天然气制备合成气
第2章 合成气

3、脱碳方法的选择
氨加工的品种
取决于
气化所用原料和方法 后继气体精炼方法 各脱碳方法的经济性
2.2.4.原料气的精炼(CO、CO2、O2、水等)
1、铜氨溶液吸收法 氯化铜氨液 吸 蚁酸铜氨液 收 碳酸铜氨液 液 醋酸铜氨液 (1)、铜液的组成
总量≤10ppm
铜离子浓度(铜比) 氨含量 醋酸浓度 残余CO、CO2(再生液)
3、甲烷化法
互逆 甲烷蒸汽转化 机理分析:
甲烷蒸汽转化机理
CH4 + [ ] ? [CH 2 ]
[CO] [ ] + CO
甲烷化机理
CO + [ ] [CO]
H2
[CH2 ] + H2O [CO] + 2H2
[CO] + [ ] [C ] + [O]
[C] + H2 ? [CH2 ] H2 揪快? CH4 [ ]
CH 4 + H 2O CO + 3H 2
H2O + [ ] [O] + H 2
[O] + H2 ? H2O [ ]
CO2 + [ ] ? [CO2 ]
[CO2 ] + [ ] [CO] + [O* ]
CO + [O] [ ] + CO2
CO + H 2O CO2 + H 2
利用催化剂使CO、CO2加氢生成CH4使气体 精炼的方法,可使CO、CO2&度增加都会造成扩散系数下降
5.活性系数与催化剂用量
活性系数指真实工业条件下的使用活性与标准条件下的比值 催化剂用量:
VK
yCO ,2 dy G CO = r òyCO ,1 xA k
2合成气(化学工艺学)解析

K P1
P CO
P3 H2
P P CH 4 H 2 O
K P2
P P CO 2 H 2 P CO P H 2 O
b.平衡组成的计算
已知条件: m原 料 气 中 的 水 碳 比 (m H2O)
CH4 P 系 统 压 力 ; T 转 化 温 度 假定:无炭黑析出
计算基准:1mol CH4 在甲烷转化反应达到平衡时,设x为按式(2-3)转化了
压力和水碳比确定后,按平衡甲烷的浓度来确定温度。一般要
求yCH4<0.005,出口温度应为1000℃ 左右。实际生产中,转
化炉出口温度比达到出口气体浓度指标对应的平衡温度高, 这个差值叫平衡温距。
T =T-Te(实际温度-平衡温度) 平衡温距低,说明催化剂活性好。一、二段平衡温距通常分 别为 10~15 ℃ 和 15~30 ℃ 。
为代表来讨论气态烃类蒸汽转化 的主要反应及其控制条件。
➢ 烃类主要进行的反应 烷烃
烯烃 CnH2n n2H2O34nCH4 n4CO2 CnH2n nH2OnCO2nH2 CnH2n 2nH2OnCO2 3nH2
2.1.1.1 甲烷蒸汽转化反应
主要反应
高温、催化 剂
( 1 ) C 4 H H 2 O = C 3 H O 2 2.4 0 km 6 J o ( 2 ) C H O 2 O = C 2 H O 2 4 .2 k 1 /m J
水碳比 反应温度 反应压力
➢ 温度增加,甲烷平衡含量下降,反应温度每降 低10℃,甲烷平衡含量约增加1.0%-1.3%;
➢ 增加压力,甲烷平衡含量随之增大;
➢ 增加水碳比,对甲烷转化有力;
➢ 甲烷蒸汽转化在高温、高水碳比和低压下进行 有利
天然气转化成柴油的原理
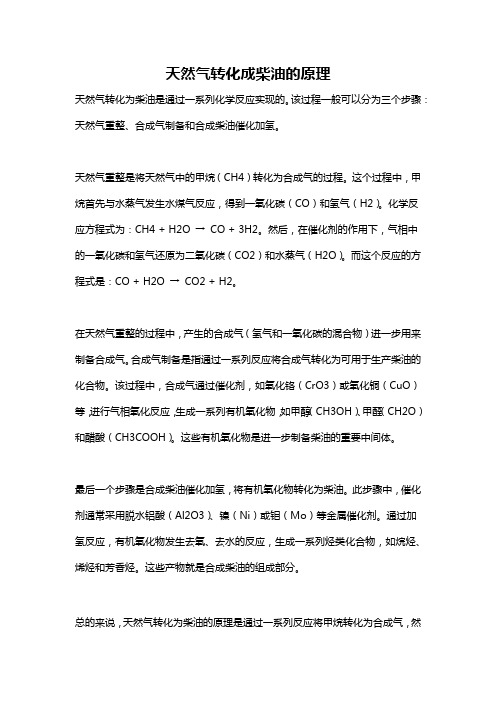
天然气转化成柴油的原理天然气转化为柴油是通过一系列化学反应实现的。
该过程一般可以分为三个步骤:天然气重整、合成气制备和合成柴油催化加氢。
天然气重整是将天然气中的甲烷(CH4)转化为合成气的过程。
这个过程中,甲烷首先与水蒸气发生水煤气反应,得到一氧化碳(CO)和氢气(H2)。
化学反应方程式为:CH4 + H2O →CO + 3H2。
然后,在催化剂的作用下,气相中的一氧化碳和氢气还原为二氧化碳(CO2)和水蒸气(H2O)。
而这个反应的方程式是:CO + H2O →CO2 + H2。
在天然气重整的过程中,产生的合成气(氢气和一氧化碳的混合物)进一步用来制备合成气。
合成气制备是指通过一系列反应将合成气转化为可用于生产柴油的化合物。
该过程中,合成气通过催化剂,如氧化铬(CrO3)或氧化铜(CuO)等,进行气相氧化反应,生成一系列有机氧化物,如甲醇(CH3OH)、甲醛(CH2O)和醋酸(CH3COOH)。
这些有机氧化物是进一步制备柴油的重要中间体。
最后一个步骤是合成柴油催化加氢,将有机氧化物转化为柴油。
此步骤中,催化剂通常采用脱水铝酸(Al2O3)、镍(Ni)或钼(Mo)等金属催化剂。
通过加氢反应,有机氧化物发生去氧、去水的反应,生成一系列烃类化合物,如烷烃、烯烃和芳香烃。
这些产物就是合成柴油的组成部分。
总的来说,天然气转化为柴油的原理是通过一系列反应将甲烷转化为合成气,然后将合成气制备为有机氧化物。
最后,通过催化加氢反应,将有机氧化物转化为柴油。
这个过程中的化学反应涉及到催化剂、高温和高压等条件的控制,以及反应物和产物的多相状态转换。
天然气转化为柴油的工艺在能源利用和环境保护方面具有一定的优势,但也需要注意对催化剂的选择、反应条件的控制等技术问题。
合成天然气制备技术的研究
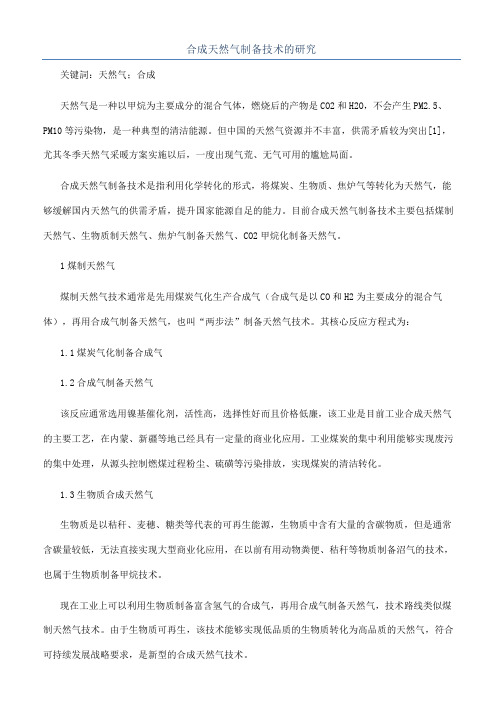
合成天然气制备技术的研究关键詞:天然气;合成天然气是一种以甲烷为主要成分的混合气体,燃烧后的产物是CO2和H2O,不会产生PM2.5、PM10等污染物,是一种典型的清洁能源。
但中国的天然气资源并不丰富,供需矛盾较为突出[1],尤其冬季天然气采暖方案实施以后,一度出现气荒、无气可用的尴尬局面。
合成天然气制备技术是指利用化学转化的形式,将煤炭、生物质、焦炉气等转化为天然气,能够缓解国内天然气的供需矛盾,提升国家能源自足的能力。
目前合成天然气制备技术主要包括煤制天然气、生物质制天然气、焦炉气制备天然气、CO2甲烷化制备天然气。
1煤制天然气煤制天然气技术通常是先用煤炭气化生产合成气(合成气是以CO和H2为主要成分的混合气体),再用合成气制备天然气,也叫“两步法”制备天然气技术。
其核心反应方程式为:1.1煤炭气化制备合成气1.2合成气制备天然气该反应通常选用镍基催化剂,活性高,选择性好而且价格低廉,该工业是目前工业合成天然气的主要工艺,在内蒙、新疆等地已经具有一定量的商业化应用。
工业煤炭的集中利用能够实现废污的集中处理,从源头控制燃煤过程粉尘、硫磺等污染排放,实现煤炭的清洁转化。
1.3生物质合成天然气生物质是以秸秆、麦穗、糖类等代表的可再生能源,生物质中含有大量的含碳物质,但是通常含碳量较低,无法直接实现大型商业化应用,在以前有用动物粪便、秸秆等物质制备沼气的技术,也属于生物质制备甲烷技术。
现在工业上可以利用生物质制备富含氢气的合成气,再用合成气制备天然气,技术路线类似煤制天然气技术。
由于生物质可再生,该技术能够实现低品质的生物质转化为高品质的天然气,符合可持续发展战略要求,是新型的合成天然气技术。
生物质气化的主体反应过程如下:1.4CO2甲烷化合成天然气技术全世界每年排放大量的CO2,对环境造成了严重的污染,常规理解下CO2是没有再利用价值的废气,其实CO2是潜在的含碳资源,首先CO2是必不可缺的光合作用的原料,其次,CO2也可以作为反应物直接合成天然气,从而实现碳资源的循环利用。
化学工艺学 第 2 章 合成气
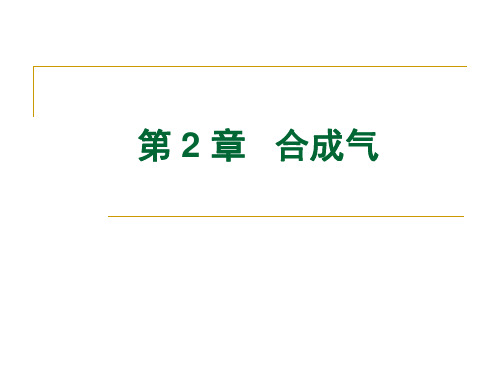
2.1 合成气的制取
2.1.1 烃类蒸汽转化
2.1.1.5 转化反应工艺流程及转化炉
燃料用天然气 11
8 9 过 热 蒸 汽
5
2
1 3
一段转化
4
二段转化
对流段
7 10 蒸汽 空气 原料天然气 锅炉给水 转化气去变换 6
氢氮气来自合成
天然气蒸汽转化工艺流程
1、钴钼加氢反应器;2、氧化锌脱硫槽;3、对流段;4、辐射段(一段炉);5、二段转化炉;6、第一废热锅炉;7、批二废热 锅炉;8、汽包;9、辅助锅炉;10、排风机;11、烟囱
图解法或迭代法求解x,y
2.1 合成气的制取
2.1.1 烃类蒸汽转化
2.1.1.1 甲烷蒸汽转化反应
甲烷蒸汽转化反应的热力学分析: c.影响甲烷蒸汽转化反应平衡组成的因素
水碳比 反应温度 反应压力
2.1 合成气的制取
2.1.1 烃类蒸汽转化
2.1.1.1 甲烷蒸汽转化反应
甲烷蒸汽转化反应的热力学分析: c.影响甲烷蒸汽转化反应平衡组成的因素
2.1 合成气的制取
2.1.1 烃类蒸汽转化
2.1.1.1 甲烷蒸汽转化反应
甲烷蒸汽转化反应的热力学分析: c.影响甲烷蒸汽转化反应平衡组成的因素
温度增加,甲烷平衡含量下降,反应温度每降低 10℃,甲烷平衡含量约增加1.0%-1.3%;
增加压力,甲烷平衡含量随之增大;
增加水碳比,对甲烷转化有利; 甲烷蒸汽转化在高温、高水碳比和低压下进行有利
立式圆筒,内径约3米,高约13米;壳体材质 为碳钢,内衬不含硅的耐火材料,炉壳外保温。
上部有燃烧空间的固定床绝热式催化反应器。
合成氨技术的原理和应用

合成氨技术的原理和应用1. 原理合成氨是一种重要的工业原料,广泛用于农业、化工和能源等领域。
合成氨技术主要通过合成气的反应来制备氨气。
合成气是指由氢气和一氧化碳组成的气体混合物,一般通过以下两种方法得到:1.通过煤炭气化产生合成气。
煤炭气化是将煤炭在高温和高压的条件下与氧气或二氧化碳反应,生成合成气。
2.通过天然气重整产生合成气。
天然气重整是将天然气与水蒸气反应,在催化剂的作用下生成合成气。
合成氨的主要反应是哈柏-卡什反应(Haber-Bosch reaction),反应方程式如下:N2 + 3H2 -> 2NH3该反应发生在高温(400-500摄氏度)和高压(200-350兆帕)的条件下,需要催化剂的存在。
2. 应用合成氨具有广泛的应用领域,以下是一些常见的应用:2.1 农业合成氨被广泛用作农业肥料中的主要原料,用来满足植物对氮素的需求。
合成氨可以作为氨基酸和蛋白质的合成原料,促进作物的生长和发育。
此外,合成氨还可以用于改良土壤质量,提高土地的肥力和农作物的产量。
2.2 化工合成氨被广泛用于化工工业中的生产过程中。
它可以用作制造尿素、硝酸和其他化学品的原料。
合成氨也可以用于制造合成树脂、炸药和染料等化学产品。
2.3 能源合成氨可以用作燃料的替代品,用于替代传统的化石燃料。
合成氨的燃烧产生的废气较少,燃烧效率高,对环境污染较小。
因此,合成氨可以作为清洁能源的一种选择。
2.4 其他应用除了上述应用领域,合成氨还有一些其他的应用。
例如,合成氨可以用作金属表面处理的溶剂,用于清洗、除锈和防腐。
合成氨也可以用作氮化硼和氮化铝等特殊材料的制备。
3. 总结合成氨技术的原理是通过合成气的反应制备氨气,主要反应是哈柏-卡什反应。
合成氨广泛应用于农业、化工和能源等领域,用于制备肥料、化学品以及作为清洁能源的替代品。
此外,合成氨还有一些其他的应用,例如金属表面处理和特殊材料制备等。
通过合成氨技术,我们能满足不同领域对氨气的需求,推动农业发展、化工工业的进步以及环境污染的减少。
天然气转化制备合成气工艺进展

图2 G HR 示 意 图
为 了降 低投 资并使 能量 得 到更 合 理 的利 用 , 出现 了取 消 第 一 段 蒸 汽 重 整 用 火 管 而 以第 二段
艺 , nd L 1e的 C R ( o ie uohm ̄lR A C mbnd A tte e fr r ̄进 一 步 将 两段 转 化 置 于一 个 管壳 式 反 ome)g 应器 内完 成而 减少 了设 备 。此外 , 对 原料 天然 针
困
图 3 G R 示意 图 A
2 2 1 气体加热转化工艺( H ) . G R
II C 开发 的 G HR( 体 加热 转 化 ) 艺 , 气 工 巳在 合 成氨 装 置 中得到 工业 应用 , 甲醇 装置 则 首 先用
于澳大利 亚 海 上 平 台 的 Vioi5 4× ×14/ c r . t a 0ta 甲醇 厂 (94年 末 建成 )GHR 的 主要 特 点 是 以 19 . 二段 自热转 化 所 产 出的 热 量 作 为 一 段 蒸 汽 转 化
气工艺, 中有 一些 已获 得工业 应用 。此外 , 其 为
维普资讯
20 年第l 综述与专论 02 期
江 西 化 工
一
・ 5・ 2
降低台 戚气 的氢碳 比 , 原料 中加 入 C ( 在 O2补碳 )
的研究 也 受到重 视 。
个二级氧化反应器开发成功的联合 重整工艺 ,
件T收率太低 . 还远不 能工业 化。把 甲烷转化为
合成气 , 进一步合成氨 、 甲醇 . 或者利 用 C O再合
成一系列精细化工产品以及燃料和烯烃 , 目前 是 天然气化工上应用最广 泛的一条技术路线 , 天然 气制合成气工艺是整个天然气化 工的基础和龙
使用化学技术进行合成气转化的关键步骤

使用化学技术进行合成气转化的关键步骤在能源危机日益加深的背景下,合成气转化技术成为了当今最为重要的能源转化路径之一。
合成气转化是将天然气、煤炭等碳基资源转化为液体燃料和化学品的过程。
而在这一过程中,化学技术扮演着至关重要的角色。
本文将围绕使用化学技术进行合成气转化的关键步骤展开论述。
首先,当谈及合成气转化的关键步骤时,不得不提到合成气的制备。
合成气包括一氧化碳(CO)和氢气(H2),是合成液体燃料和化学品的基础原料。
制备合成气的方法多样,其中最常见的是煤气化和天然气重整。
煤气化是将固体煤转化为气体燃料的过程,通过高温和压力下的反应,将煤炭分解成一氧化碳和氢气。
天然气重整则是将甲烷等碳氢化合物转化为合成气的过程,通过与水蒸气催化反应,产生一氧化碳和氢气。
不论哪种方法,都需要借助催化剂来实现高效的转化。
其次,一氧化碳(CO)和氢气(H2)在合成气转化过程中起着重要的作用。
一氧化碳是浓缩能源,而氢气则具有高能量密度。
两者在合成气转化过程中可以先后或并行地通过不同的催化反应进行转化,产生液体燃料和化学品。
例如,通过费舍尔-特罗普切齐反应,将一氧化碳和氢气转化为甲醇,进而制备出柴油和其他化学品。
而通过沃特曼-伊沃诺夫反应,则可以将一氧化碳和氢气高效地转化为烯烃和芳香烃等有机化合物。
催化剂的选择和设计对于这些反应的高效进行至关重要。
除此之外,合成气转化过程中还存在氧化及还原的关键步骤。
氧化和还原反应在合成气转化中是相互交替进行的,这可以通过调控氧气的供应来实现。
在氧化反应中,氢气和一氧化碳会与氧气反应生成水蒸气和二氧化碳。
而在还原反应中,水蒸气和二氧化碳则可以通过与一氧化碳和氢气的反应还原为一氧化碳和氢气,从而循环再利用。
这种循环的氧化还原反应实现了合成气转化过程的高效和可持续。
此外,合成气转化过程中的分离和纯化步骤也是不可忽视的。
由于合成气中含有大量的杂质,如硫化物、氮气和水蒸气等,需要通过分离和纯化来提取所需的产品。
- 1、下载文档前请自行甄别文档内容的完整性,平台不提供额外的编辑、内容补充、找答案等附加服务。
- 2、"仅部分预览"的文档,不可在线预览部分如存在完整性等问题,可反馈申请退款(可完整预览的文档不适用该条件!)。
- 3、如文档侵犯您的权益,请联系客服反馈,我们会尽快为您处理(人工客服工作时间:9:00-18:30)。
此文档收集于网络,如有侵权请联系网站删除 只供学习与交流 天然气制备合成气 天然气作为一种清洁、环境友好的能源,越来越受到广泛的重视。天然气作为一种清洁、环境友好的能源,越来越受到广泛的重视。制合成气是间接利用天然气的重要步骤,也是天然气制氢的基础,充分了解天然气制合成气 的工艺与催化剂对于我们进一步研究天然气的利用将有很大帮助。天然气中甲烷含量一般大于90%,其余为小量的乙烷、丙烷等气态烷烃,有些还含有少量氮和硫化物。其他含甲烷等气态烃的气体,如炼厂气、焦炉气、油田气和煤层气等均可用来制造合成气。 目前工业上有天然气制合成气的技术主要有蒸汽转化法和部分氧化法。本文主要对蒸汽转化法进行具体的描述,并具体介绍此工艺的发展趋势。 蒸气转化法
蒸气转化法是目前天然气制备合成气的主要途径。蒸汽转化法是在催化剂存在及高温条件下,使甲烷等烃类与水蒸气反应,生成COH、2等混合气,其主反应为:
2243HCOOHCH,mol/206298KJH 该反应是强吸热的,需要外界供热。因为天然气中甲烷含量在90%以上,而甲烷在烷烃中热力学最稳定,其他烃类较易反应,因此在讨论天然气转化过程时,只需考虑甲烷与水蒸气的反应。 甲烷水蒸气转化反应和化学平衡
甲烷水蒸气转化过程的主要反应有: 2243HCOOHCH,mol/206298KJH
222442HCOOHCH,mol/165298KJH
222HCOOHCO,mol/9.74298KJH
可能发生的副反应主要是析碳反应,它们是: 242HCCH,mol/9.74298KJH
22COCCO,mol/5.172-298KJH
OHCHCO22,mol/4.131-298KJH 此文档收集于网络,如有侵权请联系网站删除 只供学习与交流 甲烷水蒸气转化反应必须在催化剂存在下才有足够的反应速率。倘若操作条件不适当,析碳反应严重,生成的碳会覆盖在催化剂内外表面,致使催化剂活性降低,反应速率下降。析碳更严重,床层堵塞,阻力增加,催化剂毛细孔内的碳遇水蒸汽会剧烈汽化,致使催化剂崩裂或粉化,迫使停工,经济损失巨大。所以对于烃类蒸汽转化过程要特别主要防止析碳,而高温有利于甲烷裂解析碳,不利于一氧化碳歧化析碳,也不利于还原析碳,却有利于碳被水蒸气所气化,温度越高,水蒸气比例越大,则越有利于消碳;如果气相中22COH、分压很大时,均有利于抑制析碳。 由此可见,影响甲烷水蒸气转化反应平衡的主要因素有温度、水碳比和压力。 温度的影响 甲烷与水蒸气反应生成2HCO和吸热的可逆反应,高温对平衡有利,即
2HCO和的平衡产率高,4CH平衡含量低。一般情况下,当温度提高10℃,甲烷的平衡含量可降低1%-1.3%,高温对一氧化碳变换反应的平衡不利,可以少生成二氧化碳,而且高温也会抑制一氧化碳歧化和还原析碳的副反应。但是,温度过高,会有利于甲烷裂解,当温度高于700℃时,甲烷均相裂解速率很快,会大量析出碳,并沉淀在催化剂和器壁上。 水碳比的影响 水碳比对于甲烷转化影响重大,高的水碳比有利于甲烷的蒸气重整反应,在800℃、2Mpa条件下,水碳比由3提高到4时,甲烷平衡含量由8%将至5%,可见水碳比对甲烷平衡含量影响是很大的。同时,高水碳比也有利于抑制析碳副反应。 压力的影响 甲烷蒸汽转化反应是体积增大的反应,低压有利于平衡,当温度800℃、水碳比4时,压力由2Mpa降低到1Mpa时,甲烷平衡含量由5%降至2.5%。低压也可抑制一氧化碳的两个析碳反应,但是低压对甲烷裂解析碳反应平衡有利,适当加压可抑制甲烷裂解。压力对一氧化碳变换反应平衡无影响。 总之,从反应平衡考虑,甲烷水蒸气转化过程应该用适当的高温、稍低的压力和高水碳比。 甲烷水蒸气转化催化剂
甲烷水蒸气转化,在没有催化剂的情况下反应速率很慢,然而在高温下甲烷会裂解,这样会导致没有工业生产价值,所以必须使用催化剂。催化剂的组成和此文档收集于网络,如有侵权请联系网站删除 只供学习与交流 结构决定了其催化性能,而对其使用是否得当会影响其性能的发挥。甲烷水蒸气转化对催化剂的基本要求是高强度、高活性、抗析碳、热稳定性好。 工业装置使用的催化剂均以Ni为活性组分。载体通常都用硅铝酸钙、铝酸钙以及难熔的耐火氧化物,如32OAl、MgO、CaO、ZIo2、2TiO等。随着工业条件的改变.对载体的耐压、强度也有不同要求。近年来一般使用32OAla作为载体。目前国内外开发的低Ni型天然气蒸汽转化催化剂含NiO 12%,而ICI公司近年来研制的PALL环负载NiO量只有2.7%,其活性与工业转化催化剂相同,可见降低Ni用量还大有潜力。 甲烷水蒸气转化反应动力学
当有催化剂时,反应活性能降低,转化速率显著增大,在700-800℃时已具有工业生产价值。催化剂的活性越高,反应速率越快。对于一定的催化剂而言,影响反应速率的主要因素有温度、压力和组成。 温度 温度升高,反应速率常数k增大,反应速率也增大。 压力 总压增高,会使各组分的分压也增高,对反应初期的速率提高很有利。此外,加压尚可使反应体积减少。 组分 原料的组成由水碳比决定,42/CHOH过高时,虽然水蒸气分压高,但甲烷分压过低,反应速率不一定高;反之,42/CHOH过低时,反应速率也不会高。所以水碳比要适当。在反应初期,反应物OHCH24和的浓度高,反应速率高。到反应后期,反应物浓度下降,产物浓度增高,反应速率降低,需要提高温度来补偿。 转化反应是气固相催化过程,包括内外扩散和催化剂表面上吸附、反应、产物脱附和扩散等多个步骤,每个步骤对整个过程的总速率都有影响,最慢的一步控制了总速率。上述动力学方程式是本征动力学方程式。在工业生产中,反应器内气流速度较快,外扩散影响可以忽略。但为了减少床层阻力,所用催化剂颗粒较大(>2mn),故内扩散阻力较大,催化剂内表面利用率较低。在500℃左右时,内表面利用率越30%;温度升到800℃时,内表面利用率仅有1%,这是因为温度升高,表面反应速率加快,孔口侧的反应物消耗快,细孔内反应物浓度因内扩散阻力大而随孔长下降迅速,更多内表面没有被利用。所以,在工业生产中的反应此文档收集于网络,如有侵权请联系网站删除 只供学习与交流 速率r低于本征动力学速率r,两者关系为rr。r考虑了传质过程的影响,减少催化剂的成型颗粒尺寸和制成环形或车轮形或多孔球形,可以提高内表面利用率,从而提高表观反应速率。 甲烷水蒸气转化过程的工艺条件
在选择工艺条件时,理论依据是热力学和动力学分析以及化学工程原理,此外,还需要结合技术经济、生产安全等进行综合优化。转化过程主要工艺条件有压力、温度、水碳比和空速,这几个条件之间互有关系,要适当匹配。 压力 从热力学特征看,低压有利转化反应。从动力学看,在反应初期,增加系统压力,相当于增加了反应物分压,反应速率加快。但到反应后期,反应接近平衡,反应物浓度高,加压反而会降低反应速率,所以从化学角度看,压力不宜过高。但从工程角度考虑,适当提高压力对传热有利,因为甲烷转化过程需要外部供热,大的给热系数是强化传热的前提。床层给热系数9.0beaR,提高压力,即提高了介质密度,是提高雷诺数Re的有效措施。为了增大传热面积,采用多管并联的反应器,这就带来了如何将气体均匀地分布的问题,提高系统压力可增大床层压降,使气流均布于各反应管。虽然提高压力会增加能耗,但若合成气是作为高压合成过程(例如合成氨、甲醇等)的原料时,在制造合成气时将压力提高到一定水平,就能降低后序工段的气体压缩功,使全厂总能耗降低。加压还可以减少设备、管道的体积,提高设备生产强度,占地面积也小。综上所述,甲烷水蒸气转化过程一般是加压的,大约3Mpa左右。 温度 从热力学角度看,高温下甲烷平衡浓度低,从动力学看,高温使反应速率加快,所以出口残余甲烷含量低。因加压对平衡的不利影响,更要提高温度来弥补。在3Mpa的压力下,为使残余甲烷含量降至0.3%(干基),必须使温度达到1000℃。但是,在此高温下,反应管的材质经受不了,以耐高温的HK-40合金钢为例,在3Mpa压力下,要使反应炉管寿命达10年,管壁温度不得超过920℃,其管内介质温度相应为800-820℃。因此,为满足残余甲烷%3.0的要求,需要将转化过程分为两段进行。第一段转化在多管反应器中进行,管间供热,反应器称为一段转化炉,最高温度(出口处)控制在800℃左右,出口残余甲烷10%(干基)左右。第二段转化反应器为大直径的钢制圆筒,内衬耐火材料,可耐1000℃以上高温。对于此结构的反应器,不能再用外加热方法供热。温度在800℃左右的一此文档收集于网络,如有侵权请联系网站删除 只供学习与交流 段转化气绝热进入二段炉,同时补入氧气,氧与转化气中甲烷燃烧放热,温度升至1000℃,转化反应继续进行,使二段出口甲烷降至0.3%。若补入空气则有氮气带入,这对于合成氨是必要的,对于合成甲醇或其他产品则不应有氮。 一段转化炉温度沿炉管轴向的分布很重要,在入口端,甲烷含量最高,应着重降低裂解速率,故温度应低些,一般不超过500℃,因有催化剂,转化反应速率不会太低,析出的少量碳也及时气化,不会积碳。在离入口端1/3处,温度应严格控制不超过650℃,只要催化剂活性好,大部分甲烷都能转化。1/3处以后,温度高于650℃,此时氢气已增多,同时水碳比相对变大,可抑制裂解,温度又高,消碳速率大增,因此不可能积碳了,之后温度继续升高,直到出口处达到800℃左右,以保证低的甲烷残余量。因而,一段转化炉是变温反应器。二段转化炉中温度虽高,但甲烷含量低,又有氧存在,不会积碳。 水碳比 水碳比是诸操作变量中最便于调节的一个条件,又对一段转化过程影响较大。水碳比高,有利于防止积碳,残余甲烷含量也低。实验指出,当原料气中无不饱和烃时,水碳比若小于2,温度到400℃时会析碳,而当水碳比大于2时,温度要高达1000℃才有碳析出;但若有较多不饱和烃存在时,即使水碳比大于2,当温度400℃时就会析碳。为了防止积碳,操作中一般控制水碳比在3.5左右。近年来,为了节能,要降低水碳比,防止积碳可采取的措施有三个,其一是研制、开发新型的高活性、高抗碳性的低水碳比催化剂;其二是开发新的耐高温炉管材料,提高一段炉出口温度;其三是提高进二段炉的空气量,可以保证降低水碳比后,一段出口气中较高残余甲烷能在二段炉中耗尽。目前,水碳比已可降至3.0,最低者可降至2.75。 气流速度 反应炉管内气体流速高有利于传热,降低炉管外壁温度,延长炉管寿命。当催化剂活性足够时,高流速也能强化生产,提高生产能力。但流速不宜过高,否则床层阻力过大,能耗增加。 天然气蒸汽转化流程和主要设备 天然气蒸汽转化制备合成气的基本步骤如下图所示。