三种常规无损检测方法的比较
常见的无损探伤方法

常见的⽆损探伤⽅法⽆损检测⽅法很多据美国国家宇航局调研分析,认为可分为六⼤类约70余种。
但在实际应⽤中⽐较常见的有以下⼏种:常规⽆损检测⽅法有:●超声检测 Ultrasonic Testing(缩写 UT);●射线检测 Radiographic Testing(缩写 RT);●磁粉检测 Magnetic particle Testing(缩写 MT);●渗透检验 Penetrant Testing (缩写 PT);●涡流检测Eddy current Testing(缩写 ET);⾮常规⽆损检测技术有:●声发射Acoustic Emission(缩写 AE);●泄漏检测Leak Testing(缩写 UT);●光全息照相Optical Holography;●红外热成象Infrared Thermography;●微波检测 Microwave TestingX光射线探伤、超声波探伤对内部探伤适⽤,不适⽤表⾯探伤.磁粉探伤主要探表层深度3mm内缺陷.渗透探伤.着⾊探伤主要探⼯件表⾯缺陷(对不锈钢探伤⽐较适⽤).常见的⽆损探伤⽅法常见的⽆损探伤⽅法VT-Visual Testing⽬测RT-Radiographic Testing射线检测UT-Ultrasonic Testing超声检测PT-(Dye) Penetrant Testing渗透检测MT-Magnetic particle Testing磁粉检测ST-Spectrum Testing光谱测试ET-Eddy Current Testing涡流检测HT-Hardness Testing硬度检测-Hydrostatic Testing ⽔压试验MPT-Mechanical performance test机械性能WT-Wall thickness Testing测厚DT-Diameter Testing管径测试MST-Metallographic inspection⾦相检验ORT-Out of roundness testing不圆度检查MMT-磁记忆OT-综合检查FT- Field test 现场检验FN- Field note现场记录⼀、RT-Radiographic Testing射线检测射线照相法(RT)是指⽤X射线或g射线穿透试件,以胶⽚作为记录信息的器材的⽆损检测⽅法,该⽅法是最基本的,应⽤最⼴泛的⼀种⾮破坏性检验⽅法。
五大常规无损检测

五大常规无损检测PT=渗透探伤MT=磁粉探伤UT=超声波探伤RT=射线探伤ET=涡流探伤五大常规无损检测:渗透探伤、磁粉探伤、超声波探伤、射线探伤、涡流探伤,1.射线探伤也就是X光拍片简称RT,2.超声波检查简称UT,射线探伤和超声波探伤一般适用于主甲板,外板,横舱壁,内底板,上下边柜斜板等对接的焊缝。
施工者对要求射线探伤的焊缝及热影响区域进行打磨处理,消除焊缝表面的凹凸不平对底片影像显示的影响,确保无油污、无油漆、无飞溅。
射线探伤有一定的杀伤性,船方及各施工部门在X光射线探伤时段、不得靠近X光射线探伤位置半径三十米范围的警示区域,防止射线伤害人员。
3.磁粉探伤又称MT或者MPT(Magnetic Particle Testing),一般适用于对接焊缝,角焊缝,尾轴及锻钢件,铸钢等磁性材料的表面附近进行探伤的检测方法。
利用铁受磁石吸引的原理进行检查。
在进行磁粉探伤检测时,使被测物收到磁力的作用,将磁粉(磁性微型粉末)散布在其表面。
然后,缺陷的部分表面所泄漏出来泄露磁力会将磁粉吸住,形成图案。
指示图案比实际缺陷要大数十倍,因此很容易便能找出缺陷。
磁粉探伤检测一般按照前处理→磁化→喷淋磁粉→观察→后处理的步骤进行4.渗透探伤简称PT,着色一般适用于船体对接焊缝,角焊缝等,螺旋桨叶根部,锻钢件、铸钢件表面。
当机械零部件需磁粉探伤或着色探伤时,则要将被探物件表面的油污清洁干净并摆放整齐,如果焊缝做磁粉探伤或着色探伤时,则需将焊道清洁干净,要求无油污、无油漆、无飞溅。
5.涡流检测(ET)的英文名称是:Eddy Current Testing工业上无损检测的方法之一。
给一个线圈通入交流电,在一定条件下通过的电流是不变的。
如果把线圈靠近被测工件,像船在水中那样,工件内会感应出涡流,受涡流影响,线圈电流会发生变化。
由于涡流的大小随工件内有没有缺陷而不同,所以线圈电流变化的大小能反映有无缺陷。
适用于导电材料..由于导体自身各种因素(如电导率,磁导率,形状,尺寸和缺陷等)的变化,会导致感应电流的变化,利用这种现象而判知导体性质,状态的检测方法叫做涡流检测方法.属于表面探伤法,适用于钢铁、有色金属、石墨等导电体工件,因为并不需要接触工件,所以检测速度很快,但设备昂贵。
无损检测技术的发展及其运用
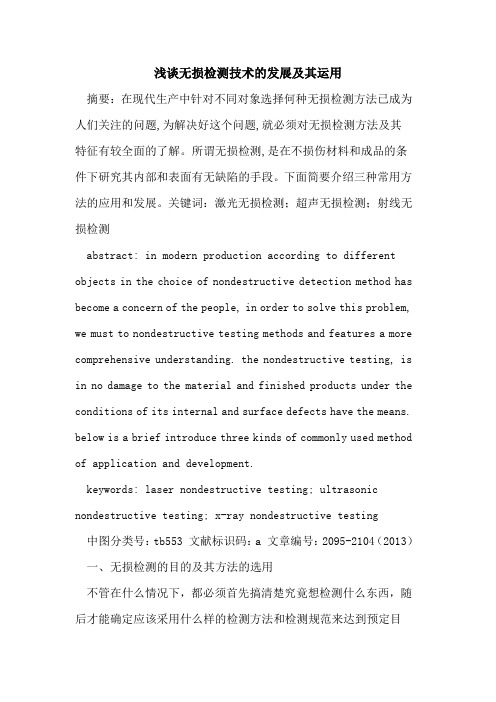
浅谈无损检测技术的发展及其运用摘要:在现代生产中针对不同对象选择何种无损检测方法已成为人们关注的问题,为解决好这个问题,就必须对无损检测方法及其特征有较全面的了解。
所谓无损检测,是在不损伤材料和成品的条件下研究其内部和表面有无缺陷的手段。
下面简要介绍三种常用方法的应用和发展。
关键词:激光无损检测;超声无损检测;射线无损检测abstract: in modern production according to different objects in the choice of nondestructive detection method has become a concern of the people, in order to solve this problem, we must to nondestructive testing methods and features a more comprehensive understanding. the nondestructive testing, is in no damage to the material and finished products under the conditions of its internal and surface defects have the means. below is a brief introduce three kinds of commonly used method of application and development.keywords: laser nondestructive testing; ultrasonic nondestructive testing; x-ray nondestructive testing中图分类号:tb553 文献标识码:a 文章编号:2095-2104(2013)一、无损检测的目的及其方法的选用不管在什么情况下,都必须首先搞清楚究竟想检测什么东西,随后才能确定应该采用什么样的检测方法和检测规范来达到预定目的。
无损检测论文
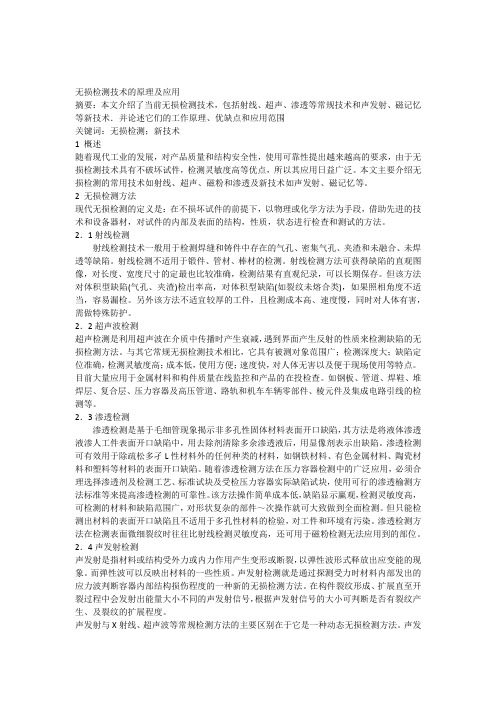
无损检测技术的原理及应用摘要:本文介绍了当前无损检测技术,包括射线、超声、渗透等常规技术和声发射、磁记忆等新技术.并论述它们的工作原理、优缺点和应用范围关键词:无损检测;新技术1 概述随着现代工业的发展,对产品质量和结构安全性,使用可靠性提出越来越高的要求,由于无损检测技术具有不破坏试件,检测灵敏度高等优点,所以其应用日益广泛。
本文主要介绍无损检测的常用技术如射线、超声、磁粉和渗透及新技术如声发射、磁记忆等。
2 无损检测方法现代无损检测的定义是:在不损坏试件的前提下,以物理或化学方法为手段,借助先进的技术和设备器材,对试件的内部及表面的结构,性质,状态进行检查和测试的方法。
2.1射线检测射线检测技术一般用于检测焊缝和铸件中存在的气孔、密集气孔、夹渣和未融合、未焊透等缺陷。
射线检测不适用于锻件、管材、棒材的检测。
射线检测方法可获得缺陷的直观图像,对长度、宽度尺寸的定最也比较准确,检测结果有直观纪录,可以长期保存。
但该方法对体积型缺陷(气孔、夹渣)检出率高,对体积型缺陷(如裂纹未熔合类),如果照相角度不适当,容易漏检。
另外该方法不适宜较厚的工件,且检测成本高、速度慢,同时对人体有害,需做特殊防护。
2.2超声波检测超声检测是利用超声波在介质中传播时产生衰减,遇到界面产生反射的性质来检测缺陷的无损检测方法。
与其它常规无损检测技术相比,它具有被测对象范围广;检测深度大;缺陷定位准确,检测灵敏度高;成本低,使用方便;速度快,对人体无害以及便于现场使用等特点。
目前大量应用于金属材料和构件质量在线监控和产品的在投检查。
如钢板、管道、焊鞋、堆焊层、复合层、压力容器及高压管道、路轨和机车车辆零部件、棱元件及集成电路引线的检测等。
2.3渗透检测渗透检测是基于毛细管现象揭示非多孔性固体材料表面开口缺陷,其方法是将液体渗透液渗人工件表面开口缺陷中,用去除剂清除多余渗透液后,用显像剂表示出缺陷。
渗透检测可有效用于除疏松多孑L性材料外的任何种类的材料,如钢铁材料、有色金属材料、陶瓷材料和塑料等材料的表面开口缺陷。
无损检测方法课件
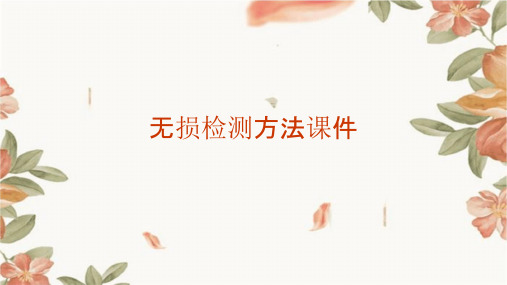
磁粉检测设备包括电磁或永磁体、电源、控制器、磁粉和辅助设备等。电磁体或永磁体用于产生磁场,电源和控 制器用于提供能量和控制磁场的大小和方向。磁粉用于显示缺陷,辅助设备包括放大镜、紫外线灯等用于观察和 记录结果。
磁粉检测应用与案例
磁粉检测应用
磁粉检测广泛应用于机械制造、航空航天、石油化工等领域。对于铁磁性材料,如铸件、锻件、焊缝 等,磁粉检测是一种常用的无损检测方法。在实际应用中,需要根据待检测工件的材质、形状和尺寸 等因素选择合适的磁粉检测工艺和设备。
详细描述
常规超声波检测使用高频声波信号,通过探头发射超声波并接收回波信号,分析回波信号的特征来判断被检测 材料或构件内部是否存在缺陷或异常情况。该方法适用于各种不同类型的材料和构件,如金属、非金属、复合 材料等。常规超声波检测具有较高的检测精度和灵敏度,同时对被检测材料或构件无损伤,是一种广泛使用的 无损检测方法。
VS
涡流检测设备
涡流检测设备包括探头、电源、控制器和 数据处理系统等。其中,探头是核心部件, 由线圈和磁芯组成,用于产生交变磁场。 电源和控制器的功能是提供能量和控制信 号。数据处理系统则是对检测数据进行采 集、分析和处理,最终得出检测结果。
涡流检测应用与案例
涡流检测应用
涡流检测被广泛应用于各种金属材料的无损 检测,如钢管、钢板、线材等。此外,涡流 检测还可以用于电力设备的无损检测,如变 压器、电机等。在航空航天领域,涡流检测 也被广泛应用于各种金属材料和复合材料的 无损检测。
要点二
详细描述
衍射时差法超声波检测使用高频声波信号,通过探头发射 超声波并接收回波信号,分析回波信号的特征来判断被检 测构件内部是否存在缺陷或异常情况。该方法适用于大型 构件和厚壁构件,如桥梁、压力容器等。衍射时差法超声 波检测具有较高的检测效率和灵敏度,同时对被检测构件 无损伤,是一种高效率的无损检测方法。
对常规无损检测方法选择的分析
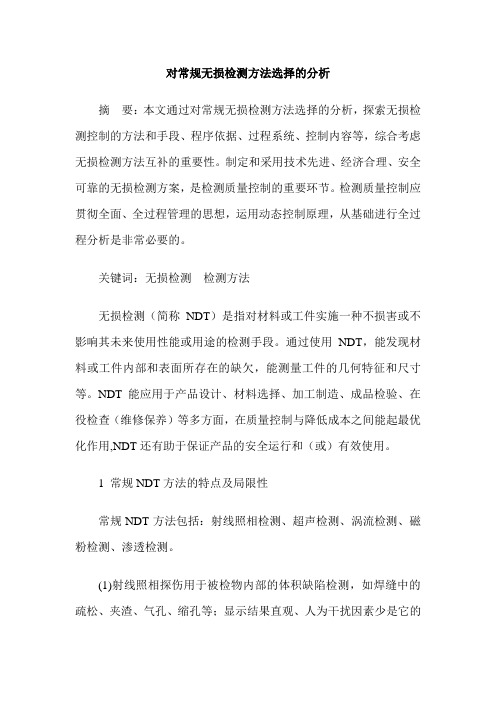
对常规无损检测方法选择的分析摘要:本文通过对常规无损检测方法选择的分析,探索无损检测控制的方法和手段、程序依据、过程系统、控制内容等,综合考虑无损检测方法互补的重要性。
制定和采用技术先进、经济合理、安全可靠的无损检测方案,是检测质量控制的重要环节。
检测质量控制应贯彻全面、全过程管理的思想,运用动态控制原理,从基础进行全过程分析是非常必要的。
关键词:无损检测检测方法无损检测(简称NDT)是指对材料或工件实施一种不损害或不影响其未来使用性能或用途的检测手段。
通过使用NDT,能发现材料或工件内部和表面所存在的缺欠,能测量工件的几何特征和尺寸等。
NDT能应用于产品设计、材料选择、加工制造、成品检验、在役检查(维修保养)等多方面,在质量控制与降低成本之间能起最优化作用,NDT还有助于保证产品的安全运行和(或)有效使用。
1 常规NDT方法的特点及局限性常规NDT方法包括:射线照相检测、超声检测、涡流检测、磁粉检测、渗透检测。
(1)射线照相探伤用于被检物内部的体积缺陷检测,如焊缝中的疏松、夹渣、气孔、缩孔等;显示结果直观、人为干扰因素少是它的主要优点,探伤对象基本不受零件材料、形状、外廓尺寸的限制;主要局限是:三维结构二维成像,前后缺陷重叠;射线束夹角与被检裂纹取向不宜超过10°。
(2)超声探伤适用于被检物内部的面积型缺陷,如锻件中的裂纹、白点、分层和焊缝中的未融合等。
主要优点是能定位缺陷的相对尺寸和坐标位置;适用焊缝、管材、板材等多种材料与制件的检测;检测大厚度件的能力超出其它方法;并且可携设备现场操作。
但用纵波脉冲反射法对近表面与表面缺陷检测存在盲区;检测复杂形状的试件可实施性影响较大;操作者需具备有较丰富的实践经验。
(3)磁粉探伤可发现的主要缺陷有:各种裂纹、夹杂、夹渣、折叠、白点、分层、气孔、未焊透、疏松、冷隔等。
主要能确定缺陷在被检物表面的形状、大小和位置,磁粉探伤机性能安全可靠,易于操作、对小开口至微米级的裂纹检测灵敏度高。
五大常规无损检测原理
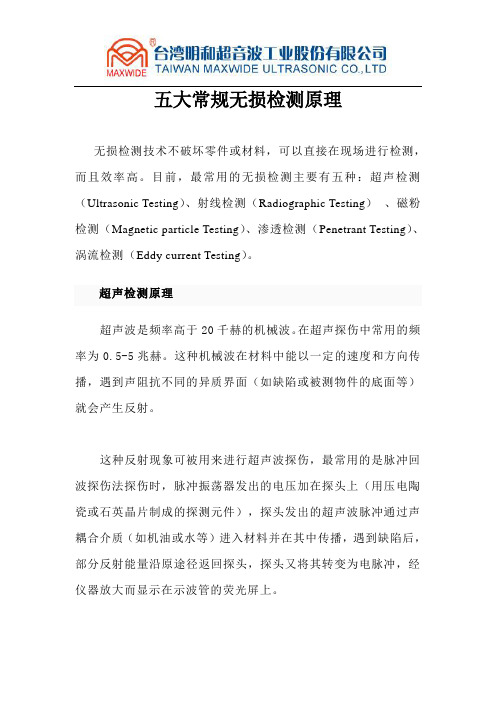
五大常规无损检测原理无损检测技术不破坏零件或材料,可以直接在现场进行检测,而且效率高。
目前,最常用的无损检测主要有五种:超声检测(Ultrasonic Testing)、射线检测(Radiographic Testing)、磁粉检测(Magnetic particle Testing)、渗透检测(Penetrant Testing)、涡流检测(Eddy current Testing)。
超声检测原理超声波是频率高于20千赫的机械波。
在超声探伤中常用的频率为0.5-5兆赫。
这种机械波在材料中能以一定的速度和方向传播,遇到声阻抗不同的异质界面(如缺陷或被测物件的底面等)就会产生反射。
这种反射现象可被用来进行超声波探伤,最常用的是脉冲回波探伤法探伤时,脉冲振荡器发出的电压加在探头上(用压电陶瓷或石英晶片制成的探测元件),探头发出的超声波脉冲通过声耦合介质(如机油或水等)进入材料并在其中传播,遇到缺陷后,部分反射能量沿原途径返回探头,探头又将其转变为电脉冲,经仪器放大而显示在示波管的荧光屏上。
根据缺陷反射波在荧光屏上的位置和幅度(与参考试块中人工缺陷的反射波幅度作比较),即可测定缺陷的位置和大致尺寸。
除回波法外,还有用另一探头在工件另一侧接受信号的穿透法。
利用超声法检测材料的物理特性时,还经常利用超声波在工件中的声速、衰减和共振等特性。
射线检测原理射线的种类很多,其中易于穿透物质的有X射线、γ射线、中子射线三种。
这三种射线都被用于无损检测,其中X射线和γ射线广泛用于锅炉压力容器焊缝和其他工业产品、结构材料的缺陷检测,而中子射线仅用于一些特殊场合。
射线检测最主要的应用是探测试件内部的宏观几何缺陷(探伤)。
按照不同特征,例如使用的射线种类、记录的器材、工艺和技术特点等,可将射线检测分为许多种不同的方法。
射线照相法是指用X射线或γ射线穿透试件,以胶片作为记录信息的器材的无损的检测方法。
该方法是最基本的,应用最广泛的一种射线检测方法。
四种常用探伤方法特点及区别

四种惯例无损检测方法的比较无损检测就是利用声、光、磁和电等特征,在不伤害或不影响被检对象使用性能的前提下,检测被检对象中能否存在缺点或不平均性,给出缺点的大小、地点、性质和数目等信息,从而判断被检对象所处技术状态 (如合格与否、节余寿命等 )的全部技术手段的总称。
常用的无损检测方法:超声检测 (UT)、磁粉检测 (MT)、液体浸透检测 (PT)及 X 射线检测 (RT)。
超声波检测 (UT)1、超声波检测的定义:经过超声波与试件互相作用,就反射、透射和散射的波进行研究,对试件进行宏观缺点检测、几何特征丈量、组织构造和力学性能变化的检测和表征,并从而对其特定应用性进行评论的技术。
2、超声波工作的原理:主假如鉴于超声波在试件中的流传特征。
声源产生超声波,采纳必定的方式使超声波进入试件;超声波在试件中流传并与试件资料以及此中的缺点互相作用,使其流传方向或特色被改变;改变后的超声波经过检测设施被接收,并可对其进行办理和剖析;依据接收的超声波的特色,评估试件自己及其内部能否存在缺点及缺点的特征。
3、超声波检测的长处:a.合用于全部金属、非金属和复合资料等多种制件的无损检测;b.穿透能力强,可对较大厚度范围内的试件内部缺点进行检测。
如对金属材料,可检测厚度为 1~2mm 的薄壁管材和板材,也可检测几米长的钢锻件;c.缺点定位较正确;d.对面积型缺点的检出率较高;e.敏捷度高,可检测试件内部尺寸很小的缺点;f.检测成本低、速度快,设施轻巧,对人体及环境无害,使用较方便。
4、超声波检测的限制性a.对试件中的缺点进行精准的定性、定量仍须作深入研究;b.对拥有复杂形状或不规则外形的试件进行超声检测有困难;c.缺点的地点、取向和形状对检测结果有必定影响;d.材质、晶粒度等对检测有较大影响;e.以常用的手工 A 型脉冲反射法检测时结果显示不直观,且检测结果无直接目睹记录。
5、超声检测的合用范围a.从检测对象的资料来说,可用于金属、非金属和复合资料;b.从检测对象的制造工艺来说,可用于锻件、铸件、焊接件、胶结件等;c.从检测对象的形状来说,可用于板材、棒材、管材等;d.从检测对象的尺寸来说,厚度可小至1mm,也可大至几米;e.从缺点部位来说,既能够是表面缺点,也能够是内部缺点。
- 1、下载文档前请自行甄别文档内容的完整性,平台不提供额外的编辑、内容补充、找答案等附加服务。
- 2、"仅部分预览"的文档,不可在线预览部分如存在完整性等问题,可反馈申请退款(可完整预览的文档不适用该条件!)。
- 3、如文档侵犯您的权益,请联系客服反馈,我们会尽快为您处理(人工客服工作时间:9:00-18:30)。
三种常规无损检测方法的比较
无损检测就是利用声、光、磁和电等特性,在不损害或不影响被检对象使用性 能的前提
下,检测被检对象中是否存在缺陷或不均匀性,给出缺陷的大小、位置、 性质和数量等信息,
进而判定被检对象所处技术状态 ( 如合格与否、剩余寿命等 ) 的 所有技术手段的总称。
常用的无损检测方法:超声检测 (UT)、磁粉检测(MT)和液体渗透检测(PT)。 超
声波检测
(UT)
1
、 超声波检测的定义:
通过超声波与试件相互作用,就反射、透射和散射的波进行研究,对试件进行 宏观缺陷检
测、几何特性测量、组织结构和力学性能变化的检测和表征,并进而对 其特定应用性进行评价
的技术。
2
、 超声波工作的原理:
主要是基于超声波在试件中的传播特性。声源产生超声波,采用一定的方式使 超声波进入
试件;超声波在试件中传播并与试件材料以及其中的缺陷相互作用,使 其传播方向或特征被改
变;改变后的超声波通过检测设备被接收,并可对其进行处 理和分析;根据接收的超声波的特
征,评估试件本身及其内部是否存在缺陷及缺陷 的特性。
3
、 超声波检测的优点:
a.
适用于金属、非金属和复合材料等多种制件的无损检测;
b.
穿透能力强, 可对较大厚度范围内的试件内部缺陷进行检测。 如对金属材料, 可检测
厚度为1〜2mm勺薄壁管材和板材,也可检测几米长的钢锻件;
c.
缺陷定位较准确;
d.
对面积型缺陷的检出率较高;
e.
灵敏度高,可检测试件内部尺寸很小的缺陷;
f.
检测成本低、速度快,设备轻便,对人体及环境无害,使用较方便。
4
、超声波检测的局限性
a.
对试件中的缺陷进行精确的定性、定量仍须作深入研究;
b.
对具有复杂形状或不规则外形的试件进行超声检测有困难;
c.
缺陷的位置、取向和形状对检测结果有一定影响;
d.
材质、晶粒度等对检测有较大影响;
e. 以常用的手工 A
型脉冲反射法检测时结果显示不直观,且检测结果无直接见 证记录。
5
、超声检测的适用范围
a.
从检测对象的材料来说,可用于金属、非金属和复合材料;
b.
从检测对象的制造工艺来说,可用于锻件、铸件、焊接件、胶结件等;
c.
从检测对象的形状来说,可用于板材、棒材、管材等;
d. 从检测对象的尺寸来说,厚度可小至 1mm
也可大至几米;
e.
从缺陷部位来说,既可以是表面缺陷,也可以是内部缺陷。锻件是金属被施
加压力,通过塑性变形塑造要求的形状或合适的压缩力的物件。这种力量典型的通 过使用铁锤
或压力来实现。铸件过程建造了精致的颗粒结构,并改进了金属的物理 属性。在零部件的现实
使用中,一个正确的设计能使颗粒流在主压力的方向。 磁粉检测
(MT)
1.
磁粉检测的原理:
铁磁性材料和工件被磁化后,由于不连续性的存在,使工件表面和近表面的磁
力线发生局部畸变而产生漏磁场,吸附施加在工件表面的磁粉,形成在合适光照下 目视可见的
磁痕,从而显示出不连续性的位置、形状和大小
2.
磁粉检测的适用性和局限性:
a. 磁粉探伤适用于检测铁磁性材料表面和近表面尺寸很小、间隙极窄 (
如可检
测出长0.1mm宽为微米级的裂纹),目视难以看出的不连续性。
b.
磁粉检测可对原材料、 半成品、成品工件和在役的零部件检测, 还可对板材、 型材、
管材、棒材、焊接件、铸钢件及锻钢件进行检测。
c.
可发现裂纹、夹杂、发纹、白点、折叠、冷隔和疏松等缺陷。
d.
磁粉检测不能检测奥氏体不锈钢材料和用奥氏体不锈钢焊条焊接的焊缝,也 不能检测
铜、铝、镁、钛等非磁性材料。对于表面浅的划伤、埋藏较深的孔洞和与 工件表面夹角小于
20
°的分层和折叠难以发现。
渗透检测
(PT)
1.
液体渗透检测的基本原理:
零件表面被施涂含有荧光染料或着色染料的渗透剂后,在毛细管作用下,经过 一段时间,
渗透液可以渗透进表面开口缺陷中;经去除零件表面多余的渗透液后, 再在零件表面施涂显像
剂,同样,在毛细管的作用下,显像剂将吸引缺陷中保留的 渗透液,渗透液回渗到显像剂中,
在一定的光源下 (紫外线光或白光 ) ,缺陷处的渗 透液痕迹被现实, (黄绿色荧光或鲜艳
红色 ) ,从而探测出缺陷的形貌及分布状态。
2.
渗透检测的优点:
a.
可检测各种材料;金属、非金属材料;磁性、非磁性材料;焊接、锻造、轧 制等加工方
式;
b. 具有较高的灵敏度(可发现0.1卩m宽缺陷)
c.
显示直观、操作方便、检测费用低。
3.
渗透检测的缺点及局限性:
a.
它只能检出表面开口的缺陷;
b.
不适于检查多孔性疏松材料制成的工件和表面粗糙的工件;
c.
渗透检测只能检出缺陷的表面分布,难以确定缺陷的实际深度,因而很难对 缺陷做出定
量评价。检出结果受操作者的影响也较大。
由于各种检测方法都具有一定的特点,为提高检测结果可靠性,应根据设备材 质、制造方
法、工作介质、使用条件和失效模式,预计可能产生的缺陷种类、形状、 部位和取向,选择最
适当无损检测方法。
任何一种无损检测方法都不是万能的,每种方法都有自己的优点和缺点。应尽
可能多用几种检测方法,互相取长补短,以保障承压设备安全运行。