轴承的选择与设计概要
机械设计基础中的轴承选择与设计
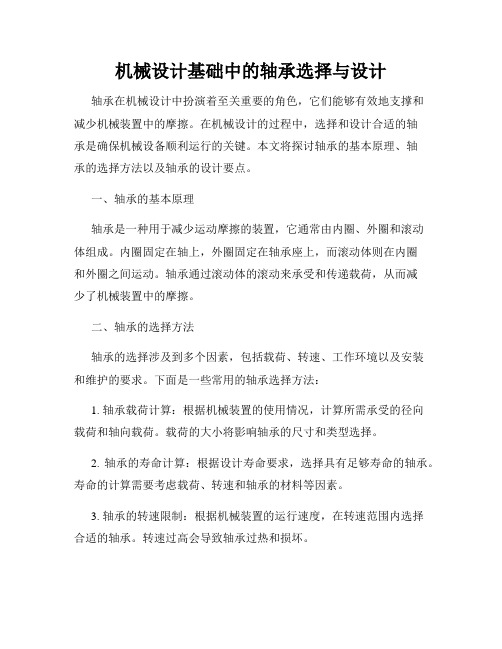
机械设计基础中的轴承选择与设计轴承在机械设计中扮演着至关重要的角色,它们能够有效地支撑和减少机械装置中的摩擦。
在机械设计的过程中,选择和设计合适的轴承是确保机械设备顺利运行的关键。
本文将探讨轴承的基本原理、轴承的选择方法以及轴承的设计要点。
一、轴承的基本原理轴承是一种用于减少运动摩擦的装置,它通常由内圈、外圈和滚动体组成。
内圈固定在轴上,外圈固定在轴承座上,而滚动体则在内圈和外圈之间运动。
轴承通过滚动体的滚动来承受和传递载荷,从而减少了机械装置中的摩擦。
二、轴承的选择方法轴承的选择涉及到多个因素,包括载荷、转速、工作环境以及安装和维护的要求。
下面是一些常用的轴承选择方法:1. 轴承载荷计算:根据机械装置的使用情况,计算所需承受的径向载荷和轴向载荷。
载荷的大小将影响轴承的尺寸和类型选择。
2. 轴承的寿命计算:根据设计寿命要求,选择具有足够寿命的轴承。
寿命的计算需要考虑载荷、转速和轴承的材料等因素。
3. 轴承的转速限制:根据机械装置的运行速度,在转速范围内选择合适的轴承。
转速过高会导致轴承过热和损坏。
4. 轴承的工作环境:考虑机械装置的工作环境,包括温度、湿度、腐蚀性气体等因素,选择耐腐蚀和适应环境变化的轴承。
5. 轴承的安装和维护要求:根据机械装置的安装和维护要求,选择易于安装和维护的轴承。
注意轴承的安装方法和润滑方式等因素。
三、轴承的设计要点在进行轴承设计时,需要考虑以下几个重要的要点:1. 轴承的几何尺寸:确定轴承的内径、外径和宽度等几何尺寸。
合理的几何尺寸能够确保轴承在承受载荷时保持稳定。
2. 轴承的材料选择:选择适合工作条件的轴承材料,包括轴承内圈、外圈和滚动体的材料。
常见的轴承材料有钢、陶瓷和塑料等。
3. 轴承的润滑方式:确定轴承的润滑方式,包括油润滑和脂润滑。
润滑方式的选择应考虑机械装置的运行速度和工作环境等因素。
4. 轴承的密封方式:选择适当的轴承密封方式,以防止外界杂质进入轴承并确保润滑油或脂膜的有效性。
机械设计基础机械设计中的轴承选择与设计
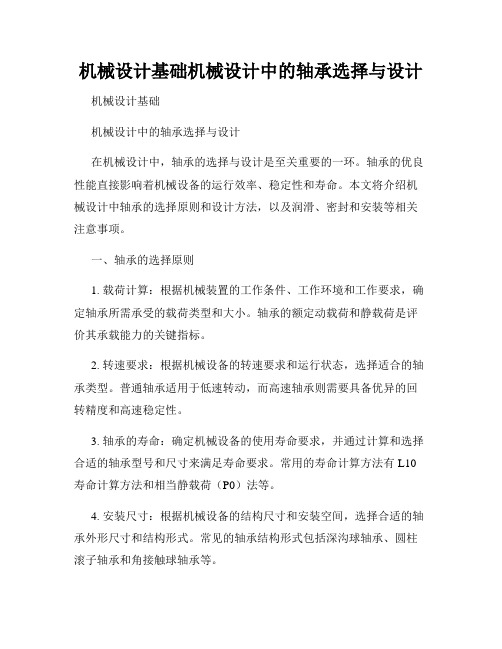
机械设计基础机械设计中的轴承选择与设计机械设计基础机械设计中的轴承选择与设计在机械设计中,轴承的选择与设计是至关重要的一环。
轴承的优良性能直接影响着机械设备的运行效率、稳定性和寿命。
本文将介绍机械设计中轴承的选择原则和设计方法,以及润滑、密封和安装等相关注意事项。
一、轴承的选择原则1. 载荷计算:根据机械装置的工作条件、工作环境和工作要求,确定轴承所需承受的载荷类型和大小。
轴承的额定动载荷和静载荷是评价其承载能力的关键指标。
2. 转速要求:根据机械设备的转速要求和运行状态,选择适合的轴承类型。
普通轴承适用于低速转动,而高速轴承则需要具备优异的回转精度和高速稳定性。
3. 轴承的寿命:确定机械设备的使用寿命要求,并通过计算和选择合适的轴承型号和尺寸来满足寿命要求。
常用的寿命计算方法有L10寿命计算方法和相当静载荷(P0)法等。
4. 安装尺寸:根据机械设备的结构尺寸和安装空间,选择合适的轴承外形尺寸和结构形式。
常见的轴承结构形式包括深沟球轴承、圆柱滚子轴承和角接触球轴承等。
5. 环境适应性:考虑机械设备的工作环境,选择适应特定工况需求的轴承材料和润滑方式。
常见的轴承材料有高碳铬钢、不锈钢、聚四氟乙烯和陶瓷等。
二、轴承的设计方法1. 载荷分析:通过对机械装置的工作原理和受力情况的分析,确定主要受力部位和受力方向,进而计算出轴承所需的载荷大小和方向。
2. 选型计算:根据已确定的载荷和工作条件,借助轴承手册或专业软件进行选型计算。
选型时需要考虑轴承额定动载荷、静载荷、转速限制和寿命等参数。
3. 轴承布局:根据机械设备的结构特点和轴承的尺寸,确定轴承的布局方式。
合理的轴承布局可以提高机械设备的传动效率和稳定性。
4. 轴承内部设计:根据轴承所承受的载荷和运行条件,设计轴承内部结构,包括滚动体数量、尺寸、角接触、接触角度和保持架等参数。
三、润滑、密封和安装1. 润滑方式:根据工作条件和轴承的要求,选择合适的润滑方式。
直线轴承的选型与计算
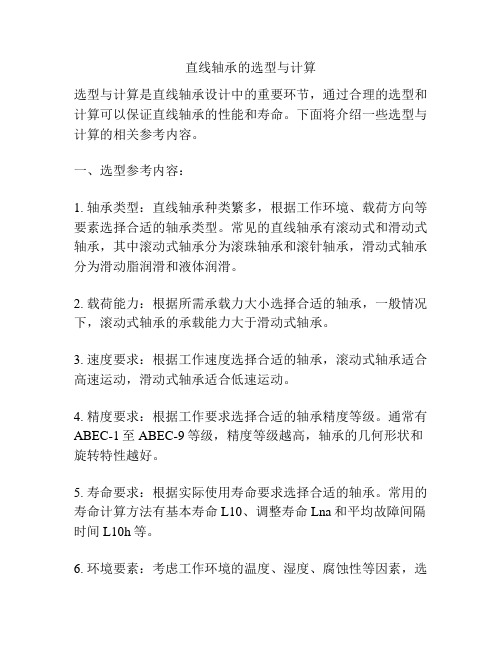
直线轴承的选型与计算选型与计算是直线轴承设计中的重要环节,通过合理的选型和计算可以保证直线轴承的性能和寿命。
下面将介绍一些选型与计算的相关参考内容。
一、选型参考内容:1. 轴承类型:直线轴承种类繁多,根据工作环境、载荷方向等要素选择合适的轴承类型。
常见的直线轴承有滚动式和滑动式轴承,其中滚动式轴承分为滚珠轴承和滚针轴承,滑动式轴承分为滑动脂润滑和液体润滑。
2. 载荷能力:根据所需承载力大小选择合适的轴承,一般情况下,滚动式轴承的承载能力大于滑动式轴承。
3. 速度要求:根据工作速度选择合适的轴承,滚动式轴承适合高速运动,滑动式轴承适合低速运动。
4. 精度要求:根据工作要求选择合适的轴承精度等级。
通常有ABEC-1至ABEC-9等级,精度等级越高,轴承的几何形状和旋转特性越好。
5. 寿命要求:根据实际使用寿命要求选择合适的轴承。
常用的寿命计算方法有基本寿命L10、调整寿命Lna和平均故障间隔时间L10h等。
6. 环境要素:考虑工作环境的温度、湿度、腐蚀性等因素,选择耐腐蚀、耐高温或特殊环境下使用的轴承。
二、计算参考内容:1. 轴承载荷计算:根据工作载荷大小计算轴承所受力,并根据轴承的载荷能力选择合适的轴承型号。
2. 轴承寿命计算:根据工作条件和要求计算轴承的基本寿命L10、调整寿命Lna或平均故障间隔时间L10h。
其中基本寿命L10是一定数量的轴承在同样的负荷下无故障运行的寿命,调整寿命Lna是根据实际应力、轴承标称寿命及使用寿命系数计算的轴承寿命。
3. 轴承选择计算:根据轴承装配尺寸和工作条件等计算选用合适的轴承型号和数量。
4. 润滑计算:根据轴承摩擦需要选择适当的润滑方式,包括润滑脂润滑和液体润滑,并计算所需的润滑剂量。
5. 轴承温升计算:根据轴承所受载荷、工作速度、环境温度等因素计算轴承的温升情况,以确保轴承正常工作。
以上是直线轴承选型与计算的一些相关参考内容。
在实际应用中,根据具体情况和要求,还需要考虑其他因素,如振动、噪音、安装方式等。
滚动轴承的设计和选择
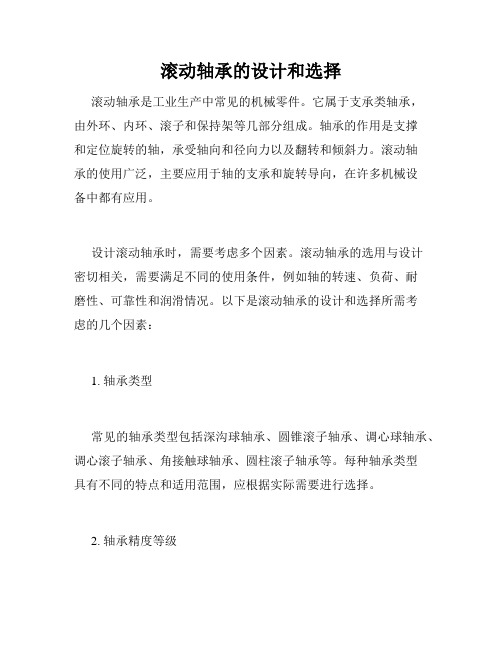
滚动轴承的设计和选择滚动轴承是工业生产中常见的机械零件。
它属于支承类轴承,由外环、内环、滚子和保持架等几部分组成。
轴承的作用是支撑和定位旋转的轴,承受轴向和径向力以及翻转和倾斜力。
滚动轴承的使用广泛,主要应用于轴的支承和旋转导向,在许多机械设备中都有应用。
设计滚动轴承时,需要考虑多个因素。
滚动轴承的选用与设计密切相关,需要满足不同的使用条件,例如轴的转速、负荷、耐磨性、可靠性和润滑情况。
以下是滚动轴承的设计和选择所需考虑的几个因素:1. 轴承类型常见的轴承类型包括深沟球轴承、圆锥滚子轴承、调心球轴承、调心滚子轴承、角接触球轴承、圆柱滚子轴承等。
每种轴承类型具有不同的特点和适用范围,应根据实际需要进行选择。
2. 轴承精度等级轴承精度等级决定了轴承在旋转时的稳定性、噪声和寿命等特性。
标准的轴承精度等级由高到低依次为P0、P6、P5、P4、P2。
在实际应用中,一般选择P5或P4等级的轴承。
3. 轴承负荷轴承负荷分为径向负荷、轴向负荷和复合负荷。
在设计和选择轴承时,需要考虑到轴承的额定静载荷和额定动载荷,并根据工作负荷确定实际的轴承尺寸。
4. 轴承尺寸和材料轴承的尺寸和材料的选择要根据受力情况和轴承使用环境来确定。
轴承的尺寸通常由外径、内径和厚度等参数来定义,轴承材料应具有高的强度、硬度和耐磨性,在选择时应考虑经济性和可靠性。
5. 轴承的润滑方式轴承的润滑方式有干摩擦润滑和润滑油润滑两种。
干摩擦润滑是指轴承在不需要油脂或润滑油的情况下能够正常工作,并且还能够减小生产成本。
润滑油润滑则需要使用润滑油来润滑,以减少轴承的磨损和延长使用寿命。
除以上因素外,滚动轴承的设计和选择时还需要考虑噪音、震动和可靠性等因素。
实际应用中,为了保证轴承的长期可靠性,其工作寿命需要预计和估算。
同时应根据实际工况选取合适的轴承类型和材料,并为轴承提供充足的润滑和保养。
总的来说,滚动轴承的设计和选择需要考虑众多因素,只有在加以综合考虑的前提下才能满足实际需要。
轴承设计和选用
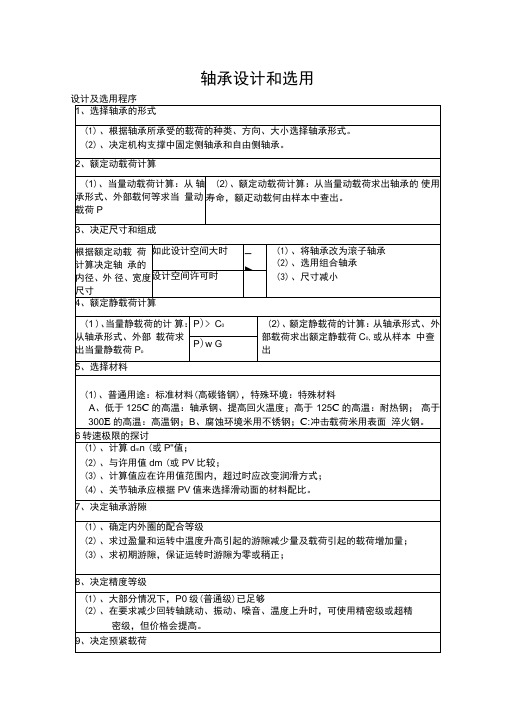
轴承设计和选用设计及选用程序轴承性能:一、深沟球轴承:1、结构特点:一般由内圈、外圈、保持架和一组钢球组成,是使用最为简单、广泛、和价格较低的一种轴承。
2、载荷及转速特性:主要承受径向载荷,但也用于承受径向和轴向的联合载荷,其中轴向载荷不应超过未被利用的径向载荷的70%;在转速很高不宜采用推力轴承时,本轴承可以承受双向纯轴向载荷;此时轴承所承受的轴向载荷一般不应超过0.25~0.5C;3、轴向限位能力与对轴线歪斜的敏感性:深沟球轴承可以将轴(外壳)的两面轴向移动限制在轴承的轴向游隙内,轴承的内圈(轴)相对于外圈(外壳)的相对位置误差应加以控制,两轴线的相互倾斜角一般不宜超过2' ~10'双列深沟球轴承的相互倾斜角一般不宜超过2',在这个限度内轴承能正常工作。
当轴承游隙增大时,倾斜角也相应增大,并且具有角接触球轴承的特性,可承受较大的轴向载荷,但轴承的倾斜角愈大,轴承使用寿命也随之有所缩短,并会出现较大的运行噪音。
4、适用范围:与外型尺寸相同的其它类轴承相比,具有摩擦力最小、允许转速最高的特点,适用于刚性的双支承轴,支承间距离小于轴承内径十倍的短轴。
二、调心球轴承:1、结构特点:一般有两列钢球,外圈的内滚道表面为内球面、在内圈轴线与外圈轴线有较大的倾斜时仍能正常工作。
2、载荷及转速特性:主要承受径向载荷,但也可同时承受较小的轴向载荷,不能承受纯轴向载荷,因为在纯轴向载荷作用下会只有一列滚子在工作,会大大减少轴承寿命,允许的转速低于深沟球轴承。
3、轴向限位能力与对轴线歪斜的敏感性:这类轴承可以将轴(外壳)的两面轴向移动限制在轴承的轴向游隙内,但轴向限位的精度较低,对轴线歪斜误差的补偿能力最强,轴承的内圈(轴)相对于外圈(外壳)的相互倾斜角一般可达2°~3°,实际许用的倾角取决于轴承的配置设计及密封形式。
4、适用范围:适用于多支承的传动轴,在外载荷的作用下有较大弯曲的双支承轴,轴承在外壳配合处不能保证严格同轴度的机构中,还可以用于车辆经受颠簸的轮轴上。
轴承设计和选用

轴承设计和选用
轴承设计和选用是机械设计和维护的关键任务之一。
下面是一些关键的考虑因素:
1. 轴承类型:根据应用需求和工作条件选择合适的轴承类型,如球轴承、滚子轴承、滑动轴承等。
2. 载荷和转速:根据轴承所需要承受的载荷和旋转速度来确定轴承的尺寸和类型。
载荷主要分为径向载荷和轴向载荷,而转速决定了轴承的疲劳寿命。
3. 环境条件:考虑环境中的温度、湿度、腐蚀性和污染程度等因素,选择适合的轴承材料和润滑方式。
4. 安装和维护需求:考虑轴承的安装和维护便捷性,以及可能的振动和噪音控制要求。
5. 经济性:在设计和选用轴承时,需要综合考虑轴承的价格、寿命和性能等因素,以确保经济合理性。
除了上述因素外,还应该进行轴承的正确安装和定期维护,以延长轴承的使用寿命。
同时,需要根据实际情况对轴承进行监测和检修,及时处理可能的问题。
机械设计中的轴承选型计算要点
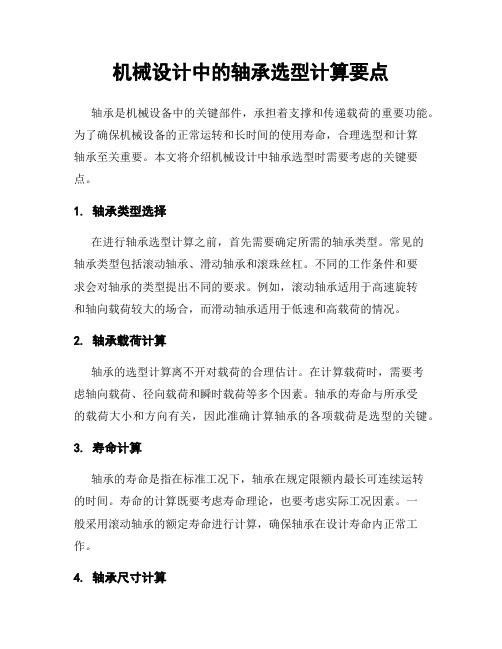
机械设计中的轴承选型计算要点轴承是机械设备中的关键部件,承担着支撑和传递载荷的重要功能。
为了确保机械设备的正常运转和长时间的使用寿命,合理选型和计算轴承至关重要。
本文将介绍机械设计中轴承选型时需要考虑的关键要点。
1. 轴承类型选择在进行轴承选型计算之前,首先需要确定所需的轴承类型。
常见的轴承类型包括滚动轴承、滑动轴承和滚珠丝杠。
不同的工作条件和要求会对轴承的类型提出不同的要求。
例如,滚动轴承适用于高速旋转和轴向载荷较大的场合,而滑动轴承适用于低速和高载荷的情况。
2. 轴承载荷计算轴承的选型计算离不开对载荷的合理估计。
在计算载荷时,需要考虑轴向载荷、径向载荷和瞬时载荷等多个因素。
轴承的寿命与所承受的载荷大小和方向有关,因此准确计算轴承的各项载荷是选型的关键。
3. 寿命计算轴承的寿命是指在标准工况下,轴承在规定限额内最长可连续运转的时间。
寿命的计算既要考虑寿命理论,也要考虑实际工况因素。
一般采用滚动轴承的额定寿命进行计算,确保轴承在设计寿命内正常工作。
4. 轴承尺寸计算根据载荷和寿命的计算结果,可以确定轴承的尺寸。
对于滚动轴承,需要考虑内径、外径和宽度等参数。
为了保证轴承的正常工作,需要参考相关的标准和规范,计算出合适的轴承尺寸。
5. 温度和润滑计算轴承在工作过程中会产生热量,因此需要计算轴承的工作温度。
温度过高会对轴承寿命和性能造成不良影响,因此需要合理选择润滑方式和材料,保证轴承的工作温度在可接受范围内。
6. 安装和维护要求在进行轴承选型之前,需要考虑轴承的安装和维护要求。
轴承的正确安装和定期的维护保养对于确保轴承的正常工作和延长轴承寿命非常重要。
7. 选型软件的应用为了简化轴承选型计算过程,可以借助各种轴承选型软件来辅助计算。
这些软件不仅可以提供轴承选型的准确计算结果,还能提供更多关于轴承的技术参数和性能指标,帮助设计人员更好地选择合适的轴承。
总结在机械设计中,轴承的选型计算是一个复杂的过程,需要综合考虑多个因素。
机械设计中的轴承选择与设计

机械设计中的轴承选择与设计轴承是机械设计中非常重要的一个组成部分,它承载着机械设备的旋转部件,起着支撑和减小摩擦的作用。
准确选择和设计轴承可以确保机械设备的正常运行和延长使用寿命。
本文将从轴承的选择和设计两个方面进行探讨,旨在帮助读者更好地理解机械设计中轴承的重要性和应用。
一、轴承的选择在进行轴承选择时,需要考虑以下几个因素:1. 轴承负载能力:根据机械设备的工作条件和负载要求,确定轴承的额定负载。
根据经验公式和相关标准,计算出所需的额定负载,并选择相应的轴承类型和规格。
2. 轴承转速:根据机械设备的工作转速范围,选择适应的轴承。
通常情况下,轴承有一个额定转速范围,超过该范围可能会导致轴承失效。
3. 轴承寿命:根据机械设备的使用寿命要求,选择适合的轴承。
不同类型的轴承有不同的额定寿命,需要根据设备的使用条件进行合理选择。
4. 轴承摩擦损失:轴承的摩擦损失会导致能量损耗和热量产生,影响机械设备的效率和稳定性。
因此,在选择轴承时,要考虑轴承的运行摩擦损失,并尽量选择低摩擦系数、高效率的轴承。
5. 轴承材料和润滑方式:不同的工作条件需要选择适合的轴承材料和润滑方式。
轴承材料可以选择金属材料、聚合物材料或陶瓷材料,而润滑方式可以是干摩擦、润滑脂或润滑油。
二、轴承的设计轴承的设计是指根据机械设备的工作要求和轴承的选择结果,对轴承进行具体的尺寸定位和结构设计。
1. 轴承尺寸设计:根据所选择的轴承类型和规格,确定轴承的内径、外径和宽度等尺寸。
在确定了轴承的负载和转速后,可以根据相关公式计算出所需的尺寸,并进行合理的修正。
2. 轴承间隙设计:轴承间隙是指轴承内部各零部件之间的间隙,它会直接影响到轴承的运行性能和寿命。
根据设备的工作条件和要求,选择适当的轴承间隙,并根据实际情况进行设计。
3. 轴承安装设计:轴承的安装方式及其设计也是轴承设计的重要部分。
根据设备的结构和要求,选择适当的安装方式,并提供合适的安装孔和支持结构。
- 1、下载文档前请自行甄别文档内容的完整性,平台不提供额外的编辑、内容补充、找答案等附加服务。
- 2、"仅部分预览"的文档,不可在线预览部分如存在完整性等问题,可反馈申请退款(可完整预览的文档不适用该条件!)。
- 3、如文档侵犯您的权益,请联系客服反馈,我们会尽快为您处理(人工客服工作时间:9:00-18:30)。
→e1在0.26-0.28之间,插值得 e1 = 0.27
②求X、Y: Fa1/R1 = 1606/3500 = 0.459>e
X1=0.56, Y1=1.7 ∵Fa2=0 X2=1, Y2=0
③求P:
P1=fP(X1R1+Y1Fa1)=1.2(0.56×3500+1.7×1606) =5628N P2=fPR2=1.2×2500=3000N ∵P1>P2 ∴1轴承危险, 计算1的寿命
§15—7 滚动轴承的组合设计
正确选用轴承类型和型号之后,为了保证轴与轴 上旋转零件正常运行,还应解决轴承组合的结构问题, 其中包括,轴承组合的轴向固定,轴承与相关零件的 配合,间隙调整、装拆、润滑等一系列问题。
一、滚动轴承内、外圈的轴向定位
表15-9 滚动轴承内圈的轴向固定方法
表15-10 滚动轴承外圈的轴向固定方法
§ 滚动轴承失效形式、寿命 计算和静强度计算
一 、滚动轴承的失效形式及设计准则
(1)疲劳破坏(点蚀) ←疲劳接触应力→ 寿命计算 (2)塑性变形 (3)磨损
←n极低、F较大 →静强度计算
润滑不良,杂质、灰尘的侵入→暂无公式
1. 疲劳点蚀
安装润滑和维护良好
2. 塑性变形
转速很低或作间歇摆动
3. 磨损 润滑不良、 密封不严、 多尘条件
一端支承的轴承,内、外圈双向固定,另一端 支承的轴承可以轴向游动。双向固定端的轴承可承 受双向轴向载荷,游动端的轴承端面与轴承盖之间 留有较大的间隙。以适应轴的伸缩量,这种支承结 构适用于轴的温度变化大和跨距较大的场合。
3、两端游动
两端游动支承结构的轴承,分别不对轴作精确的 轴向定位。两轴承的内、外圈双向固定,以保证轴能 作双向游动。两端采用圆柱滚子轴承支承,适用于人 字齿轮主动轴。但与其啮合的另一轴系必须两端固定。
→Fd1+Fae+S1=Fd2
∴┌ Fa1= Fd1+S1=Fd2-Fae └ Fa2= Fd2
S1
Fae
Fd1
Fd2
计算轴向载荷的方法: ① 画安装简图→标明轴承的派生轴向力Fd方向 ② 计算Fd1、Fd2 ③ 根据Fd1、Fae、Fd2三者的关系判断压紧、放松端 压紧端=除本身的派生轴向力外其余轴向力之和 放松端=本身的派生轴向力 判断压紧、放松端时要注意正、反装 ⑴当Fd1+Fae>Fd2 右边压紧 左边压紧 2 Fae 1 Fae Fd1 F d2 Fd1 Fd2 R2 R1 左边压紧 右边压紧 ⑵当Fd1 +Fae < Fd2
例1:已知齿轮轴采用一对6211轴承,已知轴承 载荷R1=3500N,Fa1=1606N,R2=2500N,Fa2=0 fP=1.2,试求P1、P2。
0.28 0.26 解:查得:C0=29200N e1 0.28 1.03 0.6891.03 0.8085
f0Fa1/C0 =14.7×1606/29200 = 0.8085 ①查e :
2. 轴承的转速 若轴承的尺寸和精度相同,则球轴承的极限转速 比滚子轴承高,所以当转速较高且旋转精度要求较高 时,应选用球轴承. 推力轴承的极限转速低。当工作转速较高,而轴 向载荷不大时,可采用角接触球轴承或深沟球轴承。
对高速回转的轴承,为减小滚动体施加于外圈滚道 的离心力,宜选用外径和滚动体直径较小的轴承。一 般应保证轴承在低于极限转速条件下工作。 若工作转速超过轴承的极限转速,可通过提高轴承 的公差等级、适当加大其径向游隙等措施来满足要求。
四. 滚动轴承的安装与拆卸
轴承内圈与轴颈配合较紧,对于小尺寸的轴 承,一般可用压力直接将轴承的内圈压入轴颈。 对于尺寸较大的轴承,可先将轴承放在温度为80100℃的热油中加热,使内孔胀大,然后用压力机 装在轴颈上。拆卸轴承时应使用专用工具。为便 于拆卸,设计时轴肩高度不能大于内圈高度。
滚动轴承的装拆要求: 1)压力应直接加于配合较紧的套圈上 2)不允许通过滚动体传递装拆力 3)要均匀施加装拆力
2 Fd2
R2
四. 轴承寿命计算步骤
→求Fa1、Fa2→ 求P1、P2→ 求Lh(C′) 求 R 1、 R 2 例3:接上题,如果n=960r/min,fP=1.2, 求轴承寿命。
解:查得7212AC轴承的C=42800N,e=0.68 Fa1/R1=7440/5000=1.488>e R1=5000N, R2=8000N Fa1=7440N Fa2=5440N
轴承的选择与设计
§6 滚动轴承类型的选择
1. 载荷条件 轴承承受载荷的大小、方向和性质是选择轴 承类型主要依据。如载荷小而平稳时,可选球轴 承;载荷大又有冲击时,宜选滚子轴承;如轴承 仅受径向载荷时,选径向接触球轴承或圆柱滚子 轴承; 只受轴向载荷时,宜选推力轴承; 轴承同时受径向和轴向载荷时,选用角接触轴 承。轴向载荷越大,应选择接触角越大的轴承, 必要时也可选用径向轴承和推力轴承的组合结构。 应该注意推力轴承不能承受径向载荷,圆柱滚子 轴承不能承受轴向载荷。
3. 调心性能 轴承内、外圈轴线间的偏移角应控制在极限值之 内,否则会增加轴承的附加载荷而降低其寿命。 对于刚度差或安装精度差的轴系,轴承内、外圈 轴线间的偏位角较大,宜选用调心类轴承。 如调心球轴承(1类)、调心滚子轴承(2类)等。
4. 允许的空间 当轴向尺寸受到限制时,宜选用窄或特窄的轴承。 当径向尺寸受到限制时,宜选用滚动体较小的轴承。 如要求径向尺寸小而径向载荷又很大时,可选用滚 针轴承。
1.滚动轴承内圈轴向紧固常用方法。
(a)弹性挡圈和轴肩 (b)轴端端盖和轴肩 (c)圆螺母和轴肩 (d)圆螺母和止推垫圈
2.滚动轴承外圈轴向紧固常用方法
(a) 弹性挡圈紧固 (c) 端盖紧固
(b) 止动环紧固 (d) 螺纹环紧固
二、轴系的固定
正常的滚动轴承支承 应使轴能正常传递载荷而 不发生轴向窜动及轴受热 膨胀后卡死等现象。常用 的滚动轴承支承结构型式 有三种: 1、两端单向固定
5. 装调性能 圆锥滚子轴承(3类)和圆柱滚子轴承(N类) 的内外圈可分离,装拆比较方便。 6. 经济性 在满足使用要求的情况下应尽量选用价格低 廉的轴承。一般情况下球轴承的价格低于滚子轴 承。轴承的精度等级越高,其价格也越高。
在同尺寸和同精度的轴承中深沟球轴承的价格最 低。 同型号、尺寸,不同公差等级的深沟球轴承的价 格比约为P0∶P6∶P5∶P4∶P2≈1∶1.5∶2∶7∶10。 如无特殊要求,应尽量选用普通级精度轴承,只 有对旋转精度有较高要求时,才选用精度较高的轴承。 除此之外,还可能有其他各种各样的要求,如轴 承装置整体设计的要求等。因此设计时要全面分析比 较,选出最合适的轴承。
3. 滚动轴承的额定动载荷 额定动载荷:当轴承额定寿命为106转时, 轴承能承受的最大载荷,用C表示。 C ={ Cr——径向载荷或分量 Ca——轴向载荷
C
(二) 滚动轴承寿命的计算公式
C=25.6
轴承寿命曲线:
LC 常数
LP C 常数
1 2 3 4
L10
轴承寿命计算公式
式中:n——转速 r/min ε——寿命指数(球轴承ε=3; 滚子轴承ε=10/3) P——当量动载荷 假定的载荷→与实际载荷相当 高温下轴承C值将减小,引入温度系数ft 表14—13
d
Fd
(2)安装型式(成对使用)
角接触轴承应成对使用→以抵消派生轴向力和避 Fd1 免轴产生轴向窜动 Fd2 ①正安装( X 型、面对面)→ 两轴承外圈的窄边相对→Fd面对面 Fd1 跨距减少 ②反安装( O型、背对背)→ 两轴承外圈的宽边相对→Fd背对背 跨距增大 说明:轴承支点(压力中心)偏移,但为方便计 算,仍取轴承宽度中点为支点
m6
n6
0
js6
j6
k6
轴承内径公差带
G7,H7,JS7,J7
7
0
6
G7 轴承座孔公差带 H7 Js7 J7
轴承外径公差带
滚动轴承配合的选择原则: 1)转动圈比不动圈配合松一些
2)高速、重载、有冲击、振动时,配合应紧一些, 载荷平稳时,配合应松一些
3)旋转精度要求高时,配合应紧一些 4)常拆卸的轴承或游动套圈应取较松的配合 5)与空心轴配合的轴承应取较紧的配合。
Fd2
(3)角接触轴承的轴向载荷Fa1、 Fa2 轴向载荷┌轴上外载荷Fae→Fa=? └轴承的派生轴向力Fd Fd1 分析: Fd1 +Fae与 Fd2比较
Fae
S2
Fd2
⑴当Fd1+Fae>Fd2 →右边压紧→S2 ┌ Fa1= Fd1 → Fd1+Fae=Fd2+S2 └ Fa2= Fd2+S2=Fd1+Fae ⑵当Fd1+Fae<Fd2→ 左边压紧→S1
二、轴承的寿命计算 (一)寿命出现疲劳点蚀前,一个套圈相对 另一套圈的转数或工作小时数。 2.基本额定寿命L10: 指一批相同的轴承,在相同工作条件下,有90% 的轴承没有发生疲劳点蚀前的转数或总工作小时数。 含义:⑴一批轴承中有90%的寿命将比其基本额 定寿命长;⑵一个轴承在基本额定寿命期内正常工作 的概率有90%,失效率为有10%
DH7
滚动轴承配合是指内圈与轴颈、 外圈与外壳孔的配合。 内孔与轴的配合采用基孔制,外 径与外壳孔的配合采用基轴制。 轴承内圈与轴 基孔制:松 →紧 js6,j6,k6,m6,n6 轴承外圈与轴承座孔 基轴制:松 →紧
d k6
三、配合 1、滚动轴承与轴和座孔的配合
0
轴承外径公差带
轴外径公差带
②判 Fa/Fr 与 e 的关系→定X、Y
Fa/Fr ≤e-轴向力较小,可忽略不计,只计R→ P=fPR 即:X=1 , Y=0 Fa/Fr >e -轴向力较大,要计 即:X≠1, Y≠0
只能承受纯径向载荷的轴承(N、NA类):P=fP Fr