薄壁零件加工及如何减少变形
消除薄壁工件加工夹紧力变形的夹具技术研究

6 HRC 0 图 3
变形。
3 夹 具 设 计 .
原 理 夹 具 由 心 轴
图 1
心 轴 作 用
是 :完成工件正确地定位 、夹紧 ,与机床连收管接 部位 为直径 5 。 0 mm直柄 ,与收 管配合公差为0
~
1 凹 圈 2 凸 圈 3 螺 钉 4 成 ,工 件 在 夹 具 上 心 、 、 和 组 轴 定 中心 、端 面 定 位 、 螺 纹 夹 紧 ,一 次 完 成 工 件
不 产 生 径 向 压
l 2 3
联接 产品的薄壁锥形螺母。通用工件 的加工变形、
定 位 、装夹 ,使 技 术 人 员及 操 作者 不 知 如 何 下 手 。 按 常 规 工 艺 采 用 端 面 或 径 向夹 紧 ,但 在 轴 向 力 或 径 向 力 作用 下 ,使 工 件 受 到夹 紧 力 ,从 而 产 生 弹性
口
消除薄壁工件加工夹紧力变形的 夹具技术研究
北方 光 电股份有 限公 司技术 中心工 艺研究所 ( 陕西 西安 7 0 4 ) 张利 军 1 0 3
随着机 械 制造业 的发展 ,要 求精 度高 、体 积
小 、 重 量轻 ,高 精 度 的 薄 壁 工 件逐 渐 增 多 ,尤 其是 外 圆 、锥 面 、端 面 加 工 。夹 具 靠 工 件 自身 的 螺 纹 拉 紧 , 对 工 件
凸 圈3 位 ,当 工件 加 工 后 进行 转 动 ,保证 凸 圈3 定 的 三个 凸 面尺 寸 5 。 0 移 动 到 尺 寸 6 。 0 9 ±3 1 ±3 凹面
余 量02 . mm;两 端 加 工 中心 孔 ,淬 火 后 首 先 研 磨 两
一 、
3 9 I :
控制薄壁零件变形的工艺措施

G 向
摩擦等综合 作用 , 使零 件表层 内部产 生新 的加工残余应 力。 残
余 应 力 是 一 个 不 稳 定 的应 力 状 态 , 零 件 受 到 外 力 作 用 时 , 当 外
力与残余应 力相互作 用 , 其某些 局部呈现塑性 变形 , 使 截面 内
!——
G向
服被加工材 料的弹性 变形 、塑性 变形 以及 刀具与切 屑和工件
之间 的摩擦 , 会产 生切削力 和切削热 , 在切 削力 和切 削热 的作 用下, 容易产生振动和变形 , 响工件加工质量 。 影
( )圆支管零件 图 a
( )圆支管工序 图 b
图 1 设 计工艺加 强筋 , 提高刚性
另外 , 机床、 工装 的刚度 , 切削刀具及其角度 、 削参数 和零 切
件冷却散热情况等对零件的变形也有一定的影 响。 所有因素 中 ,
24 对 称 分 层 铣 削 。 应 力 均 匀 释 放 . 让
毛坯初始 残余应力 对称释放 ,可 以有 效减小零件 的加 工
切削力 、 夹紧力 以及残余应力 , 产生加工变形 的主要因素 。 是
随着零件壁厚 的减小 , 其刚性降低 , 加工变形增 大。因此 , 在切 削过程 中 , 可能地利 用零件 的未 加工部分 , 为正在切 尽 作 削部分 的支 撑 , 切削过程 处在刚性较 佳 的状态 。如 : 内有 使 腔 腹板 的腔体类 零件 , 加工 时 , 刀从毛坯 中间位置 以螺 旋线方 铣
有较好的效 果。 关键词 : 薄壁 零 件 ; 变形 ; 工 精 度 加 中图 分 类 号 : H1 1 T 6 文献标识码 : B 文 章 编 号 : 6 2 5 5 ( 0 0)6 0 1 - 2 17 — 4 X 2 1 0 — 19 0
薄壁零件的加工特点及工艺分析

薄壁零件的加工特点及工艺分析机械加工肯定少不了薄壁零件的加工,而这类零件加工更需要仔细认真,所以了解其加工特点及工艺很有必要。
以下是店铺为你整理推荐薄壁零件的加工特点及工艺分析,希望你喜欢。
薄壁零件的加工特点1)易受力变形:因工件壁薄,在夹紧力的作用下容易产生变形,从而影响工件的尺寸精度和形状精度;(2)易受热变形:因工件较薄,切削热会引起工件热变形,使工件尺寸难于控制;(3)易振动变形:在切削力(特别是径向切削力)的作用下,容易产生振动和变形,影响工件的尺寸精度、形状、位置精度和表面粗糙度。
薄壁零件的加工工艺薄壁零件加工精度的容易受到多方面因素的影响,归纳起来主要有以下三方面:(1)受力变形;(2)受热变形;(3)振动变形。
如果采用传统的数控加工工艺,很难加工出符合精度要求的薄壁零件,甚至使薄壁产生破裂。
主要原因如下:(1)在粗加工时,切削量较大,在切削力、夹紧力、残余应力和切削热的作用下,会使薄壁产生一定程度的变形。
(2)半精加工和精加工时,随着材料的去除,工件的刚度已降至非常低,薄壁部分的变形会进一步加剧。
因此,根据薄壁零件的结构特点和加工精度要求,对于薄壁零件,应尽可能选择高速切削技术来加工。
采用高速切削技术,可有效地降低切削力和切削热,消除工件的残余应力,以提高薄壁零件的尺寸稳定性,同时要兼顾加工效率。
除采用高速切削技术外,薄壁零件的加工,还要合理安排加工顺序,尽可能保证内外轮廓线依次交叉切削加工。
以进一步消除工件变形带来的尺寸误差。
薄壁零件的加工举例1、工序的划分本任务划分为两道工序,共分(1)工序一:薄壁加工;(2)工序二:铣凸台和椭圆槽。
(3)工序三:孔加工。
其中工序一是难点。
划分2个工步,具体加工顺序如下:(1)选择φ10 mm双刃键槽铣刀粗加工薄壁内外轮廓线,刀补值选8.3mm,留出半精加工余量,深度方向分层切削,留0.2mm余量;(2)换φ10 mm 四刃立铣刀,采用高速切削技术半精加工薄壁内外轮廓线,刀补值选8.1 mm,深度方向分别留0.1mm余量;(3)用φ10 mm四刃立铣刀,采用高速切削技术,精加工薄壁两条轮廓线,并根据实际测量尺寸控制零件加工精度。
薄壁零件加工的特点

•摘要:在数控车加工过程中,经常碰到一些薄壁零件的加工。
本文详细分析了薄壁零件加工的特点、防止变形的工艺方法、车刀几何角度及切削参数的选择,结合在教学实践中的实例设计出加工方案。
关键词:薄壁零件工 ...•摘要:在数控车加工过程中,经常碰到一些薄壁零件的加工。
本文详细分析了薄壁零件加工的特点、防止变形的工艺方法、车刀几何角度及切削参数的选择,结合在教学实践中的实例设计出加工方案。
关键词:薄壁零件工艺分析加工方案1 薄壁工件的加工特点车薄壁工件时,由于工件的刚性差,在车削过程中,可跑产生以下现相。
1.1 因工件壁薄,在夹压力的作用下容易产生变形。
从而影响工件的尺寸精度和形状精度。
当采用如图1所示三爪卡盘夹紧工件加工内孔时,在夹紧力的作用下,会略微变成三角形,但车孔后得到的是一个圆柱孔。
当松开卡爪,取下工件后,由于弹性恢复,外圆恢复成圆柱形,而内孔则如图2所示变成弧形三角形。
若用内径千分尺测量时,各个方向直径D相等,但已变形不是内圆柱面了,这种现相称之为等直径变形。
1.2 因工件较薄,切削热会引起工件热变形,从而使工件尺寸难以控制。
对于线膨胀系数较大的金属薄壁工件,如在一次安装中连续完成半精车和精车,由切削热引起工件的热变形,会对其尺寸精度产生极大影响,有时甚至会使工件卡死在夹具上。
1.3 在切削力(特别是径向切削力)的作用下,容易产生振动和变形,影响工件的尺寸精度,形状、位置精度和表面粗糙度。
2 减少和防止薄壁件加工变形的方法2.1 工件分粗,精车阶段粗车时,由于切削余量较大,夹紧力稍大些,变形也相应大些;精车时,夹紧力可稍小些,一方面夹紧变形小,另一方面精车时还可以消除粗车时因切削力过大而产生的变形。
2.2 合理选用刀具的几何参数精车薄壁工件时,刀柄的刚度要求高,车刀的修光刃不易过长(一般取0.2~0.3mm),刃口要锋利。
2.3 增加装夹接触面如图3所示采用开缝套筒或一些特制的软卡爪。
使接触面增大,让夹紧力均布在工件上,从而使工件夹紧时不易产生变形。
航空薄壁件加工技巧
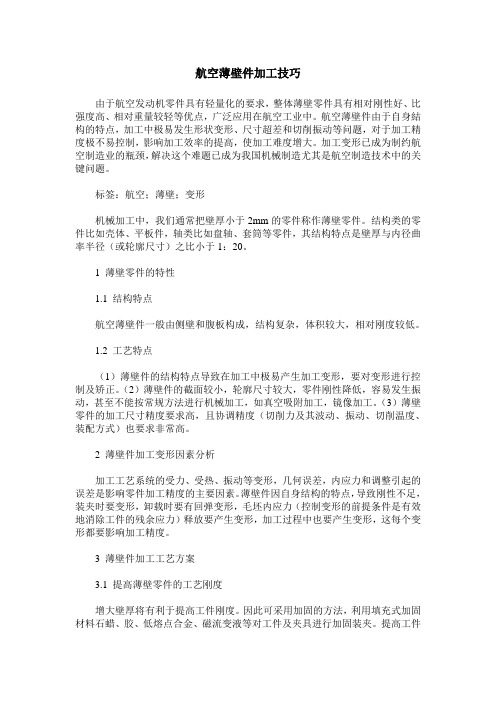
航空薄壁件加工技巧由于航空发动机零件具有轻量化的要求,整体薄壁零件具有相对刚性好、比强度高、相对重量较轻等优点,广泛应用在航空工业中。
航空薄壁件由于自身結构的特点,加工中极易发生形状变形、尺寸超差和切削振动等问题,对于加工精度极不易控制,影响加工效率的提高,使加工难度增大。
加工变形已成为制约航空制造业的瓶颈,解决这个难题已成为我国机械制造尤其是航空制造技术中的关键问题。
标签:航空;薄壁;变形机械加工中,我们通常把壁厚小于2mm的零件称作薄壁零件。
结构类的零件比如壳体、平板件,轴类比如盘轴、套筒等零件,其结构特点是壁厚与内径曲率半径(或轮廓尺寸)之比小于1:20。
1 薄壁零件的特性1.1 结构特点航空薄壁件一般由侧壁和腹板构成,结构复杂,体积较大,相对刚度较低。
1.2 工艺特点(1)薄壁件的结构特点导致在加工中极易产生加工变形,要对变形进行控制及矫正。
(2)薄壁件的截面较小,轮廓尺寸较大,零件刚性降低,容易发生振动,甚至不能按常规方法进行机械加工,如真空吸附加工,镜像加工。
(3)薄壁零件的加工尺寸精度要求高,且协调精度(切削力及其波动、振动、切削温度、装配方式)也要求非常高。
2 薄壁件加工变形因素分析加工工艺系统的受力、受热、振动等变形,几何误差,内应力和调整引起的误差是影响零件加工精度的主要因素。
薄壁件因自身结构的特点,导致刚性不足,装夹时要变形,卸载时要有回弹变形,毛坯内应力(控制变形的前提条件是有效地消除工件的残余应力)释放要产生变形,加工过程中也要产生变形,这每个变形都要影响加工精度。
3 薄壁件加工工艺方案3.1 提高薄壁零件的工艺刚度增大壁厚将有利于提高工件刚度。
因此可采用加固的方法,利用填充式加固材料石蜡、胶、低熔点合金、磁流变液等对工件及夹具进行加固装夹。
提高工件的工艺刚度还可以从下面几个方面着手,一是提高工件与工装接触定位面的加工精度和表面光洁度,二是提高接触刚度(增强接触面硬度或采用高弹性模量材料)。
浅谈薄壁零件的加工

浅谈薄壁零件的加工文章以典型薄壁零件在三轴机床上的加工为例,探讨薄壁件在数控铣加工过程中存在的易变形、工件尺寸及表面粗糙度不易控制等技术问题,对加工难点要点进行分析,给出了工艺路线和加工方案,通过优化、完善夹具及装夹方法,优化加工参数,优化加工工艺从而有效解决薄壁件的加工精度和批量加工的尺寸稳定的难题,为其它同类薄壁零件的加工提供借鉴。
标签:薄壁;装夹;工艺方法;加工参数;变形1 概述在数控加工中,薄壁零件因其自身具有重量轻,节约材料,结构紧凑等特点在航空航天、通讯、国防等各个领域产品中得到了越来越广泛的应用,而薄壁零件因其壁薄、刚性差、易变形加工困难也成了同时需要面对的棘手问题,由于薄壁零件自身的特点,在实际加工中不易达到设计的形位公差要求,其加工工艺较为繁复,编程、加工需要注意的细节较多,实际操作较为复杂。
作者针对这类薄壁零件以曾经加工过的一批零件为例介绍薄壁件的加工方法、夹具使用、刀具选用、参数选择及编程要点等。
此零件使用MasterCAM 9.1编程,在FANUC系统三轴机床上加工完成。
数控加工薄壁零件时,零件因刚度不足引起的加工变形成为影响尺寸精度的主要矛盾。
为了提高零件尺寸的稳定性,对于薄壁零件的加工必须从工艺安排、夹具设计、设备选择、刀具选择、加工参数选择、程序编制等方面进行综合考虑,以解决零件在反复装夹后保证零件的加工精度的问题。
下面通过具体实例来介绍薄壁件的加工。
2 实例零件加工2.1 示例零件特点实例零件(如图2)为不久前加工的某型号产品光学系统的前镜头板,共45件,材料为L Y12铝板,下料尺寸为185mm*130mm*15mm,转入本工序时已经经过粗加工及时效工序,粗加工后余量为单面1.5mm,零件变形较大约为1mm-1.8mm。
从图2中可以看出,零件形状并不复杂,多为平面、台阶,但零件外形尺寸较大,由于中部为D形空腔,其有效截面积很小,并且截面面积变化较大不均匀。
对于数控加工来说,此零件的尺寸公差较大,除注意选择合适的加工参数外,在编程上基本没有什么难度。
加工薄壁零件的方法浅析
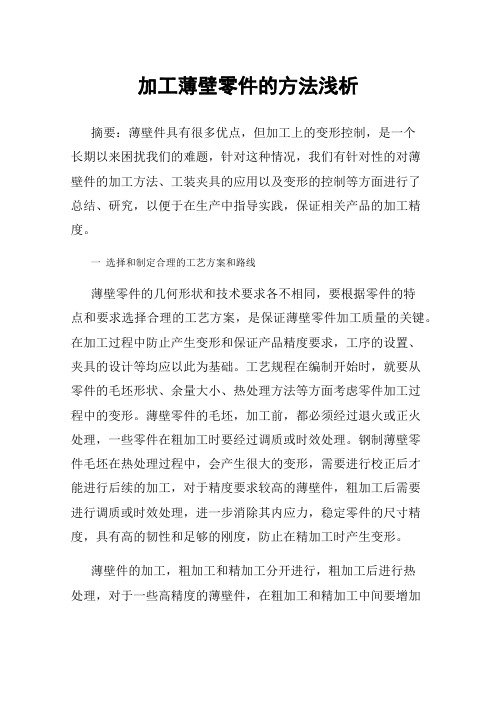
加工薄壁零件的方法浅析摘要:薄壁件具有很多优点,但加工上的变形控制,是一个长期以来困扰我们的难题,针对这种情况,我们有针对性的对薄壁件的加工方法、工装夹具的应用以及变形的控制等方面进行了总结、研究,以便于在生产中指导实践,保证相关产品的加工精度。
一选择和制定合理的工艺方案和路线薄壁零件的几何形状和技术要求各不相同,要根据零件的特点和要求选择合理的工艺方案,是保证薄壁零件加工质量的关键。
在加工过程中防止产生变形和保证产品精度要求,工序的设置、夹具的设计等均应以此为基础。
工艺规程在编制开始时,就要从零件的毛坯形状、余量大小、热处理方法等方面考虑零件加工过程中的变形。
薄壁零件的毛坯,加工前,都必须经过退火或正火处理,一些零件在粗加工时要经过调质或时效处理。
钢制薄壁零件毛坯在热处理过程中,会产生很大的变形,需要进行校正后才能进行后续的加工,对于精度要求较高的薄壁件,粗加工后需要进行调质或时效处理,进一步消除其内应力,稳定零件的尺寸精度,具有高的韧性和足够的刚度,防止在精加工时产生变形。
薄壁件的加工,粗加工和精加工分开进行,粗加工后进行热处理,对于一些高精度的薄壁件,在粗加工和精加工中间要增加半精加工等工序,首先保证基准的准确和统一,要反复对簿壁零件的内、外表面进行加工,能大大减小零件的变形。
在薄壁零件的加工过程中,加工余量的分配是否得当,将影响零件的加工质量。
对于薄壁零件,加工余量的分配,主要是粗加工和精加工之前的余量要留的适当。
同时为了保证零件的加工精度,精加工工序虽然余量很小,但一般仍要分几次走刀将其加工到最终尺寸。
在进行薄壁件加工过程中,一些精度要求很高的产品,要将车削和磨削相结合来进行薄壁件内、外径的加工。
二防止零件装夹时的变形薄壁零件在加工过程中,采用合理的工艺路线等工艺措施,是保证产品精度的重要保证,在薄壁件加工中另一个重要的环节就是零件的装夹。
零件加工前的合理装夹,是防止因装夹不当引起零件变形,保证薄壁件加工质量的一项重要措施。
如何消除零件加工的变形问题

9 6-
科 技论 坛
如何消 除零件加工 的变形 问题
张 军
( 哈 尔滨博 实 自动化股份有 限公 司工机械加 工过程 中, 尺寸和形状会发 生改 变。改变的原 因不 同, 也决定 了解决的方法不 同。机械h_ r - 中对这些变形的处 理措施是否得 当, 直接决定了零件加工质量的好坏 , 也反 应 了机h . r - 艺水平的高低 。文章 对机械加 工过程 q - 零件 经常 出现 的变形 问题做 出简单分析 , 并提 出一些减少零件 变形的技 术方法, 以此 来控制和消除零件的变形 。 关键词 : 机械加工 ; 薄壁 ; 夹紧; 变形 机械加 工中的零 件变形问题 , 是客观存在 的 , 也是 比较难 以解 力 , 零件阻碍刀具切 削时产生的弹性变形和塑性变 形 , 使切削 区温 决的问题 , 它会决定成品质量的高低 。 为 了更好的解决 问题 , 首先必 度升高而产生热变形 。 所 以, 我们要在粗加工时 , 背吃刀量和进 给量 须分析产生变形的原因。产生变形的原因是多方面的 : 可 以取 大些 ;精 加工时 ,刀量一般在 0 . 2~0 . 5 m m,进给量一般在 1零件的材料和结构会影响零件的变形 0 . 1— 0 . 2 m m / r , 甚 至更小 , 切 削速 度 6—1 2 0 m / m i n , 精 车时用 尽量 高 变形量 的大小与形状复杂程度 、 壁厚大小 、 长宽 比、 材质 的稳定 的切削速度 , 但不易过为高。 合 理选择好切削用量 , 从而到达减少零 性和刚性成正 比, 所 以在设计零件时应 尽可能的减小这些 因素对零 件变形的 目的。 件变形 的影 响。在加工前也要对毛坯疏松 、 硬度 等缺 陷进行严格控 4 加 工后 应 力 变 形 制, 保证毛坯质量 , 减少其带来 的零件变形 。 加工后 , 零 件本身存在 内应力 , 这些 内应 力分布是 一种相对 平 2 零 件 装 夹 时造 成 的 变 形 衡 的状 态 , 零件 外形相对稳定 , 但是去除一些材料 和热处理后 内应 零件装夹时 , 首先要选择正确的夹紧点 , 然后 根据夹紧点 的位 力发生变化 , 这 时零件需要重新达到力的平衡所以外形就发生 了变 置选择适当的夹 紧力 。因此尽可 能使夹 紧点和支撑点一致 , 使 夹紧 化 。 解决这类变形可 以通过热处理 的方法 , 去除应力残留。 铸件要做 力作用在支撑上 , 夹紧点应尽可 能靠 近加 工面 , 且 选择不易引起 夹 到时效处理 , 尽量消除 内部的残余 应力 , 采用变形后再加工 的方式 , 紧变形的位 置。 其次要增大零 件与夹具 的接触面积或采用轴向夹紧 即粗加工 一时效 一 再加工 。 力。 增大零件与夹具 的接触面积 , 可有效 降低零件件装夹时的变形 。 综 上所述 , 对于易变 形零件 , 在毛坯 和加工工艺上 都要采 用相 如在铣 削加 工薄壁件时 , 使用 弹性压 板 , 目的就是 增加接触零 件的 应 的解决办法 , 需根据不 同情况加 以分析 , 都会 找到一条合适 的工 受力面积 ; 在车削薄壁套 的内径及外 圆时 , 无论是采用开 口过渡环 , 艺路 线 的 。 还是使 用弹性芯轴 、 整 弧卡爪 等 , 采用 的都是增大零件装夹 时的接 参 考文 献 触 面积 。 这种方法避免零件 的变形。 采用轴向夹紧力 , 在生产 中也被 【 1 ] 孟 少农 . 机 械 加 工 工 艺 手 册『 M 1 . 北京 : 机 械 工业 出版社 . 广泛使 用 , 设计制作专 用夹具可使夹紧力作用在端 面上 , 可以解决 [ 2 1 齐 宏. 现代机械制造技 术概论f M 1 . 北京 : 机械 工业 出版社. 由于零件壁薄 , 刚性较差 , 导致的零件 弯曲变形 。
- 1、下载文档前请自行甄别文档内容的完整性,平台不提供额外的编辑、内容补充、找答案等附加服务。
- 2、"仅部分预览"的文档,不可在线预览部分如存在完整性等问题,可反馈申请退款(可完整预览的文档不适用该条件!)。
- 3、如文档侵犯您的权益,请联系客服反馈,我们会尽快为您处理(人工客服工作时间:9:00-18:30)。
薄壁零件加工及如何减少变形
摘要:金属零件,尤其是薄壁零件在加工过程中由于材质本身的状态及加工过
程中热应力等因素的影响,变形是不可避免的。本文就此讨论如何减少薄壁零件
的加工过程中的变形。实践证明,通过选择合理的装夹方式、刀具的几何角度、
切削用量、冷却液等,是完全可以减少薄壁零件在加工过程中的变形,保证零件的
加工质量的。
关键词:变形热应力切削用量切削液几何角度数铣
1 概述
零件在加工过程中由于各种因素导致变形是无法消除的,零件在加工中变形
的大小除与零件本省材质、结构有关外,也与加工中零件的装夹方式、刀具选用、
切削用量及冷却也的选择等有很大的关系。材质、结构与其用途有关,有时是无
法取代的。但作为工艺员在零件材料一定的情况下,我们就必须从加工中想办法。
我们知道,采用正确的装夹方式、合理选用刀具、切削用量、冷却液是减少零件
变形的关键之所在。其中又尤以薄壁零件变形最大,最难控制,主要原因是薄壁零
件刚性差、强度弱,在加工中极易产生变形,使零件的形位误差增大,不易保证零件
的加工质量。薄壁零件也因为重量轻、节约材料、结构紧凑,应用极为广泛。为
此,对薄壁零件加工以及加工过程中零件的装夹,刀具的选用、切削用量、冷却液
的选用等作一些探讨和分析,为今后更好的加工薄壁零件,保证零件的加工质量提
供一些建议。
2 工艺分析
2.1 零件材料的组成
该零件材料为ZL1,他的成分见表1
2.2零件结构分析
零件总体结构比较简单,但属于薄壁类形腔零件,大部分壁厚仅有3㎜。加工
中要去除大部分材料,加工中会产生大部分铣削热量,从而,导致零件产生热变形,
这一点是我们制定工艺方案前必须考虑的。
2.3工艺流程的分析
钳:按零件外形及内腔尺寸,单面放1.5㎜划外形、内腔线为下一道工序提供
依据
铣:参照钳工划线,单面留余量1.5㎜余量铣外形及内腔、铣厚度二面,本工序
加工中去掉大部分材料,因此,余量放得多,保证后序加工由于变形不能保证加工
尺寸
数铣:单面留0.5㎜余量铣外形及内腔,该工序时零件厚度大部分仅有6㎜,加
工时,在考虑生产率的同时,还必须保证加工中变形不得过大
热:进行时效,作稳定处理,用途时是去除加工中应力
数铣:铣对外形、内腔及各下陷尺寸,本工序零件尺寸要加工到位,在考虑变形
同时还得保证产品表面质量
钳:借助钻模,制对各孔,并锉修清角
该零件也可上线切割加工外形及内腔,但上线切割加工生产率低,成本较高,
因此,不宜选用。
2.4加工中的减少变形措施
该零件结构简单,从工艺流程不难看出,零件工艺流程并不复杂,接下来的问
题是在加工中如何减少二道数铣关键工序中变形来满足产品的质量。为此,我们
主要要从以下四个方面来采取具体措施减少两件加工中的变形。
2.4.1选择正确装夹方式
由于该零件属于腔体薄壁零件,在铣削加工不能按常规采用虎钳装夹,因为虎
钳装夹使零件受力情况不理想。零件在加工过程中随着大部分材料去除,零件在
垂直受力的方向有延伸的趋势,使零件略鼓,一旦取下零件,往往使加工出来的零
件产生回弹,极易变形,对零件的尺寸影响极大。因此,在加工中我们对装夹方式进
行改进,采用压板式装夹,使零件上每一点的夹紧力都保持均衡,增大零件装夹的
接触面,从而减少每一点的夹紧力,零件的变形会好得多。因为,根据物理学中压强
公式:P=F/S可以知道:当压力一定时,受力面积越大,压强就越小,从理论分析可以
看出,增大装夹接触面,减少每一点的夹紧力,这种方法是可行的。实践证明也是行
之有效的。因此,今后在加工薄壁零件时,应充分重视装夹的问题。
2.4.2选择合理的切削用量
切削用量是机床调整前必须确定的重要参数,而且其值的合理与否对加工质
量、加工效率、生产成本等有着非常重要的影响。所谓“合理的”切削用量是指充
分利用刀具切削性能和机床的动力性能(功力、扭矩),在保证质量的前提下,获得
高的生产率和低的加工成本的切削用量。切削用量的三要素指切削速度V、进给
量F、切削深度ap,对于薄壁零件加工切削用量更是选择的非常合理。我们知道,
切削力的大小与切削用量是密切相关的,从加工角度来看,吃刀量和进给量如果选
得过大,对铣削加工薄壁零件极为不利,工件阻碍刀具切削时产生的弹性变形和塑
性变形,切削区随着切削热的升高而产生热变形。减少吃刀量,增大进给量,切削力
虽有所下降,但零件表面的粗糙度增大,因此针对该零件我们选用粗加工和精加工
二道工序。粗加工采用转速高,吃刀量大,进给量小,可减少零件在加工时所产生切
削热带来的变形,提高零件的表面粗糙度,来保证零件的质量。
2.4.3合理选择刀具的几何角度
在薄壁零件的铣削中,合理的刀具几何角度对铣削时切削力的大小、铣削中
产生的热变形、工件表面的微观质量都是至关重要的。从工艺学中,我们可以知
道,刀具的几何角度对切削力的影响是很大的。刀具的前角大小决定着切削力变
形与刀具前角的锋利程度。前角大,则切削变形和摩擦力减少,切削力相应减少。
但前角太大,会使刀具的强度降低,刀具散热情况变差且刀具的磨损加快。在铣削
加工中,考虑到粗铣时余量大,为了有利于排屑,故而在粗加工中选择疏齿铣刀,而
精加工时选用密齿铣刀,铣刀刀子齿数越少,表明刀子的容屑槽越大,有利于排屑,
精加工时选用密齿铣刀,有利于提高工件的表面光洁度,而在螺旋角的选择方面来
看,粗加工选择30-45度的螺旋角,而精加工选择45-60的螺旋角。从实际加工我
们可以看到,当吃刀深度一样时,螺旋角为30-45的铣刀参加切削的刃要少,切削力
相应要小,但其表面粗糙度将增大,而45-60的螺旋角铣刀刀刃参加切削的要多,虽
然切削力要稍大,但精加工时余量要小,故而仍可选用45-60的螺旋角,以提高工件
表面光洁度。
2.4.4充分利用切削液
在铣削过程中,由于切削变形和切屑、刀具、工件间的摩擦,产生大量的切削
热,传到刀具上会使刀具的硬度降低,加速刀具的磨损,使工件表面粗糙度值提高,
而传到工件上会使工件产生热变形。切削热的存在,对铣削薄壁零件十分的不利。
在铣削过程中充分适用切削液不仅减少了切削力,提高刀具的耐用度和工件表面
的粗糙度,同时也减少工件受且须热的影响,从而保证了加工零件的尺寸和几何精
度,保证了零件的加工质量。
表2、表3是经过反复实验的粗、精加工切削参数。实践证明,通过选择合理
的装夹方式、刀具、切削进度、进给量、切削深度、螺纹角、夹头等,完全是可
以减少薄壁零件变形的。
附:以上刀具均采用英格硬质合金刀具,冷却液用Rocol Vltracut 370 plus或福
斯ALU-CF,如使用其他刀具或冷却液应相应的调整切削用量。
3 结论
综上所述,工艺规程合理安排再加上合理装夹方式、切削用量和刀具几何角
度的合理选择以及切削液的充分使用是保证薄壁零件的顺利铣削关键。