提高零件疲劳强度的方法
第三章 机械零件的疲劳强度计算

m
max min
2
200 100 2
50
a
max min
2
200 100 2
150
200
a
50
0
-100
min
max
m
t
机械设计 第三章 机械零件的疲劳强度计算
机械设计
3.2 材料的疲劳特性
3.2.1 材料的疲劳曲线
表示N次循环和疲劳极限间的关系曲线,称为疲劳曲线。
机械设计
曲线的BC段,随着循环次数的增加, 使材料疲劳破坏的最大应力不断下降。 C点相应的循环次数大约为104。把这一 阶段的疲劳现象称为应变疲劳。由于 应力循环次数相对很少,所以也叫低 周疲劳。
机械设计 第三章 机械零件的疲劳强度计算
机械设计
当N≥104时,称为高周循环疲劳。曲
线CD代表有限疲劳阶段。D点对应的 疲劳极限ND称为循环基数,用N0表示。 曲线CD段上任何一点所代表的疲劳极 限,称为有限寿命疲劳极限。
机械设计
1.稳定循环变应力
1) 对称循环变应力
最大应力σmax和最小应力σmin的
绝对值相等而符号相反
即σmax=-σmin
例如,转动的轴上作用一方向 不变的径向力,则轴上各点的弯曲 应力都属于对称循环变应力
机械设计 第三章 机械零件的疲劳强度计算
机械设计
2) 脉动循环变应力 脉动循环变应力中
σmin=0
劳极限。连接A′、D′得
直线A′D′
机械设计 第三章 机械零件的疲劳强度计算
机械设计
取C点的坐标值等于材料的 屈服极限σS,并自C点作一直 线与直线CO成45°的夹角, 交A′D′的延长线于 G′, 则CG′上的任何一
金属表面处理中的改善疲劳性技术及应用

金属表面处理中的改善疲劳性技术及应用金属材料在各种工程应用中广泛使用,其疲劳性能是评估其在循环载荷作用下使用寿命的重要指标。
金属的疲劳性能是指材料在交变应力或应变作用下,经过一定的循环次数后发生断裂或失效的能力。
金属的疲劳性能不仅取决于材料的化学成分和微观结构,还受到表面处理技术的影响。
本文将重点讨论金属表面处理中的改善疲劳性技术及其应用。
1. 金属疲劳的原因及影响因素金属疲劳的原因主要是由于交变应力或应变的作用,导致材料表面产生微观裂纹,随着循环次数的增加,裂纹逐渐扩展,最终导致材料失效。
金属疲劳的影响因素包括:材料的化学成分、微观结构、晶粒大小、应力集中、环境因素等。
2. 改善金属疲劳性的表面处理技术为了提高金属的疲劳性能,可以采用多种表面处理技术,主要包括:表面强化、表面改性和表面涂层等。
2.1 表面强化技术表面强化技术是通过改变金属表面层的微观结构和力学性能,提高其抵抗疲劳破坏的能力。
常见的表面强化技术包括:热处理、冷处理、表面淬火、离子注入等。
2.2 表面改性技术表面改性技术是通过改变金属表面层的化学成分和微观结构,提高其疲劳性能。
常见的表面改性技术包括:电化学沉积、化学气相沉积、等离子体喷涂等。
2.3 表面涂层技术表面涂层技术是在金属表面涂覆一层或多层保护材料,以提高其疲劳性能。
常见的表面涂层技术包括:热喷涂、电镀、阳极氧化等。
3. 改善疲劳性技术的应用金属疲劳性改善技术在许多工程领域都有广泛应用,例如:航空发动机、汽车零部件、桥梁建筑、石油管道等。
通过应用改善疲劳性技术,可以提高金属部件的使用寿命,降低维修成本,提高经济效益。
3.1 航空发动机中的应用航空发动机工作环境恶劣,要求材料具有高疲劳性能。
通过采用表面强化和表面涂层技术,可以显著提高航空发动机关键部件的疲劳寿命,降低维修成本。
3.2 汽车零部件中的应用汽车零部件在行驶过程中受到交变载荷的作用,容易产生疲劳破坏。
应用改善疲劳性技术,可以提高汽车零部件的疲劳强度,延长使用寿命,提高汽车的安全性能。
第3章 机械零件的强度(用)
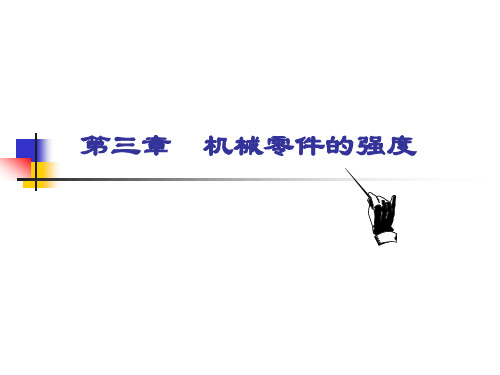
汽车的齿轮和轴所承受的动载荷。
注意:在设计计算中,载荷又可分为名义载荷和计 算载荷,计算载荷等于载荷系数乘以名义载荷。
名义载荷: 根据机器在稳定和理想工作条件下的工作阻力,
按力学公式求出的载荷称为名义载荷. 计算载荷:
考虑机器在工作中载荷的变化和载荷在零件上
s
m rN
N
C (NC
N
ND)
D点以后(无限寿命区间):
s rN s r (N ND )
用N0及其相对应的疲劳极限σr来近
似代表ND和 σr∞,有:
s
m rN
N
s
m r
N0
C
s-N疲劳曲线
§3-1 材料的疲劳特性 疲劳曲线
2、 s-N疲劳曲线
有限寿命区间内循环次数N与
疲劳极限srN的关系为:
CG'直线的方程为:
s a s m s s
σ为试件受循环弯曲 应力时的材料常数,其值 由试验及下式决定:
s
2s 1 s 0 s0
对于碳钢,σ≈0.1~0.2,对于合金钢,σ≈0.2~0.3。
§3-2 机械零件的疲劳强度计算
1、零件的极限应力线图
如设弯曲疲劳极限的综合影响系数 Kσ ,且 s 1 ―材料对称循环弯曲疲劳极限
s rN s r
m
N0 N
KNsr
式中, N0为循环基数;
sr为与N0相对应的疲劳极限
s-N疲劳曲线
m为材料常数,值由材料试验确定。
疲劳曲线的意义
s rN
sr m
N0 N
KNsr
机械原理简答题答案(新)
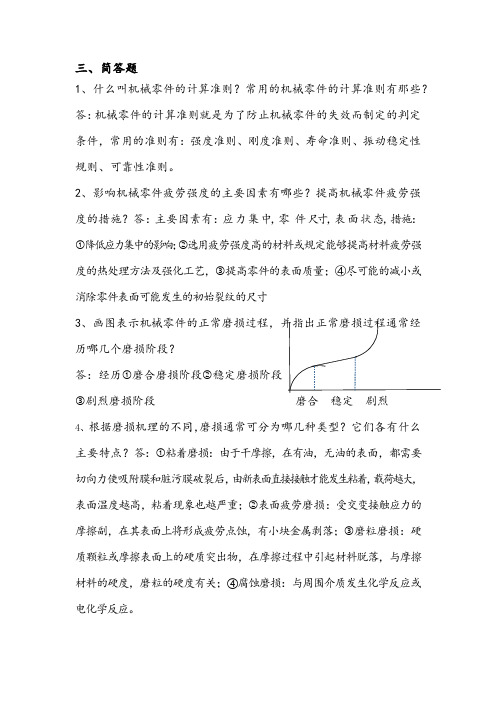
三、简答题1、什么叫机械零件的计算准则?常用的机械零件的计算准则有那些?答:机械零件的计算准则就是为了防止机械零件的失效而制定的判定条件,常用的准则有:强度准则、刚度准则、寿命准则、振动稳定性规则、可靠性准则。
2、影响机械零件疲劳强度的主要因素有哪些?提高机械零件疲劳强度的措施?答:主要因素有:应力集中,零件尺寸,表面状态,措施:①降低应力集中的影响;②选用疲劳强度高的材料或规定能够提高材料疲劳强度的热处理方法及强化工艺,③提高零件的表面质量;④尽可能的减小或消除零件表面可能发生的初始裂纹的尺寸3、画图表示机械零件的正常磨损过程,并指出正常磨损过程通常经历哪几个磨损阶段?答:经历①磨合磨损阶段②稳定磨损阶段③剧烈磨损阶段磨合稳定剧烈4、根据磨损机理的不同,磨损通常可分为哪几种类型?它们各有什么主要特点?答:①粘着磨损:由于干摩擦,在有油,无油的表面,都需要切向力使吸附膜和脏污膜破裂后,由新表面直接接触才能发生粘着,载荷越大,表面温度越高,粘着现象也越严重;②表面疲劳磨损:受交变接触应力的摩擦副,在其表面上将形成疲劳点蚀,有小块金属剥落;③磨粒磨损:硬质颗粒或摩擦表面上的硬质突出物,在摩擦过程中引起材料脱落,与摩擦材料的硬度,磨粒的硬度有关;④腐蚀磨损:与周围介质发生化学反应或电化学反应。
5、何谓螺纹联接的预紧,预紧的目的是什么?预紧力的最大值如何控制?答:螺纹连接的预紧:螺纹连接的预紧是指在装配时拧紧,是连接在承受工作载荷之前预先受到预紧力的作用。
目的:增强连接的可靠性与紧密性,以防受载后被连接件间出现间隙或者发生相对滑移。
6、螺纹联接有哪些基本类型?适用于什么场合?答:①螺栓联接:用于被联接件不太厚且两边有足够的安装空间的场合。
②螺钉联接:用于不能采用螺栓联接,如被联接件之一太厚不宜制成通孔,或没有足够的装配空间,又不需要经常拆卸的场合。
③双头螺柱联接:用于不能采用螺栓联接且又需要经常拆卸的场合。
材料疲劳断裂的改善方法

材料疲劳断裂的改善方法
材料疲劳断裂是指材料在受到循环载荷作用下逐渐发展并最终导致断裂的现象。
为了改善材料的疲劳断裂性能,可以采取以下方法:
1. 材料选择,选择具有较高抗疲劳性能的材料,如高强度钢、铝合金等,以提高材料的抗疲劳能力。
2. 表面处理,通过表面处理方式如喷丸、表面渗碳、氮化等提高材料表面的强度和耐疲劳性能,延长材料的使用寿命。
3. 结构设计,合理设计零部件结构,避免应力集中和缺口等缺陷,采用圆角、过渡半径等设计措施,减小应力集中,从而提高疲劳强度。
4. 表面涂层,采用表面涂层技术,如热喷涂、镀层等方式改善材料的表面性能,提高抗疲劳性能。
5. 热处理,通过热处理方式如回火、正火等改善材料的组织结构和性能,提高材料的抗疲劳能力。
6. 残余应力控制,通过冷加工、热处理等方式控制材料的残余
应力,减小应力集中,提高疲劳寿命。
7. 疲劳监测与预测,建立疲劳损伤的监测与预测体系,对材料
进行定期检测,及时发现疲劳损伤并采取相应措施。
综上所述,改善材料疲劳断裂的方法包括材料选择、表面处理、结构设计、表面涂层、热处理、残余应力控制以及疲劳监测与预测
等多种途径,通过综合应用这些方法可以有效提高材料的抗疲劳性能,延长材料的使用寿命。
第3章机械零件的疲劳强度

(kt ) D
说明
t t
kt
应力集中、零件尺寸和表面状态都只对应力幅有影 响,即疲劳极限主要受应力幅的影响
第三节 许用疲劳极限应力图
稳定变应力和非稳定变应力 许用(零件)疲劳极限应力图 工作应力增长规律
一、稳定变应力和非稳定变应力
稳定变应力:在每次循环中,平均应力σm、应力幅σa
和周期T都不随时间变化的变应力
2
45°
O
s0
2
45°
F S
sS
sm
sB
三、工程中的简化极限应力图(2)
sa
A B
疲劳塑性失 效区
s -1 s 0
疲劳和 塑性安 全区
2
45°
O
s0
2
F
sS
S
sm
sB
三、工程中的简化极限应力图(3)
sa
A B
疲劳塑性失 效区
s -1 s 0
疲劳和 塑性安 全区
2
45°
O
s0
2
45°
F
sS
S
sm
sB
sa
A
B
E
s -1
s0
2
45°
O
s0
2
45°
sS
S
sm
F
sB
s AE上各点: max s lim s m s a
如果 s max s max 不会疲劳破坏
s ES上各点: lim s m s a s s 如果 s max s s 不会屈服破坏
第三章 机械零件的疲 劳强度
机械零件的疲劳强度设计方法
1、安全——寿命设计
疲劳强度设计

疲劳强度设计对承受循环应力的零件和构件,根据疲劳强度理论和疲劳试验数据,决定其合理的结构和尺寸的机械设计方法。
机械零件和构件对疲劳破坏的抗力,称为零件和构件的疲劳强度。
疲劳强度由零件的局部应力状态和该处的材料性能确定,所以疲劳强度设计是以零件最弱区为依据的。
通过改进零件的形状以降低峰值应力,或在最弱区的表面层采用强化工艺,就能显著地提高其疲劳强度。
在材料的疲劳现象未被认识之前,机械设计只考虑静强度,而不考虑应力变化对零件寿命的影响。
这样设计出来的机械产品经常在运行一段时期后,经过一定次数的应力变化循环而产生疲劳,致使突然发生脆性断裂,造成灾难性事故。
应用疲劳强度设计能保证机械在给定的寿命内安全运行。
疲劳强度设计方法有常规疲劳强度设计、损伤容限设计和疲劳强度可靠性设计。
简史19 世纪40 年代,随着铁路的发展,机车车轴的疲劳破坏成为非常严重的问题。
1867年,德国A.沃勒在巴黎博览会上展出了他用旋转弯曲试验获得车轴疲劳试验结果,把疲劳与应力联系起来,提出了疲劳极限的概念,为常规疲劳设计奠定了基础。
20 世纪40 年代以前的常规疲劳强度设计只考虑无限寿命设计。
第二次世界大战中及战后,通过对当时发生的许多疲劳破坏事故的调查分析,逐渐形成了现代的常规疲劳强度设计,它非但提高了无限寿命设计的计算精确度, 而且可以按给定的有限寿命来设计零件,有限寿命设计的理论基础是线性损伤积累理论。
早在1924年,德国A.帕姆格伦在估算滚动轴承寿命时,曾假定轴承材料受到的疲劳损伤的积累与轴承转动次数(等于载荷的循环次数)成线性关系,即两者之间的关系可以用一次方程式来表示。
1945 年,美国M.A. 迈因纳根据更多的资料和数据,明确提出了线性损伤积累理论,也称帕姆格伦-迈因纳定理。
随着断裂力学的发展,美国 A.K. 黑德于1953 年提出了疲劳裂纹扩展的理论。
1957年,美国P.C.帕里斯提出了疲劳裂纹扩展速率的半经验公式。
03 疲劳强度计算
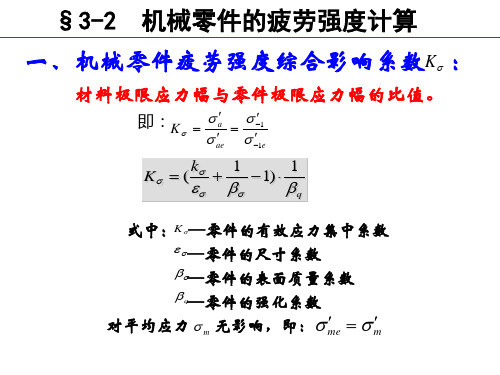
3、当量循环次数Ne
150 100 7 N e i ni 0.144 107 0.288 10 150 150 i 1
n m 9 9
80 7 7 0.36 10 0.1527 10 150
a
a a M , 1e 1e
a a M , 1e 1e
OM OC OD a a Sca OM OC OD a a
1e A
C
a Sca a , a Sca a
§3-2
机械零件的疲劳强度计算
一、机械零件疲劳强度综合影响系数K :材ຫໍສະໝຸດ 极限应力幅与零件极限应力幅的比值。
即:K a 1 ae 1e
K (
k
1
1)
1
q
式中:K —零件的有效应力集中系数 —零件的尺寸系数 —零件的表面质量系数 q—零件的强化系数 对平均应力 m 无影响,即: me m
造成的损伤相当。若满足 Sca s ,则安全。
i Ne ni i 1
n m
rN r m
e
No Ne
1 Sca S rN
e
例:有一转轴危险截面上受不稳定对称循环变应 力作用,如图示。转轴工作总时间为2400小时, 转速n=60r/min,材料为45钢, B=650MPa, -1=300MPa,疲劳曲线指数m=9, 0 107,零 N 件疲劳强度综合影响系数 K 2.413 ,许用安全 系数[s]=1.5,式校核该轴的强度。
Sca a 1e
- 1、下载文档前请自行甄别文档内容的完整性,平台不提供额外的编辑、内容补充、找答案等附加服务。
- 2、"仅部分预览"的文档,不可在线预览部分如存在完整性等问题,可反馈申请退款(可完整预览的文档不适用该条件!)。
- 3、如文档侵犯您的权益,请联系客服反馈,我们会尽快为您处理(人工客服工作时间:9:00-18:30)。
提高零件疲劳强度的方法
【摘要】 机械零件的抗疲劳破坏是造成机械运行故障的主要原因,因此,提高机
械零件的疲劳强度是机械结构设计中不容忽视的问题。针对影响零件疲劳强度的
因素并结合实际,对在设计过程中如何提高零件的疲劳强度的方法及措施做简要
的叙述和相关分析,且对工程中常见的问题,提出相应的控制方法和解决措施。
【关键词】疲劳强度 ;应力集中
1概述
在19世纪初,随着蒸汽机车的发明和铁路建设的迅速发展,机车车辆的疲
劳破坏现象时有发生,使工程技术人员认识到交变应力对金属强度的不良影响。
很多结构物都承受交变应力的作用,例如飞机,火车,船舶等交通运输工具由于
大气紊流,波浪及道路不平引起的颠簸都承受交变应力,即使是房屋,桥梁等看
来似乎完全不动的结构物也同样承受变应力作用,因为桥梁上驶过车辆时,房屋
中的机器设备运转和振动时,甚至刮风等均会引起交变应力。所以交变应力对于
结构物来说是经常遇到的。
绝大多数的机械零件是在循环变应力作用下工作的,如弹簧,齿轮,轴等都
是在循环载荷下工作的,承受交变应力或重复应力,如在工作过程中工作应力低
于屈服强度时就会发生疲劳破坏,造成重大的经济损失。为避免这些现象的发生,
提高零件的疲劳强度,在设计阶段应考虑它的使用环境和受力状态,材料性能,
加工工艺等因素。我将基于材料的疲劳特性,对提高零件疲劳强度的方法及措施
进行简要的叙述。
2零件的疲劳特性
材料的疲劳特性可用最大应力,应力循环次数,应力比(循环特性)来表述。
在一定的应力比下,当循环次数低于310时,属静应力强度,当循环次数在
43
10~10
时属于低周疲劳,然而一般零件承受变应力时,其应力循环次数通常大
于410,属高周疲劳,此阶段,如果作用的变应力小于持久疲劳极限,无论应力
变化多少次,材料都不会破坏。由于零件受加工质量及强化因素等影响,使得零
件的疲劳极限小于材料的疲劳极限,通常等于材料疲劳极限与其疲劳极限的综合
影响系数的比值。故可通过改善零件受力状况,将作用在零件上的变应力降低到
持久疲劳极限以下,对延长材料的使用寿命具有重要的意义。
3提高零件疲劳强度的方法
影响零件的疲劳强度的因素很多,比如材料的最大应力,工作环境,应力状
态,加工质量与加工工艺等。为提高零件的疲劳强度,经查阅资料得出以下方法。
(1)材料的选择
材料的选择原则是:在满足静强度要求的同时,还应具备良好的抗疲劳性能。
过去静强度选材的一个基本原则是要求强度高,但在疲劳设计中,需从疲劳强度
的观点选材:
a在达到使用期限的应力值时,材料的疲劳极限必须满足要求。
b材料的切口敏感性和擦伤疲劳敏感性小,在交变载荷作用处要特别注意。
c裂纹扩展速率慢,许用临界裂纹大些,及要求零件的断裂韧性值大,使零件或
结构在使用中出现裂纹后,不会很快导致灾难性的破坏。
d注意轧材和锻材等的纤维方向和主要受力方向应一致,因为在垂直纤维方向的
承载强度会下降百分之20左右。
e注意材料的抗腐蚀性能,同时尽量减小材料的内部缺陷,对重要零件应经探伤
检验。
f合理选择材料的热处理状态,他对疲劳特性的影响不能小看。
(2)降荷,降温设计
在实践应用中,人们发现,在较低的交变应力作用下,零件不易发生疲劳裂
纹,即使产生裂纹,其扩展速率也较慢。但究竟把应力水平控制在怎样的范围内
比较合适,尤其对确定初步设计中的应力水平非常重要。使用实践证实:组装成
型后的构件在低应力下运转一定周次后,再逐步提高到设计应力水平,也可提高
抗疲劳强度;对于发热摩擦零件采用降温设计,这些方法都能提高构件疲劳强度
及寿命。电子行业采取降荷降温设计后,会使某种电子产品的寿命由原来的平均
不足300小时,提高到3000小时左右。
(3)避免和减缓应力集中
零件的疲劳破坏一般是从最大应力处开始的,而应力集中通常是产生疲
劳裂纹的最主要原因,在设计时应尽量避免,可是在实际结构中要完全避免应力
集中问题几乎是不可能的。因此,在设计中应尽量减缓应力集中现象。结构件的
设计原则是:
a在零件中应避免横截面上出现急剧变化,当横截面形状或尺寸改变时,尽量用
大圆角来过渡,同时在设计时应避免传力路线的中断。
b尽可能采用对称结构,避免带有偏心的结构,在不对称处应注意局部弯曲引起
的应力。
c结构件应尽可能减少开口,特别在受拉表面尽量不开口,如需开口应考虑其形
状,以减小应力集中,同时开口的位置应设计在低应力区。
d铆钉及螺纹孔,焊缝等是产生应力的集中源,在其连接处适当加厚以降低局部
应力,对焊缝处磨平,采用去毛刺,边缘倒角等工艺是减小应力集中的有效方法。
e在主要零件存在应力集中的地方不应再连接次要零件,避免增大局部应力。
图(1)降低应力集中的几个案例
(4)降低表面粗糙度和改善表面质量
疲劳破坏通常从表面开始,疲劳裂纹一般在表面质量差的地方产生。因此,
在设计时需考虑:
a降低表面粗糙度,使表面状态系数增大,提高疲劳强度。
b采用表面强化工艺,是表层金属强度提高,使疲劳发生源从表面移至到表层以
下区域,达到提高零件的疲劳强度。如表面淬火等热处理,渗碳渗氮等化学热处
理以及滚压,喷丸等机械的硬化处理等方法,使材料表层的抗疲劳强度增加。
近年来,表面强化方法趋于完善,除了传统的零件硬化方法以外,液压机
械处理,振动滚压,金刚石熨平等新方法也得到了广泛应用。其中振动滚压法可
使中等硬度结构钢的冷作深度达30至50mm,而大大提高零件的疲劳极限。
还有各种复合强化方法,如表面塑性变形与表面淬火联合发,表面塑性变
形与热处理联合法,表面塑性变形与电镀联合法,表面塑性变形与对焊缝进行预
氩弧处理的复合强化等也得到了广泛应用。
c采用表面防腐措施,同时要注意防腐是否对疲劳性能产生不利影响,例如对电
镀零件应注意避免应力腐蚀现象。
d相对静止的两表面间应减小滑动,避免腐蚀擦伤,无法避免时应采用涂层或填
料来减小相互擦伤,如螺栓孔内加入紧配合的衬套。
e采用预变形工艺,即对零件在工作前使其产生部分塑性变形,造成有利的残余
压应力以提高零件的疲劳寿命,但同时要注意,引入残余拉应力会使材料的疲劳
强度下降。
f尽可能减小或消除零件表面可能发生的初始裂纹的尺寸,疲劳破坏通常是从初
始裂纹开始扩展的。止裂措施有:①采用多重受力件。一个构件由几个元件组成,
如果其中一个元件出现裂纹,不致扩展到其他元件上。②设置止裂孔和止裂缝,
当裂纹扩展到小孔或裂缝时,尖端变钝,使扩展减缓。③设置止裂件,在裂纹的
扩展途径上设置加强件。④采用断裂前自动报警的安全措施。例如压力容器断裂
前的渗漏报警等。
(5)合理的振动设计
对于高速运行或做往复振动的零件,在设计阶段应注意考虑其布局的合理性
以及运动状态的情况。
a设计时应通过与类似产品对比和计算,装配完成后经实测运动的自振频率,以
避免各个频率在适用范围内发生共振,造成零部件疲劳破坏。
b对于类似拉杆等运动机构上的操作系统,管路系统在设计时应考虑共振对其的
影响,设计时在振动大的地方加设支撑架或改变管路安装位置或将振动构件隔离
开等方法都可降低系统的振动。
c对振动系统中的板件,如翼板,振动机械支撑板等在设计时应考虑设置加强肋
以提高其整体刚度,避免因高频振动而使板件出现疲劳破坏。
e噪声源附近的结构板件应增加刚度与阻尼,例如喷气发动机的喷管后面就是一
个噪声源。夹层是较为常用的有效结构措施。
(6)可靠性设计
a冗余设计法:对薄弱零部件在设计阶段应考虑备份有能完全相同功能的结构,
如在飞机设计中采用平常不参与受力的辅助机构,当主要受力构件疲劳破坏后,
辅助构件参与承载主要受力构件的任务,保证其安全工作。
b安全使用期限设计法:对于容易损坏的构件采用有限寿命设计,这就要用可靠
性理论准确估计其疲劳寿命期限,当易损件达到使用寿命时及时更换,设计时采
用可开启式结构,易于维修,检查和更换。
c减荷设计法:设计时尽量减小结构件的内应力和应力集中,采用物理方法消除
或降低其内的应力。
d安全装置与安全检测设计法:采用信号监控装置,进行实时监控,如采用自行
监控与自行矫正的闭式反馈控制系统,这是当前安全设计的发展方向。
e采用多路传力结构或多重受力结构件设计方法:当其中一个结构件损坏后,其
它元件仍能继续受力,保证构件具有继续承载能力。如多梁飞机机翼就是一例,
此外结构的连接处和连接接头疲劳设计也不容轻视,任何结构件均由构件组合而
成,实践证明,疲劳破坏常常在连接部位出现,例如飞行器设计中的连接件设计
就是抗疲劳设计的重要内容。
4结束语
总之,在抗疲劳设计中,凡是有利于提高疲劳强度的方法及相应措施在设计
阶段应考虑及应用,凡可能会降低疲劳强度的因素应在设计中尽量避免。