硅的干法刻蚀简介
单晶硅干法刻蚀代加工

单晶硅干法刻蚀代加工
单晶硅作为半导体材料广泛应用于电子行业,单晶硅干法刻蚀是电子行业中用于制作集成电路电子元件的重要工艺。
因其具有精度高、结构紧凑、功能齐全等特点,受到越来越多的重视。
单晶硅干法刻蚀代加工是通过在单晶硅表面形成一种非晶膜来
实现的。
首先,用水素气体向单晶硅表面施加氧化热处理,以使其表面产生氧化层,氧化层可以有效地防止金属粒子进入,抑制表面失活和污染,从而使单晶硅具有高精度的加工性能。
接下来,将一种粒子状液体分布在表面上,经过恒定的电流刺激,使液体粒子的电荷发生变化,从而促进液体的分解,形成一种非晶膜。
单晶硅干法刻蚀代加工的过程是利用氧化层和非晶膜的力学性能,使多层膜的粘附力大于接触面之间的剪切力,从而进行有效的分解和消除。
接着,对非晶膜进行处理,有助于提高分解和去除效率,并有助于减少残留污垢。
此外,还可以通过水洗或酸洗来进一步去除杂质,从而实现最佳的加工结果。
单晶硅干法刻蚀代加工使得在微电子集成电路的制作中能够实
现更精确的刻蚀精度。
除了加工精度高外,它还有一个显著的优点,就是它的加工成本低廉,可以在短时间内提供大量的加工产品,满足客户的需求。
单晶硅干法刻蚀代加工技术的出现,为电子行业的发展奠定了基础,具有很强的现实意义。
它的出现,使得微电子行业能够更有效地开发新产品,制造更高精度的电子元件,节省成本,降低污染,甚至
可以提高产品的质量,提升企业的效率。
综上所述,单晶硅干法刻蚀代加工技术在微电子行业的应用前景非常广阔,它的出现为电子行业的发展带来了益处,必将在未来具有重要的作用。
1.晶体硅太阳能电池生产线刻蚀工序介绍

晶体硅太阳能电池生产线刻蚀工序介绍一、刻蚀工序基本作用目前常规太阳电池的生产流程如下:刻蚀作为太阳电池生产中的第三道工序,其主要作用是去除扩散后硅片四周的N型硅,防止漏电。
刻蚀一般情况下和去PSG联系在一起,去PSG 顾名思义,其作用是去掉扩散前的磷硅玻璃。
反应方程式如下:SiO2+6HF=H2SiF6+2H2O具体的刻蚀示意图如下:二、刻蚀的基本分类以及一般工艺流程目前,晶体硅太阳电池一般采用干法和湿法两种刻蚀方法。
下面我们分开介绍两种刻蚀方法的差别:1)干法刻蚀干法刻蚀夜叫等离子刻蚀。
即采用等离子体轰击的方法进行的刻蚀。
随着温度的升高,一般物质依次表现为固体、液体和气体。
它们统称为物质的三态。
如果温度升高到10e4K甚至10e5K,分子间和原子间的运动十分剧烈,彼此间已难以束缚,原子中的电子因具有相当大的动能而摆脱原子核对它的束缚,成为自由电子,原子失去电子变成带正电的离子。
这样,物质就变成了一团由电子和带正电的的离子组成的混合物。
这种混合物叫等离子体。
它可以称为物质的第四态。
等离子产生一般有三种方法:具体到太阳能电池中,等离子刻蚀是采用高频辉光放电反应,即采用感应耦合的方式使反应气体激活成活性粒子,如原子或游离基,这些活性粒子扩散到需刻蚀的部位,在那里与被刻蚀材料进行反应,形成挥发性生成物而被去除。
它的优势在于快速的刻蚀速率同时可获得良好的物理形貌(这是各向同性反应)。
下图为干法刻蚀的示意图:干法刻蚀具体的工艺过程如下:首先,母体分子CF4在高能量的电子的碰撞作用下分解成多种中性基团或离子,即CF4→CF3,CF2,CF,F,C以及它们的离子。
其次,这些活性粒子由于扩散或者在电场作用下到达SiO2表面,并在表面上发生化学反应(掺入O2,提高刻蚀速率)。
具体的反应过程可参考下图:在实际的太阳能电池的生产过程中,干法刻蚀中影响因素主要是CF4,O2的流量,辉光时间,辉光功率。
下面表格为常规的等离子刻蚀所用工艺。
二氧化硅 刻蚀反应原理

二氧化硅刻蚀反应原理二氧化硅刻蚀是一种常见的微细加工技术,广泛应用于集成电路制造和微电子设备的制备过程中。
其刻蚀原理涉及到化学反应、电子束、离子束等多个方面。
下面将详细介绍二氧化硅刻蚀反应原理。
首先,二氧化硅刻蚀可以通过湿法和干法两种方式进行。
湿法刻蚀是在液态介质中进行,干法刻蚀则是在气体环境中进行。
两种方式的刻蚀原理有所不同,下面将分别进行介绍。
一、湿法刻蚀反应原理湿法刻蚀是利用化学反应来去除二氧化硅材料的一种方法。
具体来说,湿法刻蚀涉及到酸或碱与二氧化硅之间的化学反应。
在这种反应中,刻蚀液中的酸或碱可以与二氧化硅反应生成可溶性的化合物,从而去除二氧化硅。
1.酸性湿法刻蚀酸性湿法刻蚀是利用酸性溶液与二氧化硅发生化学反应来去除二氧化硅。
常用的刻蚀液包括氢氟酸(HF)、硝酸(HNO3)等。
以氢氟酸刻蚀为例,二氧化硅与氢氟酸反应生成六氟硅酸:SiO2 + 6 HF → H2SiF6 + 2 H2O由于六氟硅酸是可溶性的,所以可以通过湿法刻蚀的方式去除二氧化硅。
2.碱性湿法刻蚀碱性湿法刻蚀是利用碱性溶液与二氧化硅发生化学反应来去除二氧化硅。
常用的刻蚀液包括氢氧化钠(NaOH)、氢氧化铵(NH4OH)等。
以氢氧化钠刻蚀为例,二氧化硅与氢氧化钠反应生成硅酸盐:SiO2 + 2 NaOH → Na2SiO3 + H2O由于硅酸盐是可溶性的,所以可以通过碱性湿法刻蚀的方式去除二氧化硅。
二、干法刻蚀反应原理干法刻蚀是利用离子束或电子束对二氧化硅进行刻蚀。
在干法刻蚀中,利用高能离子或电子束的撞击作用,直接将二氧化硅材料从表面剥离,从而实现刻蚀的目的。
干法刻蚀的过程中,主要包含物理击穿效应、表面反应和辅助剂等几个方面的原理。
1.物理击穿效应高能离子或电子束在撞击二氧化硅表面时,会导致二氧化硅材料的电子和空穴的产生。
当撞击能量达到一定程度时,二氧化硅表面的原子与气体分子之间会发生碰撞,从而引起碰撞粒子的散射或原子间的重新排列,最终导致二氧化硅的剥离和刻蚀。
干法刻蚀的优点和过程
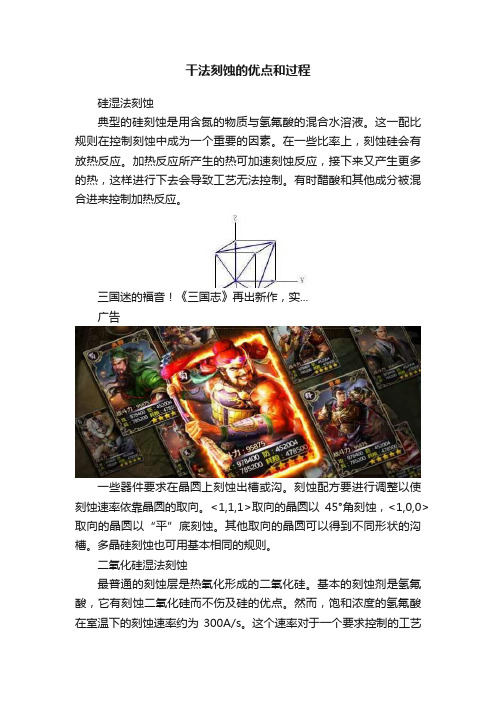
干法刻蚀的优点和过程硅湿法刻蚀典型的硅刻蚀是用含氮的物质与氢氟酸的混合水溶液。
这一配比规则在控制刻蚀中成为一个重要的因素。
在一些比率上,刻蚀硅会有放热反应。
加热反应所产生的热可加速刻蚀反应,接下来又产生更多的热,这样进行下去会导致工艺无法控制。
有时醋酸和其他成分被混合进来控制加热反应。
三国迷的福音!《三国志》再出新作,实...广告一些器件要求在晶圆上刻蚀出槽或沟。
刻蚀配方要进行调整以使刻蚀速率依靠晶圆的取向。
<1,1,1>取向的晶圆以45°角刻蚀,<1,0,0>取向的晶圆以“平”底刻蚀。
其他取向的晶圆可以得到不同形状的沟槽。
多晶硅刻蚀也可用基本相同的规则。
二氧化硅湿法刻蚀最普通的刻蚀层是热氧化形成的二氧化硅。
基本的刻蚀剂是氢氟酸,它有刻蚀二氧化硅而不伤及硅的优点。
然而,饱和浓度的氢氟酸在室温下的刻蚀速率约为300A/s。
这个速率对于一个要求控制的工艺来说太快了。
展开剩余79%在实际中,氢氟酸与水或氟化铵及水混合。
以氟化铵来缓冲加速刻蚀速率的氢离子的产生。
这种刻蚀溶液称为缓冲氧化物刻蚀或BOE。
针对特定的氧化层厚度,他们以不同的浓度混合来达到合理的刻蚀时间。
一些BOE公式包括一个湿化剂用以减小刻蚀表面的张力,以使其均匀地进入更小的开孔区。
暴露硅晶圆表面的过刻蚀可以引起表面的粗糙。
在氢氟酸工艺期间,当暴露于OH-离子时,在刻蚀中硅表面会变粗糙。
铝膜湿法刻蚀对于铝和铝合金层有选择性的刻蚀溶液是居于磷酸的。
遗憾的是,铝和磷酸反应的副产物是微小的氢气泡。
这些气泡附着在晶圆表面,并阻碍刻蚀反应。
结果既可能产生导致相邻引线短路的铝桥连,又可能在表面形成不希望出现的雪球的铝点。
特殊配方铝刻蚀溶液的使用缓解了这个问题。
典型的活性溶液成分配比是:16:1:1:2。
除了特殊配方外,典型的铝刻蚀工艺还会包含以搅拌或上下移动晶圆舟的搅动。
有时超声波或兆频超声波也用来去除气泡。
淀积氧化物湿法刻蚀晶圆上的最终膜层之一是一层在铝膜上的二氧化硅钝化膜。
干法刻蚀工艺文件
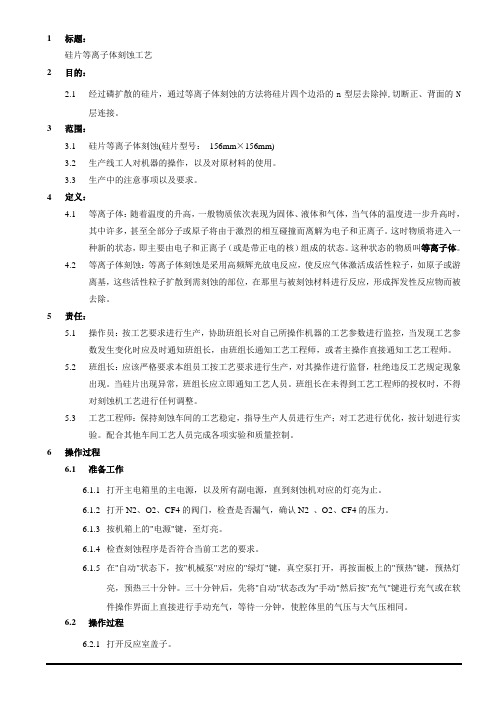
1标题:硅片等离子体刻蚀工艺2目的:2.1经过磷扩散的硅片,通过等离子体刻蚀的方法将硅片四个边沿的n型层去除掉,切断正、背面的N层连接。
3范围:3.1硅片等离子体刻蚀(硅片型号:156mm×156mm)3.2生产线工人对机器的操作,以及对原材料的使用。
3.3生产中的注意事项以及要求。
4定义:4.1等离子体:随着温度的升高,一般物质依次表现为固体、液体和气体,当气体的温度进一步升高时,其中许多,甚至全部分子或原子将由于激烈的相互碰撞而离解为电子和正离子。
这时物质将进入一种新的状态,即主要由电子和正离子(或是带正电的核)组成的状态。
这种状态的物质叫等离子体。
4.2等离子体刻蚀:等离子体刻蚀是采用高频辉光放电反应,使反应气体激活成活性粒子,如原子或游离基,这些活性粒子扩散到需刻蚀的部位,在那里与被刻蚀材料进行反应,形成挥发性反应物而被去除。
5责任:5.1操作员:按工艺要求进行生产,协助班组长对自己所操作机器的工艺参数进行监控,当发现工艺参数发生变化时应及时通知班组长,由班组长通知工艺工程师,或者主操作直接通知工艺工程师。
5.2班组长:应该严格要求本组员工按工艺要求进行生产,对其操作进行监督,杜绝违反工艺规定现象出现。
当硅片出现异常,班组长应立即通知工艺人员。
班组长在未得到工艺工程师的授权时,不得对刻蚀机工艺进行任何调整。
5.3工艺工程师:保持刻蚀车间的工艺稳定,指导生产人员进行生产;对工艺进行优化,按计划进行实验。
配合其他车间工艺人员完成各项实验和质量控制。
6操作过程6.1准备工作6.1.1打开主电箱里的主电源,以及所有副电源,直到刻蚀机对应的灯亮为止。
6.1.2打开N2、O2、CF4的阀门,检查是否漏气,确认N2 、O2、CF4的压力。
6.1.3按机箱上的"电源"键,至灯亮。
6.1.4检查刻蚀程序是否符合当前工艺的要求。
6.1.5在"自动"状态下,按"机械泵"对应的"绿灯"键,真空泵打开,再按面板上的"预热"键,预热灯亮,预热三十分钟。
多晶硅刻蚀特性的研究
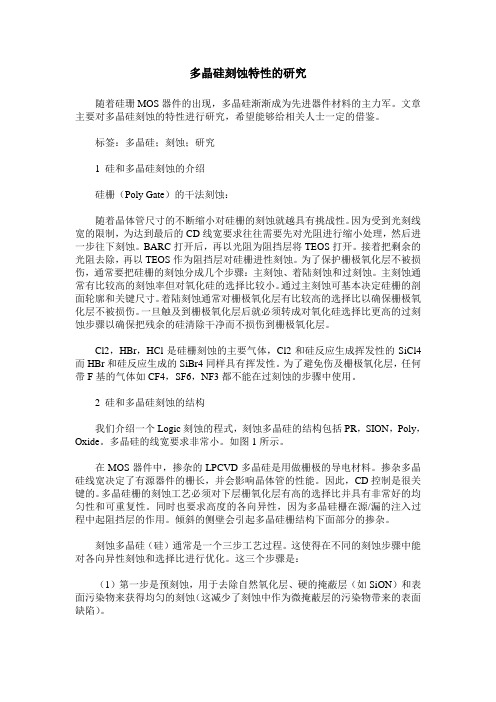
多晶硅刻蚀特性的研究随着硅珊MOS器件的出现,多晶硅渐渐成为先进器件材料的主力军。
文章主要对多晶硅刻蚀的特性进行研究,希望能够给相关人士一定的借鉴。
标签:多晶硅;刻蚀;研究1 硅和多晶硅刻蚀的介绍硅栅(Poly Gate)的干法刻蚀:随着晶体管尺寸的不断缩小对硅栅的刻蚀就越具有挑战性。
因为受到光刻线宽的限制,为达到最后的CD线宽要求往往需要先对光阻进行缩小处理,然后进一步往下刻蚀。
BARC打开后,再以光阻为阻挡层将TEOS打开。
接着把剩余的光阻去除,再以TEOS作为阻挡层对硅栅进性刻蚀。
为了保护栅极氧化层不被损伤,通常要把硅栅的刻蚀分成几个步骤:主刻蚀、着陆刻蚀和过刻蚀。
主刻蚀通常有比较高的刻蚀率但对氧化硅的选择比较小。
通过主刻蚀可基本决定硅栅的剖面轮廓和关键尺寸。
着陆刻蚀通常对栅极氧化层有比较高的选择比以确保栅极氧化层不被损伤。
一旦触及到栅极氧化层后就必须转成对氧化硅选择比更高的过刻蚀步骤以确保把残余的硅清除干净而不损伤到栅极氧化层。
Cl2,HBr,HCl是硅栅刻蚀的主要气体,Cl2和硅反应生成挥发性的SiCl4而HBr和硅反应生成的SiBr4同样具有挥发性。
为了避免伤及栅极氧化层,任何带F基的气体如CF4,SF6,NF3都不能在过刻蚀的步骤中使用。
2 硅和多晶硅刻蚀的结构我们介绍一个Logic刻蚀的程式,刻蚀多晶硅的结构包括PR,SION,Poly,Oxide。
多晶硅的线宽要求非常小。
如图1所示。
在MOS器件中,掺杂的LPCVD多晶硅是用做栅极的导电材料。
掺杂多晶硅线宽决定了有源器件的栅长,并会影响晶体管的性能。
因此,CD控制是很关键的。
多晶硅栅的刻蚀工艺必须对下层栅氧化层有高的选择比并具有非常好的均匀性和可重复性。
同时也要求高度的各向异性,因为多晶硅栅在源/漏的注入过程中起阻挡层的作用。
倾斜的侧壁会引起多晶硅栅结构下面部分的掺杂。
刻蚀多晶硅(硅)通常是一个三步工艺过程。
这使得在不同的刻蚀步骤中能对各向异性刻蚀和选择比进行优化。
单晶硅刻蚀工艺原理
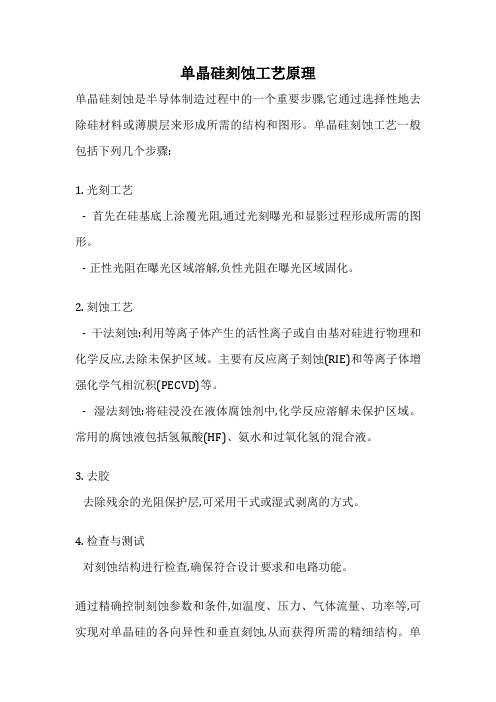
单晶硅刻蚀工艺原理
单晶硅刻蚀是半导体制造过程中的一个重要步骤,它通过选择性地去除硅材料或薄膜层来形成所需的结构和图形。
单晶硅刻蚀工艺一般包括下列几个步骤:
1. 光刻工艺
- 首先在硅基底上涂覆光阻,通过光刻曝光和显影过程形成所需的图形。
- 正性光阻在曝光区域溶解,负性光阻在曝光区域固化。
2. 刻蚀工艺
- 干法刻蚀:利用等离子体产生的活性离子或自由基对硅进行物理和化学反应,去除未保护区域。
主要有反应离子刻蚀(RIE)和等离子体增强化学气相沉积(PECVD)等。
- 湿法刻蚀:将硅浸没在液体腐蚀剂中,化学反应溶解未保护区域。
常用的腐蚀液包括氢氟酸(HF)、氨水和过氧化氢的混合液。
3. 去胶
去除残余的光阻保护层,可采用干式或湿式剥离的方式。
4. 检查与测试
对刻蚀结构进行检查,确保符合设计要求和电路功能。
通过精确控制刻蚀参数和条件,如温度、压力、气体流量、功率等,可实现对单晶硅的各向异性和垂直刻蚀,从而获得所需的精细结构。
单
晶硅刻蚀工艺广泛应用于集成电路、MEMS器件和其他微纳米结构的制造。
08工艺-刻蚀

Etch PR strip
Test Packaging Final Test
刻蚀的定义
• 基于光刻技术的腐蚀:刻蚀 • 湿法称腐蚀?干法称刻蚀? • 将光刻胶上的IC设计图形转移到硅片
表面 • 腐蚀未被光刻胶覆盖的硅片表面,实
现最终的图形转移 • 化学的,物理的或者两者的结合
栅极光刻曝光
Gate Mask
• 刻蚀本身的均匀性和材料膜厚的均匀性 • 特征尺寸的负载效应(loading effect) • 通常用标准偏差来定义 • 不同的定义给出不同的结果
非均匀性表达式
刻蚀的非均匀性(NU)可由下 面的公式计算(称为Max-Min uniformity, 适用于超净厂房的作业)
NU(%) = (Emax - Emin)/ 2Eave Emax = 测量到的最大刻蚀速率 Emin = 测量到的最小刻蚀速率 Eave = 刻蚀速率平均值
BOE)
二氧化硅的湿法刻蚀
• 氢氟酸溶液 (HF),极高的选择比。 • 通常用缓冲剂或去离子水稀释减少刻蚀速率
SiO2 + 6HF H2SiF6 + 2H2O • 广泛的应用于CVD长膜质量控制 • BOE: Buffered oxide etch缓冲氧化层腐蚀液
NH4F (6Vol 40%) : HF(1Vol 49wt%) • BSG > CVDSiO2 > 热SiO2 > PSG?
湿法刻蚀-2
• 纯化学性工艺,各向同性的侧壁形貌,高选 择比
• 在特征尺寸大于3微米时曾被广泛应用于IC制 造业。目前已被干法(等离子)刻蚀取代。
• 仍被应用在先进的IC厂
– 硅片的清洗 – 无图形的薄膜去除,如氮化硅和钛的去除。 – 测试硅片的薄膜去除和清洗。 – 应用于 CVD膜质量的控制 (缓冲氧化层刻蚀剂或
- 1、下载文档前请自行甄别文档内容的完整性,平台不提供额外的编辑、内容补充、找答案等附加服务。
- 2、"仅部分预览"的文档,不可在线预览部分如存在完整性等问题,可反馈申请退款(可完整预览的文档不适用该条件!)。
- 3、如文档侵犯您的权益,请联系客服反馈,我们会尽快为您处理(人工客服工作时间:9:00-18:30)。
→
着硅珊MOS器件的出现,多晶硅渐渐成为先进器件材料的主力军。
除了用作MOS栅
极之外多晶硅还广泛应用于DRAM的深沟槽电容极扳填充,闪存工艺中的位线和字线。
这些工艺的实现都离不开硅的干法刻蚀技术其中还包括浅槽隔离的单晶硅刻蚀和金属硅化物的刻蚀。
为了满足越来越苛刻的要求,业界趋向于采用较低的射频能量并能产生低压和高密度的等离子体来实现硅的干法刻蚀。
感应耦合等离子刻蚀技术(ICP)被广泛应用于硅及金属硅化物刻蚀,具有极大技术优势和前景。
它比典型的电容耦合(CCP)等离子刻蚀技术高出10 ̄20倍。
此外,其对离子浓度和能量的独立控制扩大了刻蚀工艺窗口及性能。
硅栅(Poly Gate)的干法刻
蚀:
随着晶体管尺寸的不断缩小对硅栅的刻蚀就越具有挑战性。
这种挑战体现在对关键尺寸(CD)及其均匀性的控制,即对栅氧化层选择比的提高,对剖面轮廓的一致性控制以及减少等离子导致的损伤。
因为受到光刻线宽的限制,为达到最后的CD 线宽要求往往需要先对光阻进行缩小处理,然后进一步往下刻蚀。
BARC打开后,再以光阻为阻挡层将TEOS 打开。
接着把剩余的光阻去除,再以TEOS作为阻挡层对硅栅进行刻蚀。
为了保护栅极氧化层不被损伤,通常要把硅栅的刻蚀分成几个步骤:主刻蚀、着陆刻蚀和过刻蚀。
主刻蚀通常有比较高的刻蚀率但对氧化硅的选择比较小。
通过主刻蚀可基本决定硅栅的剖面
硅的干法刻蚀简介
应用材料中国,葛强
轮廓和关键尺寸。
着陆刻蚀通常对栅极氧化层有比较高的选择比以确保栅极氧化层不被损伤。
一旦触及到栅极氧化层后就必须转成对氧化硅选择比更高的过刻蚀步骤以确保把残余的硅清除干净而不损伤到栅极氧化层。
CL2,HBr,HCL是硅栅刻蚀的主要气体,CL2和硅反应生成挥发性的SiCl4而HBr和硅反应生成的SiBr4 同样具有挥发性。
通常会在这些主刻蚀气体中加入小流量的氧气,一方面是为了在侧壁生成氧化硅从而增加对侧壁的保护;另一方面也提高了对栅极氧化层的选择比。
在标准的ICP双耦合刻蚀腔体中,HBr-O2的组合通常能达到大于100:1的选择比。
为了避免伤及栅极氧化层,任何带F基的气体如CF4,SF6,NF3都不能在过刻蚀的步骤中使用。
浅沟槽(STI)的干法刻蚀:
在0.25um和以下的技术节点中,浅沟槽隔离技术被广泛应用。
因为它在减小表面积的同时提供更加有效的隔离。
作为沟槽硅刻蚀的阻挡层可以直接用光阻但更多是采用氮化硅作为硅刻蚀的阻挡层。
先用光阻作为氮化硅刻蚀的阻挡层,然后用氧等离子体将剩余的光阻除去,最后以氮化硅为阻挡层完成浅沟槽的刻蚀。
浅沟槽刻蚀的难点在于沟槽深度的匀度小于100仯
饩拖嗟庇谛∮?.25%
的均匀性。
随着硅片尺寸的增加要达到这样的要求就必须严格控制氮化过刻蚀、BT刻蚀和浅槽刻蚀的均匀性,每一步都会对最后的结果产生影响。
其次为了满足沟槽隔离氧化物的填充要求,剖面轮廓的控制也是非常重要的环节。
因
随
为太垂直的轮廓不利于HDPCVD的沉积,所以通常会要求适当的倾斜度。
另外随着工艺尺寸的缩小,要求达到更高的深宽比使得剖面轮廓控制和深度均匀性控制受到更大的挑战.。
当然CD 的均匀性和剩余氮化硅的均匀性也是重要的技术指标。
CL2和HBr依然是浅沟槽的刻蚀的主要气体,再配合小流量的氧气和氮气来产生氮氧化硅形成侧壁钝化层从而达到理想的刻蚀剖面轮廓。
氦气和氩气通常用作辅助稀释的作用。
另外浅槽底部轮廓同样影响到氧化物的填充。
采用CL2 做为主刻蚀的气体容易形成比较直的剖面轮廓和凸型的底部轮廓。
采用HBr 作为主刻蚀气体能得到比较斜的剖面轮廓和凹形的底部轮廓。
在实际生产中经常会遇到硅刻蚀的反应物没有被及时的清洗从而导致产品被污染的现象。
这是因为硅片完成刻蚀离开反应腔时,在硅片的表面还有大量的Cl 和Br 残留。
它们具有较强的挥发
性。
当硅片暴露在空气中,空气中的水汽和CL、Br形成HCL和 HBr。
这些酸性物质会腐蚀和它们接触的表面形成一定程度的污染。
为了防止这样的现象发生可以采用O2等离子清除表面的残留,或者利用腔体净化功能减少污染源。
另外还应尽量减少硅片暴露在空气中的时间,尽快洗去表面污染物。
随着关键尺寸的不断缩小和硅片尺寸的扩大。
先进的300mm 硅刻蚀工艺腔体的气体和温度多采用内圈和外圈独立的控制以满足苛刻的工艺要求。
可变的腔体尺寸也是业界的方向之一。
腔体内环境的控制和不同硅片的一致性控制也是生产中最常遇到的问题。