制动系统设计计算分析
CRH和谐系列动车组制动系统分析

摘要制动系统是动车组的一个重要组成部分,他直接影响动车组的安全性。
动车组制动系统是用以强制性适中的动车减速或停车、使下坡形式的动车车速保持稳定以及使已停驶的动车组驻留不动的机构。
随着和谐系列动车组迅速发展和撤诉的提高一级车流密度的日益增大,为了保证行车安全,动车租制动系统的工作可靠性显得日益重要。
也只有制动效能良好,制动系统工作可靠地“CRH”和谐系列动车组才能成分发挥其动力性能。
本文主要以动车组制动系统为题,展开分析与讨论,本文主要讨论工作有:分析动车组制动系统的基本特点:提出动车组制动系统的基本组成空气制动,电空制动电制动等各项功能的实现方法分析动车组电制动、空气制动、防滑装置系统工作的原理参考现有动车组牵引、制动计算教材,系统地研究整理出动车组的制动计算公式,包括作用在动车上的合力、空气制动的计算、再生制动计算、空气制动和再生制动的分配简单介绍CRH和谐系列的概述并比较CRH1、CRH2、CRH3、CRH5的同异关键词:CRH,动车组,制动系统,计算公式目录第一章动车组制动系统 (1)1.1 动车组制动系统的组成 (1)1.2 动车组制动系统的分类 (1)第二章动车制动系统工作原理 (3)2.1 电制动系统 (3)2.2 空气制动系统 (3)2.3 防滑装置 (4)第三章动车组制动力的计算 (6)3.1 作用在动车组上的合力 (6)3.2 空气制动力的计算 (7)3.3 再生制动力的计算 (9)3.4 空气制动力与再生制动力的分配 (9)第四章CRH和谐系列动车组的比较 (14)4.1 CRH和谐系列动车组的概述 (14)4.2 CRH和谐系列动车组制动系统比较 (14)结论 (16)参考文献 (17)引言我国铁路第六次大提速上线运行的动车组名称为“和谐号”,原名CRH系列。
CRH2型动车组为动力分散型,列车由8节车编组,其中有4个车带动力。
每节带动力的车都有4个牵引电机,单机功率为300千瓦以上,整列车的牵引功率达到4800千瓦以上,动力配置均衡合理,完全满足高速运行要求。
制动系统设计计算学习
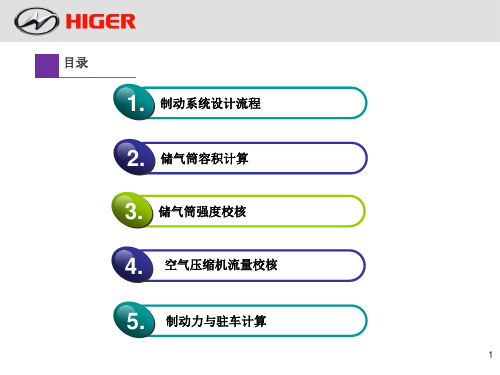
11
5.制动力与驻车计算 制动力
根据图3-2给出的汽车制动时的整车受力情况 ,并对后轴车轮的接地点取力矩,得平衡式 为: 对前轴车轮的接地点取力矩,得平衡式为:
12
5.制动力与驻车计算 制动力
公式推导得:
公式推导得: 式中:q—制动强度,亦称比减速度或比制动力 FB1, FB2—前后轴车轮的地面制动力。
许用应力:机械设计或工程结构设计中允许零件或构件承受的最大应力 值。塑性材料(大多数结构钢和铝合金)以屈服极限为基准,除以安全系数
后得许用应力,即[σ]=σs/n(n=1.5~2.5)
以Q235为例:许用应力为235/2=117.5mPa 储气筒壁厚2mm,计算应力为62.5mPa≤117.5mPa
如图6-32所示,在储气罐壁上取一单元体,其左、右侧面作用着拉应力σ
x,上、下侧面作用着环向拉应力σ y,单元体的外表面为自由表面,内面
为圆筒内壁,作用着内压Pc,根据材料力学的计算公式,可求出:
pc—储气罐内的气压
D —储气罐圆筒部分内径
t —储气罐的壁厚
7
3.储气筒强度校核
按第三强度理论的强度条件有:
4
2.储气筒容积计算
经验计算
Vc =(20 ∽ 40)∑Vs ∑Vg=(25% ∽ 50% )∑Vs
∑Vs —各制动气室压力腔最大容积(L) ∑Vg —全部制动管路的总容积之和(L) Vc —储气筒总容积(L)
5
2.储气筒容积计算
XC1计算实例
6
3.储气筒强度校核
储气罐为薄壁结构,应按薄壁圆筒对其壁厚进行强度计算:
13
5.制动力与驻车计算 制动力
地面制动力FB受着附着条件的限制,其值不可能大于附着力Fφ, 即FB ≤ Fφ=Zφ 或: FBmax =Fφ=Zφ 式中φ一一轮胎与地面间的附着系数; Z一一地面对车轮的法向反力。
某车型制动系统设计计算书
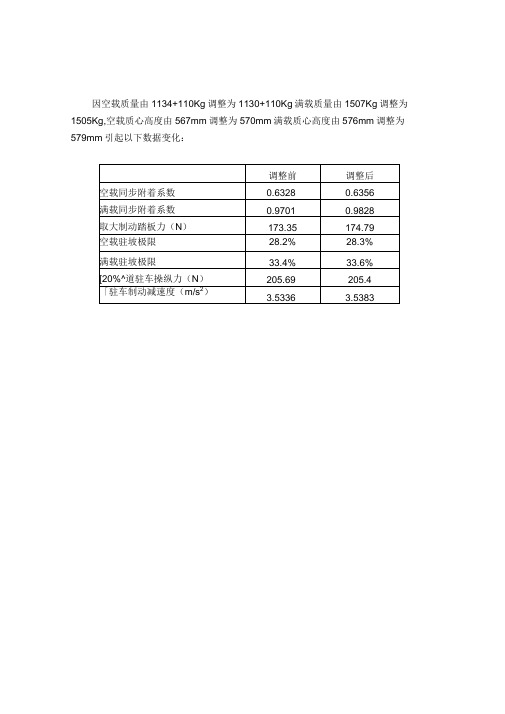
因空载质量由1134+110Kg调整为1130+110Kg满载质量由1507Kg调整为1505Kg,空载质心高度由567mm调整为570mm满载质心高度由576mm调整为579mm引起以下数据变化:目录1 概述 (1)2 引用标准 (1)3 计算过程 (1)3.1 整车参数 (1)3.2 理想的前、后制动器制动力分配曲线. (1)3.3 NA01制动系统性能校核 (3)3.3.1 NA01 制动系统基本参数 (3)3.3.2 制动力分配曲线绘制及同步附着系数确定 (4)3.3.3 前、后轴利用附着系数曲线绘制 (5)3.3.4 空、满载制动距离校核 (7)3.3.5 真空助力器失效时制动减速度校核 (7)3.3.6 ESP 系统失效制动减速度校核 (8)3.3.7 任一管路失效制动减速度校核 (8)3.3.8 制动踏板力校核 (8)3.3.9 制动主缸排量校核 (9)3.3.10 制动踏板行程校核 (9)3.3.11 驻车制动校核 (10)4 结论 (12)参考文献 (13)1概述根据NA01乘用车设计开发目标,设计和开发NA01制动系统,要求尽量沿用M2 零部件。
NA01制动系统共有三种配置:ESP前盘后盘式制动器,ABS前盘后鼓式制动器,比例阀+前盘后鼓式制动器,此三种配置需分别校核其法规要求符合性。
本计算书是根据整车室提供的NA01整车的设计参数(空载质量、满载质量、轴荷、轴距及质心高度),对经过局部改善(制动主缸直径由22.22mm更改为20.64mm)的制动系统(ESP+前盘后盘式制动器)的适宜性进行校核计算,以选择合适的参数作为NA01制动系统的设计值。
2引用标准GB 21670-2008乘用车制动系统技术要求及试验方法。
GB 7258-2004 机动车运行安全技术条件3 计算过程3.1整车参数表整车参数3.2理想的前、后制动器制动力分配曲线制动时前、后车轮同时抱死,对附着条件的利用、制动时汽车方向稳定性均较为有利,此时的前、后轮制动器制动力F!和F2的关系曲线,常称为理想的前、后轮制动器制动力分配曲线。
汽车制动系统计算

后
b.
F1
Gb L hg
jd1 max
F1 m
g b L hg
前
F 2
Ga L hg
j d 2 max
F 2 m
g a L hg
制
S
1 3.6
(t1
t2 ) v 2
v2 25.92 jmax
根
a
2
b
L
g g
0 .8
各个设计方案均能满足法规对行车制动性能的要求,同时也满足设计要求。 4 ) 助施力器失效时,制动力完全由人力操纵踏板产生,最大踏板力要求:N1类车700N。 加
△g2—鼓式制动器的蹄、鼓间隙
△g3—鼓式制动器摩擦衬片的厚度公差
(3)储油壶总容量Vmax
空载同步附着系数
0
车满载同步附着系数
' 0
型
标杆
方案
P201-NAM-SD-DP-G3-2
选配方案(四轮盘式)
Fif
Fir
图2 车型的I曲线与β线 ©版权归江淮汽车股份有限公司所有 未经授权禁止复制
第 4 页,共 13 页
制动系统方案设计计算说明书
P201-NAM-SD-DP-G3-2
通 过 1、在空载状态下,地面附着系数为0.8,标杆管路压力达到6MPa,管路压力达到5MPa,选 配方案管路压力达到5MPa,制动器发生抱死,此时后轴早于前轴抱死,这时整车稳定性非常差 。需要ABS进行调节。
n1、n2—前、后制动器单侧油缸数目(仅对盘式制动器而言)
Kv—考虑软管膨胀时的主缸容积系数,汽车设计推荐:轿车 =1.1,货车 =1.3
其中 要根据制动器的类型、参考同类车型确定,对鼓式制动器:汽车设计推荐δ=2-2.5mm;汽车工 程手册推荐3.5-5.5(考虑软管膨胀量及磨损间隙不能自调的影响),公司目前车型均可实现间隙
制动系统车重计算

制动系统车重计算
制动系统车重计算是车辆设计和工程中一个非常重要的环节。
车辆的总重量直接影响着制动系统的设计和性能,因此在进行制动系统车重计算时需要考虑多个因素。
车辆的基本重量是进行制动系统车重计算的关键因素之一。
车辆的基本重量包括车身重量、底盘重量、动力总成重量等。
这些重量需要准确测量和计算,以确保在设计制动系统时考虑到车辆整体的重量分布情况。
车辆的额定载重量也是进行制动系统车重计算时必须考虑的因素。
额定载重量是指车辆设计时所规定的最大载重量,超过这个载重量将会对制动系统造成严重影响。
因此,在进行车重计算时,需要考虑到车辆额定载重量,并确保制动系统能够应对额定载重量下的制动需求。
车辆的使用环境也会影响制动系统车重计算。
例如在不同的道路条件下,车辆的制动性能需求会有所不同。
在湿滑路面或者急转弯情况下,车辆对制动系统的要求会更高。
因此,在进行车重计算时,需要考虑到车辆的使用环境,以确保制动系统在各种情况下都能够正常工作。
车辆的行驶速度也会对制动系统车重计算产生影响。
高速行驶时,车辆的制动距离会更长,对制动系统的要求也会更高。
因此,在进
行车重计算时,需要考虑到车辆的最大行驶速度,以确保制动系统在高速行驶时也能够正常工作。
制动系统车重计算是车辆设计中一个至关重要的环节。
在进行车重计算时,需要考虑车辆的基本重量、额定载重量、使用环境和行驶速度等因素,以确保制动系统能够满足各种情况下的制动需求。
只有在对车辆的车重计算进行全面考虑和分析的基础上,才能设计出安全可靠的制动系统,保障车辆和乘客的安全。
牵引车车轮总成的制动系统设计与性能分析
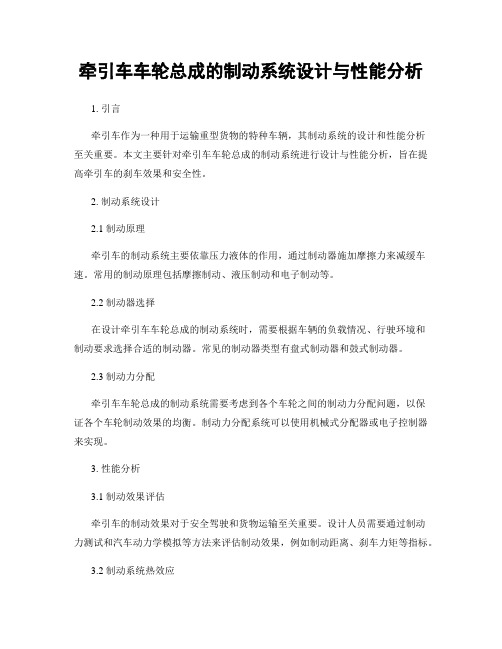
牵引车车轮总成的制动系统设计与性能分析1. 引言牵引车作为一种用于运输重型货物的特种车辆,其制动系统的设计和性能分析至关重要。
本文主要针对牵引车车轮总成的制动系统进行设计与性能分析,旨在提高牵引车的刹车效果和安全性。
2. 制动系统设计2.1 制动原理牵引车的制动系统主要依靠压力液体的作用,通过制动器施加摩擦力来减缓车速。
常用的制动原理包括摩擦制动、液压制动和电子制动等。
2.2 制动器选择在设计牵引车车轮总成的制动系统时,需要根据车辆的负载情况、行驶环境和制动要求选择合适的制动器。
常见的制动器类型有盘式制动器和鼓式制动器。
2.3 制动力分配牵引车车轮总成的制动系统需要考虑到各个车轮之间的制动力分配问题,以保证各个车轮制动效果的均衡。
制动力分配系统可以使用机械式分配器或电子控制器来实现。
3. 性能分析3.1 制动效果评估牵引车的制动效果对于安全驾驶和货物运输至关重要。
设计人员需要通过制动力测试和汽车动力学模拟等方法来评估制动效果,例如制动距离、刹车力矩等指标。
3.2 制动系统热效应在长时间连续制动过程中,制动系统会产生大量热量,对制动效果和制动器寿命造成影响。
设计人员需要分析制动系统的热效应,选择合适的散热措施和材料,以确保制动器的正常工作。
3.3 制动系统的抗干扰能力牵引车在复杂的道路环境和恶劣的天气条件下行驶,制动系统需要具备抗干扰能力,以保证制动效果的稳定性。
设计人员应对制动系统进行抗干扰性能测试和环境适应能力评估。
4. 改善设计与优化4.1 制动材料的选择制动系统的性能和耐用性与所选制动材料密切相关。
设计人员应选择高级制动材料,如碳陶瓷制动片或金属陶瓷制动片,以提高制动效果和延长制动器寿命。
4.2 制动力分配系统优化针对制动力分配不均衡的问题,设计人员可以通过调整制动力分配系统的参数或采用先进的电子控制技术来优化系统设计,以达到制动效果均衡的目标。
4.3 制动系统的智能化随着科技的进步,智能化制动系统正在逐渐应用于牵引车的设计。
制动系统设计计算报告
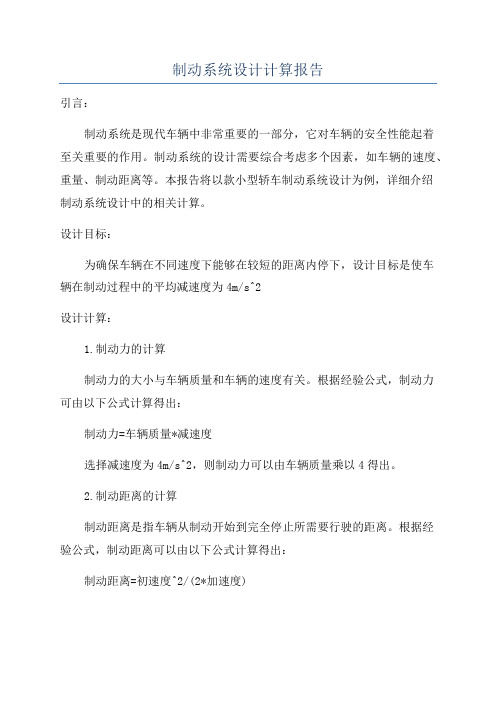
制动系统设计计算报告引言:制动系统是现代车辆中非常重要的一部分,它对车辆的安全性能起着至关重要的作用。
制动系统的设计需要综合考虑多个因素,如车辆的速度、重量、制动距离等。
本报告将以款小型轿车制动系统设计为例,详细介绍制动系统设计中的相关计算。
设计目标:为确保车辆在不同速度下能够在较短的距离内停下,设计目标是使车辆在制动过程中的平均减速度为4m/s^2设计计算:1.制动力的计算制动力的大小与车辆质量和车辆的速度有关。
根据经验公式,制动力可由以下公式计算得出:制动力=车辆质量*减速度选择减速度为4m/s^2,则制动力可以由车辆质量乘以4得出。
2.制动距离的计算制动距离是指车辆从制动开始到完全停止所需要行驶的距离。
根据经验公式,制动距离可以由以下公式计算得出:制动距离=初速度^2/(2*加速度)在制动过程中,加速度是负值(减速),所以加速度取为-4m/s^2、根据具体车辆的初始速度,可以计算出相应的制动距离。
3.制动盘和制动钳的尺寸计算制动盘和制动钳的尺寸需要考虑车辆的速度和质量。
根据经验公式,制动盘的直径与车速和减速度有关,可以通过以下公式计算得出:制动盘直径=停车速度*车辆质量*系数/制动力在本设计中,选择停车速度为60 km/h,车辆质量为1000 kg,系数为0.7、根据以上参数,可以计算出制动盘的直径。
根据制动盘的直径,可以确定制动钳的尺寸。
制动盘和制动钳的尺寸需要满足制动力的需求,并能够有效散热,以免在制动过程中过热导致制动力减弱。
4.制动液系统的计算制动液的压力和制动钳的工作效果有关。
根据经验公式,制动液的压力可以由以下公式计算得出:制动液压力=制动力/制动钳有效面积制动液压力需要根据制动钳的效率和制动力来选择合适的值。
根据经验,选择制动液压力为5MPa。
结论:根据以上计算结果,制动系统的设计可以满足要求。
制动力、制动距离、制动盘和制动钳的尺寸以及制动液压力的计算都能够保证车辆在制动过程中的安全性。
矿用制动车制动系统的设计及计算
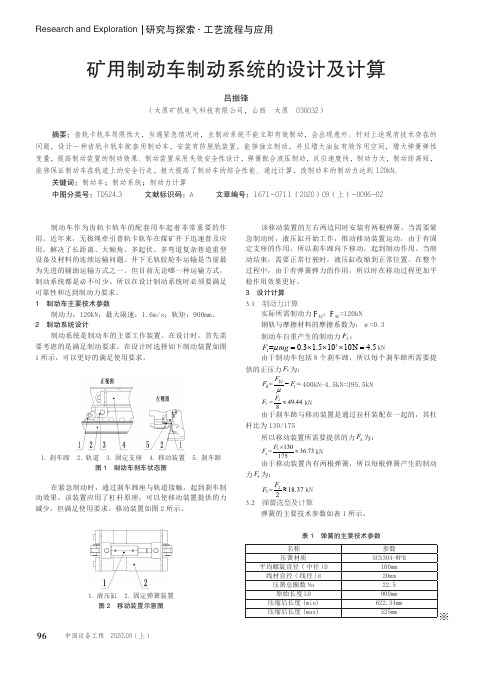
96研究与探索Research and Exploration ·工艺流程与应用中国设备工程 2020.09 (上)制动车作为齿轨卡轨车的配套用车起着非常重要的作用。
近年来,无极绳牵引普轨卡轨车在煤矿井下迅速普及应用,解决了长距离、大倾角、多起伏、多弯道复杂巷道重型设备及材料的连续运输问题。
井下无轨胶轮车运输是当前最为先进的辅助运输方式之一。
但目前无论哪一种运输方式,制动系统都是必不可少。
所以在设计制动系统时必须要满足可靠性和达到制动力要求。
1 制动车主要技术参数制动力:120kN;最大限速:1.6m/s;轨矩:900mm 。
2 制动系统设计制动系统是制动车的主要工作装置。
在设计时,首先需要考虑的是满足制动要求。
在设计时选择如下制动装置如图1所示,可以更好的满足使用要求。
1.刹车蹄2.轨道3.固定支座4.移动装置5.刹车蹄图1 制动车刹车状态图在紧急制动时,通过刹车蹄座与轨道接触,起到刹车制动效果。
该装置应用了杠杆原理,可以使移动装置提供的力减少,但满足使用要求。
移动装置如图2所示。
1.液压缸2.固定弹簧装置图2 移动装置示意图矿用制动车制动系统的设计及计算吕振锋(太原矿机电气科技有限公司,山西 太原 030032)摘要:齿轨卡轨车局限性大,当遇紧急情况时,主制动系统不能立即有效制动,会出现意外。
针对上述现有技术存在的问题,设计一种齿轨卡轨车配套用制动车,安装有防脱轨装置,能够独立制动,并且增大油缸有效作用空间,增大弹簧弹性变量,提高制动装置的制动效果。
制动装置采用失效安全性设计,弹簧配合液压制动,反应速度快,制动力大,制动距离短,能够保证制动车在轨道上的安全行走,极大提高了制动车的综合性能。
通过计算,改制动车的制动力达到120kN。
关键词:制动车;制动系统;制动力计算中图分类号:TD524.3 文献标识码:A 文章编号:1671-0711(2020)09(上)-0096-02该移动装置的左右两边同时安装有两根弹簧。
- 1、下载文档前请自行甄别文档内容的完整性,平台不提供额外的编辑、内容补充、找答案等附加服务。
- 2、"仅部分预览"的文档,不可在线预览部分如存在完整性等问题,可反馈申请退款(可完整预览的文档不适用该条件!)。
- 3、如文档侵犯您的权益,请联系客服反馈,我们会尽快为您处理(人工客服工作时间:9:00-18:30)。
制动系统计算分析
一制动技术条件:
1. 行车制动:
2. 应急制动:
3. 驻车制动:
在空载状态下,驻车制动装置应能保证机动车在坡度20%(对总质量为整备质量的1.2倍以下的机动车为15%),轮胎与地面的附着系数不小于0.7的坡道上正反两个方向上保持不动,其时间不应少
于5分钟。
二制动器选型
1.最大制动力矩的确定
根据同步附着系数和整车参数,确定前后轴所需制动力矩的范围,最大制动力是汽车附着质量被完全利用的条件下获得的,设良好路面附着系数φ=0.7。
满载情况下,确定前后轴制动器所需要的最大制动力矩。
为:前轴Mu1=G*φ(b+φ*h g)*r e /L (N.m)
后轴Mu2=G*φ(a-φ*h g)*r e /L (N.m)
或者Mu1=β/(1-β)* Mu2 【β=(φ*h g+b)/L】
其中r e -轮胎有效半径a-质心到前轴的距离
b-质心到后轴的距离h g -质心高度
L-轴距φ-良好路面附着系数
G-满载总重量(N;g=9.8m/s2)
同理:空载亦如此。
前轴;Mu11 后轴:Mu21
根据满载和空载的情况,确定最大制动力矩,此力满足最大值。
所以:前轮制动器制动力矩(单个)≥Mu1或Mu11/2
后轮制动器制动力矩(单个)≥Mu2或Mu21/2
2.行车制动性能计算(满载情况下)
已知参数:前桥最大制动力矩Tu1(N.m) 单个制动器
后桥最大制动力矩Tu2(N.m) 单个制动器
满载整车总质量M(kg)
①整车制动力
Mu1= Tu1*φ*2 (N.m)
Mu2= Tu2*φ*2 (N.m)
Fu= (Mu1+ Mu2)/r e (N)
②制动减速度
a b=Fu/M (m/s2)
③制动距离
S= U a0*(t21+ t211 /2)/3.6+ U a02 /25.92* a b
其中:U a0 (km/h)-制动初速度,t21+ t211 /2 为气压制动系制动系作用时间(一般在0.3-0.9s)
3.驻车制动性能计算
满载下坡停驻时后轴车轮的附着力矩:Mf
Mf=M*g*φ(a*cosα/L -h g*sinα/L)*r e (N.m)
其中附着系数φ=0.7 坡度20%(α=11.31o)
在20%坡上的下滑力矩:M滑
M滑=M*g*sinα*r e (N.m)驻车度α=11.31o
则Mf>M滑时,满足驻车要求。
三储气筒容量校核
设储气筒容积为V储,全部制动管路总容积为∑V管,各制动气室压力腔最大容积之和为∑V s , 其中∑V管约为∑Vs的25%-50%,V储
/∑V s=20-40(推荐值)。
①未制动时
因为∑V s=0,管路中的压力与大气压力P o相等。
所以制动管路、储气筒和制动气室系统中的空气绝对压力与容积的乘积和为:
∑PV=(P储+P o)*V储+ P o*∑V管
②完全制动时
当制动管路和气室中的相对压力达到制动阀所控制的最大压力P max后,将储气筒、制动管路、制动气室隔绝,此时制动气室的容积被充分利用,同时制动后储气筒中相对压力降至P1储。
则制动系统中的空气绝对压力与容积的乘积总和为:
(∑PV)1 =(P1储+P o)*V储+ (P o+P max)*(∑V管+∑V s)设系统的空气膨胀过程为等温过程。
则∑PV=(∑PV)1
即:(P储+P o)*V储+ P o*∑V管=(P1储+P o)*V储+(P o+P max)*(∑V管+∑V s)
因此,在空压机不工作时进行一次完全制动后储气筒压力降(一般不超过0.03Mpa).
△P储= P储- P1储=[(∑V管+∑V s)(P max+P o)- P o*∑V管]/ V储储气筒中的压力有最大压力降至最小安全压力(一般取0.5Mpa)前的连续制动次数(一般取8-12次)
n=lg(P储max/ P储min)/lg[(+(∑V管+∑V s)/ V储]
其中P储max为储气筒内空气的最高绝对压力
P储min为储气筒内空气的最低绝对压力
四空压机的选择
空压机的出气率应根据汽车各个气动装置的耗气率来确定。
每次制动所消耗的压缩空气的容积为:
V=∑V管+∑V s
每次制动所消耗的压缩空气的质量(耗气率)为:
W=P*V/9.8*R*T
其中:P-制动管路压力(Pa)R-空气的气体常数取29.27
T-热力学温度(K)
每单位时间内制动消耗的压缩空气的质量为:
W=W*m
其中:m-单位时间内制动次数,市内取0.8-1.4次/min,郊外取0.2-0.5次/min。
所以:客车制动总耗气率(W O)=W+∑W f+W e
其中:∑W f-车上各种气动附属装置的耗气率总和(kg/min)W e-单位时间内容许漏气量,一般取3x10-6 kg/min
考虑压缩空气其他一切损失,所以空压机出气率应为W空=(5-6)W O
取空气密度为1.3kg/m3
则按容积计算的空气压缩机出气率应为V空=W空/1.3。