关于水冷电机散热结构的优化设计分析
研究风力发电变流器水冷系统的优化设计

研究风力发电变流器水冷系统的优化设计摘要:为解决风电变流器水冷系统由于突然失电而导致变流器不能正常运行的问题,本文在介绍水冷系统基本特征的基础上,提出具体的系统优化设计方案,并经分析与实践验证了该优化设计系统的合理性、可行性与有效性,以期为相关人员提供参考,保证风电变流器水冷系统运行可靠性。
关键词:风力发电;变流器;水冷系统;系统优化设计在风电变流器运行过程中,需采用水冷系统进行冷却,但水冷系统会由于不同方面因素的影响而产生一些问题,这就需要在实际工作中在明确系统基本特征的基础上,制定合理可行的优化设计方案,并对该方案予以严格执行,从而保证方案的实施效果,使系统始终处在良好运行状态。
1水冷系统概述首先需要简述风力发电系统中变流器的重要作用,以及变流器正常工作中发热量大的问题,正常要配置冷却系统,以及冷却系统如果无法正常运行及时冷却变流器,将使得变流器超温等各种情况。
水冷系统主要包含以下几个组成部分:主泵、空冷器、电加热器、电动三通阀、膨胀罐与脱气罐,该系统基本工作原理:变流器的水冷系统中低温冷却水吸收变流器工作产生的热量后,冷却水温度升高,后由主循环泵驱动高温冷却水通过系统管道进入空气冷却器进行冷却换热,完成降温后冷却水再次参与到变流器的冷却过程中,以此往复循环,实现循环冷却目标[1]。
在冷却介质循环过程中,以主泵为动力源,同时也是系统运行的重要基础。
空冷器采用大功率风扇冷却从空冷器翅片上流过的冷却介质,以此降低介质温度。
为避免冬季温度过低等外界因素对变流器运行造成影响,系统应配备电加热器,以此对冷却介质温度进行有效控制,此外还配备电动三通阀,对进入到变流器当中的冷却介质流量予以有效调节。
为了使冷却回路的压力和流量保持稳定,主泵冷却水的进口部位应配置囊式膨胀罐与脱气罐。
在膨胀罐当中预充适当压力,可通过改变囊的形状缓冲介质体积发生的变化。
脱气罐和膨胀罐之间采用软管相连,使冷却回路当中存在的冷却介质能够快速脱气,最终使系统运行始终保持在稳定状态。
液冷技术优化设计

液冷技术优化设计1. 引言液冷技术是一种高效、可靠的散热方式,广泛应用于高性能计算机、数据中心、通信设备等领域。
随着科技的不断发展,设备功耗的不断提高,对液冷技术的性能要求也日益严格。
本文档旨在探讨液冷技术的优化设计,以提高其散热效率、降低能耗、延长设备寿命。
2. 液冷技术原理液冷技术利用液体作为冷却介质,通过循环流动将热量带走,实现设备的散热。
液冷系统主要包括冷却液、冷却器、泵、管道、传感器等组件。
冷却液在循环过程中吸收设备产生的热量,然后流经冷却器进行热量交换,将热量传递给环境。
泵负责驱动冷却液循环,管道负责输送冷却液,传感器负责监测液冷系统的运行状态。
3. 优化设计目标液冷技术的优化设计应围绕以下目标展开:1. 提高散热效率:降低冷却液的温升,提高热交换效率。
2. 降低能耗:减小泵的功率消耗,提高系统整体能效。
3. 提高系统稳定性:降低系统故障率,延长设备寿命。
4. 降低维护成本:简化系统结构,减少维修保养工作。
4. 优化设计方案针对液冷技术的优化设计,可以从以下几个方面入手:4.1 冷却液选择选用高热导率、低比热容的冷却液,可以提高热交换效率,降低温升。
同时,考虑冷却液的腐蚀性、生物降解性等因素,以保证系统安全稳定运行。
4.2 冷却器设计优化冷却器结构,提高其热交换面积,降低风阻,从而提高散热效率。
可以采用多翅片、微通道等技术,提高冷却器的散热性能。
4.3 泵选型及管道设计选用高效、低功耗的泵,以减小泵的功率消耗。
同时,合理设计管道布局,降低管道阻力,减少泵的负载。
4.4 系统控制策略采用先进的控制策略,实现液冷系统各组件的协同工作,提高系统整体性能。
可以采用PID控制、模糊控制等算法,实现泵、冷却器等组件的优化控制。
4.5 系统监测与维护增加液冷系统的监测点,实时掌握系统运行状态,及时发现并处理故障。
同时,简化系统结构,降低维护成本。
5. 总结液冷技术的优化设计是提高其散热性能、降低能耗、延长设备寿命的关键。
冷却水循环系统的优化设计

冷却水循环系统的优化设计冷却水循环系统是工业生产中不可或缺的重要组成部分。
在工业生产中,许多设备需要冷却水循环系统进行冷却,保证设备正常运行。
因此,设计一套稳定、高效的冷却水循环系统是非常重要的。
现代冷却水循环系统通常由水泵、冷却塔、换热器、管道等组成。
为了达到优化设计的目的,需要从以下几个方面考虑:首先,需要考虑冷却塔的选型。
冷却塔的选型是冷却水循环系统设计的关键之一。
一般情况下,可以选择多项指标进行综合评估来选择最适合的冷却塔。
其中,冷却塔的散热面积、通风方式、传热能力等都是需要考虑的因素。
另外,根据工业生产的实际需要,还需要考虑冷却塔的防腐、耐腐蚀等性能。
其次,需要考虑水泵的功率选择。
水泵的功率大小直接影响到冷却水循环量、循环时间等多项指标。
通常,可以通过计算系统的压降来确定水泵的功率。
特别是在大流量、高温的场合下,需要考虑水泵的过载能力,防止出现过载故障。
第三,需要考虑换热器的选型。
换热器作为冷却水循环系统中的重要组成部分,其选型也是优化设计的重要内容之一。
在选型时,需要根据冷却水循环系统的实际需求来确定换热器的规格型号以及材料。
同时,应考虑到换热器的传热效率、结构强度以及可靠性等因素。
最后,需要考虑管路的设计。
冷却水循环系统中的管路设计直接关系到系统的稳定性和安全性。
在管路的设计中,需要考虑材料的选择、管径的大小、管道布局、管道的支撑、接头的连接方式等多项因素。
特别是在贮槽、水泵等重要设备周围,应通过设置支架、管夹等固定装置来保证管路的安全性。
综上所述,冷却水循环系统的优化设计需要从多个方面进行综合考虑。
在选型、功率选择、设计等多方面应尽可能地满足工业生产的实际需求,同时应注意到系统的稳定性、安全性等因素。
只有在实际操作过程中,加强系统的维护保养,不断优化系统的设计方案,才能有效地提高冷却水循环系统的性能,为工业生产提供更加可靠、高效的保障。
基于SolidWorks的电机控制器水冷散热器热分析

耗。
IGBT导通损耗的计算公式如下。
(1)设计要求,电机控制器所要求的峰值输考虑到电流要增加一点裕度,故设定I CP=500CE(sat)=1.5 V。
由于占空比不断在变化,取经验值=600 W。
(2)开关损耗。
开关损耗是指由IGBT在控制极收到控制信号时,对电路进行开关操作所产生的能量损耗。
由于每一次开关操作都会产生损耗,所以随着IGBT开关的频率提高,开关损耗会越来越大。
得到开关损耗最精确的方法是测量在开关过程中图1 IGBT导通电流与压降关系曲线=500 A,从上图可得:E (on)=42 mJ,E (off =15 kHz,P sw_I=1 755 W。
1.2 续流二极管导通损耗和开关损耗(1)导通损耗。
二极管的导通损耗与IGBT类似,计算公式如下。
F(sat)×I cp ×D F (4)为续流二极管压降,D F 为二极管占空比因子,极管导通损耗。
FF900R12IE4型号的续流二极管压降与电流关系如图3所示。
图2 IGBT开通和关断损耗与电流关系曲线图4 续流二极管反向恢复损耗与电流关系图3 续流二极管压降与电流关系曲线由图可得E rec =58 mJ。
故P sw_F=870 W。
1.3 IGBT控制单元总损耗IGBT控制单元的总损耗为IGBT芯片和续流二极管的导通损耗与开关损耗之和,故总损耗P t 可由下公式(6)求得。
+P sw_I+P sat_F +P sw_F (6)估算出的总损耗P t =3 365 W。
2 散热器的设计1 散热器材料的选择散热器材料的选择要从多方面来考虑,不仅要有良好的机械强度和加工工艺性,还应具有抗腐蚀性与优良的热传导性,更要考虑表2 平直肋片尺寸参考值散热功率与基板厚度之间的计算公式如下[4]。
t =7×log P 总-6 (7)其中t 为基板的厚度,单位为mm;P 总为IGBT控制单元的热损耗,单位为kW。
计算可得基板的厚度为18.6 mm,这里计算的基板厚度还包括了IGBT控制单元中PCB板与其焊层,以及铝基板的图5 平直肋片式意图图6 肋片的尺寸符号参数值T/mm 2~44~66~88~10≥10t/mm 1.0 1.5 2.0 2.0 2.5h/mm≥6≥8≥8≥10≥10图7 散热器模型图8 散热器流动示意图3 散热器热仿真分析本文选用SolidWorks中的Flow Simulation模块流体分析工具进图9 模型设置3.3 网格的划分在Flow Simulation中,网格的划分有2种形式,分别为自动的网格划分和手工的网格划分。
电动机水冷却结构设计说明
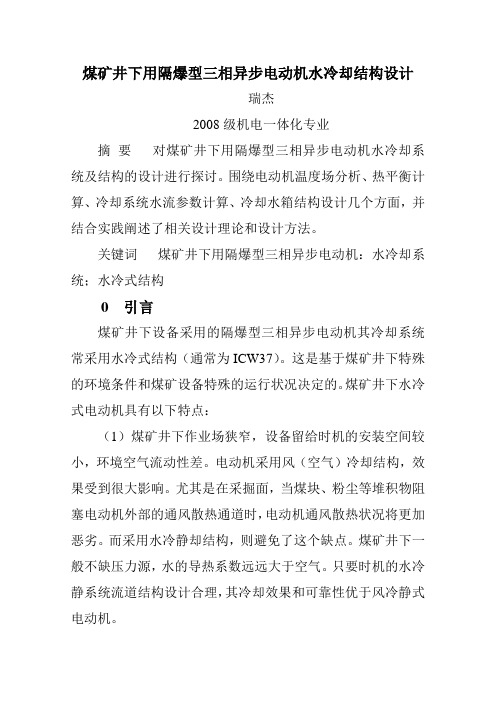
煤矿井下用隔爆型三相异步电动机水冷却结构设计瑞杰2008级机电一体化专业摘要对煤矿井下用隔爆型三相异步电动机水冷却系统及结构的设计进行探讨。
围绕电动机温度场分析、热平衡计算、冷却系统水流参数计算、冷却水箱结构设计几个方面,并结合实践阐述了相关设计理论和设计方法。
关键词煤矿井下用隔爆型三相异步电动机:水冷却系统;水冷式结构0 引言煤矿井下设备采用的隔爆型三相异步电动机其冷却系统常采用水冷式结构(通常为ICW37)。
这是基于煤矿井下特殊的环境条件和煤矿设备特殊的运行状况决定的。
煤矿井下水冷式电动机具有以下特点:(1)煤矿井下作业场狭窄,设备留给时机的安装空间较小,环境空气流动性差。
电动机采用风(空气)冷却结构,效果受到很大影响。
尤其是在采掘面,当煤块、粉尘等堆积物阻塞电动机外部的通风散热通道时,电动机通风散热状况将更加恶劣。
而采用水冷静却结构,则避免了这个缺点。
煤矿井下一般不缺压力源,水的导热系数远远大于空气。
只要时机的水冷静系统流道结构设计合理,其冷却效果和可靠性优于风冷静式电动机。
(2)煤矿井用电动机因受设备安装要求限制,往往要求有较小的外形体积和简单的外形结构。
水冷式电动机结构上没有风扇、风罩、散热片等零件,并且水道布置在封闭的壳体之,因此其外形简约,体积小于相同功率的风冷式电动机。
(3)煤矿井下采掘、运输等设备,因其特殊的工作条件,往往负荷波动很大,所用电动机超负荷运行状况进有发生,造成电动机温升增高。
另外在设计这些设备使用的电动机时,考虑到其外形体积和功率大小两方面要求,往往采用减小电动机定、转子铁心外径,加长定、转子铁心长度的设计方案。
由典型的时机温升设计理论可知,铁心较长的时机其热负荷往往偏高,温升计算误差也较大,这两方面的原因致使电动机的温升处于不可靠状态。
尽管采用提高电动机绝缘等级的方法进行弥补,但电动机使用寿命也将大打折扣。
而水冷式结构的电动机具有较好的冷却效果,可弥补电动机温升设计误差及超负荷运行带来的缺点。
水冷电机散热原理

水冷电机散热原理
水冷电机散热原理的详细解析如下:
水冷电机散热原理是一种利用水的吸热、传热和排热能力来降低电机温度的方法。
在水冷电机中,水被用作冷却介质,通过水的流动,将电机产生的热量带走,以保持电机的工作温度在可接受的范围内。
具体而言,水冷电机散热原理可以分为以下几个步骤:
1. 热量传导:水冷电机的内部有产生热量的部件,例如电机转子、定子和电线等。
这些部件会将产生的热量传导到水冷电机的壳体上。
2. 管道连接:水冷电机中设置有进水管和出水管,用于将冷却水引入和排出。
这些管道会与电机壳体相连接,确保冷却水可以流动到电机的热区。
3. 冷却水流动:冷却水从进水管进入电机壳体,并通过管道分布到电机的热区,例如电机的热源部件。
在经过热源部件时,冷却水会吸收部分热量。
4. 热量吸收:冷却水在经过热源部件时,由于温度差,会吸收部分热量。
这部分热量通过水分子的振动和碰撞,将部分热能转化为水分子的动能。
5. 热量带走:随着冷却水流动,吸收的热量将从热源部件带走,
并带到出水管。
在此过程中,冷却水的温度会升高,形成热量梯度。
6. 热量排出:冷却水从出水管排出电机壳体,将带走的热量散发到周围环境中。
同时,冷却水的温度也会逐渐降低。
通过这样的循环过程,水冷电机能够降低电机温度,避免过热,提高电机的工作效率和寿命。
此外,水冷电机还具有散热均匀、热量承载能力强等优点,广泛应用于许多需要散热的场景。
电动机水冷却结构设计

电动机水冷却结构设计 Standardization of sany group #QS8QHH-HHGX8Q8-GNHHJ8-HHMHGN#煤矿井下用隔爆型三相异步电动机水冷却结构设计姜瑞杰2008级机电一体化专业摘要对煤矿井下用隔爆型三相异步电动机水冷却系统及结构的设计进行探讨。
围绕电动机温度场分析、热平衡计算、冷却系统水流参数计算、冷却水箱结构设计几个方面,并结合实践阐述了相关设计理论和设计方法。
关键词煤矿井下用隔爆型三相异步电动机:水冷却系统;水冷式结构0 引言煤矿井下设备采用的隔爆型三相异步电动机其冷却系统常采用水冷式结构(通常为ICW37)。
这是基于煤矿井下特殊的环境条件和煤矿设备特殊的运行状况决定的。
煤矿井下水冷式电动机具有以下特点:(1)煤矿井下作业场狭窄,设备留给时机的安装空间较小,环境空气流动性差。
电动机采用风(空气)冷却结构,效果受到很大影响。
尤其是在采掘面,当煤块、粉尘等堆积物阻塞电动机外部的通风散热通道时,电动机通风散热状况将更加恶劣。
而采用水冷静却结构,则避免了这个缺点。
煤矿井下一般不缺压力源,水的导热系数远远大于空气。
只要时机的水冷静系统流道结构设计合理,其冷却效果和可靠性优于风冷静式电动机。
(2)煤矿井用电动机因受设备安装要求限制,往往要求有较小的外形体积和简单的外形结构。
水冷式电动机结构上没有风扇、风罩、散热片等零件,并且水道布置在封闭的壳体之内,因此其外形简约,体积小于相同功率的风冷式电动机。
(3)煤矿井下采掘、运输等设备,因其特殊的工作条件,往往负荷波动很大,所用电动机超负荷运行状况进有发生,造成电动机温升增高。
另外在设计这些设备使用的电动机时,考虑到其外形体积和功率大小两方面要求,往往采用减小电动机定、转子铁心外径,加长定、转子铁心长度的设计方案。
由典型的时机温升设计理论可知,铁心较长的时机其热负荷往往偏高,温升计算误差也较大,这两方面的原因致使电动机的温升处于不可靠状态。
采煤机用隔爆水冷三相电动机的散热优化设计

采煤机用隔爆水冷三相电动机的散热优化设计段小燕【摘要】针对采煤机常采用JOY 30EB500J型电机散热性能不足时常导致电机烧毁的问题,对电动机发热的原理进行了分析,从电磁设计、机械结构设计和绝缘设计三方面进行了优化设计.通过实测电动机在连续开机8h后,电动机中心转子的温度由优化前的95.4℃降低到优化后的64.6℃.说明改进设计符合生产使用中散热的要求.【期刊名称】《机械管理开发》【年(卷),期】2018(033)012【总页数】3页(P13-14,24)【关键词】JOY 30EB500J型电机;电磁设计;机械结构设计;绝缘设计【作者】段小燕【作者单位】山西省吕梁市柳林县煤炭工业局, 山西吕梁 033300【正文语种】中文【中图分类】TM302引言采煤机是地下煤矿生产过程中的关键设备,采煤机的工作效率直接决定着综采工作面的原煤产量。
在实际生产中为保证持续生产,采煤机截割部电机就会不停运转。
由于电机在运转过程中会产生热量,尤其是在电机运行时间过长且散热效率过低时,就会导致电机温度过高[1]。
发热异常可能会烧坏绝缘,导致线路短路致使绕组损坏;铜条的端环出现热塑形变而造成铜条断裂和轴承膨胀抱死而烧毁电机等事故。
并且在有限的采煤工作面之中,由于割煤或打锚杆等作业产生煤尘在电机表面覆盖堆积导致电机外壳热量无法释放,最终造成人员烫伤甚至爆炸事故[2]。
亟待对采煤机截割部上转载的隔爆水冷三相电动机的散热进行改进。
本文以采煤机截割部常用的JOY 30EB500J型电机(JOY 30EB500J型电机的功率为750 kW,额定电压为3300 V,采用水冷设计)为例,进行散热优化,为采煤机的持续安全运行提供保障。
1 电动机散热改进分析电动机在运转过程中将电能转化为电磁能,利用转子在磁场中受到的磁场力作用而转动。
在转子转动的过程中,会出现电磁互换,定子绕组与转子电枢中会有持续的电流流动。
由于定子绕组与转子电枢中不可避免的会有电阻,因此会产生热能。
- 1、下载文档前请自行甄别文档内容的完整性,平台不提供额外的编辑、内容补充、找答案等附加服务。
- 2、"仅部分预览"的文档,不可在线预览部分如存在完整性等问题,可反馈申请退款(可完整预览的文档不适用该条件!)。
- 3、如文档侵犯您的权益,请联系客服反馈,我们会尽快为您处理(人工客服工作时间:9:00-18:30)。
关于水冷电机散热结构的优化设计分析
摘要:以电动汽车电机采用的特殊结构为切入点,结合定子机壳内周向螺旋水槽的结构,对其水冷系统进行了优化设计,分析与计算了其散热能力以及流阻损失影响因素,最终得出了对电机水槽结构设计的有益之处。
关键词:水冷电机;散热结构;优化设计
作为新时期电动汽车的关键技术,汽车的电机驱动系统对于其各功能的运行意义重大,需要其电机具备高效率、高可靠性等特点,高功率密度驱动电机的持续运行会加剧电机温升,降低系统可靠性,因此,合理设计电机冷却结构,对于降低电机温升,保证电机可靠性意义重大,本文将结合定子机壳内周向矩形水槽的结构,对其水冷系统进行了优化设计。
1 电机水冷套内流体流动及传热相关计算 1.1 流体运动基本方程
借助于连续性方程和纳斯一斯托克斯方程表示不可压缩流体的运动,具体可用式(1)表示圆管中流体的雷诺数如下[1-2]:
v
d
u e =R (1)
式中,v 为流体动力粘度,且μ
ρ
=
v ,d 为 圆管直径,u 则为平均流速,对非圆形截面的管道,对应的尺寸为管道当量直径为e d ,其满足以下关系:
S
A
4d e =
(2) 其中,S 为道润湿周长,A 为管道截面面积。
管道内总阻力损失f h 具备以下关系:
g
2u
d h 2
1⋅⋅=L f λ (3)
其中,L 为管道长度,λ为沿程阻力系数,u 为水流平均速度,d 为圆管直径,则局部阻力损失2h f 可表示如下:
g
u
f 2h 2
2⋅=ς (4)
其中沿程阻力系数用ς表示,其由道的结构形状决定。
1.2 电机水冷套传热基本方程
用冷却公式表示电机冷却水道表面的对流换热情况如下:
()
f w h T T hA -=Φ (5)
其中,A 为散热面积,h 为流换热系数,f T 为流体温度,w T 为固体壁面温度,h Φ则表
示单位时间内对流换热量。
结合图斯-贝尔特公式及管内紊流换热规律,对对流换热系数进行计算得:
4
.08
.0r
e 023.0u P R N = (6)
其中,Re 为流体雷诺数,Nu 为努塞尔数,流体普朗特殊则用Pr 表示。
其中Nu 包含对流换热系数h ,其可用下式计算得到:
e
d Nu h λ
⋅=
(7) 2 水冷电机周向水槽水冷结构及流场 2.1 螺旋水槽水冷电机结构
具体说来,轴向结构和周向结构为常用的典型结构,将水冷电机的水槽内置于电机壳内,如图1,为周向水槽水冷电机结构。
图1 结构及水流流向示意图
周向水槽水冷电机结构常采用螺旋式和折返式两种基本结构型式,螺旋式绕电动机外壳,结构通畅,道截面积比较均衡,本文以螺旋水道为例进行分析。
从上图中可看出两端的环形水道和中间的螺旋形水道共同组成了周向水槽
从上图中可看出,周向水槽有着较为复杂的结构,电机的两端间的温差较大,冷却水从其一端流向另一端。
2.2 冷电机周向水槽结构的流场分析
借助于有限元法,笔者研究了水槽流场的分布,对其进行了仿真计算,得出电机周向水槽内的水流速度分布,发现两端的环形水道与中间的螺旋形水道的水流速度不同,这与水道截面积不同有关,且二者间存在过渡区,且在螺旋水道与环形水道的交汇处、入水口后方均存在流动低速区,共同组成了其流场[3]。
3 向水槽结构散热能力影响因素分析
(1)截面尺寸。
结合前述的公式(1)~(3)可看出,等效直径会随着截面尺寸的变小而变小,且对应的努赛尔数越大,雷诺数越大,则其散热系数就越大。
在设计水道方面,显然不应只看重散热能力,还应对水道的流阻的限制作用进行考虑,结合流阻公式可知,不可任意缩小水道尺寸,所以应考虑到水道的阻力损失。
(2)隔板厚度。
螺旋水道中间的隔板的散热效果类似于肋板散热,基于其隔板较薄的
现状,除主散热面是直接将传导来的热量散掉外,水道的四个散热表面中的三个表面皆是借助隔板传递的,所以,对于水道散热能力而言,隔板的厚度的影响较大。
在隔板厚度对水道散热能力的影响的分析方面,笔者借助耦合场汁算的方法,就不同厚度隔板下的电机冷却水套等效散热系数进行了计算。
如图2,为仿真用电机水套的结构图[4]。
图2 某车用水冷却电机水套结构图
上图显示出水套与电机定子外表面的接触面,水套加热面积A=0.44mm ²,在此前提下,我们假设电机发热功率为660W ,且对隔板厚度mm 6,mm 4,mm 2t =时水套的等效散热系数进行计算得出的结果具体如表1所示,其中,D 为水套加热面温度/u T ℃,B 为发热功率
W /Φ,G 为等效散热系数h e /W /(m 2-k),A 为隔板厚度t /mm ,E 为冷却水平均温度/T ℃,
C 为水套加热面积A/m ²,F 为等效散热系数()
k m //h 2e ⋅W 。
表1 不同厚度隔板的水套等效散热系数计算结果 A B C D E F 2
660
0.44
72.46 70.38 5807 4 72.57 70.39 6818 6
73.67
70.82
5250
结合上述计算结果可看出,当隔板厚度分别为2、4、6mm 时,对应的电机的等效散热系数并不相同,等效散热系数最大得时刻出现在的隔板厚度为4mm 时,当其厚度为2mm 和6mm 时,以4mm 时等的等效系数为标准,另外二者的等效散热系数为其的14.8%和23%,所以,就水道的散热能力看来,隔板厚度对其影响较大,本电机中,隔板厚度的最佳值仍然不是4mm ,有待进一步计算分析确定。
(3)加工制造工艺。
具体说来,如果水套并非一次成型铸造,会分为外部水套壳和内部水槽部分,基于安装精度及加工制造工艺方面的原因,水槽的水套壳和隔板间存在微小间隙。
在其对水冷套散热能力的影响的研究方面,笔者以图2的某车用水冷永磁电机为例,研究了其等效散热系数,最终发现隔板和水槽套外壳之间微小间隙的存在,对向水套壳传热的作用和隔扳的导流作用会形成削弱,并通过对水流平均速度的降低,最终使得水套散热能力被降低,所以,需采取密封措施进行电机水套加工与装配,从而使得隔板的导流作用和传热作用得到保障。
结束语:
综上所述,影响周向水槽散热能力的因素众多,本文结合对水冷电机散热结构的优化
设计,从截面尺寸、隔板厚度等方面分析了其向水槽结构散热能力影响因素,后续实际运用证明,此优化设计方案具备了较高的实用价值。
参考文献:
[1]陈辛波,黄露,卫镜周,等.车用水冷电机散热结构优化设计[C]// 第十六届全国机械设计年会2012.
[2]李青青,黄勤,杨立,等.永磁同步电机水冷系统散热参数分析与热仿真[J].机械设计与制造, 2014, (4):188-191.
[3]Hillhouse.J,Lyles.K.Consideration of Employing Motors with Oil MistLubrication[C].Petroleum and Chemical Industry Technical Conference (PCIC),USA,2013:1-7.
[4]于光义,李钟勇,牛占林.水冷机柜散热系统风道结构设计优化分析[J].制冷, 2012, 31(1):19-24.。