材料成型设备
汽车尼龙管成型炉设备工艺原理

汽车尼龙管成型炉设备工艺原理概述尼龙管是一种用于制造汽车冷却系统、刹车管路、燃料系统和油路系统的管道材料。
汽车尼龙管成型炉是用于制造尼龙管的一种特殊设备,其工艺原理主要包括工件加热、熔化、压力成型、冷却等过程。
本文将介绍汽车尼龙管成型炉设备的工艺原理及其相关知识。
设备分类1.垂直成型炉:顶部为模具,下部为加热器和控制装置,利用重力将尼龙颗粒材料自动输送到加热器中,经过熔化后在模具中成型,主要用于生产大直径的管道。
2.水平成型炉:采用卧式结构,工件通过传送带送入成型炉内,加热器和模具平行设置,利用压力和流速控制尼龙材料的成型,主要用于生产小直径管道和异形管道。
工艺原理汽车尼龙管成型炉设备的工艺原理主要包括以下几个方面:工件加热在汽车尼龙管成型炉中,采用电热管、电加热法和加热棒等方式对工件进行加热,使其达到熔点,并以此为基础实现热加工成型。
在加热过程中,需要保持尼龙材料的熔点稳定,避免过度热化造成焦炭、裂纹和气泡等缺陷。
熔化将加热后的尼龙材料通过熔化,使其变成一种流动状态,方便成型。
熔化需要控制加热器的温度、熔融材料的速度和流向,以达到适当的熔化状态。
压力成型在汽车尼龙管成型炉中,采用压力成型的方式来实现材料的成型。
成型时,工件被挤入模具中,应用足够的压力进行形状的成型。
压力成型时,需要控制形状、温度、压力等参数,以保证产品的合格率和成型质量。
冷却成型完成后,尼龙材料需要进行冷却。
冷却可分为自然冷却和强制冷却两种方式。
在汽车尼龙管成型炉中,通常采用冷却水循环的方式,来对成型的尼龙管进行冷却处理,以达到预定形状的效果。
常见问题Q1:汽车尼龙管成型炉对环境的影响大吗?汽车尼龙管成型炉在成型过程中,会产生少量的尾气和废气,但不会对环境造成大的影响。
同时,这些废气和尾气可以通过处理高效地净化,以确保环境的可持续性发展。
Q2:浸泡式尼龙管热加工和汽车尼龙管成型炉有何区别?浸泡式尼龙管热加工和汽车尼龙管成型炉在热加工原理上是类似的,但是二者的工艺流程并不相同。
《高分子材料成型加工设备》--第五章--压延机
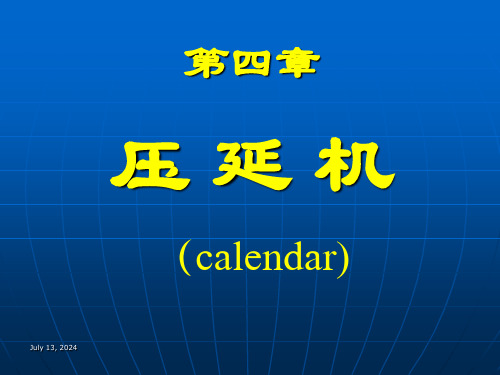
2.1 辊筒长度和长径比 这是表征压延机规格大小的特征参数。
1、辊筒长度和直径 辊筒长度是指辊筒工作部分的长度,表征了可压
延制品的最大幅度。 辊筒直径是指辊筒工作部分的直径。表征了压延
机规格的大小。
L+X L
July 13, 2024
D
2、辊筒长径比 辊筒工作部分长度和直径的比值叫长径比(L/D)。
A、压延时两辊筒消耗功率与辊筒的线速度成正比 若两辊筒线速度分别为V1、V2,功率分别为N1、
N2,则: N1/N2=V1/V2
July 13, 2024
B、贴胶时所消耗的功率仅为总功率的6% N贴=0.06N总η
式中 N贴——贴胶辊功率, N总——有效总功率, η——传动总效率。
根据以上两点,就可以计算出各个辊筒所占的功 率。
式准确地求得。现介绍几种经验公式近似地计算: 1)单台电动机传动时的功率计算
A、按辊筒线速度计算 N =a·L·v
B.按辊筒数目计算 N=K·L·n
式中 a, K——计算系数 L——辊筒工作部分长度 v——压延线速度 n——辊筒个数。
July 13, 2024
以上两式的共同缺点是没有考虑被加工胶料的性 质和加工方法,以及辊筒的直径对功率的影响, 而它们对功率消耗的影响又是十分大的。可见上 述二个公式都是片面的。
July 13, 2024
3)超前角 超前区和滞后区的交界面称之为临界面即cd面,即 胶料运动速度等于辊筒的线速度的面,其厚度为h, co’或do与辊筒中心线的夹角φ称为超前角。
4)计算 假定:压延材料从辊距中引出后其厚度等于辊距的 大小。经过推导,可以得出如下结果:
a、超前角φ:
July 13, 2024
波纹管成型机的原理

波纹管成型机的原理
波纹管成型机是一种用途广泛的金属成型设备,它的原理基于以下几个步骤:
1. 材料预处理:首先将金属原料进行预处理,通常是通过剪切或切割机将原料切割成适当的大小和形状。
2. 加热:将切割好的金属原料放入波纹管成型机的加热区域。
加热的目的是让金属原料达到足够的可塑性,以便在后续的成型过程中能够被轻松形成。
3. 成型:一旦金属原料达到适当的温度,它会通过传动系统被送入成型区域。
成型区域通常包含一个上模和一个下模,它们的形状会被电脑控制的液压机械系统精确地调整。
金属原料在成型区域中受到上下模的挤压和塑性变形,逐渐形成波纹管的形状。
4. 冷却和固化:成型后的波纹管被送入冷却区域,通过冷却使金属原料固化并保持其形状。
冷却通常通过局部或整体水冷却系统进行。
5. 最后的处理:成型后的波纹管可能需要一些后续的加工步骤,如切割、清洗、表面处理等,以满足特定的需求。
总之,波纹管成型机利用热加工和塑性变形原理,通过加热、成型、冷却和后续处理等步骤,将金属原料转变为波纹管的形状。
这种设备具有高效、精确和可重
复性的特点,在许多行业中都有广泛的应用。
挤压成型机操作说明

挤压成型机操作说明一、引言随着工业生产的不断发展,挤压成型机在塑料加工、金属制品生产等领域中发挥着重要作用。
本文旨在向操作者提供详细的挤压成型机操作说明,以确保操作的安全性和生产的高效性。
二、设备概述挤压成型机是一种将材料通过机械压力挤压成型的设备。
其结构主要包括进料系统、挤压系统、冷却系统和控制系统等部分。
在操作挤压成型机之前,应先熟悉其各部分的功能和操作方式。
三、安全操作1. 穿戴个人防护装备:操作者在操作挤压成型机前,应穿戴好符合安全标准的个人防护装备,如安全帽、护目镜、防护手套等。
2. 检查设备安全:在操作前,需仔细检查挤压成型机各部件的运行状况是否正常,如有发现损坏或异常的地方,应及时报告维修人员进行处理。
3. 维护清洁操作环境:保持操作环境的干净整洁,减少因杂物造成的安全隐患。
四、操作步骤1. 准备材料:根据生产需求,准备好需要加工的材料,并进行初步处理,确保其质量符合要求。
2. 启动挤压成型机:按照操作面板上的启动程序依次操作,确保设备正常启动。
3. 设置生产参数:根据产品要求,在控制面板上设置合适的挤压速度、温度及压力等参数。
4. 进料操作:将处理好的材料放入进料系统,并确保其均匀地进入到挤压螺杆中。
5. 挤压操作:挤压机螺杆旋转,通过内部压缩将材料挤压出模具,形成所需产品的形状。
6. 冷却固化:挤压出的产品通过冷却系统迅速冷却,以使其迅速固化。
7. 剪切成型:冷却固化后的产品经过剪切机构的作用,按照预定尺寸进行剪切成型。
8. 整理检查:将剪切成型后的产品进行整理和检查,确保无明显的缺陷和变形。
9. 关闭机器:在确认生产完毕后,按照操作面板上的关闭程序依次操作,停止挤压成型机的运行。
五、操作注意事项1. 遵循操作规程:严格按照挤压成型机的操作规程进行操作,避免违规操纵导致事故发生。
2. 定期维护保养:挤压成型机需要定期进行保养维护,如定期清洁设备、检查润滑油量等。
3. 注意材料选择:选择适合挤压成型机的材料,避免使用不符合要求的材料导致操作困难或设备损坏。
成型加工设备 4.密炼机

小孔并联
因蒸汽或冷却水 在孔中易走捷径 及呆滞现象,传 热效果仍不理想
小孔串联式
因蒸汽或冷却水 流速度大,导热 系数高(孔为机 械加工而成), 故传热效果好。
3、密封装置
基本结构形式:由动环和定环组成。动环与 轴颈相连,而定环与侧壁相连,动定环之间 压紧并相对运动,故接触面要耐磨,一般堆 焊硬质合金。
(1)外压式端面密封装置
结构简单、使用寿命 长 ,适用于低速低压 密炼机
(2)内压式端面自动密封装置
密封效果好,适 用于高压快速密 炼机。
(3)反螺纹与自压端面接触密封装置
旧式慢速橡胶密炼 机采用。不能用于 塑炼密炼机。
(3)夹套式
能加热或冷却侧壁 ,
传热效果比上两种好。 塑料密炼机多采用这 种形式和钻孔式,同 样也适合于橡胶密炼 机。
(4)钻孔式
包括:大孔串联、小孔并联、小孔串联三 种形式,其加热冷却效果依次递增。
小孔串联--加热冷却效果最好的结 构形式
大孔串联:
ห้องสมุดไป่ตู้
橡胶密炼机的混炼室容量一般比塑料密炼机 的混炼室大。 橡胶密炼机主要规格有:50(橡塑通用)、 75、245、253、270升。 而塑料密炼机主要规格为:46、50(橡 塑通用)、75。
第二节 基本结构
一、整体结构与传动系统 1、整体结构
五个部分:①密炼室和转子部分;②加料和压 料机构部分;③卸料机构部分;④传动装置部 分;⑤机座部分。 五个系统:①加热冷却系统;②气压传动系统; ③液压传动系统;④润滑系统;⑤电控系统。
4、密炼机转子表面的突棱,使胶料作轴向移动 和翻转。
材料成型设备及控制

材料成型设备及控制课程负责人:陈泽中开课部门:材料学院编写时间:2009 年 2 月一、课程内容简介《材料成型设备及控制》是材料成型及控制工程专业的基础课,是其骨干课程之一。
主要包括锻压设备、挤压与拉拔设备、塑料成型设备、连续铸造设备、焊接设备、轧制设备、剪切机与矫直机的基本结构、控制参数和性能等内容。
二、教学目标本课程的教学目标是让学生在本科学习期间掌握材料成型设备及控制的基础知识,如锻压设备、挤压与拉拔设备、塑料成型设备、连续铸造设备、焊接设备、轧制设备、剪切机与矫直机等。
重点掌握锻压设备、塑料成型设备等的结构、控制参数选用和性能。
熟悉挤压与拉拔设备、连续铸造设备、焊接设备、轧制设备、剪切机与矫直机的结构、控制参数与性能。
了解材料成型设备的现状及发展趋势。
三、教学方式主要采用理论教学,辅以教学实验和作业练习。
五、教学内容与要求(一)理论教学第1章锻压设备(4学时)。
包括:1.1 锻压设备分类,1.2 锻锤,1.3 曲柄压力机,1.4 液压机。
要求掌握曲柄压力机和液压机的结构和性能,了解锻压设备分类、锻锤的结构和性能。
第2章挤压与拉拔设备(2学时)。
包括:2.1 挤压设备,2.2 拉拔设备。
要求熟悉挤压设备和拉拔设备的结构和性能。
第3章塑料成型设备(5学时)。
包括:3.1 概述,3.2 塑料注射成型机,3.3 塑料挤出成型机,3.4 塑料吹塑成型机。
要求掌握塑料注射、挤出和吹塑成型机的结构和性能,了解塑性成型设备概况。
第4章连续铸造设备(4学时)。
包括:4.1 连续铸造的分类,4.2 传统连续铸造设备,4.3 连铸连轧设备,4.4 连续铸轧设备。
要求熟悉传统连续铸造设备、连铸连轧设备和连续铸轧设备的结构和性能,了解连续铸轧设备的分类。
第5章焊接设备(4学时)。
包括:5.1 埋弧焊,5.2 气体保护焊,5.3 电渣焊,5.4 等离子弧焊接设备。
要求熟悉埋弧焊、气体保护焊、电渣焊、等离子弧焊接设备的结构和性能,了解焊接设备概况。
复合材料成型工艺与设备之模压设备
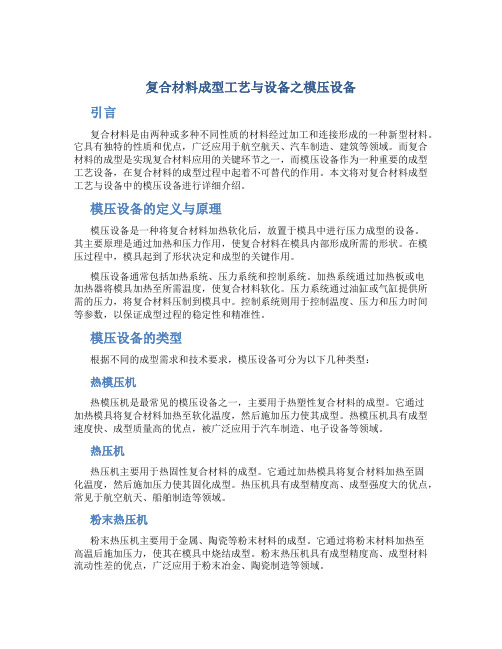
复合材料成型工艺与设备之模压设备引言复合材料是由两种或多种不同性质的材料经过加工和连接形成的一种新型材料。
它具有独特的性质和优点,广泛应用于航空航天、汽车制造、建筑等领域。
而复合材料的成型是实现复合材料应用的关键环节之一,而模压设备作为一种重要的成型工艺设备,在复合材料的成型过程中起着不可替代的作用。
本文将对复合材料成型工艺与设备中的模压设备进行详细介绍。
模压设备的定义与原理模压设备是一种将复合材料加热软化后,放置于模具中进行压力成型的设备。
其主要原理是通过加热和压力作用,使复合材料在模具内部形成所需的形状。
在模压过程中,模具起到了形状决定和成型的关键作用。
模压设备通常包括加热系统、压力系统和控制系统。
加热系统通过加热板或电加热器将模具加热至所需温度,使复合材料软化。
压力系统通过油缸或气缸提供所需的压力,将复合材料压制到模具中。
控制系统则用于控制温度、压力和压力时间等参数,以保证成型过程的稳定性和精准性。
模压设备的类型根据不同的成型需求和技术要求,模压设备可分为以下几种类型:热模压机热模压机是最常见的模压设备之一,主要用于热塑性复合材料的成型。
它通过加热模具将复合材料加热至软化温度,然后施加压力使其成型。
热模压机具有成型速度快、成型质量高的优点,被广泛应用于汽车制造、电子设备等领域。
热压机热压机主要用于热固性复合材料的成型。
它通过加热模具将复合材料加热至固化温度,然后施加压力使其固化成型。
热压机具有成型精度高、成型强度大的优点,常见于航空航天、船舶制造等领域。
粉末热压机粉末热压机主要用于金属、陶瓷等粉末材料的成型。
它通过将粉末材料加热至高温后施加压力,使其在模具中烧结成型。
粉末热压机具有成型精度高、成型材料流动性差的优点,广泛应用于粉末冶金、陶瓷制造等领域。
冷模压机冷模压机主要用于冷却条件下的复合材料成型。
它通过施加压力,将复合材料在低温条件下成型。
冷模压机具有成本低、成型周期短的优点,适用于某些对成型温度要求不高的复合材料。
复合材料模压成型设备的结构强度与稳定性性能评价

复合材料模压成型设备的结构强度与稳定性性能评价复合材料模压成型是一种常用的加工方法,用于制造具有高强度和轻量化特性的复合材料制品。
在模压成型过程中,设备的结构强度和稳定性是影响制品质量和生产效率的重要因素。
本文将对复合材料模压成型设备的结构强度和稳定性性能进行评价。
首先,复合材料模压成型设备的结构强度是指设备能够承受的外部载荷,以及设备中各组件的强度能力。
要评价设备的结构强度,需要对设备进行结构分析和强度计算。
结构分析可以通过有限元方法进行,通过建立模型并施加模拟载荷,分析设备在不同工况下的应力分布和变形情况。
强度计算则可以根据材料的弹性模量、屈服强度等参数,结合设备的尺寸和几何形状,计算设备在极限载荷下是否会发生破坏。
评价设备结构强度时,需要确保设备在正常工作条件下不会发生破坏,并且具备一定的安全系数。
其次,设备的稳定性性能也是评价复合材料模压成型设备的重要指标。
稳定性指设备在作用力下的不易产生失稳或变形的能力。
对于模压成型设备来说,稳定性能的评价主要包括抗变形能力、抗震动能力和抗疲劳能力。
抗变形能力是指设备在工作过程中,由于热胀冷缩或外部力影响而引起的变形情况。
抗震动能力是指设备在震动环境下的耐受能力,这主要通过对设备的振动分析来评价。
抗疲劳能力是指设备在长时间运行工况下不会因疲劳损伤而失效。
评价稳定性性能需要考虑材料的热膨胀系数、结构的刚度和阻尼等因素,综合分析设备的稳定性能。
为了确保设备的结构强度和稳定性,需要在设计和制造过程中考虑以下几个方面。
首先,选择适合的材料,复合材料具有优异的强度和刚度,同时具备轻量化的特点,是模压成型设备的首选材料。
其次,优化设备的结构,合理设计设备的刚度和连结方式,通过增加设备的刚度和刚性连接的方式来提高结构的强度和稳定性。
第三,加强设备的调试和检验工作,在设备运行之前对其进行全面的检查和测试,确保设备的性能符合要求。
最后,进行定期的维护和保养工作,检查设备是否存在磨损、松动或腐蚀等情况,并进行及时的维修和更换。