釉料成分与色料系统的匹配性
釉料配制注意事项
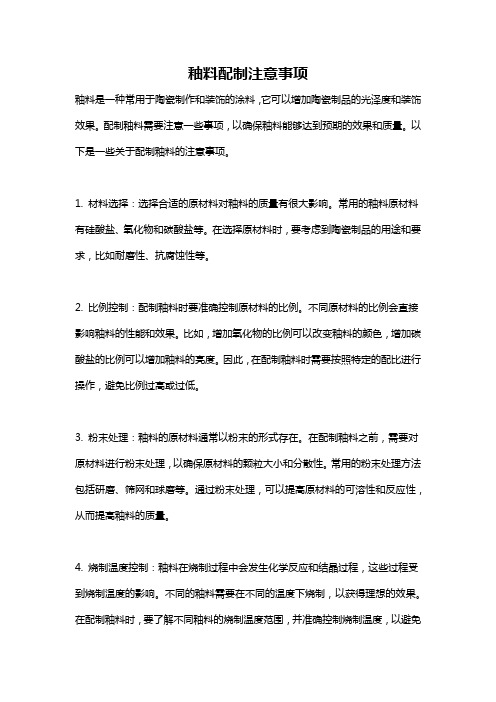
釉料配制注意事项釉料是一种常用于陶瓷制作和装饰的涂料,它可以增加陶瓷制品的光泽度和装饰效果。
配制釉料需要注意一些事项,以确保釉料能够达到预期的效果和质量。
以下是一些关于配制釉料的注意事项。
1. 材料选择:选择合适的原材料对釉料的质量有很大影响。
常用的釉料原材料有硅酸盐、氧化物和碳酸盐等。
在选择原材料时,要考虑到陶瓷制品的用途和要求,比如耐磨性、抗腐蚀性等。
2. 比例控制:配制釉料时要准确控制原材料的比例。
不同原材料的比例会直接影响釉料的性能和效果。
比如,增加氧化物的比例可以改变釉料的颜色,增加碳酸盐的比例可以增加釉料的亮度。
因此,在配制釉料时需要按照特定的配比进行操作,避免比例过高或过低。
3. 粉末处理:釉料的原材料通常以粉末的形式存在。
在配制釉料之前,需要对原材料进行粉末处理,以确保原材料的颗粒大小和分散性。
常用的粉末处理方法包括研磨、筛网和球磨等。
通过粉末处理,可以提高原材料的可溶性和反应性,从而提高釉料的质量。
4. 烧制温度控制:釉料在烧制过程中会发生化学反应和结晶过程,这些过程受到烧制温度的影响。
不同的釉料需要在不同的温度下烧制,以获得理想的效果。
在配制釉料时,要了解不同釉料的烧制温度范围,并准确控制烧制温度,以避免釉料过烧或未烧结的情况发生。
5. 试验和调整:配制釉料是一个复杂的过程,很难一次就达到理想的效果。
因此,需要进行多次试验和调整,以确定最佳的配方和工艺参数。
在试验过程中,可以根据实际情况对配方进行微调,调整比例和温度等参数,以获得更好的结果。
6. 健康安全:在配制釉料时,需要采取适当的健康安全措施,以避免对人体造成伤害。
一些釉料原材料可能含有有害物质,如重金属等。
在操作过程中,应佩戴防护装备,如手套和口罩,确保人员的健康和安全。
7. 储存和保存:配制好的釉料可以保存一段时间,但需要采取适当的措施防止其变质。
釉料应储存在干燥、通风和不受阳光直射的地方。
同时,应密封好容器,并避免暴露在空气中。
陶瓷釉料成分对色泽影响
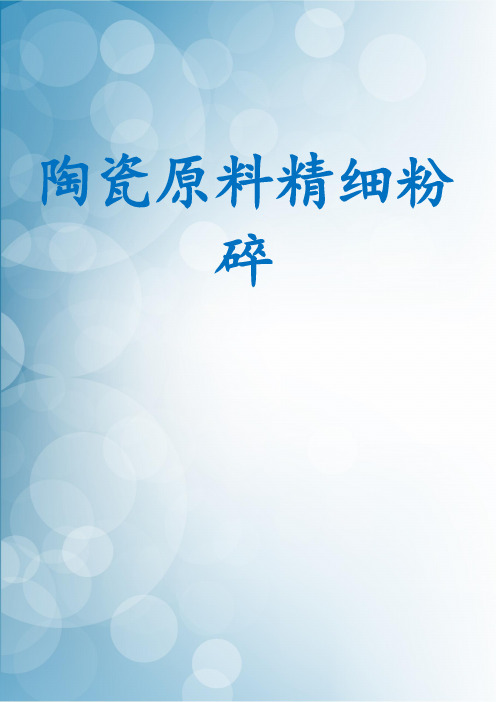
陶瓷原料精细粉碎陶瓷原料精细粉碎陶瓷原料精细粉碎是制作高质量陶瓷产品的重要工艺环节。
在陶瓷生产过程中,原料的粒度和细度对于产品的质量和性能有着直接的影响。
因此,通过精细粉碎技术,将陶瓷原料研磨至所需的粒度,能够提高陶瓷产品的致密性、硬度和强度,从而增加产品的使用寿命。
陶瓷原料通常是由天然矿石经过选矿、破碎、磨矿等过程得到的。
然而,这些原料中的颗粒往往较大,不利于后续的成型和烧结。
因此,需要对原料进行精细粉碎,以获得较细的颗粒。
精细粉碎主要通过研磨机来实现。
研磨机采用高速旋转的研磨介质,将原料颗粒与介质进行摩擦、撞击和剪切,使其逐渐破碎和细化。
研磨介质可以是钢球、陶瓷球、研磨棒等。
在研磨过程中,通过调整研磨介质的大小和比例,控制研磨时间和速度,可以实现对原料颗粒的精细粉碎。
精细粉碎的好处不仅在于改善陶瓷产品的性能,还可以提高产品的加工效率和产量。
首先,精细粉碎可以增加原料的比表面积,使其更易于与其他组分混合和反应,从而提高产品的均匀性和稳定性。
其次,精细粉碎可以减少原料的烧结温度和时间,节约能源和降低生产成本。
此外,精细粉碎还可以减少产品中的孔隙和缺陷,提高陶瓷的密度和抗压强度,增加产品的使用寿命。
然而,精细粉碎也面临着一些挑战和问题。
首先,研磨过程中会产生大量的热量和摩擦,可能引起原料的结块和变质,影响产品的质量。
其次,研磨过程中还会产生大量的粉尘和噪音,对环境和工人的健康造成影响。
此外,研磨机的运行和维护成本也比较高,需要定期检修和更换磨损部件。
综上所述,陶瓷原料精细粉碎是陶瓷生产中不可或缺的工艺环节。
通过精细粉碎,可以改善陶瓷产品的质量和性能,提高生产效率和产量。
然而,精细粉碎也存在一些难题和挑战,需要在实践中不断探索和改进。
瓷砖生料釉的调试

瓷砖生料釉的调试摘要:本文叙述了陶瓷砖生料釉的调试基础入门,列举了调试生料釉的常用原料的化学属性,釉料配方构架体系及配方性能的调试方法。
关健词:生料釉;原料;热膨胀系数值;构架1 引言釉料是陶瓷坯体的外衣,如果说人的外表需要靠衣服装扮,那么釉料就可以看成是装扮陶瓷坯体的衣服,人根据身体高矮胖瘦以及审美观来挑选合适的衣服,陶瓷坯体则依据膨胀系数表面质感等来进行配方的调试选择,如何调试出一个科学合理的配方,那就需要对釉用原材料、配方构架等理论知识有相当的掌握。
本文围绕原料、配方构架简单谈谈对于生料釉的调试方法。
2 生料釉概念生料釉是指釉用的全部原料都不经过预选熔制,直接加水研磨加工调制而成浆料。
生料釉由不溶于水的原料所组成,制备工艺过程与坯料基本相同,一般是先将洗选好的硬质原料粉碎,再与精选的粘土原料配合进行湿法球磨,磨细的釉浆,须经除铁、过筛、陈腐,方可使用。
3 生料釉釉用常见原料与分类3.1 主熔剂类原料钾长石:K2O·Al2O3·6SiO2,碱金属和碱土金属的铝硅酸盐,主熔剂长石族中最常见的一种长石。
钾长石熔点约在1130 ~ 1450℃开始分解熔融,粘度较大,由于钾长石矿常常伴生钠长石,故钾长石中或多或少含钠成分,而钠含量越高则该钾长石熔点越低,越易熔融;钾长石烧成范围较钠长石宽;钾长石在喷墨发色中利红色;K2O 的热膨胀系数值为 8.5,属膨胀系数较大的矿物,依此可调节釉料的膨胀系数。
钠长石:Na2O·Al2O3·6SiO2,碱金属和碱土金属的铝硅酸盐,主熔剂长石族中最常见的一种长石。
钠长石是常用低温熔剂,助熔效果比钾长石好,烧成范围比钾长石窄;钠长石在喷墨发色中利黄色;Na2O 的热膨胀系数值为10.0,膨胀系数值比钾长石大,据此可用来调节釉料的膨胀系数。
锂长石或叫锂辉石:Li2O·Al2O3·4SiO2,碱金属和碱土金属的铝硅酸盐。
第六章 陶艺制品所用色料和釉料
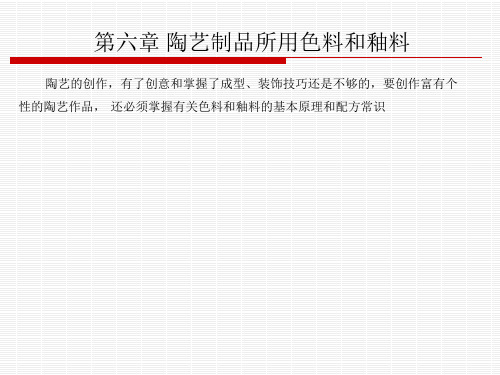
制而成,因颜料在釉的下面,故称为釉下彩
1.釉下彩的配方:
。
第一节 陶艺制品所用色料
2.釉下彩的常用类: (1) 青花:主要是以氧化钴做呈色剂,用茶叶水调配,经高温烧制呈现蓝色。 (图133A图133B)(明 青花瓷) (2) 釉里红:以氧化铜做呈色剂,用桃胶水或清水调配,经高温烧制呈现红色。(图134A图134B)
(2) 如何提高釉的温度:增加石英土(瓷土、陶土等)。减少助熔剂。
7 釉的研磨 将配制好的原料放进磨釉机研磨过筛(筛网80目)即可。
第二节 陶艺制品所用釉料
(二)常见的釉料
1常见的色釉有:
白釉、黑釉、青釉、龙泉釉、茶叶末釉、铜红釉、钧窑釉(花釉)、铜绿釉、土耳 其蓝釉、金砂釉、开片(裂纹)釉、结晶釉、黑天目釉、树叶天目釉,铁红釉、条痕釉、
(图139A、B)
(2) 结晶釉料:分为低、中、高温釉,由两种以上显色能力和结晶特点不相溶的 金属氧化物和熔块配制而成.烧造前不能分辨结晶和色彩,在不同窑炉和不同烧造气
氛下呈现不同的颜色和结晶效果。低温釉烧成温度在1100℃左右,中温釉烧成温度在
1200℃左右,高温釉烧成温度在l350℃左右。(图140A、B)
(1) 降低釉的温度:在釉料中减少泥料比例,增加碳酸钙,氧化锌、碳酸钡、氧
化镁、氧化铅等助熔剂的比例,即可降低釉的烧结温度。 (2) 提高釉的温度:在釉料中增加泥料、硅、铝的比例,减少助熔剂的比例,即 可提高釉的烧结温度。 (与坯体烧成相适应,但要注意膨胀系数,防止破裂)
第二节 陶艺制品所用釉料
5 一般陶艺的釉料烧成温度可分为: 低温釉——1000℃以下。中温釉——1000℃一l260℃。高温釉——1260℃以上。 烧成火焰可分 还原烧——烧成时“缺氧”烧成。氧化烧——烧成时“多氧”烧成。 6 釉的配置基本原则 (1) 如何降低釉的温度:减少石英土(瓷土、陶土等)。 增加助熔剂(如碳酸钙、氧化锌、碳酸钡、氧化镁等)。
彩釉
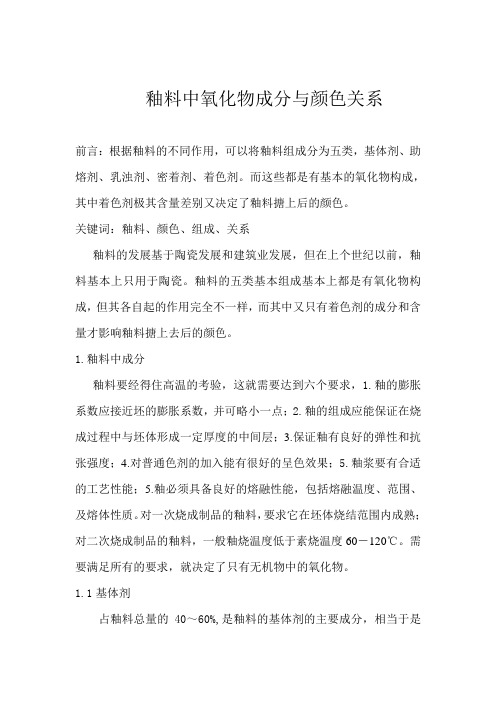
釉料中氧化物成分与颜色关系前言:根据釉料的不同作用,可以将釉料组成分为五类,基体剂、助熔剂、乳浊剂、密着剂、着色剂。
而这些都是有基本的氧化物构成,其中着色剂极其含量差别又决定了釉料搪上后的颜色。
关键词:釉料、颜色、组成、关系釉料的发展基于陶瓷发展和建筑业发展,但在上个世纪以前,釉料基本上只用于陶瓷。
釉料的五类基本组成基本上都是有氧化物构成,但其各自起的作用完全不一样,而其中又只有着色剂的成分和含量才影响釉料搪上去后的颜色。
1.釉料中成分釉料要经得住高温的考验,这就需要达到六个要求,1.釉的膨胀系数应接近坯的膨胀系数,并可略小一点;2.釉的组成应能保证在烧成过程中与坯体形成一定厚度的中间层;3.保证釉有良好的弹性和抗张强度;4.对普通色剂的加入能有很好的呈色效果;5.釉浆要有合适的工艺性能;5.釉必须具备良好的熔融性能,包括熔融温度、范围、及熔体性质。
对一次烧成制品的釉料,要求它在坯体烧结范围内成熟;对二次烧成制品的釉料,一般釉烧温度低于素烧温度60-120℃。
需要满足所有的要求,就决定了只有无机物中的氧化物。
1.1基体剂占釉料总量的40~60%,是釉料的基体剂的主要成分,相当于是釉料的填充剂,其性能的好坏直接影响着搪釉的效果,主要成分有氧化硅、氧化锆、氧化钛等。
1.2 助熔剂主要作用是促进搪釉料熔融改善其工艺性能和物理化学性能,主要成分有氧化钠、氧化钾、氧化硼等。
1.3 乳浊剂其作用是赋予坯体以良好的遮盖能力,主要成分有氧化钛、氧化锑、氧化锆、氧化锶等。
1.4 密着剂使瓷釉同坯体牢固结合,成分有氧化钴、氧化镍、氧化铜、氧化锑、氧化钼等。
1.5 着色剂赋予搪瓷釉以各种颜色,以达到彩饰效果,成分有氧化钴(呈鲜蓝色)、氧化铜(呈绿色或红色)、氧化铬(呈深绿色)、氧化铁(呈赭红色)等,这类氧化物的用量一般为0.1~2.5%,含量虽少,但承担着釉料的整个颜色。
2 氧化物与颜色关系要获得高质量的陶瓷产品,就得用高质量的、稳定的色釉料。
陶瓷工艺学釉料配方与计算釉层形成过程坯釉适应性
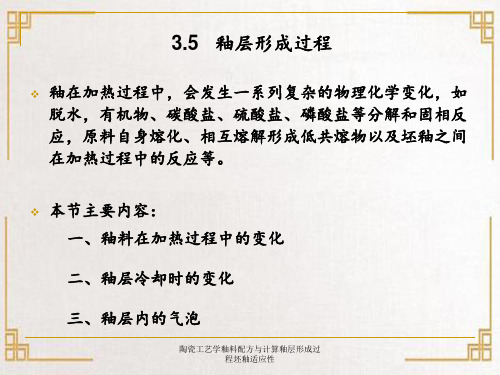
陶瓷工艺学釉料配方与计算釉层形成过 程坯釉适应性
二、釉层冷却时的变化
熔融的釉层在冷却时要经过三个阶段: ①从低粘度的流动状态冷却到软化温度(Tf ) ; ②粘度增加,经过粘性状态; ③超过转变温度( Tg)后凝固形成玻璃体。
第一阶段,粘度小于10Pa•s,温度与粘度大致成直线关系, 釉处于熔融状态。 第二阶段,随温度降低,熔体粘度增加, 粘度在10~100Pa•s,为硬化阶段或转变区域,此范围内釉 还处于粘性状态。第三个阶段,粘度大于100Pa•s,温度低 于转变温度点(Tg)时,釉面由粘性状态进入脆性状态,釉 面硬化。
多化合物间的固相反应发生。在温度继续升高时,易熔氧 化物同Al2O3和SiO2等发生反应,形成新的共熔物。
❖ 研究表明,Na2CO3与SiO2在700℃以下能发生完全固相反 应,在800℃时能发生少量烧结现象。 CaCO3与SiO2 固 相接触可反应生成偏硅酸钙(CaSiO3),如果加热时间很 长,在610℃可以起反应,在800℃时反应剧烈,950℃可 完全形成可熔性硅酸盐,1150℃时成为流动性熔体。
❖ 因此,在实际配制釉的时候,应配制出釉的膨胀系数略小 于坯的膨胀系数的釉料,使釉中产生不大的压应力,可以 在提高釉的热稳性及力学强度的情况下而不出现裂纹。
提高烧成温度,延长保温时间,使釉中组分Na2O、B2O3、PbO 挥发,坯料中Al2O3通过中间层向釉中迁移,从而降低釉的膨胀 系数,使釉层造成压应力,提高了坯釉结合强度。
硬化的釉层封闭在其中形成气泡。
陶瓷工艺学釉料配方与计算釉层形成过 程坯釉适应性
❖ 釉中气泡的存在,会给釉面性能带来很大影响。 1)在外观品质上,气泡的存在使釉面透光度降低,
建筑陶瓷用釉料 标准
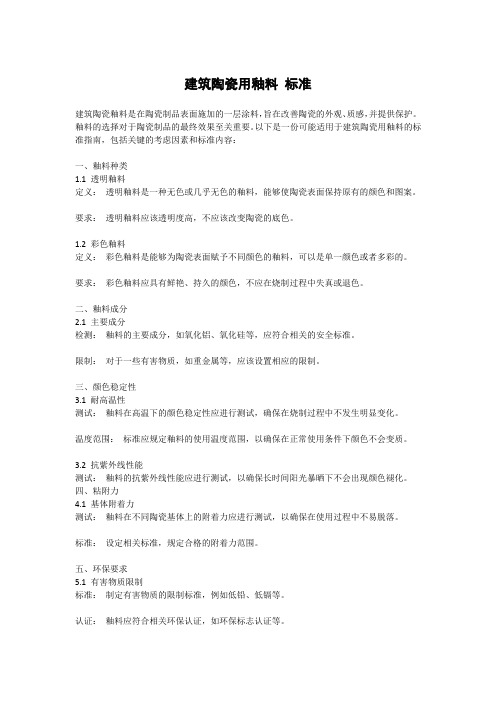
建筑陶瓷用釉料标准建筑陶瓷釉料是在陶瓷制品表面施加的一层涂料,旨在改善陶瓷的外观、质感,并提供保护。
釉料的选择对于陶瓷制品的最终效果至关重要。
以下是一份可能适用于建筑陶瓷用釉料的标准指南,包括关键的考虑因素和标准内容:一、釉料种类1.1 透明釉料定义:透明釉料是一种无色或几乎无色的釉料,能够使陶瓷表面保持原有的颜色和图案。
要求:透明釉料应该透明度高,不应该改变陶瓷的底色。
1.2 彩色釉料定义:彩色釉料是能够为陶瓷表面赋予不同颜色的釉料,可以是单一颜色或者多彩的。
要求:彩色釉料应具有鲜艳、持久的颜色,不应在烧制过程中失真或退色。
二、釉料成分2.1 主要成分检测:釉料的主要成分,如氧化铝、氧化硅等,应符合相关的安全标准。
限制:对于一些有害物质,如重金属等,应该设置相应的限制。
三、颜色稳定性3.1 耐高温性测试:釉料在高温下的颜色稳定性应进行测试,确保在烧制过程中不发生明显变化。
温度范围:标准应规定釉料的使用温度范围,以确保在正常使用条件下颜色不会变质。
3.2 抗紫外线性能测试:釉料的抗紫外线性能应进行测试,以确保长时间阳光暴晒下不会出现颜色褪化。
四、粘附力4.1 基体附着力测试:釉料在不同陶瓷基体上的附着力应进行测试,以确保在使用过程中不易脱落。
标准:设定相关标准,规定合格的附着力范围。
五、环保要求5.1 有害物质限制标准:制定有害物质的限制标准,例如低铅、低镉等。
认证:釉料应符合相关环保认证,如环保标志认证等。
六、施工性能6.1 流动性测试:釉料的流动性应进行测试,以确保在施工过程中能够均匀涂抹。
稠度:确定釉料的理想施工稠度,以适应不同施工方式。
6.2 烧结特性测试:釉料的烧结特性应进行测试,确保在烧制过程中能够形成均匀、致密的釉层。
烧制温度:标准应规定釉料的烧制温度范围。
七、质量控制7.1 检验标准制定检验标准:制定详细的检验标准,规定釉料的检验方法和评价标准。
7.2 生产记录和追溯记录要求:生产过程中应保留详细的记录,以便追溯产品的生产批次、成分和生产条件。
温润细腻柔光砖釉的调配
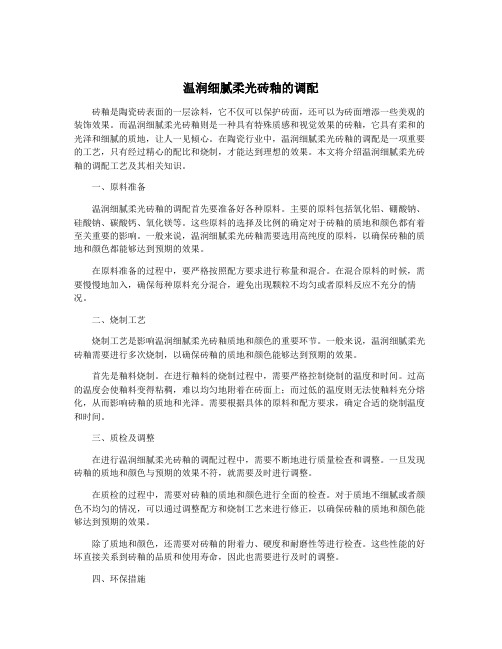
温润细腻柔光砖釉的调配砖釉是陶瓷砖表面的一层涂料,它不仅可以保护砖面,还可以为砖面增添一些美观的装饰效果。
而温润细腻柔光砖釉则是一种具有特殊质感和视觉效果的砖釉,它具有柔和的光泽和细腻的质地,让人一见倾心。
在陶瓷行业中,温润细腻柔光砖釉的调配是一项重要的工艺,只有经过精心的配比和烧制,才能达到理想的效果。
本文将介绍温润细腻柔光砖釉的调配工艺及其相关知识。
一、原料准备温润细腻柔光砖釉的调配首先要准备好各种原料。
主要的原料包括氧化铝、硼酸钠、硅酸钠、碳酸钙、氧化镁等。
这些原料的选择及比例的确定对于砖釉的质地和颜色都有着至关重要的影响。
一般来说,温润细腻柔光砖釉需要选用高纯度的原料,以确保砖釉的质地和颜色都能够达到预期的效果。
在原料准备的过程中,要严格按照配方要求进行称量和混合。
在混合原料的时候,需要慢慢地加入,确保每种原料充分混合,避免出现颗粒不均匀或者原料反应不充分的情况。
二、烧制工艺烧制工艺是影响温润细腻柔光砖釉质地和颜色的重要环节。
一般来说,温润细腻柔光砖釉需要进行多次烧制,以确保砖釉的质地和颜色能够达到预期的效果。
首先是釉料烧制。
在进行釉料的烧制过程中,需要严格控制烧制的温度和时间。
过高的温度会使釉料变得粘稠,难以均匀地附着在砖面上;而过低的温度则无法使釉料充分熔化,从而影响砖釉的质地和光泽。
需要根据具体的原料和配方要求,确定合适的烧制温度和时间。
三、质检及调整在进行温润细腻柔光砖釉的调配过程中,需要不断地进行质量检查和调整。
一旦发现砖釉的质地和颜色与预期的效果不符,就需要及时进行调整。
在质检的过程中,需要对砖釉的质地和颜色进行全面的检查。
对于质地不细腻或者颜色不均匀的情况,可以通过调整配方和烧制工艺来进行修正,以确保砖釉的质地和颜色能够达到预期的效果。
除了质地和颜色,还需要对砖釉的附着力、硬度和耐磨性等进行检查。
这些性能的好坏直接关系到砖釉的品质和使用寿命,因此也需要进行及时的调整。
四、环保措施在温润细腻柔光砖釉的调配过程中,需要重视环保措施。
- 1、下载文档前请自行甄别文档内容的完整性,平台不提供额外的编辑、内容补充、找答案等附加服务。
- 2、"仅部分预览"的文档,不可在线预览部分如存在完整性等问题,可反馈申请退款(可完整预览的文档不适用该条件!)。
- 3、如文档侵犯您的权益,请联系客服反馈,我们会尽快为您处理(人工客服工作时间:9:00-18:30)。
釉料成分与色料系统的匹配性要获得呈色稳定、颜色上佳的色调,除了选择质量稳定的色料以外.基础釉的配方设计也很重要。
要使不同颜色的色料发出最佳的颜色,选择合适的基础釉非常重要。
在选定色料后,釉料组成是制约色料发色的另一个重要因素。
配方组分不好的基础釉,不仅难以使色料发色变浅.使色调改变,使产品出现色差,甚至还会使釉面出现针孔、气泡、闭光等缺陷。
而一个优良的基础釉配方,则需要工厂技术人员付出大量心血才呵能获得。
釉料中不同的化学组分对各种色料的影响是不一样的,需要根据不同情况具体分析结合我公司色料,对色料与基础釉的匹配性简单说明如下:a.对于铬绿(Cr-A1)色料,釉料中应避免使用锌、锡、镁等成分,以免影响呈色;墨绿(Co—Cr—A1)色料在含少量锌的釉中发色更好:孔雀绿(Co—Cr—Al—Zn)、蓝绿(Co—Cr)不适合用于高锌、高锡、高镁的釉中。
所有含铬的绿色在透明釉中呈色鲜艳,铬绿不适合在乳浊釉中使用。
b.含钴的蓝色料,使用时必须注意kTL问题。
钴蓝(Co—AI—Sn—Zn)色料做色釉时,釉中的锌、镁含量可过高,否则颜色易偏红。
c.锆基三原色在透明釉、锆乳浊釉中发色很好。
稳定性也很好。
但是钒蓝(Zr__Si—V)色料不适合用于高铅、高碱金属釉;镨黄(Zr—Si—Pr)色料使用时不能超过1250oC:锆铁红(Zr—Si—Fe)色料不适合用于含锌、含硼和高碱金属釉。
钒黄(Zr—V)色料不适合用于高铅、高锌、高钙、高镁和高硼的釉,其在透明釉和乳浊釉中均发色良好。
不过,由于钒黄色料的结构稳定性羞,粒度变化对其色调影响明垃,所以在使用时球磨时间不町过长.以免引起釉面缺陷。
d含铬的黑色色料在使用时,釉中的锌、镁含量要低,以免引起色涮偏绿或偏红。
含钡的石灰釉有利于黑色料的发色。
黑色料在乳浊釉中使用时,色调偏灰,非黑色。
e.灰色料非常适合在乳浊釉中使用,发色稳定,呈色均匀锆灰(Zr一一Si—Ni—Co)色料对釉烧温度和釉料组成比较敏感,在含锌釉中偏蓝,在高铅釉中偏绿。
蓝灰(Sn-Sb)包料在各种釉中发色均很好棕色色料适合在含锌釉中使用f铬锡系列色料,如桃红、玛瑙红、紫色色料等,不适合在高锌高硼釉中使用,也不适合在高锂釉和高镁釉巾使用。
否则会导致颜色变浅或者褪色。
任釉巾添加少量石灰石、氧化锡有利于铬锡系列色料的呈色。
g.包裹系列色料对釉料成分有苛刻的要求,要想发出鲜艳的颜色,有一个良好的基础釉是十分关键的。
包裹色料要求基础釉的折射率要高、高温粘度要大、碱金属含量要低,同时釉中不能含有强氧化性物质,以免色料分解出现黑心现象,优良的大红釉配方要靠大量的反复试验才能获得、总之.要得到色彩鲜艳、釉面良好的优良色釉产品.除了使用好的色料以外,使用与之相的基础釉是非常重要的。
陶瓷颜料制造注意事项(一)原料原料的种类,质量都必考虑。
所谓种类以氧化铝作为原料来说,有氧化铝、氢氧化铝、明矾、高岭土等,应用其中那一种都可以。
原料种类甚多,又各有特性,主要是使其适应于使用的要求。
在质量方面成问题的是化学组成(或纯度),矿物组成与制造过程。
所谓制造过程是指以什么样的工艺,在什么样的条件下制造。
矿物组成必须注意使用像高岭土那样的天然原料。
纯度方面没有必要使用特别纯的物质。
很多情况下一般使用化学纯,工业纯或统一配方的物质。
最重要的是经常使用质量稳定的原料,且严格掌握成分,不应含有超过允许量的杂质。
原料加工粉碎时,最好不用铁质器械,以免铁粉掺入。
此外,放置地方也应注意,不让灰尘混入而影响色泽。
制造陶瓷颜料所用的原料,大致分为土石原料、易熔原料与呈色原料三种。
现将常用主要的陶瓷原料的种类列如表1。
表1 使用于陶瓷颜料的原料(二)混合制造陶瓷颜料所用的一切原料,必须经过2500孔/厘米2的筛,毫无筛余,其湿度不大于0.3%,方可进行配料。
配料后着重仔细混合。
颜料在混合中有继续磨细的作用。
颜料的细度一般要求通过10000孔/厘米2筛,毫无筛余。
混合的方法,大致分为干式和湿式两种。
普通在具有硬质瓷(其硬度不低于石英)内衬的球磨机中进行。
但硬度特高的色料的粉碎和混合则必须采用刚玉质磨球及内衬的球磨机,以免瓷质球磨机的瓷质混入颜料中。
一般以湿式混合法为最常用。
在混合时决不能与铁质器具接触,以免铁分混入,此点尤为要紧。
干、湿二种混合方法,均匀粉末混合,其粉末无论怎样微细,总不及由物料的可溶性溶液彼此混合更为均匀当溶液彼此混合后,在混合液中再加入氢氧化钠或碳酸钠使之中和成为沉淀。
当混合多种不同的金属盐类时,尤须采用溶液混合和化学沉淀法。
这样可使色料发色均匀、鲜艳。
在色料煅烧后,如需配加熔剂或其他添加物,仍可送入湿式球磨机中,进行精研。
湿式球磨混合,一般多用清水,如遇特殊贵重颜料,在出磨后不应在空气中或恶劣气氛中(如碳酸气、灰尘等)干燥,或暴露过久,以免损害色泽。
为此可用酒精混研,出磨后置电热或蒸汽干燥器中,瞬间即可完全干燥。
但因成本较贵,普通很少采用。
溶液混合和化学沉淀法多在搅拌木桶中进行。
木桶的制造很简单,通常以厚约50~70毫米的硬木板制成。
桶中插入气管或橡皮管,以便通入蒸汽加热。
木桶中并装有供水管,在木桶不同高度上装置截门,便于施行倾泻洗涤操作。
(三)烧成将调制的生料混合均匀干燥后,装于坩埚或匣钵内烧成,但不要进行加压烧固。
烧成温度、烧成时间、烧成气氛必须分别适应各种不同的调制颜料,没有必要用还原焰烧成,一般都采用氧化焰烧成。
但铬锡桃红则必须规定用氧化焰烧成。
烧成温度是1000℃和1300℃。
也可以与陶瓷制品一起放在窑中共烧。
烧成时间愈长愈好。
有时须煅烧2次到3次。
如煅烧2次时其操作过程如下:1.粉碎一次煅烧物,水洗后以相同温度进行再一次煅烧。
这种情况下开始不加矿化剂,往往进行第二次煅烧再添加矿化剂。
3.第一次仅配入两种或三种成分进行混合煅烧,然后以烧成物与其余部分混合而调之。
(四)烧成物的处理烧成物的是处理根据煅烧过程的不同而异。
如系加入熔剂后烧成的熔融物,则须立即流入冷水中,制成熔块使之易于粉碎。
如果是低温或高温的烧成物,则须进行粉碎,并用温水或稀盐酸、稀硝酸溶液反复洗涤除净可溶性物质,至洗涤水呈中性反应为止,最后再用清水洗涤,进行干燥。
(五)矿化剂和呈色补助剂所谓矿化剂就是具有一种作用帮助矿物的生成。
它不仅能降低生成的温度,在一定情况下能促使某种矿物的优先形成。
而且还能左右生成矿物的色,所以它的选择是非常重要的。
一般使用矿物如表2所示。
碱金属的化合物、铅和硼的化合物很多都是熔剂,有时候也称为熔块。
如果其主要作用控制颜料的色时,就称为呈色补助剂。
作为呈色补助剂的时候,它应用的范围比矿化剂更广泛。
矿化剂的使用与其他硅酸盐业制品相比较,能够不限量地添加。
这是因为烧成后能采用洗涤除去。
因此它是制造陶瓷颜料最方便的方面。
表2 主要矿化剂(六)成品超细度的研磨现代陶瓷颜料发展迅速,为了提高颜料的质量,必须在技术上不断改进。
目前,国内釉上陶瓷在烧成时,能抵抗窑内化学变化及恶劣气氛如碳酸气、氧化硫气的作用。
为了使颜料具有较好的化学能力,在颜料组成中必须含有硅,硼等氧化物,甚至还须含有少量的铝、镁、锡、钙等氧化物。
但是,这样会使颜料的烧成温度提高而影响光亮色泽。
唯一补救之法,是将成品进行超细度的研磨,使颜料的颗粒极为微细,从而适当地降低其烧成温度,使之易于熔融,光亮色泽也不为熔剂冲淡。
釉下颜料的细度愈小,发色愈强,与坯体结合愈紧密,不易发生变化。
因此,颜料生产过程的最后,阶段的成品研磨,实为非常重要的一个环节。
一般进料细度在2毫米以内,出料细度在先60微米以下时,已非一般球磨机所能达到,因此颜料成品的最后研磨最好的在前述的高频率振动磨机中进行。
(七)颜料使用方法陶瓷颜料必须使用得法,才能达到预期效果。
由于釉上、釉下颜料不同,其使用方法也不相同。
釉下颜料品种不多,过去使用较少。
使用方法尚有许多值得研究。
釉下颜料是施于多孔性的生坯或素烧瓷坯上。
如果单用水混和,易被素坯吸收而使颜料失其效用。
因此,必须添加少量胶结物质,使颜料紧固于素坯上,此胶结物在烧成时可以挥发掉。
最适当的添加物为极稀薄的阿拉伯树胶溶液。
其配方比例,由熟练工人的经验而定。
若此种物质用量过多,烧成时必然炭化,污损色泽。
根据经验,亦可取蒸馏松节油,再加入经过糖密煮沸的1%亚麻仁油,与颜料仔细混研进行彩绘。
这种方法在绘画上并不感困难,而且也不被素瓷坯吸收。
彩绘后松节油迅速蒸发,所剩的只有痕迹的亚麻仁油。
这样可使颜料附着适当,而又无油质炭化,污损颜色的可能。
釉下颜料的彩绘方法如下:先由熟练工人设计,在素烧瓷坯上用浓墨描成花纹图样。
再把用上法配成的颜料胶水用毛笔浸饱,填绘于浓墨之间,干燥后,置于素烧窑中,在600~700℃下煅烧,则浓墨及颜料中的胶结物均被烧掉,而露出生动的空筋花样。
然后再施以透明釉(以石灰釉较好),在瓷器本烧窑中烧成(1300~1320℃),则成精美的釉下彩制品。
釉上颜料使用已久,积累有相当多的经验。
常用油脂作为胶粘剂来调和颜料。
胶粘剂的配方如下松节油 65~70%松香 35~30%此种配方与使用目的及季节性有关,可由熟练工人的酌定之。
如果用水调色时,必须配制成胶粘剂,其配方为:糊精 10水 10白明胶 0.03甘油 0.1使用此种胶粘剂时,在加热中应特别注意只可用文火徐徐加热,切不可使糊精炭化。
用油脂作胶粘剂时松节油质量十分重要,必须通过蒸馏温度与质量有关:第一部分155℃以下第二部分155~175℃以下第三部分175℃其中以第二部分蒸馏的松节油在60%以上适用。
松香质量以燃烧后无灰分或以在丙酮(乙醚)中完全溶解者为合格色料产品应用说明1.包裹系列色料不能研磨过长,在总研磨时间达95%一97%以后再加入色料磨匀即可。
2.黑色等含Fe成份之色料,与釉浆、泥浆研磨后不宜除铁,以免影响发色。
3.含V成份之色料用于印刷时,当加入比较大时可能会有凹釉之隐患,敬请留意。
4.釉用黑色色料在含锌釉中发色可能不利。
5.胶辊印刷色料与釉粉及印油混合均匀后,建议过325目筛后再使用。
6.研磨细度之差异会导致发色差异,请控制色料研磨时间。
7.施釉重量不同有产生色调差异之可能。
8.应避免因釉浆沉淀而造成颜色分布不均之现象。
9.勿以少量强发色色料产生弱发色,会影响发色品质。
例如:用少量黑色去调浅灰色的方法可能导致瓷砖色差比较大。
10.部分坯用色料的发色稳定性与坯体中化学成份有一定的关联。
色料物理特性说明:1.釉用色料系列:粉体细度325目筛余≤0.3%,含水率≤O.5%。
2.胶辊色料系列:粉体细度400目筛余≤O.3%,同时325目全过,含水率≤0.5%。
3.坯用色料系列:粉体细度325目筛余≤1.0%,但250目筛全通过,含水率≤0.5%。
色料三原色和色料减色法若将黄、品红、青色料,每两种以“适当”的比例混合,又可以得到色光三原色的颜色(参看彩图),即:黄+品红=红黄+青=绿品红+青=蓝品红+青+黄=黑改变黄、品红、青三种色料的混合比例,因选择性地吸收和反射色光,便可以获得各种不同的颜色。