准双曲面锥齿轮传动计算
锥齿轮设计计算

锥齿轮的设计计算
.选择齿轮的资料和精度等级
资料选择查表选用大小齿轮资料均为45号钢调质。
小齿轮齿面硬度为250HBS,大齿轮齿面硬度为220HBS。
250HBS-220HBS=30HBS;切合要求;220<250<350;为软齿面。
齿轮为8级精度。
3. 试选小齿轮齿数=20 = = =70。
二.按齿面接触疲惫强度设计
由齿面接触疲惫强度设计公式
1. 试选载荷系数。
计算小齿轮传达的转矩
=
3.由表选用齿宽系数。
4.确立弹性影响系数据表得。
5.确立地区载荷系数标准直齿圆锥齿轮传动。
6.依据循环次数公式计算应力循环次数
=
查图得接触疲惫寿命系数
查图得排除疲惫极限应力
计算排除疲惫许用应力
取无效概率为1%,安全系数
=540MPa
MPa
由接触强度计算小齿轮的分度圆直径
计算齿轮的圆周速度
计算载荷系数查表得
接触强度载荷系数
按实质的载荷系数校订分度圆直径
取标准m=5.
计算齿轮的有关参数
圆整并确立齿宽三.校核齿根曲折疲惫强度确立曲折强度载荷系数
1.计算当量齿数
查表得
计算曲折疲惫许用应力
由图得弯曲疲劳寿命系数
按脉动循环变应力确立许用应力
校核曲折强度
依据曲折强度条件公式进行校核
知足曲折强度,所选参数适合。
参照资料:
1. 《机械设计手册》第四版化学工业第一版社第3卷成大先主编。
2. 《机械设计同步指导及习题全解》中国矿业大学第一版社
3.。
螺旋双面法加工小模数准双曲面锥齿轮的切齿计算

螺旋双面法加工小模数准双曲面锥齿轮的切齿计算
吕传贵;罗建勤;汪慧君
【期刊名称】《机械传动》
【年(卷),期】2018(42)7
【摘要】利用啮合原理,通过对Gleason双重螺旋运动法的分析,提出了双面法加工小模数准双曲面锥齿轮的切齿计算方法,并推导了相关公式。
经实践,该计算方法为数控铣齿机的双重双面法加工小模数弧齿锥齿轮提供了齿面修形的理论研究基础,具有理论指导意义。
【总页数】5页(P92-95)
【关键词】双重螺旋运动法;切齿计算;准双曲面锥齿轮;齿面修形
【作者】吕传贵;罗建勤;汪慧君
【作者单位】金华新天齿轮有限公司
【正文语种】中文
【中图分类】TH132.421
【相关文献】
1.基于统一转换模型的螺旋锥齿轮和准双曲面齿轮数控加工 [J], 李琳;冯美君
2.任意指定计算点的弧齿锥齿轮与准双曲面齿的切齿... [J], 俞维华;刘福利
3.弧齿锥齿轮和准双曲面齿轮切齿调整计算新方法——按大轮齿面任一基准点配切小轮的原理 [J], 董学朱
4.产形线切齿法加工准双曲面齿轮的产形线建模及代用方法 [J], 李栎楠;杨兆军;王
彦鹍;张学成
5.螺旋锥齿轮和准双曲面齿轮的端面滚齿法 [J], 曾韬;吕传贵
因版权原因,仅展示原文概要,查看原文内容请购买。
最新锥齿轮的设计计算知识讲解

锥齿轮的设计计算一. 选择齿轮的材料和精度等级1.材料选择查表选取大小齿轮材料均为45号钢调质。
小齿轮齿面硬度为250HBS,大齿轮齿面硬度为220HBS。
250HBS-220HBS=30HBS;符合要求;220<250<350;为软齿面。
2.齿轮为8级精度。
3.试选小齿轮齿数=20 ==3.520=70。
二.按齿面接触疲劳强度设计由齿面接触疲劳强度设计公式1.试选载荷系数。
2.计算小齿轮传递的转矩=26527.78 N.MM3.由表选取齿宽系数。
4.确定弹性影响系数据表得。
5.确定区域载荷系数标准直齿圆锥齿轮传动。
6.根据循环次数公式计算应力循环次数=7.查图得接触疲劳寿命系数8.查图得解除疲劳极限应力9.计算解除疲劳许用应力取失效概率为1%,安全系数=540MPaMPa10.由接触强度计算小齿轮的分度圆直径11.计算齿轮的圆周速度12.计算载荷系数查表得接触强度载荷系数13.按实际的载荷系数校正分度圆直径取标准m=5.14.计算齿轮的相关参数15.圆整并确定齿宽三.校核齿根弯曲疲劳强度1.确定弯曲强度载荷系数2.计算当量齿数3.查表得4.计算弯曲疲劳许用应力由图得弯曲疲劳寿命系数按脉动循环变应力确定许用应力4.校核弯曲强度根据弯曲强度条件公式进行校核满足弯曲强度,所选参数合适。
参考资料:1.《机械设计手册》第四版化学工业出版社第3卷成大先主编。
2.《机械设计同步辅导及习题全解》中国矿业大学出版社3.百度文库UI设计师试卷试卷编号:(182) 试题总分:150分-----------------------------------------------------------------------单选题共20题:(60分,每小题3分)1. 题干:UI设计是什么意思?(A)A:User Interface的缩写,是指用户界面设计B:User Identity的缩写,是指用户识别设计C:User Ideal的缩写,是指用户目标设计D:UserIntention的缩写,是指用户意图设计2. 题干:网页设计中的网页界面栅格化是指(C)A:使用ps设计网页界面过程中,将所有的层都格式化图层B:在页面制作时,将所有的层宽度统一C:栅格系统英文为“grid systems”,是从平面栅格系统中发展而来,以规则的网格阵列来指导和规范网页中的版面布局以及信息分布。
准双曲面齿轮的设计 ppt
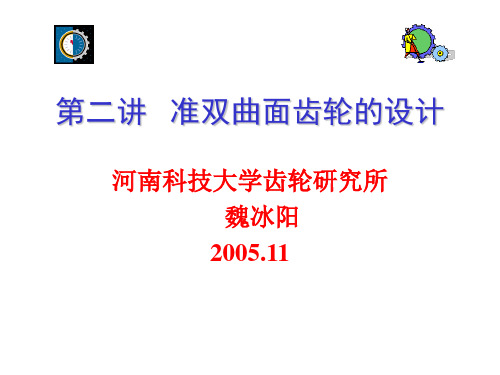
准双曲面齿轮
弧齿锥齿轮
图 2.1 准双曲面齿轮与弧齿锥齿轮对比
同等条件下准双曲面小轮比弧齿锥齿轮小 轮大得多。
2. 准双曲面齿轮概述
优点: 优点: 3) 比弧齿锥齿轮传动的重叠系数更大,传 动更加平稳,而且齿面所受的正压力小。 4) 轴线位置的偏置,使传动在空间的布置 具有了更大的自由度。如下偏可以用于降 低汽车的重心增加平稳性;也可以用来增 加车身的高度,增加汽车的越野性。
小 相 等 、符 号 相 反 。为 了 使 极 限 曲 率 半 径 符 合 标 准 刀 盘 尺 寸 ,可 以 改 变 原 设 的 大 轮 偏 置 角 ε值 。
5.准双曲面齿轮的设计过程
• 如果螺旋角不满足要求,通过改变r1 如果螺旋角不满足要求,通过改变r 来满足 • 如果极限曲率半径不符合标准刀盘 尺寸,通过改变小轮轴截面偏置角η 尺寸,通过改变小轮轴截面偏置角η 来满足 • 过程通常由计算机叠代完成
cos β 2 R1 sin δ 1 z2 r1 z2 = × = × cos β1 R2 sin δ 2 z1 r2 z1
r1 、r2 确定之后,不同的螺 旋角可以适应不同的传动比, 因此对于给定的传动比准双 曲面齿轮的节锥并不唯一, 轮齿法线可以在任意方向垂 直于轮齿切线,因此压力角 可以自由选取。
E tgη1 = ' ' r2 (tgδ2 sinΣ + cosΣ) + r1
给定大轮刀盘半径 r0=d2/(2sinδ2’)
三.准双曲面齿轮的初始参数的选取
•齿坯设计需输入的初始参数
1. 齿数的选取
• 对于准双曲面齿轮,虽然齿数可任意选定,但在一 般情况下,小轮的齿数不得小于5,小轮与大轮的 齿数和应不小于40,且大轮齿数应与小轮齿数之间 避免有公约数。表2.1为格里森推荐的不同传动比 下小轮的最少齿数。若是设计汽车用的准双曲面齿 轮,则小轮齿数可以选得较小。对于格里森调整卡 和计算程序都作了以上限制,突破上述范围将不能 进行设计计算。也有突破以上齿数限制设计的方法, 比如“非零变位”设计,小轮齿数可小到2~3齿的。
锥齿轮的计算 校核
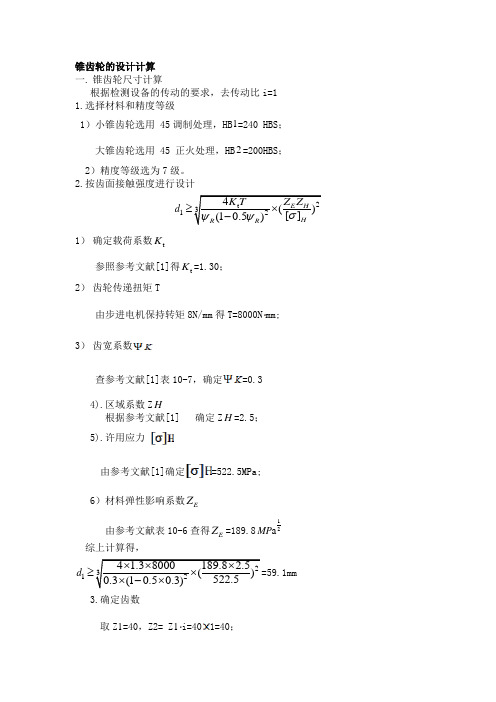
锥齿轮的设计计算一. 锥齿轮尺寸计算根据检测设备的传动的要求,去传动比i=11.选择材料和精度等级1)小锥齿轮选用 45调制处理,HB 1=240 HBS ; 大锥齿轮选用 45 正火处理,HB 2=200HBS ;2)精度等级选为7级。
2.按齿面接触强度进行设计 2t 3124()[](10.5)E H HR R d Z Z K T σψψ≥⨯- 1) 确定载荷系数t K参照参考文献[1]得t K =1.30;2) 齿轮传递扭矩T由步进电机保持转矩8N/mm 得T=8000N mm;3) 齿宽系数查参考文献[1]表10-7,确定=0.3 4).区域系数Z H根据参考文献[1] 确定Z H =2.5;5).许用应力由参考文献[1]确定=522.5MPa; 6)材料弹性影响系数E Z由参考文献表10-6查得E Z =189.812a MP 综上计算得, 23124 1.38000189.8 2.5()522.50.3(10.50.3)d ⨯⨯⨯≥⨯⨯-⨯=59.1mm 3.确定齿数取Z 1=40,Z2= Z 1i=401=40;4.选大端模数m= d 1/Z 1=59.1/40=1.48圆整取m=2 ;5.计算分度圆锥角锥距 11240=arctan arctan 4540Z Z δ==21=90904545δδ-=-= 121mZ 1()56.572Z R mm Z =+=6.计算大端分度圆直径121d =d =m Z 24080mm ⨯=⨯= 7.确定齿宽=0.356.57=16.9R b R ψ=⋅⨯ b 1= b2=11 mm二. 齿根弯曲疲劳强度校核a 222214(10.5)u 1a F F S R R KT Y Y Z m σψψ=⋅⋅-+1. 查参考文献[1]10-5得 a F Y =2.4,a S Y =1.67 查阅参考文献[1]得[]=390 MPa;2.计算得 22224 1.38000 2.4 1.570.3(10.50.3)40211F σ⨯⨯=⨯⨯-⨯⨯⨯+ =79.9<[]=390 MPa;故所选齿轮满足齿根弯曲疲劳强度要求。
锥齿轮传动设计

锥齿轮传动设计一、引言锥齿轮传动是一种广泛应用于各种机械传动中的一种传动方式。
其主要特点是具有较高的承载能力、传递效率高、工作平稳等优点。
在设计锥齿轮传动时,需要考虑多方面因素,包括输入输出功率、转速比、载荷类型和大小等因素。
本文将从锥齿轮传动的基本原理、设计方法以及常见问题解决方法等方面进行详细介绍。
二、锥齿轮传动的基本原理1. 锥齿轮传动的结构锥齿轮传动由两个相交的圆锥形齿轮组成,分别为主动齿轮和从动齿轮。
主动齿轮通常为小端直径较小的圆锥形,从动齿轮通常为大端直径较大的圆锥形。
2. 锥齿轮传动的工作原理当主动齿轮旋转时,其直径较小的小端将驱使从动齿轮转动。
由于两个圆锥形齿轮之间产生了相对运动,因此在接触线上产生了滚切运动。
这种滚切运动可以保证齿轮之间的接触面积均匀分布,从而使得传动效率提高。
三、锥齿轮传动的设计方法1. 锥齿轮传动的参数计算在进行锥齿轮传动设计时,需要计算出一系列参数,包括模数、压力角、齿数、分度圆直径等。
具体计算方法可以参考国家标准GB/T 10095-2008《锥齿轮》。
2. 锥齿轮传动的选型在进行锥齿轮传动选型时,需要考虑多方面因素,包括输入输出功率、转速比、载荷类型和大小等因素。
通常可以根据输入输出功率和转速比来确定合适的模数和齿数范围,在此基础上进行具体选型。
3. 锥齿轮传动的结构设计在进行锥齿轮传动结构设计时,需要考虑多方面因素,包括主动从动端的位置关系、两个圆锥形齿轮之间的啮合角度等因素。
通常可以采用CAD软件进行三维建模和仿真分析,以确保结构设计合理可靠。
四、常见问题解决方法1. 锥齿轮传动噪声问题锥齿轮传动在运行时会产生一定的噪声,主要原因是由于啮合面的滑动和滚动摩擦所引起的。
为了解决这一问题,可以采用降低齿轮间啮合角度、改善齿形等方法。
2. 锥齿轮传动润滑问题锥齿轮传动在运行时需要进行润滑以减少磨损和摩擦。
通常可以采用油浸式润滑或者油雾润滑等方法。
在选择润滑方式时需要考虑输入输出功率、转速比和工作环境等因素。
锥齿轮的设计计算

锥齿轮的设计计算一.选择齿轮的材料和精度等级1.材料选择查表选取大小齿轮材料均为45号钢调质。
小齿轮齿面硬度为250HBS,大齿轮齿面硬度为220HBS。
250HBS-220HBS=30HBS;符合要求;220<250<350;为软齿面。
2.齿轮为8级精度。
3.试选小齿轮齿数=20 ==3.520=70。
二.按齿面接触疲劳强度设计由齿面接触疲劳强度设计公式1.试选载荷系数。
2.计算小齿轮传递的转矩=26527.78 N.MM3.由表选取齿宽系数。
4.确定弹性影响系数据表得。
5.确定区域载荷系数标准直齿圆锥齿轮传动。
6.根据循环次数公式计算应力循环次数=7.查图得接触疲劳寿命系数8.查图得解除疲劳极限应力9.计算解除疲劳许用应力取失效概率为1%,安全系数=540MPaMPa10.由接触强度计算小齿轮的分度圆直径11.计算齿轮的圆周速度12.计算载荷系数查表得接触强度载荷系数13.按实际的载荷系数校正分度圆直径取标准m=5.14.计算齿轮的相关参数15.圆整并确定齿宽三.校核齿根弯曲疲劳强度1.确定弯曲强度载荷系数2.计算当量齿数3.查表得4.计算弯曲疲劳许用应力由图得弯曲疲劳寿命系数按脉动循环变应力确定许用应力4.校核弯曲强度根据弯曲强度条件公式进行校核满足弯曲强度,所选参数合适。
参考资料:1.《机械设计手册》第四版化学工业出版社第3卷成大先主编。
2.《机械设计同步辅导及习题全解》中国矿业大学出版社3.百度文库Welcome To Download !!!欢迎您的下载,资料仅供参考!。
齿轮传动的设计计算

齿轮传动的设计计算
齿轮传动的设计计算通常涉及以下几个方面:
1. 齿轮尺寸计算:首先需要确定主动轮和从动轮的模数(齿轮的模数是齿轮齿数与齿轮直径的比值),根据传动比和齿数关系,计算主动轮和从动轮的齿数。
然后根据齿轮的模数和齿数,计算出齿轮的分度圆直径、齿顶圆直径和齿根圆直径。
2. 传动比计算:根据所需的输入转速和输出转速,计算传动比。
传动比可以通过齿轮齿数之比来确定。
3. 齿轮强度计算:根据传动功率和转速,计算齿轮的弯曲强度和接触强度。
弯曲强度是指齿轮在承受力矩时的抗弯能力,接触强度是指齿轮齿面在传递力矩时的抗磨损能力。
根据齿轮材料的强度参数和几何参数,使用相应的公式计算弯曲强度和接触强度,并与所需的传动功率和转速进行比较,确保齿轮能够满足设计要求。
4. 齿轮齿形计算:根据齿轮的模数、齿数和压力角,计算齿轮的齿形。
齿形计算包括计算齿顶高度、齿根高度、齿根圆曲率半径等参数。
通过合理选择这些参数,可以确保齿轮传动的平稳运行和高效传动。
5. 齿轮轴的计算:根据齿轮的传动功率和转速,计算齿轮轴的强度。
齿轮轴的强度计算涉及到材料的抗弯强度和抗剪强度,并考虑到齿轮轴的几何参数。
以上是齿轮传动设计计算的一般步骤,具体的计算方法和公式可能会根据不同的设计要求和标准有所差异。
在实际的工程设计中,通
常需要参考相关的齿轮设计手册或使用专业的齿轮设计软件来完成计算。
- 1、下载文档前请自行甄别文档内容的完整性,平台不提供额外的编辑、内容补充、找答案等附加服务。
- 2、"仅部分预览"的文档,不可在线预览部分如存在完整性等问题,可反馈申请退款(可完整预览的文档不适用该条件!)。
- 3、如文档侵犯您的权益,请联系客服反馈,我们会尽快为您处理(人工客服工作时间:9:00-18:30)。
准双曲面锥齿轮传动计算 1 小轮齿数Z1:6.00000000 2 大轮齿数Z2:38.00000000 3 齿数比的倒数Z1/Z2:0.15789474 4 大轮齿面宽b2:62.00000000 5 偏置距E:35.00000000 6 大轮节圆直径de2:384.94000000 7 刀盘名义半径rb:152.40000000 8 初选小轮螺旋角βm1c:35.00000000 9 βm1c正切值tanβm1c:0.70020754 10 初选大轮节锥角之余切值cotδ2c:0.18947368 11 δ2c之正弦值sinδ2c:0.98251915 12 初定大轮中点分圆半径rm2c:162.01190624 13 大、小轮螺旋角差角正弦值sinΔβc:0.21225706 14 Δβc之余弦值cosΔβc:0.97721387 15 初定小轮扩大系数Kc:1.12583786 16 小轮中点分度圆半径换算值rm1H:25.58082730 17 初定小轮中点分圆半径rm1c:28.79986382 18 轮齿收缩系数H:1.18000000 19 近似计算公法线K1K2在大轮轴线上的投影(截距)Q:883.86270231 20 大轮轴线在小轮回转平面内偏置角正切tan纾?0.03942507 21 偏置角余割sec纾?1.00077687 22 偏置角正弦sin纾?0.03939447 23 大轮轴线在小轮回转平面内偏置角纾?2.25772108 24 初算大轮回转平面内偏置角正弦sin錭:0.20903059 25 an錭:0.21375258 26 初算小轮节锥角正切tan?1c:0.18429939 27 ?1c角余弦cos?1c:0.98343761 28 第一次校正螺旋角差值拟'的正弦sin拟':0.21255094 29 拟'角余弦cos拟':0.97714999 30 第一次校正小轮螺旋角正切tan?'m1:0.69953993 31 扩大系数的修正量腒:0.00014190 32 大轮扩大系数修正量的换算值腒H:0.00002241 33 校正后大轮偏置角的正弦值sin澹?0.20902971 34 an澹?0.21375163 35 校正后小轮节锥角正切tan洌?0.18430020 36 小轮节锥角?1:10.44244478 37 ?1角的余弦cos?1:0.98343747 38 第二次校正后的螺旋角差值的正弦sin拟:0.21255008 39 拟值拟:12.27183520 40 拟余弦cos拟:0.97715018 41 第二次校正后小轮螺旋角的正切值tan鈓1:0.70020951 42 小轮中点螺旋角鈓1:35.00007567 43 鈓1余弦cos鈓1:0.81915129 44 大轮中点螺旋角鈓2:22.72824047 45 鈓2余弦cos鈓2:0.92234777 46 鈓2正切tan鈓2:0.41888832 47 大轮节锥角余切cot?2:0.18860991 48 大轮节锥角?2:79.31892387 49 ?2正弦sin?2:0.98267407 50 ?2余弦cos?2:0.18534206 51 B1c:29.28858679 52 B2c:874.12378276 53 两背锥之和B12:903.41236955 54 大轮锥距在螺旋线中点切线方向投影T2:152.06600583 55 小轮锥距在螺旋线中点切线方向投影T1:130.17773758 56 极限齿形角正切负值-tana0:0.03038813 57 极限齿形角负值-a0:1.74057618 58 腶0的余弦cos腶0:0.99953860 59 B59:0.00072650 60 B60:0.00001456 61 B61:19,795.60860062 62 B62:0.00110571 63 B63:0.00184677 64 B64:152.33128390 65 齿线中点曲率半径r'0:152.40160197 66 比较r'0与rb比值V:0.99998949 67 A67:0.02926454 68 A68:158.43361730 69 A69:1.01203332 70 rm2圆心至轴线交叉点距离Am2:28.78113466 71 大轮节锥顶点至小轮轴线的距离A02,正数表示节锥顶点越过了小齿轮的轴线,负值表示节锥顶点在大轮与轴线之间:1.77591592 72 大轮节锥上中点锥距Rm2:164.86840541 73 大轮节锥上外锥距(节锥距)R2:195.86351847 74 大轮节锥上齿宽之半0.5bm:30.99511305 75 大轮在平均锥距上工作齿高h'm:13.76341107 76 A76:0.44530771 77 A77:0.62009744 78 两侧压力角总和ac:20.00000000 79 ac角正弦值sinac:0.34202014 80 平均压力角a:10.00000000 81 a角余弦cosa:0.98480775 82 a角正弦tana:0.17632698 83 A83:3.51674737 84 齿顶角与齿根角总和栌:16.28809306 85 大轮齿顶高系数ha*2:0.11000000 86 大轮齿根高系数hf*2:1.04000000 87 大轮中点齿顶高ham2:1.51397522 88 大轮中点齿根高hfm2:14.36394751 89 大轮齿顶角鑑2:0.52612841 90 鑑2角正弦sin鑑2:0.00918254 91 大轮齿根角鑖2:4.97924801 92 鑖2角正弦sin鑖2:0.08679492 93 大轮大端齿顶高hae2:1.79858921 94 大轮大端齿根高hfe2:17.05416602 95 径向间隙c:2.11451166 96 大轮大端齿全高he2:18.85275523 97 大轮大端工作齿高h'e2:16.73824356 98 大轮顶锥角(面锥角)鋋2:79.84505228 99 鋋2角正弦sin鋋2:0.98433455 100 鋋2角余弦cos鋋2:0.17631080 101 大轮根锥角鋐2:74.33967586 102 鋐2角正弦sin鋐2:0.96287890 103 鋐2角余弦cos鋐2:0.26993374 104 鋐2角余切cot鋐2:0.28034028 105 大轮大端齿顶圆直径dae2:385.60670847 106 大端节圆中心至轴线交叉点距离Akm2:34.52583289 107 大轮轮冠至轴线交叉点距离Ake2:32.75840593 108 大端顶圆齿顶与节圆处齿高之差膆am:-0.00006485 109 大端节圆处与根圆处齿高之差膆mf:-0.05629646 110 大轮面锥顶点到小轮轴线的距离Aoa2(参考71):1.77598076 111 大轮根锥顶点到小轮轴线的距离Aof2(参考71):1.71961946 112 A112:170.08041764 113 修正后小轮轴线在大轮回转平面内的偏置角正弦sin澹?0.20578501 114 偏置角余弦cos澹?0.97859723 115 偏置角正切tan澹?0.21028570 116 小轮顶锥角正弦sin鋋1:0.26415641 117 小轮顶锥角(面锥角)鋋1:15.31683263 118 顶锥角余弦cos鋋1:0.96447985 119 顶锥角正切tan鋋1:0.27388484 120 A120:13.96749042 121 小轮顶锥顶点到轴线交叉点的距离Aoa1(参考71):-6.91297194 122 A122:0.00614622 123 A123:0.35214803 124 A124:11.91968716 125 A125:4.87438786 126 A126:-0.00795509 127 A127:1.02201778 128 A128:158.70802187 129 A129:0.96798067 130 A130:31.67755676 131 小轮轮冠到轴线交叉点的距离Ake1:189.26179545 132 :31.68754585 133 小轮前轮冠到轴线交叉点的距离Aki1:123.15540512 134 :182.34882351 135 小轮大端齿顶圆直径dae1:99.88515678 136 :167.16708946 137 在大轮回转平面内偏置角正弦sin澹?0.20937135 138 偏置角澹?12.08551458 139 偏置角余弦cos澹?0.97783620 140 :21.90830528 141 小轮根锥顶点到轴线交叉点的距离Aof1(参考71):-14.91078756 142 :0.17240309 143 小轮根锥角鋐1:9.92756899 144 cos鋐1:0.98502649 145 tan鋐1:0.17502381 146 允许的最小侧隙jnmin:0.20320000 147 允许的最大侧隙jnmax:0.27940000 148 :0.09597747 149 :12.90215216 150 大轮内锥距Ri:133.86351847