洁净钢的成分控制
第二篇洁净钢发展及钢中夹杂物控制

Institute of Ferrous Metallurgy
脱氧产物总结
• 单个脱氧产物的直径一般小于10μm,由于尺寸较小,除非最终产品要求极高, 一般不会危害钢材的使用性能; • 若脱氧产物与炉渣、耐材反应形成大颗粒夹杂,则会对钢材性能产生严重影响。
表 不同钢中发现的典型脱氧产物 钢种 Al镇静钢 Si镇静钢 Ca处理镇静钢 Al镇静钢,有残余Mg 钛处理镇静钢 脱氧产物类型 Al2O3 SiO2 、MnO-SiO2 CaO-Al2O3 MgAl2O4 Al2O3、 TiOx、 TiN 备注 脱氧后在钢液中形成,固态 脱氧或凝固过程中形成,固态或液态夹杂物 与氧化铝反应形成,固态或液态 与氧化铝反应形成,固态 TiOx形成于二次氧化过程, TiN形成于凝固 过程,均为固态夹杂物
2.3 钢种对夹杂物特征的要求
钢种 IF钢 汽车深冲钢板 易拉罐钢 压力容器钢 抗HIC钢(油气管) 管线钢 滚珠轴承 帘线钢 重轨钢 最高纯净度,×10-6 [C]≤30, [N] ≤40, T.O ≤40 [C]≤10, [N] ≤50 [C]≤10, [N] ≤30 [C]≤30, [N] ≤30, T.O ≤20 [P] ≤70 [P]≤50, [S] ≤10 [S]≤30, [N] ≤35, T.O ≤30 T.O ≤10 [H]≤30, [N] ≤40, T.O ≤15 [H]≤2, [N] ≤40, T.O ≤20 最小夹杂物尺寸,μm
图 FeO-MnO-SiO2 三元相图
Institute of Ferrous Metallurgy
钢中夹杂物来源Ⅰ---脱氧产物
• Si+Mn+Al脱氧
• 脱氧产物:
MnO·SiO2
℃ 1150
洁净钢与纯净钢
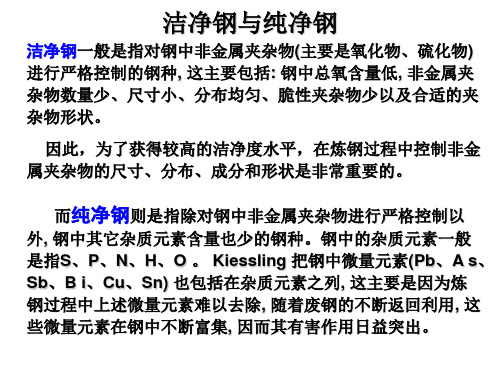
洁净关钢于一纯般净是钢指(对pu钢ri中ty非st金ee属l)夹或杂洁物净(钢主(要c是lea氧n化st物ee、l) 硫的化概物念), 进目行前严国格内控外制尚的无钢统种一, 这的主定要义包。括: 钢中总氧含量低, 非金属夹 杂物数量少、尺寸小、分布均匀、脆性夹杂物少以及合适的夹 杂物形状。
纯净钢除了要考虑[S]+[P]+[N]+[O]+[H]五大元素外,随废钢
量的增加,还要关注Cu、Zr、Sn、Bi、Pb等伴生元素。
研究发现,即Байду номын сангаас将钢中总氧降到10ppm以下,钢液中仍 然存在15微米尺度的夹杂物,因此洁净钢的研究目前沿 着两种发展方向进行: 一种是控制钢中总氧量来降低夹杂物含量; 另一种是控制夹杂物成分以减小其对钢性能的影响。
洁净钢是一个相对概念
当1.2某钢0世中一纪的杂杂6质0质年含元代量素:降或[S]非低+[金P到]属+什[N夹么]杂+[水O物]平直+[H接决]或<定9间0于0接p钢p影m种响;和产产品的品生用产途; 性金么不程能属这同度或夹种的决使杂钢年定用物就78代 于性的可00年年, 装能数以代代对 备时量认::,、为洁 和[[SS该尺是净工]]++钢寸洁[[钢艺PP就或净]]++有现不分钢[[NN不代是布。]]++同化洁对可[[OO净产见的水]]++钢品,[[平要HH;的“]]。求<<而性洁8600;如能净00pp有果都钢ppmm害杂没”;;质有不元元影同素素响于降或,“低非那纯 净念地<22钢不生.0高p”是产p附的为出m加概了可;9值念一以0年夹,味稳产代杂“追定品:物洁求地对[S净纯满数]洁+钢净足量[P净”用,]而要+度并户[是N少不加的]为+;指工[要了O夹越和]能求+纯使杂[够H是越用物]高<:好要1效尺0。求0T率寸p[所的p、O要m以优]低;要小质,成洁低商<本净5品0、钢μ钢成的m材批概;。 这夹2样杂1世的物纪“形洁态净要钢合”概适[S念。]+不[P仅]+具[N有]+质[O量]+含[H义]<,5而0p且pm具。有经济含义。
洁净钢生产技术的发展与耐火材料的相互关系

总之,洁净煤技术作为一项重要的能源技术,在缓解全球能源危机和保护环 境方面具有重要意义。今后,我们应进一步加大洁净煤技术的研究与推广力度, 促进其在全球能源转型中发挥更大的作用。
在当今时代,空气洁净技术已经成为我们日常生活中不可或缺的一部分。尤 其在最近几年,随着全球气候变化的加剧和新冠疫情的爆发,空气洁净技术的度 越来越高。本次演示将介绍空气洁净技术的新发展,包括其应用领域、技术原理、 创新实践等方面,并探讨未来的发展方向。
近年来,空气洁净技术取得了许多突破性进展。其中,一种新型的空气净化 技术——光触媒净化技术备受。光触媒净化技术主要利用紫外线的照射,激活光 触媒反应,产生具有氧化能力的自由基,从而分解和去除空气中的有害物质。与 传统的空气净化技术相比,光触媒净化技术具有更高效、更环保、更持久等优点, 因此被广泛应用于室内空气净化、工业废气处理等多个领域。
洁净钢生产技术的未来发展
随着科技的不断发展,洁净钢生产技术也在不断创新和进步。未来洁净钢生 产技术的发展将朝着高效、节能、环保的方向发展。同时,新材料的研发和应用 也将推动洁净钢生产技术的进步。例如,以纳米技术为基础的纳米耐火材料、纳 米金属陶瓷等新型材料的出现和应用,将为洁净钢生产技术的发展带来新的机遇 和挑战。
1、建筑领域:洁净钢在建筑领域被广泛应用于桥梁、高层建筑、厂房等结 构件的制作。
2、汽车领域:洁净钢在汽车制造业中具有重要作用,用于生产高性能汽车 零部件,提高汽车的安全性和舒适性。
3、家电领域:洁净钢在家电行业主要用于生产高档次、高性能的家电产品, 如高档冰箱、洗衣机等。
四、洁净钢的优势
相比其他钢种,洁净钢具有以下优势:
五、结论
综上所述,洁净钢因其优良的性能和广泛的应用领域,具有极大的重要性和 价值。随着科技的不断发展,相信洁净钢在未来还将发挥更大的作用,推动工业 领域的进步。我们期待着洁净钢在未来的发展趋势和更多创新应用。
钢洁净度的评定和控制二

A C D钢公司 " # $ 7 2 / : &’ $ 0 2 K" # $ 0 2 K : &’ $ 8 2 / 0 / / 7 克利夫兰厂 美国 . / / 7 " # $ 6 1 2 / : &’ $ 6 2 /" # $ @ 2 6 : &’ $ 6 2 8 0 内陆钢公司 # $ ( 2 0 : &’ $ 1 2 6" # $ 6 2 @ : &’ $ 0 2 @ 0 / / 8 美国 . " @号 ; $ " -
? @ & BA> &含量对中间包内钢水总氧含量 # $ % & ’ 的影响 ) ! 1 " 策+ 为了减少 ? 采取了如下对 @ &和 A> &的污染 *
& B( % A> ’ ( A> & B1 % 7 8 ’ C7 8 1 (
钢洁净度的评定和控制 二.
OQ P O
从根本上降低补吹频率 4 ; $ "采用副枪 : 采用高效的机械挡渣设备 : 如挡渣球 浮在钢 水和炉渣界面之间 . 有助于减少出钢带入钢包的 : 渣 量约7 钢. 也 可 采 用 一 些 传 感 器9 出 钢 < = > ? : 后: 钢包厚渣层引起了大量渣携带问题 9 例如 : 美 国内陆钢公司第 @ ; $ "车间标准钢种通过机械扒 渣 使钢包炉 渣层厚度低于 @ A &" . 8 B B90 / / 7年 A C D钢 公 司 克 力 夫 兰 厂 最 后 钢 包 渣 平 均 厚 度 为 厂低碳铝镇 ! 1 B B: A C D钢 公 司 印 第 安 那 E F G H I G 静钢钢包渣层厚 / 高强度低合金钢钢包渣 ! B B: 层厚 0 要求增碳条件的钢种渣层厚 7 1 B B:
为什么通过控制渣成分能提高钢的洁净度

为什么通过控制渣成分能提高钢的洁净度?由于轴承部件处于机械设备的连接轴位置,故受到反复应力,因此在使用一定时同之后,可能产生疲劳裂纹。
所以为了保证再与机械设备的使用寿命同步,必须提高轴承钢的品质。
一般来讲.大部分产品所用的轴承钢主要具有较高的Cr-C系成分。
影响轴承钢寿命的因素是非金属夹杂和确偏析等。
在这些因素中,已经用各种方籣对非金属夹杂的影响进行了研究。
根据这些研究可知,非金属天杂起到了应力集中点的作用,并且最终导致了疲劳裂纹的产生和扩大微信公众号:hcsteel。
主要结论是:①当碱度高于4时,由于Si02是稳定的且不作为氢源.所以对于成分[%(质量分数)]为0.99C-O,3Mn-l. 3Cr的轴承钢的去除夹杂来讲,顶渣的碱度并不影响钢的洁净度。
②对于轴承钢去除夹杂来讲,控制CaO/Al2 03比是最为有效的方法(控制其值在1. 7---1.8最有效)。
通过采用这种方法,可以使全氧T[OJ从(10~12) Xl0-6降低到(5-8)Xl0-6。
③随着出钢时氧含量的降低,轴承钢的T[0]降低,但当CaO/AI2 03; >2,O时,由于在炼钢时间内要达到平衡状态的Ti0太高,所以对出钢时的氧含量没有实质性影响。
在原有工艺的基础上,可增加A1量对降低氧化物、硫化物、夹杂物起到积极的作用。
主要原因在蓋跞初期钢中的氧主要是以Al2 03夹杂物形式存在,这有利于在喷吹过程中去除。
在喷吹过程中,Ca0与Alz。
S结合,提供了很好的去除条件,优化后的工艺使轴承钢的质量有明显的改善,这是降低钢中氧化物夹杂的重要技术思路。
这是因为喷人钢液中的Ca具有相当强的脱硫能力。
喷吹Si-Ca粉的过程,应主要是Ca的脱硫,但覆盖渣对脱硫的影响不可忽略。
具有强的脱氧能力的覆盖渣,在出钢及喷吹过程中在渣钢界面进行脱硫反应,还通过钙脱硫产物间的相互作用,促进钙脱硫反应的进行,保证了深脱硫效果的实现。
喷粉精炼工艺之所以取得比电炉工艺成倍的提高材质的使用寿命,关键在于喷粉工艺通过喷吹装置吹入粉状物质,大大加速反应的动力学,有利于夹杂物细化和上浮,提高了材质的纯洁度。
洁净钢的生产实践

洁净钢的生产实践
洁净钢是一种高质量、低含杂质的钢,它的生产实践主要有以下几个方面。
一、原料准备
使用洁净钢前,必须对原料进行良好的准备,包括对原料的分析、检测和加工。
首先,应检查原料的成分,如少量元素的含量、碳含量和其它元素的含量,以确保原料的质量。
其次,通过进行化学分析,确保原料不含有杂质,以及原料中应该有的元素含量。
最后,应将原料进行冶炼或热处理,以达到所需的物理性能。
二、清洗
为了确保洁净钢的质量,必须在生产过程中进行清洗。
清洗的目的是去除原料上的污垢和油污,以便更好地精炼钢,使其达到洁净钢的要求。
清洗的方法有化学法和物理法。
常用的物理法清洗方法有振动清洗、气动清洗、风力清洗、旋流清洗、喷射清洗等。
三、精炼
精炼是洁净钢生产实践中最重要的环节,因为它是洁净钢质量的决定因素。
精炼的目的是去除杂质,使钢中的各种元素达到所需的含量。
精炼的方法有电弧炉精炼法、渣浆精炼法和熔渣精炼法。
四、冷却
冷却是洁净钢生产实践的重要一步,它主要是为了确保洁净钢的结构稳定,同时也是为了改善洁净钢的耐腐蚀性和焊接性能。
冷却的方法有水冷却、空气冷却等。
五、检测
检测是洁净钢生产实践的最后一步,目的是确定洁净钢的质量。
检测主要有机械性能检测、表面质量检测、化学成分检测、热处理检测等。
以上是洁净钢生产实践中的主要步骤,其中每一步都必须精确控制,才能保证洁净钢的质量。
只有通过严格的检测,才能保证洁净钢的质量,从而满足客户的要求。
如何冶炼洁净钢

冶炼洁净钢应根据品种和用途要求,铁水预处理-炼钢-精炼-连铸的操作都应处于严格的控制之下,主要控制技术对策如下:(1)铁水预处理。
对铁水脱硫或三脱工艺(脱Si、脱P、脱S),入炉铁水硫含量应小于0.005%甚至小于0.002%。
(2)转炉复合吹炼和炼钢终点控制。
改善脱磷条件,提高终点成分和温度一次命中率,降低钢中溶解氧含量,减少钢中非金属夹杂物数量。
(3)挡渣出钢。
采用挡渣锥或气动挡渣器,钢包内渣层厚度控制在50mm以下,转炉内流出的氧化性炉渣会增加氧化物夹杂。
防止出钢下渣可避免回磷和提高合金吸收率。
为保证钢包渣百分之百合格,在钢水接收跨设置钢渣扒渣机是有利的。
(4)钢包渣改质。
出钢过程向钢流加入炉渣改质剂,还原FeO并调整钢包渣成分。
(5)炉外精炼。
根据钢种质量要求选择一种或多种精炼组合方式完成钢水精炼任务,达到脱氢、极低C化、极低S化、脱氮、减少夹杂物和夹杂物形态控制等。
1)LF炉。
包盖密封,造还原渣,可扩散脱氧、脱硫、防止渣中FeO和MnO对钢水再氧化。
调整和精确控制钢水成分、温度,排除夹杂物并进行夹杂物形态控制。
2)真空处理。
冶炼超低碳钢的脱碳和脱氧、脱氢、脱氮,排除脱氧产物。
(6)保护浇注。
在浇注过程中采用保护浇注技术对生产洁净钢尤为重要。
1)钢包→中间包注流用长水口+吹氩保护,控制钢水吸氮量小于1.5ppm(1.5×10-4%),甚至为零。
2)中间包→结晶器用浸入式水口+保护渣的保护浇注,钢水吸氮小于2.5ppm(2.5×10-4%)。
3)浇注小方坯时,中间包→结晶器采用氩气保护浇注,气氛中Φ02<1%。
4)在第一炉开浇前中间包内充满空气,为防止钢水中生成大量的Al203和吸氮,在中间包内充入氩气,并用耐火纤维密封中间包体与包盖间的缝隙。
(7)中间包冶金。
在中间包内组织钢水的合理流动,延长钢水停留时间,促进夹杂物上浮。
1)采用碱性包衬的大容量深熔池中间包;2)中间包加砌挡墙+坝、多孔挡墙、过滤器,采用吹氩搅拌、阻流器;3)中间包覆盖剂可保温、隔绝空气,吸附夹杂物;生产洁净钢中间包采用碱性覆盖剂为宜;4)滑动水口高的自开率,自开率应大于95%;5)开浇、换包、浇注即将结束时防止卷渣;6)应用中间包热态循环使用技术;7)应用中间包真空浇注技术。
钢中夹杂物控制原理

钢中夹杂物控制原理钢中氧的存在形式T[O]=[O]溶+[O]夹(1)转炉吹炼终点:[O]夹=>0,T[O]→[O]溶=200~1000ppm[O]溶决定于:l 钢中[C],转炉吹炼终点钢中[C]与a[O] 关系如图l 渣中(FeO);l 钢水温度。
1 顶底复吹转炉炉龄C–Fe的选择性氧化平衡点根据式[C] + [O] = {CO} (1) lg (Pco/ac* [%O])= 1149/T–2.002以及反应[Fe] + [O] = (FeO)(2) lg aFeo/[%O] = 6317/T – 2.739得到反应(FeO)+ [C] = [Fe] + {CO} (3) lg (Pco/ac* aFeo)= –5170/T+4.736 结论钢液中C-Fe的选择性氧化平衡点为[C]=0.035%,也就是说终点[C] < 0.035%时,钢水的过氧化比较严重。
图1-1的统计数据也说明了这点。
同时由式(1)可以求出此时熔池中的平衡氧含量为740ppm。
理论分析1)终点[C]-[O]关系1) 当终点[C]<0.04%时钢水的终点氧含量较高2) 当终点[C]在0.02~0.04%范围时,有些炉次钢水氧波动在平衡曲线附近(区域Ⅰ)有些炉次钢水氧含量则远离平衡曲线(区域Ⅱ),说明在该区域钢水过氧化严重。
2)温度对氧含量的影响在终点[C] = 0.025~0.04%时,终点氧含量虽然较分散,但总的趋势是随着终点温度的升高,终点氧基本呈上升趋势。
1620℃~1680℃之间,氧含量总体水平较低,平均为702ppm ,该范围的炉次共占总炉次的30%左右;出钢温度大于1680℃时,终点钢水氧含量有明显的升高趋势,平均为972ppm ,占总炉次的70%左右。
3)终渣氧化性对终点氧的影响20040060080010001200140016001800160016201640166016801700172017401760终点温度(℃)终点氧含量(p p m )渣中(FeO+MnO)增加,终点[O]有增加趋势;终点[C]<0.04%,渣中(FeO+MnO)增加且波动较大,说明此时吹氧脱碳是比较困难的,而铁则被大量氧化。
- 1、下载文档前请自行甄别文档内容的完整性,平台不提供额外的编辑、内容补充、找答案等附加服务。
- 2、"仅部分预览"的文档,不可在线预览部分如存在完整性等问题,可反馈申请退款(可完整预览的文档不适用该条件!)。
- 3、如文档侵犯您的权益,请联系客服反馈,我们会尽快为您处理(人工客服工作时间:9:00-18:30)。
洁净钢的成分控制在钢铁冶炼过程中,一部分杂质元素可以去除,但仍有一部分将残留在钢中,这些残余元素的存在是钢材质量产生不稳定的主要因素之一。
在这些元素中,某些残余元素由于易于偏析,即使其含量很低,也对钢材性能产生很强的有害影响。
因此正确认识钢铁产品中残余元素问题,建立洁净钢的概念及其工艺控制是保证现代钢铁工业生产优质钢材的重要前提。
提高钢的洁净度,可以明显改善钢材的机械性能和加工性能。
主要表现在:(1) 洁净度对钢材机械性能的影响降低钢中的S、P、N等的杂质含量,可以明显提高钢材的强度和韧性,如当钢中的[S]≤0.004%时,NiCrMo钢的冲击韧性明显提高;对于AIST4340钢,[P]从0.03%下降到0.003%,室温C型缺口冲击能约提高20%,而对于含B钢,控制[N]≤20ppm,可以获得很高的强度和低温韧性。
对于轴承钢,降低钢中的全氧含量,可以明显提高轴承的寿命。
因此,高质量的轴承钢,要求钢中T[O]≤10×10-4%。
同时,钢中夹杂物的尺寸、分布与性质对钢材的疲劳极限也有很大的影响。
降低钢中夹杂物,有利于提高钢材的疲劳强度。
对于硅钢(Si=3%),降低钢中的S和T[O]的含量([S] ≤20ppm,T[O] ≤15ppm),可以使无取向硅钢片的铁芯损失降低到2.3w/kg以下。
而降低钢中的[C]和[N]含量,可以提高硅钢片的最大导磁率,降低矫顽力。
(2) 洁净度对钢材加工性能的影响焊接性能是钢材最重要的使用性能之一,降低钢中的含C量或降低钢的碳当量,有利于改善钢的焊接性能。
汽车板、家用电器和DI罐用钢等钢材,不仅要求一定的强度,还要求要有良好的深冲性能,降低钢中C含量,可以明显改善钢的深冲性能。
汽车用高质量IF钢,要求钢中C+N≤50ppm。
此外,生产热轧薄板,必须严格控制钢中大型Al2O 3夹杂物的数量,才能避免轧制过程中产生裂纹,获得良好的表面质量。
如生产0.3mmDI罐用钢板的关键技术是彻底杜绝30~40mm的大型脆性夹杂的出现。
钢中夹杂物的数量与类型对切削刀具寿命有明显的影响,这是由于钢种的脆性夹杂增大了工件与刀具间的摩擦阻力,不利于钢材的切削性能。
因此,尽量降低钢中的脆性夹杂物的含量,有利于改善钢材的切削性能。
钢中的脆性夹杂物对耐磨性有着极坏的影响,对于钢轨钢和轴承钢,钢中Al2O3等脆性夹杂往往造成钢材表面剥落、腐蚀。
因此,严格控制钢中Al2O3近似等于零,可以解决表面磨损的问题,提高钢材的耐磨性能。
N和C一样,是间隙型杂质。
低温时,容易在Fe原子晶格内扩散,引起时效,使钢材低温锻造性能下降。
对于0.35%的碳钢,如果控制钢中的固溶N含量≤50ppm,可以明显降低钢材冷锻时裂纹的产生率。
钢中含有硅及锰元素时,将大大促进残余元素引起的第二类回火脆性。
这可能是由于硅、锰促进残余元素在钢中的扩散及偏析能力。
相反,钢中如果添加适量的钼,一般为0.2~0.5,则可有效地抑制第二类回火脆性。
理论研究和生产实践都证明钢材的纯净度越高,其性能越好,使用寿命也越长。
钢中杂质含量降低到一定水平,钢材的性能将发生质变。
如钢中碳含量从40×10-6降低到20×10-6,深冲钢的伸长率可增加7%。
提高钢的纯净度还可以赋予钢新的性能(如提高耐磨腐蚀性等),因此纯净钢已成为生产各种用于苛刻条件下高附加值产品的基础,其生产具有巨大的社会经济效益。
需要指出的是对不同钢种其中的杂质元素的种类是不同的,如硫在一般钢中都视为杂质元素,但在易切削钢中其为有益元素;IF钢中氮是杂质元素,但在不锈钢中氮可以代替一部分镍和其它贵重合金元素,其固溶强化和弥散强化作用可提高钢的强度。
钢中[H]含量过多,易于产生氢发裂和白点,导致钢的严重缺陷。
硫是钢中的有害元素之一,是表面活性元素,常以MnS的形式在钢材晶界上或异相界面上偏析聚集。
硫对钢材最大的危害是引起钢的热脆,显著降低了钢的热加工性能。
而对于铁素体不锈钢,要求钢中S≤20ppm,保证钢材的热加工性能。
碳钢的S ≤ppm,热加工时可避免产生热裂纹现象。
此外,硫降低钢材的韧性,恶化钢的Z向性能,并对氢致裂纹有较大影响。
因此,要求管线钢具有较高的抗氢致裂纹(HIC)和抗硫应力裂纹(SSCC)的能力,要求控制钢中S≤10×10-6。
近20年来,随着宇航、航空、石油、汽车、国防及微电子工业的蓬勃发展,对钢铁杂质含量的要求越来越苛刻,因为人们发现钢的纯净度愈高,性能愈好。
例如轴承钢:当含氧量[O%]由30×10-4%降为15×10-4%时接触疲劳寿命提高5倍:降到10×10-4%时接触疲劳寿命提高15倍:降到5×10-4%时接触疲劳寿命提高30倍;又如为满足汽车工业对深冲压成型薄板的需求而推出的IF钢(无间隙相元素钢)对碳含量的要求更降至[%C]<30×10-4%已属于超低碳钢。
生产工艺:纯净钢的生产主要集中在两方面:(1)尽量减少钢中杂质元素的含量;(2)严格控制钢中的夹杂物,包括夹杂物的数量、尺寸、分布、形状、类型。
减少钢中溶质元素的含量主要在各种铁水预处理以及二次精炼设备中营造最佳去除的热力学和动力学条件来实现,钢中夹杂物的控制主要是减少其生成、对其进行改性、促其上浮。
通常纯净钢生产工艺包括以下几部分:铁水预处理,转炉复吹,出钢挡渣、扒渣、对炉渣改性,二次精炼(真空、吹气、加热、造渣)、全程保护浇铸、中间包冶金、结晶器冶金及采取各种促使夹杂物去除的措施等。
根据对脱磷采取的不同工艺,洁净钢生产工艺大致可以分为以下两种工艺流程[12]:(1)铁水“三脱”洁净钢生产工艺:以日本为代表,主要的工艺特点是采用铁水预处理脱磷工艺,生产洁净钢。
技术特点是:采用铁水三脱预处理工艺,脱Si、脱S和脱P。
目前,多采用转炉作为铁水“三脱”的反应器,不再需要铁水预脱硅。
复合吹炼转炉采用少渣冶炼工艺,脱碳升温并进行脱磷;通常采用多功能的RH 进行钢水精炼,深脱磷、深脱硫和脱气;转炉弱脱氧“沸腾”出钢,避免钢水吸氮,适宜冶炼超低氮钢;连铸采用保护浇注、夹杂物过滤等一系列技术措施,保证钢水质量。
(2) 钢水精炼洁净钢生产工艺;以欧美为代表,主要依靠转炉脱磷,并采用钢包喷粉深脱磷。
其技术特点是:采用转炉冶炼低碳钢脱磷,脱碳、脱硅、脱磷和升温精炼;转炉弱脱氧出钢,钢包喷粉深脱磷,然后扒渣;LF升温脱硫精炼;RH脱氧和深脱硫,连铸保护浇注;不适宜生产超低N和低P钢种。
(3) 两种精炼工艺的技术比较采用铁水“三脱”工艺,脱P的热力学、动力学条件优于铁水精炼工艺;铁水“三脱”工艺流程短,工艺简单,更适宜冶炼超纯净钢;铁水“三脱”工艺生产纯净钢,生产成本明显低于钢水精炼工艺洁净钢的成分控制--钢液碳的控制钢中碳对钢的性能影响最大,碳含量高能增加钢的强度,但使塑性下降、冲压性能变坏。
因此一般优质深冲型铝镇静钢要求[C]≤0.05%、IF钢要求[C]≤0.007%。
钢中碳的控制主要集中于两点:炉外精炼使钢中碳达到极低水平、防止连铸过程增碳。
RH处理脱碳主要受制约有以下两个因素:一是钢液环流量(是浸渍管直径的函数);二是钢液向气泡[C]传递速率(是真空室横截面积及搅拌能的函数)。
因此可以通过增加钢液循环流量和净化气体流量来提高反应速度。
其主要手段是增大浸渍管直径和吹Ar流量。
目前,国外RH处理,吹Ar流量有500NL/min的记录,浸渍管直径有达1m的记录,国外一些厂家RH处理后钢中[C]最好的降到9~12×10-4%。
防止增碳,首先是防止RH处理从真空罐渣壳中吸碳。
特别是钢包用炭化稻壳保温,这一现象就显得尤为突出。
其次是防止连铸过程中增碳。
中钢公司研究了中间包不同覆盖剂对增碳的影响,发现:使用炭化稻壳,增[C]11.7×10-4%;使用某种粒状保护渣,增[C]7.3×10-4%;使用Mg基粒状覆盖剂,增[C]3.5×10-4%。
法国Sollac Dumkirk厂研究发现,开浇和换钢包期间,增[C]严重,可达10~20×10-4%。
因此,为防止增碳应注重以下几点:一是进一步降低耐火材料中的[C]量,使钢水与含碳材料接触面最小;二是中间包使用含碳少的保温材料;三是减少结晶器保护渣中的[C]含量。
采用RH可以实现超低碳钢精炼。
但当钢中w([C])≤0.002%时,由于钢水静压力的影响,RH脱碳速度减弱,趋于停止。
为了进一步降低钢中含碳量,日本近几年开发出以下新工艺:(1)提高钢水循环流量Q,促进脱碳反应——REDA法。
新日铁八幡钢厂对350tDH 炉进行改造:取消真空室下部槽和吸嘴,将真空室直接插入钢水中,利用钢包底吹Ar搅拌能,大幅度提高RH钢水的循环流量。
使熔池混匀时间从80s降低到40~60s,脱碳速度明显提高。
处理20min,可保证钢水w([C])≤10×10-6;处理30min,钢水[C]可达到3×10-6。
(2)提高容量传质系数αk,促进脱碳反应。
日本川崎钢铁公司为实现超低碳钢冶炼,采用H2作为搅拌气体,吹入RH真空室。
利用RH真空脱气的功能,使H2气从钢液中逸出时增加了反应界面,提高RH的容量传质系数αk。
处理20min,可使钢中[C]达到3×10-6。
众所周知脱硫的热力学条件是高温、高碱度、低的氧化性,因此脱硫应注意以下三点:金属液和渣中氧含量要低、使用高硫容量的碱性渣、钢渣要混合均匀。
铁水预处理可以深度脱硫,也可以部分脱磷。
目前广泛采用在铁水包或鱼雷罐中喂线、喷粉的铁水预处理方法,,喷粉可以造就良好的动力学条件,极大扩展反应界面。
二次精炼是生产超低硫钢所必不可少的手段,所用方法主要为喷粉、真空、加热造渣、喂线、吹气搅拌,实践中常常是几种手段综合采用。
钢中的长条形(尤其是沿晶界分布的)硫化物是产生氢致裂纹的必然条件,对钢水进行钙处理可将其改变为球形,降低其危害,一般钙硫比(Ca/S)接近2为佳。
炉渣的脱硫能力决定于炉渣碱度和渣中FeO含量;对于高碱度炉渣,脱硫反应速度的限制性环节是金属侧硫的传质速度,增强熔池搅拌,有利于提高脱硫速度。
采用低碱度精炼渣可有效地消除钢中点状夹杂物。
实践证明,碱度控制在2.0~2.5范围内,渣量为2%时,脱硫率可达70%。
在EBT电炉出钢过程中投入的脱硫剂,若添加适量的萤石(<10%),可显著提高脱硫效果,且不会对钢包的使用寿命构成危害。
通过含BaO和不含BaO渣系的脱硫动力学对比实验表明:含BaO脱硫渣系具有比不含BaO的脱硫渣系有更快的脱硫速率。
含BaO精炼渣系具有较好的深脱硫作用,在实验室条件下,可将钢中硫稳定的脱除至5×10-6以下,完全适用于极低硫钢的精炼。