釉料知识
釉料——精选推荐
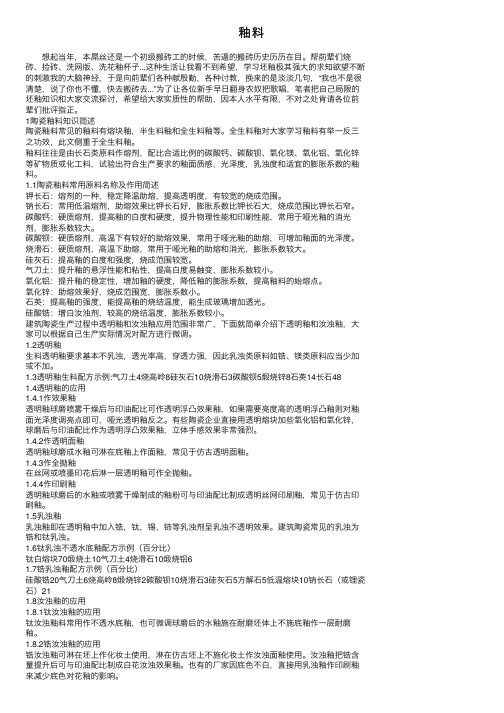
釉料 想起当年,本屌丝还是⼀个初级搬砖⼯的时候,苦逼的搬砖历史历历在⽬。
帮前辈们烧砖、捡砖、洗⽹版、洗花釉杯⼦...这种⽣活让我看不到希望,学习坯釉极其强⼤的求知欲望不断的刺激我的⼤脑神经,于是向前辈们各种献殷勤,各种讨教,换来的是淡淡⼏句,“我也不是很清楚,说了你也不懂,快去搬砖去...”为了让各位新⼿早⽇翻⾝农奴把歌唱,笔者把⾃⼰局限的坯釉知识和⼤家交流探讨,希望给⼤家实质性的帮助,因本⼈⽔平有限,不对之处肯请各位前辈们批评指正。
1陶瓷釉料知识简述陶瓷釉料常见的釉料有熔块釉,半⽣料釉和全⽣料釉等。
全⽣料釉对⼤家学习釉料有举⼀反三之功效,此⽂侧重于全⽣料釉。
釉料往往是由长⽯类原料作熔剂,配⽐合适⽐例的碳酸钙、碳酸钡、氧化镁、氧化铝、氧化锌等矿物质或化⼯料,试验出符合⽣产要求的釉⾯质感,光泽度,乳浊度和适宜的膨胀系数的釉料。
1.1陶瓷釉料常⽤原料名称及作⽤简述钾长⽯:熔剂的⼀种,稳定降温助熔,提⾼透明度,有较宽的烧成范围。
钠长⽯:常⽤低温熔剂,助熔效果⽐钾长⽯好,膨胀系数⽐钾长⽯⼤,烧成范围⽐钾长⽯窄。
碳酸钙:硬质熔剂,提⾼釉的⽩度和硬度,提升物理性能和印刷性能,常⽤于哑光釉的消光剂,膨胀系数较⼤。
碳酸钡:硬质熔剂,⾼温下有较好的助熔效果,常⽤于哑光釉的助熔,可增加釉⾯的光泽度。
烧滑⽯:硬质熔剂,⾼温下助熔,常⽤于哑光釉的助熔和消光,膨胀系数较⼤。
硅灰⽯:提⾼釉的⽩度和强度,烧成范围较宽。
⽓⼑⼟:提升釉的悬浮性能和粘性,提⾼⽩度易触变,膨胀系数较⼩。
氧化铝:提升釉的稳定性,增加釉的硬度,降低釉的膨胀系数,提⾼釉料的始熔点。
氧化锌:助熔效果好,烧成范围宽,膨胀系数⼩。
⽯英:提⾼釉的强度,能提⾼釉的烧结温度,能⽣成玻璃增加透光。
硅酸锆:增⽩汝浊剂,较⾼的烧结温度,膨胀系数较⼩。
建筑陶瓷⽣产过程中透明釉和汝浊釉应⽤范围⾮常⼴,下⾯就简单介绍下透明釉和汝浊釉,⼤家可以根据⾃⼰⽣产实际情况对配⽅进⾏微调。
颜色釉介绍

颜色釉介绍1. 什么是釉料?在陶瓷制作过程中,釉料是一种用来给陶瓷器物上釉的材料。
釉料可以赋予陶瓷器物丰富多样的色彩和光泽,同时还能保护器物表面,增加器物的耐磨性和耐水性。
釉料主要由一种或多种含有玻璃形成元素的氧化物以及一定比例的石英、白云石、长石等酸性氧化物制成。
不同的釉料成分和釉料的烧制温度可以产生各种不同的颜色和效果。
2. 颜色釉的分类颜色釉是指通过添加了金属氧化物或某些特殊成分的釉料,使陶瓷器物表面产生各种不同的颜色。
根据不同的金属氧化物或成分的添加,颜色釉可以被分为以下几类:2.1 氧化铁系列釉料氧化铁系列釉料是最常见的一类颜色釉。
通过添加氧化铁(Fe2O3)可以制作出茶色、红褐色、红色和黑色等釉料。
茶色釉是氧化铁系列釉料中的一种常见釉料。
茶色釉具有一种深浅不一的棕色,给人一种宁静和温暖的感觉。
茶色釉常用于茶具和日常用陶瓷器物的制作。
2.2 氧化铜系列釉料氧化铜系列釉料可以制作出绿色和蓝绿色的釉料。
通过在釉料中添加氧化铜(CuO)可以产生独特的绿色效果,常用于景德镇青花瓷的制作。
蓝绿色釉是氧化铜系列釉料中的一种常见釉料。
蓝绿色釉可以给人一种清新、自然的感觉,常用于装饰瓷器、花瓶等陶瓷作品。
2.3 氧化钴系列釉料氧化钴系列釉料是制作蓝色釉料的常用材料。
通过在釉料中添加氧化钴(CoO)可以制作出不同深浅不一的蓝色釉料。
氧化钴的添加量可以影响蓝色的深浅和明暗度。
蓝色釉是氧化钴系列釉料中的一种常见釉料。
蓝色釉可以给人一种清新、纯净的感觉,常用于制作青花瓷等陶瓷作品。
2.4 氧化铬系列釉料氧化铬系列釉料可以制作出绿色和黄绿色的釉料。
添加氧化铬(Cr2O3)可以制作出不同深浅的绿色釉料,特别适合制作山水画瓷和花卉瓷。
黄绿色釉是氧化铬系列釉料中的一种常见釉料。
黄绿色釉可以给人一种清新、明亮的感觉,常用于装饰瓷器、盘子等陶瓷作品。
3. 颜色釉的使用与应用颜色釉在陶瓷制作中起到重要的装饰作用,可以给作品增添美感和艺术价值。
第六章 陶艺制品所用色料和釉料
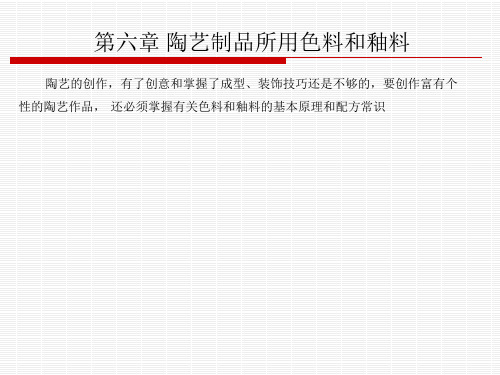
制而成,因颜料在釉的下面,故称为釉下彩
1.釉下彩的配方:
。
第一节 陶艺制品所用色料
2.釉下彩的常用类: (1) 青花:主要是以氧化钴做呈色剂,用茶叶水调配,经高温烧制呈现蓝色。 (图133A图133B)(明 青花瓷) (2) 釉里红:以氧化铜做呈色剂,用桃胶水或清水调配,经高温烧制呈现红色。(图134A图134B)
(2) 如何提高釉的温度:增加石英土(瓷土、陶土等)。减少助熔剂。
7 釉的研磨 将配制好的原料放进磨釉机研磨过筛(筛网80目)即可。
第二节 陶艺制品所用釉料
(二)常见的釉料
1常见的色釉有:
白釉、黑釉、青釉、龙泉釉、茶叶末釉、铜红釉、钧窑釉(花釉)、铜绿釉、土耳 其蓝釉、金砂釉、开片(裂纹)釉、结晶釉、黑天目釉、树叶天目釉,铁红釉、条痕釉、
(图139A、B)
(2) 结晶釉料:分为低、中、高温釉,由两种以上显色能力和结晶特点不相溶的 金属氧化物和熔块配制而成.烧造前不能分辨结晶和色彩,在不同窑炉和不同烧造气
氛下呈现不同的颜色和结晶效果。低温釉烧成温度在1100℃左右,中温釉烧成温度在
1200℃左右,高温釉烧成温度在l350℃左右。(图140A、B)
(1) 降低釉的温度:在釉料中减少泥料比例,增加碳酸钙,氧化锌、碳酸钡、氧
化镁、氧化铅等助熔剂的比例,即可降低釉的烧结温度。 (2) 提高釉的温度:在釉料中增加泥料、硅、铝的比例,减少助熔剂的比例,即 可提高釉的烧结温度。 (与坯体烧成相适应,但要注意膨胀系数,防止破裂)
第二节 陶艺制品所用釉料
5 一般陶艺的釉料烧成温度可分为: 低温釉——1000℃以下。中温釉——1000℃一l260℃。高温釉——1260℃以上。 烧成火焰可分 还原烧——烧成时“缺氧”烧成。氧化烧——烧成时“多氧”烧成。 6 釉的配置基本原则 (1) 如何降低釉的温度:减少石英土(瓷土、陶土等)。 增加助熔剂(如碳酸钙、氧化锌、碳酸钡、氧化镁等)。
陶瓷釉料知识

陶瓷釉料知识陶瓷原料包括高岭土、粘土、瓷石、瓷土、着色剂、青花料、石灰釉、石灰碱釉等。
高岭土陶瓷原料,是一种主要由高岭石组成的粘土。
因首先发现于江西省景德镇东北的高岭村而得名。
它的化学实验式为:Al203·2Si02·2H20,重量的百分比依次为:39.50%、46.54%、13.96%。
纯净高岭土为致密或松疏的块状,外观呈白色、浅灰色。
被其他杂质污染时,可呈黑褐、粉红、米黄色等,具有滑腻感,易用手捏成粉末,煅烧后颜色洁白,耐火度高,是一种优良的制瓷原料。
粘土陶瓷原料是一种含水铝硅酸盐矿物,由长石类岩石经过长期风化与地质作用而生成。
它是多种微细矿物的混合体,主要化学组成为二氧化硅、三氧化二铝和结晶水,同时含有少量碱金属、碱土金属氧化物和着色氧化物等。
粘土具有独特的可塑性和结合性,其加水膨润后可捏练成泥团,塑造所需要的形状,经焙烧后变得坚硬致密。
这种性能,构成了陶瓷制作的工艺基础。
粘土是陶瓷生产的基础原料,在自然界中分布广泛,蕴藏量大,种类繁多,是一种宝贵的天然资源。
瓷石也是制作瓷器的原料,是一种由石英、绢云母组成,并有若干长石,高岭土等的岩石状矿物。
呈致密块状,外观为白色、灰白色、黄白色、和灰绿色,有的呈玻璃光泽,有的呈土状光泽,断面常呈贝壳状,无明显纹理。
瓷石本身含有构成瓷的多种成分,并具有制瓷工艺与烧成所需要的性能。
我国很早就利用瓷石来制作瓷器,尢其是江西、湖南、福建等地的传统细瓷生产中,均以瓷石作为主要原料。
瓷土由高岭土、长石、石英等组成,主要成分为二氧化硅和三氧化二铝,并含有少量氧化铁、氧化钛、氧化钙、氧化镁、氧化钾和氧化钠等。
它的可塑性能和结合性能均较高,耐火度高,是被普遍使用的制瓷原料。
着色剂存在于陶瓷器的胎、釉之中,起呈色作用。
陶瓷中常见的着色剂有计三氧化二铁、氧化铜、氧化钴、氧化锰、二氧化钛等,分别呈现红、绿、蓝、紫、黄等色。
青花料是绘制青花瓷纹饰的原料,即钴土矿物。
青花瓷釉料基本知识

青花瓷釉料基本知识
青花瓷是中国传统的陶瓷工艺之一,它具有独特的装饰效果和艺术价值。
而青花瓷的釉料对于青花瓷的质量和外观起着至关重要的作用。
以下是青花瓷釉料基本知识。
1. 釉料成分
青花瓷釉料的成分主要包括石英、长石、黏土和氧化物等。
其中,石英和长石是主要的硅酸盐矿物,可以提高釉料的硬度和耐磨性。
黏土是增加釉料粘度和黏度的关键成分,而氧化物则是调节釉料颜色和透明度的重要因素。
2. 釉料制备
青花瓷釉料的制备通常需要经过多个步骤。
首先,将原材料进行研磨、筛选和混合,然后加入水进行搅拌。
接着,将釉料涂在瓷器表面并进行干燥,最后进行高温烧制,使釉料与瓷体完全融合。
3. 釉料特点
青花瓷釉料的主要特点是具有良好的透明度和光泽度,并且能够抵御酸、碱和高温等多种化学腐蚀。
此外,釉料的颜色和纹路也是青花瓷的重要特征,有些釉料呈现出深浅不一的青色,而有些则呈现出咖啡色或红色。
4. 釉料分类
根据不同的成分和用途,青花瓷釉料可以分为透明釉、半透明釉和不透明釉等。
其中,透明釉是最常用的一种釉料,它能够保护瓷器表面并增加光泽度,而半透明釉和不透明釉则主要用于装饰和修补瓷
器表面。
总之,青花瓷釉料是青花瓷制作过程中不可缺少的重要组成部分,它可以影响到青花瓷的质量、外观和装饰效果。
因此,瓷器制作者需要对釉料的成分、制备和特点有一定的了解,才能制作出高质量的青花瓷。
釉料概述、性质、依据和计算

熔融温度范围过窄,烧成操作控制困难, 易产生流釉或生釉;
熔融温度范围过宽,导致①始熔点前移; ②使上限与下限釉面质量不同(组分挥发、内 扩散)
15
实际应用时中,考虑釉的始熔温度和熔融温度范围 不能脱离坯体的烧结性能和具体的烧成条件。 对于日用瓷: ①始熔温度应高于坯体烧结温度的下限;(便于排气) ②始熔温度不应超过制品烧成温度(范围)的下限; ③流动温度(熔融温度范围上限)应与制品烧成温度 (范围)的上限相对应。
16
釉熔融温度范围
T始融
●● ●
T坯烧结 T烧成下
T流动
●● ●
T烧成上 T坯膨胀
制品烧成温度范围
坯体烧结温度范围
17
··釉的烧成温度的估算
(1) 酸度系数法 (C.A) C.A =(酸性氧化物mol数)/(碱性氧化物mol数)
C.A
RO 2
R2ORO 3R2O3
式中:RO2— 酸性氧化物mol数; R2O、RO、R2O3—碱性氧化物mol数;
慢速烧成釉、快速烧成釉
一次烧成釉、二次烧成釉
主要熔剂 长石釉、石灰釉(石灰—碱釉、石灰—碱土釉)、锂釉、镁
组
釉、锌釉、铅釉(纯铅釉、铅硼釉、铅碱釉、铅碱土釉)、无
成 主要着色剂 铅釉(碱釉、碱土釉、碱硼釉、碱土硼釉)
铜红釉、镉硒红釉、铁红釉、铁青釉、玛瑙红釉
外观特性 透明釉、乳浊釉、虹彩釉、无光釉、半无光釉、金属光泽釉
23 23
(B)硬度
硬质瓷
划痕硬度
釉面硬度一般为 莫氏硬度7~8;维氏硬度5200~7500MPa
影响硬度的因素: (1)化学组成:适应加和性法(p166)
第7章 釉料

釉料加热时的变化
釉层冷却时的变化
坯釉中间层的形成
中间层:由于坯釉化学组成不同,高温下相互扩散、溶解、 反应、结晶,生成一层组成和性能介于坯釉之间的过渡性
物质。
釉料与坯体相互作用导致中间层的出现。 对坯釉之间因膨胀系数之 差产生的应力起缓冲作用; 提高制品的热稳定性; 增加制品的强度
二 釉用原料
矿物原料 化工原料
长石、霞石正 长岩、火山灰、 碎玻璃、瓷土、 粘土 辅助原料
B2O3、R2O、 RO、ZnO、
PbO和Pb3O4
乳浊剂、悬浮 剂、粘结剂、 分散剂和解凝 剂
三 釉层形成
釉层形成过程的反应 坯釉适应性
1 釉层形成过程的反应 釉层形成过程的反应为:原料的分解、化合、熔 化及凝固(包括析晶) 交叉或重复出现。
四 釉料制备
(一)生料釉 原料选择 煅烧 配料 釉料研磨
(二) 熔块釉料配制
熔块釉包括熔块与生料两部分。 坩锅炉 熔块的配制 原料准备 配料 熔制 池炉
回转炉
水淬成粒
贮存备用
熔块釉的制备 熔块 生料 配料 球磨 检查细度
助剂
除铁 过筛 试烧样品
贮存备用(陈腐)
釉料的熔制
坩埚炉 池 炉 回转炉
釉层受力分析
坯体 釉层剥落
正釉
(3) 坯釉的热膨胀系数接近或相等(釉=坯)
一般来说,脆性材料的耐压强远高于抗张强度,所以 开裂的情况较剥落更容易出现。 希望釉的膨胀系数接近于坯体而稍低于坯体
中间层对坯釉适应性的影响
发育好的中间层可填满坯体表面的缝隙,减弱坯
釉间的应力,增大制品的机械强度。
五 施 釉
浸釉(蘸釉) 坯的吸水性或热坯的 附着作用使釉浆吸附着。
第三章 釉料汇总
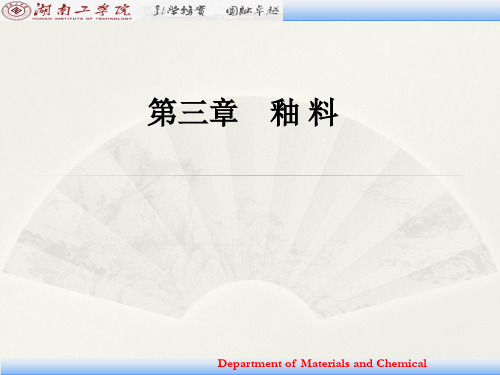
第一节 釉的作用及特点
一、釉的作用 釉的概念: 釉是施于陶瓷坯体表面的一层极薄的物质,它
是根据坯体性能的要求,利用天热矿物原料及 某些化工原料按着比例配合,在高温作用下熔 融而覆盖在坯体表面的富有光泽的玻璃质层 (渗彩釉及自然釉例外)。
③熔融温度系数法。首先计算釉的熔融温 度系数K,根据计算所得K,再由表3-4查出 釉的相应熔融温度t。参见P150。
Department of Materials and Chemical
2、釉熔体的高温粘度、表面张力、润湿性
釉熔体能否在坯体表面平滑的铺展,与其 粘度、表面张力和润湿性有关。
第三章 釉 料
Department of Materials and Chemical
汉字中的“釉”,其含义是指有油状的光 泽,所以古代用“油”字表示陶瓷制品表 面的光泽,但又因为“油”字这个字代表 食物,后人经过种种考虑,修改结果就取 表示光彩的“采”合成为“釉”。陶瓷制 品表面多半穿着一件光滑、平滑、漂亮的 外衣,“赤膊上阵”的很少。这件五彩缤 纷的外衣就是我们所要介绍的”釉“。
引入SiO2、Al2O3等成分,而从釉内引入RO 和R2O等成分。坯釉中间层的化学组成和性 质介于坯釉之间,并逐渐由坯过渡到釉,
无明显界限。
Department of Materials and Chemical
为了获得良好的坯釉中间层,在坯体酸性 较高的情况下,即SiO2 / RO的摩尔比高,则 应该采用中等酸性的釉料;如果坯体的酸 性弱,则釉应该是接近中性或弱碱性。否 则由于两者之间化学性质相差过大,由于 作用强烈,会使釉被坯体吸收,出现“干 釉”现象。
- 1、下载文档前请自行甄别文档内容的完整性,平台不提供额外的编辑、内容补充、找答案等附加服务。
- 2、"仅部分预览"的文档,不可在线预览部分如存在完整性等问题,可反馈申请退款(可完整预览的文档不适用该条件!)。
- 3、如文档侵犯您的权益,请联系客服反馈,我们会尽快为您处理(人工客服工作时间:9:00-18:30)。
釉是指覆盖在陶瓷坯体上的玻璃态薄层,但它的组成较玻璃复杂,其性质和显微结构也和玻璃有较大的差异,如它的高温粘度远大于玻璃;其组成和制备工艺与坯料相接近而不同于玻璃。
釉的作用在于:改善陶瓷制品的表面性能,使制品表面光滑,对液体和气体具有不透过性,不易沾污。
其次可以提高制品的机械强度、电学性能、化学稳定性和热稳定性。
釉还对坯起装饰作用,它可以覆盖坯体的不良颜色和粗糙表面。
许多釉如颜色釉、无光釉、砂金釉、析晶釉等具有独特的装饰效果。
第一节釉的分类釉的品种很多,分类方法也较多,常用的有:1按与其结合的坯体的种类分可分为瓷釉、陶釉。
2.按制备方法分:生料釉——所有制釉的原料均不预先熔制,而是直接加入球磨机混合,制成釉浆。
熔快釉——先将部分易熔、有毒的原料以及辅助原料熔化成熔快,再与粘土等其它原料混合、研磨成釉浆。
盐釉——当坯体煅烧到高温时,向窑内投入挥发性盐(常用NaCl),使之气化后直接与坯体作用形成薄的釉层。
3.按釉的外观特征分可以分为透明釉、乳浊釉、半无光釉、结晶釉、金属光泽釉、裂纹釉等。
4.按釉的成熟温度分可分为高温釉(>釉250℃)、中温釉(釉釉00~釉250℃)、低温釉(<釉釉00℃)。
5.按釉的主要熔剂矿物分类可分为长石釉、石灰釉铅釉、锂釉、镁釉、锌釉等。
长石釉——以长市为主要熔剂,釉式中K2O+Na2O的分子数等于或稍大于RO的分子数,长石釉的高温粘度大、烧成范围宽、硬度较大、热膨胀系数也较大。
石灰釉——主要熔剂为CaO,釉式中CaO的摩尔数≥,石灰釉的光泽很强、硬度大、透明度高,但烧成范围较窄,气氛控制不好易产生“烟熏”。
如果用一部分长石代替石灰石,使CaO含量<8%则称为石灰碱釉,以部分MgO(分子数>)代替部分CaO则称为镁釉,以ZnO代替CaO(分子数>)则称为锌釉. 铅釉——以PbO为助熔剂的易熔釉。
它的特点是成熟温度较低,烧熔范围较宽,釉面光泽强,表面平整光滑,弹性好。
?第二节釉的形成一、釉料在加热过程中的变化1.分解反应这类反应包括碳酸盐、硝酸盐、硫酸盐及氧化物的分解和原料中吸附水、结晶水的排除。
2.化合反应在料中出现夜相之前,已有许多生成新化合物的反应在进行。
如Na2CO3与SiO2在500℃以下生成Na2SiO3;CaCO3与高岭土在800℃以下形成钙铝尖晶石(CaO·Al2O3),在800℃以上形成硅酸钙;PbO与SiO2在600~700℃生成PbSiO3。
此外ZnO 和SiO2通过固相反应生成硅锌矿(2ZnO·SiO2)。
3.熔融釉料在两种情况下出现液相。
一是原料本身的熔融,如长石、碳酸盐、硝酸盐的熔化。
另外是一些低共熔物的形成,如碳酸盐与石英、长石;铅丹与石英、粘土;硼酸与石英及碳酸盐;F化物与长石、碳酸盐;乳浊剂与含硼原料、铅丹等。
由于温度的升高,最初出现的液相使粉料由固相反应逐渐转为有液相参与,不断溶解釉料成分,最终使液相量急剧增加,大部分边成熔液。
二、釉层冷却时的变化?1.有些晶相溶解后再析晶,形成微析晶。
2.高温粘度随温度的降低而增加,再继续冷却,釉熔体变成凝固状态。
3.有些物质分解不完全,产生的气味未完全排除,以及坯体中碳素氧化后生成的气体未来得及排除,这些气体在坯体中形成气泡。
?三、坯、釉中间层的形成由于坯、釉化学组成上的差异,烧成时两者相互通过固相反应、相互渗透,在接触面处形成中间层。
坯釉中间层形成好坏对制品的性质,特别是外观质量有非常重要的影响。
第三节釉层的性质(一)釉的熔融态的性质?1.釉的熔融温度范围釉和玻璃一样无固定的熔点,而是在一定的温度范围内逐渐熔化,因而熔化温度有上限和下限之分。
熔融温度的下限系指釉的软化变形点,习惯上称为釉的始熔温度。
熔融温度上限是指完全熔融时的温度,又称为流动温度。
由始熔温度至完全熔融之间的温度范围称为熔融温度范围。
釉的成熟温度可以理解为在某温度下釉料充分熔化,并均匀布于坯体表面,冷却后呈现一定光泽玻璃层时的温度。
釉的成熟温度是在熔融温度范围内选取的。
现在通常用高温显微镜来测定釉料的始熔温度、熔融温度和流动温度。
实验方法如下:274页将磨细的釉料制成¢2mm x 3mm的式样,用高温显微镜观察,当其受热至棱角变圆时的温度为始熔温度;当软化与底盘平面成半球形时的温度为熔融温度;当试样流散开来,高度降至原有的1/3时,此温度(扁平二格温度)。
釉的熔融温度又称为成熟温度即烧成温度,由于釉的组成和结构不同,其成熟温度常常在半球点与流动点之间选取。
釉的熔融温度与釉的化学组成、细度、混合均匀程度及烧成时间有密切关系。
2.影响熔融温度的因素化学组成对熔融性能的影响取决于釉式中Al2O3、SiO2和碱组分的含量和配比。
根据釉式,釉的熔融温度随Al2O3和SiO2的含量增而提高,且Al2O3对熔融温度提高所作的贡献大于SiO2。
碱和碱土金属氧化物作为熔剂,降低釉的熔融温度。
碱金属氧化物的助熔作用强于碱土金属氧化物。
溶剂可分为软熔剂硬熔剂。
前者包括Na2O、K2O、Li2O、PbO,大部分金属属于R2O族。
它们能在低温下起助熔作用。
后者包括Na2O、MgO、ZnO等属于RO族,它们在高温下起起助熔作用。
根据酸度系数可以初步估计釉的熔融温度。
它是指釉中酸性氧化物的摩尔数之比,一般以C·A 表示:C·A=R2O/(R2O+RO+3R2O3)(3-6-1)对于精陶器用含硼釉(除铅釉外),有的学者认为Al2O3与B2O3的某些相似处,故计算时可合并,此时:C·A= SiO2/((R2O+RO)+3(Al2O3+ B2O3))(3-6-2)对于精陶器用含铅釉,由于Al2O3是提高釉的耐酸性的,可作为酸性氧化物,相反B2O3是减弱酸性的,此时:C·A=(SiO2 +Al2O3)/((R2O+RO)+3 B2O3)(3-6-3)酸性系数越大,釉的烧成温度越高。
例如硬瓷釉的组成范围为:(R2O+RO)·(~)Al2O3·(5~12) SiO2,C·A=~。
烧成温度1320~1450℃。
软瓷釉的组成范围为:(R2O+RO)·(~)Al2O3·(3~4) SiO2,C·A=~。
烧成温度1250~1280℃。
此外釉的细度、混合均匀程度、烧成时间对釉的熔融温度也有影响,釉料磨得越细,混合越均匀,烧成时间越长其始熔和熔融温度均相应降低。
(二)釉熔体的粘度、润湿性和表面张力?熔化的釉料能否在坯体表面铺展成平滑的优质釉面,与釉熔体的粘度、润湿性和表面张力有关。
在成熟温度下,釉的粘度过小,则流动性过大,容易造成流釉、堆釉及干缺陷;釉的粘度过大,则流动性差,易引起橘釉、针眼、釉面不光滑,光泽不好等缺陷。
流动性适宜的釉料,不仅能填补坯体表面的一些凹坑,而且还有利于釉与坯体之间的相互作用,生成中间层。
釉熔体的粘度主要取决于其化学组成和烧成温度。
碱金属氧化物对粘度降低的作用以Li2O最大,其次是Na2O,再次是K2O;碱土金属氧化物CaO、MgO、BaO在高温下降低釉的粘度,而在低温中相反地增加釉的粘度。
CaO在低温冷却时使釉的粘度增大,熔融温度范围窄,Zn、PbO对釉的粘度影响与CaO基本相同,粘度增加速度较慢或熔融温度范围宽。
碱土金属阳离子降低粘度顺序为:Ba2+>Sr2+>Ca2+>Mg2+,但它们降低粘度的均匀较碱金属离子弱。
+3价和高价的金属氧化物,如Al2O3、SiO2、ZrO2都增加釉的粘度。
其中B2O3对釉粘度的影响呈现反常,即加入量<15%时,B2O3处于【BO4】状态,粘度随B2O3含量的增加而增大,超过15%时,B2O3处于【BO3】状态,粘度随B2O3含量的增加而减小。
Fe3+比Mg2+能显着降低釉的粘度。
水蒸气、CO、H2S也降低熔融釉的粘度。
一般陶瓷在成熟温度下的粘度值为200Pa·s左右。
釉的表面张力对釉的外观质量影响很大。
表面张力过大,阻碍气体的排除和熔体的均化,在高温时对坯的湿润性不好,容易造成缩釉缺陷;表面张力过小,则易造成“流釉”(当釉的粘度也很小时,情况更严重),并使釉面小气孔破裂时形成针孔难以弥合,形成缺陷。
当坯、釉热膨胀系数差别超出一定范围,无论是“负釉”还是“正釉”均会造成釉层开裂或剥落的缺陷如图3-6-2所示。
2.中间层对坯、釉适应性的影响中间层可促使坯釉间的热应力均匀。
发育良好的中间层可填满坯体表面的隙缝,减弱坯釉间的应力,增大制品的机械强度。
3.釉的弹性、抗张强度对坯釉适应性的影响具有较高弹性(即弹性模量较小)的釉能补偿坯、釉接触层中形变差别所产生的应力和机械作用所产生的应变。
即使坯、釉热膨胀系数相差较大,釉层也不开裂、剥落。
釉的抗张强度高,抗釉裂的能力就强,坯釉适应性就好。
化学组成与热膨胀系数、弹性模量、抗张强度三者间的关系较复杂,难以同时满足这三方面的要求,应在考虑热膨胀系数的前提下使釉是抗张强度较高,弹性较好为佳。
4.釉层厚度对坯釉适应性的影响薄釉层在煅烧时组分的改变比厚釉层大,釉的热膨胀系数降低得也多,而且中间层相对厚度增加,有利于提高釉中的压力,有利于提高坯釉的适应性。
对于厚釉层,坯、釉中间层厚度相对地降低,因而不足以缓和两者之间因热膨胀系数差异而出现的有害应力,不利于坯釉适应性。
釉层厚度对于釉面外观质量有直接影响,釉层过厚就会加重中间层的负担,易造成釉面开裂及其它缺陷,而釉层过薄易发生干釉现象,一般釉层通常小于或通过实验来确定。
第四节釉料制备和施釉确定釉料配方的原则1.根据坯体的烧结性质来调节釉的熔融性质釉料必须在坯体烧结温度下成熟并具有较宽的熔融温度范围(不小于30℃),在此温度范围内釉熔体能均匀的铺在坯体上,不被坯体的微孔吸收造成干釉,在冷却后能形成平整光滑的釉面。
2.使釉的热膨胀系数与坯体热膨胀系数相适应。
一般要求釉的热膨胀系数略低于坯体的膨胀系数,两者相差程度取决于坯釉的种类和性质。
3.坯釉的化学组成要相适应为了保证坯釉紧密结合,形成良好的中间层,应使两者的化学性质,既要相近又要保持适当差别。
一般以坯釉的酸度系数来控制。
酸度强的坯配酸性弱的釉,酸性弱的坯配以偏碱性的釉,含SiO2高的坯配长石釉,含Al2O3高的坯配石灰釉。
4.正确选用原料釉用原料较用原料复杂得多,既有天然原料又有多种化工原料。
天然原料主要有石英、长石、粘土、石灰石、滑石等。
釉料中Al2O3最好用长石而不是粘土引入,以避免因熔化不良而失去光泽。
为提供釉浆的悬浮性,釉中的Al2O3部分地由粘土引入,其用量应限制在10%以下。
引入碳酸钡可使釉更加洁白或增大乳白感;碳酸锶对减少釉中气泡是颇有效的;用等量的萤石置换石灰石,可制成玻化完全、熔融非常好的釉;用硅灰石代替部分长石,能消除釉面针孔缺陷,增加釉面光泽,扩大熔融范围。