变速器齿轮断裂失效分析
高速动车组齿轮箱断齿故障分析刘昊霖

高速动车组齿轮箱断齿故障分析刘昊霖发布时间:2021-07-30T08:37:02.482Z 来源:《中国科技人才》2021年第12期作者:刘昊霖[导读] 为进一步精准掌握高速动车组齿轮箱动力学响应,更高效分析高速动车组故障齿轮箱系统振动特性,从本质解决开发动车组齿轮箱故障检测存在不足。
基于相关参数模拟构建相应的模式,通过仿真模拟正常工况各断齿故障,获取相应的检测方案点的响应状况,最终数据显示,断齿故障会增强其振动能量,出现振动冲击特征,啮合频次降低。
本文就高速动车组齿轮箱断齿故障振动特性分析,为后续采取故障检测开发提供便捷。
刘昊霖中车唐山机车车辆有限公司河北唐山 063035摘要:为进一步精准掌握高速动车组齿轮箱动力学响应,更高效分析高速动车组故障齿轮箱系统振动特性,从本质解决开发动车组齿轮箱故障检测存在不足。
基于相关参数模拟构建相应的模式,通过仿真模拟正常工况各断齿故障,获取相应的检测方案点的响应状况,最终数据显示,断齿故障会增强其振动能量,出现振动冲击特征,啮合频次降低。
本文就高速动车组齿轮箱断齿故障振动特性分析,为后续采取故障检测开发提供便捷。
关键词:高速动车组;齿轮箱;断齿故障齿轮传动系统作为高速动车核心构成,由于其自身传动特征,决定齿轮箱高发故障,对齿轮箱故障进行诊断,对高速动车行车安全性及可靠性至关重要。
齿轮箱安装位置具有一定隐蔽性,且结构复杂繁琐,拆卸难度较大,对齿轮箱故障无损检测技术需求日渐增强。
我国高速动车组故障诊断技术受时间限制,应用缺乏一定的成熟性,影响其故障位置精准确定。
本文通过构建仿真模型,分析其实际振动机理,方针齿轮正常、断齿振动信号,组中掌握其故障出现振动特征,为齿轮箱故障诊断算法提供保证。
一、齿轮箱多体动力学按照多刚体系统动力学为理论基础,构建完善的构架、轮对和齿轮箱计算模型,车辆系统各级悬挂、轴承和C型架结构选取相应的弹簧、阻尼衔接。
构造系统与各部件垂向动力学方程如(1):G+Fr+Fa=0(1)Gb+Fp+Fc+Fb=0(2)Gg+Fc+Fg=0(3)Gw+Fr+Fp+Fw=0(4)式(1)为系统动力学方程,G为系统整体实际重量;Fr为轨道对轮对实际陈承载力;Fa为系统惯性力;式(2)是系统中构架动力学方程,其中Gb为构架重量的1/2;Fp为一系悬挂实际作用力;Fc为C型架作用力;Fb为构架惯性力。
机械基础-齿轮传动失效分析

二、齿面点蚀
产生原因 接触应力——疲劳裂纹 ——裂纹扩展——麻点状小坑
二、齿面点蚀
发生场合及产生部位
发生在:闭式齿轮传动中 靠近节线的齿根面处
二、齿面点蚀
预防措施
提高齿面硬度 降低表面粗糙度值 改善润滑条件 改变设计参数
轮齿折断
齿面点蚀
齿面磨损
齿面胶合
塑性变形
一、轮齿折断
产生原因 疲劳折断 过载折断
一、轮齿折断
硬齿面(齿面硬度>350HBW)闭式传动齿轮,失效形式是轮齿折断
发生场合及产生部位 发生在:开式齿轮传动和 闭式硬齿面齿轮传动中 直齿轮:全齿折断 斜齿轮:局部折断
一、轮齿折断
硬齿面(齿面硬度>350HBW)闭式传动齿轮,失效形式是轮齿折断
带式输送机的设计
学习导图
CONTENTS
一、轮齿折断 二、齿面点蚀 三、齿面磨损 四、齿面胶合 五、塑性变形 六、总结
任务导入
某齿轮箱,齿轮使用一段时间后发生如下损坏,请分析失效形式,产生原因, 提出防止失效措施。
任务导入
齿轮设计首要考虑齿轮在传动中不发生失效,常见的齿轮失效一般发生在轮齿 上。
三、齿面磨损
产生原因 硬质微粒进入——轮齿表面磨损
三、齿面磨损
发生场合及产生部位
发生在:开式齿轮传动中 全齿面磨损
三、齿面磨损
预防措施
加防护装置 提高齿面硬度 减小接触应力 降低表面粗糙度值 保持润滑油的清洁
四、齿面胶合
产生原因
压力大,温度升高 ——金属相互粘连 ——粘住的地方被撕破——带状或 大面积的伤痕
四、齿面胶合
减速机高速齿轮轴断裂失效分析

减速机高速齿轮轴断裂失效分析摘要:本文通过分析减速机高速轴位置的断口的宏观上的特性,及表面的金相组织,化学成分以及硬度等方面的物理性质加以观察和分析,同时进行相关的测试。
由实验所得数据结果显示出,减速机的高速轴并未按照图纸上的要求选用42crmo钢;在使用之前也没有按照所规定的进行调制处理。
由于键槽并未按照规定的位置设计以及原材料组织上的缺陷导致其发生早期断裂现象而导致最终失效。
关键词:高速轴;魏氏体组织;;断裂;失效中图分类号:tg115 文献标识码:a 文章编号:1674-7712 (2013)02-0151-01在某工厂二辊压机构中的减速机高速轴上线运行13天后出现了断裂的现象。
在之前给出的图纸样例中提到了,这个轴的制造图纸上对于原材料的要求是42crmo锻钢,硬度为270~300hb,调质热处理。
同时还要对端口位置的宏观上的形态,金相组织,物理性质如硬度以及化学成分等进行相应的观察和测试,进而为今后这类轴零件的生产量的提升,以及在具体应用时候的使用提供有效的理论参考。
进而防止断裂一类的事件发生。
一、对于检测结果的分析和研究(一)端口宏观相貌的观察结果。
轴同轴间的过渡和链接的位置是减速机高速轴发生断裂的最主要的地方。
此处直径大小发生突变,最为关键的是这是轴的直径最小的地方。
结构圆角的常见现象由于截面形状的变化以及轴间和轴的相交位置的几何关系处于垂直的状态而导致必将会出现的应力集中现象。
端口经常见到的形貌特点便是具有很高的脆性以及较为平整,例如一种极为常见的是扭转应力所导致的断裂口。
只有受力的地方才是裂纹出现的根源,及轴键槽的受力的一面。
应力的大小和半径的大小呈现反比的关系,也就是说半径较小的地方应力则很大。
半径最小的便是轴键槽的根部位置,在此处经常出现应力集中地现象从而承受很大的拉应力;如果不进行强化处理就会提高出现裂纹(这种裂纹是由于疲劳产生的),对于轴类具有很强的破坏性,出现提前失效,很大程度上减少了其寿命。
第1节 齿轮的失效模式

第一节齿轮强度的失效模式变速器齿轮强度的失效模式有:轮齿断裂、齿面点蚀及剥落、齿面胶合、齿面磨损一、轮齿断裂齿轮在啮合过程中,齿面承受有集中载荷的作用。
我们可以把轮齿看作悬臂梁,轮齿根部弯曲应力很大,过渡圆角处又有集中应力作用,故轮齿根部容易发生断裂。
轮齿折断有两种情况,疲劳断裂和过载断裂。
(附图片)1、疲劳断裂在长时间交变载荷的情况下,齿轮根部经受交变的弯曲应力。
如果高应力点的应力超过材料的耐久极限,则首先在齿根处产生很短的裂纹,随着载荷次数的不断增加,裂纹不断扩大,最后导致轮齿部分地或整个地断掉。
在开始出现裂纹处和突然断掉前出现裂纹处,在载荷作用下由于裂纹断面间的摩擦,形成一个光亮的断面区域,这是疲劳断裂的特征。
其余断面由于是突然形成的故为粗糙表面的新断面。
参见图2.1-1。
图2.1-12、过载断裂由于设计不当或齿轮材料不符合要求或热处理不符合要求,或由于突然性的峰值载荷的冲击。
使载荷超过了齿轮弯曲强度所允许的范围,而引起轮齿的一次性突然折断。
此外,由于装配的齿侧间隙调节不当、安装刚度不够、安装位置不对等原因,使齿轮表面接触区偏向一端,轮齿受到局部集中载荷时,往往会使一端沿斜向产生局部齿端折断,各种形式的过载断裂的断面均为粗糙的新断面。
参见图2.1-2。
图2.1-2为避免齿轮轮齿折断,需降低轮齿的弯曲应力,即提高齿轮的弯曲强度,采用下列措施可提高轮齿的弯曲强度:1.)增大齿轮的根部厚度;2.)加大齿轮的齿根圆弧半径;3.)增大齿顶高系数,以提高重合度,使同时啮合的齿数增多;4.)使齿根部过渡圆角的粗糙度尽量的低;5.)提高材料的弯曲疲劳极限,采用优质的齿轮钢;6.)采用强力喷丸提高齿轮根部的压应力;二、齿面点蚀及剥落齿面点蚀及剥落是闭式渗碳齿轮传动经常出现的一种损坏形式。
约占损坏报废齿轮的70%以上,它主要由于齿轮的接触应力不够引起。
1、齿面点蚀因闭式齿轮传动齿轮在润滑油中工作,齿面长期受到脉动的交变应力的作用,会逐渐产生大量与齿面成尖角的小裂缝。
齿轮断裂失效机理分析

化层的深度与梯度分布 ,采用淬透性更好的材料获 得 更平 缓 的硬 度梯 度 , 高 材质 疲 劳强 度 , 提 并缩 短 渗 碳 周期 , 降低工 艺 成本 。 () 2 提升 产 品检测 手 段 , 对关 键部 件 的零部 件进 行 细致 检验 。 () 3 借助 C E仿真技 术以及相关理论计算 , A 对 关键部件进行模拟分析 , 通过预先结构优化 , 避免失
Th c a im ay i o h a r c u e a d F i r e Me h ns An lss f e Ge r a t r n al e t F u
H i — iQ N H o UX a q, I a o
( iG n h nh i o ev d s yC , t,h nh i 0 2 1 C ia Lu ogS a g a H l H ay n ut O. d S a g a 2 10 , hn ) d I r L
效 发生 。
参考文献 : 【张 栋, 1 ] 钟培道. 失效分析[ . E : M】= 京 国防工业 出版社 ,0 4 j 20 .
[ 王 国凡 . 属 脆 性 断 裂 与 疲 劳 失 效 , 料 成 形 与 失 效 [ . 2 ] 金 .
参 考 文献 :
3 结束 语
在引人电子节气 门体后 ,节气门体对进气量的
[] 1麻友 良 , 尹华敏 , 国栋 . 刘 电控发动机 电子 节气 门控 制系统 [. J 汽车电器 ,0 6 8 3 — 0 】 20 , :9 4 . [ 韩 玉敏. 2 】 汽车智 能电子节气 门控制 系统的研究 L.交 通科 『 ]
重载齿圈的断裂失效分析及预防措施

重载齿圈的断裂失效分析及预防措施内容摘要:对损坏齿圈进行了系统的分析,针对问题产生的原因,提出切实有效的预防措施——从原材料、热处理、图纸设计及机加工等多方面把控,提高了产品质量,提升企业形象。
本文分享给机械加工业同行,生产中以供参考,避免我们走过的弯路。
关键词:齿根裂纹;失效分析;预防措施我单位是生产矿用汽车轮边减速器的专业厂,主要服务主机厂及露天矿山终端客户,矿用汽车轮边减速器同时承担驱动载荷和轴重载荷,加之矿区路况差、尘土大,轮边减速器常处于高温、动载荷及润滑较差的工况中,造成轮边减速器的故障居高不下,对生产带来严重的影响。
近期,我公司收到客户反馈,在保养维修轮边减速器时,发现齿圈齿根部位有严重裂纹,且齿圈上车使用仅半年时间,如下图1所示。
我司对存在问题的齿圈进行更换及相关赔付,此次事故不但给公司造成经济上的直接损失,更大的危机是客户对企业产品的质疑,对市场的冲击。
为此,引起了我单位的高度重视,对于问题齿圈我司进行了系统的分析,并根据实际情况提出了相应的预防措施。
一、齿圈技术参数及技术要求1、齿圈参数:m=5;Z=222;a=20°2、齿圈的技术要求齿圈的材料:40CrNi2MoA;齿圈热处理为整体调质处理,硬度290HBS-340HBS,内齿圈部位中频淬火,淬火硬化层深度:①齿面3.0~4.5(㎜)②齿根1.9~3.0(㎜),淬火硬度54~59HRC。
二、齿圈检测及分析1. 对材料化学成分的分析在断面附近取样进行化学成分分析,材料化学成分符合40CrNi2MoA标准。
2. 对材料气体成分的分析在断面附近取样进行N、O、H气体成分分析:N含量97PPM,0含量30PPM,H含量5PPM,除N含量正常外,其它元素含量均严重超标。
3. 断口的宏观分析内齿圈裂纹断面如下图1所示,断口位于齿根尖角处,齿根圆角过小,造成应力集中,断面可见清楚的贝壳纹状疲劳扩展。
齿圈承受载荷,其根部受到脉动循环的弯曲应力作用,当这种周期性的应力过高时,会在根部产生裂纹,并逐渐扩展,此裂纹属于弯曲疲劳断裂。
齿轮常见失效形式及其解决方法

齿轮常见失效形式及其解决方法(总2页)-CAL-FENGHAI.-(YICAI)-Company One1-CAL-本页仅作为文档封面,使用请直接删除齿轮失效分析与解决方法摘要通过对齿轮失效形式的分析,找出相应解决方法,提高机械传动齿轮质量,延长机械设备的使用寿命。
分析研究失效形式有助于建立齿轮设计的准则,提出防止和减轻失效的措施。
关键词失效;轮齿折断;齿面点蚀;齿面胶合;齿面磨损;齿面塑性变形齿轮是现代机械中应用最广泛的重要基础零件之一。
齿轮类型很多,有直齿轮、斜齿轮、人字齿等,齿面硬度有软齿面和硬齿面,齿轮转速有高有低,传动装置有开式装置和闭式装置,载荷有轻重之分,因此影响因素很多,所以实际应用中会出现各种不同的失效形式。
齿轮的失效主要发生在轮齿部分,其常见失效形式有:轮齿折断、齿面点蚀、齿面磨损、齿面胶合和齿面塑性变形五种。
1 轮齿折断轮齿折断有多种形式,在正常情况下,有以下两种:1)过载折断。
因短时过载或冲击载荷而产生的折断。
过载折断的断口一般都在齿根部位。
断口比较平直,并且具有很粗糙的特征。
2)疲劳折断。
齿轮在工作过程中,齿根处产生的弯曲应力最大,再加上齿根过渡部分的截面突变及加工刀痕等引起的应力集中作用,当轮齿重复受载后,齿根处就会产生疲劳裂纹,并逐步扩展,致使轮齿疲劳折断轮齿。
齿面较小的直齿轮常发生全齿折断,齿面较大的直齿轮,因制造装配误差易产生载荷偏置一端,导致局部折断;斜齿轮和人字齿齿轮,由于接触线倾斜,一般是局部齿折断。
为了提高齿轮的抗折断能力,除设计时满足强度条件外,还可采取下列措施:①采用高强度钢;②采用合适的热处理方式增强轮齿齿芯的韧性;③增大齿根过度圆角半径,消除齿根加工刀痕,齿根处强化处理;④加大齿轮模数;⑤采用正变位齿轮。
为避免轮齿折断,设计时要进行轮齿弯曲疲劳强度计算和静弯曲强度计算。
齿面磨损有磨粒磨损和跑合磨损两种。
在齿轮传动中,随着工作环境的不同,齿面间存在多种形式的磨损情况。
齿轮的失效形式
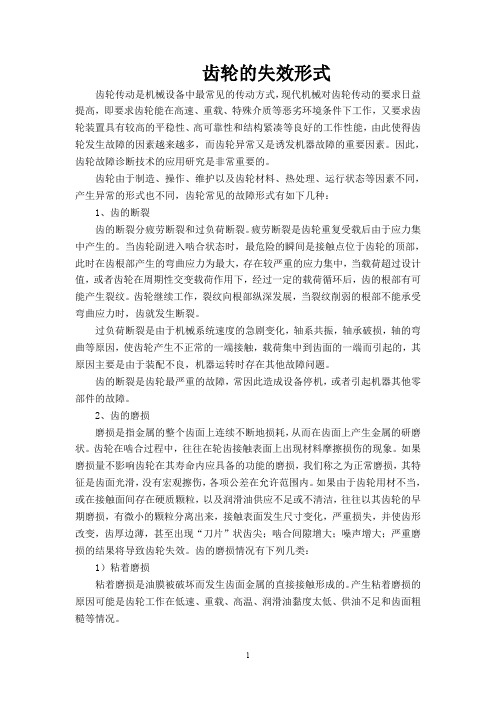
齿轮的失效形式齿轮传动是机械设备中最常见的传动方式,现代机械对齿轮传动的要求日益提高,即要求齿轮能在高速、重载、特殊介质等恶劣环境条件下工作,又要求齿轮装置具有较高的平稳性、高可靠性和结构紧凑等良好的工作性能,由此使得齿轮发生故障的因素越来越多,而齿轮异常又是诱发机器故障的重要因素。
因此,齿轮故障诊断技术的应用研究是非常重要的。
齿轮由于制造、操作、维护以及齿轮材料、热处理、运行状态等因素不同,产生异常的形式也不同,齿轮常见的故障形式有如下几种:1、齿的断裂齿的断裂分疲劳断裂和过负荷断裂。
疲劳断裂是齿轮重复受载后由于应力集中产生的。
当齿轮副进入啮合状态时,最危险的瞬间是接触点位于齿轮的顶部,此时在齿根部产生的弯曲应力为最大,存在较严重的应力集中,当载荷超过设计值,或者齿轮在周期性交变载荷作用下,经过一定的载荷循环后,齿的根部有可能产生裂纹。
齿轮继续工作,裂纹向根部纵深发展,当裂纹削弱的根部不能承受弯曲应力时,齿就发生断裂。
过负荷断裂是由于机械系统速度的急剧变化,轴系共振,轴承破损,轴的弯曲等原因,使齿轮产生不正常的一端接触,载荷集中到齿面的一端而引起的,其原因主要是由于装配不良,机器运转时存在其他故障问题。
齿的断裂是齿轮最严重的故障,常因此造成设备停机,或者引起机器其他零部件的故障。
2、齿的磨损磨损是指金属的整个齿面上连续不断地损耗,从而在齿面上产生金属的研磨状。
齿轮在啮合过程中,往往在轮齿接触表面上出现材料摩擦损伤的现象。
如果磨损量不影响齿轮在其寿命内应具备的功能的磨损,我们称之为正常磨损,其特征是齿面光滑,没有宏观擦伤,各项公差在允许范围内。
如果由于齿轮用材不当,或在接触面间存在硬质颗粒,以及润滑油供应不足或不清洁,往往以其齿轮的早期磨损,有微小的颗粒分离出来,接触表面发生尺寸变化,严重损失,并使齿形改变,齿厚边薄,甚至出现“刀片”状齿尖;啮合间隙增大;噪声增大;严重磨损的结果将导致齿轮失效。
- 1、下载文档前请自行甄别文档内容的完整性,平台不提供额外的编辑、内容补充、找答案等附加服务。
- 2、"仅部分预览"的文档,不可在线预览部分如存在完整性等问题,可反馈申请退款(可完整预览的文档不适用该条件!)。
- 3、如文档侵犯您的权益,请联系客服反馈,我们会尽快为您处理(人工客服工作时间:9:00-18:30)。
2009年度北索市t于i般学研讨垂莹第±届争目宴胯童管理协作服务交流套
变速器齿轮断裂失效分析
杨春朱衍勇
(钢铁研兜总院
北京市学院南路76号)
1前言:
某公司研制的汽车变速器齿鞋在台架实验考棱过程中经常发生早期断裂失效事件,为了
找出齿轮发生断裂的原因,以便采取措施改进生产工艺,提高变速器齿轮的质量,公司将断
裂件送中心进行断裂失教分析。齿轮材料是一种中碳含Cr、Mo的调质钢,表面通过溶碳进
行硬化处理,洛碳后硬化处理后.作糟磨加工。本工作通过对失效齿轮的断口、剖面金相组
织、硬度等检测,分析导承齿轮早期断裂的主要原因,并提出相应的解决措施。
2分析过程和结果:
21.断口分析
变速器齿轮轴和齿轮的形状如图l,断裂件为箭头所指的斜齿轮.该齿轮与齿轮轴为热
装紧密配合。齿轮断裂面如图2所示,为径向断裂面,从侧面观察.断面非常平齐,完全处
在齿轮径向面上,只在靠近齿部附近断面才有较大起优,断面是与轮齿相交的。将裂纹启开
看到的断口宏观形貌如图3,断面有精楚的辐射状花样.由此看出断裂起裂于齿轮薄照段内
表面(图3标注位置),沿图中白色箭头所指方向扩展,起裂区和扩展区断口较平坦,没有
塑性变形,最后断裂的轮齿部位呈银灰色,有少量变形,总体上属于宏观脆性断裂断口。
一。
’
二
圈I变速#齿转轴和齿轮形状
田2童速嚣*轮断Ⅲ位置图3断口宏观形貌
观察齿轮内表面,看到有两处严重的滑动摩擦损伤瘫迹,其中损伤较为严重的一处恰位
于断裂起始位置,如圉4中箭头所示。损伤区形状为宽度大约4mm左右的环形带.显然是
运行中与齿轮轴发生相对柑动所致。扫描电镜下观察可咀看到损伤表面有许多微裂纹,紧接
2009年皮北索市t子l枝学研讨套暨第女届奎目实验童菅理协作服务交流套
断口槔区可蛆观察剑平行十断口的微裂纹,看来齿轮与轴的相对滑动造成齿轮内表面损伤,
可能是导致齿轮断裂的重要原因。但是局部损伤到底是断裂的因还是果,j丕需要对组织进行
进一步研究。
图4变速器齿轮形状和宏观断口分析
起裂源区的断口形貌如图5.看出断裂起裂于齿轮内表面机械损伤堆为严重的区域.源
区断口具有穿晶和沿晶混台的疲劳断口的特征,以穿晶疲劳断口为主。而扩展区边部渗碳层
断口均为脆性沿晶断口,断口典型形貌照片见图6。断面薄壁段中部微观形貌均为穿晶和沿
晶棍台断口。轮齿部主要为韧高状断口,断口形貌如图7。断口分析显示,裂纹源形成之前
局部组织可能由于摩擦热影响发生了回二J‘软化,故源区附近疲劳断口呈现穿晶为主的特征,
离开源区的疲劳扩展区边部断口为严重的沿晶脆性断口则与边部组织保持较高的硬度有关。
囤5断裂源区断口形貌(右图为左图的局部放大)
图6扩展区边部涪碳层沿晶断口图7轮齿部终断区韧窝断口
2.2剖面金相分析
在断面附近垂直表面损伤痕作剖面金相,断裂酥区的组织形貌如图8。齿轮内表面涪碳
2009平友北京市电子芏般荦研讨奋至第女届全国宾静童菅理协作服各交流套
区正常组织为针状马氏体+残余奥氏体组织,心部为马氏体+贝氏体组织。断裂源所在位置
的表层可以观察到由于摩擦损伤导致的自亮带组织和徽裂纹,白亮区附近组织有回火现象。
用显微维氏硬度计捌试齿轮各区域的硬度,结果如袭1所示,齿轮轮毂内表层组织显微
硬度基本在730HV以上:轮毂内缘两处摩擦损伤形成的白亮区硬度830HV以上白亮区附
近组织的硬度则明显低于正常区,有回火现象;齿轮内部非溘碳区组织的硬度在430--510HV
之同。
港碳表层组织的硬度很高,是其表层区在疲劳载荷下出现完全的沿晶断口的主要原因。
也因为表面硬度很高,也使得表层组织对表面损伤更加敏感。另外,过盈配台接触面硬度很
高也不利于相互咬台.容易发生滑动。
圈8断裂谭附近的摩擦损伤组织形貌(左光学金相;右sEM金相
表1显徽碗度检验结晕0tV0
2)
牦毂内缘Ⅲ常Ⅸ
轮毂内缘自亮区
轮毂内缘白亮区附《■日
轮般中部
3.讨论和结论:
分析结果显示.齿轮断裂起始于齿轮薄壁段内表面滑动摩擦损伤位置,是在表面损伤缺
陷的基础上发生裂纹疲劳打展最后导致齿轮断裂的。
5
2009年度北京市电子显微学研讨会曼第七届全国实验室管理协作服务交流会
由于裂纹起始区域的断口为穿品和沿品混合断口,有别于扩展区域的沿晶断口,说明裂
纹起裂于表面发生滑动摩擦损伤和损伤局部组织发生回火软化之后,因此可以断定齿轮与齿
轮轴接触面发生滑动摩擦损伤是在裂纹产生之前发生的,即滑动摩擦产生的损伤缺陷经疲劳
过程形成疲劳裂纹源。齿轮与齿轮轴之间的尺寸配合不佳,是使用中出现相对滑动的原因。
因为看到有两处滑动摩擦损伤区,因此可能配合不佳主要是配合面只形成局部接触,没有形
成大的接触面,使得局部接触应力过大而损伤表面,直至产生滑动。
齿轮材料表面硬度较高而韧性塑性较差,因而接触面咬合性不好,不能通过变形分散装
配应力和工作应力,容易发生滑动和损伤,以致最后发生疲劳断裂。因此适当对接触面进行
回火软化有利于避免该类损伤和失效的发生。
因此,接触面发生滑动摩擦损伤是导致齿轮断裂的基本原因;提高匹配面加工精度和适
当降低装配接触面硬度有利于避免齿轮接触面损伤和齿轮失效的发生。
6