浅析薄壁零件加工中变形振动分析和消振措施
防止和减少薄壁件变形及振动的方法

防止和减少薄壁件变形及振动的方法
❖ 增加工艺肋
有些薄壁工件在其装夹部位特制几 个工艺肋,以增强此处刚性,使夹 紧力作用在工艺肋上,以减少工件 的变形,加工完毕后,再去掉工艺 肋,如图10-4-5所示。
图10-4-5 增加工艺肋减少变形
防止和减少薄壁件变形及振动的方法
❖ 浇注充分切削液
降低切削温度,减少工件热变形。
❖ 增加弹性心轴安装
胀力心轴胀力心轴依靠材料弹性变形所产生的胀力来固定工件,如图104-4所示。胀力心轴的圆锥角最好为30°左右,最薄部分壁厚6mm。为 了使胀力均匀,槽可做成三等分。长期使用的胀力心轴可用弹簧钢制成。 胀力心轴装卸方便,定心精度高,故应用广泛。
图10-4-4 用弹性胀力心轴装夹工件
❖ 应用轴向夹紧装置
车薄壁工件时,尽量不使用径向夹紧,而优先选用轴向夹紧的方法,如 图10-4-3所示。工件1靠螺母2的端面实现轴向夹紧,由于夹紧力F沿工 件轴向分布,而工件轴向刚度大,不易产生夹紧变形。
图10-4-3 薄壁套的夹紧 a)错误 b)正确 1-工件 2-螺母
防止和减少薄壁件变形及振动的方法
❖ 合理选择刀具的几何参数
精车薄壁工件时,刀柄的刚度要求高,车刀的修光刃不易过长(一般取 0.2~0.3mm),刃口要锋利。 • 外圆精车刀 kr=90°~93°,k`r=15°,αo=14°~16°,αol=15°, γo适当增大。 • 内孔精车刀 kr=60°,k`r=30°,γo=35°,αo=14°~16°, αol=6°~8°,λs=5°~6°。 • 刀尖圆弧半径要小。
防止和减少薄壁件变形及振动的方法
❖ 增加装夹接触面积
采用开缝套筒和特质的软卡爪,使接触面积增大,让夹紧力均布在工件 上,如图10-4-2所示,因而夹紧时工件不易产生变形。
薄壁零件数控加工工艺质量改进方法

薄壁零件数控加工工艺质量改进方法
薄壁零件在数控加工过程中往往面临一系列质量问题,如变形、振动、表面粗糙度等。
为了有效解决这些问题,我们可以采取以下改进方法来提高薄壁零件的加工质量。
首先,选用适当的加工参数是至关重要的。
合理的加工参数能够控制零件变形和振动的发生。
我们应该根据零件材料的特性、加工设备的性能及工件的尺寸来合理选择切削速度、进给速度和切削深度等参数,确保零件在加工过程中能够保持稳定的状态。
其次,合理设计夹具和刀具也是提高薄壁零件加工质量的重要手段。
薄壁零件因其材料薄弱而容易发生变形和振动,因此我们需要设计稳定而牢固的夹具,以确保零件在加工过程中能够始终保持稳定的位置和形状。
同时,选择合适的刀具也能够减少振动和提高表面光洁度。
此外,采用适当的加工策略也能够改善薄壁零件的加工质量。
在进行高速切削时,可以考虑采用多道次深浅切削的方法,避免一次性过深切削造成零件变形。
同时,在切削过程中要注意冷却润滑和切屑处理,以避免因摩擦产生的热量影响零件的加工质量。
最后,进行必要的表面处理也能够改善薄壁零件的加工质量。
通过进行抛光、打磨和喷砂等表面处理,可以增加零件的表面光洁度和光泽度,提高零件的整体美观度。
总而言之,薄壁零件数控加工工艺质量的改进方法包括选用适当的加工参数、合理设计夹具和刀具、采用适当的加工策略以及进行必要的表面处理。
通过综合运用这些方法,我们可以有效地提高薄壁零件的加工质量,满足客户的需求。
薄壁零件加工振动原因及控制

状 复杂 ,刚度较 低 ,加 工时 的余量较 大 ,速 度快 ,容
易发生变 形及振 动 。但 在航空 工业领 域广泛使 用薄 壁 零件 ,主要是 因为其质 量较轻 ,强 度较高 的特 点 。薄 壁零件 的结构特 点是质 量轻 、强度 高 。由于其这样 的
总第8 8 期 2 0 1 5 年第4 期
现 代 工业 经济 和信 息化
M o de r n I ndus t r i a l Ec o nom y a nd I nf o r ma t i on i z a t i on
Tot a l of 88
N o. 4 2 01 5
2 影 响薄 壁 零件 铣 削振 动 的 因素
薄 壁 零 件 铣 削 加 工 中 ,机 床 结 构 参数 、工 艺 参
数 、刀具 参数 等 因素都 会产 生振 动 。 第 一 ,在 加 工 零 件 时 ,机 床 型 号 、 刀具 型号 、 夹 具结 构 以及 定位 固定 方式 都 会 引 起震 动 ;高 速切 削 环境 下 主 轴 及 刀具 系 统 的超 高 速 旋转 ,刀 具 受 到 很 大 的离 心 力 和切 削抗 力 作 用 ,也 会 引起 刀 具 系统 及 机 床 的 振 动 。第 二 ,机 床 的 旋 转 速 度 、进 给 速 度 、背 吃 刀 量 、走 刀方 式 等 加工 工 艺 参数 也 会 引起
作者简介 :徐 磊 ( 1 9 8 3 一 ),男 ,辽 宁铁岭人 ,学士,现就职 于南京机电职业技 术学院,初级职称 ,研 究方 向:机械设计 与
制造。
现 代工 业 经济和 信 息化
・
5 6・
减少薄壁零件产生变形的主要措施

减少薄壁零件产生变形的主要措施薄壁零件在现代制造中可是常客,但说到它们的变形问题,那可真是让人头疼得像一颗老鼠在心里跑。
今天就聊聊,怎么才能有效减少这些变形,让咱的薄壁零件在工厂里乖乖待着,不再像个调皮的小孩。
1. 材料选择很重要1.1 材料性质说到材料,真是不能掉以轻心。
薄壁零件的材料就像是打比赛的运动员,得选对了,才能发挥出最佳状态。
通常,咱们得选那些强度高、韧性好的材料,比如某些铝合金或者高强度钢。
这样一来,就能减少在加工和使用过程中出现的变形情况。
毕竟,强者自有强者的道理嘛。
1.2 材料处理除了选择好材料,后续的处理工艺也不能马虎。
热处理、冷加工这些小细节,都是决定材料最终性能的大功臣。
比如,适当的热处理可以让材料内部的晶体结构更加稳定,变形的几率自然就降低了。
就像咱们吃饭一样,讲究的不是光有好菜,还得看怎么烹饪,才能把味道调到最佳。
2. 设计阶段得用心2.1 设计优化设计环节可是重中之重,咱们可不能草草了事。
薄壁零件的结构设计得合理,才能避免后续的变形问题。
要尽量让受力均匀,避免局部应力集中。
要是设计得不够合理,变形就跟过年一样,年年有余,没完没了。
2.2 加工余量加工余量也得考虑清楚,太少了会让零件受力不均,太多了又浪费材料。
就像做菜,要有点盐,但不能放太多,否则味道就变了。
我们可以在设计时就合理规划一下加工余量,这样才能做到既经济又实用。
3. 加工过程的细节把控3.1 加工工艺咱们进入加工环节,得注意工艺参数的设置。
比如,刀具的选择、切削速度、进给率等,这些都是影响零件加工质量的重要因素。
选择合适的切削工具,不仅可以提高加工效率,还能有效减少变形。
就像选对了鞋子,走路也能轻松许多。
3.2 夹具的使用夹具的使用更是不能忽视!好的夹具能牢牢把住零件,让它在加工过程中不乱跑。
就像是给小孩系好安全带,才能确保他乖乖待在座位上。
如果夹具设计得不合理,零件就容易在加工中发生变形,最后吃亏的可是咱自己。
薄壁零件加工易变形,这里有绝招!
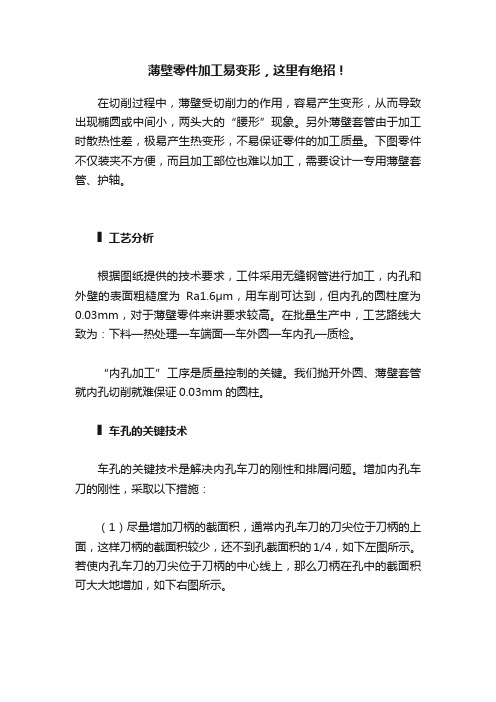
薄壁零件加工易变形,这里有绝招!在切削过程中,薄壁受切削力的作用,容易产生变形,从而导致出现椭圆或中间小,两头大的“腰形”现象。
另外薄壁套管由于加工时散热性差,极易产生热变形,不易保证零件的加工质量。
下图零件不仅装夹不方便,而且加工部位也难以加工,需要设计一专用薄壁套管、护轴。
▌工艺分析根据图纸提供的技术要求,工件采用无缝钢管进行加工,内孔和外壁的表面粗糙度为Ra1.6μm,用车削可达到,但内孔的圆柱度为0.03mm,对于薄壁零件来讲要求较高。
在批量生产中,工艺路线大致为:下料—热处理—车端面—车外圆—车内孔—质检。
“内孔加工”工序是质量控制的关键。
我们抛开外圆、薄壁套管就内孔切削就难保证0.03mm的圆柱。
▌车孔的关键技术车孔的关键技术是解决内孔车刀的刚性和排屑问题。
增加内孔车刀的刚性,采取以下措施:(1)尽量增加刀柄的截面积,通常内孔车刀的刀尖位于刀柄的上面,这样刀柄的截面积较少,还不到孔截面积的1/4,如下左图所示。
若使内孔车刀的刀尖位于刀柄的中心线上,那么刀柄在孔中的截面积可大大地增加,如下右图所示。
(2)刀柄伸出长度尽能做到同加工工件长度长5-8mm,以增加车刀刀柄刚性,减小切削过程中的振动。
▌解决排屑问题主要控制切削流出方向,粗车刀要求切屑流向待加工表面(前排屑),为此采用正刃倾角的内孔车刀,如下图所示。
精车时,要求切屑流向向心倾前排屑(孔心排屑),因此磨刀时要注意切削刃的磨削方向,要向前沿倾圆弧的排屑方法,如下图所示精车刀合金用YA6,目前的M类型,它的抗弯强度、耐磨、冲击韧度以及与钢的抗粘和温度都较好。
刃磨时前角磨以圆以圆弧状角度10-15°,后角根据加工圆弧离壁0.5-0.8mm(刀具底线顺弧度),c切削刃角k向为§0.5-1为沿切屑刃B点修光刃为R1-1.5,副后角磨成7-8°为适,E内刃的A-A点磨成圆向外排屑。
▌加工方法(1)加工前必须要做一件护轴。
薄壁零件变形分析及改进建议

薄壁零件变形分析及改进建议薄壁零件变形分析及改进建议摘要:随着我国社会主义经济的快速发展,各行各业都呈现繁荣景象。
由于薄壁零件具有质量轻、节约材料、结构较为紧密等优良特点,而被广泛应用于机械加工行业。
但是薄壁零件具有口小内大、薄壁、刚性差的缺陷,极易在机械加工过程中发生振动和形变,致使加工过程不能保证加工精度。
通过对薄壁零件进行反复的实验,找出在加工过程中零件发生形变的解决策略。
本文从实际出发,总结和分析了薄壁零件易发生振动和变形的原因,阐述了控制加工过程中薄壁零件发生振动和变形的有效方法,从而保证加工的精度。
关键词:薄壁零件;变形;分析;方法;前言由于薄壁零件具有刚性差、易变形的特点,严重影响了机械加工的精度。
薄壁零件的加工易变形的问题一直是困扰着机械加工行业的主要难题。
为此,许多国内外的专家学者通过反复的实验和验证,建立了多种动态或静态模型,采用先进的有限元技术对加工过程中的刀具和工件进行分析,并依据结论提出了改进加工的有效方法,从而使得薄壁零件的加工工艺有了一些进步。
但在实际生产过程中,我们需要对加工过程中出现的实际变形情况,采用不同的控制措施,以取得较好的生产效率。
影响薄壁零件变形的主要因素在机械加工过程中薄壁零件发生振动和变形的原因多种多样,具有各个方面的影响因素,首先就是在进行零件的设计时,要对零件的结构、工艺性及刚性进行充分的考虑,不断提高薄壁零件的刚性,尽可能的避免加工过程中零件变形,还要保证薄壁零件的对称结构和均一厚度。
在进行零件加工时,选择消除了内应力的毛坯材料。
2.1工件的装夹条件因为薄壁零件具有较差的刚性,在进行加工过程中,如果夹紧力和承受力的作用位置选择不合适,就会增加薄壁零件的内应力;夹、压所产生的弹力极易造成变形,从而影响了零件的表面尺寸、形状和精度,进而导致薄壁零件的变形。
因此,对零件的装夹、定位的合理设计,有助于降低变形的可能性,充分保证加工质量。
2.2加工的残余应力在机械加工过程中,对零件进行加工时会造成刀具与零件的挤压、刀具前刀面和后刀面与已加工表面的挤压、摩擦等作用,从而增加了薄壁零件内部的加工残余应力。
薄壁零件加工中存在的问题

薄壁零件加工中存在的问题在薄壁零件加工中,可能会面临一些常见的问题。
解决这些问题需要仔细分析每个步骤,并采取相应的措施。
以下是一些可能存在的问题和解决建议:1.变形问题:原因:薄壁零件在加工中容易发生变形,主要是由于切削力引起的材料内应力释放。
解决方案:选择合适的切削参数,采用适当的刀具,减小切削力。
可以考虑采用工艺补偿或者后续的校正工序。
2.毛刺和切屑:原因:薄壁零件的切屑很容易残留在切削区域,形成毛刺。
解决方案:采用适当的切削速度和进给速度,选择合适的切削刃具。
可以考虑添加冷却液以减少热影响,避免切削区域积聚切屑。
3.表面质量问题:原因:薄壁零件的加工可能导致表面粗糙度增加或表面平整度降低。
解决方案:使用高精度的加工设备和刀具。
确保刀具磨损良好,避免振动和共振问题。
定期检查和维护设备。
4.工艺稳定性问题:原因:薄壁零件的加工可能受到环境温度、湿度等因素的影响,导致工艺不稳定。
解决方案:控制加工环境的温湿度,采用合适的工艺参数。
在加工之前,对材料和设备进行预热,确保加工过程中的稳定性。
5.材料选择问题:原因:不同的材料对于薄壁零件加工的难度不同。
解决方案:在设计阶段选择适合加工的材料,考虑材料的强度、塑性等特性。
必要时,进行材料热处理以提高加工性能。
6.加工成本问题:原因:薄壁零件的加工可能涉及到高难度的工艺,导致加工成本增加。
解决方案:寻找合适的工艺和设备,优化刀具选择和切削参数,以降低加工成本。
考虑批量生产以提高效益。
通过综合考虑材料、工艺、设备和人员等因素,可以有效解决薄壁零件加工中可能出现的问题,提高加工质量和效率。
铝合金薄壁件加工变形控制
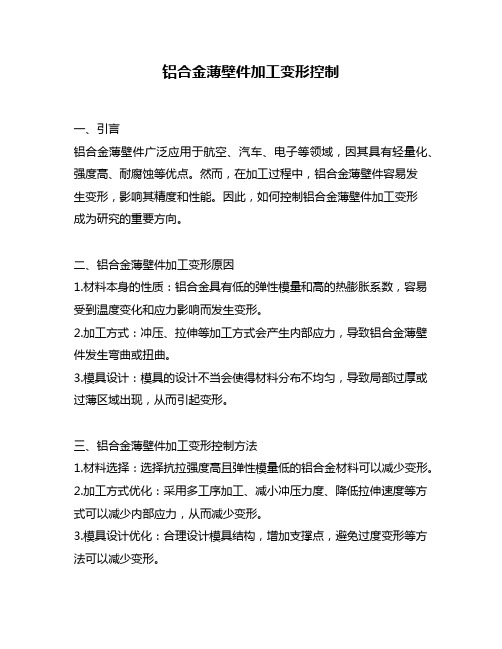
铝合金薄壁件加工变形控制一、引言铝合金薄壁件广泛应用于航空、汽车、电子等领域,因其具有轻量化、强度高、耐腐蚀等优点。
然而,在加工过程中,铝合金薄壁件容易发生变形,影响其精度和性能。
因此,如何控制铝合金薄壁件加工变形成为研究的重要方向。
二、铝合金薄壁件加工变形原因1.材料本身的性质:铝合金具有低的弹性模量和高的热膨胀系数,容易受到温度变化和应力影响而发生变形。
2.加工方式:冲压、拉伸等加工方式会产生内部应力,导致铝合金薄壁件发生弯曲或扭曲。
3.模具设计:模具的设计不当会使得材料分布不均匀,导致局部过厚或过薄区域出现,从而引起变形。
三、铝合金薄壁件加工变形控制方法1.材料选择:选择抗拉强度高且弹性模量低的铝合金材料可以减少变形。
2.加工方式优化:采用多工序加工、减小冲压力度、降低拉伸速度等方式可以减少内部应力,从而减少变形。
3.模具设计优化:合理设计模具结构,增加支撑点,避免过度变形等方法可以减少变形。
四、铝合金薄壁件加工变形控制实践1.材料选择:选择抗拉强度高的6061-T6铝合金材料进行试验。
结果表明,该材料相较于普通铝合金材料能够有效降低变形。
2.加工方式优化:采用多工序加工、缩短冲压时间、降低拉伸速度等方式进行试验。
结果表明,这些方法能够有效减少内部应力和变形。
3.模具设计优化:采用增加支撑点、增加模具刚度等方式进行试验。
结果表明,这些方法能够有效避免过度变形。
五、结论通过以上实践和研究,我们可以得出以下结论:1.选择抗拉强度高且弹性模量低的铝合金材料可以减少变形。
2.采用多工序加工、缩短冲压时间、降低拉伸速度等方式可以减少内部应力和变形。
3.合理设计模具结构,增加支撑点,避免过度变形等方法可以减少变形。
六、展望随着科技的不断进步,铝合金薄壁件加工变形控制的研究将会更加深入。
我们可以通过模拟分析、人工智能等方式来预测和控制铝合金薄壁件的变形,从而进一步提高其精度和性能。
- 1、下载文档前请自行甄别文档内容的完整性,平台不提供额外的编辑、内容补充、找答案等附加服务。
- 2、"仅部分预览"的文档,不可在线预览部分如存在完整性等问题,可反馈申请退款(可完整预览的文档不适用该条件!)。
- 3、如文档侵犯您的权益,请联系客服反馈,我们会尽快为您处理(人工客服工作时间:9:00-18:30)。
薄壁零件加工中
变形振动分析和消振措施
摘要:车削过程中,工艺系统由于受到各种力的作用,工件和刀具之间常会发生相对振动。
它不仅使加工表面产生波纹,严重恶化加工精度和表面质量。
特别是最后一刀精车,当切削速度提高,常常会发生刺耳的响声,使车削无法继续加工下去。
所以,在加工薄壁零件中,不仅要考虑装夹中工件受力变形的问题,还要注意解决加工中振动问题
关键词:薄壁零件加工变形振动措施
车削薄壁零件在加工中很容易出现问题,如果我们在加工中善于总结经验,就能在加工中找出它的共性、个性和矛盾突出点。
变被动为主动。
从而才能够加工出合格的产品。
要想解决薄壁零件加工中出现的问题,我想从以下几个方面来加以分析。
一、薄壁零件装夹分析
1、薄壁零件的加工特点
薄壁零件以日益广泛地应用个工业部门生产机器零件中,车削薄壁零件的关键是变形、振动问题。
工件产生变形振动的原因大多是由于切削力、夹紧力、定位误差和弹性变形。
其中影响最大的是切削力和夹紧力。
我们在实践过程中减小切削力和切削热主要采取方法是:合理地选择切削用量、合理地选择刀具几何角度、减小夹紧力引起的变形,主要改变和改善夹紧力对零件的作用。
2、车削薄壁零件时采用的装夹方式
以上讲的薄壁零件加工特点是车削中变形和振动问题。
由于薄壁零件的刚性差,车削中容易变形。
所以在装夹时要考虑到夹紧力的方向和着力点。
夹紧力的方向应选择在有利于减小夹紧力的部位。
如薄壁零件为套类,则可将径向夹紧力改为轴向夹紧力;薄壁零件为盘类,
则可该轴向夹紧力为径向夹紧力;当薄壁零件径向和轴向刚性都很差时,保证夹紧力方向与切削力方向一致,就能使较小夹紧力起到较大夹紧力的作用。
还要夹紧力着力点应落在支承点正对面和切削力部位的附近以减小变形振动。
二、减小薄壁套装夹中变形的措施
1、合理确定夹紧力的大小、方向、作用点。
粗、精车加工分开,当粗精车加工使用同一夹具时,粗加工余量大,切削力大。
因而需要较大的夹紧力。
而精车时余量小,切削力小,所需要的夹紧力也就小。
1)改变夹紧力的作用方向。
也就是变径向夹紧力为轴向夹紧力。
因为薄壁套轴向承载能力比径向大,在可能的情况下,尽可能是夹紧力与切削力的方向一致。
这样可以减小夹紧力。
2)增大夹紧力的作用面积。
当我们加工薄壁套零件完毕时,卸下来时会发现零件发生变形。
这是由于三爪夹紧力作用于工件受力面积太小而导致的结果。
我们可以把工件小面积上局部受力变为大面积的均匀受力。
就可以大大地减小工件夹紧力变形。
在实际生产过程中,小批量生产我们都采用结构简单容易制作的扇形卡爪,开缝套来增大夹紧力作用面积以减小变形。
另外引起薄壁套零件在加工中除了夹紧力大小影响工件变形以为,我们还要关注在车削过程中,切削力和切削热对零件加工的影响。
影响切削力大小和切削程度高低主要因素是切削用量选择和刀具几何角度选择。
3)切削用量中对切削力影响最大的是背吃刀量。
对切削热影响最大的是切削速度和刀具锋利状况。
因此车削薄壁套零件应减小背吃刀量和适当降低切削速度,同时应适当增大进给量。
4)车刀几何角度中对切削力影响最大的是主偏角、前角和刃倾角。
增大前角使车刀锋利,排屑顺利,减小切屑与前刀面之间的摩擦,减小切削力和切削热。
根据薄壁套轴向承载能力比径向承载能力大的特点。
适当增大主偏角,可以减小背向力,减小工件变形。
刃倾角取正值,使车刀实际前角增大,刃口圆弧减小。
提高刀具锋利程度,从而减小切削力和切削热。
同时还要兼顾副刀刃与工件之间的摩擦,增大副偏角,减小副刀刃和工件之间的摩擦。
但副偏角过大,刀具散热条件差,刀尖容易磨损,应根据实际加工情况而定。
三、减小薄壁套车削振动的措施
我们知道,机械加工中的振动有三种类型,即自由振动、强迫振动和自激振动。
而在这三种类型中,主要是强迫振动和自激振动。
而自激振动约占比例的65%。
因此薄壁套车削中出现振动现象除了要保证薄壁套有足够的夹紧力使工件不变形,还要研究分析和解决加工中出现工件内外圆表面出现规律性振动波纹,产生刺耳的响声。
那么车削薄壁套产生振动响声是什么原因造成的呢?我们经过实践加工过程中,经常在加工刚性较差的轴类和套类时,当切削量中,如果选择切削速度高,背吃量大,进给量小的,就会出现振动现象,发出异常的响声。
当切削速度降低时,吃刀量变小,进给量增大,振动就会自然消失。
由此得出结论,车削中振动现象与合理选择切削用量有关。
实践证明,在任何情况下,都应该尽量避免切除宽而薄的切屑(即在切削深度大和进给量小的情况下切除切屑),实践还证明,当切削速度在每分钟15~20米低速度和每分钟80~100米高速度。
它可以避免自激振动产生。
在中等切削速度每分钟35~50米时,容易自激振动。
车削薄壁工件,因变形而易引起振动,而振动又将加剧工件的变形,两者相互关联。
完全的消除振动甚为困难,但采取必要措施来减小或消除局部振动却是可行的。
(1)调整车床、床鞍、刀架和滑动部位。
如间隙过大,须进行调整,减小间隙使各转动和滑动部位达到最佳状态。
(2)使用吸振材料。
用橡胶片、软橡胶管填充或包裹工件后车削。
当工件旋转时,在离心力的作用下橡胶片将紧贴孔壁,能阻碍减振并防止振动传播。
(3)填充低熔点物质。
通常选用石蜡、低熔点物质。
(4)合理选择刀杆,尽可能增大刀杆截面积,缩短刀杆伸出长度,以增加刀杆刚性,还可以选择弹性刀杆。
(5)合理选择车刀几何参数。
1)选择适当的主偏角。
主偏角过小,切削面积增大。
易产生振动。
车内孔时主偏角不能过大(不能大于90°)否则切削不稳定,易产生振动。
2)增大副偏角可以减小刀刃与工件的接触面,减小摩擦抗力,使切削平稳。
3)前角对振动强度很大,应在前刀面磨出尺槽以增大前角,使刀刃锋利,出屑顺利。
车削薄壁零件发生振动现象,即便是同型号机床,采用完全相同的装夹,选用完全相同的切削量和刀具几何参数,对材料相同,形状相同的零件进行同样切削,其振动程度也可能不一样。
因此在实践过程中,完全要依靠自己摸索掌握,任何书本都不能规定出具体的数值。
因此要求操作者基本功扎实,善于在加工过程中积累经验,勇于摸索。
企图通过加工少许的零件,并在短时间内掌握技术的,是不可能的。
下面以加工薄壁套零件为加工实例。
通过分析,来提高掌握薄壁套的加工方法,从而保证加工质量,提高生产效率。
见下图1
图1 薄壁套零件
一、工件特点分析
从零件图样要求及加工精度来看,加工此零件难度有几点:它的内外圆直径差很小,强度当然就弱。
如果在卡盘上三爪夹紧力过大,
就会使零件变形,造成零件圆度误差这是其一;其二,根据图样要求内孔与外圆有同轴交要求,如果按常规装夹方式很难保证精度的要求,还会发生变形振动,无法加工下去。
二、解决方案
通过以上难点分析,此零件要想在加工中不变形,不振动可以采取两种装夹方法:
第一、采用扇形软卡爪或开缝套筒,将工件小面积上的局部受力变为大面积上的均匀受力。
因为此零件内外圆直径差很小,强度弱,以外圆装夹定位加工内孔。
如用三爪夹紧定位粗车内孔时还不会发生太大变形。
到精车时,内孔尺寸与外圆尺寸直径差很小且容易发生变形,影响尺寸和精度,所以采用扇形软卡爪或开缝套筒就能解决此问题。
第二、内孔精车好以后,采用在车床上加工一个芯轴,以芯轴作为内孔定位基准。
即能保证零件同轴要求,又能很好防止零件变形振动。
因为芯轴作用把径向夹紧转为轴向夹紧,薄套轴向承载能力比径向大,且轴向夹紧力与切削力方向不一致。
这样可以减小轴向夹紧力,使工件不易产生变形。
(见图2所示)
芯轴工件轴向夹紧套压紧螺母
图2
另外,在加工此零件还要充分考虑车削和切削用量选择以及刀具的合理角度,并且在加工过程中加注切削液冷却,保证工件不受热变形。
结束语:薄壁套零件日益在工业部门广泛应用。
如何减少消除加工中的变形振动,保证工件加工精度,一直是困扰我们的一个难题。
我想在今后实践过程中,不管遇到什么样的难加工的薄壁零件,只要
通过实践摸索,善于积累经验,认真总结分析,采取正确装夹方式。
选择合理切削用量和刀具角度,就能变被动为主动,就能加工出合格的产品。
参考文献:
(1)高级车工技能训练中国劳动出版社 1991.6
(2)车工工艺与技能训练中国劳动社会保障出版社 2006.1
(3)徐平田主编机床加工操作禁忌实例中国劳动社会保障出版社 2004.9。