软磁铁氧体烧结过程的质量问题
铁氧体生产工艺技术——铁氧体的烧结(一)
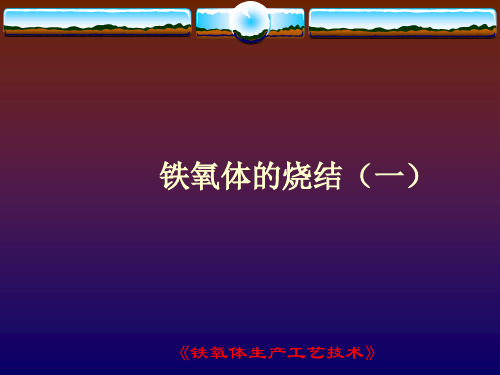
❖ 永磁铁氧体的烧成中,在择优取向方面利用二次再 结晶是有益的,这种磁材的烧结要求获得高密度以 及高度择优取向,成型时通过强大的磁场作用可使 粉料颗粒达到相当大程度的取向,
❖ 3、第二相、气孔对晶粒生长的作用 ❖ 在烧结过程中晶粒生长常被少量第二相或气孔所抑
制,夹杂物的存在增大了晶粒界面移动所需的能量, 因而抑制了晶粒的长大 ❖ 夹杂物可能:(1)与界面一起移动,阻碍小;(2) 与界面一起移动,
《铁氧体生产工艺技术》
❖ 对于所有气孔均符合热力学收缩密度有所不同 的磁体,初始密度对烧结密度的影响是不大的。 但如果初始密度过低,热力学稳定,致密化将 受明显影响,初始密度高,R小,σp大,有利 于致密化。
❖ 铁氧体内部气孔的大小、形状、分布与烧结温 度和时间有关。
❖ 当原始配方中氧化铁含量略低于正分比时,可 获得高密度;反之,如氧化铁含量略高于正分 比,则很难得到致密的样品
《铁氧体生产工艺技术》
❖ 复习上次课重点: ❖ 固相反应; ❖ 固相反应分析; ❖ 加速固相反应,缩短烧结周期(时间),需
考虑的有关因素; ❖ 添加剂的作用。
《铁氧体生产概念 ❖ 烧结是将成型好的坯件,在常压或加压下, ❖ 在空气中或保护气体中, ❖ 高温(T<T熔点)加热, ❖ 使颗粒之间互相结合(粘结),从而提高成型坯件的
《铁氧体生产工艺技术》
❖ 课后小结: ❖ 一、气孔与致密化的关系,气孔与晶粒生长和致密度
有关, ❖ R<Rc,气孔收缩,R>Rc,气孔趋于生长; ❖ 二、降低气孔率的措施(六条); ❖ 三、常用烧结技术有:①低温烧结,②热压烧结,③
气氛烧结。 ❖ 作业布置: ❖ 制备高密度铁氧体,降低气孔率应采取哪些措施? ❖ 2、常用的烧结技术有哪些?
烧结料层不达标检查书

烧结料层不达标检查书摘要:1.引言:背景介绍和检查目的2.烧结料层不达标的原因3.检查方法和步骤4.改进措施和建议5.结论:总结和下一步工作正文:一、引言烧结矿是钢铁行业的重要原材料之一,其质量直接影响到钢铁产品的质量和性能。
在烧结矿的生产过程中,烧结料层的质量和稳定性至关重要。
然而,近期我国某钢铁企业的烧结料层出现了不达标的情况,为了查明原因,采取有效措施进行改进,我们进行了一系列的检查和分析工作。
二、烧结料层不达标的原因经过现场勘查和数据分析,我们发现烧结料层不达标的主要原因有以下几点:1.原料成分不稳定:烧结原料中某些元素含量波动较大,导致烧结过程中料层结构不稳定。
2.混合料均匀性差:烧结原料在混合过程中,部分原料未能充分混合,导致料层中存在明显的原料分布不均现象。
3.烧结温度控制不当:烧结过程中,温度波动较大,导致料层中某些区域的烧结矿结晶不充分。
三、检查方法和步骤为了查明烧结料层不达标的具体原因,我们采取了以下检查方法和步骤:1.采集烧结矿样品,进行化学成分分析,了解原料成分波动情况。
2.对烧结矿生产过程进行现场观察,检查原料混合、布料等环节是否存在问题。
3.查阅烧结矿生产过程中的温度监测数据,分析温度波动情况。
4.结合现场观察和数据分析,找出导致烧结料层不达标的主要原因。
四、改进措施和建议针对检查中发现的问题,我们提出以下改进措施和建议:1.优化原料成分管理:加强对原料成分的检测和控制,确保原料成分稳定。
2.提高混合料均匀性:改进混合料设备,提高混合料均匀性,避免原料分布不均。
3.调整烧结温度控制策略:优化烧结矿生产过程中的温度控制,减小温度波动,保证烧结矿结晶充分。
五、结论通过本次检查和分析,我们找到了导致烧结料层不达标的主要原因,并提出了相应的改进措施和建议。
接下来,我们将密切关注烧结矿生产过程,确保改进措施的落实,以提高烧结矿的质量和稳定性。
烧结料层不达标检查书

烧结料层不达标检查书一、问题概述近日,我厂在进行烧结料层检查时发现,部分烧结料层存在不达标现象。
这一问题严重影响了烧结矿的品质和产量,同时也带来了环境污染的风险。
为了确保生产稳定、环保达标,我们对相关问题进行了详细检查。
二、原因分析1.原料问题在检查过程中,我们发现部分原料的品质不佳,如品位低、杂质含量高等。
这些问题导致烧结料层不达标,影响了烧结过程的顺利进行。
2.工艺问题生产过程中,烧结工艺参数设置不合理,如烧结温度、保温时间等。
这些参数与实际生产需求不符,导致烧结料层不达标。
3.设备问题部分设备存在磨损严重、故障率高的问题,影响了烧结料层的质量。
此外,设备维护不到位,也是导致烧结料层不达标的原因之一。
4.操作问题操作人员在生产过程中,操作不规范、责任心不强,导致烧结料层质量不稳定。
此外,操作人员对烧结料层质量的认识不足,也是问题的一部分。
三、整改措施1.改进原料采购和储存针对原料问题,我们将优化原料采购渠道,确保原料品质。
同时,加强原料储存管理,降低杂质污染风险。
2.优化生产工艺对烧结工艺进行调整,确保烧结温度、保温时间等参数符合生产要求。
同时,加强对烧结过程的监控,确保工艺执行到位。
3.设备维修与升级对磨损严重、故障率高的设备进行维修或更换,提高设备运行稳定性。
此外,定期对设备进行保养,降低设备故障率。
4.培训操作人员加强对操作人员的培训,提高他们的操作技能和责任心。
同时,加强质量意识教育,确保操作人员充分认识到烧结料层质量的重要性。
四、验收标准与流程为确保整改措施的有效实施,我们将建立严格的验收标准和流程。
整改完成后,对烧结料层进行抽样检测,确保质量达标。
如未达标,将继续整改,直至满足生产要求。
五、预防措施为了避免烧结料层不达标问题的再次发生,我们将加强生产过程中的监控与管理,确保各环节符合规定要求。
同时,建立健全质量管理体系,形成长期稳定的生产环境。
六、总结与建议通过此次检查,我们深刻认识到烧结料层不达标问题的严重性。
07.磁性材料第一部分-软磁铁氧体材料

•
引言
• 磁性材料是功能材料的重要分支; • 磁性元器件具有转换、传递、处理信息、存储能量、节约能源等 功能, • 应用于能源、电信、自动控制、通讯、家用电器、生物、医疗卫 生、轻工、选矿、物理探矿、军工等领域,尤其在信息技术领域 已成为不可缺少的组成部分。 • 信息化发展的总趋势是向小、轻、薄以及多功能、数字化、智能 化方向发展;要求磁性材料制造的元器件不仅大容量、小型化、 高速度,而且具有可靠性、耐久性、抗振动和低成本的特点。
二、提高µ 的方法 i
(一).提高材料的Ms 尖晶石铁氧体 Ms = | MB - MA| 1.选高Ms的单元铁氧体 如:MnFe2O4(4.6--5 µ ); NiFe2O4 (2.3 µ ) B B 2.加入Zn,使MAs降低 另外: CoFe2O4 (3.7 µ )磁晶各向异性 B Fe3O4(4 µ ) 电阻率低,K也较大 B Li0.5Fe2.5O4(2.5 µ ) 烧结性差,10000C, Li挥 B 发
§1-3
软磁铁氧体的磁谱
一、软磁铁氧体磁谱及形状 磁谱:软磁材料在弱交变磁场中,复磁导率µ = r µ ' - µ " 随频率变化的曲线 r r
µ µ' r
1
µ" r
2
3
4
f
一般软磁铁氧体材料的磁谱
铁氧体磁谱分区: 1.低频( f<104Hz): 复磁导率µ 大, µ 小,损耗小, r r 磁导率随频率变化不大; 2.中频(f=104 106Hz):与低频相似,可能出现尺寸 共振和磁力共振; µ 下降, µ 出现峰值 ; r r
<<磁性材料>>(铁氧体部分)
引言
• 无论是电子技术、电力技术、通信技术、还是空间技术、计算技术、生 物技术,乃至家用电器,磁学和磁性材料都是不可缺少的重要部分。
锰锌铁氧体材料生产工艺控制要点

工艺·技术·应用锰锌铁氧体材料生产工艺控制要点钟家全摘 要:锰锌铁氧体是一种重要的软磁材料,其应用日益广泛,并对材料性能提出了越来越高的要求。
材料的性能不仅取决于合理的配方,更与生产工艺密切相关。
结合材料的生产工艺,归纳了各道生产工序对材料性能的影响及相应的质量控制要点,为企业生产技术人员提供实践参考。
关键词:锰锌铁氧体;工艺;质量控制中图分类号:TM277 文献标识码:B 文章编号:1001-3830(2011)02-0069-041 引言随着科学技术的发展,锰锌铁氧体材料的需求量越来越大,对其性能也提出了越来越高的要求。
然而,锰锌铁氧体制造工序虽然不多,但每一道工序都会对最终产品性能产生重大影响。
所以可以说,锰锌铁氧体生产的每一道工序都是关健工艺。
本文归纳了各个工序的质量控制要点,以期对行业提供参考。
2 各工序质量控制要点2.1 原材料理化分析在锰锌铁氧体生产过程中,原材料的纯度、活性、含杂量等因素对产品性能、工艺过程等起着非常重要的作用。
有时,甚至是决定性的作用。
因此,原材料在使用前,都应进行非常准确的理化分析,以保证基本配方不偏离。
由于现在铁氧体原材料厂家众多,各厂家甚至一个厂家的不同批次原料的纯度、含杂量、活性等都不尽相同,因而,在使用前,就应对其进行准确的理化分析。
其中纯度和含杂量的分析最为重要。
纯度不准确,配方就会偏离,后果自然不言而喻。
含杂量的准确测定,对后续工艺具有指导性的作用。
如对功率铁氧体,为降低涡流损耗,一般都加入适量的SiO2 、CaCO3等杂质使其在烧结过程中于晶粒边界形成CaSiO3高电阻率层。
如果原材料的这些杂质含量较高,在后面的掺杂中就可以少加或不加。
同时,杂质含量高的原材料不能用于高磁收稿日期:2010-02-08 修回日期:2010-09-21通讯作者:钟家全 E-mail: 824322479@ 导率磁心的生产,否则在高温烧结状态下会发生异常晶粒长大,使产品磁性能大大降低。
磁性材料烧结

磁性材料烧结
磁性材料烧结是一种常见的制备方法,通过高温处理使粉末颗粒结合成致密的块状材料。
磁性材料烧结的过程对于材料的性能和微观结构具有重要影响,因此在实际应用中具有广泛的意义。
首先,磁性材料的选择至关重要。
不同种类的磁性材料具有不同的烧结特性,因此在烧结过程中需要根据具体材料的特点进行相应的工艺调控。
例如,铁氧体材料在烧结过程中需要考虑到磁性能和机械性能的平衡,而钕铁硼材料则需要更高的烧结温度和压力。
其次,烧结工艺参数的选择对于磁性材料的性能具有重要影响。
烧结温度、压力、时间等参数的选择需要根据具体材料的特点以及所需的最终性能进行合理的设计。
过高或过低的烧结温度都会对材料的性能产生不利影响,因此需要进行严格的控制。
在烧结过程中,粉末颗粒之间的结合是一个关键环节。
通过烧结工艺,粉末颗粒之间产生了颗粒间的结合,从而形成了致密的块状材料。
这种结合方式对于材料的性能具有重要影响,因此烧结工艺的优化是磁性材料制备过程中的关键环节。
此外,烧结过程中的气氛对于材料的性能也具有重要影响。
不同的气氛会对材料的表面氧化状态产生影响,从而影响材料的磁性能。
因此,在烧结过程中需要选择合适的气氛,并严格控制气氛的成分和流动性。
总的来说,磁性材料烧结是一项复杂的制备工艺,需要综合考虑材料的特性、工艺参数的选择、颗粒间的结合以及烧结过程中的气氛等因素。
通过合理的烧结工艺,可以获得具有优良磁性能和机械性能的磁性材料,从而满足不同领域的应用需求。
在今后的研究和生产中,磁性材料烧结工艺的优化将继续是一个重要的研究方向,为磁性材料的应用提供更好的支撑。
烧结料层不达标检查书

烧结料层不达标检查书摘要:一、问题背景及重要性二、烧结料层不达标的原因分析1.原料问题2.设备问题3.工艺问题4.操作问题三、整改措施及实施方案1.原料选购与储存2.设备维护与更新3.优化工艺参数4.操作培训与规范四、验收标准与效果评估五、预防措施及持续改进正文:一、问题背景及重要性近年来,我国钢铁行业面临着环保压力、市场竞争加剧等问题,烧结工序作为钢铁生产的重要环节,其能耗和污染物的排放对整个生产线有着重大影响。
然而,在很多钢铁企业中,烧结料层不达标的现象较为普遍,这不仅浪费了资源,还加剧了环境污染。
为了提高烧结矿质量,降低能耗,减少污染物排放,本文针对烧结料层不达标的问题进行深入分析,并提出相应的整改措施。
二、烧结料层不达标的原因分析1.原料问题烧结矿的原料主要包括铁矿石、燃料、熔剂等,原料的品质直接影响到烧结矿的质量。
不合格的原料可能导致烧结矿品位低、强度差等问题。
2.设备问题烧结设备的性能和状态对料层的均匀性和稳定性有很大影响。
设备磨损、故障等问题会导致烧结料层不达标。
3.工艺问题烧结工艺参数设置不合理,如布料速度、烧结温度、保温时间等,都会影响料层的形成和烧结矿的质量。
4.操作问题操作人员的技能水平、操作规范性以及对异常情况的处理能力,也会对烧结料层产生影响。
三、整改措施及实施方案1.原料选购与储存(1)严格把控原料质量,选购符合国家标准的优质原料;(2)对进厂原料进行抽样检测,确保合格;(3)加强原料储存管理,防止污染、潮湿等问题。
2.设备维护与更新(1)定期对设备进行检查、维护,确保设备状态良好;(2)对磨损严重的设备部件进行及时更换;(3)提高设备自动化程度,减少人为操作失误。
3.优化工艺参数(1)根据原料特点和设备性能,合理设置烧结工艺参数;(2)加强对工艺参数的监控,确保烧结过程稳定;(3)根据实际情况,适时调整工艺参数。
4.操作培训与规范(1)加强操作人员培训,提高技能水平;(2)制定操作规程,规范操作行为;(3)加强对异常情况的应对措施,降低生产风险。
铁氧体生产工艺技术——铁氧体的烧结(一)
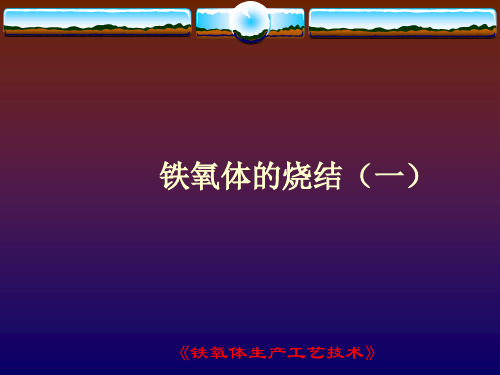
《铁氧体生产工艺技术》
烧结温度曲线
《铁氧体生产工艺技术》
烧结窑炉
《铁氧体生产工艺技术》
烧结窑炉
《铁氧体生产工艺技术》
❖ 2、烧结推动力 ❖ (1)致密化与瓶颈形成的推动力与机制 ❖ 物质由曲率半径小处向曲率半径较大处传递,同一颗
粒内物质传递的结果导致所谓的颗粒“球化”;不同 颗粒接触时,物质将由小颗粒向大颗粒传递,促使颗 粒“粗化”。 ❖ (2)晶体生长的驱动力——界面能 ❖ 晶界移动对晶粒生长的贡献取决于初始的颗粒尺寸比。 ❖ 三、晶粒长大与二次再结晶现象 ❖ 1、晶粒生长与致密化的关系
❖ 复习——讲授——小结—生产工艺技术》
❖ 复习上次课重点: ❖ 烧结的概念,将成型好的坯件在常压或加压下,在空
气中(或保护气体中)高温(T<T熔点=加热,使颗 粒相互结合,排除颗粒间的气孔,提高材料的机械强 度,使之充分铁氧体化(充分固相反应)。
❖ 二、烧结过程分为烧结初期、烧结中期、烧结后期三 个阶段。不同颗粒接触时,物质将由小颗粒向大颗粒 传递,促使颗粒“粗化”,晶界移动对晶粒长大的贡 献取决于初始颗粒的尺寸比。
❖ 这里有一个容易混淆的问题:是否是由于晶粒 长大的结果才导致了烧结体的致密化呢?
《铁氧体生产工艺技术》
❖ 烧结初、中期表面扩散是最有可能的致密化及 粗化的物质传输途径或至少是其中之一,而烧 结后期只有晶界或体积扩散是可能的机制。
❖ 表面扩散传质可同时导致颗粒列阵的收缩和晶 粒生长,
❖ 并且传质过程对颗粒列阵收缩的贡献远大于晶 粒生长导致烧结重新启动(颗粒间二面角的重 新形成)所引起的收缩。
《铁氧体生产工艺技术》
❖ 对于所有气孔均符合热力学收缩密度有所不同 的磁体,初始密度对烧结密度的影响是不大的。 但如果初始密度过低,热力学稳定,致密化将 受明显影响,初始密度高,R小,σp大,有利 于致密化。
- 1、下载文档前请自行甄别文档内容的完整性,平台不提供额外的编辑、内容补充、找答案等附加服务。
- 2、"仅部分预览"的文档,不可在线预览部分如存在完整性等问题,可反馈申请退款(可完整预览的文档不适用该条件!)。
- 3、如文档侵犯您的权益,请联系客服反馈,我们会尽快为您处理(人工客服工作时间:9:00-18:30)。
软磁铁氧体烧结过程的质量问题现象及解决措施 一、烧结条件对磁性能的影响 烧培条件对铁氧体的磁性能有很大影响。烧结温度、烧结气氛和冷却方式是烧结条件的三个主要方面。
(一)烧结温度对磁性能的影响 一般说来,烧结温度偏低时,晶粒大小不均匀,气孔分散于晶界和晶粒内部,呈不规则多面形。磁导率μi和剩磁感应强度Br都较低,但是矫顽力HCB较大。烧结温度适当,则晶粒趋于均匀、气孔呈球形、烧结密度较低、磁导率μi和剩磁感应强度Br较大,矫顽力HCB有所减少。烧结温度过高时,晶粒虽然增大,但是由于内部的气孔迅速膨胀,有的杂质发生局部熔融而使晶界变形,则不仅烧结密度低,磁导率μi和剩磁感应强度Br也将显著下降,机械性能极其脆弱,无实用价值。
对软磁铁氧体而言,在一定的烧结温度范围内,初始磁导率μi随烧结温度升高而增大,损耗角正切tgδ也随温升而增大(即Q值减少)。对硬磁铁氧体而言,烧结温度高,剩磁感应强度Br也高,而矫顽力HCJ减小。对旋磁铁氧体而言;烧结温度高,则饱和磁化强度也较高。在生产中,必须针对各种材料的不同特点,结H合产品的其它性能要求而区别对待,由试验确定最佳的烧结温度。
(二)烧结气氛对磁性能的影响 气氛条件对铁氧体烧结非常重要,尤其对含有易变价的Mn,Fe,Cu,Co等金属元素的铁氧体,在烧结过程中随着氧分压和温度的变化而发生电价的变化以至相变,过度的氧化与还原,就有另相析出(如α-Fe2O3,FeO,Fe3O4,Mn2O3等),将导致磁性能的急剧变化。
在升温阶段,因为还没有形成单一尖晶石相,对周围气氛要求不苛刻,在空气中、真空中或氮气中升温均可;在保温过程中,由于发生了气孔的排除、晶粒的长大和完善、单一结构铁氧体的生成,这些均要求控制好烧结气氛。可以说,烧结气氛是影响磁性能的一个重要因素。烧结气氛和固相反应速度、产物及微观结构均有直接关系。因此要控制好烧结气氛来生产各种不同性能的铁氧体(如各种高磁导率、低损耗、高密度的软磁铁氧体和高电阻率的旋磁铁氯体等)。
当所需的烧结气氛为氧化气氛(高氧分压气氛)时,可向炉(窑)内通纯氧气;烧结气氛为还原气氛(低氧分压气氛)时,可向炉(窑)内通氧气或抽真空。抽真空时应注意真空度不可太高。真空度太高容易使空气电离,造成硅碳棒间打火烧坏硅碳棒,因此用充氮气的方法控制氧分压为好。
对含Zn的软磁铁氧体的烧结,控制好烧结气氛十分关键,因为Zn的挥发与烧结气氛密切相关。
1、Zn的游离与挥发 含锌铁氧体在高温热处理过程中有可能发生游离与挥发。Zn挥发必然导致产品性能下降,例如μi大幅度下降,Zn挥发产生了Fe2+,使电阻率下降等。以ZnFe2O4为例,将有如下反应:
ZnFe2O4→(1-x) ZnFe2O4 +2/3xFe3O4+xZnO+x/6 O2↑ 游离的ZnO进一步分解:ZnO→Zn(熔点:9070C)+1/2 O2↑ 任何减少方程式右边含量的变化都会促使化学反应向右进行,因此,从理论上讲,动态气氛和静态气氛必然对Zn挥发产生影响。此外,若埋粉为氧化铝,会发现埋粉的颜色由白色变成了篮绿色。
Al2O3+Zn(g)+1/2 O2→ZnAl2O4 (篮绿色) 当温度高于12000C时,锌的蒸汽压大幅度提高,挥发严重。 2、影响锌的游离与挥发的因素主要有: (1)铁氧体组成中ZnO的含量 若组成中ZnO的含量下降或Fe2O3,MnO等成分上升时,Zn挥发将难以进行,挥发开始的温度也升高。
(2)加热温度与时间 Zn挥发随加热温度的上升和加热时间的延长而加剧。 (3)周围气氛的影响 ①、气氛状态对含锌铁氧体表面Zn挥发有较大影响。动态气氛流动的气体不断地将铁氧体表面挥发的Zn带出窑外,加剧了ZnO分解,使产品表面产生内应力,因此产品机械强度明显低于静态气氛烧结产品。
②、如果体系内缺氧,Zn的挥发就容易进行,所以氧分压提高,则Zn或ZnO就不易游离或分解,对MnZn铁氧体而言,Zn挥发的抑制与防止氧化是矛盾的。
(4)Al2O3粉能加剧产品表面Zn的挥发 这是由于Zn与Al2O3反应生成ZnAl2O4(篮绿色)的缘故。由于Zn大量挥发,使表面晶粒之间空隙加大,并产生许多网状孔洞,这种松散的"框架",使磁芯应力进一步增大,从而大大降低磁芯机械强度。
(三)冷却条件对磁性能的影响 冷却速度和冷却气氛对磁性能也有很大影响。一般锰锌铁氧体冷却时要防止氧化,故采用真空冷却或氮气冷却方法。镍锌铁氧体却需要适当的氧化气氛,这样可以大大提高铁氧体的电阻率ρ,从而降低涡流损耗,提高产品的Q值。
对Ni00.4·ZnO0.6·Fe2O4铁氧体,同样的烧结温度(1300℃)下,氧气中烧结,氧气中缓冷比空气中缓冷电阻率ρ降低400倍,具体见表5-5,可见该变气氛对Ni00.4·ZnO0.6·Fe2O4铁氧体的电阻率ρ的影响较大。
表5-5烧结温度、烧结气氛、冷却方式对NiZn铁氧体电阻率ρ的影响 烧结温度℃ 烧结气氛 冷却方式 电阻率ρ(欧.厘米)
1300 氧气 氧气中缓冷 5.4*105 1300 氧气 空气中快冷 1.3*103 1300 空气 空气中缓冷 1.3*105 1300 空气 空气中快冷 1.1*103 1200 空气 空气中缓冷 9.6*105 降温过程中主要涉及两方面的问题: 1、冷却过程中将会引起产品的氧化或还原,产生脱溶物等。对易变价的锰锌铁氧体高磁导率材料。控制冷却过程中的氧气氛尤为重要。
2、合适的冷却速度有利于提高产品合格率。若冷却速度过快,出窑温度过高,因热胀冷缩导致产品冷(降温)开裂,或产生大的内应力,恶化产品性能。
烧结铁氧体产品的窑炉设计对提高产品档次、合格率十分重要。早期,国内曾采用烧砖瓦的倒焰窑,由于温差大,不能连续生产及产品质量差而被淘汰,继而发展为推车式的隧道窑炉,由于温差大,能耗高及气氛难控制,亦逐步被淘汰。目前,隧道式的辊道窑,推板窑以及两者结合而成的辊道--推板窑已普遍采用,多数采用电热式(硅碳棒)。烧结中、低档永磁铁氧体产品时,为了降低成本亦采用煤推板窑。烧结高磁导率软磁铁氧体时,采用可控气氛的钟罩式电炉较为理想。对于不同类型的产品,应采用适合的窑炉、合理的窑炉温度曲线以及相应的气氛控制。
二、其他质量问题 在烧结工序中,除电磁性能方面的问题外,还会出现开裂、变形、尺寸超差等方面的质量问题。 (一)开裂 开裂。即产品表面出现裂纹或裂口。烧结过程中开裂可分为两类情况,即升温开袋[见图5-9(a)(b)]和降瀑开裂 [见图5-9(c)(d)]
5-9 几种常见的产品开裂类型 1.升温开裂 在升温阶段,由于干燥的速度太快,坯件内的水份和粘合剂急剧挥发出来,导致干燥开裂。再者,粘合剂挥发完以后。升温速度太快,引起坯件的不均匀收缩也会导致开裂。这两种升温开裂的断面均不平整,这是因为坯件开裂时尚未完全铁氧体化。
2.降温开裂 在降温过程中,由于冷却速度太快,或出炉温度太高,会引起炸裂。其裂纹一般细而直,裂纹断面也较齐整。
还有裂纹遍布产品表面的开裂,称龟裂。龟裂的原因对锰锌铁氧体来说,多是由于锰锌铁氧体的严重氧化(实践中,粘合剂的挥发也可以导致产品出现龟裂)。有时,产品表面上的这种"龟纹"很细,在磨加工前不易看出,可用敲击方法根据其发出的声音来判别,有龟裂时,敲击发出暗哑声,无龟裂时发出类似金属的清脆声。
3.避免产品开裂的方法 (1)严格按产品烧结工艺操作,不得擅自更改烧结工艺,尤其是升温速度、进车时间和装车高度。
(2)尺寸大的产品,进窑前要充分干燥,500℃以后的降温速度不能太快,实验室烧大产品在出炉时,应用石棉布连同耐火盘包好,让产品缓慢降至室温。
(3)烧结锰锌铁氧体产品时,如用真空淬火法要注意按工艺要求保证罐内的真空度。尽量难免产品在高温区停留时间过长。当高温区的碳棒断掉而不能维持烧结温度时,应立即更换碳棒,否则高温区的产品将去因氧化而报废。
(二)变形 变形多发生于薄壁的环形、管形、罐形铁芯、长条(棒)形天线及E(U)形磁芯等,克服变形的关键在于成型时产品密度的均匀性以及产品的装坯工艺,E(U)形磁芯在装盒时可将坯件的腿朝上放置以减少变形,还可采取成型时压制成"日"字或"口"字形坯件,烧结后再切割成E或U形磁芯,这样可有效地防止这类磁芯的变形。
(三)尺寸超差 尺寸超差是指产品烧结后的尺寸(磨加工面除外)超过了产品所规定的尺寸公差允许范围。从工艺规定来说,产品的电磁性能所需的最佳烧结温度应该与产品合格尺寸所要求的烧结温度相一致,然而实际生产中,由于种种原因二者有时不能统一,有时需将产品尺寸烧在公差的上限或下限,性能才合格。此时,则易容易发生尺寸超差的质量问题。
除上述原因外,产生尺寸超差的原因还有: 1.烧结温度不当; 2.坯件粉料的预烧温度偏高或偏低,成型坯件的重量一致性差; 3.成型模具长时间使用后,模具的某些零件磨损大,造成产品的个别尺寸超差。 此外,烧结过程中物相变化的系统研究对产品质量的控制十分重要。对于石榴石以及某些六角铁氧体,在其生成反应过程中,先生成某些中间产物。例如由Fe2O3,BaCO3,Co3O4制备Co2Z(Ba3Co2Fe24O41),经XRD物相分析发现共经历S、F、M、Y四个中间产物,最后才生成"Z"相,且Z相的成相区间较窄,对烧结过程相态变化的研究对于烧结制度的确定无疑具有指导意义。