干法刻蚀和湿法刻蚀
纳米刻蚀工艺中的干法刻蚀与湿法刻蚀比较

纳米刻蚀工艺是纳米制造中的一项关键技术,它通过物理或化学方法去除材料,以达到制造纳米级别结构的目的。
在纳米刻蚀工艺中,干法刻蚀和湿法刻蚀是两种主要的刻蚀方法,它们各自具有不同的特点,也适用于不同的应用场景。
首先,让我们来看看干法刻蚀。
在干法刻蚀中,我们通常使用物理手段如离子刻蚀、反应离子刻蚀(RIE)、机械研磨等。
这些方法的主要优点是刻蚀速度快,对材料的兼容性好,能够处理各种不同类型的材料。
然而,这种方法也存在一些缺点。
首先,它对设备的要求较高,需要专门的设备和技术支持。
其次,由于其刻蚀过程中可能产生微小碎片,因此在处理敏感材料时需要特别小心。
此外,干法刻蚀对于深宽比的保持相对较差,即对同一尺寸的图形,干法刻蚀可能需要更大的实际面积。
接下来是湿法刻蚀,这种方法主要利用化学反应来去除材料。
常见的湿法刻蚀技术包括化学腐蚀、等离子体腐蚀等。
与干法刻蚀相比,湿法刻蚀对许多材料具有更强的兼容性,特别是在高分子材料和绝缘材料上。
此外,湿法刻蚀在处理大面积样品时更具优势,因为它不需要精确的定位和设备支持。
然而,湿法刻蚀也存在一些问题,如腐蚀液的选择和配比需要严格控制,以及对一些材料可能产生过敏反应的风险。
而且,湿法刻蚀的刻蚀深度较浅,对于深结构可能无法达到预期的刻蚀效果。
总的来说,干法刻蚀和湿法刻蚀各有优缺点,适用于不同的应用场景。
在选择使用哪种方法时,我们需要考虑待处理材料的性质、刻蚀速度的需求、设备的可用性以及成本等因素。
而且,随着技术的进步,我们期待在未来看到更多创新的纳米刻蚀方法出现,以满足更复杂、更高精度的纳米制造需求。
晶圆刻蚀工艺

晶圆刻蚀工艺
晶圆刻蚀工艺是一种制造集成电路的重要工艺。
其基本原理是将蚀刻液浸入晶圆表面,通过光刻等工艺制作出待加工部位,然后加入激发剂和酸碱等反应物,使其与晶圆表面发生化学反应,将待加工部位去除,从而形成所需的模式和结构。
具体的刻蚀工艺可以分为干法和湿法两种。
其中,干法刻蚀工艺利用离子束、电子束或激光等能量高、速度快的精密加工工具,将待加工部位“烧掉”或“削掉”,精度高。
湿法刻蚀工艺则是通过刻蚀液与晶圆表面反应,将待加工部位溶解和蚀刻,具有速度快、成本低的优点。
晶圆刻蚀工艺在微电子、光电子、纳米科学等领域都有广泛应用,并且不断发展创新。
半导体制造工艺刻蚀
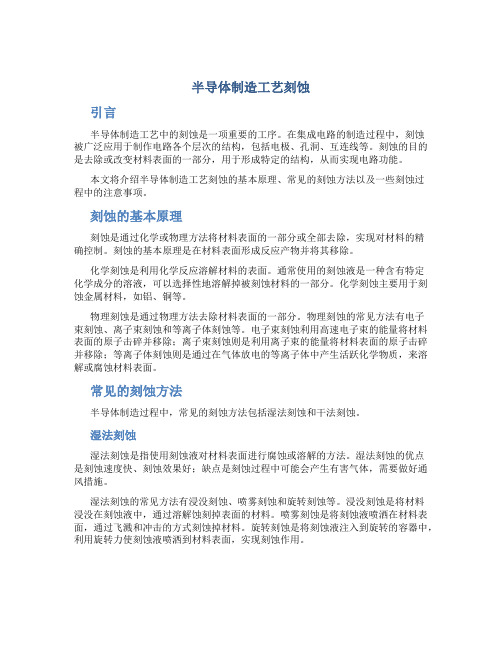
半导体制造工艺刻蚀引言半导体制造工艺中的刻蚀是一项重要的工序。
在集成电路的制造过程中,刻蚀被广泛应用于制作电路各个层次的结构,包括电极、孔洞、互连线等。
刻蚀的目的是去除或改变材料表面的一部分,用于形成特定的结构,从而实现电路功能。
本文将介绍半导体制造工艺刻蚀的基本原理、常见的刻蚀方法以及一些刻蚀过程中的注意事项。
刻蚀的基本原理刻蚀是通过化学或物理方法将材料表面的一部分或全部去除,实现对材料的精确控制。
刻蚀的基本原理是在材料表面形成反应产物并将其移除。
化学刻蚀是利用化学反应溶解材料的表面。
通常使用的刻蚀液是一种含有特定化学成分的溶液,可以选择性地溶解掉被刻蚀材料的一部分。
化学刻蚀主要用于刻蚀金属材料,如铝、铜等。
物理刻蚀是通过物理方法去除材料表面的一部分。
物理刻蚀的常见方法有电子束刻蚀、离子束刻蚀和等离子体刻蚀等。
电子束刻蚀利用高速电子束的能量将材料表面的原子击碎并移除;离子束刻蚀则是利用离子束的能量将材料表面的原子击碎并移除;等离子体刻蚀则是通过在气体放电的等离子体中产生活跃化学物质,来溶解或腐蚀材料表面。
常见的刻蚀方法半导体制造过程中,常见的刻蚀方法包括湿法刻蚀和干法刻蚀。
湿法刻蚀湿法刻蚀是指使用刻蚀液对材料表面进行腐蚀或溶解的方法。
湿法刻蚀的优点是刻蚀速度快、刻蚀效果好;缺点是刻蚀过程中可能会产生有害气体,需要做好通风措施。
湿法刻蚀的常见方法有浸没刻蚀、喷雾刻蚀和旋转刻蚀等。
浸没刻蚀是将材料浸没在刻蚀液中,通过溶解蚀刻掉表面的材料。
喷雾刻蚀是将刻蚀液喷洒在材料表面,通过飞溅和冲击的方式刻蚀掉材料。
旋转刻蚀是将刻蚀液注入到旋转的容器中,利用旋转力使刻蚀液喷洒到材料表面,实现刻蚀作用。
干法刻蚀干法刻蚀是指利用气体等离子体或物理方法对材料表面进行刻蚀的方法。
干法刻蚀的优点是刻蚀过程中不产生液体,可以避免污染问题;缺点是刻蚀速度较慢。
干法刻蚀的常见方法有等离子体刻蚀、离子束刻蚀和电子束刻蚀等。
等离子体刻蚀是通过在气体放电的等离子体中产生活跃化学物质,来溶解或腐蚀材料表面。
光伏电池刻蚀原理
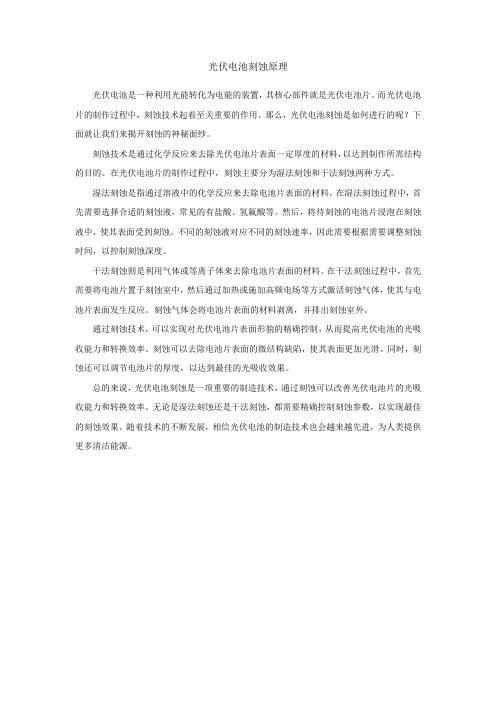
光伏电池刻蚀原理
光伏电池是一种利用光能转化为电能的装置,其核心部件就是光伏电池片。
而光伏电池片的制作过程中,刻蚀技术起着至关重要的作用。
那么,光伏电池刻蚀是如何进行的呢?下面就让我们来揭开刻蚀的神秘面纱。
刻蚀技术是通过化学反应来去除光伏电池片表面一定厚度的材料,以达到制作所需结构的目的。
在光伏电池片的制作过程中,刻蚀主要分为湿法刻蚀和干法刻蚀两种方式。
湿法刻蚀是指通过溶液中的化学反应来去除电池片表面的材料。
在湿法刻蚀过程中,首先需要选择合适的刻蚀液,常见的有盐酸、氢氟酸等。
然后,将待刻蚀的电池片浸泡在刻蚀液中,使其表面受到刻蚀。
不同的刻蚀液对应不同的刻蚀速率,因此需要根据需要调整刻蚀时间,以控制刻蚀深度。
干法刻蚀则是利用气体或等离子体来去除电池片表面的材料。
在干法刻蚀过程中,首先需要将电池片置于刻蚀室中,然后通过加热或施加高频电场等方式激活刻蚀气体,使其与电池片表面发生反应。
刻蚀气体会将电池片表面的材料剥离,并排出刻蚀室外。
通过刻蚀技术,可以实现对光伏电池片表面形貌的精确控制,从而提高光伏电池的光吸收能力和转换效率。
刻蚀可以去除电池片表面的微结构缺陷,使其表面更加光滑。
同时,刻蚀还可以调节电池片的厚度,以达到最佳的光吸收效果。
总的来说,光伏电池刻蚀是一项重要的制造技术,通过刻蚀可以改善光伏电池片的光吸收能力和转换效率。
无论是湿法刻蚀还是干法刻蚀,都需要精确控制刻蚀参数,以实现最佳的刻蚀效果。
随着技术的不断发展,相信光伏电池的制造技术也会越来越先进,为人类提供更多清洁能源。
太阳能电池刻蚀原理

太阳能电池刻蚀原理太阳能电池是一种将太阳能直接转化为电能的装置,它起到了关键的作用,使得可再生能源的利用成为可能。
而太阳能电池的核心部件就是光伏电池芯片。
光伏电池芯片是由多层材料组成的薄片,其中的刻蚀工艺在制造过程中起到了至关重要的作用。
刻蚀是一种通过化学或物理手段将材料表面的一部分去除的加工方法。
在太阳能电池的制造过程中,刻蚀被广泛应用于光伏电池芯片的制备。
刻蚀的目的是为了改变材料的形状、尺寸和性能,从而提高光伏电池的效率。
在太阳能电池的制造中,常用的刻蚀方法有湿法刻蚀和干法刻蚀两种。
湿法刻蚀是利用化学溶液对材料表面进行腐蚀,以达到改变表面形态的目的。
干法刻蚀则是通过高能离子束或者等离子体对材料进行加工,使其表面发生形貌的变化。
光伏电池芯片的刻蚀主要是为了增加其表面积,从而增强光伏效应。
太阳能电池的工作原理是通过光子的能量激发材料中的电子,使其跃迁到导电层,形成电流。
而光伏电池芯片的表面积越大,能够吸收太阳光的能力就越强,从而产生的电流也就越大。
在制造光伏电池芯片时,刻蚀可以通过控制刻蚀液的浓度、温度和刻蚀时间来实现。
刻蚀液中的化学物质会与材料表面的原子相互作用,使其发生腐蚀。
通过调整刻蚀液的参数,可以控制刻蚀速率和刻蚀深度,从而达到理想的刻蚀效果。
刻蚀过程中还需要考虑材料的选择和掩膜的设计。
材料的选择要考虑其对刻蚀液的耐蚀性和刻蚀速率的影响。
而掩膜的设计则是为了保护不需要刻蚀的区域,防止刻蚀液对芯片其他部分的损伤。
刻蚀技术的发展对太阳能电池的制造起到了重要的推动作用。
通过刻蚀工艺的优化,可以实现光伏电池芯片表面的微纳结构调控,提高光的吸收能力,增加电流输出,从而提高太阳能电池的转化效率。
刻蚀是太阳能电池制造中不可或缺的工艺之一。
通过刻蚀,可以改变光伏电池芯片的表面形态和性能,提高光的吸收能力,增加电流输出。
刻蚀技术的不断发展和优化将进一步推动太阳能电池的性能提升和应用拓展。
简述刻蚀工艺的主要作用

简述刻蚀工艺的主要作用
刻蚀工艺的主要作用是在光刻的基础上,有选择地转移图形。
具体来说,刻蚀是用化学或物理方法有选择地从硅片表面去除不需要的材料,其基本目标是在涂胶的硅片上正确地复制掩模图形。
在半导体制程中,刻蚀就是用化学的、物理的或同时使用化学和物理的方法,在光刻的基础上有选择地进行图形的转移。
刻蚀技术主要分为干法刻蚀与湿法刻蚀。
干法刻蚀主要利用反应气体与等离子体进行刻蚀;湿法刻蚀主要利用化学试剂与被刻蚀材料发生化学反应进行刻蚀。
刻蚀工艺发展历程
刻蚀工艺发展历程刻蚀工艺是一种常用的微纳加工技术,通过控制化学反应或物理过程,将材料表面的部分物质去除,从而得到所需的结构和形状。
在微电子、光学、生物医学等领域都有广泛应用。
本文将从刻蚀工艺的起源开始,逐步介绍其发展历程。
一、起源与初期发展刻蚀工艺的起源可以追溯到20世纪初期。
最早的刻蚀方法是机械刻蚀,即使用机械设备进行刻蚀,如机械雕刻机。
这种方法虽然简单粗暴,但却被广泛应用于半导体和光学器件的制造中。
随着科学技术的进步,人们开始尝试利用化学方法进行刻蚀。
1927年,美国化学家R. W. Wood首次提出了化学刻蚀的概念,并成功地利用酸性溶液对金属表面进行了刻蚀。
这一发现开启了刻蚀工艺的新篇章。
二、湿法刻蚀的发展在20世纪中叶,随着半导体工业的兴起,湿法刻蚀成为主流。
湿法刻蚀是利用酸性或碱性溶液对材料表面进行刻蚀。
最早的湿法刻蚀方法是浸泡刻蚀,即将待刻蚀的材料浸泡在溶液中,通过溶液与材料表面的化学反应来实现刻蚀。
随着对刻蚀工艺的深入研究,人们逐渐发现了湿法刻蚀的一些局限性,如刻蚀速率低、刻蚀精度不高等。
为了解决这些问题,人们开始探索新的湿法刻蚀方法。
1950年代,美国贝尔实验室研究人员发现,通过加热溶液可以显著提高刻蚀速率,这就是热刻蚀。
热刻蚀利用高温加速化学反应速率,从而提高刻蚀速率和精度。
人们还发现了选择性刻蚀的方法。
选择性刻蚀是指在刻蚀过程中,只对特定材料或特定方向进行刻蚀,而不影响其他材料或方向。
这种方法广泛应用于半导体器件的制造中,可以实现微米级的精确刻蚀。
三、干法刻蚀的崛起随着微纳加工技术的发展,湿法刻蚀逐渐暴露出一些局限性,如溶液的浓度控制困难、污染问题等。
为了解决这些问题,人们开始研究干法刻蚀。
干法刻蚀是利用气体或等离子体进行刻蚀。
最早的干法刻蚀方法是离子束刻蚀,即利用高能离子束对材料表面进行刻蚀。
离子束刻蚀可以实现高速刻蚀和高精度刻蚀,但设备复杂、成本高,限制了其应用范围。
后来,人们发现了等离子体刻蚀的方法。
刻蚀工艺名词解释
刻蚀工艺名词解释
把未被抗蚀剂掩蔽的薄膜层除去,从而在薄膜上得到与抗蚀剂膜上完全相同图形的工艺。
在集成电路制造过程中,经过掩模套准、曝光和显影,在抗蚀剂膜上复印出所需的图形,或者用电子束直接描绘在抗蚀剂膜上产生图形,然后把此图形精确地转移到抗蚀剂下面的介质薄膜(如氧化硅、氮化硅、多晶硅)或金属薄膜(如铝及其合金)上去,制造出所需的薄层图案。
刻蚀就是用化学的、物理的或同时使用化学和物理的方法,有选择地把没有被抗蚀剂掩蔽的那一部分薄膜层除去,从而在薄膜上得到和抗蚀剂膜上完全一致的图形。
刻蚀技术主要分为干法刻蚀与湿法刻蚀。
干法刻蚀主要利用反应气体与等离子体进行刻蚀;湿法刻蚀主要利用化学试剂与被刻蚀材料发生化学反应进行刻蚀。
刻蚀相关知识点总结
刻蚀相关知识点总结刻蚀技术主要分为湿法刻蚀和干法刻蚀两种。
湿法刻蚀是在溶液中通过化学反应去除材料表面的工艺,而干法刻蚀是在气相中通过物理或化学反应去除材料表面的工艺。
下面将详细介绍刻蚀的相关知识点。
一、刻蚀的基本原理1. 湿法刻蚀原理湿法刻蚀是利用化学溶液对材料表面进行腐蚀或溶解的工艺。
湿法刻蚀的原理是在溶液中加入具有特定功能的化学试剂,使其与被刻蚀物质发生化学反应,从而去除材料表面的部分物质。
湿法刻蚀通常可以实现较高的刻蚀速率和较好的表面质量,但需要考虑溶液中的成分和温度对环境的影响。
2. 干法刻蚀原理干法刻蚀是利用气相中的等离子体或化学反应对材料表面进行腐蚀或清除的工艺。
干法刻蚀的原理是在高能离子束或化学气体的作用下,使被刻蚀物质表面发生物理或化学反应,从而去除材料表面的部分物质。
干法刻蚀通常可以实现更高的加工精度和更好的表面质量,但需要考虑设备的复杂性和成本的影响。
二、刻蚀的工艺参数1. 刻蚀速率刻蚀速率是刻蚀过程中单位时间内去除的材料厚度,通常以单位时间内去除的厚度为单位。
刻蚀速率的选择需要综合考虑刻蚀材料的性质、刻蚀条件、刻蚀设备和加工要求等因素。
2. 刻蚀选择性刻蚀选择性是指在多种材料叠加或混合结构中选择性地去除某一种材料的能力。
刻蚀选择性的选择需要考虑被刻蚀材料和其它材料之间的化学反应性和物理性质的差异,以实现精确的刻蚀。
3. 刻蚀均匀性刻蚀均匀性是指在整个刻蚀过程中去除材料的厚度分布情况。
刻蚀均匀性的选择需要考虑刻蚀设备和刻蚀条件对被刻蚀物质的影响,以实现均匀的刻蚀。
4. 刻蚀深度控制刻蚀深度控制是指在整个刻蚀过程中去除材料的深度分布情况。
刻蚀深度控制的选择需要综合考虑刻蚀设备和刻蚀条件对被刻蚀物质的影响,以实现精确的刻蚀深度。
5. 刻蚀环境控制刻蚀环境控制是指在整个刻蚀过程中对刻蚀环境(如溶液中的成分、气相中的气体、温度和压力等)的控制。
刻蚀环境控制的选择需要考虑被刻蚀材料的特性和加工的要求,以实现良好的刻蚀效果。
(第六章)刻蚀知识讲解
干法刻蚀的缺点(与湿法腐蚀比) 1. 对下层材料的刻蚀选择比较差 2. 等离子体诱导损伤 3. 设备昂贵
干法刻蚀过程
1. 刻蚀气体进入反应腔 2. RF电场使反应气体分解电离 3. 高能电子、离子、原子、自由基等结合产生等离子体 4. 反应正离子轰击表面-各向异性刻蚀(物理刻蚀) 5. 反应正离子吸附表面 6. 反应元素(自由基和反应原子团)和表面膜的表面反
= ΔTsio2/ΔT胶
(a)0时刻
(b)t1时刻
5. 均匀性 刻蚀均匀性是指刻蚀速率在整个硅片或整批硅片上 的一致性情况。非均匀性刻蚀会产生额外的过刻蚀。
ARDE效应-微负载效应:Aspect Ratio Dependence Etching
Emax:最大刻蚀速率 Emin:最小刻蚀速率 Eave:平均刻蚀速率
(b) Substrate after etch
6.1 引 言
刻蚀的工艺目的: 把光刻胶图形精确地转移到硅片上,最后达到复制 掩膜版图形的目的。它是在硅片上复制图形的最后 主要图形转移工艺。
刻蚀工艺分类:干法刻蚀和湿法刻蚀
✓ 干法刻蚀:把要刻蚀的硅片放在具有反应气体的等 离子体真空腔中去除表面层材料的工艺过程。亚微 米
硅槽
湿法刻蚀是各向同性腐蚀, 干法刻蚀有各向同性腐蚀,也
不能实现图形的精确转移, 有各向异性腐蚀。各向异性腐
一般用于特征尺寸较大的
蚀能实现图形的精确转移,是
情况(≥3μm) 。
集成电路刻蚀工艺的主流技术。
3. 刻蚀偏差
刻蚀偏差是指刻蚀以后线宽或关键尺寸的变化 刻蚀偏差=Wa-Wb
Wb
Wa
Bias
✓ 湿法刻蚀:把要腐蚀的硅片放在化学腐蚀液里去除 表面层材料的工艺过程。大于3微米
- 1、下载文档前请自行甄别文档内容的完整性,平台不提供额外的编辑、内容补充、找答案等附加服务。
- 2、"仅部分预览"的文档,不可在线预览部分如存在完整性等问题,可反馈申请退款(可完整预览的文档不适用该条件!)。
- 3、如文档侵犯您的权益,请联系客服反馈,我们会尽快为您处理(人工客服工作时间:9:00-18:30)。
1 干法刻蚀和湿法刻蚀
干法刻蚀是把硅片外表暴露于空气中产生的等离子体,等离子体通过光刻胶中开出的窗口,与硅片发生物理或化学反响,从而去掉暴露的外表材料。
湿法腐蚀是以液体化学试剂以化学方式去除硅片外表的材料。
2刻蚀速率是指在刻蚀过程中去除硅片外表材料的速度,通常用。
A/min表示
刻蚀速率=T/t(。
A/min)
其中T=去掉的材料厚度
t=刻蚀所用的时间
为了高的产量,希望有高的刻蚀速率。
3刻蚀选择比指的是同一刻蚀条件下一种材料与另一种刻蚀材料相比刻蚀速率快多少。
他定义为被刻蚀材料的刻蚀速率与另一种材料的刻蚀速率的比。
干法刻蚀的选择比低,通常不能提供对下一层材料足够高的刻蚀选择比。
高选择比意味着只刻除想要刻去的那层。
4干法刻蚀的主要目的完整的把掩膜图形复制到硅片外表上。
优点:刻蚀剖面是各向异性,具有非常好的侧壁剖面控制,
好的CD控制
最小的光刻胶脱落或粘附问题
好的片内,片间,批次间的刻蚀均匀性
较低的化学制品使用和处理费用
缺乏:对下层材料的差的刻蚀选择比,等离子体带来的器件损伤和昂贵的设备。
5化学机理:等离子体产生的反响元素与硅片外表的物质发生反响,为了获得高的选择比,进入腔体的气体都经过了慎重选择。
等离子体化学刻蚀由于它是各向同性的,因而线宽控制差。
物理机理:等离子体产生的带能粒子在强电场下朝硅片外表加速,这些离子通过溅射刻蚀作用去除未被保护的硅片外表材料。
6根本部件:发生刻蚀反响的反响腔,一个产生等离子体的射频电源,气体流量控制系统,去除刻蚀生成物和气体的真空系统。
氟刻蚀二氧化硅,氯和氟刻蚀铝,氯,氟和溴刻蚀硅,氧去除光刻胶。
7z微波鼓励源来产生高密度等离子体。
ECR反响器的一个关键点是磁场平行于反映剂的流动方向,这使得自由电子由于磁力的作用做螺旋形运动。
当电子的盘旋频率等于所加的微波电场频率时,能有效把电能转移到等离子体中的电子上。
这种振荡增加了电子碰撞的可能性,从而产生高密度的等离子体,获得大的离子流。
8氟基气体
三个步骤:1,预刻蚀,用于去除自然氧化层,硬的掩蔽层和外表污染物来获得均匀的刻蚀2,刻至终点的主刻蚀,用来刻蚀大局部的多晶硅膜,并不损伤栅氧化层和获得理想的各向异性的侧壁剖面。
3,过刻蚀,用于去除刻蚀残留物和剩余多晶硅,并保证对栅氧层的高选择比。
9 氮化硅掩蔽层是用热磷酸进行湿法化学剥离的,这种酸槽一般维持在160摄氏度左右并对露出的氧化硅具有所希望的高选择比,通过使用检控样片进行定时操作。
在暴露的氮化硅上会形成一层氮氧化硅,在去除前,需要在氢氟酸中进行短时间的处理。