
运动形式:旋转运动(车削、镗削的主轴运动)直线运动(刨削、拉削的刀具运动)运动主体:工件(车削);刀具(铣削)。
2)进给运动:使新切削层不断投入切削,使切削工作得以继续下去的运动。
进给运动的速度一般较低,功率也较少。
其数量可以是一个,也可以是多个。
可以是连续进行的,也可以是断续进行的。
可以是工件完成的,也可以是刀具完成的。
运动形式:连续运动:如车削;间歇运动:如刨削。
一个运动,如钻削;多个运动,如车削时的纵向与横向进给运动;没有进给运动,如拉削。
运动主体:工件,如铣削、磨削;刀具,如车削、钻削。
3、切削用量切削用量是指切削速度c v 、进给量f (或进给速度)和背吃刀量p a 。
三者又称为切削用量三要素。
1)切削速度c v (m/s 或m/min):切削刃选定点相对于工件的主运动速度称为切削速度。
主运动为旋转运动时,切削速度由下式确定1000dn v c π=式中:d-工件或刀具的最大直(mm)n-工件或刀具的转速(r/s 或r/min)2)进给量f:工件或刀具转一周(或每往复一次),两者在进给运动方向上的相对位移量称为进给量,其单位是mm/r(或mm/双行程)。
3)背吃刀量p a (切削深度mm)2m w p d d a -=式中:w d -工件上待加工表面直径(mm);m d -工件上已加工表面直径(mm)。
4、工件表面:切削过程中,工件上有三个不断变化的表面待加工表面:工件上即将被切除的表面。
过渡表面:正被切削的表面。
下一切削行程将被切除。
己加工表面:切削后形成的新表面。
5、刀具上承担切削工作的部分称为刀具的削部分,刀具切削部分由一尖二刃三面组成。
金属切削原理第1章

主讲 尚晓峰
一、本课性质:专业基础课
二、本课主要任务(三点) 1. 掌握金属切削过程一般现象和基本规律; 2. 初步掌握金属切削实验研究的基本方法和技能; 3. 初步了解本学科的发展趋势和成就。 三、金属切削在机械制造中的重要作用 1. 机械制造技术发展必然影响国民经济发展; 2. 切削加工在21世纪仍将占机械加工量的90%; 3. 机械制造自动化和精密加工发展。
沿进给运动方向上的相对位移
单位: mm/r
v f = fn / 60 = nf z Z / 60 v f 进给速度(mm / s或mm/min); n 刀具每分钟转数(r/min); Z 刀具的齿数; f z 每齿进给量(mm/z)
(3)切削深度ap :指待加工表面与已加工表面
的垂直距离(单位mm)。
动方向。
切削速度 vc: 切削刃选定点相对于工件的主运动的
瞬时速度。
进给动方向 : 切削刃选定点相对于工件的瞬时进给
运动方向。
进给速度 vf:
切削刃选定点相对于工件的进给运动 的瞬时速度。
主运动、进给运动和合成切削运动示意图
切削运动与切削表面示意图
各种切削加工的工作运动 Ⅰ—主运动;Ⅱ—进给运动
待加工表面:即将被切除的工件表面; 已加工表面:已经被切除的工件表面; 过渡表面(切削表面):正在形成。
待加工表面 过渡表面 已加工表面
进给 运动
车削外圆时的加工表面
车削外圆时的加工表面
车削内孔时的加工表面
二、主运动、进给运动和合成切削运动
工作运动:
机床为实现切削加工所必须具有的 加工工具与工件间的相对运动。 包括:Ⅰ—主运动和Ⅱ—进给运动
《金属切削基础原理》第12章[磨削]
![《金属切削基础原理》第12章[磨削]](https://img.taocdn.com/s3/m/fe77a2cf33687e21af45a9c5.png)
第十二章磨削磨削用于加工坚硬材料及精加工、半精加工内圆磨削外圆磨削平面磨削普通平面磨削圆台平面磨削超精磨削加工第一节砂轮的特性及选择砂轮由磨料、结合剂、气孔组成特性由磨料、粒度、结合剂、硬度、组织决定一、磨料分为天然磨料和人造磨料人造磨料氧化物系刚玉系(Al2O3)碳化物系碳化硅系碳化硼系超硬材料系人造金刚石系立方氮化硼系二、粒度表示磨粒颗粒尺寸的大小>63µm号数为通过筛网的孔数/英寸(25.4mm)机械筛分一般磨粒<63µm号数为最大尺寸微米数(W)显微镜分析法微细磨粒精磨细粒降低粗糙度粗磨粗粒提高生产率高速时、接触面积大时粗粒防烧伤软韧金属粗粒防糊塞硬脆金属细粒提高生产率国标用磨粒最大尺寸方向上的尺寸来表示三、结合剂作用:将磨料结合在一起,使砂轮具有必要的强度和形状1、陶瓷结合剂(A)常用由黏土等陶瓷材料配成特点:粘结强度高、耐热、耐酸、耐水、气孔率大、成本低、生产率高、脆、不能承受侧向弯扭力2、树脂结合剂(S)切断、开槽酚醛树脂、环氧树脂特点:强度高、弹性好、耐热性差、易自砺、气孔率小、易糊塞、磨损快、易失廓形、与碱性物质易反应、不易长期存放3、橡胶结合剂(X)薄砂轮、切断、开槽、无心磨导轮人造橡胶特点:弹性好、强度好、气孔小、耐热性差、生产率低4、金属结合剂(Q)磨硬质合金、玻璃、宝石、半导体材料青铜结合剂(制作金刚石砂轮)特点:强度高、自砺性差、形面成型性好、有一定韧性四、硬度在磨削力作用下,磨粒从砂轮表面脱落的难易程度分为超软、软、中软、中、中硬、硬、超硬工件材料硬砂轮软些防烧伤工件材料软砂轮硬些充分发挥磨粒作用接触面积大软砂轮精度、成形磨削硬砂轮保持廓形粒度号大软砂轮防糊塞有色金属、橡胶、树脂软砂轮防糊塞五、组织磨粒、气孔、结合剂体积的比例关系分为:紧密(0~3)、中等(4~7)、疏松(8~14)(磨粒占砂轮体积%↘)气孔、孔穴开式(与大气连通)占大部分,影响较大闭式(与大气不连通)尺寸小、影响小开式空洞型蜂窝型前两种构成砂轮内部主要的冷却通道管道型5~50µm六、砂轮的型号标注形状、尺寸、磨料、粒度号、硬度、组织号、结合剂、允许最高圆周线速度P300x30x75WA60L6V35外径300,厚30,内径75第二节磨削运动一、磨削运动1、主运动砂轮外圆线速度 m/s2、径向进给运动进给量fr 工件相对砂轮径向移动的距离间歇进给 mm/st 单行程mm/dst 双行程连续进给 mm/s3、轴向进给运动进给量fa 工件相对砂轮轴向的进给运动圆磨 mm/r平磨 mm/行程4、工件速度vw线速度 m/s二、磨削金属切除率ZQ=Q/B=1000·vw·fr·fa/B mm^3/(s·mm)ZQ:单位砂轮宽度切除率Q:每秒金属切除量用以表示生产率B:砂轮宽度三、砂轮与工件加工表面接触弧长lc=sqrt(fr·d0)影响参加磨削磨粒数目及磨粒负荷,容屑,冷却条件四、砂轮等效直径将外圆(内圆)砂轮直径换算成接触弧长相等的假想平面磨削的砂轮直径结论:对砂轮耐用度影响内圆>平面>外圆第三节磨削的过程一、单个磨粒的磨削过程磨粒的模型锐利120°圆锥钝化半球实际磨粒:大的负前角,大的切削刃钝圆半径滑擦、耕犁、切削滑擦:(不切削,不刻划)产生高温,引起烧伤裂纹耕犁:(划出痕迹)磨粒钝或切削厚度小于临界厚度,工件材料挤向两侧隆起切削:切削厚度大于临界厚度,形成切屑v↑→隆起↓(线性)塑性变形速度<磨削速度二、磨削的特点1、精度高、表面粗糙度小高速、小切深、机床刚性2、径向分力Fn较大多磨粒切削3、磨削温度高磨粒角度差、挤压和摩擦、砂轮导热差4、砂轮的自砺作用三、磨削的阶段1、初磨阶段实际磨深小于径向进给量2、稳定阶段实际磨深等于径向进给量3、清磨阶段实际磨深趋向于0提高生产率缩短1、2提高质量保证3第四节磨削力及磨削功率一、磨削力的特征分解成三个分力Ft切向力 Fn法向力 Fa轴向力特征:1、单位切削力k很大磨粒几何形状的随机性和参数的不合理性7000~20000kgf/mm^2 其他切削方式k<700kgf/mm^22、Fn值最大Fn/Ft 通常2.0~2.5工件塑性↓、硬度↑→Fn/Ft↑切深小,砂轮严重磨损 Fn/Ft 可达5~103、磨削力随磨削阶段变化初磨、稳定、光磨二、磨削力及磨削功率摩擦耗能占相当大的比例(70~80%)切向力(N):Ft=9.81·(CF·(vw·fr·B/v)+µ·Fn)径向力(N):Fn=9.81·CF·(vw·fr·B/v)·tan(α)·(π/2) vw:工件速度v:砂轮速度fr:径向进给量B:磨削宽度CF:切除单位体积切屑所需的能 kgf/mm^2µ:工件-砂轮摩擦系数α:假设粒度为圆锥时的锥顶半角磨削功率P=Ft·v/1000 Kw理论公式精度不高,常用实验测定(顶尖上安装应变片)第五节磨削温度耕犁、滑擦和形成切屑的能量全部转化成热,大部分传入工件一、磨削温度砂轮磨削区温度θA:砂轮与工件接触区的平均温度影响:烧伤、裂纹的产生磨粒磨削点温度θdot:磨粒切削刃与切屑接触部分的温度温度最高处,是磨削热的主要来源影响:表面质量、磨粒磨损、切屑熔着工件温升:影响:工件尺寸、形状精度受影响二、影响磨削温度的因素切削液为降温的主要途径1、工件速度对磨粒磨削点温度的影响大于砂轮速度vw↑→acgmax↑→F↑→θdot↑大v↑→acgmax↓→θdot↑小→摩擦热↑↗acgmax:单个磨粒最大切削厚度 mm假设:磨粒前后对齐,均匀分不在砂轮表面平面磨:acgmax=(2·vw·fa/(v·m·B))sqrt(fr/dt)外圆磨:acgmax=(2·vw·fa/(v·m·B))sqrt((fr/dt)+(fr/dw))dt:砂轮直径m:每毫米周长磨粒数用于定性分析2、径向进给量Frfr↑→acgmax↑→θdot↑fr↑→接触区↑→同时参加切削磨粒数↑→θA↑3、其他因素fa↑→θdot↑、θA↑工件材料硬度↑、强度、↑韧性↑→θdot↑、θA↑θA↑→工件温升↑vw↑→被磨削点与砂轮接触时间↓→工件温升↗三、磨削温度的测量(热电偶)第六节砂轮的磨损及表面形貌一、砂轮的磨损类型磨耗磨损磨粒磨损破碎磨损磨粒或结合剂破碎(取决于磨削力与磨粒、结合剂强度)破碎磨损消耗砂轮多磨耗磨损通过磨削力影响破碎磨损阶段初期磨损磨粒破碎磨损(个别磨粒受力大,磨粒内部应力与裂纹)二期磨损磨耗磨损三期磨损结合剂破碎磨损二、砂轮的耐用度T砂轮相邻两次修整期间的加工时间 s各因素通过平均切削厚度来影响T经验公式:T=6.67·(dw^0.6)·km·kt/(10000·(vw·fa·fr)^2)dw:工件直径kt:砂轮直径修正系数km:工件材料修正系数粗磨时间常用单位时间内磨除金属体积与砂轮磨耗体积之比来选择砂轮三、砂轮的修整作用去除钝化磨粒或糊塞住的磨粒,使新磨粒露出来增加有效切削刃,提高加工表面质量工具单颗金刚石、单排金刚石、碳化硅修整轮、电镀人造金刚石滚轮、硬质合金挤压轮等使用单颗金刚石:导程小于等于磨粒平均直径,每颗磨粒都能修整深度小于等于磨粒平均直径,提高砂轮寿命四、表面形貌单位面积上磨粒数目越多→acgmax↓→磨粒受力↓→磨粒寿命↑→T↑磨粒高度分布越均匀→粗糙度↓磨粒间距均匀性越好→粗糙度↓第七节磨削表面质量与磨削精度一、表面粗糙度比普通切削小小于 Ra2~4µmvw↓、v↑、R工↑、R砂↑、细粒度→粗糙度↓细粒度→m↑→粗糙度↓B↑→acgmax↓→粗糙度↓磨粒等高性好→粗糙度↓二、机械性能1、金相组织变化烧伤:C↑、合金元素↑→导热性↓→易烧伤高温合金↑→磨削功率↑→θA↑→易烧伤影响:破坏工件表层组织,产生裂纹,影响耐磨性和寿命2、残余应力原因:相变引起金相组织体积变化温度引起热胀冷缩和塑性变形的综合结果光磨10次残余应力减少2~3倍光磨15次残余应力减少4~5倍fa↓、fr↓→拉应力↓3、磨削裂纹磨削速度垂直方向上的裂纹(局部高温急冷造成热应力)三、磨削精度1、磨床与工件的弹性变形2、磨床与工件的热变形3、砂轮磨损导致形状尺寸变化3、磨床与工件振动研磨加工是应用较广的一种光整加工。
第1章 金属切削原理 《机械制造技术》课件

图1-7 车刀的主要标注角度
1.2.3 刀具的工作参考系及工作角度
如前所述,刀具的标注角度是在忽略进给速度 的影响,且 刀具安装在理想工作位置的情况下确定的。在实际的切削加工 中,当刀具进入工作状态后,由于刀具安装位置和进给运动的 影响,选定点的实际切削速度的方向以及刀具的实际安装位置 相对于假定的理想状态发生了改变,即上述标注角度会发生一 定的变化。而刀具角度变化的根本原因是切削平面、基面和正 交平面位置的改变,因此,研究切削过程中的刀具角度,必须 以刀具与工件的相对位置、相对运动为基础建立参考系,这种 参考系称为工作参考系。用工作参考系定义的刀具角度称为工 作角度。
刀具设计时标注、刃磨、测量角度最常用的是正交平面参 考系。但在标注可转位刀具或倒刃倾角刀具时,常用法平面参 考系。在刀具制造过程中,如铣削刀槽、刃磨刀面时,常需用 假定工作平面、背平面参考系中的角度,或使用前、后刀面正 交平面参考系中的角度。这四种参考系刀具角度是ISO 3002/1—1997标准所推荐的。本章只介绍前三种。
1.2.2 刀具静止参考系和刀具的几何角度
3. 刀具几何角度与标注 刀具的几何角度是指刀具上的切削 刃、刀面与参考系中各参考面间的 夹角,用以确定切削刃、刀面的空 间位置。由于切削刃上各点的主运 动方向可能不同,因此据其建立的 参考系的方位也是变化的,所以定 义的角度必须指明是切削刃上选定 点的角度;凡未经特殊注明的,均 指切削刃上与刀尖毗连的那一点的 角度。在刀具静止参考系中度量标 注的角度通称刀具角度,如图1-7 所示。
2. 金刚石
金刚石刀具有三种:天然单晶金刚石刀具、人造聚晶金刚 石刀 具和金刚石复合刀具。天然金刚石由于价格昂贵等原因, 应用很少。人造金刚石是在高温高压和其他条件配合下由石墨 转化而成。金刚石复合刀片是在硬质合金基体上烧结上一层厚 度约0.5 mm的金刚石,形成了金刚石与硬质合金的复合刀片。
金属切削原理(基本理论)
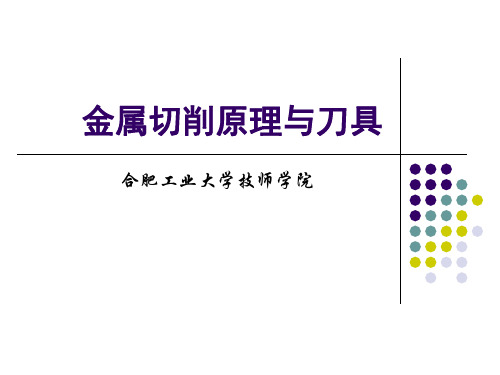
减小切屑与刀具前刀面的摩擦,并能降低切削温度,所以不易
产生积屑瘤。
积屑瘤对切削过程的影响
1. 影响刀具耐用度:
积屑瘤包围着切削刃,同时覆盖着一部分前刀面。积屑
瘤相对稳定时,可代替切削刃进行切削。切削刃和前刀面
都得到积屑瘤的保护,减少了刀具的磨损,提高刀具耐用
如铜、20钢、40Cr钢、1Crl8Ni9Ti等,随着工件材料的强
度和硬度的依次增大,摩擦系数μ略有减小;
这是由于在切削速度不变的情况下,材料的硬度、强度
大时,切削温度增高,故摩擦系数下降。
切削厚度ac增加时, μ也略为下降;如20钢的ac从0.
lmm增大到0. 18mm, μ从0 .74降至0 .72。因为ac增加
最后长成积屑瘤。
影响积屑瘤产生的因素:
①工件材料的影响:塑性高的材料,由于切削时塑性
变形较大,加工硬化趋势较强,积屑瘤容易形成;而
脆性材料一般没有塑性变形,并且切屑不在前刀面流
过,因此无积屑瘤产生。
②切削速度主要通过切削温度影响积屑瘤。
低速(Vc<3~5m/min)时,切削温度较低(低于
300℃),切屑流动速度较慢,摩擦力未超过切屑分子的结
工件母体分离,一部分变成切屑,很小一部分留在已加
工表面上。
第Ⅰ变形区
近切削刃处切削层内产生的塑性变形区——剪切滑移变形;
第Ⅱ变形区
与前刀面接触的切屑底层内产生的变形区——挤压变形;
第Ⅲ变形区
近切削刃处已加工表层内产生的变形区——已加工表面变形。
三) 第一变形区内金属的剪切变形
追踪切削层上任一点P,可以观察切屑的变形和形
系数ξ可直观反映切屑的变形程度,并且容易测量。
【金属切削原理】第12章:磨削详解
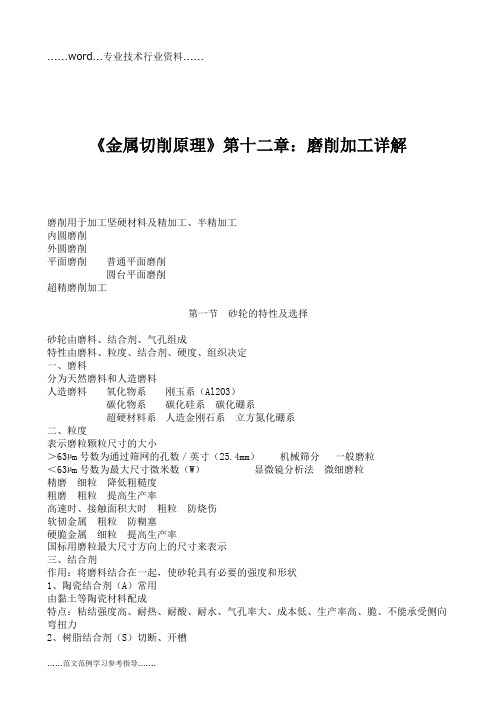
《金属切削原理》第十二章:磨削加工详解磨削用于加工坚硬材料及精加工、半精加工内圆磨削外圆磨削平面磨削普通平面磨削圆台平面磨削超精磨削加工第一节砂轮的特性及选择砂轮由磨料、结合剂、气孔组成特性由磨料、粒度、结合剂、硬度、组织决定一、磨料分为天然磨料和人造磨料人造磨料氧化物系刚玉系(Al2O3)碳化物系碳化硅系碳化硼系超硬材料系人造金刚石系立方氮化硼系二、粒度表示磨粒颗粒尺寸的大小>63µm号数为通过筛网的孔数/英寸(25.4mm)机械筛分一般磨粒<63µm号数为最大尺寸微米数(W)显微镜分析法微细磨粒精磨细粒降低粗糙度粗磨粗粒提高生产率高速时、接触面积大时粗粒防烧伤软韧金属粗粒防糊塞硬脆金属细粒提高生产率国标用磨粒最大尺寸方向上的尺寸来表示三、结合剂作用:将磨料结合在一起,使砂轮具有必要的强度和形状1、陶瓷结合剂(A)常用由黏土等陶瓷材料配成特点:粘结强度高、耐热、耐酸、耐水、气孔率大、成本低、生产率高、脆、不能承受侧向弯扭力2、树脂结合剂(S)切断、开槽酚醛树脂、环氧树脂特点:强度高、弹性好、耐热性差、易自砺、气孔率小、易糊塞、磨损快、易失廓形、与碱性物质易反应、不易长期存放3、橡胶结合剂(X)薄砂轮、切断、开槽、无心磨导轮人造橡胶特点:弹性好、强度好、气孔小、耐热性差、生产率低4、金属结合剂(Q)磨硬质合金、玻璃、宝石、半导体材料青铜结合剂(制作金刚石砂轮)特点:强度高、自砺性差、形面成型性好、有一定韧性四、硬度在磨削力作用下,磨粒从砂轮表面脱落的难易程度分为超软、软、中软、中、中硬、硬、超硬工件材料硬砂轮软些防烧伤工件材料软砂轮硬些充分发挥磨粒作用接触面积大软砂轮精度、成形磨削硬砂轮保持廓形粒度号大软砂轮防糊塞有色金属、橡胶、树脂软砂轮防糊塞五、组织磨粒、气孔、结合剂体积的比例关系分为:紧密(0~3)、中等(4~7)、疏松(8~14)(磨粒占砂轮体积%↘)气孔、孔穴开式(与大气连通)占大部分,影响较大闭式(与大气不连通)尺寸小、影响小开式空洞型蜂窝型前两种构成砂轮内部主要的冷却通道管道型5~50µm六、砂轮的型号标注形状、尺寸、磨料、粒度号、硬度、组织号、结合剂、允许最高圆周线速度P300x30x75WA60L6V35外径300,厚30,内径75第二节磨削运动一、磨削运动1、主运动砂轮外圆线速度 m/s2、径向进给运动进给量fr 工件相对砂轮径向移动的距离间歇进给 mm/st 单行程mm/dst 双行程连续进给 mm/s3、轴向进给运动进给量fa 工件相对砂轮轴向的进给运动圆磨 mm/r平磨 mm/行程4、工件速度vw线速度 m/s二、磨削金属切除率ZQ=Q/B=1000·vw·fr·fa/B mm^3/(s·mm)ZQ:单位砂轮宽度切除率Q:每秒金属切除量用以表示生产率B:砂轮宽度三、砂轮与工件加工表面接触弧长lc=sqrt(fr·d0)影响参加磨削磨粒数目及磨粒负荷,容屑,冷却条件四、砂轮等效直径将外圆(内圆)砂轮直径换算成接触弧长相等的假想平面磨削的砂轮直径结论:对砂轮耐用度影响内圆>平面>外圆第三节磨削的过程一、单个磨粒的磨削过程磨粒的模型锐利120°圆锥钝化半球实际磨粒:大的负前角,大的切削刃钝圆半径滑擦、耕犁、切削滑擦:(不切削,不刻划)产生高温,引起烧伤裂纹耕犁:(划出痕迹)磨粒钝或切削厚度小于临界厚度,工件材料挤向两侧隆起切削:切削厚度大于临界厚度,形成切屑v↑→隆起↓(线性)塑性变形速度<磨削速度二、磨削的特点1、精度高、表面粗糙度小高速、小切深、机床刚性2、径向分力Fn较大多磨粒切削3、磨削温度高磨粒角度差、挤压和摩擦、砂轮导热差4、砂轮的自砺作用三、磨削的阶段1、初磨阶段实际磨深小于径向进给量2、稳定阶段实际磨深等于径向进给量3、清磨阶段实际磨深趋向于0提高生产率缩短1、2提高质量保证3第四节磨削力及磨削功率一、磨削力的特征分解成三个分力Ft切向力 Fn法向力 Fa轴向力特征:1、单位切削力k很大磨粒几何形状的随机性和参数的不合理性7000~20000kgf/mm^2 其他切削方式k<700kgf/mm^22、Fn值最大Fn/Ft 通常2.0~2.5工件塑性↓、硬度↑→Fn/Ft↑切深小,砂轮严重磨损 Fn/Ft 可达5~103、磨削力随磨削阶段变化初磨、稳定、光磨二、磨削力及磨削功率摩擦耗能占相当大的比例(70~80%)切向力(N):Ft=9.81·(CF·(vw·fr·B/v)+µ·Fn)径向力(N):Fn=9.81·CF·(vw·fr·B/v)·tan(α)·(π/2) vw:工件速度v:砂轮速度fr:径向进给量B:磨削宽度CF:切除单位体积切屑所需的能 kgf/mm^2µ:工件-砂轮摩擦系数α:假设粒度为圆锥时的锥顶半角磨削功率P=Ft·v/1000 Kw理论公式精度不高,常用实验测定(顶尖上安装应变片)第五节磨削温度耕犁、滑擦和形成切屑的能量全部转化成热,大部分传入工件一、磨削温度砂轮磨削区温度θA:砂轮与工件接触区的平均温度影响:烧伤、裂纹的产生磨粒磨削点温度θdot:磨粒切削刃与切屑接触部分的温度温度最高处,是磨削热的主要来源影响:表面质量、磨粒磨损、切屑熔着工件温升:影响:工件尺寸、形状精度受影响二、影响磨削温度的因素切削液为降温的主要途径1、工件速度对磨粒磨削点温度的影响大于砂轮速度vw↑→acgmax↑→F↑→θdot↑大v↑→acgmax↓→θdot↑小→摩擦热↑↗acgmax:单个磨粒最大切削厚度 mm假设:磨粒前后对齐,均匀分不在砂轮表面平面磨:acgmax=(2·vw·fa/(v·m·B))sqrt(fr/dt)外圆磨:acgmax=(2·vw·fa/(v·m·B))sqrt((fr/dt)+(fr/dw))dt:砂轮直径m:每毫米周长磨粒数用于定性分析2、径向进给量Frfr↑→acgmax↑→θdot↑fr↑→接触区↑→同时参加切削磨粒数↑→θA↑3、其他因素fa↑→θdot↑、θA↑工件材料硬度↑、强度、↑韧性↑→θdot↑、θA↑θA↑→工件温升↑vw↑→被磨削点与砂轮接触时间↓→工件温升↗三、磨削温度的测量(热电偶)第六节砂轮的磨损及表面形貌一、砂轮的磨损类型磨耗磨损磨粒磨损破碎磨损磨粒或结合剂破碎(取决于磨削力与磨粒、结合剂强度)破碎磨损消耗砂轮多磨耗磨损通过磨削力影响破碎磨损阶段初期磨损磨粒破碎磨损(个别磨粒受力大,磨粒内部应力与裂纹)二期磨损磨耗磨损三期磨损结合剂破碎磨损二、砂轮的耐用度T砂轮相邻两次修整期间的加工时间 s各因素通过平均切削厚度来影响T经验公式:T=6.67·(dw^0.6)·km·kt/(10000·(vw·fa·fr)^2)dw:工件直径kt:砂轮直径修正系数km:工件材料修正系数粗磨时间常用单位时间内磨除金属体积与砂轮磨耗体积之比来选择砂轮三、砂轮的修整作用去除钝化磨粒或糊塞住的磨粒,使新磨粒露出来增加有效切削刃,提高加工表面质量工具单颗金刚石、单排金刚石、碳化硅修整轮、电镀人造金刚石滚轮、硬质合金挤压轮等使用单颗金刚石:导程小于等于磨粒平均直径,每颗磨粒都能修整深度小于等于磨粒平均直径,提高砂轮寿命四、表面形貌单位面积上磨粒数目越多→acgmax↓→磨粒受力↓→磨粒寿命↑→T↑磨粒高度分布越均匀→粗糙度↓磨粒间距均匀性越好→粗糙度↓第七节磨削表面质量与磨削精度一、表面粗糙度比普通切削小小于 Ra2~4µmvw↓、v↑、R工↑、R砂↑、细粒度→粗糙度↓细粒度→m↑→粗糙度↓B↑→acgmax↓→粗糙度↓磨粒等高性好→粗糙度↓二、机械性能1、金相组织变化烧伤:C↑、合金元素↑→导热性↓→易烧伤高温合金↑→磨削功率↑→θA↑→易烧伤影响:破坏工件表层组织,产生裂纹,影响耐磨性和寿命2、残余应力原因:相变引起金相组织体积变化温度引起热胀冷缩和塑性变形的综合结果光磨10次残余应力减少2~3倍光磨15次残余应力减少4~5倍fa↓、fr↓→拉应力↓3、磨削裂纹磨削速度垂直方向上的裂纹(局部高温急冷造成热应力)三、磨削精度1、磨床与工件的弹性变形2、磨床与工件的热变形3、砂轮磨损导致形状尺寸变化3、磨床与工件振动研磨加工是应用较广的一种光整加工。
金属切削原理
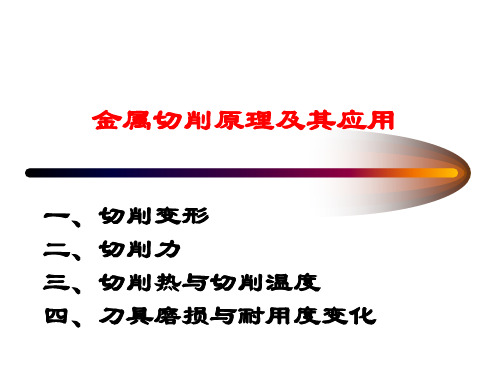
切削时消耗的功率
金属切削原理及其应用
一、切削变形 二、切削力 三、切削热与切削温度 四、刀具磨损与耐用度变化
1.1 金属切削过程的基本规律
一、切削变形 变形Ⅰ,Ⅱ,Ⅲ区, 剪切面间距0.02-0.2mm。
1. 切屑的形成
图为金属切削过程中的滑移线
1.1 金属切削过程的基本规律.
• (1)第一变形区 从OA线开始发生塑性变形,到 OM线金属晶粒的剪切滑移基本完成。OA线和OM 线之间的区域(图中Ⅰ区)称为第一变形区。
碳素钢,合金钢,铜 铝合金; 黄铜,低速切削钢; 铝; 铸鉄,黄铜
图为切屑类型
2. 积屑瘤
图为积屑瘤与切削刃的金 相显微照片
2. 积屑瘤
积屑瘤高度及其实际工作前角
2. 积屑瘤
(1)积屑瘤对切削过程的影响: 1) 积屑瘤包围着切削刃,可以代替前面、后面和切
削刃进行切削,从而保护了刀刃,减少了刀具的磨 损。 2) 积屑瘤使刀具的实际工作前角增大,而且,积屑 瘤越高,实际工作前角越大,刀具越锋利。 3) 积屑瘤前端伸出切削刃外,直接影响加工尺寸精 度。 4) 积屑瘤直接影响工件加工表面的形状精度和表面 粗糙度。
Fx Fxy sin r
3. 影响切削力的因素
3)刀具几何参数对切削力的影响。
c)刃倾角ls 对切削力的影响; ls↑ 背前角gp↑ 侧前角gf↓
Fp↓ Ff↑
3. 影响切削力的因素
3)刀具几何参数对切削力的影响。
d)刀尖圆弧半径r 对切削力的影响;
3. 影响切削力的因素
3)刀具几何参数对切削力的影响。 e)使用切削液 对切削力的影响;
v a 273
f 0.26 0.07
c
0.01
《金属切削原理》课件
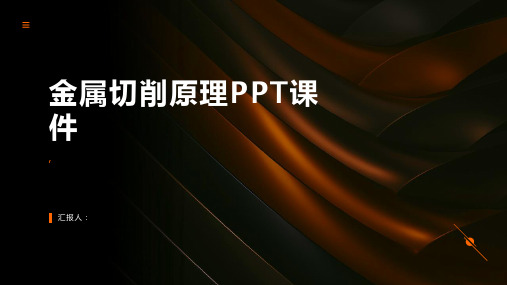
金属切削在机械制造中的应用
加工精度:金属切削可以精确地加工出各种形状和尺寸的零件 加工效率:金属切削可以提高生产效率,缩短生产周期 加工范围:金属切削可以加工各种金属材料,包括钢、铝、铜等 加工质量:金属切削可以保证加工质量,提高产品的可靠性和耐用性
金属切削在航空航天领域的应用
飞机制造:金属 切削用于制造飞 机机身、机翼、 发动机等部件
新材料硬度 高,耐磨性 好,对刀具 寿命和加工 效率产生影 响
新材料热导 率低,切削 过程中热量 难以散发, 对刀具和工 件产生影响
新材料化学 活性强,易 与刀具材料 发生化学反 应,影响刀 具寿命和加 工质量
新材料加工 难度大,对 刀具材料和 加工工艺提 出更高要求
新材料加工 过程中产生 的废料处理 问题,对环 保和资源利 用提出挑战
切削热的ห้องสมุดไป่ตู้生与散失
切削热的产生:刀具与工件之间的摩擦和剪切作用 切削热的散失:通过刀具、工件和切屑的传导、对流和辐射等方式 切削热的影响:影响刀具寿命、工件加工精度和表面质量 切削热的控制:通过优化刀具材料、切削参数和冷却方式等手段
切削表面的形成与变化
切削过程:刀具与工件之间的相对运动 切削力:刀具与工件之间的相互作用力 切削温度:刀具与工件之间的摩擦热 切削表面:刀具与工件之间的接触面
火箭制造:金属 切削用于制造火 箭发动机、燃料 箱、控制系统等 部件
卫星制造:金属 切削用于制造卫 星外壳、太阳能 电池板、天线等 部件
空间站制造:金 属切削用于制造 空间站外壳、太 阳能电池板、生 命支持系统等部 件
金属切削在汽车工业领域的应用
汽车零部件制造:金属切削用于生产汽车发动机、变速箱、底盘等零部件 汽车车身制造:金属切削用于生产汽车车身、车门、车窗等车身部件 汽车模具制造:金属切削用于生产汽车模具,如冲压模具、注塑模具等 汽车维修与保养:金属切削用于汽车维修与保养,如更换损坏的零部件、修复车身损伤等
- 1、下载文档前请自行甄别文档内容的完整性,平台不提供额外的编辑、内容补充、找答案等附加服务。
- 2、"仅部分预览"的文档,不可在线预览部分如存在完整性等问题,可反馈申请退款(可完整预览的文档不适用该条件!)。
- 3、如文档侵犯您的权益,请联系客服反馈,我们会尽快为您处理(人工客服工作时间:9:00-18:30)。
第十二章磨削磨削用于加工坚硬材料及精加工、半精加工内圆磨削外圆磨削平面磨削普通平面磨削圆台平面磨削超精磨削加工第一节砂轮的特性及选择砂轮由磨料、结合剂、气孔组成特性由磨料、粒度、结合剂、硬度、组织决定一、磨料分为天然磨料和人造磨料人造磨料氧化物系刚玉系(Al2O3)碳化物系碳化硅系碳化硼系超硬材料系人造金刚石系立方氮化硼系二、粒度表示磨粒颗粒尺寸的大小>63μm号数为通过筛网的孔数/英寸(25.4mm)机械筛分一般磨粒<63μm号数为最大尺寸微米数(W)显微镜分析法微细磨粒精磨细粒降低粗糙度粗磨粗粒提高生产率高速时、接触面积大时粗粒防烧伤软韧金属粗粒防糊塞硬脆金属细粒提高生产率国标用磨粒最大尺寸方向上的尺寸来表示三、结合剂作用:将磨料结合在一起,使砂轮具有必要的强度和形状1、陶瓷结合剂(A)常用由黏土等陶瓷材料配成特点:粘结强度高、耐热、耐酸、耐水、气孔率大、成本低、生产率高、脆、不能承受侧向弯扭力2、树脂结合剂(S)切断、开槽酚醛树脂、环氧树脂特点:强度高、弹性好、耐热性差、易自砺、气孔率小、易糊塞、磨损快、易失廓形、与碱性物质易反应、不易长期存放3、橡胶结合剂(X)薄砂轮、切断、开槽、无心磨导轮人造橡胶特点:弹性好、强度好、气孔小、耐热性差、生产率低4、金属结合剂(Q)磨硬质合金、玻璃、宝石、半导体材料青铜结合剂(制作金刚石砂轮)特点:强度高、自砺性差、形面成型性好、有一定韧性四、硬度在磨削力作用下,磨粒从砂轮表面脱落的难易程度分为超软、软、中软、中、中硬、硬、超硬工件材料硬砂轮软些防烧伤工件材料软砂轮硬些充分发挥磨粒作用接触面积大软砂轮精度、成形磨削硬砂轮保持廓形粒度号大软砂轮防糊塞有色金属、橡胶、树脂软砂轮防糊塞五、组织磨粒、气孔、结合剂体积的比例关系分为:紧密(0~3)、中等(4~7)、疏松(8~14)(磨粒占砂轮体积%↘)气孔、孔穴开式(与大气连通)占大部分,影响较大闭式(与大气不连通)尺寸小、影响小开式空洞型蜂窝型前两种构成砂轮内部主要的冷却通道管道型5~50μm六、砂轮的型号标注形状、尺寸、磨料、粒度号、硬度、组织号、结合剂、允许最高圆周线速度P300x30x75WA60L6V35外径300,厚30,内径75第二节磨削运动一、磨削运动1、主运动砂轮外圆线速度 m/s2、径向进给运动进给量fr 工件相对砂轮径向移动的距离间歇进给 mm/st 单行程mm/dst 双行程连续进给 mm/s3、轴向进给运动进给量fa 工件相对砂轮轴向的进给运动圆磨 mm/r平磨 mm/行程4、工件速度vw线速度 m/s二、磨削金属切除率ZQ=Q/B=1000·vw·fr·fa/B mm^3/(s·mm)ZQ:单位砂轮宽度切除率Q:每秒金属切除量用以表示生产率B:砂轮宽度三、砂轮与工件加工表面接触弧长lc=sqrt(fr·d0)影响参加磨削磨粒数目及磨粒负荷,容屑,冷却条件四、砂轮等效直径将外圆(内圆)砂轮直径换算成接触弧长相等的假想平面磨削的砂轮直径结论:对砂轮耐用度影响内圆>平面>外圆第三节磨削的过程一、单个磨粒的磨削过程磨粒的模型锐利120°圆锥钝化半球实际磨粒:大的负前角,大的切削刃钝圆半径滑擦、耕犁、切削滑擦:(不切削,不刻划)产生高温,引起烧伤裂纹耕犁:(划出痕迹)磨粒钝或切削厚度小于临界厚度,工件材料挤向两侧隆起切削:切削厚度大于临界厚度,形成切屑v↑→隆起↓(线性)塑性变形速度<磨削速度二、磨削的特点1、精度高、表面粗糙度小高速、小切深、机床刚性2、径向分力Fn较大多磨粒切削3、磨削温度高磨粒角度差、挤压和摩擦、砂轮导热差4、砂轮的自砺作用三、磨削的阶段1、初磨阶段实际磨深小于径向进给量2、稳定阶段实际磨深等于径向进给量3、清磨阶段实际磨深趋向于0提高生产率缩短1、2提高质量保证3第四节磨削力及磨削功率一、磨削力的特征分解成三个分力Ft切向力 Fn法向力 Fa轴向力特征:1、单位切削力k很大磨粒几何形状的随机性和参数的不合理性7000~20000kgf/mm^2 其他切削方式k<700kgf/mm^22、Fn值最大Fn/Ft 通常2.0~2.5工件塑性↓、硬度↑→Fn/Ft↑切深小,砂轮严重磨损 Fn/Ft 可达5~103、磨削力随磨削阶段变化初磨、稳定、光磨二、磨削力及磨削功率摩擦耗能占相当大的比例(70~80%)切向力(N):Ft=9.81·(CF·(vw·fr·B/v)+μ·Fn)径向力(N):Fn=9.81·CF·(vw·fr·B/v)·tan(α)·(π/2)vw:工件速度v:砂轮速度fr:径向进给量B:磨削宽度CF:切除单位体积切屑所需的能 kgf/mm^2μ:工件-砂轮摩擦系数α:假设粒度为圆锥时的锥顶半角磨削功率P=Ft·v/1000 Kw理论公式精度不高,常用实验测定(顶尖上安装应变片)第五节磨削温度耕犁、滑擦和形成切屑的能量全部转化成热,大部分传入工件一、磨削温度砂轮磨削区温度θA:砂轮与工件接触区的平均温度影响:烧伤、裂纹的产生磨粒磨削点温度θdot:磨粒切削刃与切屑接触部分的温度温度最高处,是磨削热的主要来源影响:表面质量、磨粒磨损、切屑熔着工件温升:影响:工件尺寸、形状精度受影响二、影响磨削温度的因素切削液为降温的主要途径1、工件速度对磨粒磨削点温度的影响大于砂轮速度vw↑→acgmax↑→F↑→θdot↑大v↑→acgmax↓→θdot↑小→摩擦热↑↗acgmax:单个磨粒最大切削厚度 mm假设:磨粒前后对齐,均匀分不在砂轮表面平面磨:acgmax=(2·vw·fa/(v·m·B))sqrt(fr/dt)外圆磨:acgmax=(2·vw·fa/(v·m·B))sqrt((fr/dt)+(fr/dw))dt:砂轮直径m:每毫米周长磨粒数用于定性分析2、径向进给量Frfr↑→acgmax↑→θdot↑fr↑→接触区↑→同时参加切削磨粒数↑→θA↑3、其他因素fa↑→θdot↑、θA↑工件材料硬度↑、强度、↑韧性↑→θdot↑、θA↑θA↑→工件温升↑vw↑→被磨削点与砂轮接触时间↓→工件温升↗三、磨削温度的测量(热电偶)第六节砂轮的磨损及表面形貌一、砂轮的磨损类型磨耗磨损磨粒磨损破碎磨损磨粒或结合剂破碎(取决于磨削力与磨粒、结合剂强度)破碎磨损消耗砂轮多磨耗磨损通过磨削力影响破碎磨损阶段初期磨损磨粒破碎磨损(个别磨粒受力大,磨粒内部应力与裂纹)二期磨损磨耗磨损三期磨损结合剂破碎磨损二、砂轮的耐用度T砂轮相邻两次修整期间的加工时间 s各因素通过平均切削厚度来影响T经验公式:T=6.67·(dw^0.6)·km·kt/(10000·(vw·fa·fr)^2)dw:工件直径kt:砂轮直径修正系数km:工件材料修正系数粗磨时间常用单位时间内磨除金属体积与砂轮磨耗体积之比来选择砂轮三、砂轮的修整作用去除钝化磨粒或糊塞住的磨粒,使新磨粒露出来增加有效切削刃,提高加工表面质量工具单颗金刚石、单排金刚石、碳化硅修整轮、电镀人造金刚石滚轮、硬质合金挤压轮等使用单颗金刚石:导程小于等于磨粒平均直径,每颗磨粒都能修整深度小于等于磨粒平均直径,提高砂轮寿命四、表面形貌单位面积上磨粒数目越多→acgmax↓→磨粒受力↓→磨粒寿命↑→T↑磨粒高度分布越均匀→粗糙度↓磨粒间距均匀性越好→粗糙度↓第七节磨削表面质量与磨削精度一、表面粗糙度比普通切削小小于 Ra2~4μmvw↓、v↑、R工↑、R砂↑、细粒度→粗糙度↓细粒度→m↑→粗糙度↓B↑→acgmax↓→粗糙度↓磨粒等高性好→粗糙度↓二、机械性能1、金相组织变化烧伤:C↑、合金元素↑→导热性↓→易烧伤高温合金↑→磨削功率↑→θA↑→易烧伤影响:破坏工件表层组织,产生裂纹,影响耐磨性和寿命2、残余应力原因:相变引起金相组织体积变化温度引起热胀冷缩和塑性变形的综合结果光磨10次残余应力减少2~3倍光磨15次残余应力减少4~5倍fa↓、fr↓→拉应力↓3、磨削裂纹磨削速度垂直方向上的裂纹(局部高温急冷造成热应力)三、磨削精度1、磨床与工件的弹性变形2、磨床与工件的热变形3、砂轮磨损导致形状尺寸变化3、磨床与工件振动研磨加工是应用较广的一种光整加工。
加工后精度可达IT5级,表面粗糙度可达Ra0.1~0.006μm。
既可加工金属材料,也可以加工非金属材料。
研磨加工时,在研具和工件表面间存在分散的细粒度砂粒(磨料和研磨剂)在两者之间施加一定的压力,并使其产生复杂的相对运动,这样经过砂粒的磨削和研磨剂的化学、物理作用,在工件表面上去掉极薄的一层,获得很高的精度和较小的表面粗糙度。
研磨的方法按研磨剂的使用条件分以下三类:1.干研磨研磨时只需在研具表面涂以少量的润滑附加剂。
如图8-12a所示。
砂粒在研磨过程中基本固定在研具上,它的磨削作用以滑动磨削为主。
这种方法生产率不高,但可达到很高的加工精度和较小的表面粗糙度值(Ra0.02~0.01μm)。
2.湿研磨在研磨过程中将研磨剂涂在研具上,用分散的砂粒进行研磨。
研磨剂中除砂粒外还有煤油、机油、油酸、硬脂酸等物质。
在研磨过程中,部分砂粒存在于研具与工件之间,如图8-12b所示。
此时砂粒以滚动磨削为主,生产率高,表面粗糙度Ra0.04~0.02μm,一般作粗加工用,但加工表面一般无光泽。
3.软磨粒研磨在研磨过程中,用氧化铬作磨料的研磨剂涂在研具的工作表面,由于磨料比研具和工件软,因此研磨过程中磨料悬浮于工件与研具之间,主要利用研磨剂与工件表面的化学作用,产生很软的一层氧化膜,凸点处的薄膜很容易被磨料磨去。
此种方法能得到极细的表面粗糙度(Ra0.02~0.01μm)。
刮研平面用于未淬火的工件,它可使两个平面之间达到紧密接触,能获得较高的形状和位置精度,加工精度可达IT7级以上,表面粗糙度值Ra0.8~0.1μm。
刮研后的平面能形成具有润滑油膜的滑动面,因此能减少相对运动表面间的磨损和增强零件接合面间的接触刚度。
刮研表面质量是用单位面积上接触点的数目来评定的,粗刮为1~2点/cm2,半精刮为2~3点/cm2,精刮为3~4点/cm2。
刮研劳动强度大,生产率低;但刮研所需设备简单,生产准备时间短,刮研力小,发热小,变形小,加工精度和表面质量高。
此法常用于单件小批生产及维修工作中。